Join me on an adventure into the exciting realm of precision injection molding – an important force in today’s production world.
Precision injection molding is considered the best choice due to its ability to achieve high dimensional accuracy and consistent quality across various applications. It is widely used in industries requiring precise specifications, such as electronics, medical, automotive, and aerospace.
There’s much more to this story! Learning its different uses and special benefits shows why industries probably want this new technology. Discover why precision injection molding is very important.
Precision injection molding achieves high dimensional accuracy.True
It employs regulated steps and modern tools for fewer mistakes.
How Does Precision Injection Molding Achieve High Dimensional Accuracy?
Precision injection molding stands as the benchmark for reaching unmatched dimensional accuracy in production.
Precision injection molding achieves high dimensional accuracy through controlled processes, advanced equipment, and rigorous quality standards, ensuring minimal error margins.
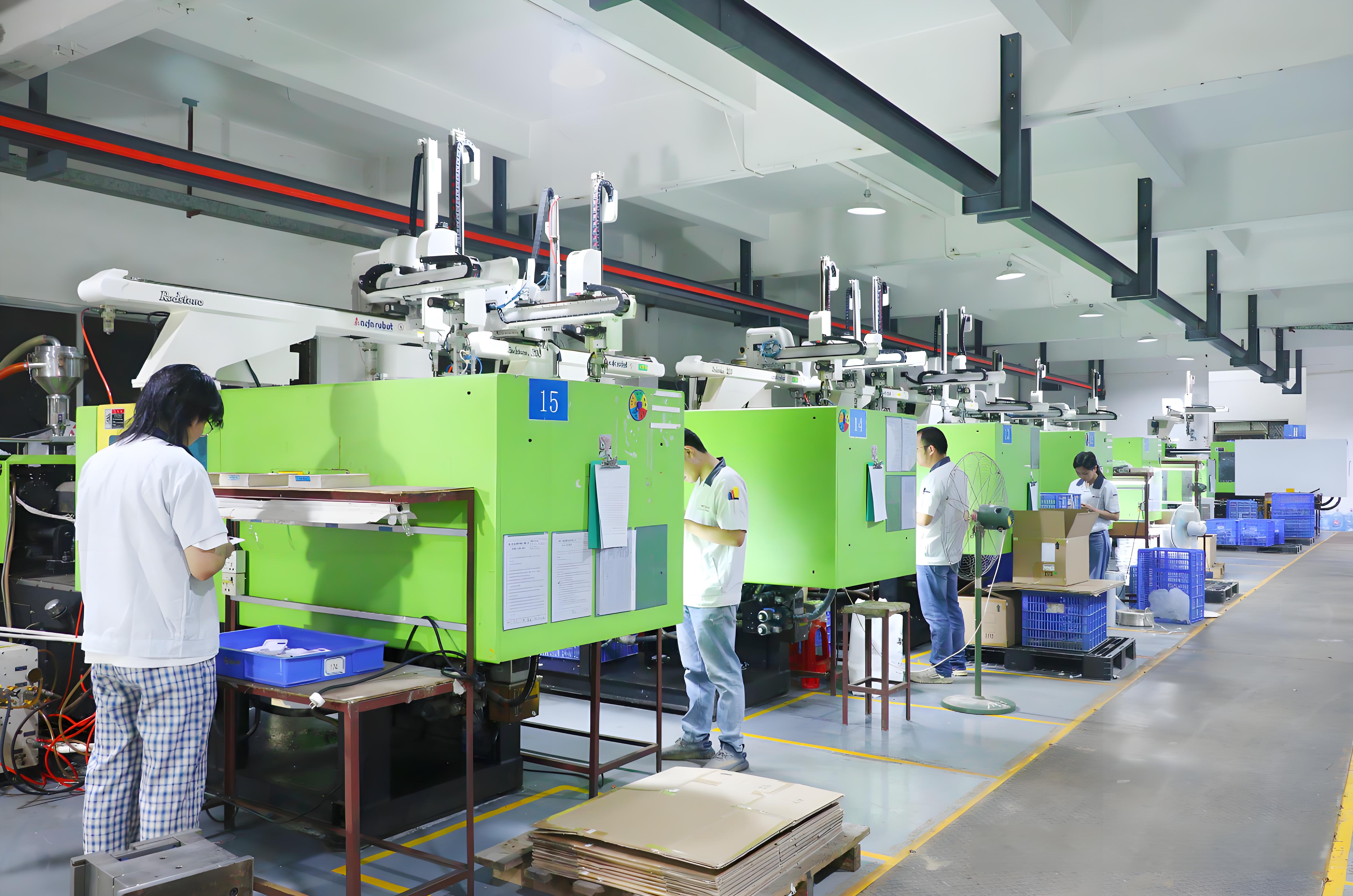
The Core Principles of Precision Injection Molding
At the heart of precision injection molding1 is a meticulous process that combines advanced technology with a deep understanding of material behavior. This process involves injecting molten plastic into a precisely crafted mold, where it cools and solidifies into the desired shape. The key to achieving high dimensional accuracy lies in the control of several critical parameters:
- Temperature Control: Precise regulation of temperature is crucial to ensure consistent material flow and shrinkage rates, which directly impact the final product’s dimensions.
- Pressure Management: Maintaining optimal pressure throughout the molding process helps achieve uniformity and reduces variations in thickness and density.
- Cycle Time Optimization: Carefully calibrated cycle times allow for proper cooling and solidification, minimizing dimensional deviations.
Advanced Equipment and Techniques
Precision injection molding employs cutting-edge machinery equipped with sensors and automated systems that allow real-time monitoring and adjustments. This advanced equipment plays a vital role in maintaining the stringent tolerances required by industries such as electronics and aerospace.
