Do you ever stop and think about the plastic things we use every day? It is very interesting. It’s really cool when you learn how they are created!
Plastic mold products are created by a technique named plastic mold molding. In this process, raw plastic materials transform into shapes using molds. This article explores what these products are and their different kinds. It also explains how manufacturers produce these common items.
As I explore this topic, memories of my first encounter with plastic molding arise. I was amazed when I first learned about plastic mold molding. This process crafts plastic mold products. Raw plastic materials transform into vibrant shapes. It resembles sculpting! These essential items appear in our daily lives. We use them in containers for our favorite snacks. They also form the shells of gadgets that we love.
I invite you to join me. Let us unravel the fascinating world of plastic mold products together. We will explore their diverse uses and the innovative techniques that bring them to life.
Plastic mold products are made using raw plastic materials.True
Plastic mold products are created by shaping raw plastic in molds, confirming the claim's accuracy.
All plastic items are produced through injection molding only.False
Not all plastic items are made via injection molding; other methods exist, making this claim false.
What is the Process of Plastic Injection Molding?
Do you ever think about how plastic things we use each day are created? Plastic injection molding gives life to many of those objects. This process is really interesting and I’m happy to tell you about it!
Plastic injection molding is a method where melted plastic goes into a mold to form different products. This process includes several steps. First, materials are prepared. Next, they are injected with pressure. Then, cooling helps solidify the shape. After that, the finished product is ejected. Finally, post-processing adds finishing touches. This is the complete process.
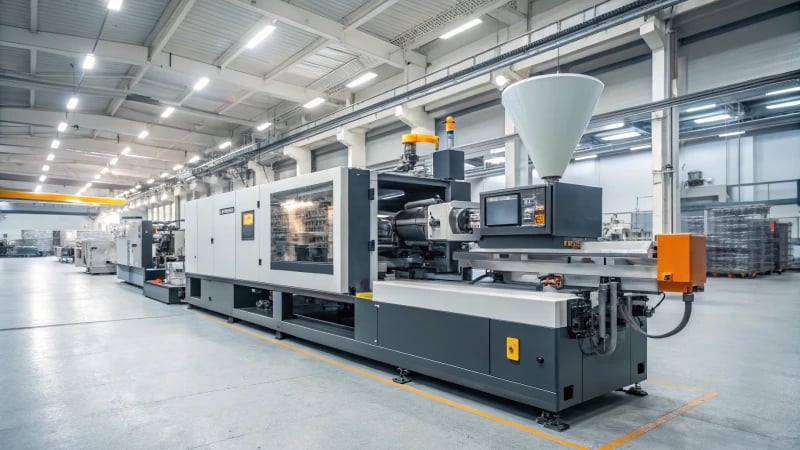
Understanding Plastic Injection Molding
Plastic injection molding amazed me with its efficiency and precision. This process creates plastic products by injecting melted plastic into molds. Imagine it as a magic show where raw materials turn into everyday items. Many industries love it for its flexibility.
Key Steps in the Injection Molding Process:
-
Material Preparation: Plastic raw materials look like colorful grains. They are put into a hopper, heated and melt into a thick liquid. I found it fascinating to see solid materials turn into something that flows!
-
Injection: The melted material is pushed into a mold cavity under high pressure. This step fills every part of the mold. Complex shapes appear from this process. It’s thrilling to watch.
-
Cooling: After injection, plastic cools and solidifies inside the mold. This part decides the final shape and strength. Watching it reminds me of a cake rising. You know something wonderful is coming!
-
Ejection: Once cooled, the mold opens and the product comes out. Ejector pins or plates often help. They give the product a gentle nudge into the world.
-
Post-Processing: Sometimes we cut extra material, paint or put the product together with other parts. This stage adds the final touches, making each item ready for use.
