Understanding the relationship between the parting surface angle and draft angle is vital in mold design.
The parting surface angle directly affects the draft angle by determining its starting direction and effective range. An inclined parting surface can alter the draft angle’s efficacy, necessitating precise calculations to ensure smooth demolding.
While this explanation offers a foundational understanding, exploring how these angles collaboratively ensure product integrity and production efficiency is essential. Delve deeper to uncover strategic insights for optimizing mold design.
Parting surface angle affects draft angle effectiveness.True
The parting surface angle influences the effective range of the draft angle.
Draft angles are unnecessary for smooth mold release.False
Draft angles are crucial for ensuring smooth product release from molds.
What Role Does the Draft Angle Play in Molding Surface Design?
Draft angles are crucial in mold design, ensuring smooth part release and optimal surface quality. Let’s explore their significance.
Draft angles in molding influence the ease of part ejection, reduce defects, and optimize surface design. They work with parting surfaces to ensure parts don’t stick to the mold, facilitating smooth production. Proper calculation of these angles prevents damage during demolding, making them vital in achieving high-quality molded parts.
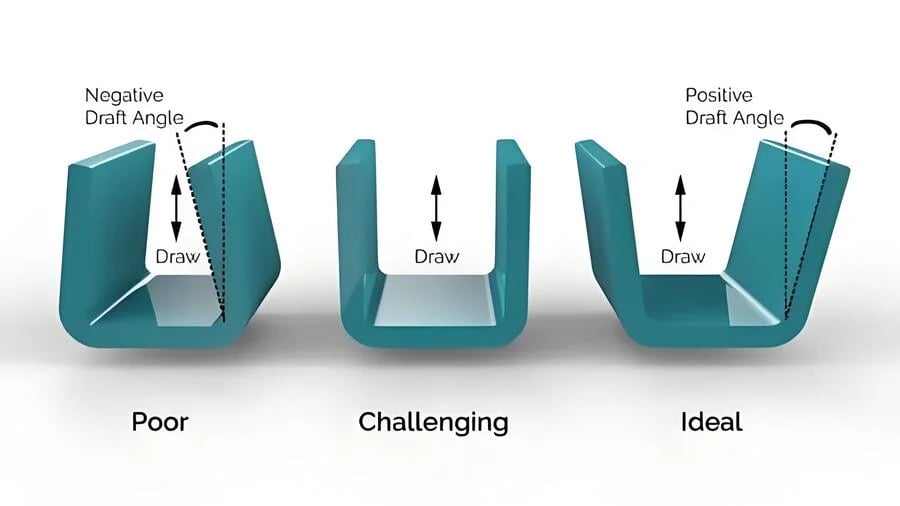
Understanding the Interacting Angle Setting
The draft angle is pivotal when setting the interacting angle with the parting surface. The influence of the parting surface angle1 on the draft angle cannot be overstated; it dictates the starting direction and effective range of the draft angle. For instance, if a parting surface is inclined at 30°, and a draft angle of 1° is set, the actual demolding angle is an integration of these two. This requires precise calculation to prevent defects during demolding.
Optimizing Molding Surface Design
A well-calculated draft angle enhances molding surface design. When specific requirements for draft angles exist, adjustments in parting face positions might be necessary. For example, a high cylindrical product may require a mid-positioned parting surface to optimize the draft angle and prevent interference during release. This adjustment ensures that the product exits smoothly, utilizing the draft angle effectively.
Ensuring Smooth Mold Release through Collaboration
The collaboration between the parting surface angle and draft angle2 is essential for seamless mold release. In design, both angles must facilitate a gradual and predetermined release direction. A complex plastic product’s surfaces need matching draft angles and parting surface angles for synchronized separation from mold cavities and cores.
Avoiding Interference with Thoughtful Angle Design
Poorly designed angles can lead to interference between the product and mold. If the parting surface angle is excessively large while the draft angle remains small, friction may occur during demolding. This situation could damage either the product or the mold, underscoring the importance of precise simulations and calculations to avoid such interference issues in mold design3.
Parting surface angle affects draft angle effectiveness.True
The parting surface angle influences the effective range of the draft angle.
