Have you ever marveled at the flawless finish of a product? That high-quality sheen is no accident; it’s the result of meticulous polishing processes!
The polishing process for injection molded products involves several methods, including mechanical, chemical, electrolytic, and ultrasonic polishing. Each technique is selected based on the product’s requirements, aiming to enhance surface smoothness and visual appeal.
But there’s more to polishing than meets the eye! Each method has its own set of intricacies that can significantly impact the final product. Let’s dive deeper into these fascinating techniques!
Chemical polishing is ideal for complex shapes.True
Chemical solutions dissolve uneven surfaces, enhancing smoothness and gloss, suitable for intricate designs.

What Are the Steps Involved in Mechanical Polishing?
Mechanical polishing is a meticulous process that transforms rough surfaces into smooth, shiny finishes.
Mechanical polishing involves using tools like sandpaper and grinding wheels to gradually refine a surface. The process begins with coarse-grained tools to remove imperfections and progresses to finer grains for a smooth finish. It requires skill to balance pressure and direction, ensuring minimal scratches.

Understanding the Mechanical Polishing Process
Mechanical polishing is essential for enhancing the surface quality of injection molded products1. Here’s how it unfolds:
-
Preparation:
- Begin by cleaning the product to remove any dust or debris. This ensures a clear view of the surface defects that need addressing.
-
Initial Coarse Polishing:
- Use coarse-grained sandpaper or grinding wheels to remove obvious flaws and rough patches. This step requires careful attention to prevent further damage to the product surface.
-
Progressive Refinement:
- Gradually switch to finer sandpaper, reducing the grit size incrementally. This smooths out the surface and removes smaller imperfections left by the coarser materials.
-
Final Fine Polishing:
- Utilize ultra-fine polishing tools to achieve the desired smoothness and gloss. This stage is crucial for ensuring a high-quality finish.
Tools Used in Mechanical Polishing
Tool Type | Description |
---|---|
Sandpaper | Available in various grits for different polishing stages |
Grinding Wheels | Used for initial removal of large surface defects |
Buffing Pads | Helps in achieving a mirror-like finish |
Challenges in Mechanical Polishing
While mechanical polishing offers a relatively straightforward approach, it comes with its set of challenges:
-
Scratch Management:
Ensuring minimal scratches involves controlling the intensity and direction during polishing. An unsteady hand can exacerbate surface defects. -
Skill Requirement:
The process demands a significant level of expertise to achieve consistent results across different products, especially larger or more complex shapes.
Understanding these steps and challenges allows manufacturers to better optimize their polishing techniques2, enhancing product quality effectively.
Mechanical polishing uses only sandpaper.False
Mechanical polishing also involves grinding wheels and buffing pads.
Final fine polishing achieves a high-gloss finish.True
Ultra-fine tools are used in this stage to ensure smoothness and gloss.
How Does Chemical Polishing Enhance Surface Smoothness?
Chemical polishing is a transformative process that improves surface smoothness by using reactive solutions.
Chemical polishing enhances surface smoothness by dissolving microscopic uneven parts of an injection molded product’s surface. This method involves using specific chemical solutions—acidic, alkaline, or neutral—to achieve a high-gloss finish, particularly beneficial for complex shapes. However, careful control of solution concentration and processing conditions is essential to prevent damage.

Understanding Chemical Polishing
Chemical polishing is a popular technique used to enhance the surface smoothness of injection molded products. By utilizing chemical reactions, this method effectively dissolves microscopic unevenness on the product’s surface. Unlike mechanical polishing3, which relies on physical abrasion, chemical polishing leverages the power of chemistry to achieve smoother surfaces.
How It Works
The process involves immersing the product in a chemical solution that reacts with the surface material. This solution could be acidic, alkaline, or neutral, depending on the material being polished and the desired outcome. As the chemical solution interacts with the surface, it selectively dissolves the high points on a microscopic level, resulting in a smoother and more reflective finish.
- Acidic Solutions: These are often used for metals and alloys, providing a controlled etching effect.
