Getting ready for injection molding isn’t just a checklist; it’s an art form that can make or break your production quality.
To prepare for injection molding, start with selecting suitable plastic raw materials, conducting mold inspections, and ensuring equipment readiness. These steps help prevent defects and ensure smooth operations.
While this brief overview touches on the essentials, a deeper dive into each preparation step will provide invaluable insights. Read on to uncover expert tips and best practices that are vital for achieving optimal results in injection molding.
Drying is crucial for hygroscopic plastics.True
Drying removes moisture, preventing defects like bubbles during injection molding.
What Are the Key Steps in Raw Material Preparation?
Raw material preparation is the foundation of successful injection molding, ensuring quality and efficiency in production.
Key steps in raw material preparation include selecting appropriate plastics, conducting thorough inspections, and ensuring proper drying. These steps are crucial to maintaining product integrity and preventing defects like bubbles and discoloration.
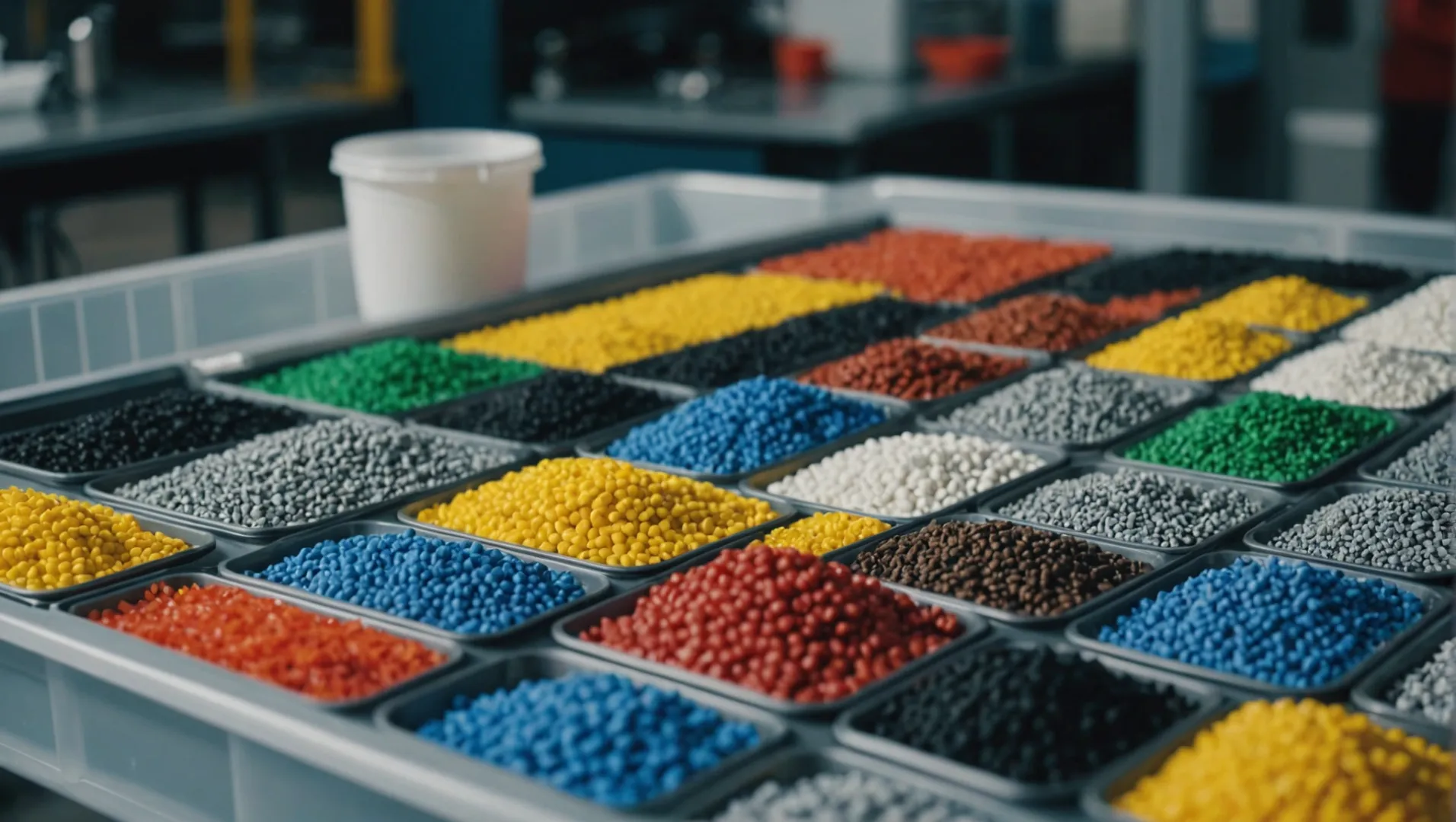
Selecting Suitable Plastic Raw Materials
Choosing the right plastic raw materials is paramount. The selection process involves evaluating the performance requirements1 of the final product, such as heat resistance and mechanical strength, as well as considering the environment in which the product will be used. For example, if a product will be exposed to high temperatures, plastics with strong heat resistance should be prioritized.
