Have you ever wondered how something as simple as a rib can transform an entire design?
Plastic ribs enhance injection-molding design by providing structural support, reducing warping, and enabling thinner walls, thus improving stability, material efficiency, performance, and reducing production costs.
I remember when I first encountered the concept of plastic ribs in my career. It was like discovering a secret ingredient that made everything just work better. These ribs not only bolster the structural integrity but also allow us to innovate with thinner, lighter designs. The journey of understanding their impact on reducing material use while maintaining strength felt like unlocking a new level in my design game. So, let’s dive into how these unassuming components can revolutionize your approach to injection molding.
Plastic ribs reduce warping in injection-molded parts.True
Ribs provide structural support, minimizing deformation during cooling.
Using plastic ribs increases production costs in molding.False
Ribs enhance material efficiency, which typically reduces overall costs.
What Are Plastic Ribs in Injection Molding?
Ever wonder how injection-molded parts manage to be both light and strong? The secret lies in the clever design of plastic ribs, those unsung heroes that add strength without the bulk.
Plastic ribs in injection molding are vertical structures that enhance part strength and rigidity, reduce material usage, improve structural integrity, minimize warping, and boost load-bearing capabilities.
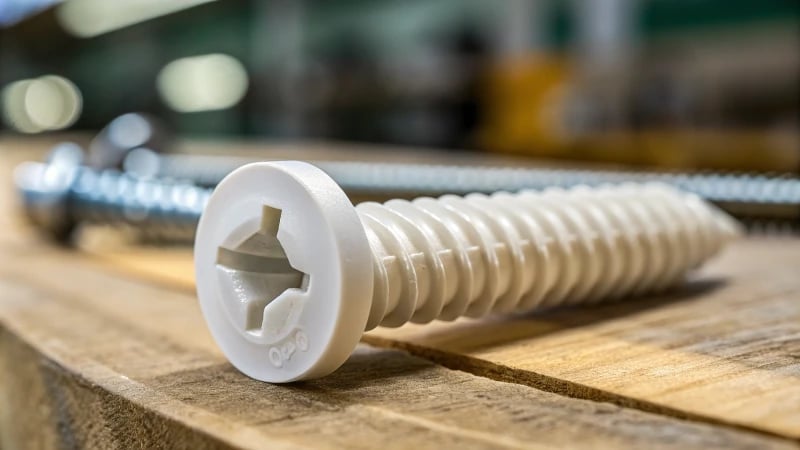
The Role of Plastic Ribs
I remember when I first stumbled into the world of injection molding; it was a maze of techniques and terminologies. But soon enough, I realized the importance of those tiny but mighty plastic ribs. They’re like the supportive beams in a skyscraper, providing much-needed strength without the added weight. These vertical structures inside a molded part make all the difference, especially when you’re trying to balance durability with cost-effectiveness.
Enhancing Structural Integrity
Thinking back to my early projects, I can recall countless times when a part seemed perfect on screen but turned out flimsy in reality. That’s where plastic ribs came to the rescue. By strategically placing these ribs, I could enhance stiffness without overloading on material. This not only kept costs in check but also prevented pesky issues like warping and weight gain. It’s like building a lightweight bridge—strong enough to hold traffic but not so heavy that it collapses under its own weight.
Rib Design Considerations | Description |
---|---|
Height | Should not exceed three times the wall thickness to avoid sink marks |
Thickness | Ideally, 0.5 to 0.7 times the wall thickness to maintain strength |
Draft Angle | Ensures easy removal from molds, typically 0.5 to 1 degree |
Best Practices in Rib Design
Drawing from both my successes and missteps, I’ve learned some valuable lessons in rib design. Proper placement and sizing are paramount to avoiding defects like sink marks or weld lines. I remember one project where ignoring this led to a costly batch of rejects. Now, I ensure rib height1 is just right to prevent surface defects, and rib thickness remains consistent to avoid internal stress.