Draft angles have no impact on mold release smoothness.False
Draft angles are crucial for ensuring smooth mold release.
How Can Precise Angle Calculations Prevent Mold Interference?
Precise angle calculations are crucial in mold design to prevent interference, ensuring smooth product release and enhancing manufacturing efficiency.
Precise angle calculations in mold design, especially for draft angles, prevent mold interference by ensuring the parting and draft angles complement each other, facilitating smooth product demolding without damage.
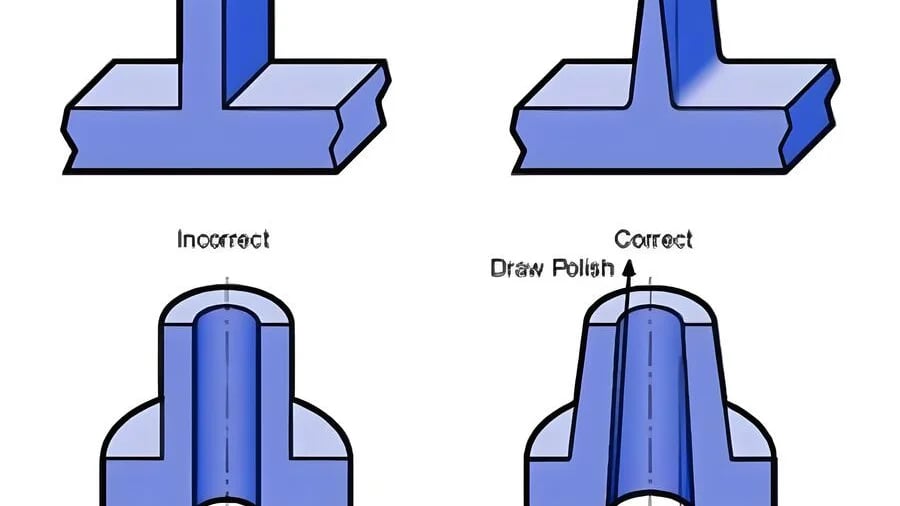
Understanding Interacting Angle Settings
In mold design, the influence of parting surface angle on draft angle plays a pivotal role. The parting surface angle determines how the draft angle is set, affecting the product’s demolding efficiency. For instance, if a parting surface is inclined at 30°, setting a draft angle of 1° requires calculating their combined effect to ensure proper release. This prevents the product from sticking or getting damaged during demolding.
A reasonable draft angle4 optimizes molding surface design. If a product’s draft angle demands are high, adjustments in parting face position might be necessary. For example, a tall cylindrical product with a large draft angle may need its parting surface placed strategically to utilize the draft effectively, avoiding mold interference during release.
Collaboration for Smooth Mold Release
Angle matching ensures a seamless mold release process. The collaboration between the parting surface angle and the draft angle is essential for smooth demolding. For complex surfaces, ensuring all angles complement each other prevents the product from getting partially stuck. This synchronization allows for the product to release in the intended direction without interference.
Moreover, designing the angle to avoid interference is critical. If there’s a mismatch, like an overly large parting surface angle paired with a small draft angle, it may lead to friction or collisions during demolding. This can harm both the product and the mold. Thus, precise calculations and simulations during design phase are vital to prevent such issues and ensure that the angles work harmoniously to avoid any interference problems.
Practical Implications and Techniques
In practice, using CAD software for simulating these angles can be highly beneficial. Advanced simulation tools allow engineers to visualize potential interferences and adjust angles accordingly. This proactive approach helps identify potential pitfalls and rectify them before production starts, ensuring efficiency and reducing costs.
For those involved in mold design, understanding the importance of draft angles5 and how they interact with parting surfaces is crucial. Engaging with resources or courses on mold design can provide deeper insights into achieving optimal designs that minimize mold interference effectively.
Parting surface angle affects draft angle efficacy.True
The parting surface angle influences the starting direction and range of the draft angle.
Large draft angles always prevent mold interference.False
Improper angle design can still cause interference, even with large draft angles.
What Are the Best Practices for Ensuring Smooth Mold Release?
Ensuring smooth mold release is crucial in manufacturing, impacting product quality and production efficiency. Let’s explore key practices.
