Have you ever wondered why some plastic items break easily? The reason is usually in the design of the mold exhaust.
Poor mold exhaust design in injection molding leads to defects like air bubbles and flow lines, compromising the appearance and strength of plastic products. Proper venting is essential for high-quality output.
I remember the first time I faced issues with mold exhaust design. It was really surprising. Everything seemed fine at first. Then, we noticed air pockets and flow marks. These flaws ruined the finish. The problems went deeper than expected. They affected the product’s strength and increased production time. Fixing these challenges became very important. Poor mold exhaust caused trouble for both quality and efficiency. We adjusted the design to allow better venting. This change improved the look, strength and production of our products.
Poor mold exhaust leads to air pockets in plastics.True
Air pockets form due to trapped gases, affecting product quality.
Effective venting is unnecessary for high-quality plastic products.False
Venting prevents defects like flow marks and uneven density.
What are the common surface defects caused by poor venting?
Have you ever felt that your carefully planned product had unexpected problems? Poor venting might be the reason. Knowing about these surface flaws could really help you. It could save your day.
Inadequate venting in molds causes annoying surface defects. Air pockets, flow marks and fusion marks appear. Trapped air interrupts the plastic flow. This really harms both the appearance and strength of the final product. It ruins it.
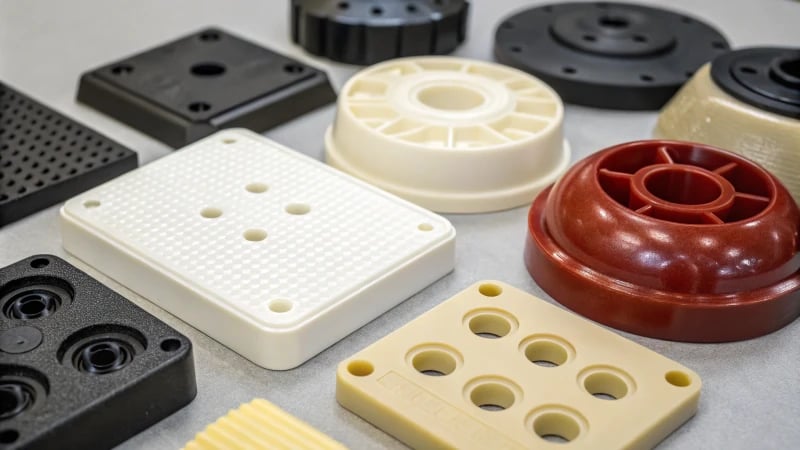
Appearance Quality Issues
Air Pockets and Bubbles
I remember a time working on a project meant to be perfect – literally. We produced optical lenses when unsightly pits and pockmarks appeared. Insufficient venting had allowed air pockets to form. Trapped air ruined the surface, especially with clear products like lenses, reducing quality1 and clarity. A well-planned vent system is essential here.
Flow Marks and Fusion Marks Aggravation
Consider designing a sleek product only to have it come out of the mold imperfect. Air can block the plastic melt flow, creating uneven patterns known as flow marks. When the melt splits and meets again, poor venting worsens fusion marks, which lowers the overall appearance quality of your product.
Defect Type | Cause | Impact |
---|---|---|
Air Pockets | Trapped Air | Pits/Pockmarks |
Flow Marks | Uneven Flow | Pattern Distortion |
Internal Quality Issues
Uneven Density
In an early project, our plastic containers lacked durability due to uneven density from trapped air, leading to voids within the product. This inconsistency weakened them, making them vulnerable to rupture—weak spots are very dangerous.
Increase in Residual Stress
Warping or unexpected cracks in products signal residual stress. Reaction forces from trapped air create pressures during cooling, converting into residual stresses that lead to deformation or cracking under pressure.
Reduced Molding Efficiency
Filling Difficulties
Imagine trying to fill a mold but the air won’t move; everything becomes more complicated. More pressure and time are necessary due to increased resistance during filling, requiring higher pressures and longer times. Incomplete fills or short shots seriously harm productivity2.
Demolding Difficulties
And demolding? Excess internal gas increases friction during demolding—it’s a nightmare to release the product without damage.
