Ever wonder how the gears that power our gadgets are made? Dive into the fascinating world of plastic gear manufacturing!
Plastic gears are made via injection molding, injecting molten plastic into molds for cooling and solidification, ideal for precise, intricate, and repeatable mass production.
Remember the first time I watched an injection molding machine in action? It was mesmerizing to see molten plastic transform into something so precise and useful. This method’s magic lies in its ability to turn complex designs into reality with such ease. But there’s more to it than just watching plastic flow into molds. Choosing the right materials and overcoming design challenges are key to ensuring your project succeeds. Injection molding isn’t just a process; it’s a craft, and mastering it can truly elevate your designs. So, let’s delve deeper and uncover how embracing this technique can be a game-changer for your projects.
Injection molding is used for manufacturing plastic gears.True
Injection molding allows for precise, repeatable production of complex gear shapes.
Plastic gears cannot be produced with high precision.False
Injection molding enables the creation of gears with high precision and repeatability.
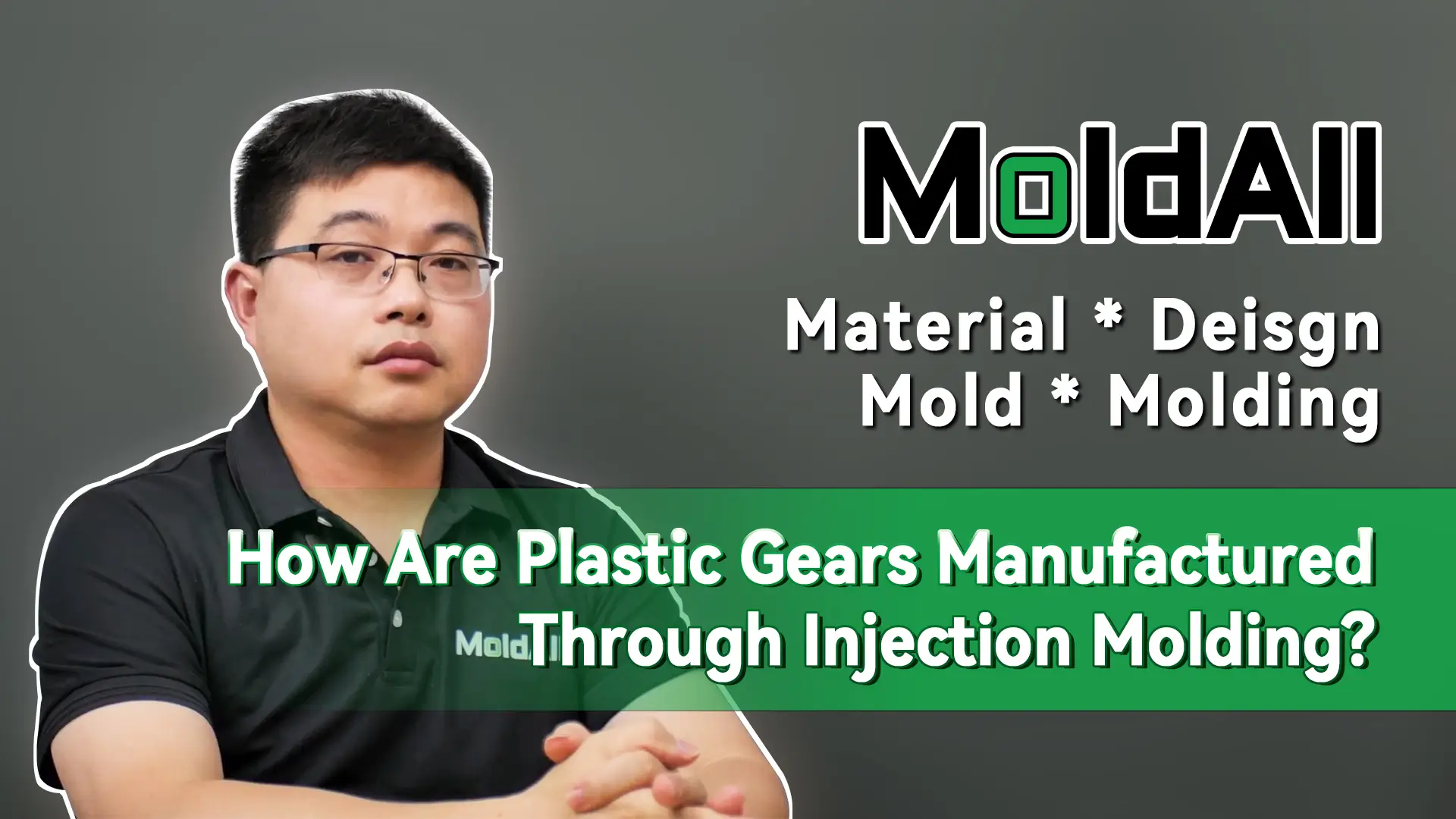
What Materials Are Best for Injection Molded Plastic Gears?
