Navigating the world of injection mold design feels like walking a tightrope—every factor must be perfectly balanced to achieve the best results.
Pressure balance control in injection mold design ensures uniform distribution of pressure within the mold cavity, reducing defects like warping and shrinkage while enhancing product consistency and manufacturing efficiency.
But there’s so much more to explore! Achieving optimal pressure balance isn’t just about understanding its importance; it’s about diving into the intricate details of design elements that play a pivotal role. Let’s unpack how these components work together to elevate mold design.
Gate design impacts pressure balance in molds.True
Gate design controls melt flow, affecting pressure distribution and quality.
What Role Does Gate Design Play in Pressure Balance?
Gate design is pivotal in ensuring pressure balance within an injection mold, impacting product quality and manufacturing efficiency.
Gate design is integral to achieving pressure balance in injection molds by controlling melt flow and distribution, reducing defects, and enhancing consistency.

Understanding Gate Design in Injection Molding
In the realm of injection mold design1, gate design serves as the entry point for molten plastic into the mold cavity. Its design significantly influences how evenly the material fills the mold, directly affecting the pressure balance. An effective gate design ensures that molten plastic enters the cavity uniformly, minimizing defects such as warping and shrinkage.
Importance of Gate Location and Quantity
The placement and number of gates are crucial. A strategically placed gate can ensure that the flow path is optimized, allowing the melt to reach all parts of the mold simultaneously. Multiple gates or a well-designed gate system can distribute pressure evenly across complex shapes, reducing localized high-pressure zones that might cause defects.
Consider a scenario where a single gate is used for a large part; this could result in uneven pressure distribution, leading to quality issues2. Conversely, multiple gates strategically placed can ensure a more balanced fill.
Gate Design Feature | Impact on Pressure Balance |
---|---|
Single Gate | Potential for uneven pressure distribution |
Multiple Gates | More uniform pressure across the mold |
Gate Size and Shape Considerations
The size and shape of the gate also play a role in pressure distribution. A larger gate might allow for quicker filling but can introduce excess material that requires trimming. Conversely, a smaller gate may restrict flow, increasing fill time and potential for defects. The choice between different gate shapes—such as fan gates or pin gates—can also impact how the melt flows and balances pressure within the cavity.
Optimizing Gate Design for Pressure Balance
To achieve optimal pressure balance, designers often use simulation software to predict how changes in gate design will affect the final product. By adjusting the gate size, shape, and placement during the design phase, engineers can preemptively address potential issues related to pressure imbalance.
