Have you ever watched a perfectly molded piece warp or shrink unexpectedly? It’s frustrating, right? That’s the challenge of shrinkage in injection molding!
To predict and control shrinkage in injection molding, it’s essential to analyze material properties, evaluate mold design, and simulate process parameters. By optimizing these factors, manufacturers can enhance product quality and dimensional accuracy.
Understanding shrinkage is just the beginning! Dive into effective strategies that tackle shrinkage head-on, ensuring you maintain exceptional standards in your production line.
Material properties affect shrinkage in injection molding.True
Material properties like thermal expansion and moisture absorption impact shrinkage.
What Role Do Material Properties Play in Shrinkage?
Material properties significantly impact shrinkage in injection molding, influencing the final product’s quality and accuracy.
Material properties like shrinkage rate, thermal expansion, and moisture absorption directly affect shrinkage in injection molding. Understanding these properties helps predict and control the shrinkage during production, ensuring optimal product dimensions and quality.

The Science Behind Material Shrinkage
Material properties are pivotal in determining the shrinkage behavior during the injection molding process. Each material exhibits unique characteristics such as a specific linear shrinkage rate, which refers to the dimensional change per unit length, and volume shrinkage rate, describing the overall change in volume. These properties are crucial for predicting shrinkage before production.
Manufacturers can consult technical data sheets provided by material suppliers to gather detailed information about these properties. This data allows them to adjust parameters in the molding process to minimize unwanted shrinkage effects.
Thermal Expansion and Its Impact
The coefficient of thermal expansion (CTE) is another critical property. Materials with high CTE are more susceptible to dimensional changes with temperature fluctuations during molding. For instance, certain polymers may expand significantly when heated and contract upon cooling, leading to variations in the final product size. Monitoring the CTE helps manufacturers anticipate these changes and adjust cooling times or mold temperatures accordingly.
Influence of Moisture Absorption
Some polymers are hygroscopic, meaning they absorb moisture from the environment. This absorbed moisture can cause swelling during processing and subsequent shrinkage as the material dries out post-molding. To combat this, manufacturers might pre-dry materials before molding to ensure consistent moisture content, thereby controlling shrinkage more effectively.
Choosing Materials with Lower Shrinkage
For applications where dimensional precision is critical, selecting materials with inherently low shrinkage rates is beneficial. Engineering plastics or materials fortified with fillers often exhibit reduced shrinkage compared to standard polymers. By choosing the right material for the job, manufacturers can naturally limit shrinkage and improve product consistency.
Analyzing Material Properties: A Practical Approach
A practical approach involves performing trial runs with different materials and observing their shrinkage patterns under controlled conditions. By using simulation software1, engineers can predict how various materials behave under specific molding conditions, making it easier to select optimal materials for each project.
These simulations often involve adjusting parameters like injection pressure and temperature to understand their interplay with material properties.
By leveraging an understanding of material properties, manufacturers can refine their injection molding processes to achieve superior dimensional accuracy and product quality.
Material shrinkage rate affects product dimensions.True
Shrinkage rate impacts the final size and accuracy of molded products.
Moisture absorption does not influence shrinkage.False
Moisture absorption causes swelling and subsequent shrinkage in polymers.
How Does Mold Design Influence Shrinkage?
Mold design is a critical factor in managing shrinkage during injection molding, affecting product quality and precision.
Mold design significantly influences shrinkage by affecting cooling uniformity, wall thickness, and demolding ease. Proper design can minimize shrinkage variations, enhancing product quality.