- Alkaline Solutions: Ideal for certain plastics and non-metal materials, offering a gentle yet effective polish.
- Neutral Solutions: Used when minimal reaction is required or when dealing with sensitive materials.
This table summarizes the key aspects:
Solution Type | Suitable Materials | Effect |
---|---|---|
Acidic | Metals, Alloys | Controlled etching |
Alkaline | Plastics | Gentle polish |
Neutral | Sensitive Materials | Minimal reaction |
Advantages of Chemical Polishing
Chemical polishing offers several advantages:
- High Gloss Finish: Achieves a more uniform and mirror-like surface that enhances visual appeal.
- Complex Shapes: Excellent for products with intricate designs or hard-to-reach areas where mechanical methods fall short.
Challenges and Considerations
While highly effective, chemical polishing requires meticulous control over various parameters:
- Solution Concentration: Must be precisely measured to prevent over-polishing or corrosion.
- Temperature and Time: Both factors influence the rate and extent of polishing; precise control prevents damage.
- Environmental Impact: The process can produce waste that needs careful handling to minimize pollution.
In summary, chemical polishing is a sophisticated technique that, when executed correctly, offers substantial benefits in terms of surface smoothness and appearance. However, it demands expert handling to mitigate potential drawbacks such as environmental impact and risk of corrosion.
Chemical polishing uses only acidic solutions.False
Chemical polishing can use acidic, alkaline, or neutral solutions.
Chemical polishing is ideal for complex shapes.True
It reaches intricate areas where mechanical methods may fail.
What Are the Benefits and Drawbacks of Electrolytic Polishing?
Electrolytic polishing offers exceptional results, but what are its real pros and cons?
Electrolytic polishing uses electrochemistry to achieve high gloss and surface flatness on injection molded products. It excels in processing harder materials but requires costly equipment and skilled technicians. Despite its efficiency, safety concerns and operational complexity pose challenges.

Understanding Electrolytic Polishing
Electrolytic polishing, a technique grounded in electrochemistry, is primarily used to enhance the surface quality of injection molded products. By functioning as the anode in an electrolytic solution, the product undergoes a controlled dissolution of its microscopic surface protrusions. This results in a smoother, more lustrous finish. The process is particularly advantageous for materials with higher hardness, which may not respond well to other polishing methods.
Key Advantages of Electrolytic Polishing
One of the most notable benefits of electrolytic polishing is the exceptional gloss and surface flatness it can achieve. This makes it highly desirable for products requiring a flawless finish, such as medical devices or automotive parts. Additionally, because it can process harder materials effectively, it’s often used where other methods fall short.
Advantages | Details |
---|---|
High Gloss | Achieves superior shine compared to mechanical or chemical polishing. |
Surface Flatness | Results in an even, smooth surface free from micro-defects. |
Effective on Hard Materials | Processes materials like stainless steel efficiently, where other methods may fail. |
Exploring the Drawbacks
Despite its impressive results, electrolytic polishing does come with several drawbacks that should not be overlooked. The initial setup costs can be prohibitively high due to the specialized equipment required. Furthermore, the process demands skilled technicians to handle operations safely and efficiently. Safety is a significant concern, as mishandling the electrolytes or electrical components can pose risks.
Drawbacks | Details |
---|---|
High Equipment Cost | Requires expensive, specialized machinery. |
Operational Complexity | Needs skilled professionals to ensure precise control over the process. |
Safety Concerns | Involves handling hazardous chemicals and electrical currents, necessitating stringent safety measures. |
Applications and Considerations
The decision to use electrolytic polishing often hinges on specific application needs. For instance, in the medical device industry4, polished surfaces are crucial for ensuring cleanliness and ease of sterilization. Meanwhile, in automotive manufacturing5, components like headlight covers benefit from reduced air resistance due to their polished finish.
Understanding both the benefits and potential challenges of electrolytic polishing allows manufacturers to make informed decisions about its application. By carefully weighing these factors, they can optimize product performance and aesthetics while managing costs and safety effectively.
