Injection molding is fascinating, isn’t it? It’s like a dance between precision and material science, where plastic fluidity takes center stage.
Plastic fluidity impacts the injection molding process by affecting mold filling efficiency, cycle times, and product quality. High fluidity enables better mold filling and surface quality while reducing cycle times. Conversely, poor fluidity may cause defects and require higher pressure and temperature adjustments.
While understanding the basic influence of plastic fluidity is crucial, diving deeper into each aspect can reveal strategies to optimize injection molding practices. Let’s explore how varying fluidity levels can be managed to enhance your manufacturing processes.
High fluidity reduces injection molding cycle times.True
High fluidity allows faster mold filling and cooling, shortening cycles.
What Role Does Fluidity Play in Mold Filling Efficiency?
In the realm of injection molding, fluidity is a critical factor that dictates how efficiently plastic fills a mold.
Fluidity in plastics is essential for efficient mold filling, as it ensures rapid and uniform cavity filling, minimizes pressure loss, and reduces defects. High fluidity plastics allow for lower injection pressures and temperatures, ensuring precise mold filling even in complex designs.

Enhancing Filling Capacity with Fluidity
Fluidity is the ease with which molten plastic flows. In injection molding, optimal fluidity allows the material to spread quickly and evenly throughout the mold cavity. This characteristic is particularly advantageous when dealing with intricate mold designs or thin-walled products. When plastics exhibit good fluidity, they fill the cavity rapidly, maintaining even distribution and reducing the potential for defects such as short shots. This efficiency is vital for achieving high dimensional accuracy1 and product integrity.
For instance, in the manufacturing of complex automotive components, plastics with high fluidity are essential. These components often feature detailed geometries where uniform filling is crucial to prevent weak points and ensure structural integrity.
Balancing Pressure and Temperature Requirements
The fluidity of plastics directly influences the pressure and temperature settings required during the injection molding process. High fluidity plastics typically require lower injection pressures and temperatures. This not only facilitates smoother filling but also minimizes stress on both the product and the machinery. Conversely, plastics with poor fluidity necessitate higher pressures and temperatures to achieve complete mold filling, potentially leading to increased internal stresses and defects such as warping or deformation.
Consider a case study involving electronic housing units, where maintaining precise tolerances is critical. Using plastics with enhanced fluidity can significantly reduce the risk of defects, thus improving yield rates and reducing material wastage.
Preventing Filling Defects
Defects like flow marks, weld lines, or incomplete fills are often a result of suboptimal fluidity. With adequate fluidity, plastics can maintain a consistent flow front during injection, preventing these issues. Additionally, good fluidity ensures that plastic molecules are uniformly distributed, enhancing both mechanical properties and surface finish.
In summary, mastering the role of fluidity in mold filling efficiency can lead to improved product quality and production efficacy. Manufacturers should consider fluidity as a pivotal factor when selecting materials and setting process parameters for injection molding.
High fluidity reduces injection pressure needs.True
High fluidity plastics fill molds easily, requiring less pressure.
Low fluidity increases risk of mold defects.True
Plastics with low fluidity may not fill molds completely, causing defects.
How Does Plastic Fluidity Affect Molding Cycle Times?
The fluidity of plastics plays a crucial role in determining the efficiency and speed of the injection molding process.
Plastic fluidity directly influences molding cycle times by determining how quickly materials fill the mold and cool. High fluidity results in faster cycles, enhancing productivity, while low fluidity extends cycle durations, impacting production efficiency and costs.