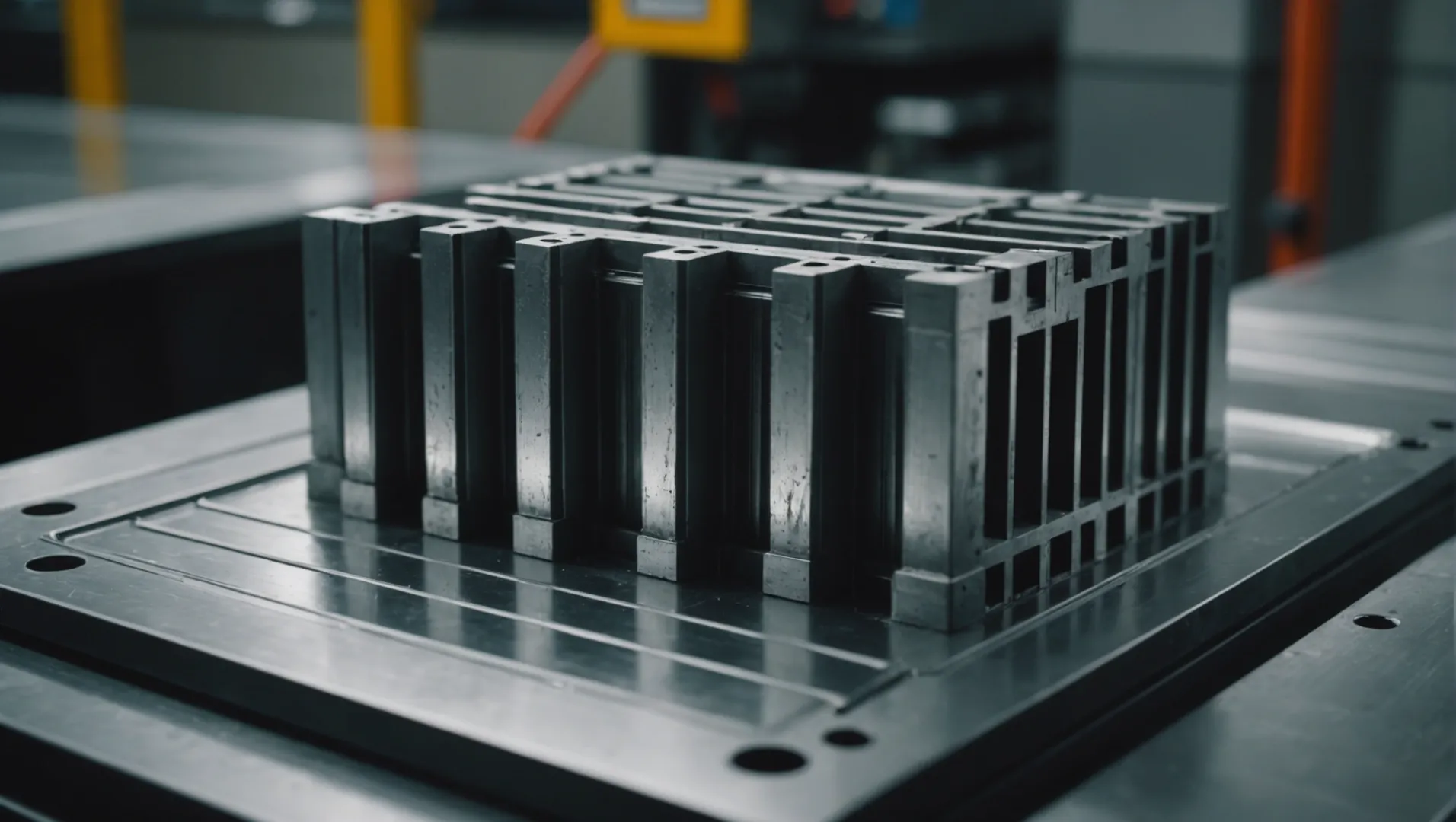
Importance of Mold Design in Shrinkage Control
The design of the mold plays a pivotal role in determining how a product shrinks after the injection molding process. Factors like wall thickness, cooling system design, and demolding slopes need to be meticulously planned to mitigate shrinkage issues.
-
Wall Thickness: Uniform wall thickness across the product ensures even cooling, which is crucial for minimizing shrinkage. Uneven thickness can lead to differential shrinkage, causing warping or distortion. Hence, maintaining a consistent wall thickness is a key design consideration.
-
Cooling System: An effective cooling system helps achieve uniform cooling across the entire mold, thereby reducing shrinkage variations. By employing simulation software, designers can evaluate the cooling effect of different system configurations and make informed adjustments. Check out cooling system simulation2 for more insights.
