Have you ever thought about how PPO injection molding forms the items we use every day?
PPO (Polyphenylene Oxide) injection molding involves using a thermoplastic known for its high-temperature stability, exceptional insulating properties, and mechanical strength. It’s commonly used in industries like electronics and automotive due to these advantageous traits.
PPO has more to offer than first appears. Knowing its particular uses and the detailed steps of injection molding provides new ideas for your designs. Explore the universe of PPO further.
PPO has excellent electrical insulation properties.True
PPO's dielectric constant and loss angle tangent are very low, offering excellent insulation.
What Are the Key Properties of PPO Material?
PPO, also known as polyphenylene ether, happens to be a high-quality thermoplastic polymer utilized in many fields.
PPO material is celebrated for its excellent thermal stability, electrical insulation, high mechanical strength, and low water absorption. Its flame retardancy and chemical resistance make it ideal for demanding applications in electronics, automotive, and aerospace industries.
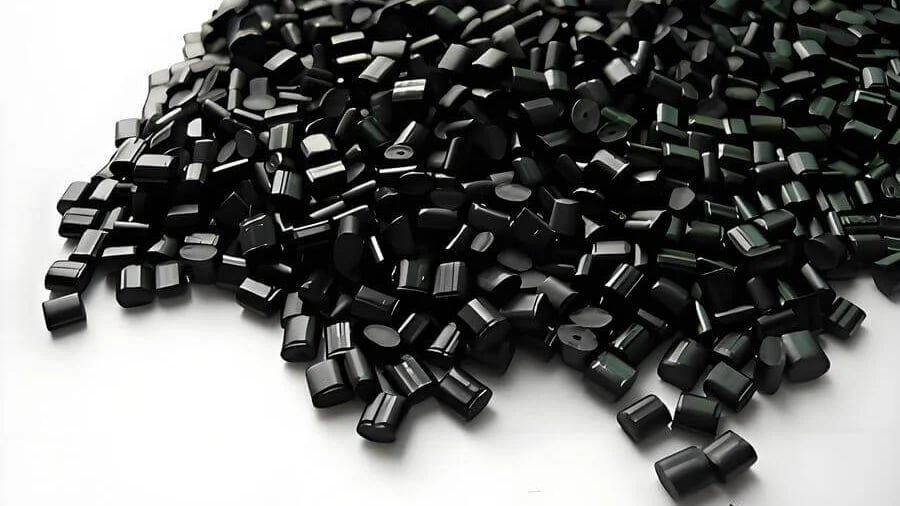
Thermal Stability and Mechanical Strength
PPO is famous for staying stable at high temperatures, with a glass transition temperature close to 211°C and a melting point of 268°C. It keeps its qualities even when hot, which suits jobs needing heat resistance. It handles high temperatures above 190°C, which keeps it steady under heat stress.
Strong mechanical traits are important for PPO. Its tensile strength holds between 60-70 MPa and its bending strength ranges from 90-100 MPa. These traits suit it for parts facing mechanical stress. The material’s stiffness and toughness help it handle outside forces without losing shape much.
Electrical Insulation and Chemical Resistance
PPO‘s low dielectric constant and loss make it a great electrical insulator. It fits electronic duties where steady work in hot and damp places is needed.
Chemical resistance is another strength of PPO. It holds up against different chemicals like acids, alkalis, and oils, so it suits corrosive areas. Plus, it resists breaking down in wet areas, adding to its lasting quality.
Dimensional Stability and Flame Retardancy
PPO takes in little water, causing tiny size changes even when wet. This fact keeps products stable where exactness matters.
Flame resistance is part of PPO‘s nature, allowing it to put out its own fires. It meets many safety rules for flames, suiting it for electronic parts needing strict safety.
Modifiability and Blending Potential
A big advantage of PPO is its ability to mix with other materials such as ABS, HDPE, PPS, PA, and HIPS. This ability lets it change to fit certain needs better. Learn about PPO blending methods1.
