Hello! Have you ever considered starting a project with POM plastic? It’s like entering a new realm full of opportunities, where knowing the injection molding method might be your helpful guide.
The injection molding process for POM plastic involves precise control of temperatures and pressures to shape this versatile material. Key steps include selecting appropriate mold materials, ensuring uniform cooling, and managing the melting temperature of POM-H (190–230°C) and POM-K (190–210°C).
This overview shows a brief view of the injection molding process for POM. Each step needs specific methods and thoughts. Look deeper to find detailed ideas about mold design, temperature control and picking materials to become very skilled in this process.
POM-H requires a melting temperature of 190–230°C.True
POM-H's melting temperature range allows proper shaping without damage.
What Are the Key Properties of POM Plastic?
POM plastic, recognized for its mechanical quality, holds a crucial part in different industries. But what exactly renders it so unique?
POM plastic boasts high strength, rigidity, and excellent chemical resistance. Homopolymerized POM provides superior mechanical properties, while copolymerized POM offers enhanced impact resistance and thermal stability, making it versatile across numerous applications.
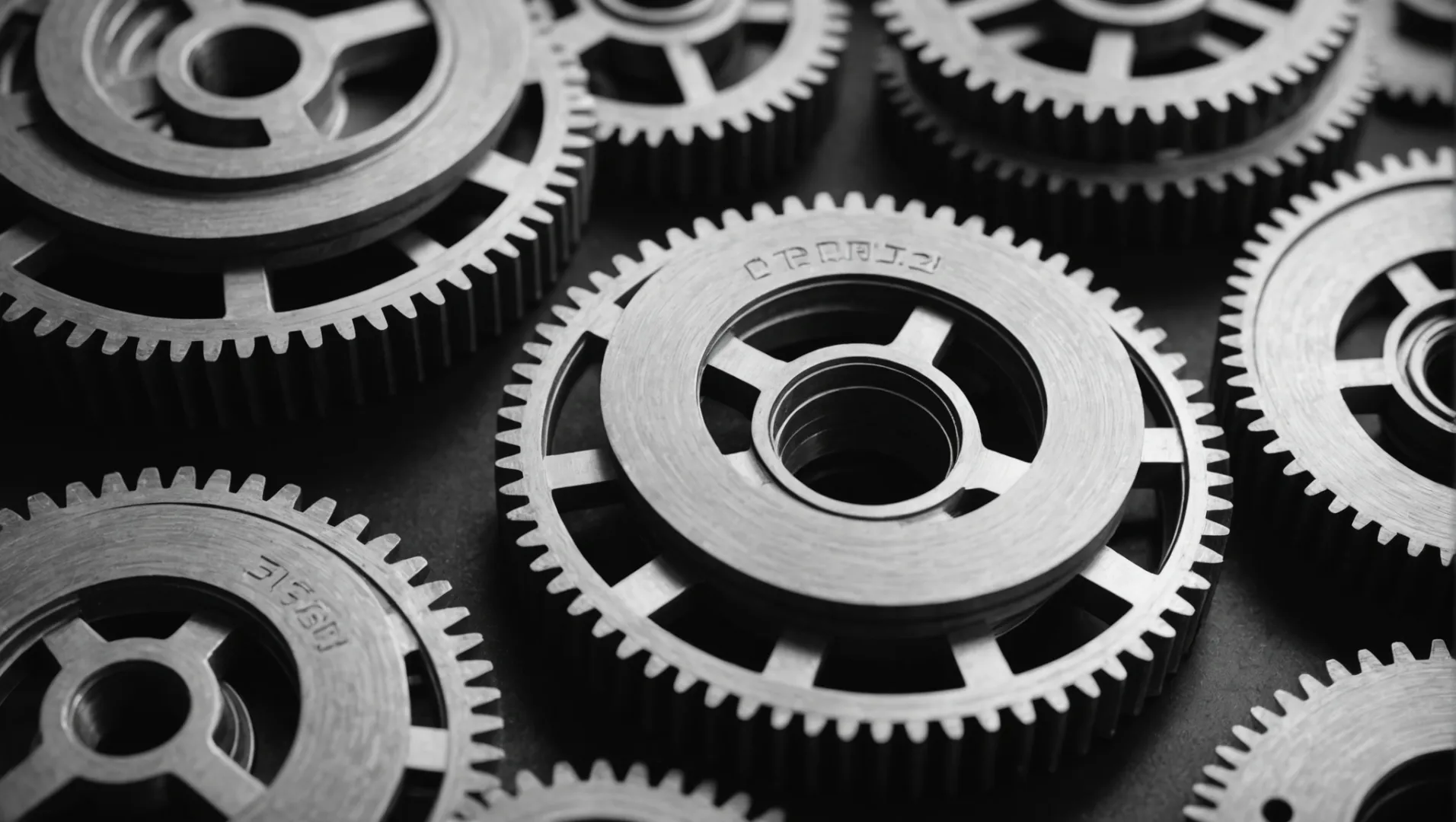
Mechanical Properties of POM Plastic
POM plastic is famous for being strong. Homopolymerized POM, with its regular molecular structure, usually offers more strength and firmness than copolymerized POM. This is because it is highly crystalline and handles large loads and pressure well. It is often utilized in creating strong gears and bearings.
