Trying out the options of injection molding PEEK might be thrilling and challenging for producers.
Yes, injection molding machines can handle PEEK material efficiently when specific conditions are met, such as precise temperature control and suitable equipment adjustments. PEEK‘s unique properties necessitate attention to drying times, mold materials, and machine specifications to ensure optimal performance.
Knowing the details of PEEK processing probably impacts production quality and efficiency. Explore the important points and methods for shaping this advanced thermoplastic so your equipment meets the requirements.
Injection molding machines can handle PEEK material efficiently.True
Using accurate heat management and equipment changes, PEEK gets shaped effectively.
What Are the Key Temperature Requirements for Molding PEEK?
Controlling temperature is important when shaping PEEK to get good results.
The key temperature requirements for molding PEEK involve specific conditions for drying, barrel settings, and mold temperatures. Drying should occur at 150℃ – 160℃ for optimal moisture removal. Barrel temperatures range from 320℃ to 410℃, while mold temperatures should be between 120℃ and 200℃ to ensure proper flow and solidification.
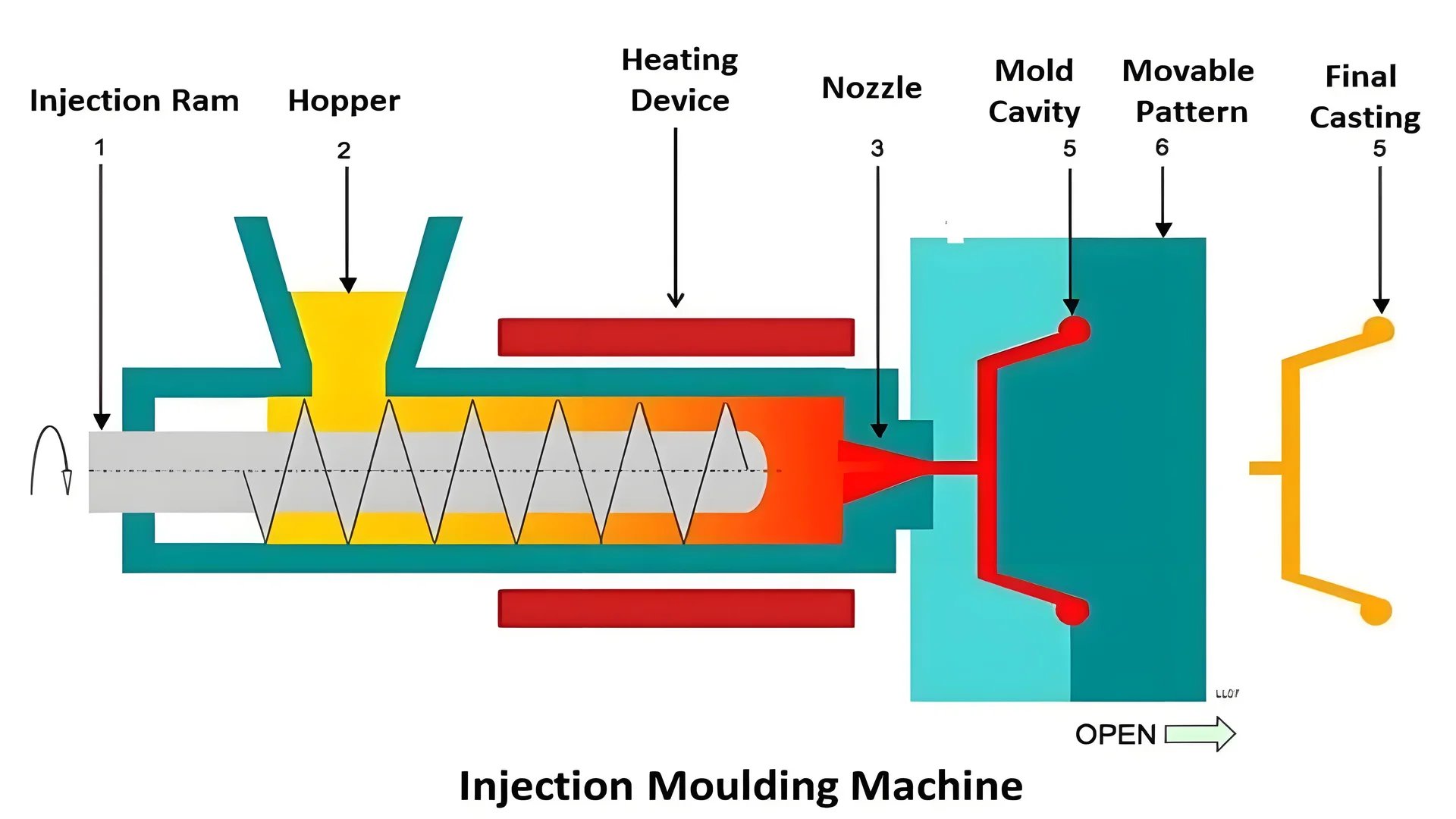
Why Temperature Control Matters in PEEK Molding
Polyether ether ketone (PEEK) stands out as a tough engineering plastic in challenging conditions. To use it well, controlling the temperature during molding is crucial.