Application Examples
Due to its qualities, PPO is common in:
- Electronics: Used in device cases, connectors, and switches for its insulative and fireproof traits.
- Automotive: Strong and heat-resistant, fitting for car parts like dashboards and bumpers.
- Aerospace: Meets high industry needs in aircraft interiors. Find out how PPO serves in aerospace2.
PPO‘s amazing traits turn it into a vital material in fields needing trustworthiness and good function.
PPO has a melting point of 268°C.True
PPO keeps its features in hot conditions, liquefying at 268°C.
PPO is unsuitable for electronic applications.False
PPO provides great electrical insulation, perfect for electronics.
How Does PPO Compare with Other Plastics?
Want to know how PPO compares with other plastics in performance and uses?
PPO (polyphenylene ether) outperforms many traditional plastics with its superior strength, heat resistance, and insulating properties. While polyethylene and polypropylene may deform at high temperatures, PPO remains stable, making it ideal for high-performance applications.
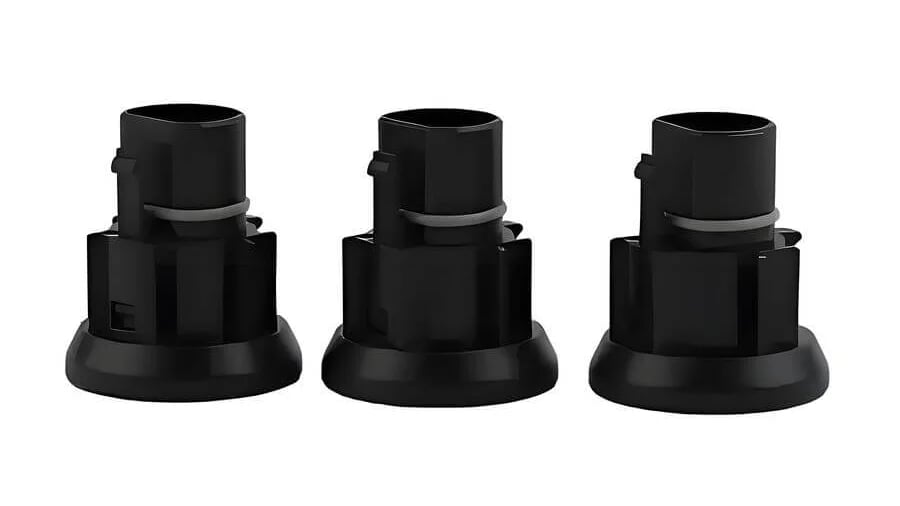
Understanding PPO and Other Plastics
Polyphenylene Ether, or PPO, is famous for being stable in heat, very strong, and good at keeping electricity from passing through. Unlike other common plastics like polyethylene and polypropylene, which change shape when it’s hot, PPO stays strong even when it’s very hot.
Property | PPO | Polyethylene | Polypropylene | ABS |
---|---|---|---|---|
Heat Resistance | High (up to 190°C) | Low | Moderate | Moderate |
Mechanical Strength | High | Low | Low | Moderate |
Electrical Insulation | Excellent | Poor | Moderate | Moderate |
Chemical Resistance | Excellent | Good | Good | Poor |
Comparing Performance in Various Conditions
PPO resists heat very well, so it is used when materials need to stay strong in high temperatures. This quality is better than polyethylene and polypropylene. For example, polyethylene might change at 80°C, but PPO stays the same even at over 190°C.
Besides, PPO is really good at stopping electricity from passing through. It works well in electronic and electrical uses because it ranks among the best for this. ABS, another plastic, is flexible but doesn’t protect from electricity as well as PPO does.
Specific Uses
In cars, where strength and heat stability matter a lot, PPO is often chosen over other plastics. It stays strong under stress and heat, making it good for parts like dashboards and bumpers.