In contrast, copolymerized POM shows more toughness and handles impacts better. Its molecular structure includes other monomers like ethylene oxide, making it suited for uses needing flexibility and strength, such as automotive interiors and electrical covers.
Thermal Properties
The heat traits of POM plastic differ between its two types. Homopolymerized POM melts at high temperatures, around 175°C, fitting for hot environments without losing strength. This is important for parts like engine components that operate under heat.
Copolymerized POM, however, offers greater thermal stability, resisting breakdown and color change over long periods at high temperatures. This is helpful in areas requiring steady performance under heat, like some car engine spaces.
Chemical Resistance
Both kinds of POM plastic resist chemicals like acids, bases, and solvents well. They behave differently in certain settings though. For example, homopolymerized POM might degrade in strong alkaline environments, while copolymerized POM stays intact better. Picking the right type of POM is key when facing chemical exposure.
Processability and Mold Design Considerations
Copolymerized POM flows better during injection molding. This helps it fill complex molds and form detailed shapes and thin parts. Additionally, while homopolymerized POM might shrink significantly during molding, copolymerized POM maintains shape better.
When creating molds for POM plastic, choosing hard and wear-resistant materials is important. Steel types like P20 or H13 are often chosen. Mold design should also consider the separation surface and removal method to allow easy extraction without bending.
Good cooling system design is crucial to keep mold temperature even and improve product quality. Water cooling channels, often 8-12 mm wide, help achieve this by ensuring efficient heat dissipation and saving time.
Applications Across Industries
Homopolymerized POM’s strong properties make it great for precise parts like gears and bearings in industrial machines where reliability is necessary. Meanwhile, copolymerized POM’s flexibility and impact resistance suit consumer goods and car parts that need to endure tough conditions.
By understanding these traits and choosing the right type of POM plastic, industries can optimize their production methods to achieve excellent product performance.
Homopolymer POM has higher strength than copolymer POM.True
Homopolymer POM's consistent structure delivers excellent mechanical strength.
Copolymer POM is unsuitable for high-temperature applications.False
Copolymer POM provides strong thermal stability and heat resistance.
How Do Homopolymer and Copolymer POM Differ in Applications?
Examining the contrasts between homopolymer and copolymer POM helps choose the best material for your uses.
Homopolymer POM, with its high strength and rigidity, is ideal for precision mechanical parts. Copolymer POM offers better toughness and impact resistance, making it suitable for automotive interiors and electrical enclosures.
