Have you ever wondered why plastics have become the go-to material in automotive design?
Plastics are ideal for automotive components due to their lightweight, versatile design capabilities, cost advantages, and functional characteristics such as corrosion resistance and sound insulation. These properties enhance vehicle performance, fuel efficiency, and sustainability compared to traditional materials like metals.
But there’s so much more beneath the surface! Let’s dive deeper into how plastics are reshaping the automotive industry.
Plastics reduce vehicle weight, improving fuel efficiency.True
Plastics are lighter than metals, reducing vehicle weight and enhancing fuel efficiency.
How Do Plastics Enhance Vehicle Performance?
Plastics are transforming the automotive industry with their multifaceted advantages, boosting performance significantly.
Plastics enhance vehicle performance by reducing weight, allowing complex designs, lowering costs, and improving durability. These benefits lead to better fuel efficiency, innovative aesthetics, and robust functionality, positioning plastics as a superior choice over traditional materials like metals.
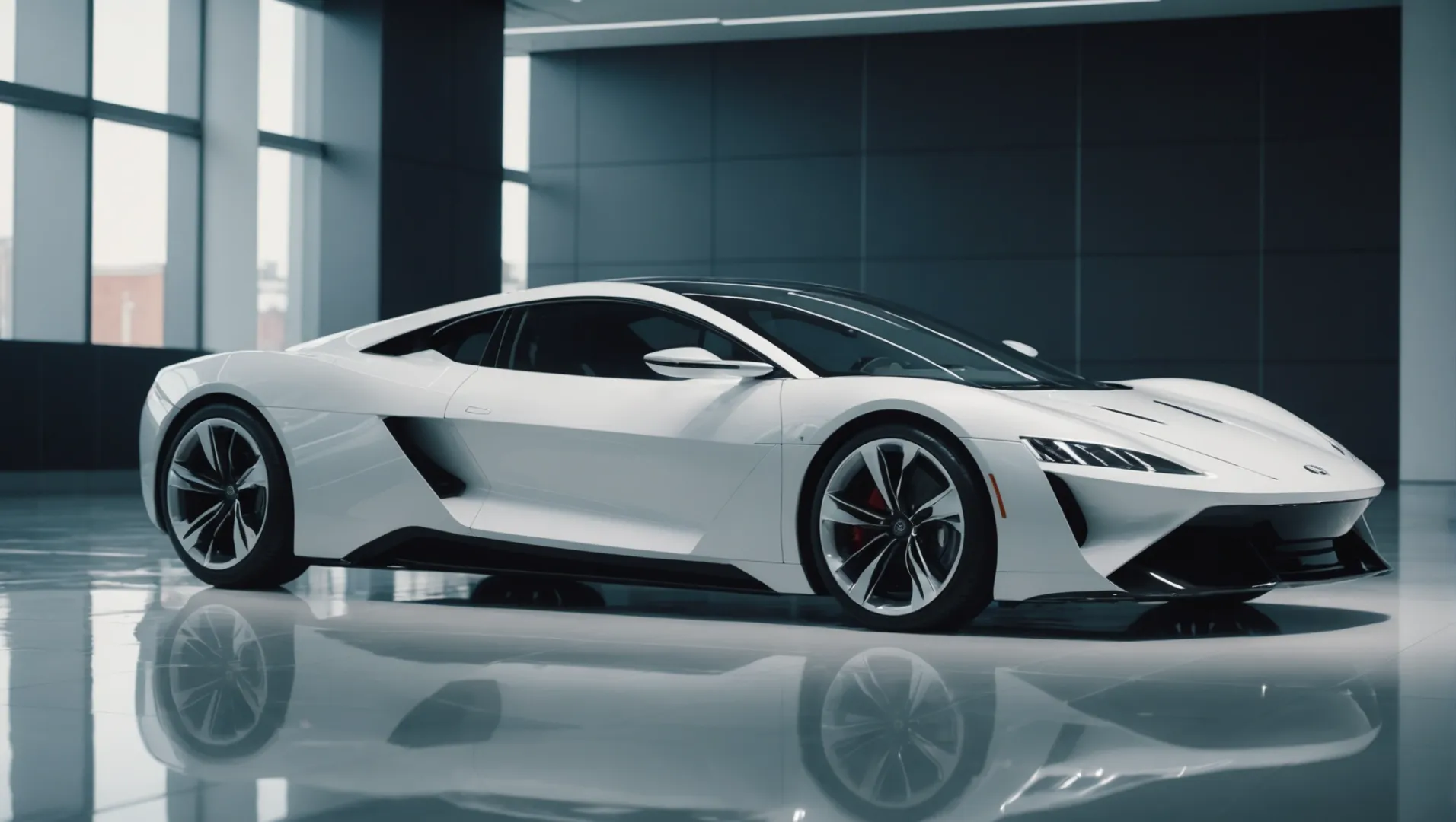
The Role of Lightweight Plastics in Fuel Efficiency
One of the primary reasons plastics are favored in automotive manufacturing is their lightweight nature1. Plastics typically have a lower density compared to metals, enabling significant weight reduction in vehicles. For instance, replacing metal components with plastic alternatives in interiors, bumpers, or body panels can decrease vehicle weight by tens or even hundreds of kilograms.
Studies show that reducing a vehicle’s weight by 100 kilograms can cut fuel consumption by approximately 0.3 to 0.6 liters per 100 kilometers. This improvement is crucial in today’s eco-conscious market, where energy conservation and emission reductions are key priorities.
Design Freedom and Innovation with Plastics
Plastics offer unparalleled design flexibility, allowing for the easy molding of complex shapes and the creation of aesthetically pleasing vehicle parts. Processes such as injection molding and blow molding facilitate the production of intricate designs that metals cannot easily replicate.
