Are you curious about the strength and durability of plastic injection molded parts? You’re not alone!
Yes, plastic injection molded parts can be strong and durable, but their performance largely depends on factors such as the type of plastic used, process parameters during molding, and the design of the mold itself.
While this initial answer is encouraging, the details behind achieving optimal strength and durability are critical. Let’s explore these fascinating aspects together!
Polycarbonate parts are impact resistant.True
Polycarbonate is known for exceptional impact resistance, ideal for stress.
What Types of Plastics Are Best for Strength?
Choosing the right type of plastic is crucial for ensuring the strength of injection molded parts. But which plastics stand out in terms of durability and robustness?
The best types of plastics for strength include engineering plastics like polycarbonate (PC) and nylon (PA), known for their high tensile strength and impact resistance.
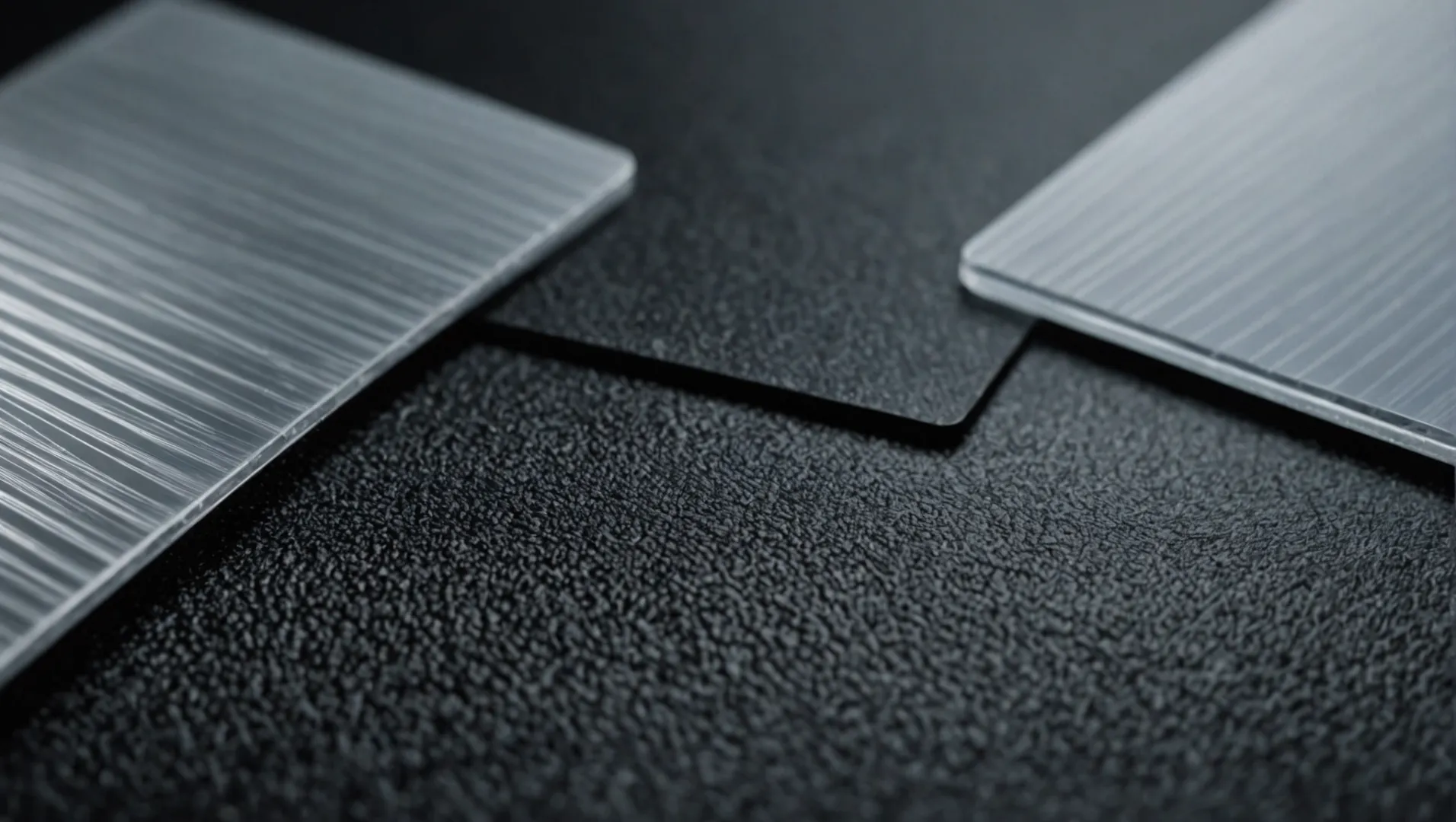
Understanding Engineering Plastics
When discussing plastics for strength1, engineering plastics often top the list due to their impressive mechanical properties. Polycarbonate (PC) and nylon (PA) are two prominent examples:
- Polycarbonate (PC): Known for its exceptional impact resistance, PC is a favorite in applications where durability is key. Its tensile strength ranges from 60-70 MPa, making it ideal for components that need to withstand physical stress.