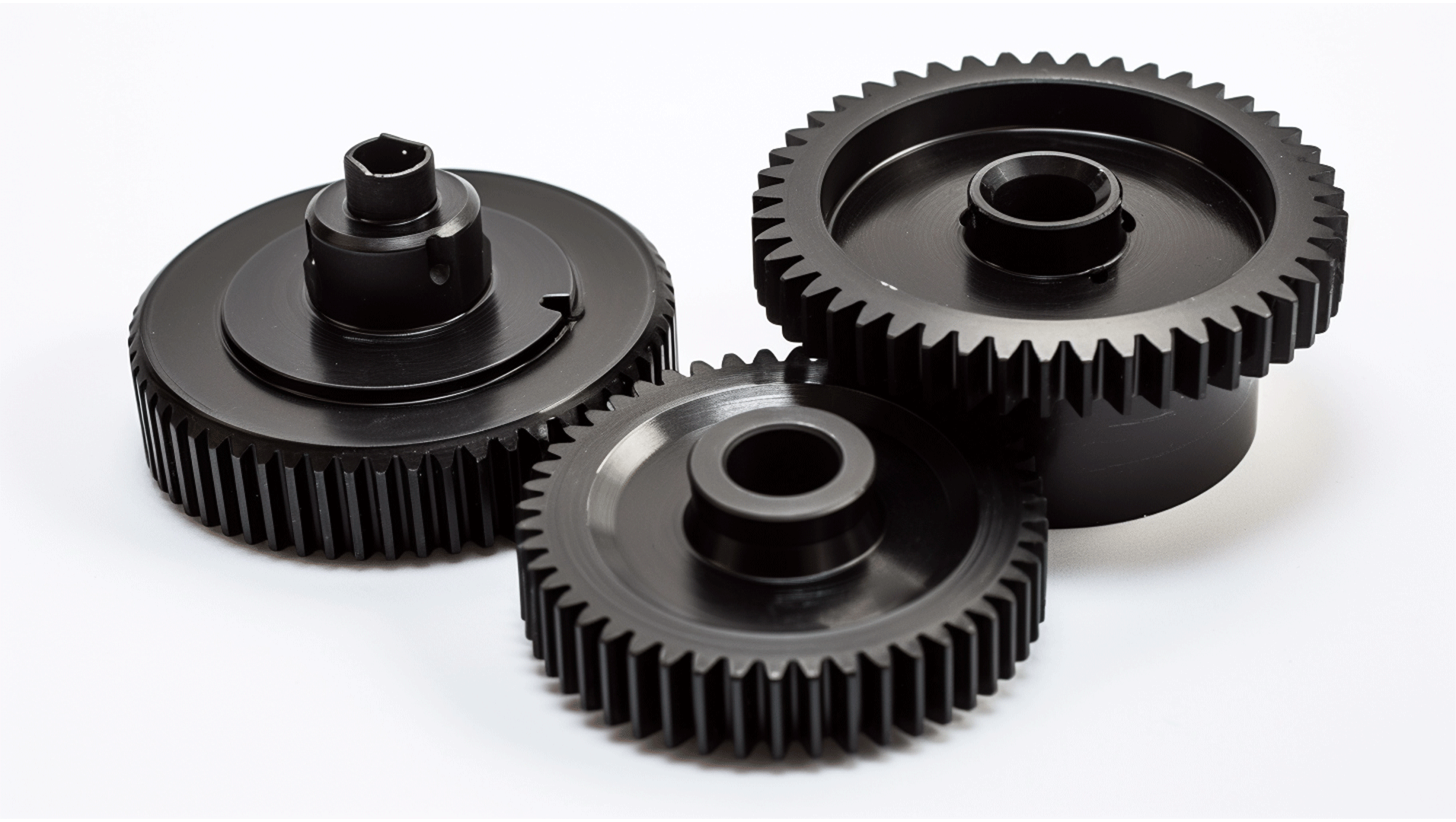
Understanding Molecular Structure
The main difference between homopolymer and copolymer POM (Polyoxymethylene) exists in their molecular structures. Homopolymer POM forms from one formaldehyde molecule, giving a very crystalline structure because of its regular molecular chains. This high crystallinity causes it to be very strong and stiff, thus chosen often for high-performance parts like gears and bearings.
In contrast, copolymer POM includes other monomers such as ethylene oxide. This method leads to a less regular chain structure, which reduces crystallinity a bit. Yet, this difference increases flexibility, offering better impact resistance and function in cold settings.
Mechanical and Thermal Performance
Regarding mechanical traits, homopolymer POM shows more tensile and bending strength. This suits it for uses needing big load support. Its higher melting point close to 175°C gives mechanical stability in hotter conditions, critical in high-heat settings.
Meanwhile, copolymer POM yields better toughness and impact resistance, vital for parts facing vibrations or hits. Its exceptional thermal stability helps it keep performing without breaking down in long-term heat. This feature helps in uses like car parts that face constant heat exposures.
Property | Homopolymer POM | Copolymer POM |
---|---|---|
Strength & Rigidity | More tensile and bending strength | Better toughness and flexibility |
Melting Point | ~175°C | A bit lower |
Thermal Stability | Good at high temperatures | Very good, less likely to fade |
Chemical Resistance and Processability
Both POM types resist chemicals well against acids, bases, and organic solvents. Still, in tough alkaline settings, copolymer POM outlasts homopolymer variants.
Looking at processability, copolymer POM has better fluidity, allowing easier mold filling in complex injection molding. This benefit aids in making detailed or thin parts where material flow matters a lot.