For example, in the electronics industry2, precision injection molding is used to create components with intricate geometries, like smartphone casings. Here, precision ensures that each part fits perfectly, maintaining the device’s sleek design and functional integrity.
Quality Assurance and Testing
Achieving high dimensional accuracy isn’t just about technology—it’s also about rigorous quality control. Precision injection molding integrates comprehensive quality assurance measures, including:
- In-process Monitoring: Continuous monitoring helps detect any anomalies in real-time, allowing for immediate corrections.
- Post-production Testing: Techniques like coordinate measuring machines (CMM) and optical inspection systems verify the dimensions and consistency of finished products.
In industries like medical devices3, where precision is paramount for safety and functionality, these rigorous standards ensure that products like disposable syringes meet exact specifications.
Materials and Mold Design
The choice of materials and the design of the mold itself are fundamental to achieving precision. Engineers select materials based on their shrinkage properties, thermal expansion, and mechanical strength. The mold is meticulously designed to accommodate these factors, ensuring consistent quality across production runs.
In aerospace applications4, where lightweight yet robust components are required, precision injection molding allows for complex designs that meet stringent performance standards.
By combining these elements—advanced technology, stringent controls, rigorous quality checks, and expert material selection—precision injection molding continues to set benchmarks in manufacturing high-dimensional accuracy components.
Precision molding uses temperature control for accuracy.True
Temperature control keeps material flow steady and reduces shrinkage.
Pressure management is not crucial in precision molding.False
Pressure kept steady creates evenness, lowering changes in thickness and density.
What Are the Cost-Effectiveness Benefits of Precision Injection Molding?
Precision injection molding involves more than accuracy – it involves saving money too. But how achieves it such economic benefits?
Precision injection molding offers significant cost-effectiveness by maximizing production efficiency, extending mold lifespan, and minimizing post-processing requirements, making it ideal for high-volume manufacturing.