In conclusion, while gate design is just one aspect of achieving pressure balance in injection molding, its influence is profound. By carefully considering factors such as location, size, and shape, designers can significantly enhance product quality and production efficiency.
Multiple gates ensure uniform pressure distribution.True
Multiple gates help distribute pressure evenly, reducing defects.
A single gate always provides better pressure balance.False
A single gate can lead to uneven pressure distribution.
How Can Runner System Design Improve Pressure Distribution?
The design of the runner system in injection molds is crucial for achieving a uniform pressure distribution, thereby enhancing product quality and manufacturing efficiency.
A well-designed runner system ensures smooth and even flow of the plastic melt, reducing pressure loss and ensuring uniform pressure distribution throughout the mold cavity.
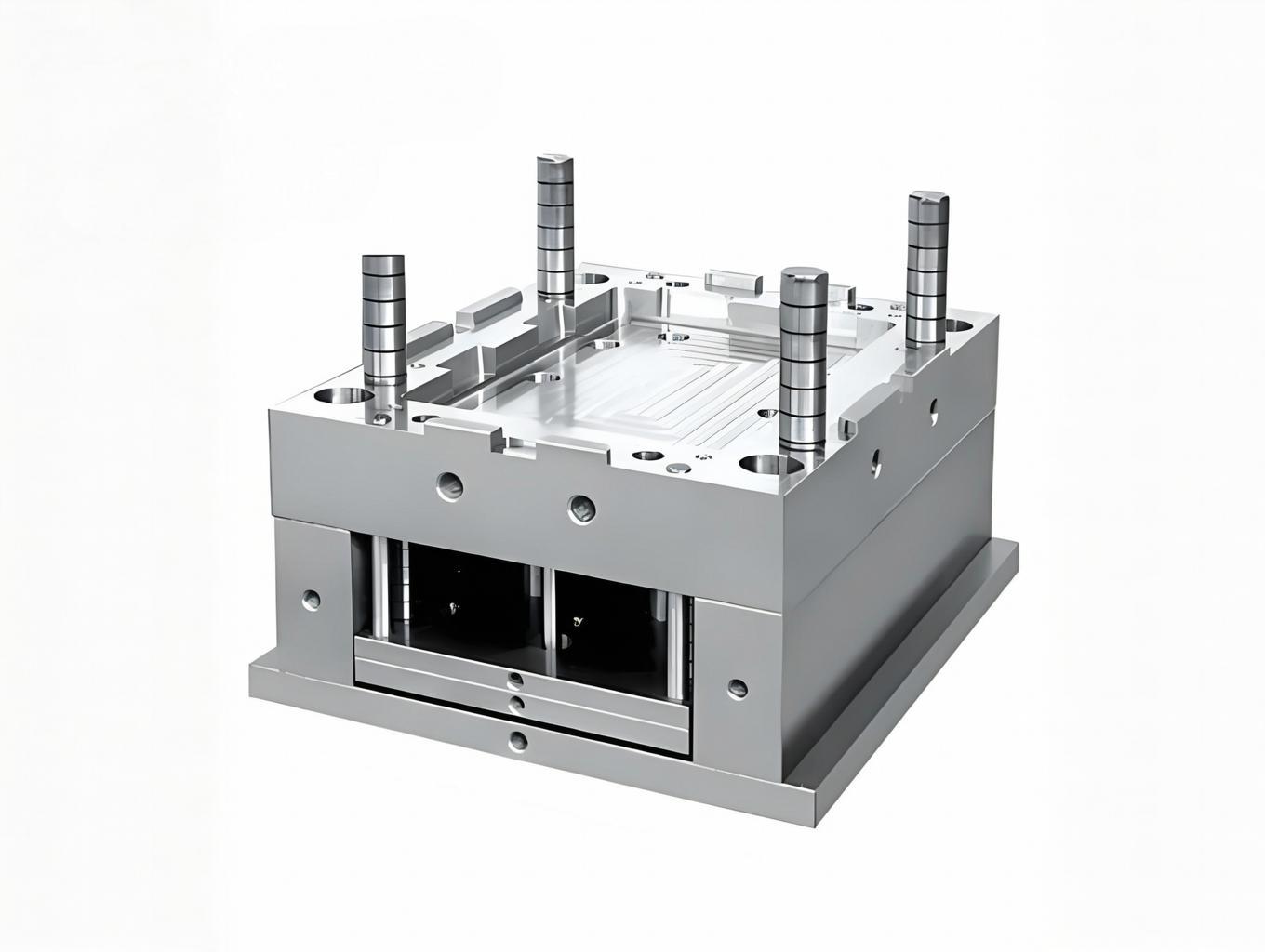
Understanding the Runner System’s Impact
The runner system acts as the pathway for the molten plastic to travel from the injection machine nozzle to the mold cavity. Its design directly influences the pressure balance3, impacting both the quality and efficiency of the molding process.
Key Aspects of Runner System Design
-
Shape and Size:
- The cross-sectional shape of the runner should ideally be circular or trapezoidal. These shapes minimize flow resistance and pressure loss, allowing for a smoother flow.
- The size of the runner needs to be proportionate to the volume of the plastic product and the parameters of the injection molding machine. Oversized runners lead to excessive material use and waste, while undersized runners can cause high-pressure loss.
-
Symmetry and Layout:
- A symmetrical runner design helps in maintaining uniform flow across all cavities. This reduces variations in pressure, which might lead to defects such as sink marks or uneven thickness.
- An optimal layout facilitates uniform filling by minimizing the distance that the melt needs to travel, thus reducing the risk of pressure drop.
Advanced Techniques in Runner Design
-
Hot Runner Systems:
- These systems keep the plastic melt at a constant temperature, minimizing pressure loss due to solidification in cold runners.
- Hot runners help in achieving a better pressure balance by enabling direct injection into multiple cavity points.
-
Use of Simulation Tools:
- Injection molding simulation software can predict how different runner designs will affect pressure distribution. Adjustments can be made based on simulated outcomes to enhance balance and efficiency.
Aspect | Benefit |
---|---|
Shape | Reduces flow resistance |
Size | Ensures adequate flow |
Symmetry | Maintains uniform pressure |
Hot Runner Systems | Minimizes pressure loss |
Simulation Software | Optimizes design parameters |
By focusing on these key aspects, designers can significantly improve pressure distribution, thereby enhancing both the quality of the finished product and the efficiency of the production process.
Circular runners reduce flow resistance in molds.True
Circular cross-sections minimize resistance, ensuring smooth plastic flow.
Oversized runners increase material waste in molding.True
Larger runners use more material than necessary, leading to wastage.
Why Is Mold Temperature Control Critical for Consistency?
