Ever considered why PEEK molding is an exact skill? Think of baking a cake where each ingredient and step matters greatly.
PEEK molding requires precise control over processing conditions, including material drying, mold temperatures, and injection parameters, to ensure high-quality results. Understanding these factors is essential for effective manufacturing with PEEK.
You know what is involved in PEEK molding. Explore each detail more. Study drying needs. Understand injection settings. Learn everything.
PEEK molding requires drying at 150-160°C for 4-6 hours.True
Correct drying stops moisture problems, keeping PEEK quality at its best.
How Do Material Drying Requirements Affect PEEK Molding?
Drying material strongly affects PEEK molding, impacting the polymer’s behavior and the finished product’s quality.
Proper material drying prevents moisture-related defects in PEEK molding, ensuring optimal mechanical properties and surface finish. It involves controlled temperature and time settings, crucial for minimizing flaws.
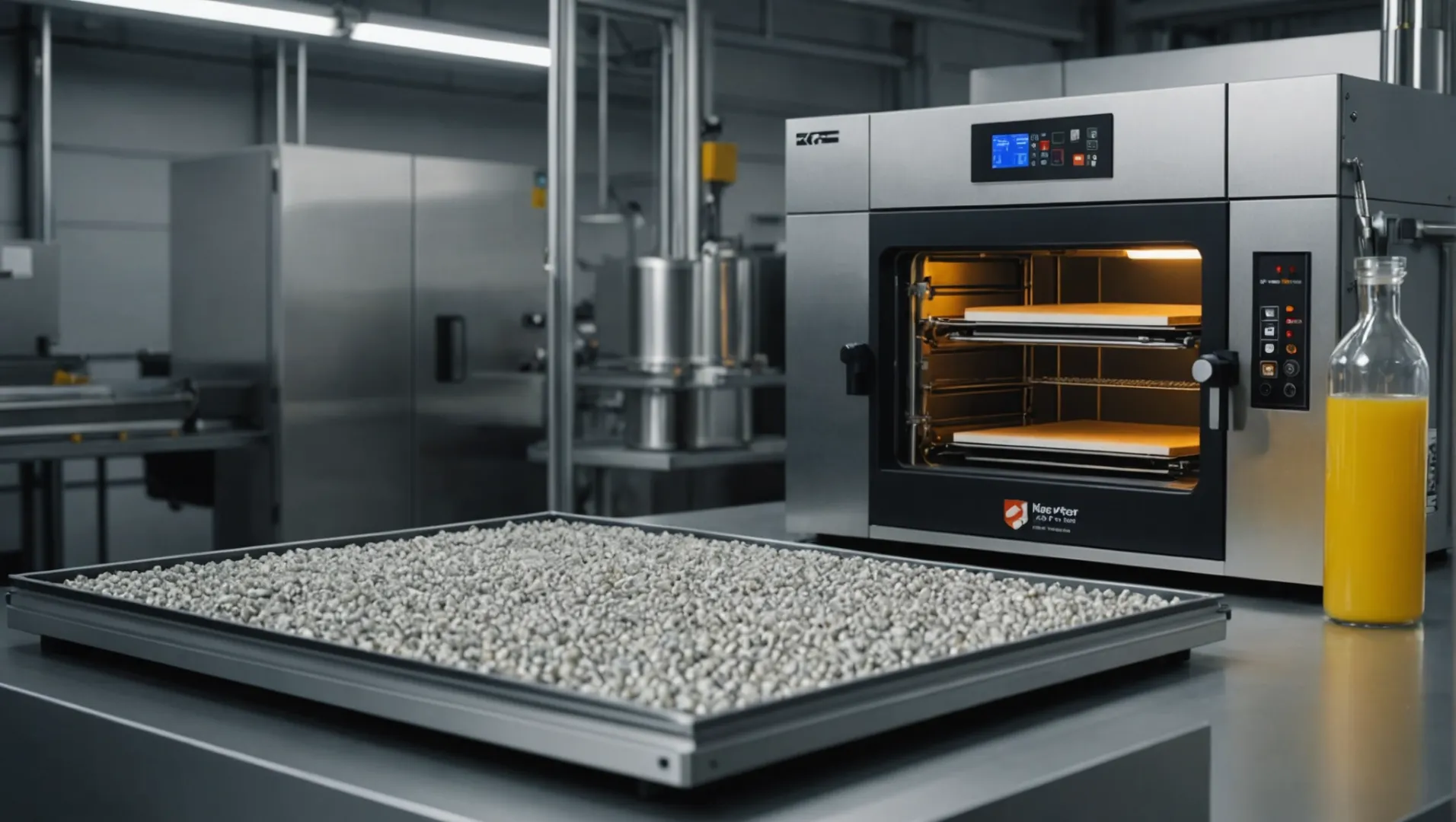
Using Why Drying PEEK is Important
Drying PEEK (Polyether ether ketone) before processing is crucial because it reacts badly with water. Even a little water can ruin the toughness of PEEK and spoil the smoothness of the finished product. Correct drying keeps the polymer strong and helps it meet strict quality rules.