Choosing the right material for injection molded plastic gears can feel like picking a favorite child—it’s all about balance.
Acetal, nylon, and polycarbonate are ideal for injection molded plastic gears, offering a balance of strength, durability, and cost-effectiveness. Each material provides unique advantages tailored to specific performance and efficiency requirements.
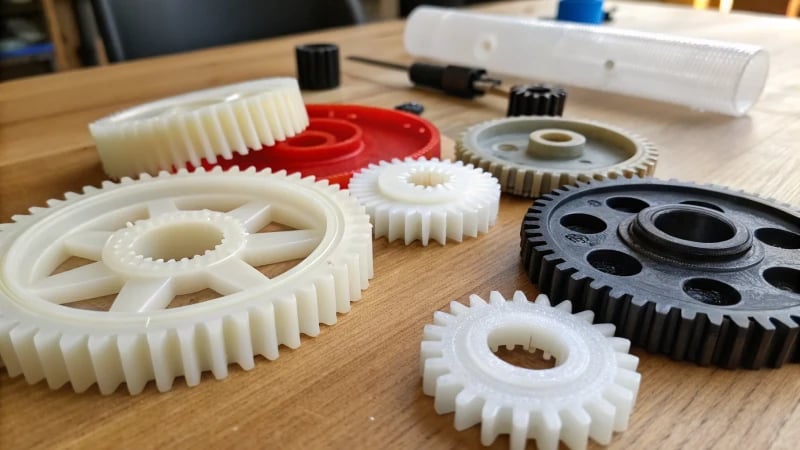
Understanding Material Properties
I remember the first time I had to choose a material for a plastic gear design; it felt a bit like standing at a crossroads with three paths leading into the unknown. Would I pick the right one? When you’re diving into the world of injection molded plastic gears, understanding material properties is your compass.
-
Acetal: This was my go-to for a project requiring precision. It’s known for its low friction1 and high stiffness, making it ideal for those intricate gears where every detail counts.
-
Nylon: I once worked on a design that had to withstand intense vibrations. Nylon came through with its excellent wear resistance and ability to handle higher loads, perfect for vibration absorption2.
-
Polycarbonate: Though not always my first choice, polycarbonate amazed me with its impact resistance and clarity—especially handy in transparent applications3.
Comparing Performance in Different Conditions
I learned the hard way that not all materials perform equally under pressure. Here’s a quick look at how they stack up:
Material | Heat Resistance | Moisture Absorption | Cost |
---|---|---|---|
Acetal | Moderate | Low | $$ |
Nylon | High | High | $ |
Polycarbonate | High | Low | $$$ |
This table became my quick-reference guide, helping me pinpoint the best material based on environmental conditions. Sometimes it felt like a game of chess, strategically deciding which piece to move.
Applications and Industry Examples
Every industry has its own love affair with these materials:
-
Automotive: I’ve seen nylon gears used time and again because they can withstand the high temperatures and vibrations typical of automotive environments.
-
Consumer Electronics: When precision and low noise were priorities, acetal proved its worth in performance4.
