I recall the first moment I learned about Polyphthalamide (PPA) – it felt like finding a hidden treasure in the realm of materials.
PPA injection molding involves processing a semi-aromatic polyamide with excellent thermal and mechanical properties, suitable for high-temperature applications in automotive and electronics. Key considerations include maintaining moisture levels under 0.15% and using high mold temperatures for optimal results.
Knowing the simple processing needs is key. Exploring the special traits and uses of PPA helps your product plans and factory work. Understand why PPA is a top pick among engineering plastics.
PPA has a heat distortion temperature of 250-300°C.True
PPA's very high heat distortion temperature renders it suitable for applications involving high temperatures.
How Does PPA Compare to Other Engineering Plastics?
Polyphthalamide (PPA) gains attention for its outstanding ability to resist heat and strong mechanical qualities, probably standing as a tough rival to other engineering plastics.
PPA stands out among engineering plastics for its high heat resistance, excellent chemical resilience, and cost-effectiveness, offering superior performance in demanding environments like automotive and electronics.
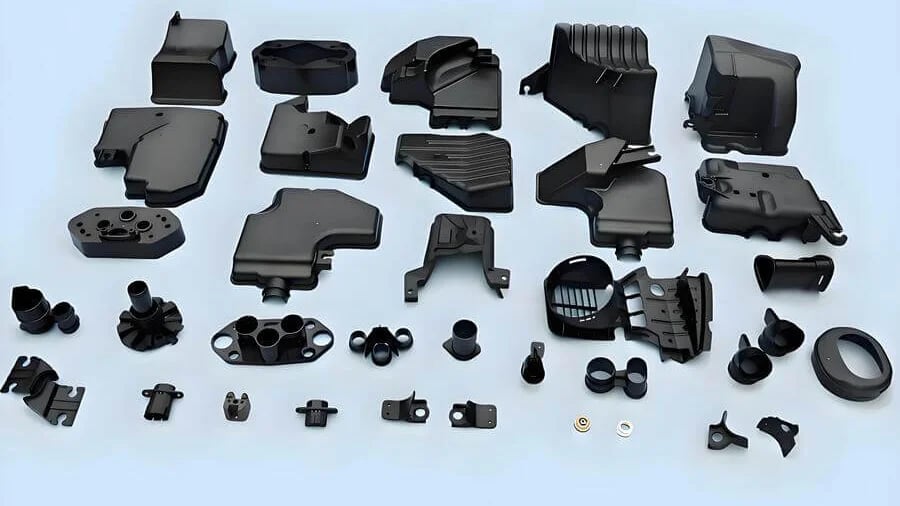
Comparing Thermal Properties
PPA excels in high-temperature applications, boasting a heat distortion temperature generally between 250-300°C. This makes it suitable for environments where traditional thermoplastics would fail. For instance, PPA is increasingly used in automotive headlight reflectors1 and engine components due to its ability to withstand elevated temperatures without losing structural integrity. In contrast, many traditional engineering plastics have lower thermal thresholds, limiting their application in such high-heat scenarios.
Mechanical Strength and Rigidity
When considering mechanical properties, PPA offers high tensile and bending strength, generally between 100-150 MPa and 150-200 MPa, respectively. This makes it an ideal choice for applications requiring durability and load-bearing capability, such as bearing housings2 and pulleys in automotive applications. Compared to specialty engineering plastics, PPA provides these mechanical advantages at a lower cost, making it both a practical and economical choice.
Chemical Resistance
The chemical resilience of PPA allows it to resist a wide range of chemicals, positioning it as a preferable option over other engineering plastics in environments exposed to harsh chemicals. This characteristic is crucial in applications such as fuel line components3, where exposure to various fuels can degrade less resistant materials.
Cost and Processability
PPA is not only competitive in performance but also in cost. Its relatively low price compared to specialty engineering plastics makes it an attractive option for industries aiming to optimize cost without sacrificing quality. Moreover, PPA‘s ease of injection molding enhances its appeal, allowing for efficient manufacturing processes. Its acceptable moisture level for processing is under 0.15%, which is manageable with standard desiccant dryers, ensuring consistent quality in production.