Aspect | Homopolymer POM | Copolymer POM |
---|---|---|
Chemical Resistance | Good overall; okay in alkalis | Superior in alkaline settings |
Processability | Higher shrinkage; needs careful control | Better fluidity; easier molding |
Application Spectrum
Choosing between homopolymer and copolymer POM needs to fit specific needs. For precise parts like gears and bearings needing stiffness and strength, homopolymer POM fits best. It’s often used in machine equipment where accuracy is crucial.
For uses needing impact resistance or facing changing environments, copolymer POM suits better. Its role in car interiors or electronic housings shows its ability to handle stress while staying solid. Car interior pieces particularly use its weather resistance and strength.
Homopolymer POM has higher tensile strength than copolymer.True
Homopolymer POM is famous for its excellent tensile and bending strength.
Copolymer POM is better for high-temperature applications.False
Homopolymer POM possesses a higher melting point, offering better heat resistance.
What Considerations Are Crucial in Mold Design for POM?
Form creation remains crucial when dealing with POM plastic to achieve smooth production and excellent outcomes.
Crucial considerations in mold design for POM include selecting suitable mold materials, ensuring effective cooling systems, and optimizing the demolding process to prevent defects.
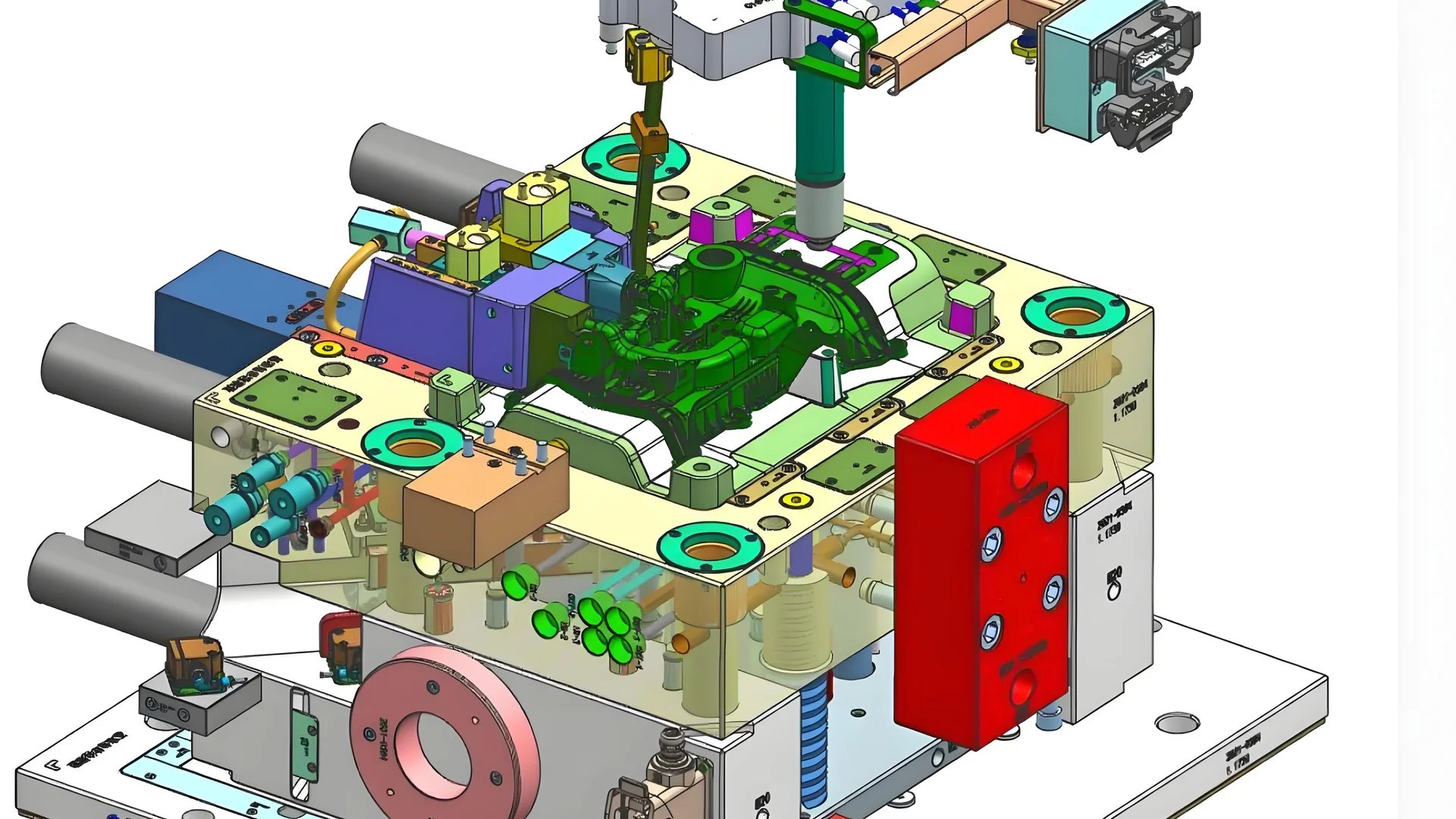
Using Picking the Right Mold Materials
When creating molds for POM, choosing the correct material is very important. Molds need materials with high hardness, strength, and wear resistance to handle POM processing demands. Typical choices include steel types like P20 and 718, which are nitrided and hardened. For productions over 500,000 cycles, H13 or S136 steel hardened to 48-52HRC is suggested.