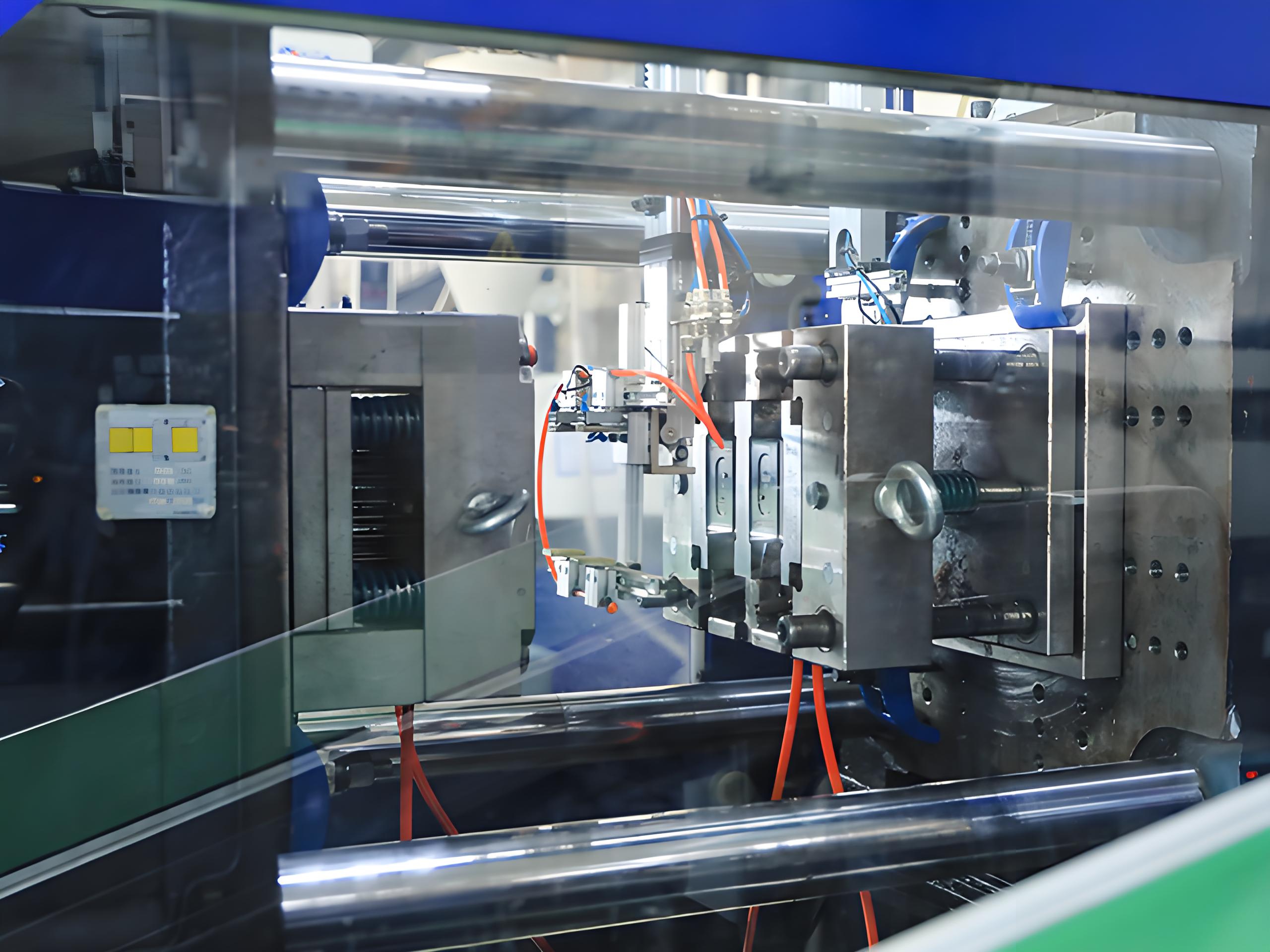
High Production Efficiency
Precision injection molding grants very efficient production. This method allows quick cycles, thus producing many parts fast. Quick production cuts labor expenses and speeds up time-to-market, crucial in tough industries like electronics and automotive.