Property | PPA | Traditional Plastics | Specialty Plastics |
---|---|---|---|
Heat Resistance | 250-300°C | Lower than 250°C | Varies, often higher |
Mechanical Strength | High (100-150 MPa tensile) | Varies, often lower | Comparable or higher |
Chemical Resistance | Excellent | Moderate to good | Often excellent |
Cost | Moderate | Lower | Higher |
Processability | Excellent | Generally good | Often more complex |
Electrical Properties
In terms of electrical characteristics, PPA provides good insulation properties with high volume resistivity and a low dielectric constant, making it suitable for electronic components like sockets and connectors4. These properties ensure that PPA components maintain performance under electrical stress, a significant advantage over many traditional plastics used in electronics.
PPA has higher heat resistance than traditional plastics.True
PPA's heat distortion temperature falls between 250-300°C, which is higher than many usual plastics.
PPA is more costly than specialty engineering plastics.False
PPA often costs less than specialty engineering plastics.
What Are the Key Processing Parameters for PPA Injection Molding?
Polyphthalamide (PPA) injection shaping requires accuracy to utilize its complete capabilities in advanced uses.
Key processing parameters for PPA injection molding include moisture control below 0.15%, melt temperatures between 324~343°C, and mold temperatures of at least 135°C for optimal crystallization and mechanical properties.
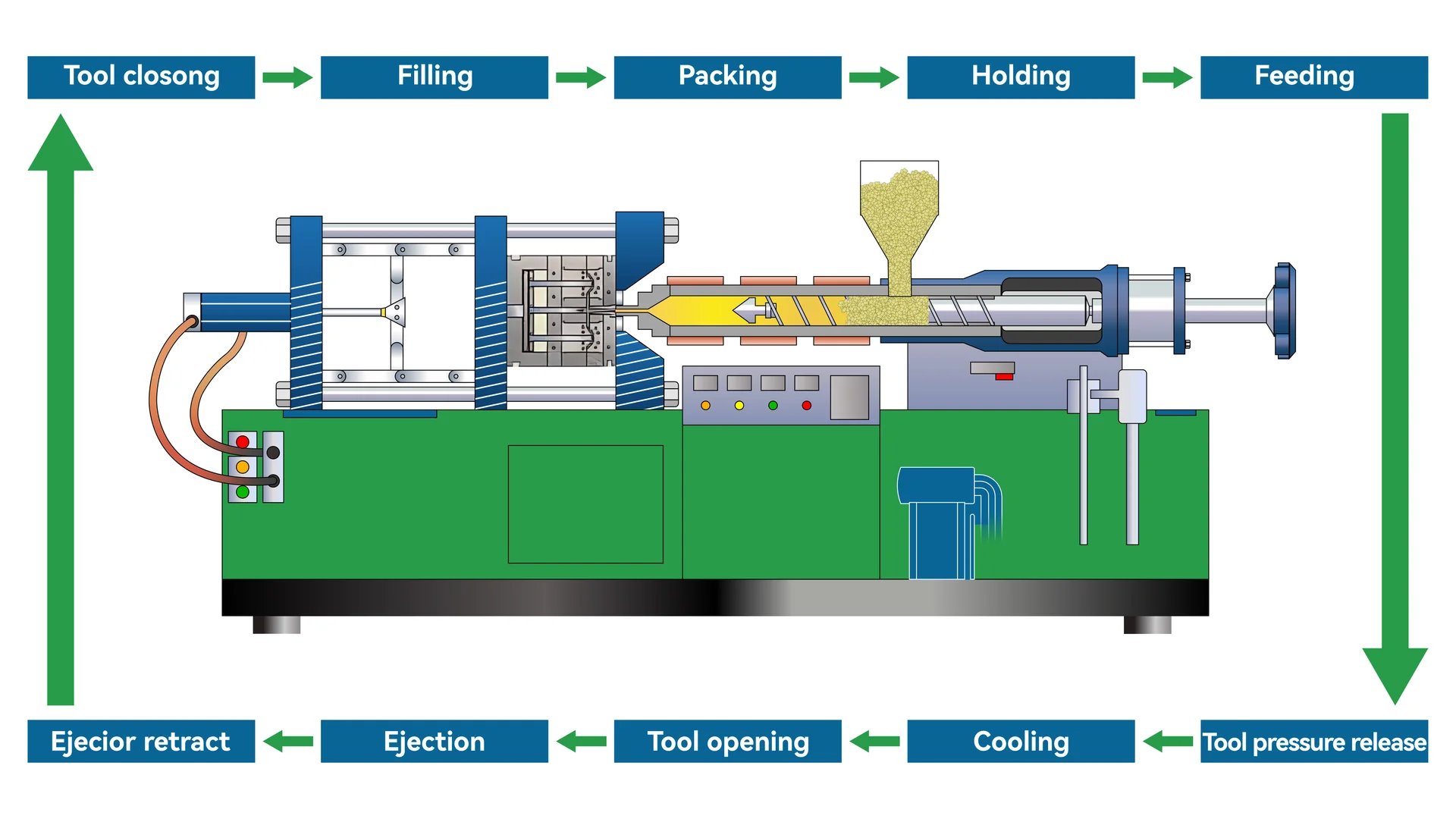
Understanding Moisture Control in PPA Injection Molding
Polyphthalamide (PPA) resins, a type of special plastic, need careful moisture control. Before processing, humidity should stay below 0.15% because too much moisture can harm the plastic strength. Drying with special dryers, PPA resins should reach a dew point of -25°C or less at 175°C. Usually, drying takes 4 to 16 hours depending on how much moisture is present at the start.