These defects show the importance of effective venting systems in molds for maintaining product integrity and aesthetic appeal. Tackling these problems3 from different angles can probably lead to improvements in mold design and efficiency.
Air pockets cause pits on transparent surfaces.True
Insufficient venting leads to air pockets, causing pockmarks on surfaces.
Poor venting decreases molding efficiency.True
Trapped air increases resistance, complicating filling and demolding processes.
Why Does Inefficient Mold Exhaust Lead to Quality Issues?
Every person has experienced a time when a tiny mistake grows into a big problem. Poor mold exhaust is one hidden foe in manufacturing that might bring sudden troubles.
Poor mold exhaust causes air pockets. These pockets create uneven density. Products develop increased stress, which reduces their appearance. Structural integrity suffers as a result. Quality issues become more common.
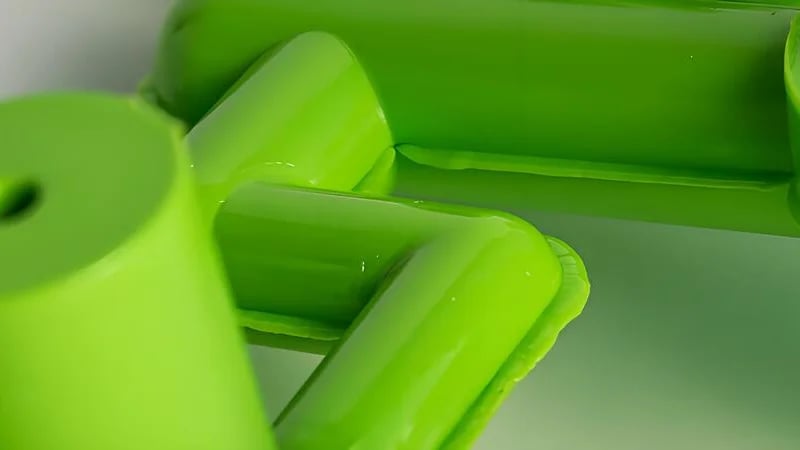
Impact on Appearance Quality
Poor mold venting leads to trapped air. This creates air pockets and bubbles, which leave ugly pits or marks. Transparent things like optical lenses suffer the most. Bubbles greatly reduce their transparency. When I was new, I worked on transparent plastic shells. Watching bubbles ruin hours of work was really frustrating. Additionally, flow marks and fusion marks become worse, damaging the product’s appearance quality.
Internal Quality Compromises
Bad exhaust results in uneven density, causing weak spots in products. I once designed plastic containers that burst under pressure due to uneven density. It reminds me that density is as important as appearance. Moreover, trapped air increases residual stress. This stress can warp or crack products over time, making them fragile and unreliable.
Reduction in Molding Efficiency
Inefficient exhaust reduces molding efficiency too. Filling resistance increases, needing higher pressures and longer cycles, often leading to short shots. I remember a production line stopping because of this problem—nobody wants that repeated. It extends cycle times and causes incomplete fills, wasting valuable materials and time. Trapped gas also complicates demolding, risking damage to both the product and the mold.
Issue Type | Cause | Effect |
---|---|---|
Appearance Problems | Air Pockets | Pits/Pockmarks |
Internal Quality Issues | Uneven Density | Weakness/Rupture |
Molding Efficiency | Filling Resistance | Short Shots/Longer Cycles |
These issues show why good mold exhaust systems are important for maintaining high-quality standards in production.
Every new design challenge reminds me of these past lessons. For those keen to explore solutions further, you may find these advanced techniques4 helpful.
Trapped air causes pits on product surfaces.True
Poor mold venting traps air, leading to surface pits or pockmarks.
Inefficient exhaust reduces molding cycle time.False
It actually increases cycle time due to higher pressure and longer fills.
How does poor exhaust design impact molding efficiency?
Have you ever thought about how something like exhaust design could completely change molding? I thought about it too, until I saw how important it really is.
Bad exhaust design really hurts molding efficiency. Problems like air pockets, uneven density and longer cycle times occur. These issues ruin productivity. They also damage product quality. Therefore, optimizing exhaust systems is important for good molding processes.