For example, in the electronics industry5, this method builds parts like phone cases with speed and accuracy, meeting high demand without losing quality.
Extended Mold Life
Precision injection molding uses top-notch materials and good engineering to craft long-lasting molds. These molds create thousands of parts with little damage, cutting down on replacements or fixes.
In the automotive industry6, where items like dashboards need consistent quality through long production runs, mold longevity greatly reduces expenses over time.
Reduced Post-Processing
Another big benefit is less post-processing work after molding. This method yields parts with exact shape and smooth finishes, often skipping extra machining or finishing. Less post-processing saves time, cuts labor costs, and reduces material waste.
In the medical field7, for instance, molding creates throwaway syringes with accurate measurements and smooth surfaces right from the mold, avoiding extra steps that raise costs.
Consistency and Quality Control
This technology provides consistent part quality, key for keeping brand reputation and customer happiness. Fewer defects save money by reducing waste and lowering the chance of recalls or rework.
In fields like aerospace8, where precision and dependability are critical, steady quality from precision injection molding helps keep high safety standards while controlling expenses.
Using these benefits, firms in different areas probably get big cost advantages, making precision injection molding a popular pick for modern manufacturing.
Precision injection molding reduces labor costs.True
High production efficiency reduces the need for workers, lowering expenses.
Precision injection molding requires frequent mold replacements.False
Durable materials increase how long mold serves before needing a replacement.
Which Industries Benefit Most from Precision Injection Molding?
Precision injection molding transforms many industries, bringing new ideas and better processes.
Industries that benefit most from precision injection molding include electronics, medical, automotive, optical, and aerospace. This technology offers high dimensional accuracy, consistency, and cost-effectiveness, making it ideal for manufacturing complex components with strict specifications.
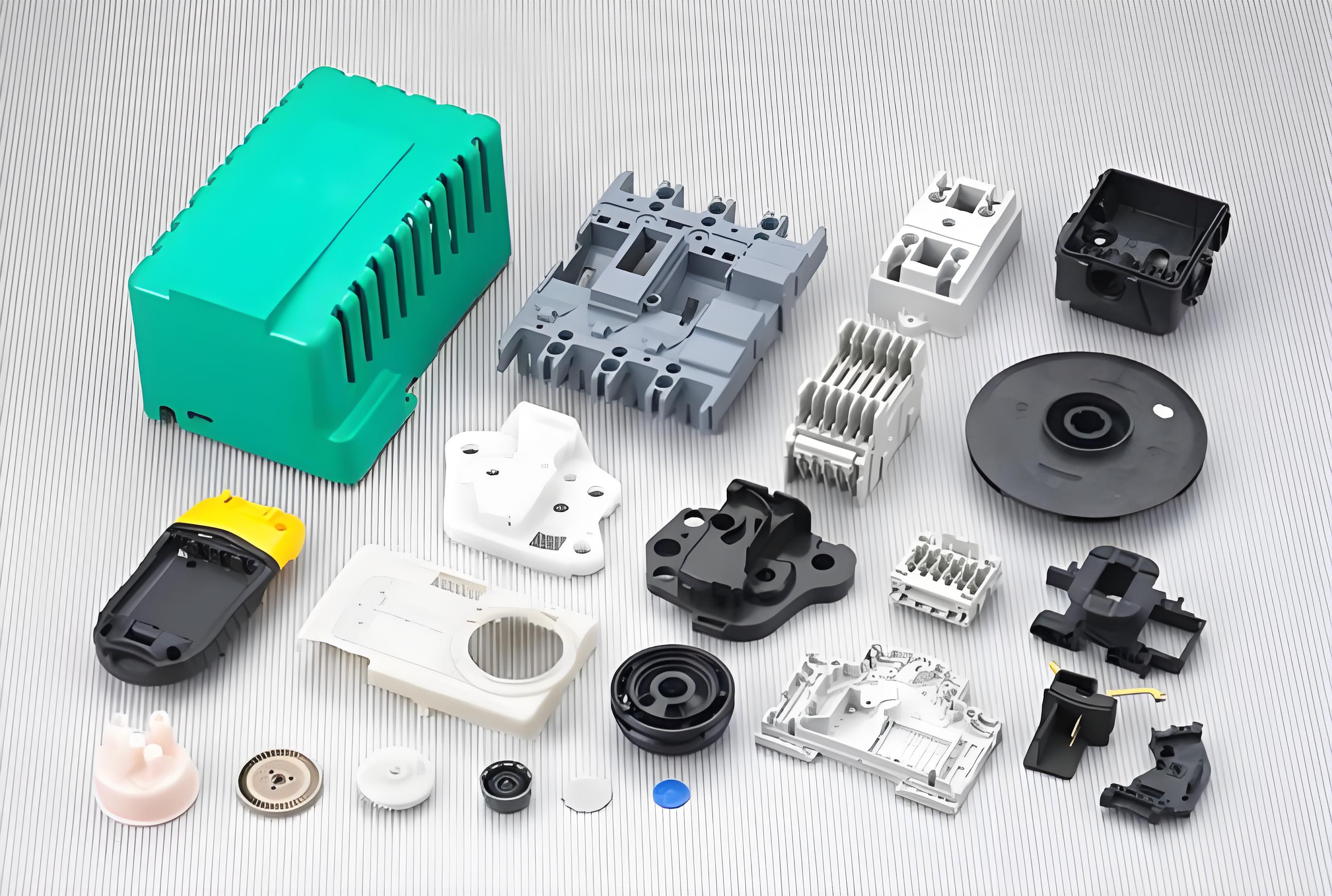
Electronics Industry: Small and Accurate