Moreover, plastics can be dyed and treated to achieve a wide array of colors and textures. This versatility supports consumer demand for personalization and high-quality interiors, often found in luxury vehicles.
Cost-Effectiveness in Automotive Production
From a cost perspective, plastics present numerous advantages. The raw material costs for plastics are generally lower than those for metals. Additionally, advancements in plastic production technology continue to drive costs down.
The processing of plastic components is straightforward and efficient, particularly with methods like injection molding that can produce large quantities swiftly. This efficiency reduces overall production costs, making it economically viable for manufacturers to incorporate high-performance plastics into their designs.
Enhancing Durability and Functionality
Plastics are not just lightweight and cost-effective; they also bring substantial functional benefits. Their corrosion resistance2 makes them ideal for components exposed to harsh environments, such as radiator grilles and fenders.
Additionally, some plastics offer excellent sound insulation and heat resistance, improving ride comfort by minimizing noise and thermal transfer within the vehicle. This property is particularly beneficial in parts like dashboards and engine hoods.
Furthermore, plastics provide exceptional electrical insulation, which is critical in automotive electrical systems to prevent short circuits and other electrical failures.
Plastics reduce vehicle weight significantly.True
Plastics' lower density compared to metals cuts vehicle weight by hundreds of kilograms.
Plastics increase car production costs.False
Plastic components are cost-effective due to lower raw material costs and efficient production.
What Types of Plastics Are Commonly Used in Cars?
Discover the essential plastics that revolutionize modern automotive design and functionality.
Commonly used plastics in cars include polypropylene, polycarbonate, acrylonitrile butadiene styrene (ABS), and polyurethane. These materials are chosen for their durability, flexibility, lightweight properties, and ability to be molded into complex shapes, enhancing both vehicle performance and aesthetic appeal.