Mold temperature control is a pivotal factor in ensuring the consistency and quality of injection-molded products. Without it, manufacturers risk defects that compromise both aesthetics and functionality.
Mold temperature control is essential for maintaining consistent material viscosity during the molding process, ensuring even pressure distribution and preventing defects like warping and shrinkage in final products.
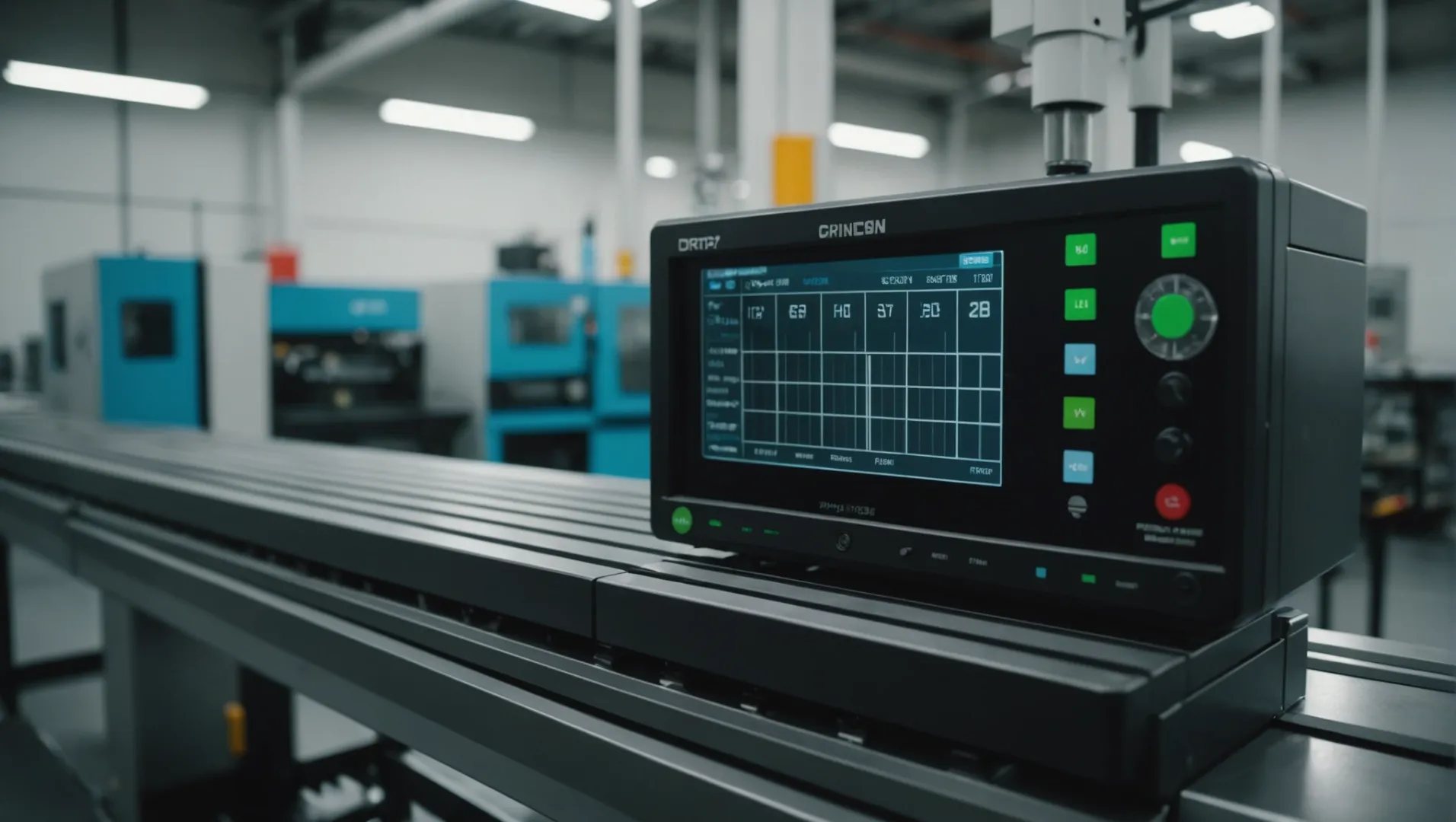
Understanding Mold Temperature Control
Mold temperature plays a crucial role in determining the flow characteristics of the plastic melt within the mold cavity. When the mold temperature is not properly controlled, it can lead to variations in melt viscosity, which in turn affects pressure distribution. This inconsistency can result in defects such as warping and shrinkage marks, ultimately impacting the quality of the final product.