In electronics, precise injection molding creates parts for smartphones, like covers and tiny circuit pieces. Apple’s iPhone covers come from this method, which gives them very accurate sizes and smooth surfaces. This precision helps electronics firms to satisfy the need for small and dependable parts. It also pushes creative design by allowing detailed shapes without losing strength or look.
Medical Industry: Strict Rules
The medical area uses precise injection molding a lot for items like throwaway syringes and other medical tools. These need high accuracy and clean standards. This method provides every syringe with correct markings, smooth sides, and no leaks. This is very important for safety and trust in medical work, proving how necessary precision molding is in healthcare.
Automotive Industry: Detailed Shapes and Strength
In the car world, precise injection molding is key for making inside parts like dashboards and door sides. These parts need to look nice and be strong, with exact sizes. This method lets detailed designs be strong and stable, giving car makers high-quality parts. The ability to blend many functions in one part without extra parts is a big benefit.
Optical Industry: Accurate Optics
For optics, precise injection molding helps create parts like camera lens cases with very exact standards. This process ensures lenses are the right size and have smooth surfaces for top performance. It also supports light designs, keeping optical gadgets easy to carry without losing quality.
Aerospace Industry: Function in Harsh Settings
The aerospace field gains from precise injection molding by using it to create light but strong parts like sensor cases and supports. These parts face tough conditions, like changes in temperature and shaking. Precision molding makes sure they meet strict rules for working and safety. This method helps aerospace experts design parts for specific jobs while keeping them light.
Precision injection molding is used in smartphone casings.True
Apple applies precise injection molding for iPhone shells, delivering high accuracy.
Precision injection molding is irrelevant to the medical industry.False
Creating exact and clean medical tools such as syringes is vital.
Are There Any Drawbacks to Using Precision Injection Molding?
Precision injection molding provides many benefits. However, it is important to think about possible downsides that could influence its use.
The main drawbacks of precision injection molding include high initial costs, complexity in mold design, and the need for specialized equipment and skilled operators. Despite these challenges, the benefits often outweigh the disadvantages, making it a valuable technology in precision-driven industries.