Cost and supply stability are also crucial factors. While high-performance plastics may offer superior qualities, they might not be cost-effective for all projects. Balancing these aspects ensures that production remains sustainable and economically viable.
Conducting Raw Material Inspections
Once the materials are selected, inspection is necessary to maintain quality. This process starts with a visual check to identify any impurities, discoloration, or abnormalities in the raw materials. These inspections prevent unwanted defects that could arise during molding.
Physical property tests, such as measuring melt index and density, ensure that the materials meet specific quality standards. This step verifies that the plastic will perform as expected under operational conditions.
Implementing Drying Treatments
Certain plastics, like nylon and polycarbonate, are highly hygroscopic, meaning they absorb moisture from the air. Before molding, these materials require drying to remove moisture content, which could otherwise vaporize during the injection process and cause defects like bubbles.
Drying involves selecting appropriate equipment and conditions, such as temperature and time, tailored to the specific plastic’s properties. This step is crucial for achieving a smooth finish and maintaining the structural integrity of the molded product.
Plastic Type | Drying Temperature | Drying Time |
---|---|---|
Nylon | 80°C – 90°C | 2 – 4 hours |
Polycarbonate | 100°C – 120°C | 2 – 6 hours |
By following these key steps in raw material preparation, manufacturers can significantly reduce the risk of defects and ensure a high-quality end product. Understanding these fundamentals provides a robust foundation for successful injection molding operations.
Nylon requires drying before injection molding.True
Nylon is hygroscopic and absorbs moisture, needing drying to prevent defects.
Polycarbonate does not need drying treatments.False
Polycarbonate is hygroscopic and requires drying to avoid defects.
How Do You Conduct a Thorough Mold Inspection?
Ensuring your molds are in top condition is critical for the efficiency and quality of the injection molding process. A comprehensive inspection helps avoid costly defects and production delays.
A thorough mold inspection involves checking for physical damage, ensuring cleanliness, verifying functionality of the cooling system, and confirming the integrity of parting surfaces and gates.
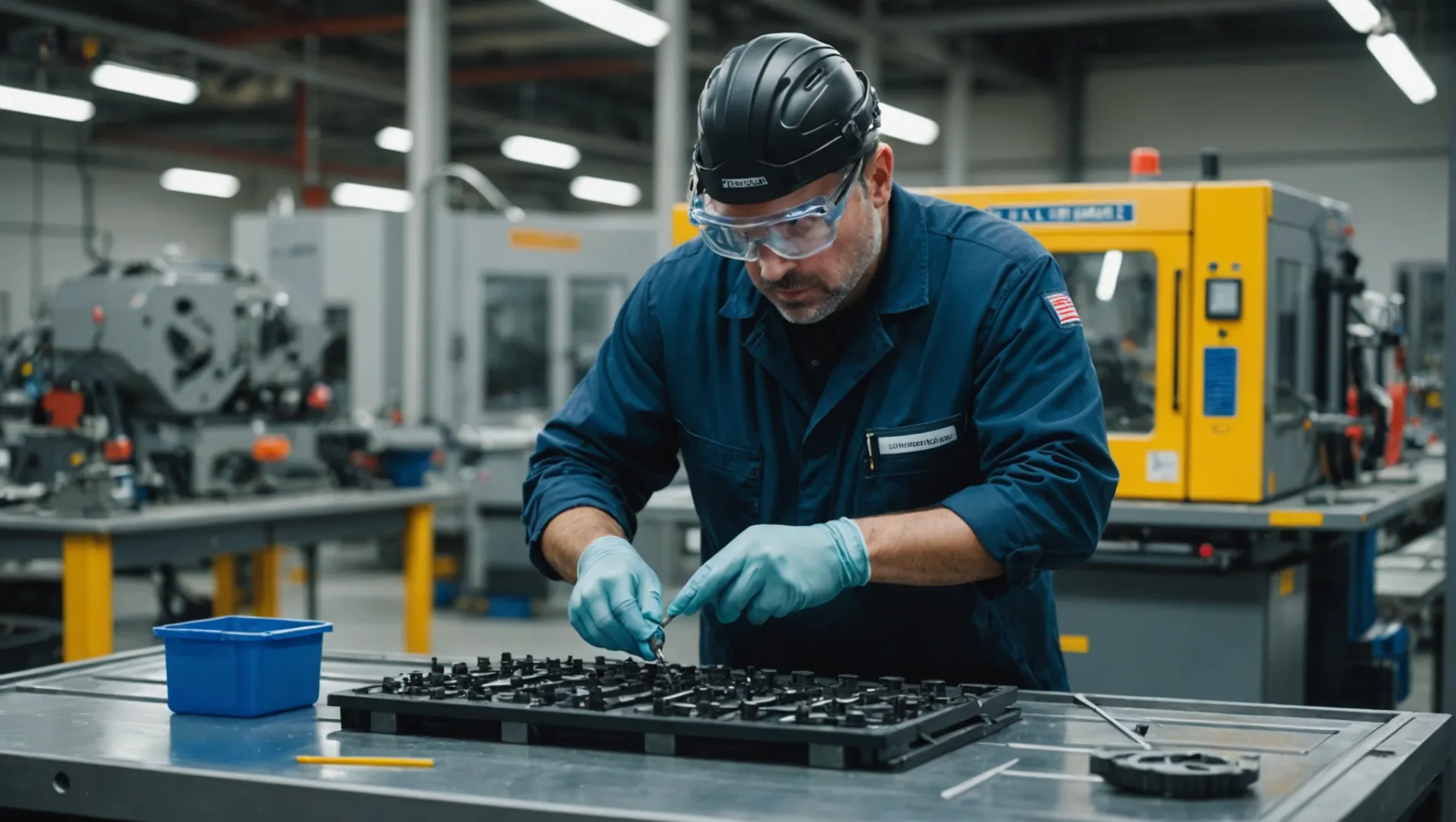
Importance of Mold Inspection
Conducting a detailed mold inspection is paramount to maintaining product quality and preventing production hiccups. Without proper checks, issues such as contamination, improper cooling, or damage can lead to defective products.
Steps for a Comprehensive Mold Inspection