-
Medical Devices: Polycarbonate’s clarity and sterilization compatibility made it a winner in many medical applications.
Navigating through these choices reminds me of how consulting with material suppliers or using CAD simulations can be game-changers. It’s about making informed decisions that align with the specific needs of each project. Just like finding the perfect piece in a jigsaw puzzle, it all fits together eventually.
Acetal gears are ideal for high-precision applications.True
Acetal's low friction and high stiffness make it suitable for precision.
Nylon gears have low moisture absorption compared to acetal.False
Nylon has high moisture absorption, unlike acetal which absorbs less.
How Does the Injection Molding Process Work for Gears?
Ever wondered how those tiny gears in your gadgets come to life? Let me take you on a journey through the fascinating world of injection molding.
Injection molding for gears involves melting plastic pellets, injecting them into a gear-shaped mold, and ejecting the solidified gear. This process ensures precision and efficiency in producing complex gear shapes.
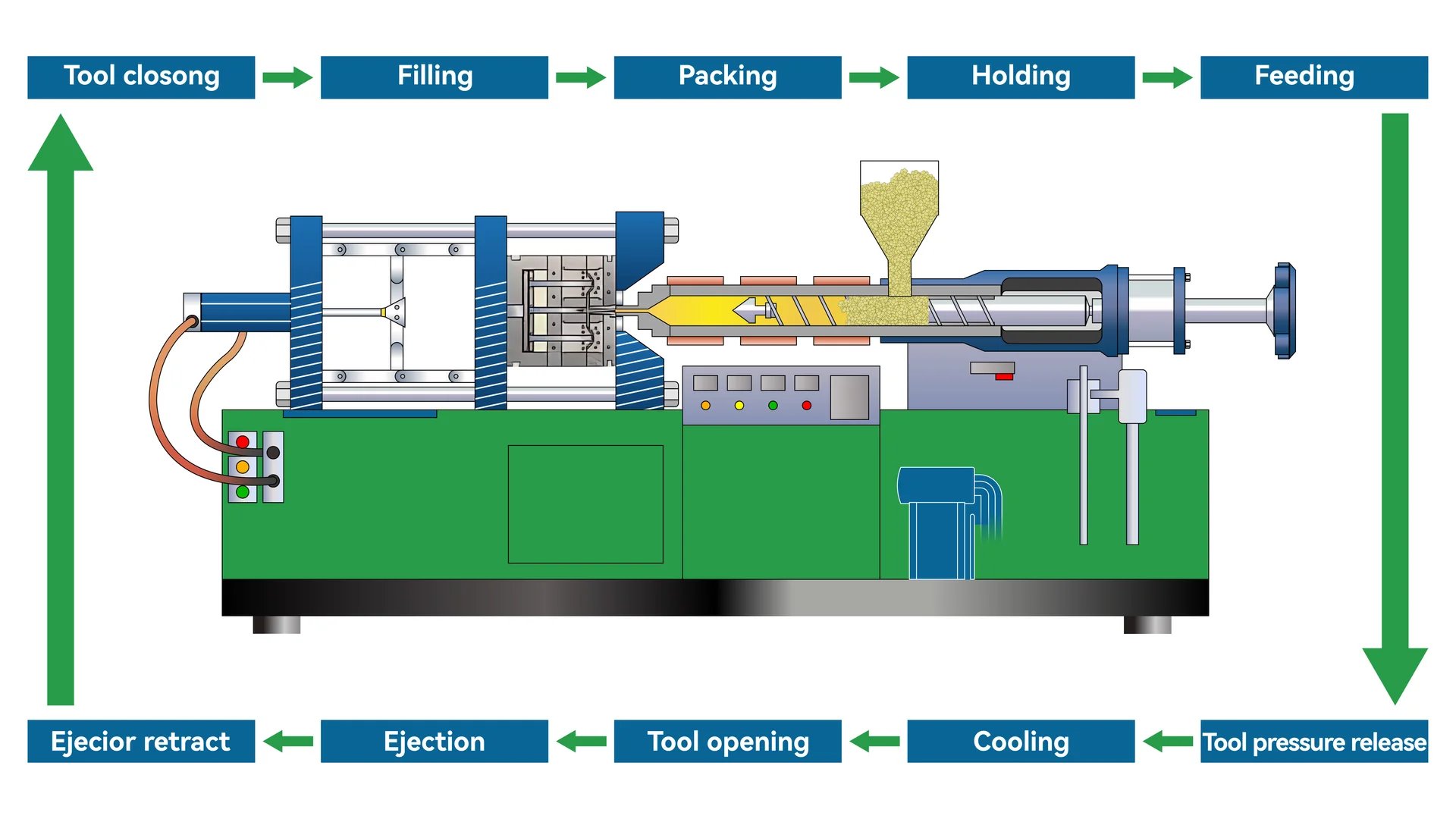
Understanding the Injection Molding Cycle
Whenever I think about the process of injection molding, I’m reminded of when I first saw it in action on a bustling factory floor. The hum of the machines, the rhythmic clamping and unclamping—it was like witnessing a symphony of engineering. Here’s how it works for gears:
Steps Involved
- Clamping: Imagine securing a treasure chest. The mold closes tightly, ready to shape our gear.