Key Factors for Good Drying
1. Time and Heat:
Typically, PEEK needs drying at 150°C to 160°C. At 150°C, it needs 4-6 hours, but at 160°C, only 2-3 hours. This time ensures that PEEK dries fully before shaping.
Temperature (°C) | Time (Hours) |
---|---|
150 | 4 – 6 |
160 | 2 – 3 |
2. Dryer Equipment:
The dryers should hold steady temperatures within the set range. Avoid mixing PEEK with other materials while drying, as this can lower quality and performance.
Effects on Formed Parts
If PEEK is not dried right, you might face these problems:
- Surface Problems: Water can create bubbles or lines on the surface.
- Lower Strength: Water can weaken PEEK, making it less strong and less wear-resistant.
- Size Changes: Water can make parts expand or shrink, causing size mistakes.
Tips for Best Outcomes
For top-quality PEEK items:
- Use special dryers meant for high-grade polymers.
- Check and adjust dryers regularly for proper heat levels.
- Always dry materials following the guidelines before shaping them.
Proper understanding and use of drying methods are key for good PEEK processing. By controlling these factors well, manufacturers probably avoid common flaws and get the best out of their PEEK products.
PEEK requires drying at 150°C for 4-6 hours.True
Right drying temperature and time are essential to stop defects.
Mixing PEEK with other materials during drying is recommended.False
Combining might harm product quality and performance.
What Are the Critical Temperature Settings for PEEK Injection Molding?
Temperature holds a key function in PEEK injection molding, affecting both quality and efficiency. Exact control remains crucial to improve performance.
Critical temperature settings for PEEK injection molding include material drying at 150-160°C, barrel temperatures from 320-410°C, and mold temperatures between 150-200°C. Proper management of these temperatures is essential to avoid defects and ensure optimal results.
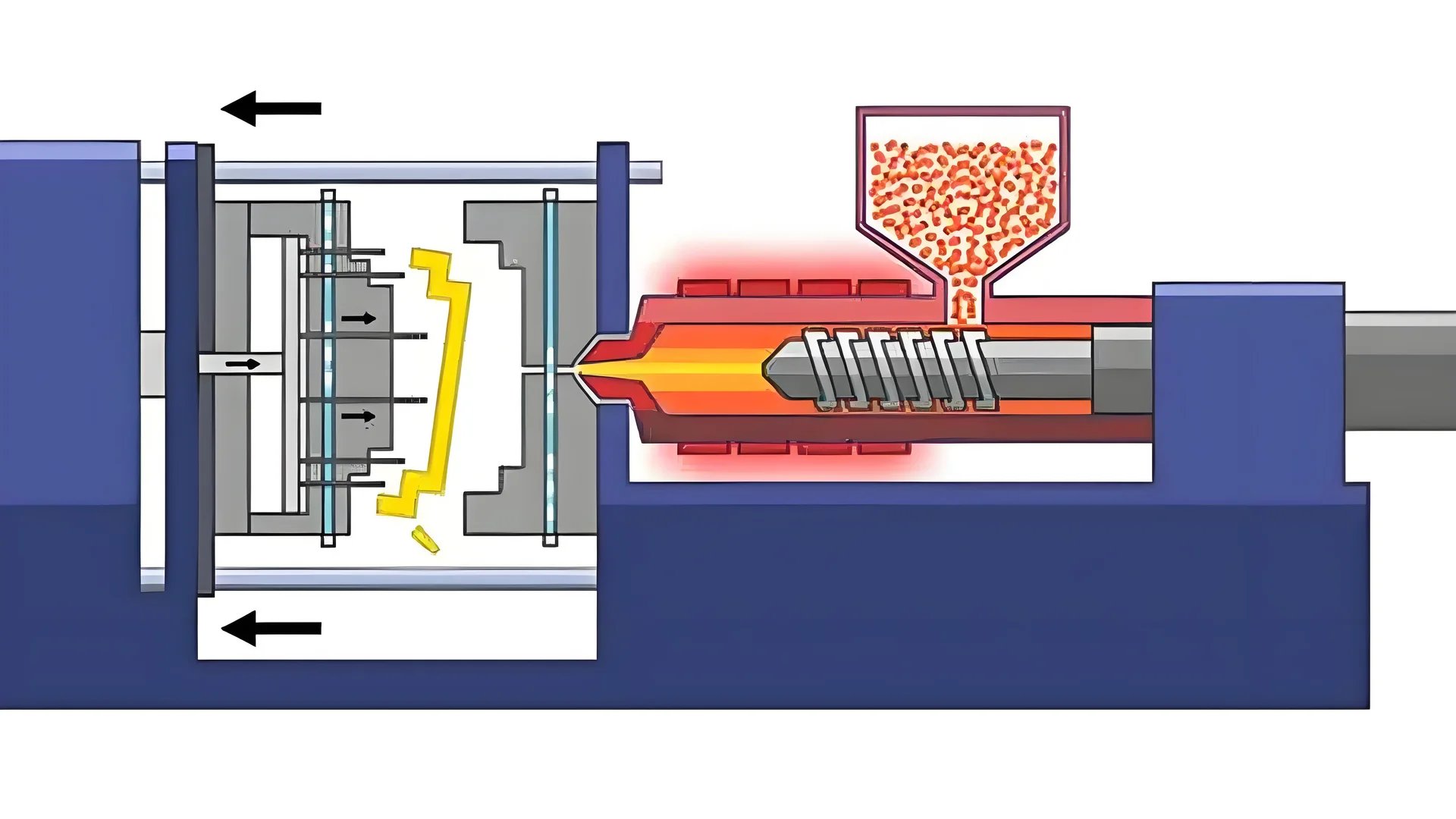
Understanding Material Drying Needs
When working with PEEK (Polyether Ether Ketone), drying is important to remove water that could change the polymer’s traits. It is wise to dry PEEK materials for a minimum of 4 hours at temperatures from 150°C to 160°C. Higher drying temperatures decrease drying time but must be kept in check to prevent damage. Drying tools should hold these temperatures steady.