- Nylon (PA): With tensile strengths between 70-100 MPa depending on the model, nylon offers robust performance in various industrial applications. Its versatility in formulation allows it to be tailored for specific needs.
General Plastics: A Comparison
While engineering plastics are favored for their strength, general plastics like polyethylene (PE) and polypropylene (PP) are more commonly used for less demanding applications due to their lower cost:
Plastic Type | Tensile Strength (MPa) |
---|---|
Polyethylene | 10-30 |
Polypropylene | 30-40 |
These materials can still offer sufficient strength for products that do not require high impact resistance.
Enhancements Through Modifications
Beyond the base material, the strength of plastics can be significantly enhanced through modifications. Reinforcements2 like glass or carbon fibers can boost the tensile strength of plastics dramatically. For instance, glass fiber-reinforced nylon can reach tensile strengths of 150-200 MPa or higher. Such enhancements make plastics suitable for high-stress applications.
Other fillers, such as talcum powder or calcium carbonate, can also contribute to increased strength, although the effects are generally more moderate compared to fiber reinforcements.
Considerations for Selection
When selecting plastics for strength, consider the specific requirements of your application. Factors like temperature resistance3, chemical exposure, and mechanical stress must guide your choice. Balancing these elements with the cost will ensure an optimal material selection that meets both performance and budget constraints.
Polycarbonate has a tensile strength of 60-70 MPa.True
Polycarbonate is noted for its exceptional impact resistance and tensile strength.
Polyethylene has higher tensile strength than nylon.False
Nylon's tensile strength exceeds that of polyethylene, which ranges from 10-30 MPa.
How Do Molding Parameters Affect Durability?
When it comes to injection molding, the parameters you choose can make or break the durability of your final product. Understanding these parameters is crucial for ensuring long-lasting parts.
Molding parameters such as temperature, pressure, and cooling time play a pivotal role in the durability of plastic parts. Optimal settings ensure proper molecular alignment and reduce internal stresses, resulting in stronger and more durable products.

The Role of Temperature
The temperature used during injection molding is a critical parameter that significantly affects the durability of the final product. Different plastics require specific temperature ranges to achieve optimal melting and molecular alignment. For instance, polycarbonate requires temperatures between 260-320°C to melt properly, ensuring that the molecular chains are arranged in a way that maximizes strength. A temperature that’s too high or too low could lead to defects such as weak spots or stress fractures.
Pressure and Speed Dynamics
Injection pressure and speed are equally vital in determining the durability of molded parts. High injection pressure ensures that the material fills the mold completely and densely, minimizing internal voids and defects. However, excessive pressure can break molecular chains, compromising strength. For example, polypropylene might require adjustments in pressure and speed to maintain its integrity.