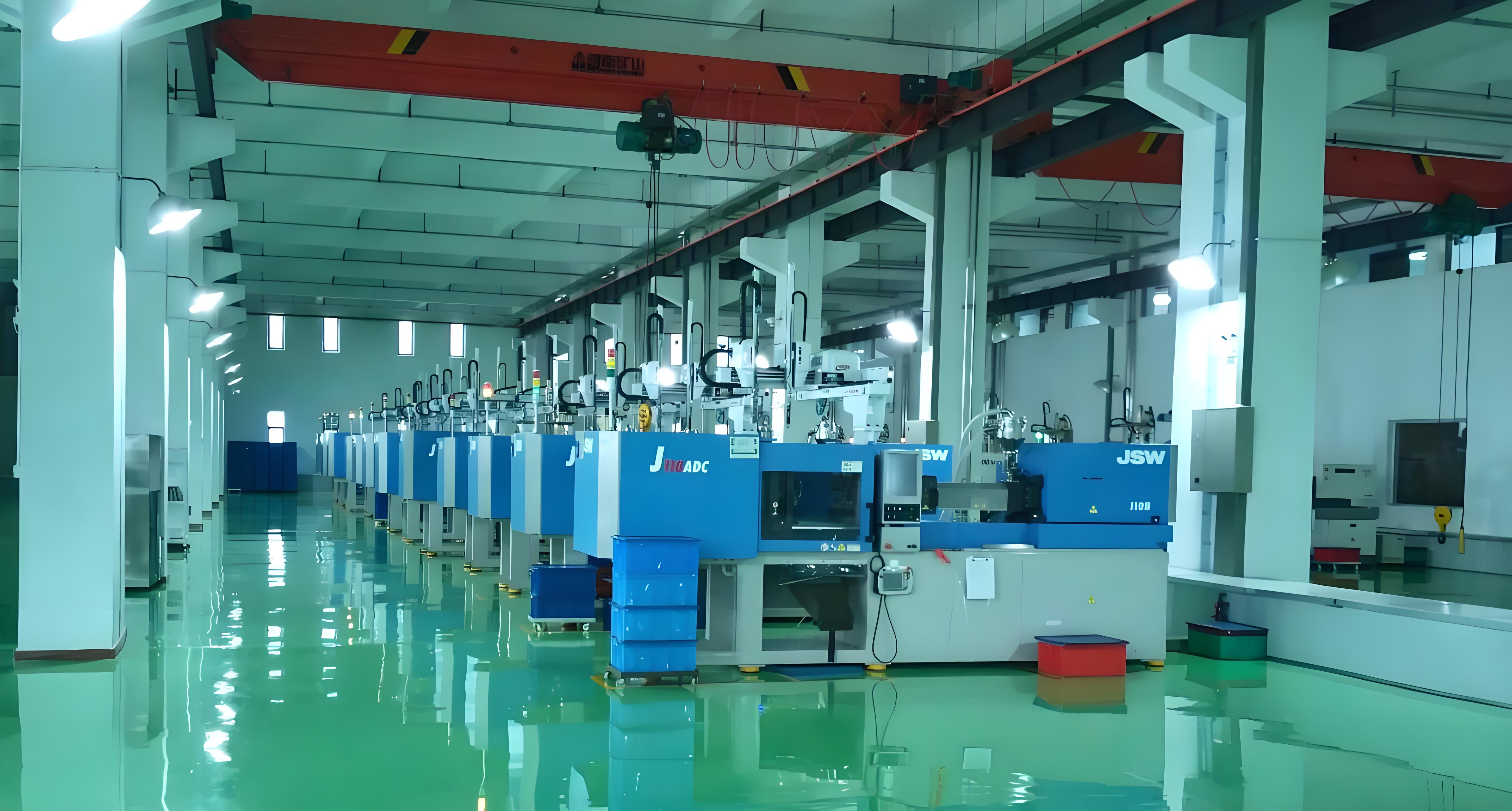
High Initial Costs
One big disadvantage of precision injection molding is the high first payment needed. This covers the cost of designing and creating molds, which must be very accurate to meet strict standards. This first cost might stop small companies or startups from entering markets that use this technology.