-
Demolding Slopes: Adequate demolding angles facilitate easy removal of the product from the mold without applying excessive force, which could otherwise cause deformation. Properly designed slopes reduce stress on the product, thus minimizing shrinkage.
Simulation and Predictive Analysis
Modern technologies allow for the use of simulation tools to predict how different mold designs will impact shrinkage. These tools simulate various scenarios, providing insights into the best design practices to reduce shrinkage.
-
Predictive Software: By simulating the injection process under various conditions, manufacturers can predict potential shrinkage and make proactive design adjustments. See mold simulation software3 for detailed guidance.
-
Material-Specific Considerations: Different materials exhibit varying shrinkage rates. Mold designs should account for these variations to ensure compatibility and optimal performance. For instance, materials with higher thermal expansion rates may require more complex cooling channel configurations.
Case Study: Successful Mold Design Adjustments
Consider a case where uneven cooling led to significant shrinkage discrepancies in a complex-shaped product. By redesigning the cooling channels and adjusting the wall thickness, the manufacturer achieved a notable reduction in shrinkage variation, highlighting the critical role of thoughtful mold design.
For more case studies, explore successful mold design cases4. This link offers practical insights into how companies have tackled shrinkage challenges through strategic mold design adjustments.
Uniform wall thickness reduces shrinkage in injection molding.True
Consistent wall thickness ensures even cooling, minimizing shrinkage.
Mold design does not affect product demolding ease.False
Proper demolding slopes reduce stress, easing product removal.
Can Simulation Software Predict Shrinkage Accurately?
Simulation software offers powerful tools for predicting shrinkage, enhancing precision in injection molding.
Yes, simulation software can accurately predict shrinkage by modeling material behavior, mold design, and processing parameters. By replicating real-world conditions, it helps manufacturers optimize their processes to reduce defects and improve product quality.

Understanding the Capabilities of Simulation Software
Simulation software is designed to replicate the intricate dynamics of injection molding processes5, providing insights that are otherwise difficult to achieve. These programs utilize mathematical models to predict how different materials will behave under various conditions.
-
Material Behavior Modeling
- Each type of plastic material has unique properties that affect its shrinkage rate. Simulation software can incorporate these specific characteristics, including the linear and volumetric shrinkage rates, allowing for precise predictions.
- By simulating different environmental conditions, such as temperature and humidity, the software helps in understanding how these factors influence material shrinkage.
-
Mold Design Analysis
- The design and structure of a mold significantly impact shrinkage. Simulation software can analyze these designs to identify potential shrinkage issues, particularly in areas with non-uniform wall thickness.
- The cooling system is a critical element in mold design. Simulations can optimize cooling channel layouts and predict their effects on product cooling and consequent shrinkage.
-
Process Parameter Simulation
- Injection molding involves several parameters like injection pressure, temperature, and cooling time. Simulation software allows experimentation with these variables to see their effects on shrinkage.
- By visualizing the filling and cooling processes, manufacturers can adjust parameters to minimize shrinkage and maintain product integrity.
Benefits of Using Simulation Software
The primary advantage of simulation software lies in its ability to test multiple scenarios without the cost and time associated with physical trials. This leads to:
- Improved Efficiency: By optimizing processes before actual production, manufacturers can reduce waste and increase throughput.
- Enhanced Quality Control: More accurate predictions mean fewer defects and higher quality products.
- Cost Savings: Reducing the need for physical prototyping and iterations saves both time and resources.
Simulation software thus becomes an invaluable tool in the arsenal of any manufacturer aiming to refine their injection molding processes6 and tackle shrinkage with precision.
Simulation software can predict shrinkage accurately.True
Simulation software uses models to replicate real-world conditions, enabling accurate predictions.
Mold design has no impact on shrinkage prediction.False
Mold design significantly affects shrinkage; simulation software analyzes this for accuracy.
What Are the Best Practices for Optimizing Process Parameters?
Process parameter optimization is crucial for ensuring efficiency and quality in injection molding.