Importance of Cooling Time
Cooling time is often an overlooked aspect that can greatly influence durability. Proper cooling allows the plastic to solidify without internal stresses, which could lead to cracking or warping over time. Extending the cooling period can enhance strength by allowing for even stress distribution within the part.
Practical Application: A Case Study
Consider a scenario involving nylon, a material known for its strength and versatility. By adjusting the injection parameters—ensuring a precise temperature range and optimal cooling time—the tensile strength of nylon parts can be increased to between 70-100MPa. This demonstrates how meticulous control over molding conditions directly correlates with enhanced durability.
To further understand these dynamics, explore how different plastics respond4 to varying molding parameters and their impacts on product life cycle.
Temperature affects plastic part durability.True
Proper temperature ensures optimal melting and molecular alignment, enhancing strength.
Excessive injection pressure improves durability.False
Too much pressure can break molecular chains, reducing strength.
Why Is Mold Design Crucial for Strength?
Mold design plays a pivotal role in determining the strength of plastic injection molded parts, impacting everything from material flow to final product integrity.
Mold design is crucial for strength as it ensures uniform material flow, reduces defects, and optimizes gate placement, directly affecting the integrity and performance of the final product.
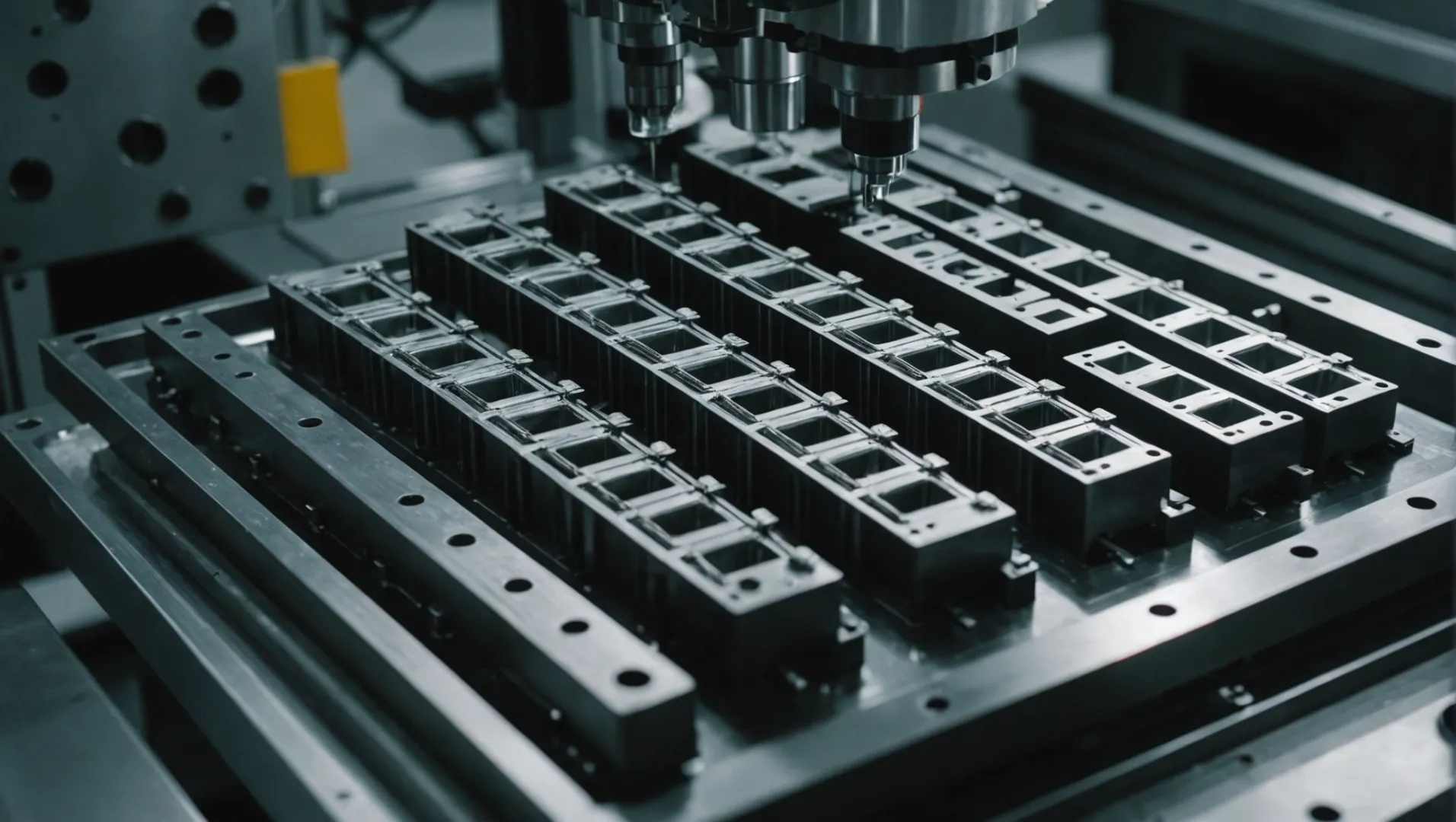
The Role of Mold Structure and Size
A well-designed mold structure is essential for maintaining the strength of injection molded parts. A uniform flow of material5 throughout the mold prevents common defects like short shots and flash, which can compromise the part’s integrity. The size and structure of the mold need to be carefully planned to ensure that the material fills every cavity evenly, minimizing stress concentrations that could weaken the part.
The position, number, and size of mold gates also play a critical role. Multi-point gates, for example, can help distribute the plastic more uniformly across the mold. This distribution reduces stress concentrations, thereby enhancing the overall strength of the part. Here’s a simplified table illustrating the impact of gate placement:
Gate Configuration | Impact on Strength |
---|---|
Single-point gate | Higher stress concentration, lower strength potential |
Multi-point gate | Reduced stress concentration, higher strength potential |
Importance of Surface Quality
The surface quality of the mold impacts not only the appearance but also the strength of the final product. A smooth mold surface reduces friction between the plastic and mold during demolding, which helps maintain structural integrity by minimizing surface defects. These defects can act as stress concentrators, leading to premature failure under load.
Balancing Complexity and Functionality
While designing a mold, engineers must balance complexity with functionality. Complex molds can offer greater strength by ensuring even distribution and accommodating intricate designs. However, increased complexity can also introduce challenges in manufacturing and maintenance. Thus, understanding when to incorporate complexity is crucial.
Enhancing Strength with Proper Cooling Channels
Effective cooling channels within the mold are vital for maintaining part strength. Proper cooling prevents warping and shrinkage, which are common issues that can lead to weaknesses in the final product. By optimizing the cooling process, manufacturers can enhance the density and uniformity of the molded parts.
In summary, mold design is a multifaceted element in injection molding that directly influences part strength. By considering factors like material flow, gate placement, surface quality, complexity balance, and cooling efficiency, manufacturers can significantly enhance the structural integrity of their products.
Uniform material flow prevents weak spots in molded parts.True
Ensures even distribution, reducing stress concentrations.
Single-point gates enhance the strength of molded parts.False
They increase stress concentration, reducing strength potential.
Can Reinforcement Improve Plastic Strength?
Ever wondered how reinforcing plastics could alter their strength and performance? Let’s delve into this fascinating process and its impacts.
Yes, reinforcement can significantly improve the strength of plastic by incorporating materials such as glass fiber or carbon fiber. These additives enhance tensile strength and durability, making plastics suitable for more demanding applications.