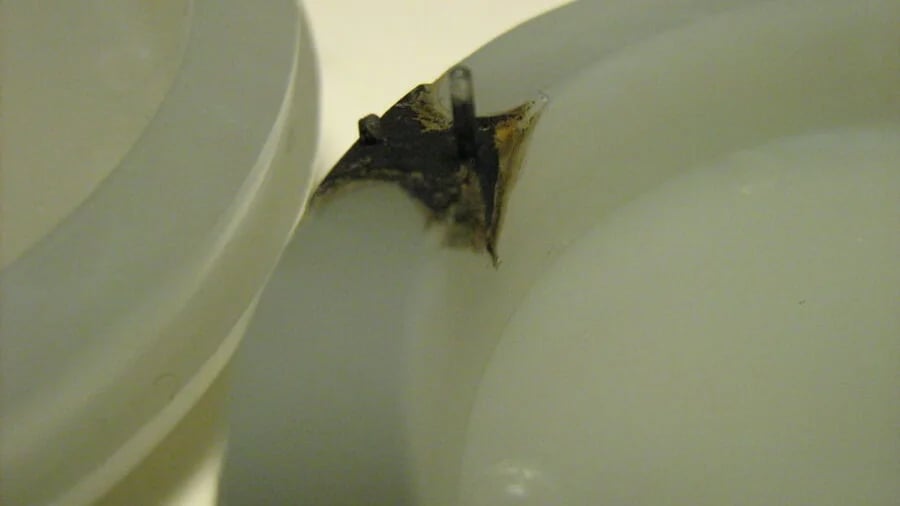
Appearance Quality Problems
I remember seeing optical lenses with ugly bubbles and pockmarks for the first time. It felt very frustrating knowing these flaws were completely avoidable. The problem was poor exhaust design, which kept air trapped inside the mold. It’s similar to pouring soda perfectly, but it overflows because of trapped air. These air pockets really harm clarity and gloss. Appearance is everything for products like optical lenses5 or clear plastic shells.
Flow marks and fusion marks create more issues. These are like spreading butter on cold toast. The air hinders the melt flow, moving unevenly and leaving noticeable marks. It is especially problematic when a smooth, seamless finish is important.
Internal Quality Problems
Internal problems are just as serious. I have seen containers intended to handle pressure burst at the seams due to uneven density. It’s like building a house on uneven ground; eventually, something breaks. Trapped air forms voids that weaken the structure, making it likely to fail under stress.
Residual stress is another hidden threat. Imagine wearing shoes that are a little too tight – uncomfortable and damaging over time. This stress builds from uneven pressure during cooling, causing warping or cracking unexpectedly.
Decrease in Molding Efficiency
Inefficiencies in molding are obvious. Cycle times sometimes stretched forever because we increased injection pressures to push out trapped air. It’s like trying to squeeze the last bit of toothpaste from a nearly empty tube—frustratingly inefficient. Worse, we occasionally had incomplete fills, which led directly to product scrap6.
Demolding, a process that should be simple, turns into a struggle due to expanding residual gas inside the product. Think of trying to peel off a sticker that refuses to come off without tearing. This delays production and risks damaging both the mold and the product.
Summary Table: Effects of Poor Exhaust Design on Molding
Issue | Description |
---|---|
Air Pockets | Surface imperfections like pits and pockmarks |
Uneven Density | Weaknesses in strength and hardness |
Flow Marks | Uneven melt flow causes visual flaws |
Residual Stress | Increased risk of warping and cracking |
Difficulty in Filling | Leads to higher cycle times and scrap |
Demolding Challenges | Causes damage and reduces efficiency |
Optimizing exhaust design may seem boring, but it really changes everything for improving efficiency and quality in molding processes.
Poor exhaust design causes air pockets in molded products.True
Trapped air due to poor venting forms air pockets, affecting appearance.
Uneven density improves the strength of plastic products.False
Uneven density weakens strength as voids form, reducing product integrity.
How Can We Enhance Mold Venting to Improve Product Quality?
Improving mold venting might sound complicated, but it’s all about product quality and reliability. We probably want better products. We really do. Let us explore some practical methods. These methods might bring significant improvements.