Barrel Temperature Settings
The injection molding machine’s barrel splits into zones, each needing distinct temperature settings. Normally, the back zone stays between 320°C and 380°C. The middle part sets between 330°C and 390°C, and the front area has temperatures from 340°C to 400°C. The nozzle is crucial as it stops early cooling and remains at 350°C to 410°C. These different settings help reach perfect melt flow and avoid damage.
Mold Temperature Control
Mold temperature greatly affects the end quality of PEEK items. Molds should have a surface temperature between 150°C and 200°C. This is possible using electric heaters for equal temperature across the mold. If temperatures are too low, PEEK might cool too fast, causing poor flow and flaws. On the flip side, too high temperatures may result in problems like expansion or surface marks.
Importance of Mold Material Choice
Since PEEK processing needs high temperatures, picking the right mold material is important. Using steels like S136 or H13, which resist heat, provides strength and accuracy. These materials endure high temperatures and resist damage from glass fiber abrasives. Proper hardening (48-52 HRC) also keeps the mold strong over long production times.
For more information on ideal PEEK molding methods, think about looking into mold temperature guidelines1 and injection machine details2. By knowing these factors, producers possibly get better product quality and fewer production problems.
PEEK drying requires temperatures of 150-160°C.True
PEEK materials require drying at 150-160°C to eliminate moisture.
Barrel temperatures for PEEK are set at 200-300°C.False
PEEK barrel temperatures vary between 320°C and 410°C, not 200-300°C.
Why Is Mold Material Selection Important in PEEK Processing?
In PEEK processing, picking the correct mold material matters for obtaining the best results and keeping the mold long-lasting.
Choosing appropriate mold materials in PEEK processing ensures high-temperature resistance and durability, crucial for product quality.