Planning for Good Cooling
Designing the cooling system keeps mold temperatures even and betters product quality. Usually, water is used for cooling with channels placed carefully in the mold. These channels usually range from 8-12 mm in diameter, with spaces based on the product’s wall thickness and shape, usually between 20-50 mm apart.
The cooling system needs equal inlet and outlet positions for even water flow and good temperature control.
Improving the Demolding Process
A good mold design should think about the parting surface and release method for easy demolding and to avoid bending. The parting surface should be picked to lower impact on how the product looks and works, while the demolding method needs to spread force evenly based on the product’s shape.
Controlling Melting Temperature and Pressure
Processing POM involves strict temperature control. For example, POM-H needs a melting temperature of 190-230°C, while POM-K needs 190-210°C. Keeping back pressure lower, ideally under 200 bar, helps stop material damage during molding.
Example: Homopolymer vs. Copolymer POM Mold Design
Homopolymer POMs are usually used for jobs needing high strength and stiffness, while copolymer POMs fit places needing better impact resistance and heat stability. This difference guides mold design, from picking cooling channels to choosing fitting release methods.
For instance, choices for mold material may change depending on if you’re designing high-performance mechanical parts or things needing more flexibility.
These key parts of mold design can really affect the efficiency and quality of POM injection molding methods.
POM requires a cooling channel diameter of 8-12 mm.True
The cooling system for POM usually employs channels between 8-12 mm wide.
POM-H melts at a lower temperature than POM-K.False
POM-H needs a greater melting heat (190-230°C) than POM-K.
How to Optimize Cooling Systems in POM Injection Molding?
Cooling systems hold immense importance in POM injection molding. Improve them to raise product quality and efficiency.
To optimize cooling systems in POM injection molding, design the cooling waterways according to the product’s shape and size, ensuring uniform mold temperature. Use water channels with a diameter of 8-12 mm, spaced 20-50 mm apart, and place inlets and outlets symmetrically for even water flow.
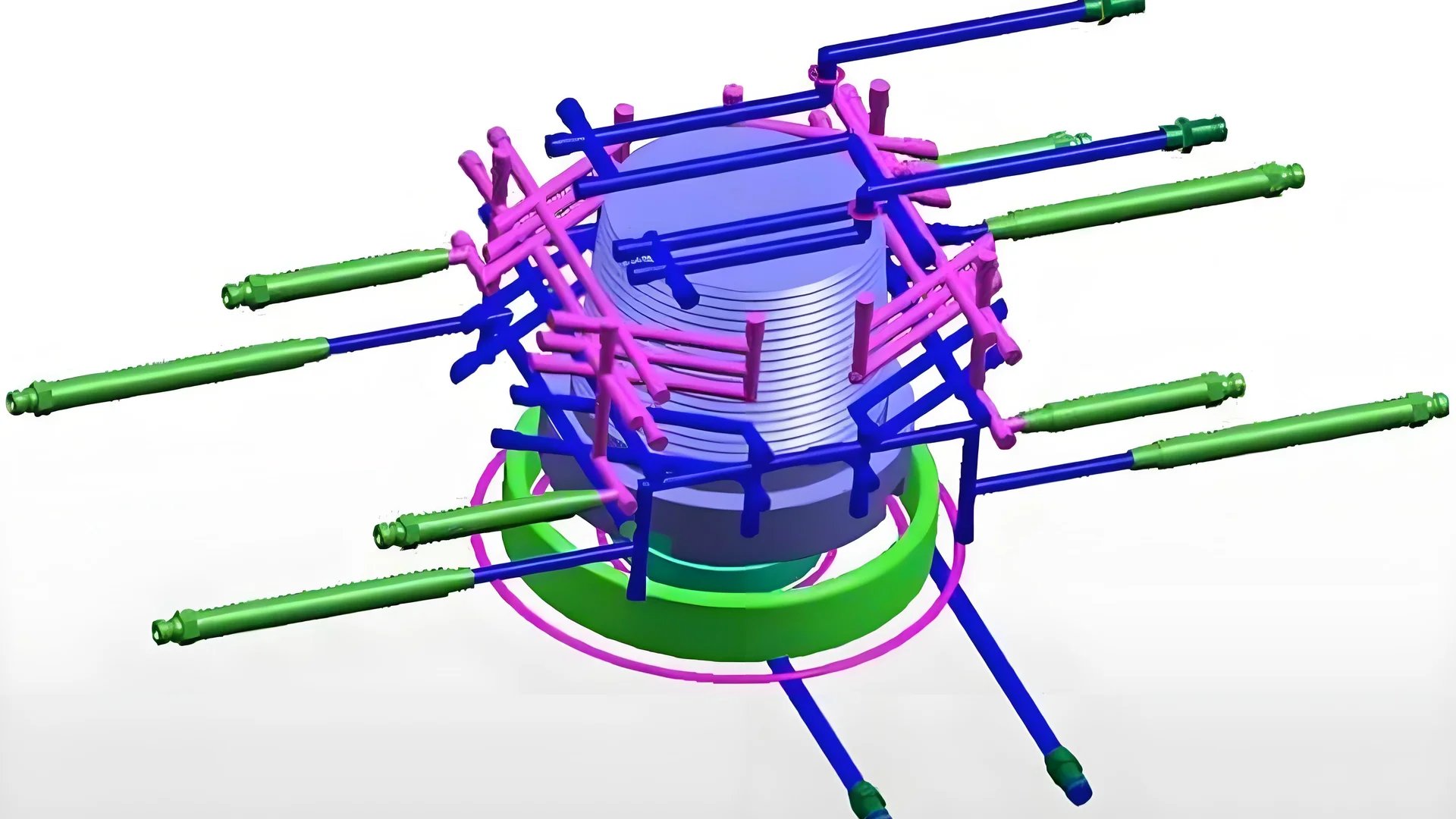
Importance of Cooling Systems in Injection Molding