Optimizing Melt and Mold Temperatures
The melt temperature for PPA should be kept between 324~343°C to get the right flow and strength. The resin should stay in the barrel less than 10 minutes to stop any damage. Mold temperatures help in getting the best crystallization. The mold should be at least 135°C for good shape and surface of the product.
Injection Molding Parameters: Pressure and Speed
Injection pressure usually falls between 80-150 MPa and speed changes from 30-80 mm/s. These settings should change based on the product shape, size, and thickness. Screw speed should help keep the material flowing well, usually between 30-60 rpm.
Challenges in Wall Thickness Design
Creating the wall thickness of PPA products is important to stop problems like uneven shrinkage or weak spots. Thicker walls mean longer cooling and may cause uneven shrinkage, while thinner walls might weaken the product. A balanced design is very necessary for good performance.
Material and Equipment Preparation
Choosing the right PPA materials for specific product needs is key. Keeping materials safe and dry under 25°C avoids moisture issues during processing. Using high-quality mold metals like H13 or S136 steels helps resist wear and heat, crucial for PPA injection molding success.
These factors highlight the importance of accuracy in PPA injection molding to fully use its benefits in fields from cars to electronics. For more knowledge on best PPA processing methods5 and mold planning ideas6, more reading is suggested.
PPA resins need drying below 0.15% moisture.True
Too much water reduces polymer's molecule size, influencing traits.
Melt temperature for PPA should be 300°C.False
Correct melt heat is 324~343°C for good flow and qualities.
Why Is PPA Ideal for Automotive Applications?
Polyphthalamide (PPA) transforms the automotive sector, providing exceptional performance in challenging settings.
PPA is ideal for automotive applications due to its superior thermal and mechanical properties, chemical resistance, and cost-effectiveness. These attributes make it suitable for components like engine parts, electrical systems, and more, ensuring reliability and efficiency.