The special molds are not only pricey but also take a lot of time to build and test. Once made, though, they can give good production efficiency9 and long mold life, which makes the money spent on them worthwhile after some time.
Complexity in Mold Design
Designing molds for precision injection molding is often more difficult than for regular molding jobs. This difficulty comes from the need to reach high dimensional accuracy and keep consistent quality over many cycles. Engineers must consider things like shrinkage, cooling speeds, and material flow for best performance.
Mold design also needs exact calculations and simulations to foresee possible issues during manufacturing. This careful attention to details might stretch development time and raise expenses.
Specialized Equipment and Skilled Operators
Precision injection molding needs specialized machines that keep tight controls over details like temperature and pressure. These machines are costly and require regular care for top-level performance.
Furthermore, working with these advanced machines requires trained technicians who understand the detailed process. Spending on training and keeping such gifted people can increase operating costs.
Limited Material Selection
Not all materials fit precision injection molding. The method often prefers high-quality polymers that handle the exact needs of precision molding. While these materials deliver great performance, they might cost more than normal plastics.
In some situations, the limited choice of materials might limit design options or need extra processing steps, which might affect how cost-effective the project is overall.
Conclusion: Balancing Benefits and Drawbacks
Though these challenges exist, the benefits of precision injection molding — like high accuracy, stable quality, and full material performance10 — often make it the chosen option for fields with tough requirements. When deciding if this technology fits your needs, think about the first costs compared to the long-term gains it offers for efficiency and product quality.
High initial costs deter small businesses from using precision molding.True
The high initial cost for molds probably creates an obstacle for small businesses.
Precision injection molding allows unlimited material choices.False
Not all materials fit the purpose; it frequently demands high-quality polymers.
Conclusion
Precision injection molding provides excellent accuracy and efficiency in many industries. Use this technology for better product quality and new designs. Think about using it for greater precision and performance.
-
Understand the fundamental processes ensuring high precision in manufacturing.: This article focuses on essential elements such as wall thickness, draft angles, ribs, holes, pillars, snaps, interference fits, and tolerances in plastic … ↩
-
Explore how electronics benefit from precision techniques for detailed components.: Injection molding plays a major part in electronic component manufacturing with the majority of electronic components utilizing plastics for their inert … ↩
-
Discover precision molding’s role in creating safe medical devices.: Our BMP plastic injection molding capabilities include injection molding, injection blow, 2-shot (two-shot molding), and insert molding (overmolding). ↩
-
Learn about the molding techniques for high-performance aerospace parts.: Aerospace parts created through injection molding include turbine housings, turbine blades and pin maps used to mold carbon or glass fibers into sheet … ↩
-
Discover how it meets high-speed demands in electronics.: We’ve been a trusted partner to the electronics industry for over 60 years using injection molding techniques to create complex shapes and geometries. ↩
-
Learn about mold longevity benefits in automotive parts.: Overview. Plastic injection molding revolutionizes automotive interiors, enabling the creation of intricate and durable components with precise designs. ↩
-
Explore how it reduces costs in medical device production.: Natech specializes in syringe molding and takes pride in the design and engineering efforts that go into creating quality products. ↩
-
Understand quality control advantages in aerospace applications.: Benefits of Injection Molding for Aerospace · Large Quantities at Low Cost · Tight Tolerance · Customized Tooling · Wide Range of Materials · Tried & True Method. ↩
-
Understand how efficiency can offset high initial costs.: Empower your technicians · Improve your asset efficiency · Streamline your product design · Reduce your lost time incidents · Higher product quality … ↩
-
Discover why specific materials are preferred for precision molding.: Enhanced mechanical properties — High-performance polymers exhibit remarkable strength and durability, enabling the production of robust and … ↩