Potential Pitfalls
Yet, even with the best intentions, mistakes can happen. Oversized ribs can lead to sink marks and other imperfections, which are not just cosmetic nightmares but also weaken the part. It’s crucial to balance rib dimensions with overall design needs, something I’ve come to appreciate through trial and error.
For more detailed insights into rib design, it’s beneficial to explore various case studies and practical applications in the field. Learning from expert opinions2 has been instrumental for me, providing tips on optimizing rib structures across various products.
Understanding these aspects of plastic ribs will empower designers like Jacky to make informed decisions that enhance product durability and performance.
Plastic ribs increase part stiffness without extra material.True
Ribs enhance stiffness by providing support, reducing material use.
Rib height should exceed three times the wall thickness.False
Exceeding this height can cause defects like sink marks.
Why Are Ribs Used Instead of Increasing Wall Thickness?
Ever wondered why ribs are the go-to choice instead of just making walls thicker in product design? It’s all about getting the right mix of strength, material savings, and keeping those pesky molding defects at bay.
Ribs are preferred over thicker walls in plastic design to enhance strength, prevent warpage, reduce material use, lower costs, and improve moldability.
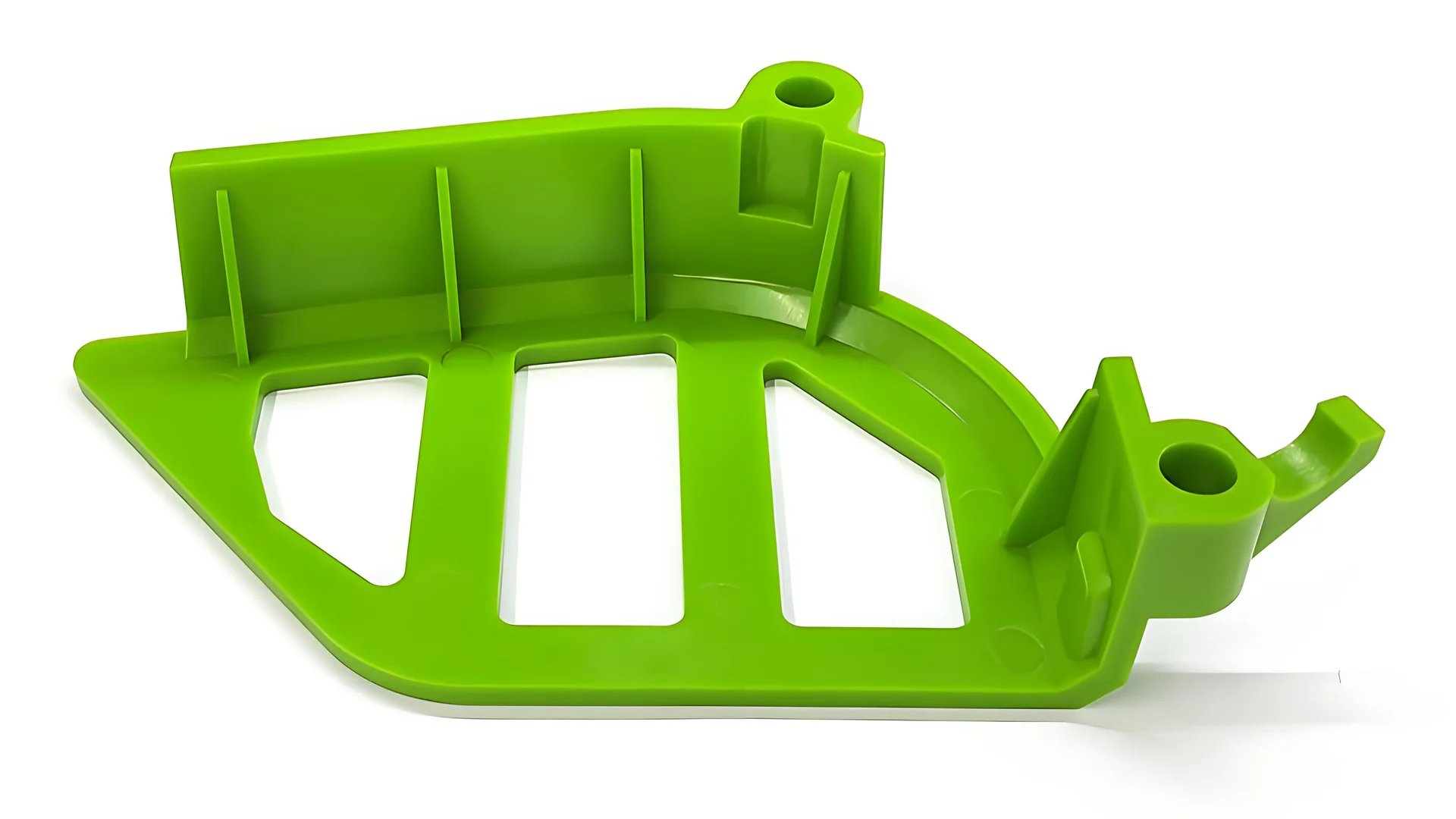
Understanding Structural Integrity
I remember my early days in design, trying to figure out how to make parts stronger without making them heavier or more expensive. It was like solving a puzzle! That’s when I discovered the magic of ribs. These little reinforcements give the component that extra oomph it needs in terms of strength, without the hassles thicker walls bring—like warping and those dreaded sink marks. Using ribs, I found I could distribute stress evenly, which was a game-changer for the quality of my designs.
Material Efficiency and Cost-Effectiveness