To ensure uniform mold temperature, manufacturers often implement a cooling system that circulates a cooling medium, such as water or oil, throughout the mold. By carefully adjusting the flow and temperature of this medium, manufacturers can maintain consistent mold temperatures and, consequently, consistent product quality.
Impact on Product Quality
Uniform mold temperature ensures that the material flows evenly throughout the mold cavity. This uniformity is critical for achieving high-quality products with precise dimensions and smooth surfaces. Without consistent temperature control, areas of the mold may cool at different rates, leading to uneven shrinkage and warping.
This control also plays a significant role in minimizing internal stresses within the molded part. Products subjected to uneven temperatures during molding may experience differential shrinkage, which can cause structural weaknesses and reduce the overall strength of the product.
Improving Production Efficiency
Proper mold temperature control does not only affect product quality but also enhances production efficiency. By maintaining a consistent temperature throughout the mold, manufacturers can reduce cycle times as the plastic melt fills the cavity more quickly and evenly. This not only speeds up production but also reduces wear and tear on molds and machinery, extending their service life.
Moreover, maintaining optimal mold temperature helps in reducing energy consumption. When temperatures are precisely controlled, less energy is required to heat or cool the mold, resulting in lower operational costs.
Techniques for Effective Temperature Control
-
Cooling System Design: The design of the cooling system is fundamental to effective temperature control. It should be tailored to ensure uniform heat distribution across the entire mold surface.
-
Use of Temperature Controllers: Modern injection molding machines are equipped with sophisticated temperature controllers that provide precise control over the mold temperature. These controllers allow for real-time adjustments based on feedback from temperature sensors embedded in the mold.
-
Simulation Analysis: Utilizing simulation analysis software4 can predict how different temperature settings will affect pressure distribution and product quality. By simulating various scenarios, manufacturers can identify optimal temperature settings before actual production begins.
In summary, mold temperature control is integral to achieving consistent quality in injection molding. It influences everything from material flow to production efficiency, making it a key consideration for manufacturers aiming to enhance both product quality and operational performance.
Mold temperature affects plastic melt viscosity.True
Proper temperature control ensures consistent viscosity, preventing defects.
Uneven mold temperatures lead to uniform shrinkage.False
Uneven temperatures cause differential shrinkage, leading to defects.
How Does Simulation Software Aid in Optimizing Pressure Balance?
Simulation software transforms how designers approach pressure balance, enabling precise control and optimization within injection molds.
Simulation software predicts and optimizes pressure distribution in injection molds by analyzing various design elements, thus enhancing product quality and efficiency.
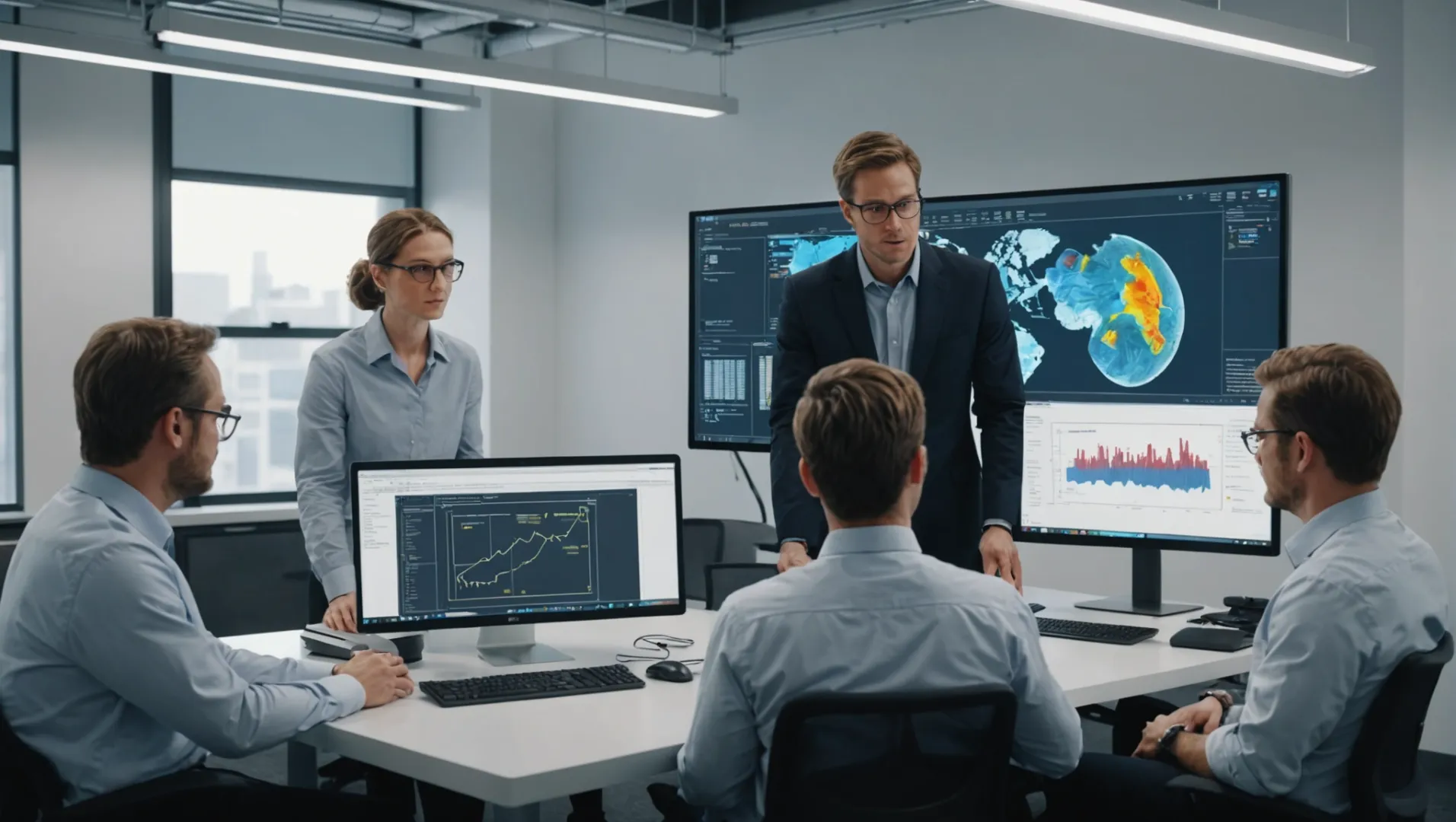
Understanding Simulation Software in Injection Molding