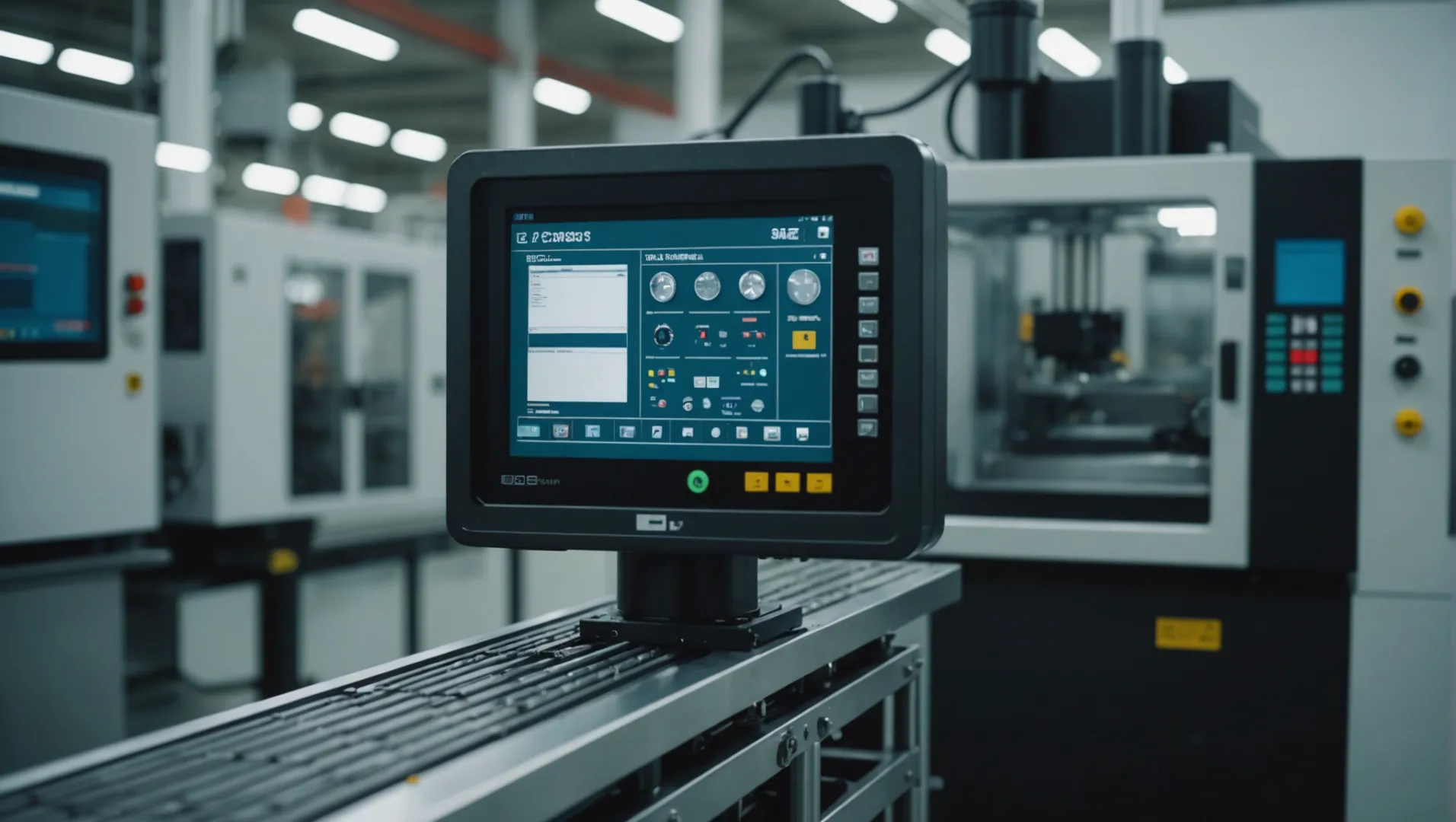
High Fluidity and Its Impact on Cycle Times
In injection molding, plastics with high fluidity can traverse the mold cavities more swiftly, minimizing the time required to fill each mold. This quick movement not only reduces the pressure needed for injection but also decreases the cooling time, as the material solidifies faster due to efficient distribution.
For instance, in high-volume manufacturing environments, a reduction in molding cycle time—even by a few seconds—can lead to substantial increases in output. This means that manufacturers can produce more units per hour, thereby significantly reducing per-unit costs. Moreover, shorter cycles lead to less energy consumption, contributing to more sustainable production practices.