PPO also resists chemicals very well, so it works in places with harsh substances where other plastics might break or wear out.
Mixing and Adjustments
PPO can mix with materials like ABS, HDPE (High-Density Polyethylene), and HIPS (High Impact Polystyrene). This ability lets makers change PPO’s qualities to fit different needs, increasing its usefulness in many areas.
Thinking about these traits, PPO stands out from other plastics. Its toughness in tough conditions makes it a key material for hard jobs.
PPO maintains integrity above 190°C.True
PPO withstands high temperatures, staying steady over 190°C.
Polyethylene outperforms PPO in electrical insulation.False
PPO provides great electrical insulation but not like polyethylene.
What Are the Common Applications of PPO Injection Molding?
Find the different industries gaining from PPO injection molding’s special traits.
PPO injection molding is predominantly used in electronics, automotive, and aerospace industries. Its superior insulating properties and flame retardancy make it ideal for electrical components, while its strength and heat resistance suit automotive and aerospace applications.

Electronics and Electrical Appliances
In the realm of electronics3 and electrical appliances, PPO‘s exceptional insulating properties combined with good flame retardancy make it a preferred choice. It is extensively utilized in manufacturing the shells of electrical appliances, connectors, switches, and other critical components. The material’s low dielectric constant and dielectric loss angle tangent ensure it performs reliably even in high-temperature and humid environments.
Application | Benefits |
---|---|
Appliance Shells | Outstanding insulating properties prevent short circuits and failures. |
Connectors | Flame retardancy ensures safety against electrical fires. |
Switches | Dimensional stability supports long-lasting performance. |
Automotive Industry
PPO injection molding finds significant application in the automotive industry due to its robust mechanical properties and high-temperature stability. Automotive parts such as instrument panels, bumpers, and interior components often employ PPO for its ability to withstand various environmental conditions without deforming. The material’s strong creep resistance ensures longevity and reliability under stress.
- Instrument Panels: Withstand high temperatures without losing form.
- Bumpers: Provide impact resistance and durability.
- Interior Parts: Maintain strength and aesthetic appeal over time.
Aerospace Industry
The aerospace sector leverages PPO‘s high-performance characteristics for applications where material integrity is non-negotiable. In aircraft interiors, PPO‘s excellent thermal stability and chemical resistance are invaluable. These properties ensure components endure the demanding conditions of aviation environments.
Comparison with Other Materials
When compared to traditional plastics like polyethylene or polypropylene, PPO stands out with higher strength and heat resistance. It also surpasses engineering plastics such as ABS in chemical resistance and electrical properties, making it a more versatile choice for advanced applications.
Understanding these applications can guide material selection in projects demanding high-performance thermoplastics. Consider how PPO might elevate your product’s quality and durability through these insights into its diverse uses.
PPO is used in aerospace for thermal stability.True
PPO's heat stability is suitable for aerospace parts.
PPO injection molding is not used in automotive parts.False
PPO serves a role in cars due to its durability and ability to handle heat.
What Best Practices Should Be Followed in PPO Injection Molding?
Understanding how to use PPO injection molding helps create strong and long-lasting parts.
For successful PPO injection molding, ensure proper material preparation, optimal storage conditions, and precise control of injection parameters. Drying the material to a specific moisture level and selecting appropriate mold steels are critical steps.