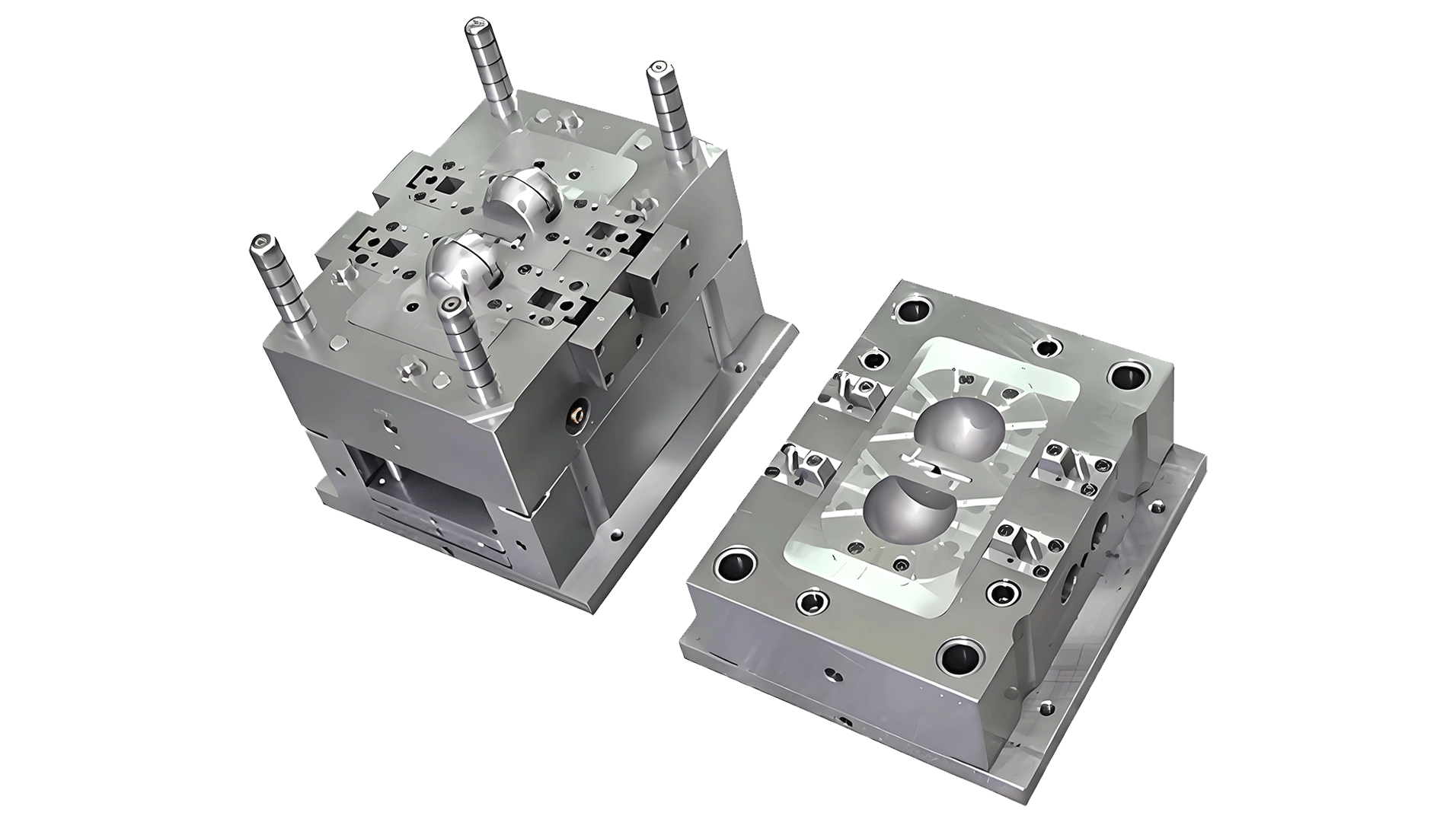
High-Temperature Endurance
PEEK (Polyether Ether Ketone) has a very high melting point. It needs mold materials that handle very high heat. During PEEK injection molding3, heat levels often rise to 400°C. Materials like S136 stainless steel or H13 mold steel keep the mold strong and useful even when it is super hot. These materials resist both heat and the scratching effect of glass fibers often mixed with PEEK.