Challenges with Low Fluidity
Conversely, plastics with low fluidity may necessitate longer molding cycles. The slower flow into the mold requires additional pressure and higher temperatures to ensure complete filling. This not only prolongs the cycle time but also risks increased wear on machinery and higher energy consumption.
Furthermore, longer cycles due to poor fluidity can lead to increased labor costs and potential bottlenecks in production schedules. Manufacturers may need to invest in additional resources or equipment to maintain desired output levels.
Balancing Fluidity with Product Requirements
Despite the advantages of high fluidity, not all products are best suited to it. Some applications require specific material properties that low-fluidity plastics provide. Therefore, manufacturers must carefully balance fluidity with other material characteristics to optimize both cycle time and product quality.
For example, by analyzing different fluidity levels2, manufacturers can decide which plastic grades offer the best trade-off between flow properties and other necessary features such as strength or resistance.
Optimizing Production Through Fluidity
To leverage the benefits of plastic fluidity fully, manufacturers can consider investing in technology that adapts to varying fluidities. Advanced control systems in injection molding machines can adjust temperatures and pressures dynamically, ensuring optimal conditions for each type of plastic used.
By implementing these technologies3, companies can enhance their production efficiency significantly, tailoring each process step to accommodate the specific fluidity of their materials.
High fluidity plastics reduce molding cycle times.True
High fluidity allows faster mold filling and cooling, reducing cycle time.
Low fluidity plastics increase production efficiency.False
Low fluidity extends cycle times, reducing efficiency and increasing costs.
In What Ways Does Fluidity Influence Product Quality?
Fluidity in plastics is pivotal in defining the quality attributes of products manufactured through injection molding.
Plastic fluidity affects product quality by ensuring smooth surfaces and reducing defects. High fluidity facilitates better molecular arrangement, enhancing mechanical and optical properties. Conversely, low fluidity can cause rough surfaces and defects like bubbles and shrinkage, impacting both appearance and durability.
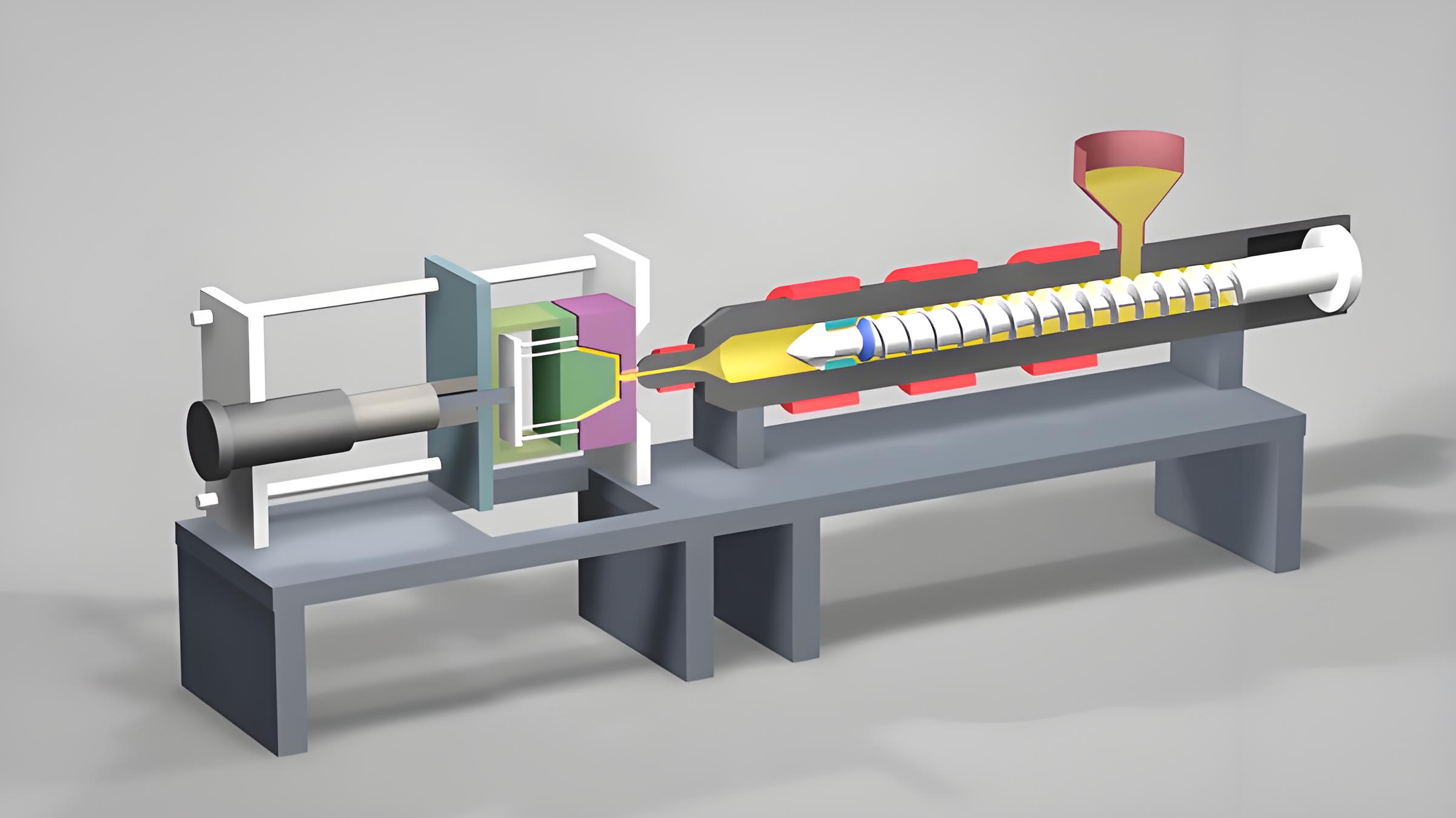
Surface Quality and Defects