Applications of Plastic Injection Molding
Plastic injection molding has very wide uses. Here are just a few examples to show its flexibility:
Product Type | Examples | Molding Technique |
---|---|---|
Packaging Products | Plastic bottles, containers | Blow molding, injection molding |
Consumer Electronics | Mobile phone shells, tablet cases | Injection molding |
Automotive Parts | Dashboards, bumpers | Injection molding |
Household Items | Furniture, kitchenware | Injection molding |
Industrial Accessories | Gears, pipes | Injection molding |
Benefits of Plastic Injection Molding
This process has many advantages:
- Efficiency: It achieves high production rates with very little waste. I always appreciate this in manufacturing.
- Precision: Producing complex shapes with accuracy impresses me.
- Material Variety: Many types of plastics create an artist’s palette.
- Cost-effectiveness: Automation cuts labor costs, keeping it economical.
If you’re curious about more plus points of plastic injection molding, explore more here! the advantages of plastic injection molding1.
Challenges in Plastic Injection Molding
Yet, there are challenges:
- Initial Setup Costs: Creating molds is expensive. Companies must think carefully before starting.
- Material Limitations: Not all plastics fit injection molding. This can limit design options.
- Cooling Time: It affects production speed. We strive to balance this.
For insights on overcoming these challenges, check out our section on injection molding challenges2.
Understanding each step and its uses helps manufacturers improve their work. They create high-quality plastic products this way. Whether for a simple bottle or a complex car part, plastic injection molding continues to matter in our lives.
Plastic injection molding requires heating plastic to a liquid state.True
The process involves melting plastic raw materials before injecting them into molds, essential for shaping products.
Injection molding is only used for automotive parts production.False
This claim is false; injection molding is used across various industries, including consumer electronics and packaging.
How Do Different Types of Plastic Molds Work?
Have you ever thought about how plastic items are created? Enter the amazing world of plastic molds. Discover how they magically shape the things we love!
Different types of plastic molds use various methods. These include injection molding, blow molding and extrusion molding. Each technique has unique uses and benefits. They play a very important role in product design. They are also essential in manufacturing.
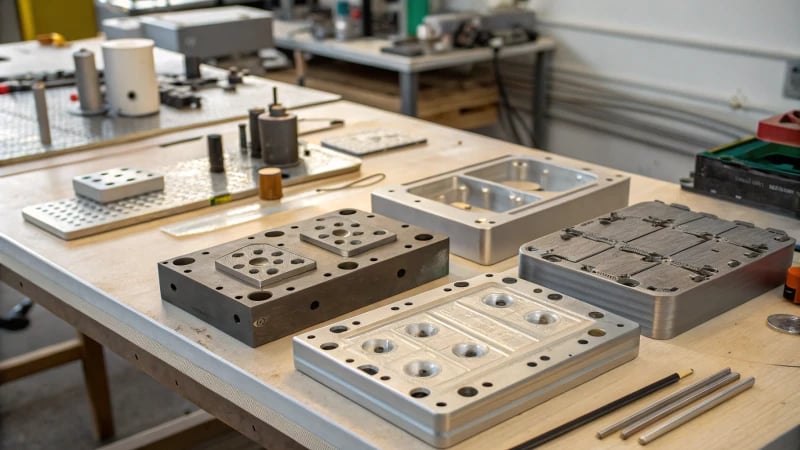
Understanding Plastic Molding Processes
Manufacturing, especially plastic molds, has always amazed me. These important tools form plastic into products we use every day. It’s fascinating to consider the details in creating simple items like a bottle or complex pieces like a phone shell.
Injection Molding
Injection molding is a widely used technique. Raw materials like polyethylene are heated until they melt. The molten plastic is then injected into a mold cavity under high pressure. I once saw a video of this process and it was like witnessing clay turn into a sculpture.
Key Characteristics:
- High precision and consistency
- Good for complex shapes
- Efficient for large productions
Think about mobile phone shells. They require detailed designs to fit buttons and camera openings just right. Molds capture every feature accurately. Really accurate.
Blow Molding
Blow molding is ideal for hollow products. Imagine blowing up a balloon. The process is similar! Hot plastic inflates inside a mold to form containers like bottles.
Common Applications:
- Beverage containers
- Plastic tanks
- Hollow automotive parts
Plastic bottles begin as preforms made through injection molding, then get their final shape in blow molding. It’s hard to believe such a familiar item involves such a detailed process!