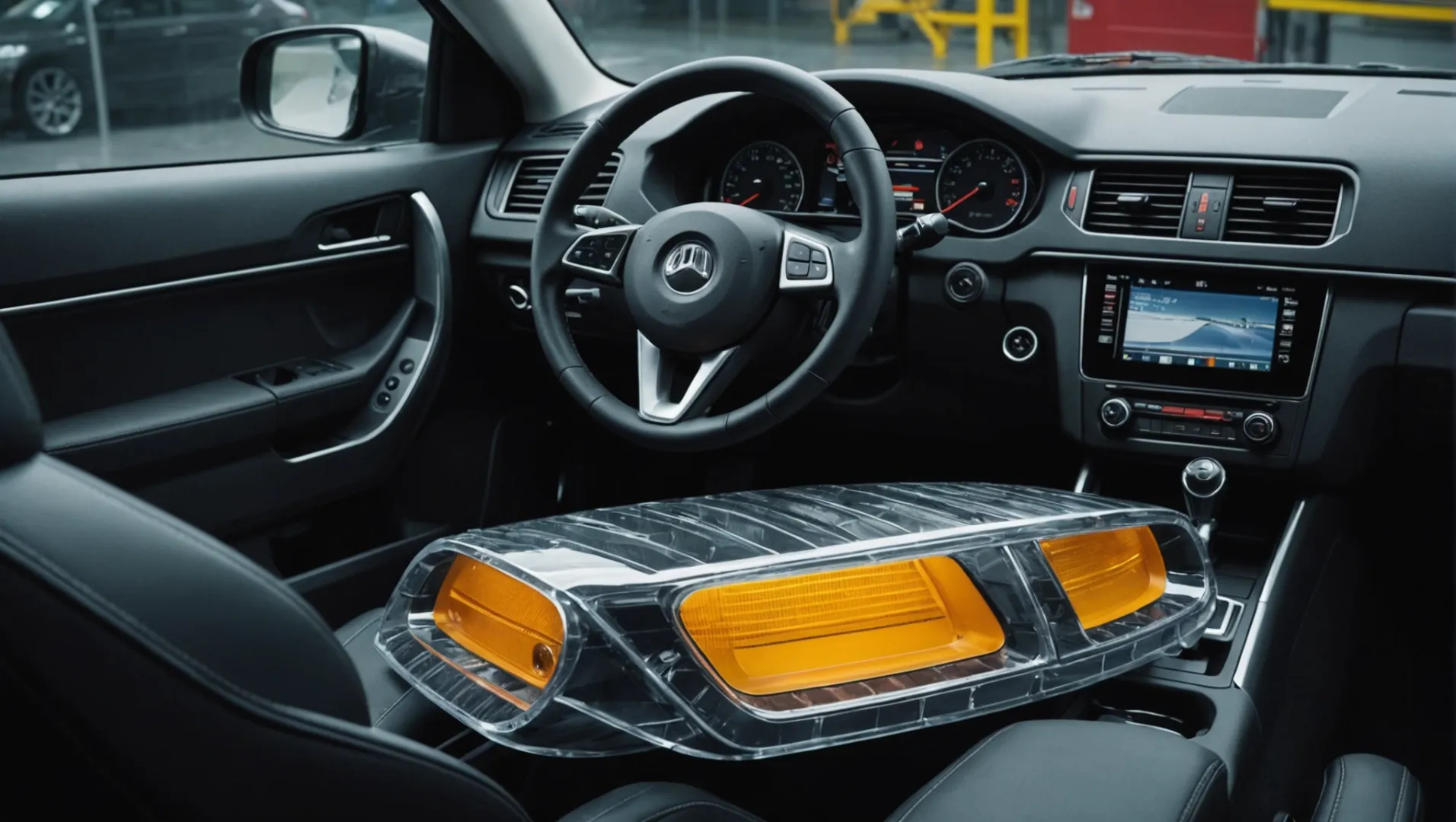
Polypropylene (PP)
Polypropylene is one of the most widely used plastics in the automotive industry due to its versatile characteristics3. This thermoplastic polymer is utilized in producing bumpers, chemical tanks, cable insulation, and interior elements like trims. Its lightweight nature contributes significantly to reducing vehicle weight, thus improving fuel efficiency.