One of the most evident influences of plastic fluidity on product quality is the surface finish. Plastics with high fluidity are more likely to produce products with smooth and even surfaces. This is crucial for consumer-facing products where aesthetics play a significant role. A smooth surface not only enhances the visual appeal but also reduces potential sites for dirt accumulation, making the product easier to clean and maintain.
Conversely, plastics with lower fluidity may struggle to flow evenly, leading to surface imperfections such as flow marks or weld lines. These defects not only detract from the aesthetic quality of the product but may also indicate underlying weaknesses in the material structure.
Molecular Arrangement and Mechanical Properties
The molecular arrangement within a plastic affects its mechanical properties, including strength, flexibility, and impact resistance. High fluidity allows for a more uniform distribution of molecules during the injection molding process, which can result in stronger and more resilient products. Such products can withstand greater mechanical stresses and have improved durability over time.
On the other hand, plastics with poor fluidity may experience uneven molecular arrangement, leading to stress concentrations that could compromise the product’s integrity. These weaknesses might not be immediately visible but can manifest as cracking or failure under stress or over time.
Optical Properties
For transparent or translucent plastics, fluidity plays a critical role in determining optical clarity. High fluidity can enhance optical properties by minimizing inclusions and imperfections that scatter light. This results in products with clearer and more consistent transparency.
Plastics with low fluidity might trap air bubbles or create inconsistencies during molding, leading to cloudy or opaque appearances. This can be particularly problematic in applications where clarity is essential, such as lenses or display covers.
Overall Product Longevity
The cumulative effect of surface quality, molecular arrangement, and optical properties due to plastic fluidity ultimately determines product longevity. Products with high fluidity plastics often exhibit longer lifespans as they are better equipped to resist environmental stresses and maintain their structural integrity over time.
In contrast, products made from plastics with inadequate fluidity may suffer from reduced lifespan due to premature wear or failure.
Exploring different approaches to managing plastic fluidity4 can significantly enhance the quality of injection-molded products by focusing on these key aspects.