Simulation software serves as a digital twin of the injection molding process5, providing insights that are otherwise difficult to obtain. By virtually modeling the mold design, engineers can predict how the plastic melt will behave under different conditions. This predictive capability is crucial for optimizing pressure balance.
The Role of Simulation Software in Pressure Distribution
-
Gate Design Analysis: Simulation allows for the testing of multiple gate designs without physically altering the mold. By running simulations, engineers can determine which gate configuration provides the most uniform pressure distribution across the mold cavity.
- Example: In one scenario, a multi-point gate system might show better results in terms of pressure balance compared to a single gate design.
-
Runner System Optimization: The software helps in visualizing the flow of plastic through the runner system. Adjustments can be made to runner size and layout based on simulation results to minimize flow resistance and pressure loss.
- Example: A circular cross-sectional shape might be recommended by the simulation over a rectangular one due to less pressure loss.
-
Mold Temperature Control: Through simulation, engineers can assess how varying mold temperatures affect the viscosity and flow of the plastic melt, impacting pressure distribution. This insight allows for better cooling system designs that ensure consistent mold temperature.
Advantages of Using Simulation Software
- Cost Efficiency: Reduces the need for physical prototyping, saving time and material costs.
- Enhanced Product Quality: Predicts potential defects like warping and shrinkage, allowing for preemptive design adjustments.
- Faster Time-to-Market: Speeds up the design process by allowing rapid iterations and testing.
Incorporating simulation software into the design process not only aids in achieving optimal pressure balance but also enhances overall product quality and production efficiency. By effectively simulating different scenarios, engineers can make informed decisions that lead to superior mold designs.
Simulation software predicts pressure in injection molds.True
Simulation software analyzes design elements to predict pressure distribution.
Physical prototyping is more efficient than simulation.False
Simulation reduces costs and time compared to physical prototyping.
Conclusion
In summary, mastering pressure balance control is essential for enhancing product quality and manufacturing efficiency in injection molding. By fine-tuning each design element, we can create molds that deliver exceptional performance.
-
Learn why gate design is crucial for effective mold filling.: The runner and gate system used in plastic injection molding is responsible for directing molten plastic from the nozzle of the molding … ↩
-
Discover how gate placement affects product quality.: The location of gates not only determines the flow direction of polymers and flow balance, but also affects the shapes of the front of the … ↩
-
Explore detailed benefits of well-designed runner systems in injection molding.: Also, with hot runner systems, lower injection pressures can generally be used, which will reduce mold and platen deflection and keep flash … ↩
-
Discover how simulation software improves mold design and temperature control strategies.: Through simulation software, manufacturers can optimize their injection molding processes while increasing part quality while decreasing … ↩
-
Learn how simulation software revolutionizes injection molding processes.: The simulation allows manufacturers to predict potential issues such as air traps, sink marks, and weld lines before creating physical molds, … ↩