- Injection: The molten plastic rushes in, much like filling a mold for a cake, ensuring every detail is captured.
- Cooling: Patience here is key. It’s like waiting for chocolate to set—solidifying into the perfect form.
- Ejection: The final moment when the gear emerges, ready to turn dreams into reality.
Material Considerations for Gears
I recall once experimenting with different materials, eager to find that perfect blend of strength and flexibility for gears. Plastics like Nylon and Polyacetal often win out due to their remarkable durability and low friction properties. For those interested in the nitty-gritty comparisons, check out these plastic material properties5.
Advantages of Injection Molding for Gears
I’ve always been fascinated by how injection molding marries precision with efficiency. The ability to produce complex geometries with consistent quality feels almost magical. Plus, it’s cost-effective—cutting down on waste and labor compared to traditional machining methods. Discover more in our advantages guide6.
Challenges and Solutions
Of course, no method is without its challenges. Material shrinkage and mold wear can be tricky hurdles. But with advanced simulation software, I’ve seen how we can predict and tackle these issues head-on before production starts. For more insights, dive into our mold design resources7.
Comparing Injection Molding to Other Methods
I often get asked how injection molding stacks up against machining or 3D printing. Each has its merits:
- Machining: Perfect for small batches but watch out for those high costs.
- 3D Printing: Great for flexibility but sometimes lacks the precision you’d need.
For a clearer picture, see our detailed manufacturing comparison chart8.
Method | Precision | Cost | Flexibility |
---|---|---|---|
Injection Molding | High | Low | Moderate |
Machining | Very High | High | Low |
3D Printing | Medium | Medium | High |
By grasping these aspects, we as engineers can choose the most fitting manufacturing process for our unique gear designs.
Injection molding uses a screw-type plunger for injection.True
A screw-type plunger is used to inject molten plastic into the mold.
3D printing offers higher precision than injection molding.False
Injection molding achieves higher precision compared to 3D printing.
Why Choose Injection Molding Over Other Methods?
Have you ever wondered why injection molding is the go-to method for creating those intricate plastic parts we use every day?
Injection molding is favored for its precision, speed, cost-effectiveness, adaptability to materials, and capability to create complex designs, making it ideal for large-scale production.