Optimizing process parameters involves adjusting temperature, pressure, holding time, and cooling time to minimize shrinkage and defects. Implementing these adjustments based on material and product specifications ensures high-quality outcomes.
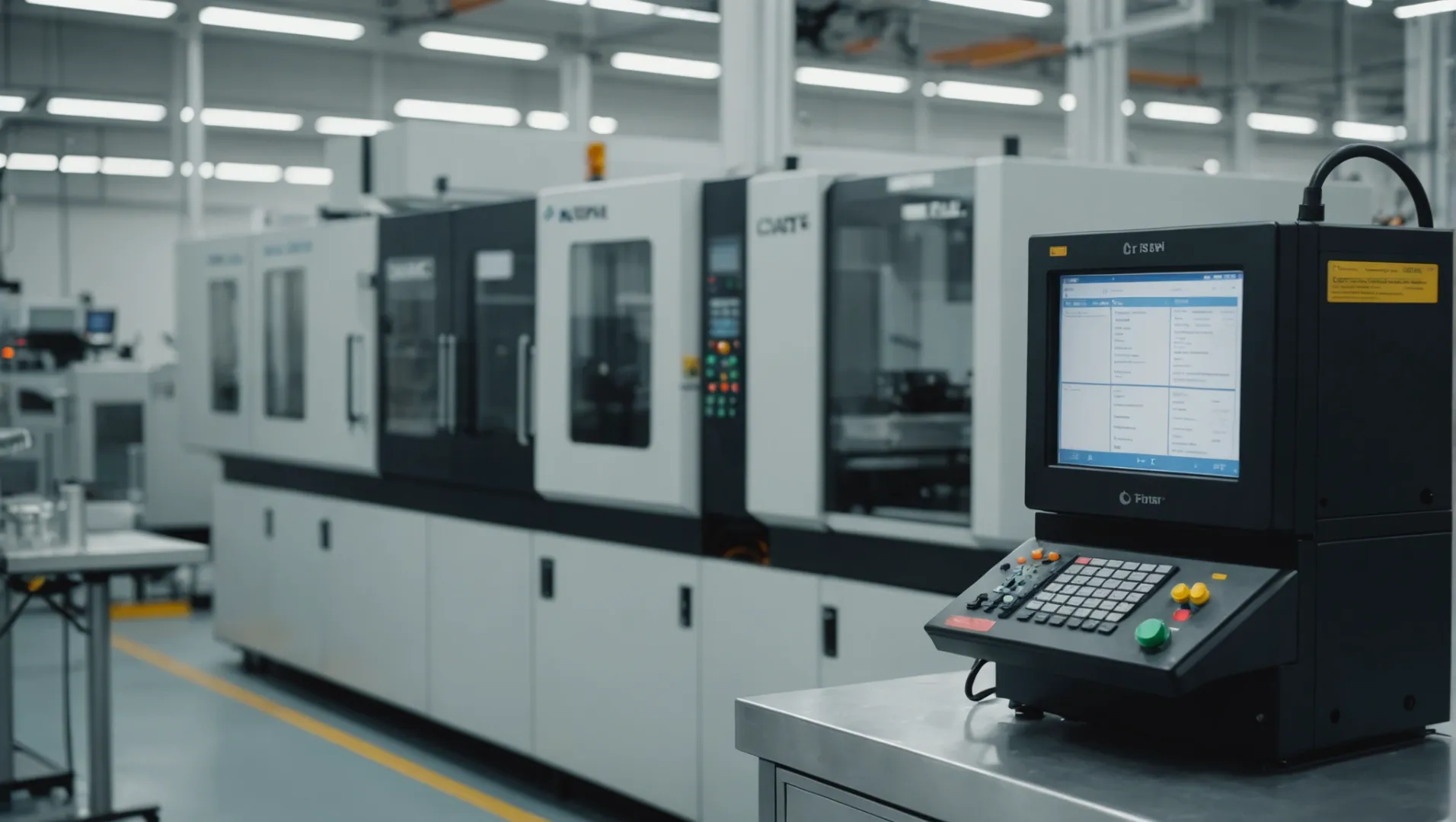
Understanding the Key Process Parameters
In the realm of injection molding, several process parameters can be fine-tuned to optimize production outcomes. These include injection temperature, injection pressure, holding time, and cooling time. Each of these parameters interacts with the others, creating a complex web of factors that influence the final product’s quality.