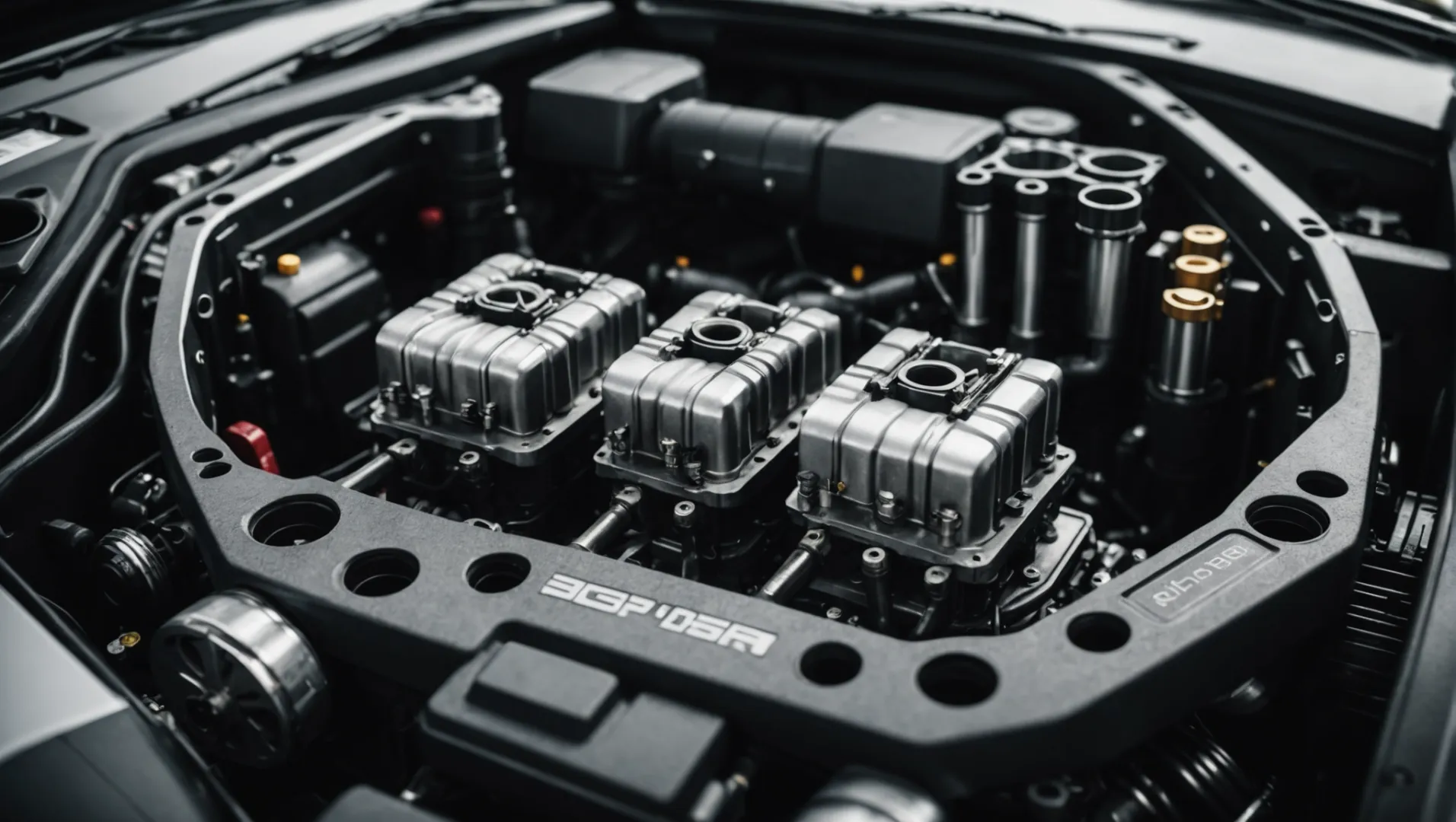
Using The Heat Edge of PPA
Cars need materials that handle high temperatures well because modern engines get really hot. PPA has a heat distortion temperature7 of about 250-300°C and stays okay up to 150-200°C in regular use. This makes it ideal for parts that face a lot of heat, like engine parts and headlight mirrors.
Strong and Lasting
PPA shows high ability to stretch (100-150 MPa) and bend (150-200 MPa) under pressure without losing shape. This toughness is very important for car parts like bearing frames and pulleys where strength is critical.
Protects Against Chemicals
Car parts often contact different chemicals and liquids. PPA does not break easily when exposed to oils, coolants, and fuels. This quality makes it the top choice for parts like fuel lines and sensor covers.
Affordable and Easy to Shape
PPA costs less compared to special engineered plastics but still works well. It is simpler to use in injection shaping processes8. Most PPA types are shaped using standard injection equipment, needing good moisture control and right mold temperatures for good results.
Useful in Different Areas
PPA‘s uses go beyond mechanical pieces. Its electrical qualities are fit for electronic parts in vehicles. It resists electricity strongly and loses little energy, useful for connectors and other car electronics.
Characteristic | PPA Features |
---|---|
Heat Distortion Temp | 250-300°C |
Tensile Strength | 100-150 MPa |
Chemical Strength | High |
Electrical Safety | Excellent |
Changing toward better airflow designs and powerful motors in the car world needs materials like PPA that meet new demands well.