Physical Inspection
-
Check for Damage: Begin by examining the mold’s exterior and interior for any signs of damage, such as cracks, dents, or rust. Such damages can affect the mold’s performance and the quality of the final product.
-
Ensure Cleanliness: The mold should be free of dirt, grease, or any foreign particles. Use appropriate cleaning solutions to maintain a spotless surface.
Parting Surface and Gates
-
Parting Surface: Ensure that the parting surfaces are smooth and free from wear or tear. Uneven surfaces can lead to flash in the molded parts.
-
Gates and Vents: Inspect gates for clogs or damage and verify that vents are clear. Blockages here can impede the flow of material and affect the part’s integrity.
Cooling System Verification
-
Waterways: Check that all waterways in the mold’s cooling system are unobstructed. This ensures efficient heat dissipation during molding, which is crucial for maintaining the cycle time and quality of the parts.
-
No Leaks: Confirm there are no leaks in the cooling system, as these can cause uneven cooling and warping in the finished product.
Additional Considerations
-
Preheat Requirements: For molds used with high-temperature plastics like engineering thermoplastics, preheating may be necessary. This ensures uniform temperature distribution, reducing stress and deformation in parts.
-
Regular Maintenance: Implement a routine maintenance schedule to address wear and prolong the lifespan of your molds. This includes replacing worn-out components such as seals and heaters.
By following these meticulous steps, you ensure that your mold is primed for optimal performance in injection molding2. Regular inspections not only help maintain quality but also extend the life of your molds.
Mold cleanliness impacts product quality.True
Clean molds prevent contamination, ensuring higher product quality.
Cooling system leaks are harmless in molds.False
Leaks cause uneven cooling, leading to warped and defective parts.
What Equipment Checks Are Essential Before Starting?
Ensuring your equipment is in top condition before starting injection molding can prevent costly delays and defects.
Essential equipment checks include inspecting the injection molding machine for damage, verifying the hydraulic and electrical systems, and ensuring precise temperature control. These steps prevent operational issues and maintain production quality.

Inspecting the Injection Molding Machine
Before starting any injection molding operation, it’s imperative to meticulously inspect the injection molding machine. This begins with a visual check to ensure there’s no visible damage or signs of oil or other fluid leaks. Any such issues should be addressed immediately to prevent operational interruptions.