Good cooling systems are crucial in POM injection molding. They influence product quality1 and how fast production goes. A well-planned cooling setup keeps the mold temperature even. This reduces cycle time and keeps the molded parts’ sizes stable.
Designing Efficient Cooling Channels
Think about the product’s shape and size when designing cooling for POM molds. Cooling channels should have a diameter of 8-12 mm. Channels should be 20-50 mm apart, based on wall thickness and structure. This helps keep the temperature the same across the mold, stopping issues like warping or shrinking.
Symmetrical Inlet and Outlet Placement
Inlets and outlets should be placed symmetrically in the mold. This arrangement helps cooling water flow evenly, keeping the mold temperature the same everywhere. Consistent temperature helps in maintaining product uniformity2 and reduces possible problems.
Material Selection for Mold Longevity
Picking the correct mold material influences cooling effectiveness. Tough materials like P20 nitrided steel work well because they resist wear and last long. For molds making over 500,000 items, materials like H13 or S136, hardened to 48-52HRC, are good. They handle repeated heating and cooling.
Role of Water Circulation in Temperature Management
Water cooling often helps in POM injection molding due to its heat removal ability. Water moving through cooling channels takes away extra heat, keeping processing temperatures ideal for POM-H and POM-K types. This not only boosts process efficiency3 but also assures the product has a high-quality surface.
Symmetrical inlets ensure even mold temperature.True
Symmetrical inlet placement provides uniform water flow, keeping temperatures consistent.
Cooling channels should be 15 mm apart for best results.False
Channels should sit 20-50 mm apart for best cooling. 15 mm is not enough.
Conclusion
Discover the detailed insights into POM injection molding to uplift your projects. Consider these principles for superior product quality and performance. Start today!
-
Learn why cooling systems are critical for product quality and efficiency.: An improper injection mold cooling process, then, will almost always result in part defects that require rework or discard. The cooling process … ↩
-
Discover how cooling uniformity prevents defects in molded products.: Temperature control is super important in injection molding because it directly affects the quality, consistency, and cycle time of molded parts … ↩
-
Explore how water circulation boosts efficiency and product finish.: Another benefit of a water cooled system is that it leaves a reduced carbon footprint versus an air cooled system. ↩