Polycarbonate (PC)
Renowned for its high impact resistance and clarity, polycarbonate is extensively used in automotive lighting4. The material is often employed in manufacturing headlamp lenses and other transparent components due to its excellent light transmission properties and durability. Moreover, its ability to withstand harsh environmental conditions makes it ideal for exterior applications.
Acrylonitrile Butadiene Styrene (ABS)
ABS is a robust engineering plastic famous for its strength and rigidity, making it suitable for dashboard components5 and trim. The material’s ease of processing and ability to take on different textures and colors allow designers to create aesthetically pleasing interiors without compromising on durability.
Polyurethane (PU)
Polyurethane is particularly valued for its versatility in automotive applications6. It is used in seating foams, headrests, and insulation panels. Polyurethane’s comfort-enhancing qualities provide superior cushioning and support while also offering excellent sound insulation properties.
Table: Comparison of Common Automotive Plastics
Plastic Type | Key Properties | Common Uses |
---|---|---|
Polypropylene | Lightweight, chemical resistant | Bumpers, trims, cable insulation |
Polycarbonate | High impact resistance, transparency | Headlamps, transparent panels |
ABS | Strength, rigidity | Dashboard components, trims |
Polyurethane | Flexible, sound insulating | Seat foams, headrests |
The Role of Plastics in Future Automotive Designs
As the automotive industry continues to innovate towards more sustainable solutions, the use of advanced plastics will play an increasingly pivotal role. The development of bio-based plastics7 presents opportunities for further reducing environmental impact while maintaining the high-performance standards expected in modern vehicles.
Polypropylene is used in car bumpers.True
Polypropylene's lightweight and durable nature makes it ideal for bumpers.
ABS is unsuitable for dashboard components.False
ABS is strong and rigid, making it perfect for dashboards.
How Do Plastics Contribute to Automotive Sustainability?