One lesson I learned the hard way is that material costs can skyrocket if you’re not careful. By using ribs, I managed to keep those costs in check. Thicker walls just eat up more material and time—both costly in mass production settings3 where every penny counts. The efficiency of ribs means less material is used while still getting the necessary strength. It’s a win-win!
Preventing Defects and Improving Moldability
I used to struggle with cooling inconsistencies leading to defects like warpage. Thicker walls made it worse. But then, I turned to ribs, and it felt like a light bulb moment. Ribs help maintain uniform wall thickness, ensuring even cooling across the part. This greatly enhanced moldability and reduced defect rates in my projects. Trust me, seeing a high-quality part come out without defects is incredibly satisfying.
Table: Comparing Ribs vs. Increased Wall Thickness
Aspect | Ribs | Increased Wall Thickness |
---|---|---|
Material Usage | Lower | Higher |
Structural Strength | Enhanced | Potentially compromised |
Defect Risk | Reduced | Increased |
Production Time | Shorter | Longer due to cooling |
Cost | More economical | More expensive |
Understanding these factors has been crucial in optimizing my designs for performance, cost, and manufacturability. The decision between using ribs and increasing wall thickness often comes down to finding the right balance for specific applications4. Making informed choices has not only improved my designs but also made me more confident in tackling new challenges.
Ribs improve structural integrity over thick walls.True
Ribs distribute stress evenly, enhancing strength without warpage risks.
Thicker walls are more cost-effective than ribs.False
Ribs use less material and reduce cooling time, lowering costs.
What Are the Best Practices for Rib Design in Injection Molding?
I remember my first dive into rib design in injection molding and how mastering these techniques was a game changer. Let’s uncover how to do it right!
Best practices for rib design in injection molding include optimizing rib thickness, height, and draft angles, along with proper spacing and orientation to prevent warping and enhance structural integrity.