PPA can withstand temperatures up to 300°C.True
PPA's heat distortion temperature lies between 250-300°C.
PPA is unsuitable for electronic components in vehicles.False
PPA has outstanding electrical qualities, which render it perfect for electronics.
What Challenges Might You Face with PPA Injection Molding?
Understanding the complexities of PPA injection molding may present many difficulties for producers.
Challenges in PPA injection molding include controlling moisture levels, managing high mold temperatures, and addressing product design considerations such as wall thickness and reinforcement. Proper handling and understanding of these aspects ensure optimal quality and performance of molded parts.
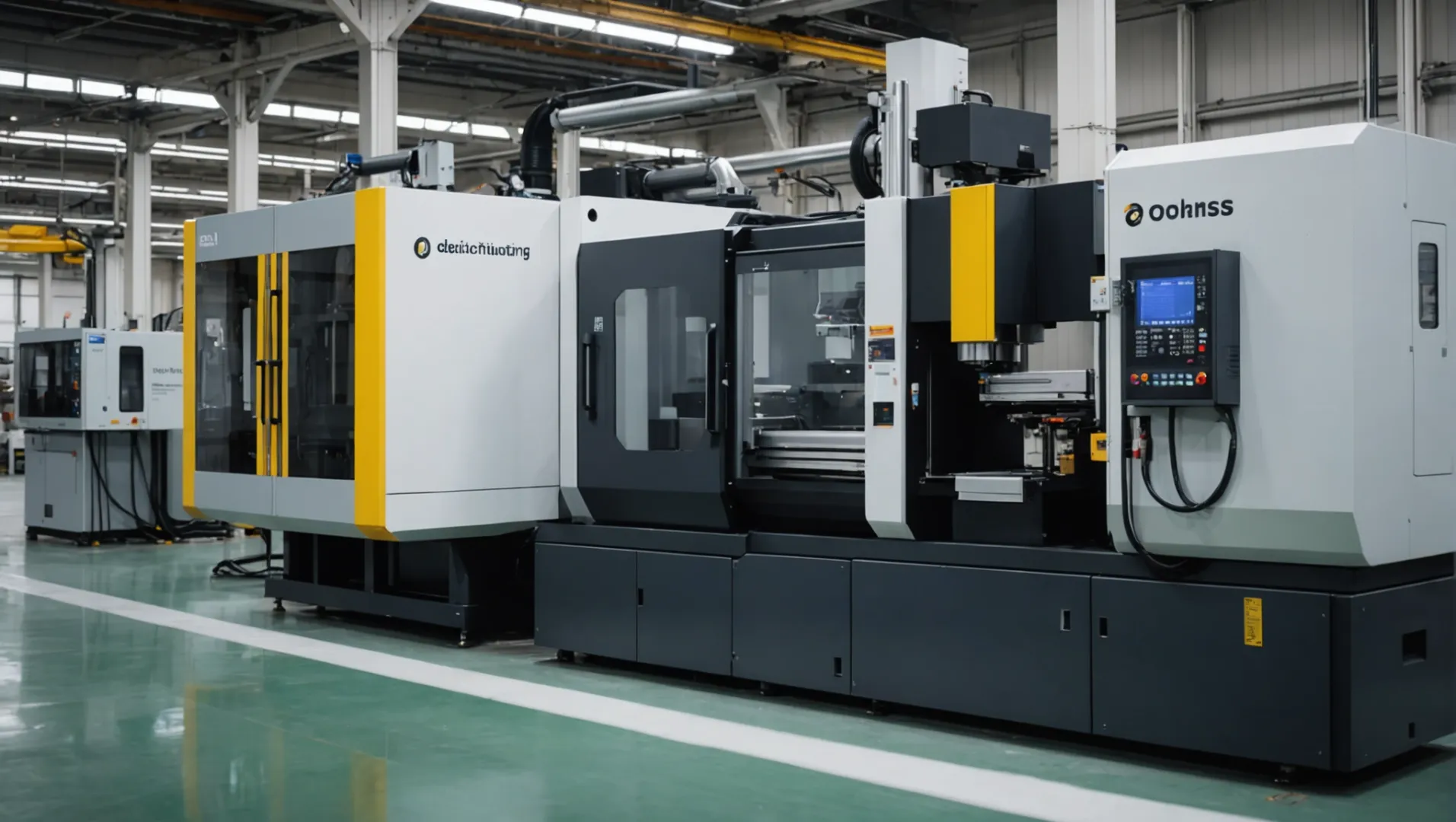
Understanding Material Preparation
Material readiness is important in PPA injection techniques. Keeping an eye on moisture is key since PPA pieces should have moisture below 0.15% to keep their strength. Using special dryers9 really helps cut down moisture, but drying could take 4 to 16 hours based on how much water is inside. Controlling how wet the material gets stops issues like lower strength and lighter weight.