Extrusion Molding
Extrusion molding intrigues me. It creates long continuous shapes. Molten plastic presses through a die, like squeezing toothpaste from a tube. This method is efficient for making films, pipes and sheets.
Advantages of Extrusion:
- Cost-effective for large volumes
- Consistent shape cross-sections
- Uses different materials
Plastic films and packaging bags often use this technique. The process starts by heating raw material, then it’s pushed through a die to create thin films or sheets used for packaging.
Compression Molding
Found compression molding fascinating. Plastic material goes in an open mold, shaped by heat and pressure. It’s best for big parts or items that don’t need precision.
Typical Uses:
- Automotive parts (e.g., bumpers)
- Electrical components
- Household items like bowls or plates
Car bumpers, for example, use this method. They’re designed to be strong and durable while looking good too. Very strong.
Rotational Molding
Rotational molding is great for large hollow products. A mold is filled with plastic powder, then rotated. The powder melts and coats the interior as it spins.
Ideal for:
- Large containers (e.g., tanks)
- Playground equipment
- Complex shapes with even wall thickness
This method creates big products that stay strong and uniform. It is very effective.
Summary of Plastic Molding Techniques
Molding Technique | Key Applications | Advantages |
---|---|---|
Injection Molding | Mobile phone shells, consumer electronics | High precision, efficient mass production |
Blow Molding | Beverage containers, hollow parts | Ideal for hollow shapes |
Extrusion Molding | Films, pipes, sheets | Cost-effective for large volumes |
Compression Molding | Automotive parts, household items | Simple and effective for large parts |
Rotational Molding | Large tanks, playground equipment | Creates complex shapes |
Understanding these processes can significantly inform product design choices and manufacturing strategies.
Injection molding is the most common plastic molding technique.True
Injection molding is widely used due to its high precision and efficiency in mass production of intricate designs.
Blow molding is used for producing solid plastic objects.False
Blow molding primarily creates hollow items, such as bottles, by inflating hot plastic inside a mold.
How Are Plastic Mold Products Used Across Different Industries?
Discover with me the intriguing world of plastic mold products. These products play a critical role in many industries. They shape parts of our daily lives.
Plastic mold products are essential in many fields. The automotive industry relies heavily on them. Packaging uses them frequently. Consumer electronics and household items also depend on these products. Their flexible nature makes them important in production. Manufacturing processes benefit from their efficiency.
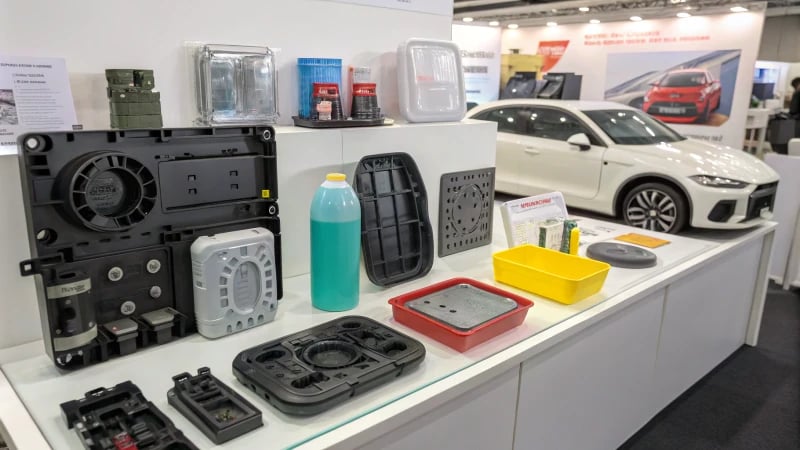
Understanding Plastic Mold Products
When I first learned about plastic mold products, I felt amazed by their versatility. I marveled at the intricate process behind creating them. Plastic mold products emerge from a technique called plastic molding. Imagine raw plastic materials, like tiny pieces of polyethylene or polypropylene. These materials are injected into molds under specific temperature and pressure conditions. After cooling and solidifying, they form distinct shapes and sizes. This process tailors products to meet certain requirements. It feels like magic in manufacturing! Very magical indeed.