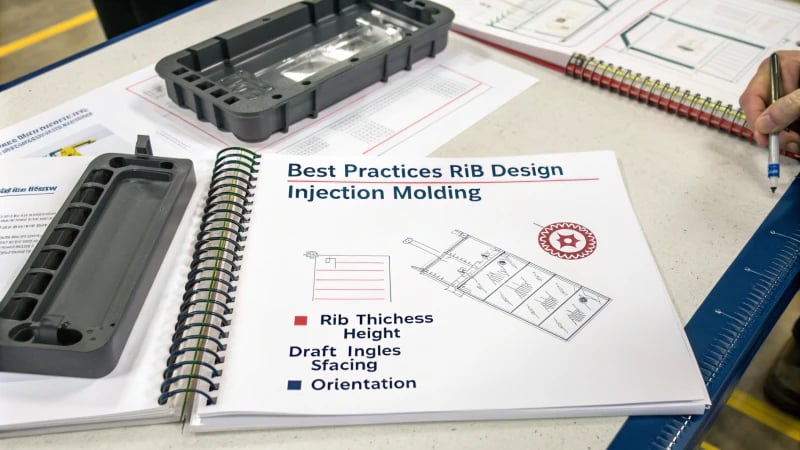
Understanding Rib Thickness
I can’t stress enough how critical getting the rib thickness right is—it’s like the backbone of your design. Ideally, you want the rib thickness to be between 50-70% of your wall thickness. Going overboard can lead to annoying sink marks and those other defects5 that can ruin your day.
Example Table:
Wall Thickness (mm) | Recommended Rib Thickness (mm) |
---|---|
2.0 | 1.0 – 1.4 |
3.0 | 1.5 – 2.1 |
Rib Height Considerations
Rib height is another piece of the puzzle. It adds stiffness without making your design a nightmare to produce. Keep it under three times the wall thickness to avoid stress concentration6. Trust me, going too high can cause more headaches than it’s worth.
Draft Angles and Spacing
Draft angles are your best friends for ensuring your parts pop out of the mold easily. I recommend a gentle draft angle of 0.5° to 1°. As for spacing, think of it like personal space—ribs should be at least twice the wall thickness apart to ensure smooth cooling and flow.
Rib Orientation and Alignment
Aligning ribs in the direction of material flow can make all the difference in strength and stability. It’s like rowing a boat with the current rather than against it. This orientation can significantly reduce filling issues and boost rigidity.
Rib Design Checklist:
- Maintain rib thickness at 50-70% of wall thickness.
- Limit rib height to no more than three times the wall thickness.
- Apply draft angles of 0.5° to 1°.
- Space ribs at least twice the wall thickness apart.
- Align ribs with material flow direction for optimal support.
Embracing these practices not only reduces problems like warping but also enhances the durability and functionality of your injection-molded parts. Don’t hesitate to explore different design strategies7 to take your product’s performance to the next level.
Rib thickness should be 50-70% of wall thickness.True
This range prevents defects like sink marks in injection molding.
Rib height can exceed three times the wall thickness.False
Exceeding this limit leads to stress concentration issues.
How Do Plastic Ribs Impact Material Flow and Cooling?
Ever wondered how those little details in plastic parts can make a big difference? Dive into the world of plastic ribs with me!
Plastic ribs enhance structural integrity and guide material flow in injection molding, impacting cooling and efficiency. They ensure uniform filling, influence cooling rates, and optimize cycle times and part quality.
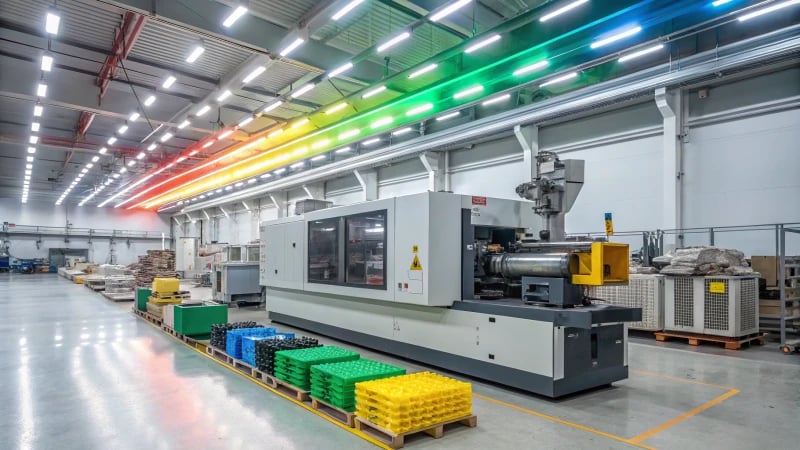
The Role of Plastic Ribs in Material Flow
I remember the first time I encountered the concept of plastic ribs in injection molding. It was during a project where I had to design a casing for a gadget. I learned that ribs are like the unsung heroes in the design—they add strength without much weight. When you place them just right, they guide the molten plastic like a maestro conducting an orchestra, ensuring it fills every nook and cranny.