High fluidity ensures smoother plastic surfaces.True
High fluidity allows plastics to flow evenly, resulting in smooth surfaces.
Low fluidity enhances optical clarity in plastics.False
Low fluidity can cause inclusions, reducing optical clarity and transparency.
How Can Process Parameters Be Adjusted for Different Plastic Fluidities?
Optimizing injection molding requires adjusting parameters based on the fluidity of the plastic being used.
Adjusting process parameters according to plastic fluidity is essential for successful injection molding. High-fluidity plastics require lower injection pressure and temperature, preventing defects like flash. Low-fluidity plastics demand higher pressure and temperature to ensure proper mold filling. These adjustments ensure product quality and process efficiency.
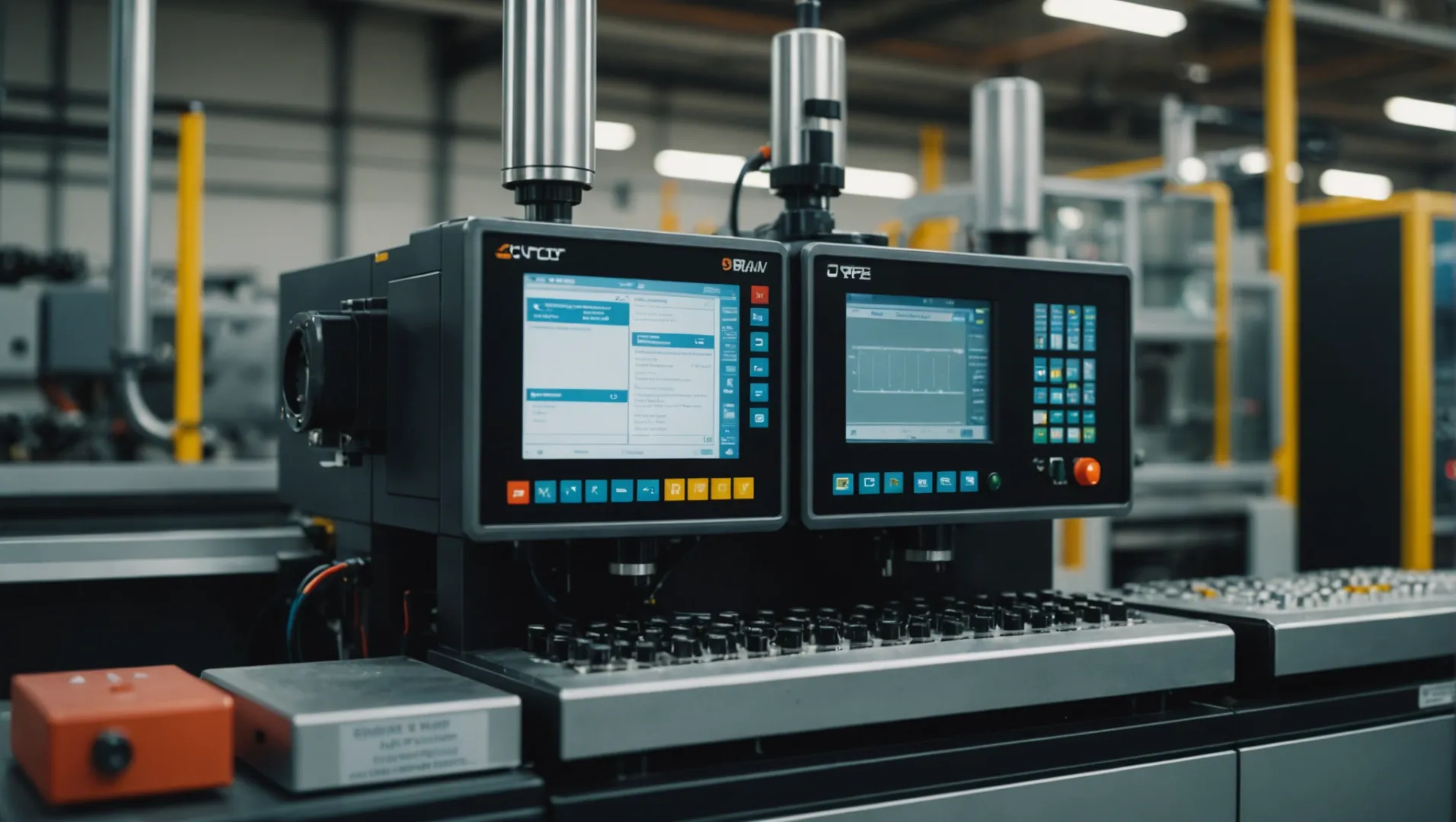
Understanding the Impact of Fluidity on Process Adjustments
Plastic fluidity plays a pivotal role in determining the settings for injection molding. When dealing with high-fluidity plastics, manufacturers must be cautious not to apply excessive pressure or temperature, which can lead to defects such as overfilling or flashing around the mold edges. Instead, settings should be optimized to leverage the natural flow characteristics of these plastics.