Electrolytic polishing achieves high gloss on hard materials.True
Electrolytic polishing is effective on hard materials, providing superior shine.
Electrolytic polishing is cost-effective for all applications.False
The process requires costly equipment, making it expensive for some uses.
Why is Ultrasonic Polishing Ideal for Complex Shapes?
Ultrasonic polishing stands out for its ability to handle intricate designs with precision and efficiency.
Ultrasonic polishing is particularly suited for complex shapes due to its high-frequency vibrations, which allow for precise surface finishing without the risk of scratches. This method ensures efficiency and quality in polishing intricate injection molded products.
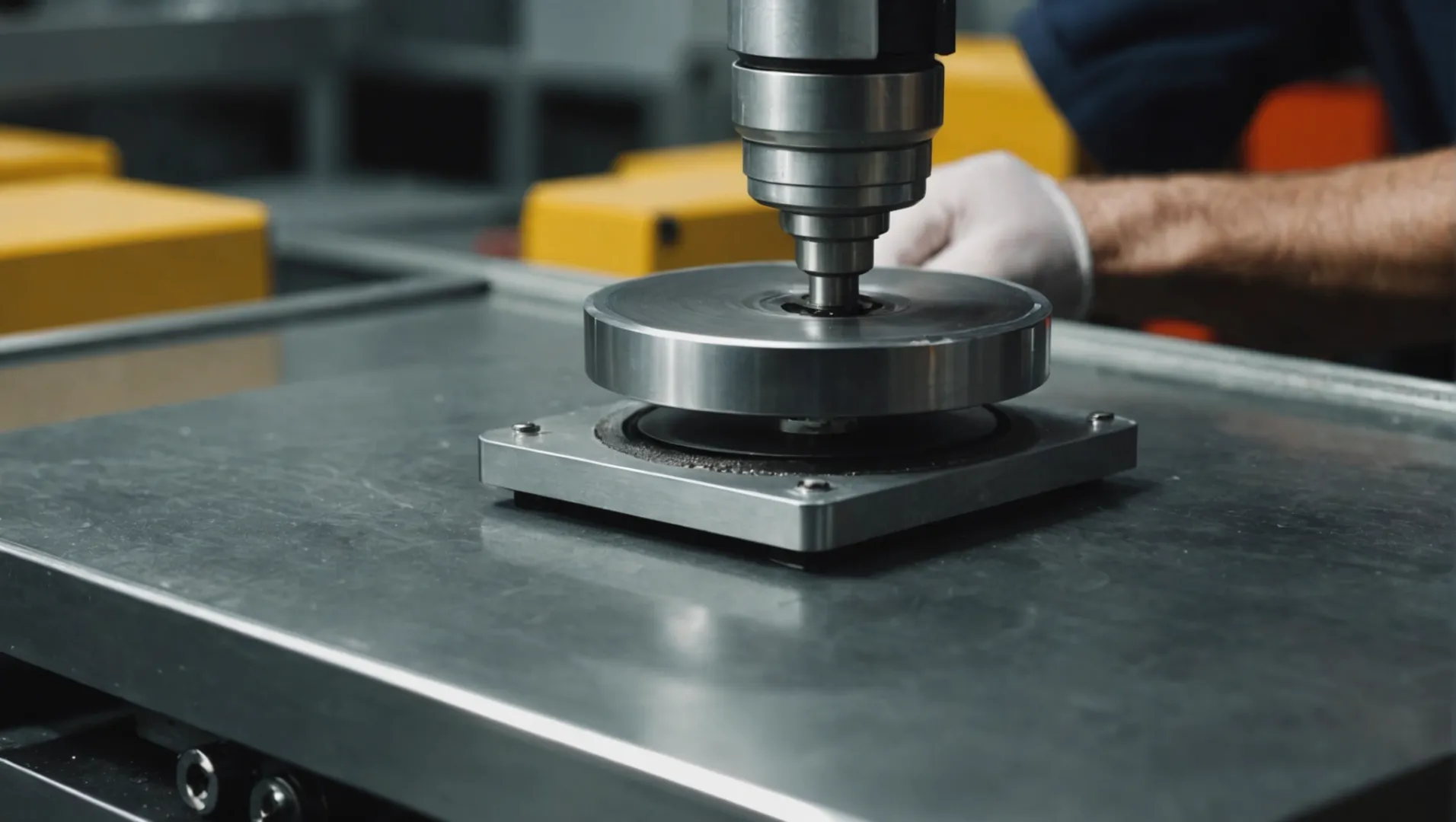
Understanding Ultrasonic Polishing
Ultrasonic polishing utilizes high-frequency sound waves to achieve a smooth and refined finish on surfaces. The process involves a polishing tool6 that vibrates at ultrasonic frequencies, effectively removing microscopic irregularities from the product’s surface. These vibrations are transferred through a medium, such as an abrasive suspension or paste, directly onto the surface being polished.