- Flow Direction: It’s amazing how a well-placed rib can steer the flow within the mold cavity8, preventing issues like air bubbles or incomplete fills. Think of it like setting up a perfect race track for the resin to zoom through.
- Flow Rate: The ribs also dictate how fast the resin moves, shaving precious seconds off the cycle time and boosting production efficiency. It’s like finding that perfect gear shift that lets you cruise effortlessly.
Impact on Cooling Rates
Ribs do more than just guide flow; they also play a pivotal role in cooling. It’s akin to how different thicknesses in a sweater can change how warm you feel.
- Heat Transfer: I’ve had instances where I didn’t account for thicker sections, leading to warping—it’s a real lesson in patience and precision. Managing these sections ensures even cooling.
- Cycle Time: By optimizing rib design, you can achieve faster cooling, reducing cycle times and revving up your production rates.
Designing Optimal Ribs
Balancing structural integrity with process efficiency is crucial. It’s like walking a tightrope—exciting yet challenging. Here’s a quick guide:
Design Aspect | Consideration |
---|---|
Rib Thickness | Should be 50-70% of wall thickness |
Rib Height | Limit to 3 times rib thickness |
Rib Draft Angle | Typically 0.5° to 1° for easy ejection |
By sticking to these guidelines, you can sidestep potential issues and enhance product performance.
Challenges in Rib Design
Designing ribs has its hurdles—like avoiding sink marks and keeping the parts looking sleek.
- Sink Marks: These can be a designer’s nightmare but can be minimized with consistent wall thickness and thoughtful rib placement.
- Aesthetics: It’s all about strategy. Ribs should blend seamlessly, enhancing function without compromising looks. Imagine them as part of the product’s DNA, subtly yet significantly altering its form and function.
For those of us always seeking the cutting edge, delving into rib placement techniques9 can unearth innovative solutions that marry function with form, ensuring our creations are both effective and eye-catching.
Plastic ribs increase injection molding cycle time.False
Ribs can optimize cooling, potentially reducing cycle time.
Proper rib orientation prevents air traps in molds.True
Correct rib placement guides flow, reducing defects like air traps.
Can Plastic Ribs Reduce Production Costs?
Ever wondered if something as simple as plastic ribs could be a game-changer in cutting production costs?
Plastic ribs can lower production costs by minimizing material usage, enhancing structural strength, optimizing injection molding designs, and maintaining product quality.