Hydraulic System Check
The hydraulic system is crucial for the machine’s function, as it controls the movement of various machine parts. Verify that there are no leaks and that all hydraulic lines are securely connected. The pressure levels should be checked to ensure they meet the specifications outlined by the manufacturer.
Electrical System Verification
Examine the electrical components of the machine, including wiring and connections, to ensure they are intact and properly insulated. This step is essential to avoid electrical failures or hazards during operation.
Ensuring Accurate Temperature Control
The heating system is another critical component that must be functioning correctly. The system’s ability to maintain precise temperature control affects the quality of the molded product. Inspect heating elements and sensors for any signs of wear or malfunction.
For a more detailed checklist on injection molding machine inspections3, industry guidelines can provide comprehensive procedures.
Debugging and Parameter Adjustment
Once the initial inspections are complete, proceed with debugging the machine. Adjust parameters such as injection pressure, speed, holding pressure, and time based on the specific requirements of the product and mold. This ensures that each cycle runs smoothly and consistently.
Perform idle operation tests to confirm that all moving parts operate smoothly without unusual noise or vibrations. This step is vital for preventing disruptions during actual production runs.
A detailed guide on parameter adjustments for injection molding4 can provide further insights into optimizing machine settings.
Final Preparations for Smooth Operations
Conclude equipment preparations by ensuring the production environment is conducive to quality molding operations. Maintain optimal temperature and humidity levels, and ensure the workspace is clean and free from debris that could interfere with machine functions.
With these checks completed, you can commence injection molding with confidence, knowing that your equipment is in prime condition to deliver high-quality results.
Hydraulic leaks can delay injection molding production.True
Leaks in the hydraulic system can cause operational interruptions.
Electrical system checks are optional before molding.False
Checking electrical components is essential to avoid failures.
Why Is Operator Training Crucial for Injection Molding Success?
Operator training is vital for injection molding success, directly impacting product quality and operational efficiency.
Operator training ensures staff understand the injection molding process, equipment handling, and safety protocols, minimizing defects and downtime.
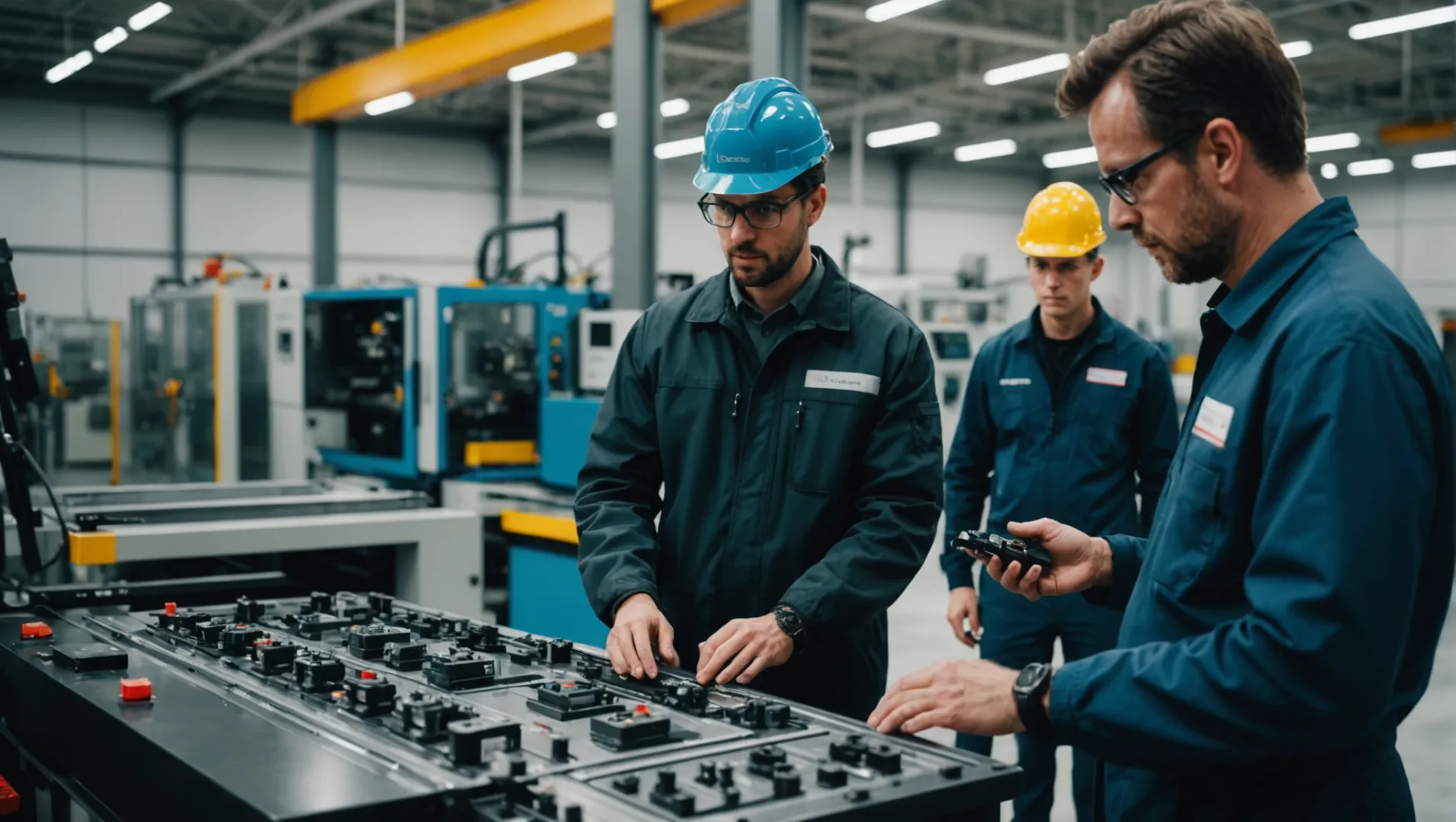
Understanding the Role of Operator Training
Operator training is not just a procedural requirement; it’s a strategic necessity for optimizing the injection molding process5. Trained operators can effectively manage the complexities of the machinery and the nuances of material properties, leading to consistent production quality.
Key Aspects of Operator Training
-
Process Familiarity: Operators must grasp the entire injection molding process, from raw material preparation to final product inspection. This understanding allows them to identify and address issues promptly, reducing waste and increasing efficiency.