Drying Material: Key Step Before Molding
Drying PEEK is very important to get rid of water that might harm the final product. Normally, dry PEEK at 150℃ to 160℃. At 150℃, dry for 4 to 6 hours; at 160℃, dry for 2 to 3 hours. This keeps the material working well and stops problems like bubbles during molding.
Temperature Settings for Injection Molding Machines
Set the barrel temperature of injection machines carefully to handle molten PEEK properly:
- Back of the Barrel: 320℃ – 380℃
- Middle of the Barrel: 330℃ – 390℃
- Front of the Barrel: 340℃ – 400℃
- Nozzle: 350℃ – 410℃
These temperatures help PEEK flow smoothly and stop it from cooling too fast, which might hurt quality.
Mold Temperature: Finding the Right Balance
Mold temperature changes the product’s quality and performance significantly. The suggested range is between 120℃ and 200℃. If the mold is cooler, the material cools fast which affects flow and appearance. If the mold is hotter, it could expand or damage the material. Adjust based on design needs and solidifying details.
Other Points for Good PEEK Molding
Besides temperature, factors like mold design1, injection settings, and machine features are important for PEEK processing. Choosing strong mold materials that handle high temperatures, like S136 stainless steel or H13, increases strength and finish quality.
Knowing these temperature details helps people working with PEEK achieve better efficiency and top-quality products by understanding these intricacies can lead to improved efficiency2 and superior product outcomes.
PEEK should be dried at 150℃ for 4 to 6 hours.True
Drying PEEK at 150℃ for 4-6 hours takes away moisture efficiently.
Mold temperatures for PEEK should be below 100℃.False
Mold heat levels need to stay from 120℃ to 200℃ for PEEK.
How Does Mold Design Affect PEEK Molding Efficiency?
Mold design greatly affects how well and how nicely PEEK molds form.
Mold design impacts PEEK molding efficiency by ensuring proper temperature control, material flow, and structural integrity. Using high-temperature-resistant materials like S136 stainless steel and optimizing inlet locations and sizes are crucial. These factors collectively enhance PEEK‘s molding performance, reducing defects and improving product quality.
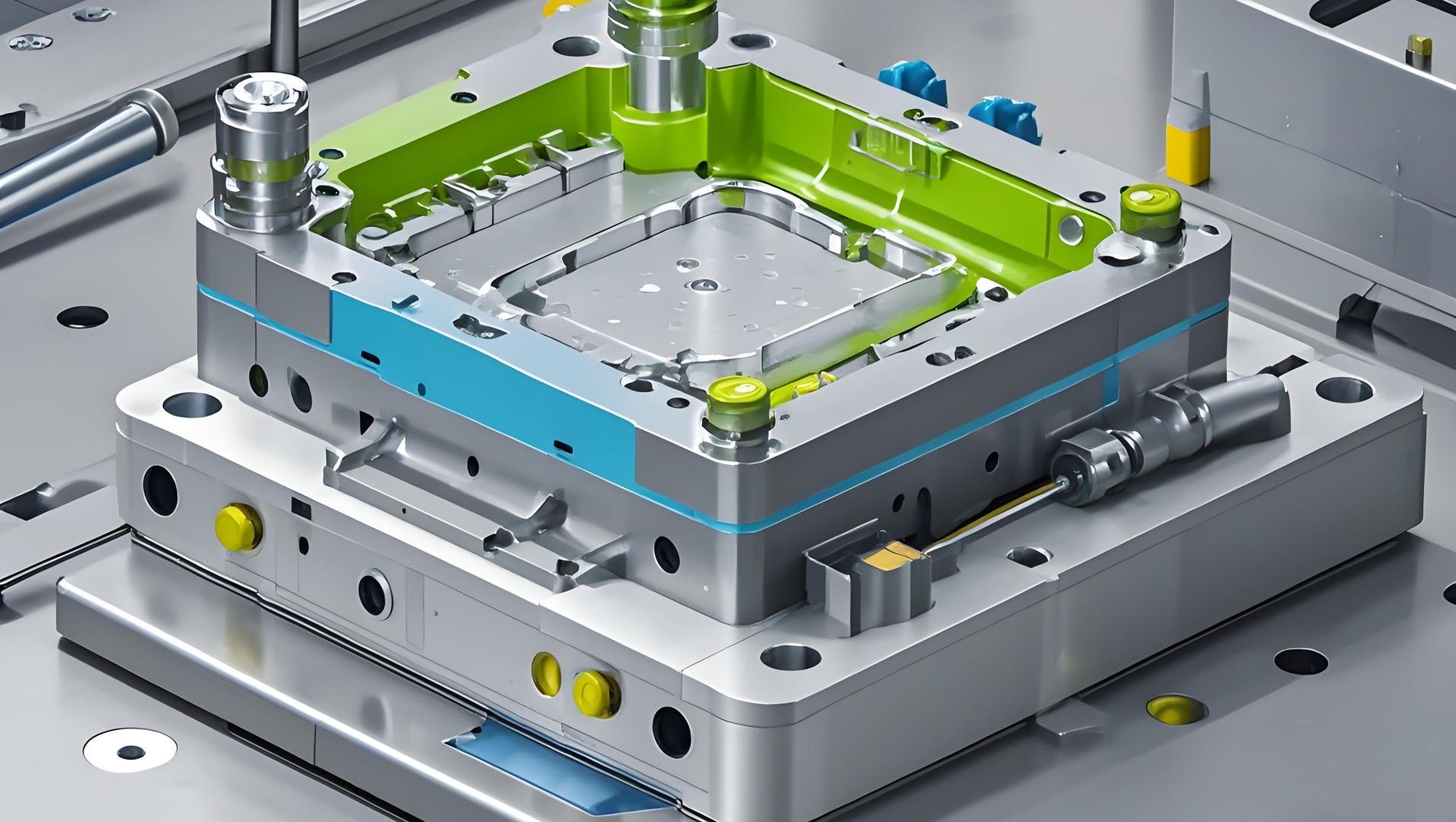