Managing Injection Molding Settings
Getting the best settings needs careful control of injection steps:
Setting | Range |
---|---|
Pressure | 80-150 MPa |
Speed | 30-80 mm/s |
Screw Speed | 30-60 rpm |
Mold Heat | 80-120°C |
Melt Heat | 300-350°C |
Mold heat is very critical, as it affects how the product forms and stays stable. Wrong settings might lead to problems like bending or bad surfaces.
Thinking About Product Design
While shaping items with PPA, thickness affects how they work. Thick parts might cool slowly and change size unevenly, while very thin ones could lose strength or stiffness. Designers maybe should add smart support structures10 to enhance strength and lower shape changes.
The demold slope also needs careful thought. Slope helps in taking out parts smoothly without harm. Picking good mold metals like H13 or S136 steel gives long use and exactness, helping to achieve good results.
Handling High Heat Needs
PPA often needs molds heated above 275°C for full forming, which brings difficulties. High heat demands molds that handle big heat pressure and keep working well over time. Choosing mold materials and cooling methods maybe helps avoid problems like heat damage or slow cycle times.
Conclusion: Overcoming Challenges with Knowledge
Getting past these hurdles requires deep knowledge of PPA’s traits and needs. By keeping moisture under control, setting parameters right, and smart design, companies possibly use PPA for high-level tasks in many fields.
PPA resins need moisture below 0.15% for optimal properties.True
Controlling moisture is very important to keep PPA's mechanical features stable.
Mold temperature in PPA molding should exceed 275°C.False
Mold temperatures vary from 80 to 120°C and do not go beyond 275°C.
Conclusion
Knowing PPA injection molding improves design and operations in different industries. This information helps select materials for top-performance uses.
-
Learn how PPA enhances performance in automotive lighting applications.: Advantages in comparison with typical parabolic headlamps: smaller dimensions, almost twice the light output, clear cutoff, and hardly any scatter loss. Hella … ↩
-
Explore the strength benefits of using PPA in bearing housings.: What Are the Advantages of Polyphthalamide (PPA) in Plastic Injection Molding? · Very high stiffness and strength · Good heat, chemical, and … ↩
-
Understand PPA’s chemical resistance benefits in fuel systems.: The reasons for this choice are the excellent chemical resistance of the PPA matrix to oils, solvents, greases and hydrocarbons, as well as the electrical and … ↩
-
Discover why PPA is ideal for electronic connectors.: 3. Nylon (PA) for electronic connectors: milky white, good toughness, abrasion resistance, odorless, can be drilled, cut, planed, injection-molded, good creep … ↩
-
Explore detailed techniques for optimizing PPA processing.: Place and route (P&R) tools and methodologies typically need to be adapted for each new technology node to achieve the best PPA for a target … ↩
-
Learn about essential mold design strategies for PPA.: Explore the properties of PPA plastic for product design. Learn about its applications, modifications, and design considerations. ↩
-
Discover how PPA’s heat resistance enhances automotive component durability.: The heat deflection temperature (HDT) is a measure of the polymer’s resistance to distortion under a given load at an elevated temperature. ↩
-
Understand the key parameters for successful PPA injection molding.: It is hygroscopic, opaque, semicrystalline, and can be used in plastic injection molding. Most PPA grades are filled with glass or minerals to … ↩
-
Learn effective drying techniques for moisture control in PPA.: Use a desiccated hopper dryer to ensure that the resin remains dry during processing. • Select a barrel capacity for a residence time no greater than 6 … ↩
-
Explore reinforcement strategies to enhance product strength.: Setting reinforcement on plastic parts can improve the strength and stiffness of plastic parts and prevent warping and deformation of plastic … ↩