Applications Across Various Industries
1. Packaging Industry
The packaging industry often showcases plastic mold products. At grocery stores or during online shopping, these products protect and present items effectively. Here are some common uses:
Product Type | Description | Molding Method |
---|---|---|
Plastic Containers | Used for beverages; made via injection and blow molding processes. | Injection, Blow Molding |
Packaging Bags | Flexible bags for food; produced by extrusion of heated plastic materials. | Extrusion |
These products feel lightweight and transparent, making them ideal for consumer goods.
2. Consumer Electronics
In electronics, plastic molded products matter for appearance and functionality. Unboxing a new smartphone reveals its sleek design. Examples include:
- Mobile Phone Shells: Precise designs shine here. These are usually created via injection molding for a glossy finish.
- Tablet and Headphone Cases: Like phone shells, they demand high standards for durability and appearance.
3. Automotive Industry
The automotive industry greatly benefits from plastic mold products. As a road trip enthusiast, I think about how these parts add to safety and comfort:
- Interior Parts: Dashboards and seats are expertly molded, ensuring comfort and safety.
- Exterior Parts: Car bumpers, important for safety, are crafted from molded plastics to absorb impact effectively.
Part Type | Functionality | Molding Process |
---|---|---|
Interior Dashboard | Offers a smooth finish and houses various controls. | Injection Molding |
Car Bumpers | Provides safety and aesthetic appeal; absorbs impact during collisions. | Injection Molding |
4. Household Items
In my home, plastic mold products make daily life easier:
- Furniture: Lightweight plastic chairs are easy to clean; they come in various designs made via injection molding.
- Kitchenware: Items like cutting boards and bowls must meet food safety standards, being non-toxic and durable.
Household Item Type | Features | Molding Method |
---|---|---|
Plastic Furniture | Lightweight, various designs, easy maintenance | Injection, Extrusion |
Kitchenware | Food-safe materials that are temperature resistant and durable | Injection Molding |
5. Industrial Applications
In industries, plastic mold products are critical:
- Gears and Mechanical Components: Used in machinery where precision is key but extreme accuracy isn’t critical.
- Piping Systems: Durable PVC fittings used in water systems showcase the strength of molded plastics.
Industrial Component | Application | Molding Process |
---|---|---|
Plastic Gears | Widely used in machinery for power transmission | Injection Molding |
PVC Pipes | Essential for construction; strong corrosion resistance | Extrusion |
After exploring these diverse applications, I clearly see that plastic mold products boost productivity and innovation across many sectors. If curious about further exploration into specific uses or benefits of these products, you may want to check out resources about the versatility of plastic molding3. These applications opened my eyes to the ways industries use plastic molding for better production and design.
Plastic mold products are vital for the packaging industry.True
Plastic molds create lightweight and durable packaging, crucial for consumer goods. Their versatility enhances efficiency in production processes across various sectors.
Plastic mold products are not used in consumer electronics.False
This claim is false as plastic mold products are essential for mobile phone shells and other electronic cases, ensuring aesthetic and functional qualities.
What Innovations Are Shaping the Future of Plastic Mold Manufacturing?
The world of plastic mold production amazes me. New technologies change processes. They really inspire fresh creativity. Innovations support sustainability too. This evolution excites many people.
Automation, 3D printing, eco-friendly materials, smart technologies and advanced simulation software shape the future of plastic mold manufacturing. These innovations improve efficiency. They focus on sustainability. This really matters.