Understanding Material Needs for PEEK Molding
PEEK, short for polyether ether ketone, is a strong plastic with very good mechanical features and heat tolerance. Mold shapes must fit these features to keep molding steps smooth.
Importance of Drying Material
Before shaping, PEEK requires careful drying to stop problems like bubbles and shrink holes. Usually, it takes about 4-6 hours at around 150℃. Lifting the heat to 160℃ cuts drying to 2-3 hours. Good drying is key for keeping PEEK strong.
Temperature in Mold Design
Managing temperature is vital because PEEK melts at high heat. Mold temperature stays between 120℃ and 200℃ for the best results. Low heat can cool it fast, hurting flow and end quality. Too much heat might cause parts to stretch.
Opt for mold materials like S136 stainless steel or H13 steel. These handle high temperatures and resist wear, helping finish surfaces well after polishing.
Inlet Design Considerations
The inlet guides material smoothly into the mold. Avoid placing it where stresses occur to keep performance and looks intact. The inlet size should not be too small, as it can block flow or too large, as it can hurt size accuracy and beauty. Later steps like CNC machining can perfect the inlet.
Structure and Flow Dynamics
Mold design should guide the flow well and keep a strong structure under high pressure common in PEEK use. Techniques such as placing vents and ribs carefully can help reduce flaws like flow marks and scratches.
By focusing on these mold design points, makers can raise the success and quality of PEEK shaping tasks.
PEEK molds must be made of S136 stainless steel.True
S136 is suggested due to its ability to withstand high temperatures and its long-lasting nature.
Inlet size does not affect PEEK product quality.False
Wrong inlet size could affect flow, appearance and precision.
What Machine Specifications Are Essential for PEEK Processing?
Your injection molding machine needs to be ready to work with PEEK to get really good results.
For PEEK processing, machines must have precise temperature control, specialized screws, and robust material handling capabilities. Key specifications include a temperature-resistant screw, advanced microprocessor controls, and appropriate compression ratios to prevent material degradation and ensure effective molding.