Conversely, low-fluidity plastics present a different set of challenges. Here, higher injection pressures and temperatures are necessary to promote adequate mold filling. This is crucial for preventing issues like short shots, where the plastic fails to completely fill the mold, leading to incomplete or structurally weak products.
Adjusting Injection Pressure and Temperature
For high-fluidity plastics:
- Lower Injection Pressure: This reduces the risk of flash and ensures a smooth fill.
- Reduced Temperature: Prevents degradation of the material while still maintaining good flow.
For low-fluidity plastics:
- Higher Injection Pressure: Essential for pushing the plastic into intricate mold areas.
- Increased Temperature: Helps in reducing viscosity, allowing the plastic to flow more readily.
Mold Design Considerations
The design of the mold itself may need alterations depending on the plastic’s fluidity:
- High-fluidity plastics can benefit from smaller gates and runners, leading to reduced mold cost and improved efficiency.
- Low-fluidity plastics require larger gates and runners to facilitate smoother flow and complete filling.
Consider a table illustrating this:
Plastic Fluidity | Injection Pressure | Temperature | Mold Design |
---|---|---|---|
High Fluidity | Low | Reduced | Smaller gates |
Low Fluidity | High | Increased | Larger gates |
Practical Application in Manufacturing
When adjusting process parameters, it’s important to consider not just the material but also the end-product requirements. For instance, thin-walled components or parts with fine details may need additional adjustments or even specific tooling to accommodate fluidity variations. Consulting with material specialists can provide valuable insights into customizing process settings5 for specific applications.
By understanding and adjusting these parameters effectively, manufacturers can enhance product quality, reduce cycle times, and improve overall efficiency in their operations.
High-fluidity plastics require lower injection pressure.True
Lower pressure prevents defects like flash and utilizes natural flow.
Low-fluidity plastics need reduced temperature for molding.False
Increased temperature is needed to reduce viscosity and aid flow.
Conclusion
Mastering plastic fluidity in injection molding is vital for achieving superior product quality and efficiency. It’s all about making informed decisions in material selection and process adjustments.
-
Explore how dimensional accuracy ensures product reliability and functional fit.: The structure design and manufacturing accuracy of the mold directly affects the dimensional accuracy of the plastic parts. In the molding … ↩
-
Explore how different fluidity levels impact material choice.: The fluidity of plastics varies with molding process conditions. Good fluidity is associated with high molding temperature and high injection pressure. ↩
-
Discover advanced technologies optimizing molding for different fluidities.: One of the new methods is water-assisted injection molding (WAIM). WAIM technology is proving to be a promising technology due to the lightness of the products … ↩
-
Discover techniques to enhance plastic fluidity for better product quality.: The lower the viscosity of the plastic, the better its fluidity. The higher the melt temperature, the lower the viscosity of the plastic resin and the better … ↩
-
Learn how to tailor injection settings for different plastic types.: Learn how to select the right material for your injection molding design with this technical overview of thermoplastic resins. ↩