-
Equipment Operation: Proficiency in equipment operation is essential. Operators should know how to set parameters like temperature, pressure, and cycle times accurately. This knowledge helps in optimizing machine performance and preventing malfunctions.
-
Safety Protocols: Injection molding involves high temperatures and pressures, posing safety risks. Comprehensive training on safety measures can prevent accidents and ensure a safe working environment.
Training Methods and Tools
-
Hands-On Workshops: Practical training sessions enable operators to experience real-time problem-solving scenarios.
-
Simulation Software: Utilizing software simulations can help operators visualize the process and practice decision-making in a risk-free environment.
-
Continuous Education: Regular updates on industry advancements keep operators informed about new techniques and technologies.
Benefits of Effective Training
Proper operator training results in reduced defect rates and improved product quality. It also contributes to better equipment maintenance and longevity, as operators can perform routine checks and minor repairs.
Incorporating structured training programs into your production setup is a proactive step towards ensuring smooth operations6 and achieving consistent success in injection molding.
Operator training minimizes injection molding defects.True
Training ensures operators understand processes, reducing errors and defects.
Untrained operators can safely manage injection molding equipment.False
Without training, operators risk mishandling equipment, causing accidents.
Conclusion
Thorough preparation is the cornerstone of successful injection molding. By focusing on each step from raw materials to operator training, you can enhance both product quality and production efficiency.
-
Discover suitable plastics based on specific performance needs.: Learn how to select the right material for your injection molding design with this technical overview of thermoplastic resins. ↩
-
Discover more about advanced techniques for inspecting injection molds.: 9:Spread mold # with lacquer and marked the direction of placement. 10:Wooden box need be fixed firmly. 11:All the things in the packing list need be full. ↩
-
Provides comprehensive procedures for thorough equipment inspections.: Injection Molding Machine Preventive Maintenance & Checklist for Most Seen Brands · (1) Selection of hydraulic oil · (2) Working temperature of … ↩
-
Offers insights into optimizing machine settings for best results.: Regularly Monitor and Adjust Parameters: Keeping a close eye on parameters like injection pressure, mold temperature, and injection speed helps … ↩
-
Learn how trained operators enhance product quality and process efficiency.: Less damage to injection molds and extrusion dies · Reductions in unplanned machine downtime · Faster, more efficient troubleshooting · Far fewer part defects … ↩
-
Discover how training boosts efficiency and reduces defects in manufacturing.: When everyone is on the same page with consistent training, fewer mistakes and accidents will happen, and productivity and morale will improve. If you’re still … ↩