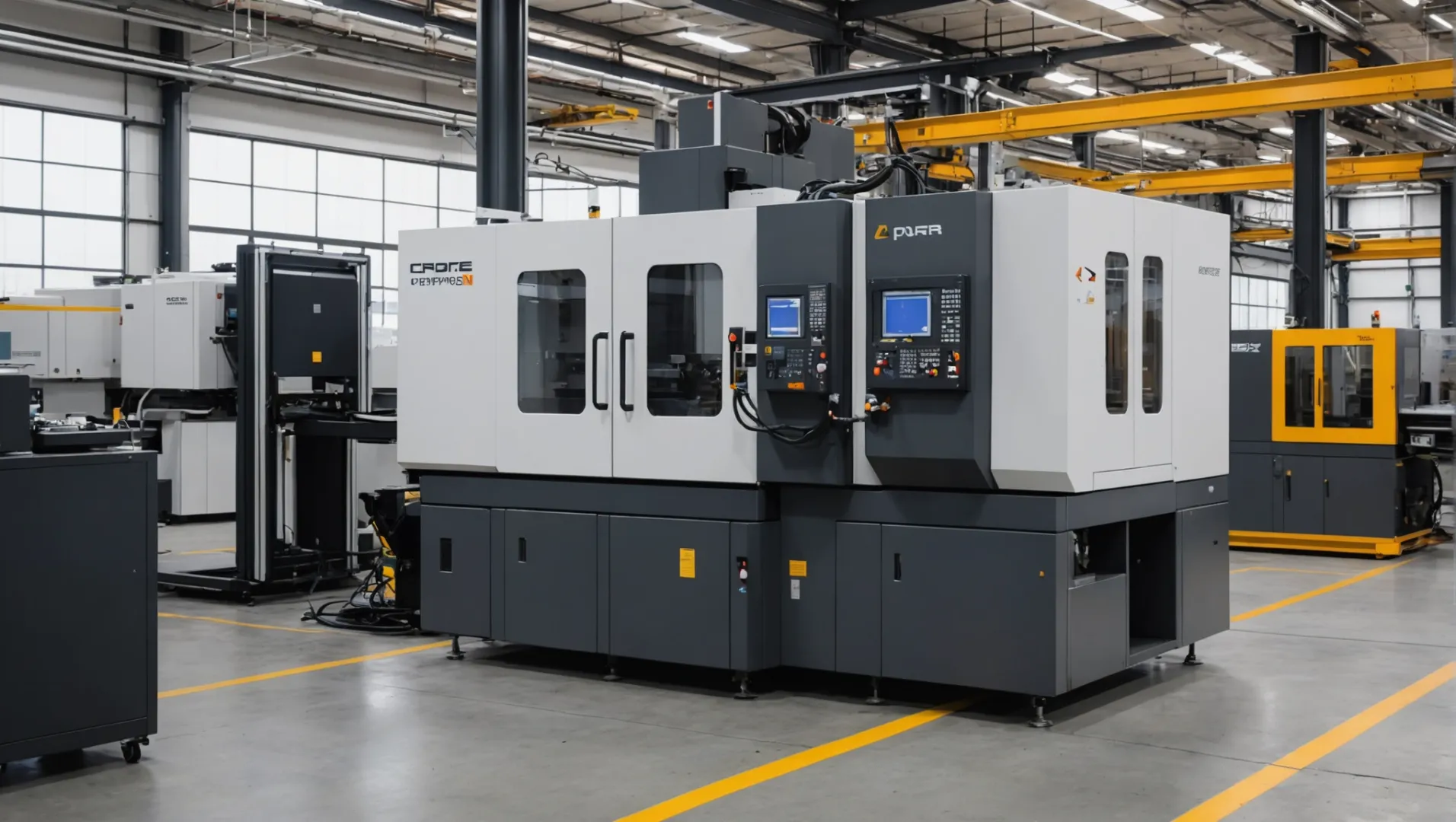
Precision in Temperature Control
PEEK processing demands an injection molding machine3 capable of maintaining high and consistent temperatures. The barrel must be divided into zones with specific temperatures: back at 320-380℃, middle at 330-390℃, front at 340-400℃, and nozzle at 350-410℃. This precision ensures the PEEK material melts uniformly without degradation.
Specialized Screw Design
The screw material should withstand temperatures over 400℃, using a low compression ratio screw (1:1 to 1.3:1) without a non-return valve. A screw length of 20-30 times its diameter ensures proper plasticizing and mixing. Screw speed should be controlled between 50-80 RPM to avoid decomposition and bubble formation.