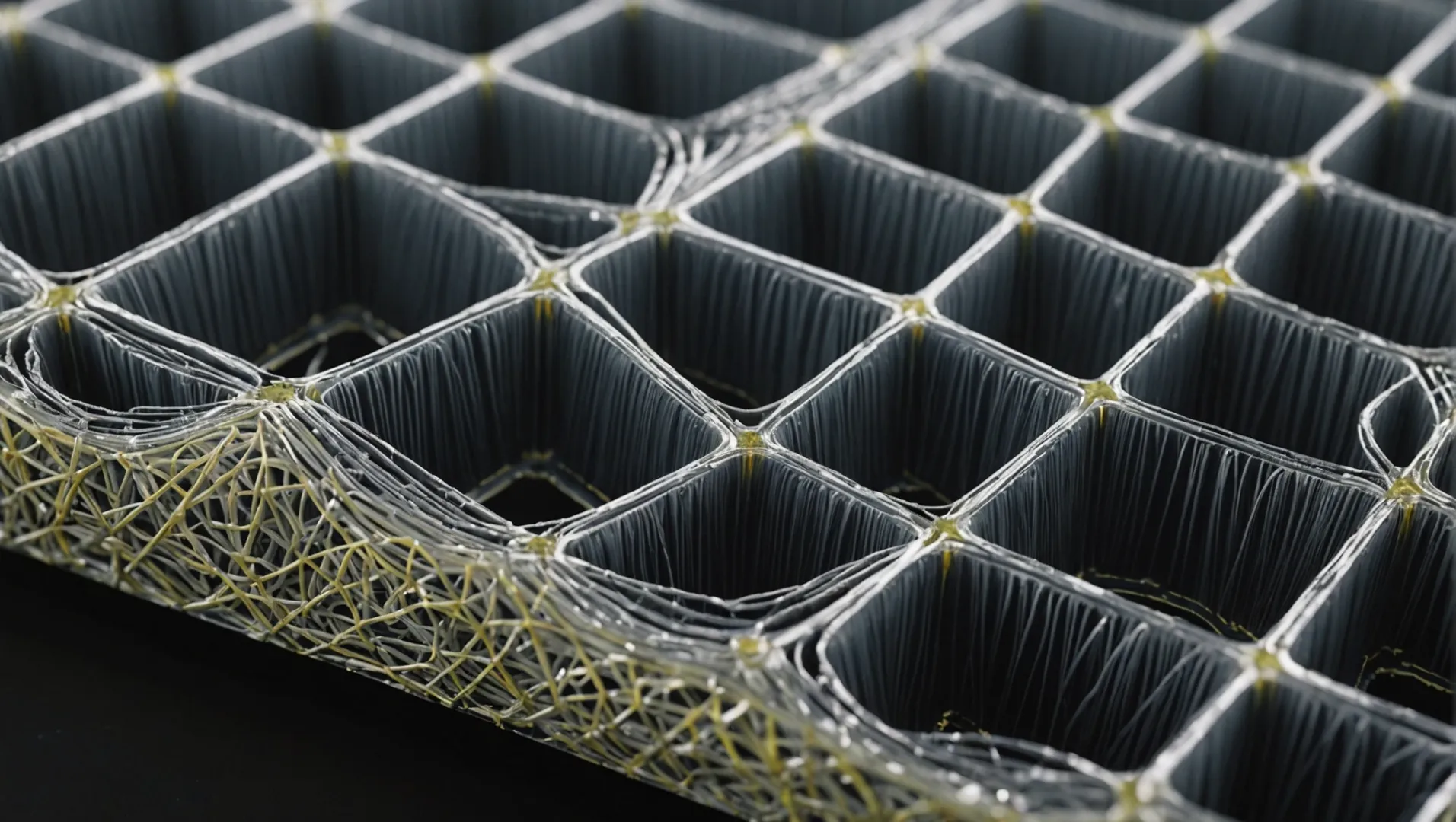
Understanding Reinforcement in Plastics
Reinforcing plastics involves embedding fibers or fillers within the polymer matrix to enhance its mechanical properties. This process can transform ordinary plastics into high-performance materials capable of withstanding greater stresses.
Types of Reinforcing Materials
-
Glass Fiber:
- Benefits: Glass fiber is commonly used due to its high tensile strength and affordable cost. When added to nylon, it can boost tensile strength from 70-100MPa to an impressive 150-200MPa.