In the quest for sustainable automotive solutions, plastics play a pivotal role in enhancing vehicle efficiency and reducing environmental impact.
Plastics contribute to automotive sustainability by enabling lightweight construction, reducing fuel consumption, and offering recyclability. Their high design flexibility and durability further support eco-friendly innovation in car manufacturing.
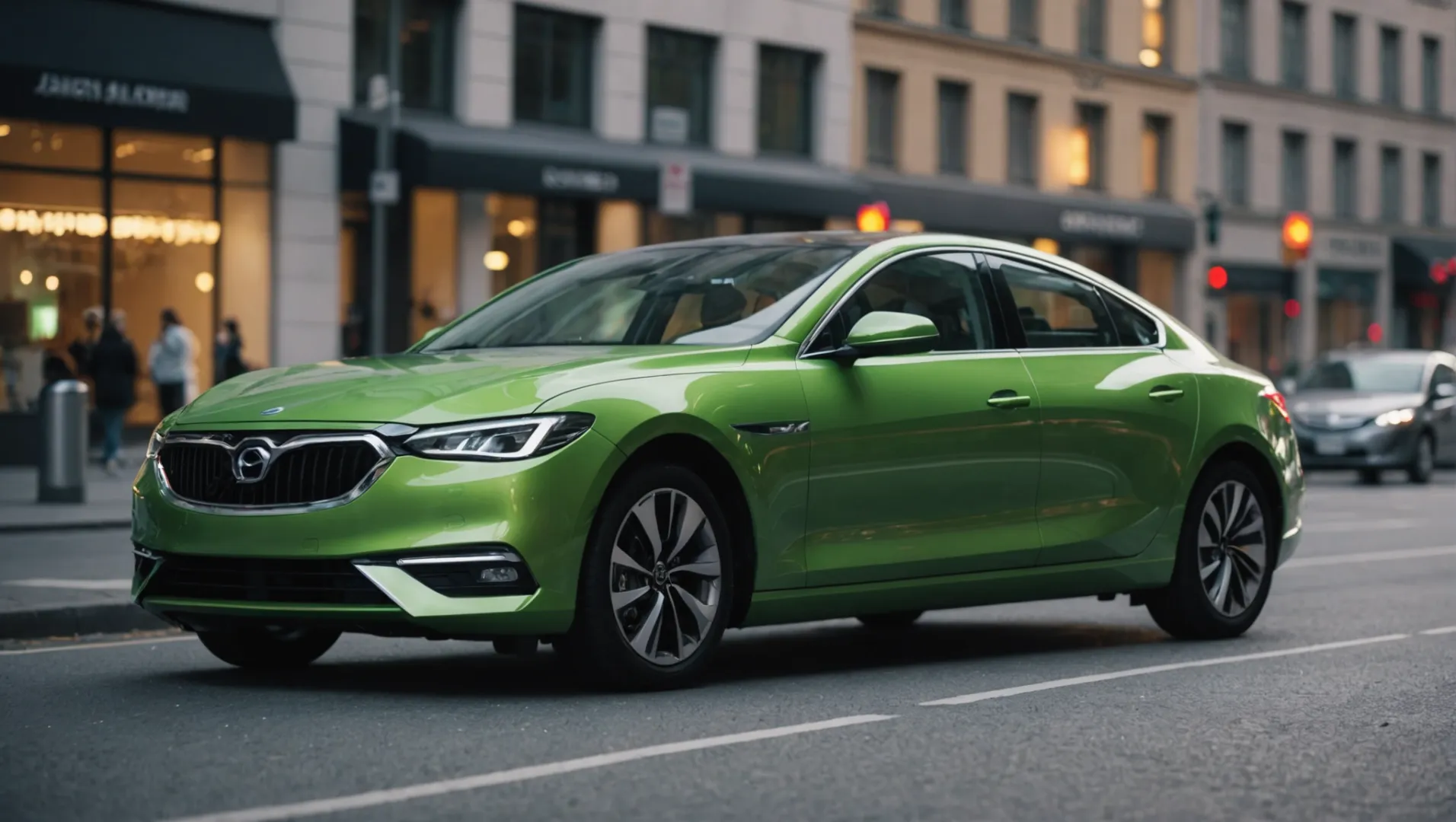
The Lightweight Advantage of Plastics
One of the foremost contributions of plastics to automotive sustainability is their lightweight nature8. Compared to traditional materials such as metals, plastics significantly reduce the overall weight of a vehicle. This reduction not only enhances fuel efficiency but also lowers carbon emissions, aligning with global sustainability goals. For instance, every 100 kilograms reduced in vehicle weight can save approximately 0.3 to 0.6 liters of fuel per 100 kilometers.
Design Freedom and Its Sustainability Benefits
Plastics offer unparalleled design freedom, allowing for the creation of complex shapes without the need for extensive machining. This capability results in less waste and more efficient use of materials. With processes like injection molding and blow molding, manufacturers can produce components that are both aesthetically pleasing and functional, reducing the need for additional finishing processes that can be resource-intensive.
Moreover, plastics can be dyed in various colors and treated for different textures, meeting consumer demands for personalized vehicles while maintaining sustainable production standards. This versatility not only appeals to market trends but also reduces the environmental footprint associated with multiple production steps.
Cost-Effective and Eco-Friendly Manufacturing
The cost advantages of plastics cannot be overstated. Lower raw material and processing costs mean that vehicles can be produced more economically without compromising on quality or sustainability. Plastics also allow for rapid production cycles, reducing energy consumption in manufacturing processes. Additionally, innovations in plastic technology continue to drive down costs while increasing the material’s eco-friendliness.