Toughness and Strength
Choosing tough mold material is very important too. PEEK, especially with glass or carbon fibers, is very rough. The mold material needs strength to survive many uses without wearing out. Usually, hardness is between 48 and 52 HRC (Rockwell Hardness Scale) so the mold keeps its shape and accuracy, which is key for steady part quality.
Surface Smoothness and Look
The mold material also affects how smooth and nice the final product looks. Good quality molds with finishing treatments can really improve the surface look of PEEK parts. This is crucial in areas where look and performance are very important, like in airplanes or medical tools.
Balance Between Cost and Performance
Choosing high-quality materials such as S136 stainless steel or H13 brings many advantages but costs more at first. Companies need to weigh these costs against less upkeep and longer mold life. Over time, spending on better mold materials is often cheaper due to less need for replacements and repairs.
Conclusion: More Than Just Material Choice
Picking mold material is very important, but it is just one part of PEEK processing success. Other things such as mold design and upkeep rules are just as important for overall success in production work.
S136 stainless steel withstands 400°C in PEEK molding.True
S136 stainless steel withstands very high heat, necessary for PEEK manufacturing.
PEEK molds require hardness above 60 HRC for durability.False
PEEK molds require 48-52 HRC for strength, not going over 60 HRC.
How to Optimize Injection Parameters for High-Quality PEEK Parts?
Learn the important elements in adjusting injection settings for high-quality PEEK components.
Optimizing injection parameters involves adjusting pressure, speed, and holding time tailored to PEEK‘s unique properties. Achieving the ideal balance ensures that molten PEEK fills the mold efficiently, minimizing defects and enhancing product quality.
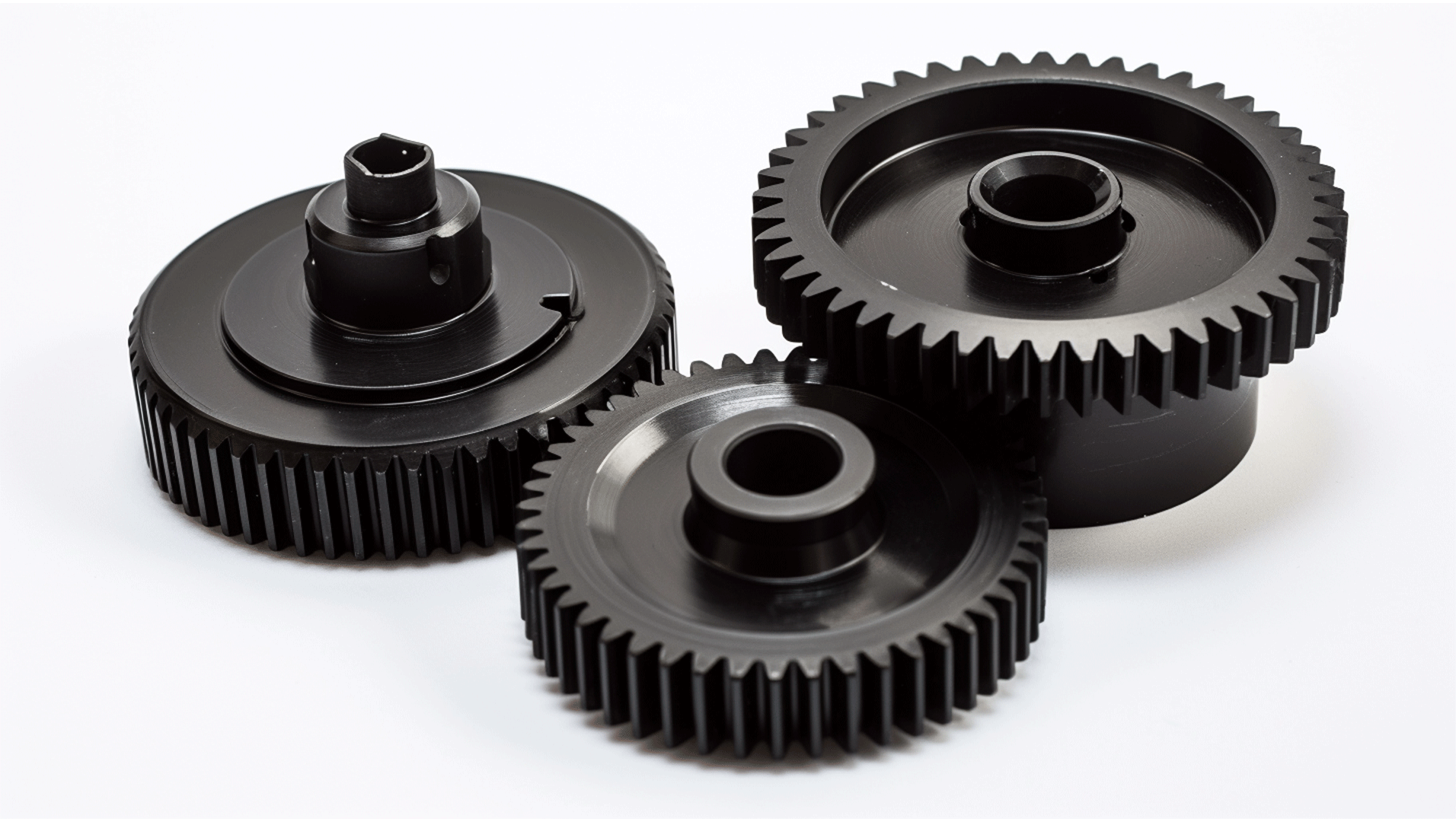
Understanding Injection Pressure and Speed
Injection pressure is critical for ensuring that molten PEEK can adequately fill the mold cavity. Typically, the pressure ranges between 80 – 120 MPa. A pressure that is too low may result in incomplete filling or weak bonding, whereas excessively high pressure can cause demolding challenges or surface abrasions. It’s essential to adjust pressure based on the product’s size and the mold’s design.
Injection speed should be controlled at a low to medium pace. This control helps in maintaining a smooth material flow while avoiding defects like bubbles or fusion marks. The correct speed ensures that the material does not degrade during injection, which can happen if the speed is too high.
Importance of Holding Time