- Applications: Ideal for automotive components and structural parts where strength and rigidity are critical.
-
Carbon Fiber:
- Benefits: Though more expensive, carbon fiber offers superior strength-to-weight ratio and thermal stability.
- Applications: Used in aerospace, sporting goods, and premium automotive sectors.
-
Other Fillers:
- Talcum powder and calcium carbonate can also enhance strength but to a lesser extent compared to fibers. These fillers are more about cost-effectiveness than performance enhancement.
Material | Strength Increase | Typical Applications |
---|---|---|
Glass Fiber | Up to 200MPa | Automotive, Structural Parts |
Carbon Fiber | Varies (Superior) | Aerospace, Sports Equipment |
Talcum Powder | Moderate | Cost-sensitive applications |
The Science Behind Reinforcement
Reinforcement works by distributing the load more evenly across the plastic matrix, thus reducing stress concentrations. This distribution is key to achieving enhanced performance in reinforced plastics.
How It Affects Properties:
- Tensile Strength: The introduction of fibers increases tensile strength by creating a network that supports the plastic under tension.
- Impact Resistance: Reinforced plastics exhibit better impact resistance, crucial for applications subjected to sudden loads or shocks.
- Thermal Stability: Adding materials like carbon fiber can improve thermal performance, making plastics viable for high-temperature environments.
Challenges and Considerations
While reinforcement offers significant benefits, it also presents challenges:
- Cost Implications: High-performance fibers like carbon are expensive.
- Process Adjustments: Modifying injection molding parameters is essential to accommodate the altered flow characteristics of reinforced plastics.
- Design Changes: Molds may require redesigning to optimize the distribution of reinforcing materials, ensuring uniformity and preventing defects.
By understanding these factors, manufacturers can strategically use reinforcement to develop stronger, more durable plastic components, expanding their application possibilities.
Real-World Applications of Reinforced Plastics
Reinforced plastics have revolutionized industries by offering tailored solutions that balance performance and cost. For instance:
- In the automotive industry, reinforced plastics reduce vehicle weight without compromising safety, enhancing fuel efficiency.
- In consumer electronics, they provide robustness while maintaining lightweight designs essential for portability.
In conclusion, while reinforcement can markedly improve plastic strength, careful consideration of materials, costs, and design modifications is crucial for success in various applications. Explore More on Reinforced Plastics6.
Glass fiber can double the tensile strength of nylon.True
Glass fiber increases nylon's tensile strength from 70-100MPa to 150-200MPa.
Carbon fiber is more cost-effective than glass fiber.False
Carbon fiber is more expensive due to its superior properties.
Conclusion
To ensure strong and durable plastic injection molded parts, consider material choice, molding process, and mold design—these elements collectively influence performance.
-
Explore why engineering plastics like PC and PA are highly regarded.: PAI – Polyamideimide (PAI) boasts the highest tensile strength of any plastic at 21,000 psi. This high performance plastic has the highest strength of any … ↩
-
Understand how fiber reinforcements enhance plastic strength.: Advantages of Fiberglass · High strength · Corrosion resistant · Light in weight · Non conductive · Electro-magnetic transparency · Maintenance free · Easy to … ↩
-
Learn about the importance of temperature resistance in material selection.: A thermoplastic’s chemical and heat resistance can be equal to or better than a thermoset’s. Here are five plastics that can handle the heat. ↩
-
Discover how plastics behave under varied molding conditions to enhance durability.: Different plastics respond distinctively to parameter changes, making it essential to understand their characteristics for optimal parameter … ↩
-
Ensures even distribution, preventing weak spots in molded parts.: The material in the center takes longer to cool. The increase in thickness increases the cooling time and Shrinkage. ↩
-
Learn more about how reinforcement transforms plastic properties.: Reinforcements, as the name suggests, are used to enhance the mechanical properties of a plastic. Finely divided silica, carbon black, talc, mica, and calcium … ↩