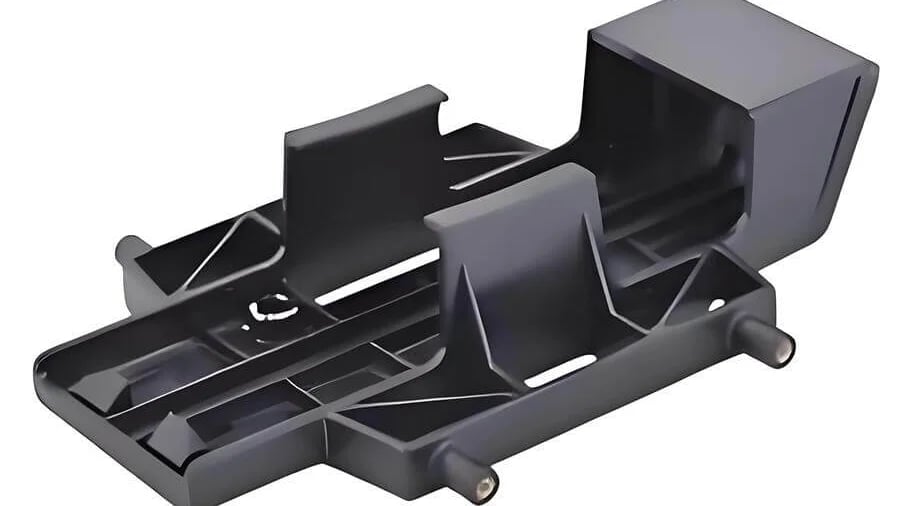
Material Preparation and Storage
Successful PPO injection molding4 begins with selecting the appropriate PPO material based on the desired specifications of the product. It’s crucial to inspect the materials prior to use, ensuring they are free from impurities and moisture. Storing PPO materials in a dry, ventilated environment at temperatures below 25°C with relative humidity under 50% prevents degradation and maintains quality.
Drying the Material
Before commencing with injection molding, it is essential to dry PPO materials to achieve a water content of less than 0.05%. This involves heating at temperatures between 120-130°C for 2-4 hours, depending on the material’s initial moisture levels and the efficiency of the drying equipment. This step ensures that the molded parts maintain their structural integrity and avoid defects like voids or cracks.
Selecting Mold Steels
Given the high temperature and pressure during the injection molding of PPO, selecting mold steels such as P20 or 718H is recommended. These materials offer high hardness and abrasion resistance, ensuring the longevity of the mold and consistency of production quality.
Injection Molding Parameters
The injection pressure for PPO should generally be maintained between 80-120 MPa, tailored to the size, shape, and wall thickness of the product. A moderate injection speed, typically between 30-60 mm/s, helps in minimizing defects such as weld marks. Additionally, controlling the screw speed within 30-60 r/min is necessary to prevent material overheating and degradation.
Advantages of PPO in Injection Molding
Leveraging outstanding properties of PPO—such as its high mechanical strength, excellent thermal stability, and good flame retardancy—can significantly enhance product performance in sectors like electronics and automotive. By following these best practices, manufacturers can capitalize on PPO‘s unique advantages to produce superior products consistently.
Mastering these best practices not only ensures efficiency but also maximizes inherent benefits that PPO brings to various applications. Understanding these nuances allows engineers and manufacturers to make informed decisions that improve product quality and performance.
PPO materials should be stored below 25°C.True
Keeping PPO under 25°C stops breakdown and keeps it in good condition.
Injection speed for PPO should exceed 100 mm/s.False
A moderate injection rate of 30-60 mm/s reduces flaws.
Conclusion
Using PPO‘s characteristics probably changes your projects. Study more to completely use this material’s power.
-
Discover how PPO blending enhances material properties for diverse applications.: The incorporation of poly(styrene-co-glycidyl methacrylate) (SG) improved interfacial compatibility between PPO/PPS phase, and the stretchability of the blend … ↩
-
Learn about PPO’s role in meeting aerospace industry standards.: Plastic materials are used for a wide variety of aerospace applications including aesthetically pleasing interior components, transparent windows and … ↩
-
Explore how PPO improves electronics safety and reliability.: Excellent electrical insulating properties and great stability · Mid-range temperature resistance · Transparent · Economical thermal performance · Good dielectric … ↩
-
Explore detailed techniques for optimizing PPO injection molding processes.: For PPO, a minimum draft angle of 1 to 2 degrees for vertical surfaces is recommended, depending on the depth and complexity of the part. ↩