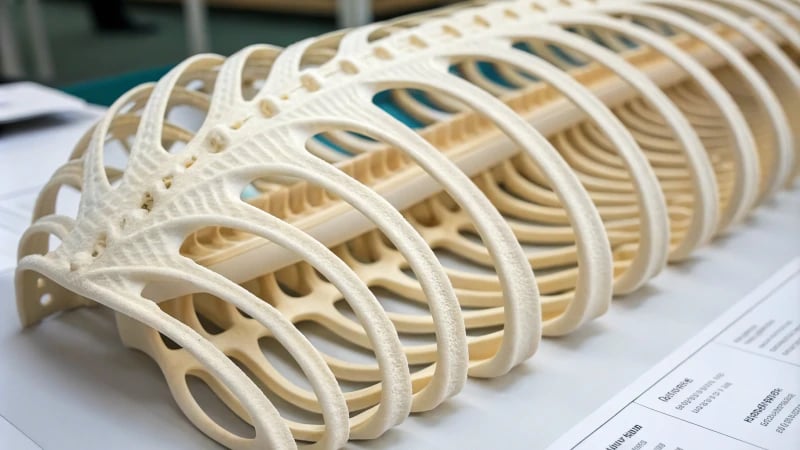
Understanding Plastic Ribs in Design
I remember my first encounter with plastic ribs when I was tasked to redesign a part for a small electronics gadget. Initially, I was skeptical—could these tiny, unseen features really make a difference? But as I dove deeper, I learned that plastic ribs are like the unsung heroes of molded parts. They provide crucial support to thin walls without adding much weight, bolstering stiffness and strength—a must for keeping gadgets durable in our ever-demanding world of consumer electronics.
Material Efficiency
Strategically placing ribs in your design is like finding the secret recipe to Grandma’s legendary pie—once you get it right, the results are spectacular. By using ribs smartly, I discovered we could cut down on raw materials significantly. This isn’t just penny-pinching; in large-scale manufacturing10, even a tiny bit of material saved can add up to big bucks.
Enhancing Structural Integrity
Beyond just cost-saving, plastic ribs are all about fortifying the structure. Imagine having fewer defects in production and less chance of product failure—that’s what ribs bring to the table. One project I worked on involved incorporating ribs to allow for thinner walls. The outcome? Not only did we save on materials, but the end products were lighter, which made them a breeze to ship and handle.
Benefits of Plastic Ribs | Description |
---|---|
Material Savings | Less material leads to reduced costs. |
Strength Enhancement | Increased part strength with minimal weight gain. |
Design Flexibility | More options for complex shapes and forms. |
Best Practices in Rib Design
When it comes to rib design, it’s all about balance. If they’re too thick, you might end up with sink marks or warping—every designer’s nightmare. The golden rule? Keep rib thickness under 60% of the wall thickness.
Incorporating Ribs in CAD Software
With advanced CAD tools11, I can simulate how ribs affect a design before we even start production. This lets me spot potential stress points and tweak the rib design for top-notch performance.
Incorporating ribs has been a game-changer for me and many others in our field. It allows us to meet aesthetic and functional needs while keeping production costs low. Plus, these strategies align with sustainable manufacturing practices—a win-win! So why not experiment with different rib configurations to hit the perfect note on your next project?
Plastic ribs reduce raw material use in manufacturing.True
Strategically placed ribs lower material needs, saving costs.
Rib thickness should exceed 60% of wall thickness for strength.False
Rib thickness should not exceed 60% to avoid defects.
Conclusion
Plastic ribs enhance injection-molding design by providing structural support, reducing warping, and enabling thinner walls, leading to improved performance and lower production costs.
-
Discovering the ideal rib height prevents defects like sink marks, improving part quality. ↩
-
Gain insights from industry experts on effective rib design practices for superior molding outcomes. ↩
-
Discover how ribs offer cost advantages in mass production compared to thicker walls. ↩
-
Explore how the choice between ribs and wall thickness varies by application. ↩
-
This link provides insights into common defects caused by incorrect rib thickness, helping you avoid design pitfalls. ↩
-
Understanding stress concentration effects aids in improving rib design and minimizing structural failures. ↩
-
Explore innovative strategies for rib design that can enhance performance and efficiency in manufacturing. ↩
-
Learn how rib orientation can optimize material flow, preventing defects like air traps and improving mold filling efficiency. ↩
-
Discover innovative rib placement strategies to enhance both part aesthetics and functional performance. ↩
-
Explore how plastic ribs reduce costs in extensive production lines, offering insights into material efficiency and structural improvements. ↩
-
Discover top CAD tools that aid in rib design, helping optimize structural integrity and cost efficiency through simulation. ↩