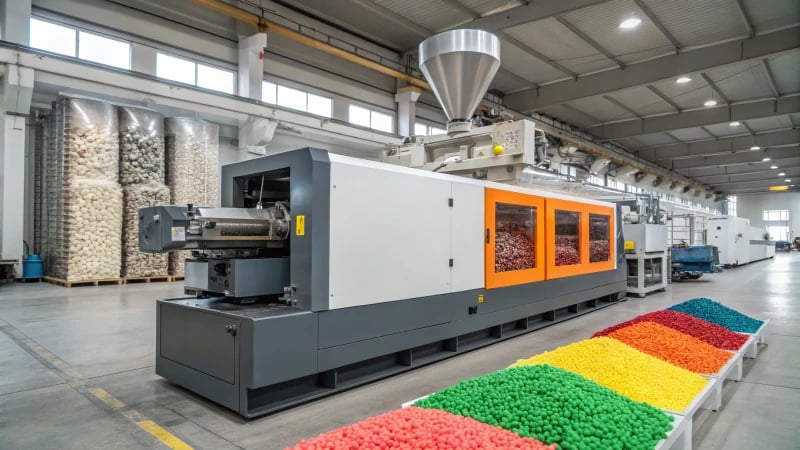
Precision and Complexity
You know, precision is like the holy grail of manufacturing. Back when I was just starting out, I remember the frustration of getting parts just a hair off from the required specifications. Injection molding completely transformed that experience for me. It can handle the most intricate designs, which is a lifesaver in fields like electronics and healthcare where accuracy is non-negotiable. With injection molding, tight tolerances are achievable, ensuring consistent quality even in large batches9 of products.
Cost Efficiency for Large Scale Production
When I first considered injection molding, the initial setup cost made me pause. But then I realized that once you get past that initial investment in mold creation, the savings kick in massively with each unit produced. It’s like buying in bulk—the more you make, the less each one costs. So if you’re looking at producing millions of units10, this method really does keep the budget in check.
Feature | Injection Molding | Other Methods |
---|---|---|
Precision | High | Variable |
Production Speed | Fast | Moderate |
Material Versatility | Extensive | Limited |
Cost Efficiency | High (in large volumes) | Moderate |
Versatility in Material Use
One aspect that really drew me to injection molding was its versatility in material use. Whether you need something incredibly durable or something with a bit more flexibility, there’s likely a thermoplastic or polymer that fits the bill. This flexibility means I can tailor my designs to meet specific requirements like durability and flexibility11, which has been a game-changer for many of my projects.
High Production Speed
Let’s talk speed—because in today’s competitive market, time is money. Injection molding’s fast production cycles mean you can churn out thousands of parts in no time. I remember the relief of hitting tight deadlines thanks to this process. Plus, with automation on our side, productivity only goes up.
Capability for Complex Designs
Now, if you’re anything like me, pushing the boundaries of design is part of the fun. Injection molding lets me explore complex shapes that would be a nightmare—or downright impossible—with other methods like CNC machining or 3D printing. This method opens doors to design innovations that keep my work fresh and exciting.
Injection molding allows for high precision in complex parts.True
Injection molding can achieve tight tolerances, ensuring precision.
Injection molding is less cost-effective for small production runs.True
High initial setup costs make it less economical for small volumes.
What Challenges Might Arise in Manufacturing Plastic Gears?
Remember the time you tried to build that perfect model, but it just didn’t work out? That’s a bit like crafting plastic gears—full of potential yet tricky!
Manufacturing plastic gears involves challenges like selecting the right material, ensuring dimensional stability, and enhancing wear resistance, all crucial for optimal performance and durability, necessitating careful design and production planning.
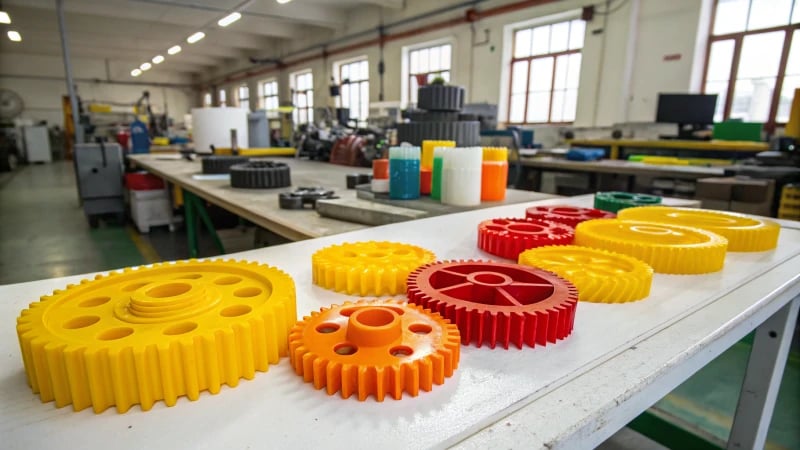
Material Selection Dilemma
I once faced a tough decision while working on a small project. It reminded me of selecting materials for plastic gears, where each choice brings its own pros and cons. Plastics like nylon12 and polycarbonate13 have unique properties that affect the gear’s strength and flexibility. Choosing poorly can spell disaster, leading to gears that wear out faster than expected.