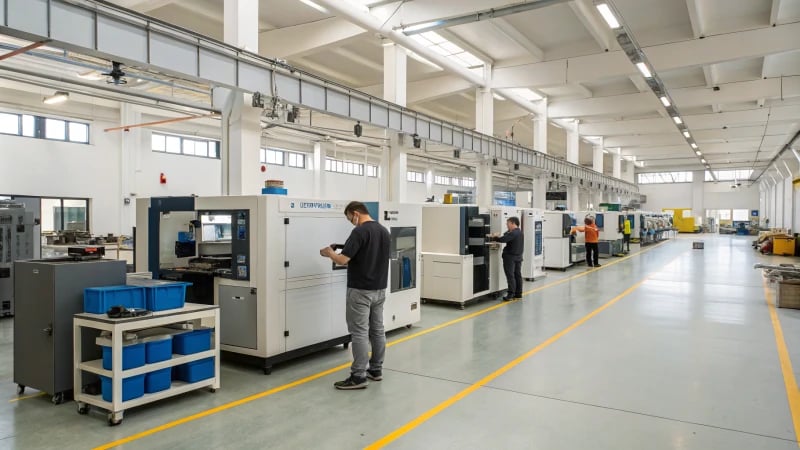
1. Automation and Robotics in Manufacturing
Automation transforms the plastic mold manufacturing world. Robotic systems now control production, making the process smoother and more dependable. I visited a factory where automated injection molding machines worked non-stop. These machines produced perfect parts all day and night. It felt like watching a well-oiled machine. Very impressive! This technology improves efficiency and lowers human errors. Designers like me find this a significant relief. Such advancements help manufacturers adapt quickly to market changes. Fast project turnarounds become possible while keeping quality high.
Learn more about how automation is changing manufacturing4.
2. 3D Printing Technologies
3D printing is the game changer I dreamed of! This technology has changed mold design by allowing fast prototyping. Once, I needed to test several mold designs quickly for a new product. Thanks to 3D printing, we improved our designs in record time. This method really reduces material waste. It offers customized solutions for specific client needs. It’s amazing how 3D-printed molds shorten lead times in product development. What a relief for us designers!
Explore more on 3D printing in mold making5.
3. Eco-friendly Materials and Processes
Sustainability matters deeply to me. I’m very encouraged to see the industry focusing on eco-friendly materials. Learning about biodegradable plastics and recycled materials inspired a sense of responsibility in me. Creating great products means protecting our planet too. Companies now develop processes to cut waste and save energy. They use energy-efficient molding techniques. I saw a project implementing closed-loop systems to recycle plastic scraps. This step towards sustainability attracts environmentally-conscious consumers.
Check out sustainable practices in manufacturing6.
4. Smart Manufacturing Technologies
The rise of smart manufacturing technologies is fascinating. Imagine monitoring equipment and production lines in real-time through IoT devices! This data-driven method lets us optimize processes and predict equipment failures. I visited a plant where smart sensors greatly improved operational efficiency. These innovations allow manufacturers to achieve precision once only imagined. We are really stepping into the future!
Learn how IoT is influencing manufacturing7.
5. Advanced Simulation Software
Simulation software works like magic in mold design! This tool is now essential in my design process. It lets engineers visualize mold performance under different conditions before production. I worked on a complex design where simulation identified potential issues early, saving both time and resources.
Many companies invest in advanced simulation tools using AI for better prediction.
How exciting is that?
Discover the benefits of simulation in mold design8.
Automation increases efficiency in plastic mold manufacturing.True
Robotic systems streamline production, reduce errors, and ensure consistent output, significantly enhancing manufacturing efficiency.
3D printing eliminates the need for prototyping in mold design.False
While 3D printing accelerates prototyping, it does not eliminate its necessity entirely; traditional methods may still be used.
Conclusion
Explore the fascinating world of plastic mold products, their manufacturing processes, and diverse applications across industries such as packaging, consumer electronics, automotive parts, and household items.
-
Gain insights into the plastic injection molding process and its applications, which can enhance your understanding and practical knowledge. ↩
-
Learn about the common challenges faced in plastic injection molding and strategies to overcome them for better production outcomes. ↩
-
Discover in-depth insights about how different industries leverage plastic molded products for their manufacturing needs. ↩
-
Discover how automation is enhancing efficiency in mold manufacturing processes. ↩
-
Find out how 3D printing is revolutionizing prototyping in mold design. ↩
-
Learn about sustainable practices that are making plastic production eco-friendly. ↩
-
Explore how IoT technologies are optimizing manufacturing operations. ↩
-
Understand the importance of simulation software in improving mold design accuracy. ↩