Specification | Requirement |
---|---|
Screw Temperature | Above 400℃ |
Compression Ratio | 1:1 to 1.3:1 |
Screw Length | 20-30 times the screw diameter |
Screw Speed | 50-80 RPM |
Advanced Machine Control Systems
Modern machines with closed-loop control capabilities and microprocessor systems are preferred. They allow for precise adjustments in injection pressure (80-120MPa) and clamping force, crucial for maintaining product quality.
Comprehensive Heating and Cooling Systems
Efficient heating and cooling systems are essential to maintain the optimal mold temperature (120-200℃) and prevent thermal expansion issues. These systems ensure the PEEK remains fluid enough to fill the mold completely without solidifying prematurely.
Importance of Proper Material Handling
To prevent contamination, PEEK must be thoroughly dried for 2-6 hours at 150-160℃ before processing. The drying equipment should exclusively handle PEEK to avoid compromising its properties.
By understanding these machine specifications, manufacturers can effectively manage PEEK processing challenges, ensuring efficient production and high-quality outcomes.
PEEK requires a screw temperature above 400℃.True
PEEK processing requires high temperatures to stop the material from breaking down.
Screw speed for PEEK should exceed 100 RPM.False
PEEK processing needs screw speeds between 50-80 RPM to prevent problems.
How Can Injection Parameters Optimize PEEK Molding?
Improving injection settings is important for getting the best outcomes in PEEK molding steps.
Injection parameters optimize PEEK molding by balancing injection pressure, speed, holding time, and back pressure. These parameters ensure proper flow, fill, and cooling, enhancing product quality and minimizing defects.

Understanding Injection Pressure
Injection pressure is critical when working with PEEK (Polyether ether ketone), a high-performance polymer known for its resistance to high temperatures and chemical degradation. The recommended injection pressure for PEEK is usually within 80 – 120MPa. This range ensures that the molten material fills the mold cavity completely, avoiding defects like incomplete fills or air traps. However, excessive pressure can lead to difficulties in demolding or surface abrasions.
Balancing Injection Speed
Controlling the injection speed is equally important. For PEEK, a low to medium speed is recommended to maintain smooth flow and prevent the formation of bubbles or fusion marks. Adjustments should be made based on the mold’s geometry and the complexity of the part being produced. By optimizing speed, manufacturers can achieve a consistent quality surface finish and structural integrity.
The Role of Holding Time
Holding time helps in ensuring that the material is fully cooled and solidified before demolding, reducing the risk of shrinkage or deformation. Typically, holding time ranges from 2 to 5 seconds but should be tailored according to the part’s thickness and mold design.
Managing Back Pressure
Back pressure settings, generally between 2 – 5MPa, are essential to maintain uniform material density during molding. Proper back pressure helps in eliminating defects such as bubbles and shrinkage holes, thus contributing to the overall quality of the finished product.
Injection Parameters Table
Parameter | Recommended Range | Purpose |
---|---|---|
Injection Pressure | 80 – 120MPa | Ensures full cavity fill without defects |
Injection Speed | Low to Medium | Prevents defects and ensures smooth flow |
Holding Time | 2 – 5 seconds | Prevents shrinkage and deformation |
Back Pressure | 2 – 5MPa | Maintains material density, eliminates bubbles |
These injection parameters4 are vital for optimizing the molding process of PEEK, making it possible to produce high-quality parts with precise dimensional accuracy and excellent mechanical properties.
PEEK molding requires 80-120MPa injection pressure.True
This pressure range fills the cavity totally and prevents problems.
Holding time for PEEK is always 10 seconds.False
Usual holding time lasts from 2 to 5 seconds, not 10.
Conclusion
To succeed in PEEK injection molding, precise machine settings and careful material handling are critical. Accept these ideas to improve your methods, achieving effective production and using PEEK’s full potential.
-
Explore how mold design impacts PEEK molding efficiency.: Typically, the recommended mold temperature range is 30-60°C (or adjusted to -40-80°C based on the specific model). Higher mold temperatures can improve flow … ↩
-
Learn how precise temperature control boosts molding efficiency.: To mould PEEK and its compounds successfully one needs to be able to maintain mould temperatures between 170-200⁰C (to avoid quench-cooling into the amorphous … ↩
-
Discover how precise temperature control affects product quality and consistency.: Temperature significantly impacts each step of the entire plastic injection molding process. This is why temperature control is crucial and … ↩
-
Learn how precise parameter control enhances PEEK molding efficiency.: Depending on the grade of PEEK that you’ll be moulding, processing temperatures on your injection moulding barrel will be somewhere in the range of 350-400⁰C. ↩