Advantages for Complex Shapes
One of the primary reasons ultrasonic polishing is ideal for complex shapes is its non-abrasive nature. The high-frequency vibrations do not rely on direct mechanical pressure, significantly reducing the risk of unwanted scratches. This method is highly efficient for intricate designs where traditional polishing tools struggle to reach.
- Precision: The ultrasonic process can target specific areas, ensuring detailed attention to complex geometries without compromising the overall integrity of the product.
- Consistency: Unlike mechanical methods that might vary in effectiveness based on the operator’s skill, ultrasonic polishing provides uniform results across multiple items, enhancing consistency in production.
Practical Applications
Ultrasonic polishing is favored in industries where detailed surface finishing is crucial:
- Medical Devices: Components such as surgical instruments and diagnostic tools require impeccable smoothness and precision to ensure patient safety and device functionality.
- Aerospace Parts: Complex parts like turbine blades benefit from ultrasonic polishing, as it ensures reduced drag and improved aerodynamic efficiency.
- Automotive Components: High-performance car parts often feature intricate designs that demand precision polishing to enhance both aesthetics and performance.
Challenges and Considerations
Despite its advantages, ultrasonic polishing does have its challenges:
- Equipment Cost: The initial investment in ultrasonic equipment can be significant, making it less accessible for smaller operations.
- Technical Expertise: Proper operation requires skilled technicians familiar with the nuances of ultrasonic systems to avoid damage to delicate components.
The benefits of ultrasonic polishing are best realized when balancing these considerations with the specific needs of the product and production scale. For businesses dealing with complex shapes, this method presents a valuable solution that combines efficiency with high-quality results.
Ultrasonic polishing reduces risk of scratches.True
High-frequency vibrations polish surfaces without direct mechanical pressure.
Ultrasonic polishing is less consistent than manual methods.False
It provides uniform results, unlike manual methods dependent on operator skill.
Conclusion
Mastering polishing techniques can significantly enhance the quality of injection molded products, making them more competitive and functional. Applying the right method ensures superior finishes suitable for diverse applications.
-
Learn about the foundational process behind injection molded products.: what injection molding is, what the injection molding machine looks like, and how the injection … ↩
-
Discover strategies to enhance polishing efficiency and quality.: Here we discuss how Quartz Crystal Microbalance with Dissipation Monitoring (QCM-D) can be used to simulate various CMP processes. ↩
-
Explore the differences between mechanical and chemical polishing methods.: Mechanical polishing fails to remove inclusions, but also tends to push them further into the surface and even increase them by further pickup of abrasive … ↩
-
Discover why polished surfaces enhance safety and hygiene in medical devices.: Surface treatment is essential in the medical industry because it ensures that medical devices and equipment are safe, effective, and reliable. For example, … ↩
-
Learn how polished surfaces improve performance and aesthetics in cars.: Surface polishing is a key process to improve the appearance of products, especially in high-end consumer products and industrial design. For … ↩
-
Discover how ultrasonic tools enhance precision in surface finishing.: ULTRAMAX® Mini Ultrasonic Polishing System allows you to polish ribs, slots and intricate details far faster than by hand. ↩