Functional Durability Reducing Environmental Impact
Plastics’ functional characteristics such as corrosion resistance and sound insulation extend the life cycle of automotive components, which contributes to sustainability by delaying landfill waste. For example, plastic fenders and grilles are resistant to rust and corrosion from environmental elements like saltwater, maintaining their integrity over time and reducing the need for replacements.
Furthermore, plastics with sound and heat insulation properties enhance vehicle comfort while improving energy efficiency by minimizing heat transfer and noise pollution. This not only benefits the user experience but also supports broader energy-saving objectives.
The Role of Recyclability in Sustainability
Recycling is a critical component of the sustainability equation, and plastics offer promising opportunities in this area. Automotive manufacturers are increasingly focusing on designing vehicles with end-of-life recyclability in mind. By utilizing thermoplastics that can be melted and reformed, the industry is moving toward a circular economy model that minimizes waste and maximizes resource efficiency.
The push towards using bioplastics derived from renewable sources further enhances the sustainability credentials of plastics in automotive applications. As these materials become more prevalent, they will likely reduce dependency on fossil fuels and contribute to a more sustainable manufacturing ecosystem.
Plastics reduce vehicle weight by 100 kg, saving 0.3-0.6L fuel/100km.True
Lightweight plastics enhance fuel efficiency, cutting emissions.
Bioplastics increase dependency on fossil fuels in car manufacturing.False
Bioplastics reduce fossil fuel use, promoting sustainability.
What Are the Challenges of Using Plastics in Cars?
While plastics offer numerous benefits in car manufacturing, they also present certain challenges that must be addressed.
The challenges of using plastics in cars include environmental concerns, limited recyclability, potential safety issues, and susceptibility to UV damage. Addressing these challenges is crucial for sustainable automotive innovation.
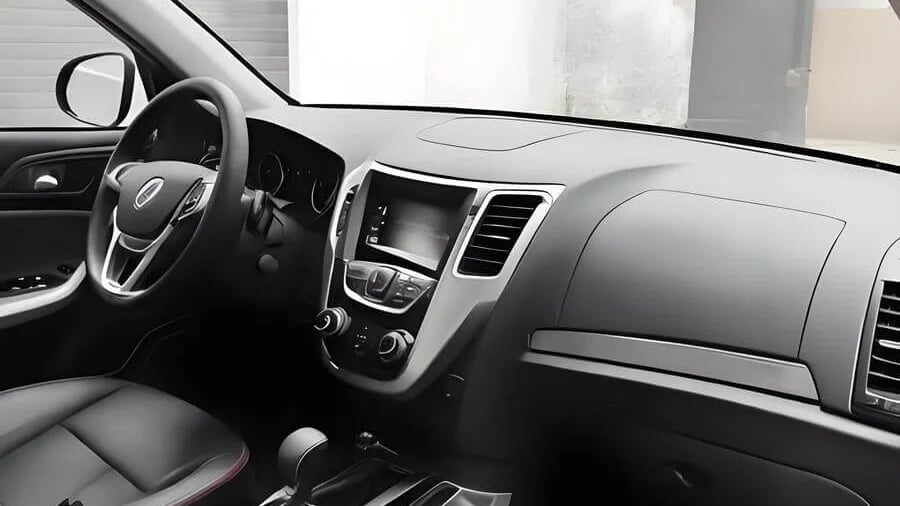
Environmental Impact and Sustainability Concerns
One of the primary challenges of using plastics in cars is their impact on the environment. Plastics are derived from non-renewable fossil fuels, contributing to greenhouse gas emissions during production. Furthermore, the end-of-life disposal of plastic components poses significant ecological concerns. Unlike metals, which are easily recyclable, plastics can be difficult to recycle due to their complex composite nature and contamination issues. This has prompted a greater focus on developing biodegradable plastics9 and enhancing recycling technologies.