The holding time allows the material to cool and cure within the mold, preventing shrinkage and deformation. For PEEK parts, this time typically ranges from 2 to 5 seconds, depending on the product’s thickness and the mold’s structure. Adequate holding time ensures that PEEK parts retain their designed dimensions and integrity.
Managing Back Pressure
Back pressure is another critical factor in optimizing injection parameters. It aids in enhancing the homogeneity of the molten polymer by increasing shear during plasticizing. However, too much back pressure can lead to increased cycle times and energy consumption.
Tailoring Injection Parameters to PEEK‘s Properties
PEEK‘s Melt Flow Index (MFI) is usually low, demanding specific adjustments in injection parameters. Utilizing a modern reciprocating screw injection molding machine with microprocessor control can significantly aid in maintaining consistent quality. Such machines offer closed-loop capability to fine-tune parameters like injection pressure and clamping force.
Recommended Settings Table
Parameter | Recommended Range |
---|---|
Injection Pressure | 80 – 120 MPa |
Injection Speed | Low to Medium |
Holding Time | 2 – 5 seconds |
Back Pressure | Adjust as needed |
By understanding and applying these specific settings, you can significantly enhance the quality of your PEEK parts. For more on how these parameters interact with mold material requirements4, further investigation into material science can provide deeper insights.
Injection pressure for PEEK ranges from 80 to 120 MPa.True
This range allows enough mold filling without flaws.
Holding time for PEEK parts should exceed 10 seconds.False
PEEK holding duration usually lasts around 2 to 5 seconds.
Conclusion
Handle PEEK molding by learning its special requirements. Adjust drying, mold and injection settings to create excellent parts. Study these methods to probably improve both efficiency and quality.
-
Explore detailed guidelines for maintaining effective mold temperatures.: In this article we consider five factors in the injection molding process that can help to avoid the need for troubleshooting when molding PEEK polymer. ↩
-
Learn about the necessary specifications for machines handling PEEK.: In order to successfully mold VICTREX PEEK materials, the cylinder heaters connected to the barrel of the injection molder must be able to reach 400°C (752°F). ↩
-
Explore detailed temperature settings essential for PEEK molding success.: Depending on the grade of PEEK that you’ll be moulding, processing temperatures on your injection moulding barrel will be somewhere in the range of 350-400⁰C. ↩
-
Learn how mold materials influence PEEK part quality.: In order to successfully mold VICTREX PEEK materials, the cylinder heaters connected to the barrel of the injection molder must be able to reach 400°C (752°F). ↩