Material Comparison Table
Material | Strength | Flexibility | Cost |
---|---|---|---|
Nylon | High | Moderate | $$ |
Polycarbonate | Medium | High | $$$ |
Dimensional Stability Issues
There’s nothing worse than your carefully crafted gear failing because it expands or shrinks with the temperature. This reminds me of a summer camping trip where nothing fit right in the heat! Plastic gears can suffer from similar dimensional shifts, messing up gear meshing and causing performance hiccups. It’s vital to factor in environmental impacts right from the design phase to keep everything running smoothly. Consideration of environmental factors during the design phase is vital for maintaining dimensional accuracy14.
Wear Resistance Concerns
Plastic gears might not be as rugged as their metal counterparts, kind of like comparing a light jacket to a winter coat in a snowstorm. Their wear resistance isn’t as robust, so designers often have to get creative with lubricants or tweak designs to make them last longer. Understanding how different plastics handle stress is key to sidestepping excessive wear problems15.
Mold Design Challenges
Creating precise molds for plastic gears can feel like putting together an intricate puzzle. One wrong piece, and the whole picture is off. Any tiny flaw in the mold could result in defects that throw off gear function completely. I’ve learned that paying close attention to mold design16 is crucial for quality and consistency.
Noise and Vibration Problems
Imagine driving down a bumpy road—it’s noisy and uncomfortable! Plastic gears can be like that under high loads, creating noise and vibrations. Addressing these issues requires clever design tweaks or material changes to significantly boost gear performance17.
By tackling these challenges during design and manufacturing, we can enhance the performance and durability of plastic gears, ensuring they fit seamlessly into their intended applications.
Nylon gears have higher flexibility than polycarbonate gears.False
Nylon has moderate flexibility, while polycarbonate has high flexibility.
Temperature changes can affect plastic gear dimensions.True
Plastic gears can suffer dimensional changes due to temperature fluctuations.
Conclusion
Plastic gears are manufactured through injection molding, which allows for precise, cost-effective production of complex shapes using materials like acetal, nylon, and polycarbonate.
-
Discover why acetal’s low friction makes it ideal for high-precision gear applications. ↩
-
Learn how nylon’s vibration absorption benefits automotive applications. ↩
-
Explore how polycarbonate’s transparency is advantageous in medical devices. ↩
-
Understand how acetal reduces noise in consumer electronics gear systems. ↩
-
Explore differences between Nylon and Polyacetal to choose the best material for your gears. ↩
-
Discover how injection molding benefits gear manufacturing with efficiency and cost-effectiveness. ↩
-
Learn about tools that enhance mold design and predict potential issues in gear production. ↩
-
Understand how injection molding stands against machining and 3D printing for gear production. ↩
-
Explore how injection molding ensures consistent quality across large volumes with tight tolerances. ↩
-
Discover why injection molding becomes more economical as production volume increases. ↩
-
Learn about the diverse range of materials compatible with injection molding. ↩
-
Explore different plastic materials used for gears to understand their properties and applications. ↩
-
Explore different plastic materials used for gears to understand their properties and applications. ↩
-
Discover how temperature variations influence plastic dimensions to ensure precise gear fitting. ↩
-
Learn about strategies to enhance the durability of plastic gears against wear. ↩
-
Gain insights into designing effective molds to prevent defects in plastic gears. ↩
-
Find techniques to minimize operational noise and enhance gear efficiency. ↩