Safety Considerations in Automotive Applications
Another concern with using plastics in cars is related to safety. While plastics have good design flexibility, there are instances where their performance under high stress or impact may be less reliable compared to metals. For instance, in a collision, metal parts tend to crumple predictably, absorbing energy efficiently. However, certain plastics may shatter or deform unpredictably, posing potential safety risks. Continuous innovation in composite materials seeks to address these issues by improving the structural integrity of plastic parts.
UV and Temperature Vulnerabilities
Plastics are also vulnerable to UV degradation and temperature fluctuations. Prolonged exposure to sunlight can lead to fading, cracking, and loss of structural integrity in plastic components. This is particularly challenging for exterior parts like bumpers and trims. High temperatures can cause warping or melting, especially in under-the-hood applications where heat resistance is crucial. Manufacturers often incorporate UV stabilizers and heat-resistant additives to mitigate these effects.
Balancing Cost with Performance
While plastics offer cost advantages, there is an ongoing challenge of balancing cost-effectiveness with performance quality. The quest for cheaper production can sometimes lead to compromises on durability or functionality. For instance, cost-cutting measures may result in thinner components that are more prone to wear and tear. The challenge lies in maintaining high standards without escalating costs significantly. Innovations in polymer chemistry are paving the way for enhanced durable plastics10 that meet rigorous automotive standards without breaking the bank.
Future Prospects: Innovation and Adaptation
Despite these challenges, the automotive industry continues to innovate in plastic applications. The development of advanced composites, bio-based polymers, and improved recycling processes offers promising avenues for overcoming current limitations. By addressing these challenges, manufacturers can harness the full potential of plastics while aligning with global sustainability goals.
Plastics in cars are easily recyclable.False
Plastics are difficult to recycle due to complex composites and contamination.
UV exposure affects plastic car parts' durability.True
UV degradation causes fading, cracking, and loss of integrity in plastics.
Conclusion
Embracing plastics in automotive design not only enhances performance but also paves the way for sustainable innovations. Reflect on how you might integrate these insights into future automotive projects.
-
Discover how lighter cars improve fuel efficiency and performance.: Polymers are currently the second most commonly used raw material in vehicle production and make up 20% of overall vehicle weight. ↩
-
Explore how plastics prevent rust and enhance durability.: The plastics that are used to make cars have contributed to more energy efficiency, mainly due to weight reduction, along with corrosion resistance. ↩
-
Understand why polypropylene is vital in car manufacturing.: Polypropylene is a low-density material, as such, it significantly reduces costs and fuel consumption associated with more substantial vehicles. ↩
-
Explore how polycarbonate enhances automotive lighting.: In automotive lighting, we have a long history. In the late 1960s, European sports cars began using LEXAN™ polycarbonate resin for taillights and indicator … ↩
-
Learn why ABS is ideal for car dashboards.: ABS generally offers advanced vehicle control and drops halting distances on dry and some smooth surfaces on loose gravel or snow-covered surfaces. ABS … ↩
-
Discover how polyurethane improves car comfort.: Automotive applications. Polyurethanes are widely used in car manufacture, offering real benefits in terms of comfort, protection and energy conservation. ↩
-
Explore the potential of bio-based plastics in cars.: Some automotive companies are already using bio-based polyesters, bio-based PET and PLA blends in significant quantities for plastic … ↩
-
Explore how lightweight materials improve fuel efficiency and reduce emissions.: Lightweight materials offer great potential for increasing vehicle efficiency. A 10% reduction in vehicle weight can result in a 6%-8% fuel economy improvement. ↩
-
Discover how biodegradable plastics can enhance automotive sustainability.: Some automotive companies are already using bio-based polyesters, bio-based PET and PLA blends in significant quantities for plastic injection … ↩
-
Explore innovations in durable plastics designed for automotive use.: Thermoplastic Olefin (TPO) is a versatile thermoplastic material known for its excellent durability, impact resistance, and UV resistance. ↩