Injection Temperature
Setting the correct injection temperature is vital. A temperature too high may cause material degradation, while a temperature too low can lead to poor flow and incomplete mold filling. Manufacturers should determine the ideal temperature range for the specific material in use by consulting technical specifications and conducting experimental trials7.
Injection Pressure
The injection pressure must be sufficient to ensure complete mold filling but not so high that it induces internal stresses or damages the mold. Adjusting pressure involves a delicate balance and often requires pressure monitoring systems8 to achieve optimal results.
Parameter | Impact on Product Quality |
---|---|
Injection Temperature | Affects material flow and potential degradation. |
Injection Pressure | Influences mold fill density and internal stress. |
Holding Time | Determines product dimensional stability. |
Cooling Time | Ensures proper solidification and reduces warping. |
Holding Time and Cooling Time
Holding Time: The duration for which pressure is applied to the mold cavity after initial filling is crucial. A longer holding time can reduce shrinkage by allowing more material to pack into the mold, yet it also increases cycle time and energy consumption.
Cooling Time: Sufficient cooling time ensures that the product solidifies correctly and reduces post-molding shrinkage. However, excessive cooling can prolong production cycles unnecessarily. Utilizing simulation software helps in determining the optimal cooling time for specific products based on their geometry and material properties.
Implementing Simulation Software
Simulation software plays an invaluable role in process parameter optimization by allowing manufacturers to visualize how changes in parameters will affect product outcomes. Through virtual trials, companies can preemptively address issues like shrinkage and warping, ensuring that process adjustments are data-driven rather than trial-and-error.
By comprehensively analyzing these elements, manufacturers can refine their injection molding processes, leading to improved efficiency and reduced defect rates. Implementing best practices in parameter optimization is not just about achieving precision; it’s about maintaining consistency and elevating production standards across the board.
High injection temperature may degrade material quality.True
Excessive heat can break down the polymer chains, affecting quality.
Cooling time should be minimized to enhance product quality.False
Adequate cooling is essential to ensure proper solidification and reduce defects.
Conclusion
Mastering shrinkage control in injection molding not only ensures product quality but also reduces waste. Implement these strategies to enhance efficiency and precision in your manufacturing processes.
-
Explore top software tools for precise shrinkage predictions.: With the best-in-class analysis technology, Moldex3D can help you carry out in-depth simulation of the widest range of injection molding processes and to … ↩
-
Explore how simulation optimizes cooling systems to reduce shrinkage.: Moldex3D Cool provides the troubleshooting tools to detect possible mold cooling system defects, such as unbalanced cooling, hot spots, prolonged cooling time … ↩
-
Learn about software that predicts shrinkage effectively.: With Warp, users can easily validate part deforming ratio of shrinkage effect and efficiently identify warpage causes. For fiber-filled material, Warp … ↩
-
Discover real-world examples of effective mold design solutions.: One of the most effective ways to avoid shrinkage problems in injection molding is to optimize the cooling effects. Cooling channels or plates in the mold … ↩
-
Learn how simulation software enhances process control and product quality.: Injection molding simulation software is used to make better molded parts and reduce defects. It does this by digitally simulating virtually every aspect of … ↩
-
Discover cost-saving advantages and efficiency gains with simulation tools.: Process simulation can be an invaluable tool to compare alternatives and justify the cost for manufacturing and manufacturing-related processes. ↩
-
Learn techniques for setting precise injection temperatures.: Suggested Temperatures for Different Plastics ; PPS (Polyphenylene Sulfide) & POM (Polyoxymethylene), PPS: 120-180℃, POM: 80-105℃, PPS can withstand high … ↩
-
Discover tools for precise pressure management.: Our sensors for the monitoring of injection molding processes includes pressure sensors (direct, indirect, contactless) and temperature sensors. ↩