To have better product quality, focus on placing vents in the right spots. Use bigger vents where possible. Try new methods like vacuum venting. These methods help get rid of air pockets. They lower the leftover stress in products. Consistent product quality emerges as a result.
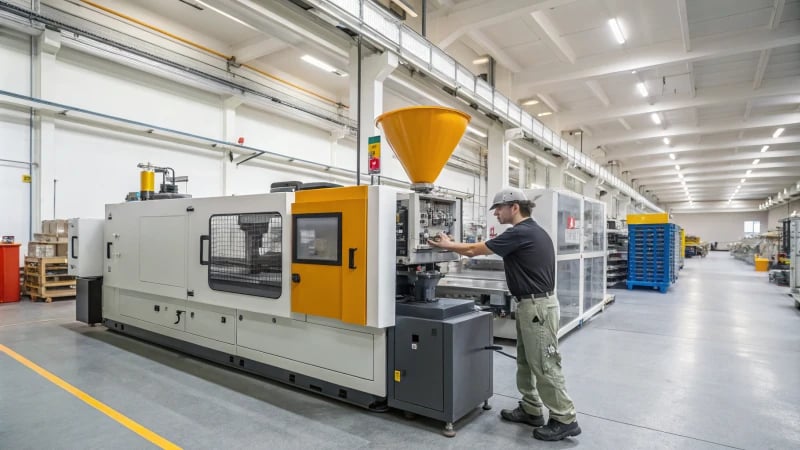
Find the Best Places for Vents
I remember joining mold design for the first time. I quickly saw that placing vents felt like solving a puzzle. Vents, in the right spots, stop air pockets and bubbles on the product’s surface. This preserves its shine and clarity. Using a CAD tool, designers can simulate how plastic flows and identify where air might get trapped, often near the flow’s end or in tricky shapes. It’s almost like being a detective, finding where those sneaky air traps hide.
Make Vents Larger
In one project, bigger vents changed everything. Larger vents allow air to escape more efficiently, reducing flow marks and fusion marks. However, it’s important to balance vent size with maintaining the structural integrity of the mold.
A table might be used to illustrate recommended vent sizes for different types of plastics:
Plastic Type | Recommended Vent Size (mm) |
---|---|
Polypropylene | 0.02 – 0.05 |
Polycarbonate | 0.03 – 0.06 |
ABS | 0.04 – 0.07 |
Use Vacuum Venting
Vacuum venting acts like a strong remedy when regular ways fail by applying a vacuum to pull out air from the mold cavity. This improves internal quality by preventing uneven density and reduces residual stresses.
Understanding how various materials respond to vacuum venting is crucial, especially when designing high-pressure plastic containers that require consistent density.
Solve Molding Efficiency Problems
Improving venting in molds directly raises molding efficiency by reducing filling difficulties and demolding challenges. It requires less injection pressure, which reduces cycle time and short shots.
Incorporating a demolding analysis7 could assist designers in predicting gas expansion problems during demolding, further enhancing productivity.
Match Vent Designs with Materials and Conditions
Lastly, matching vent designs to materials and conditions is vital as some materials need higher temperatures or pressures, affecting vent efficiency.
Research on material-specific venting8 provides insights for better products by understanding each material’s unique traits.
Optimizing vent placement reduces air pockets.True
Strategically placed vents prevent air entrapment, reducing defects.
Larger vents compromise mold structural integrity.False
Properly sized larger vents can improve air escape without damage.
Conclusion
Poor mold exhaust design leads to air pockets, uneven density, and increased residual stress in plastic products, compromising appearance quality and molding efficiency.
-
Explores how air pockets compromise transparency in optical lenses, crucial for quality control. ↩
-
Discusses how inadequate venting affects the efficiency of injection molding processes. ↩
-
Provides strategies to address common mold venting issues, enhancing product quality. ↩
-
Learn about techniques that improve mold exhaust efficiency, enhancing product quality. ↩
-
Learn about the impact of air pockets on optical clarity in lenses. ↩
-
Discover why incomplete filling results in increased product scrap. ↩
-
Learn about analyzing demolding challenges and solutions for reducing friction and improving productivity. ↩
-
Explore how different materials require unique venting strategies for optimal molding results. ↩