To ensure smooth mold release, focus on proper draft angles, collaborative angle settings, and precise mold design to prevent interference.
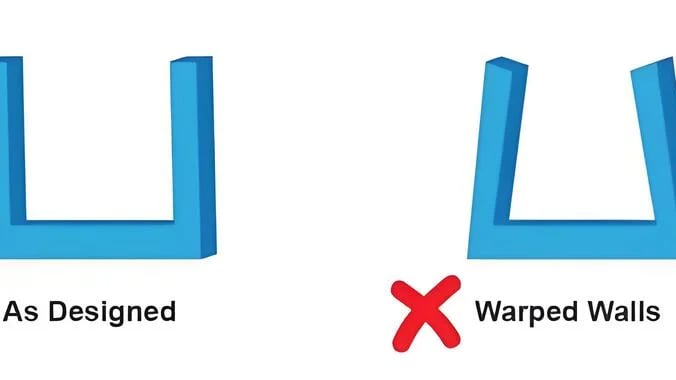
Importance of Draft Angles
Draft angles are essential in mold design, aiding in easy removal of the part from the mold. A well-calculated draft angle helps minimize friction between the part and the mold walls, reducing the chances of damaging either. The interacting angle setting6 plays a critical role here, as the angle of the parting surface can influence how the draft angle functions.
Collaborative Angle Settings
The alignment of parting surfaces with draft angles ensures that the product detaches smoothly. For complex designs, it is vital that these angles work together harmoniously. When designing molds for products with intricate shapes, the angle matching should be carefully evaluated to avoid complications during mold release. Consider using simulation tools to optimize these settings for ensuring smooth mold release7.
Design to Avoid Interference
Interference between the product and the mold during release can lead to defects or damage. Designing with adequate clearance and precise angles can prevent such issues. For instance, when the parting surface angle is large, ensure the draft angle complements it to avoid friction during demolding. Testing and simulation in the design phase can help identify potential problems, allowing for adjustments before production begins.
Use of Mold Release Agents
Choosing appropriate mold release agents can significantly ease the demolding process. These agents create a barrier between the mold and the product, reducing adhesion and facilitating a smooth release. It is important to select an agent that is compatible with both the material of the mold and the product, ensuring no adverse chemical reactions occur. For more details on selecting suitable release agents, consider exploring mold release methods8.
Parting surface angle affects draft angle effectiveness.True
The parting surface angle influences the starting direction and range of draft angles.
Improper angles can cause mold and product interference.True
Incorrect angle design may lead to product collision with the mold during demolding.
How Do Parting and Draft Angles Differ Across Various Molding Processes?
Understanding the interaction between parting and draft angles is crucial for efficient mold design and manufacturing.
Parting angles define the separation line of the mold, while draft angles ensure smooth demolding. They differ across molding processes in terms of complexity and application, with injection molding requiring precise angle matching to avoid interference. Each process demands unique angle considerations for optimal mold release.
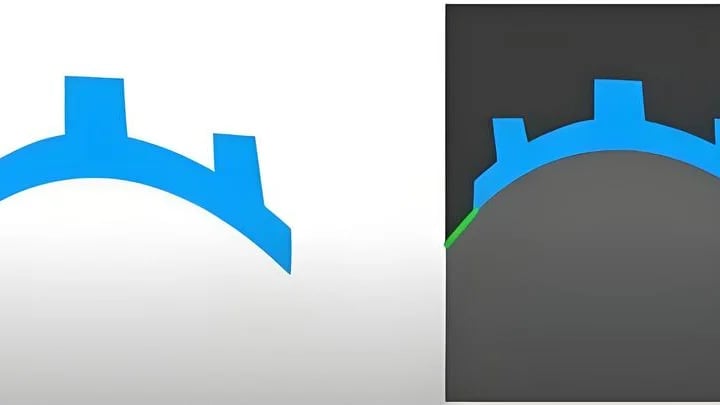
The Role of Parting and Draft Angles in Mold Design
In any molding process, understanding the interplay between parting surfaces9 and draft angles is key. The parting surface angle sets the foundation upon which the draft angle functions. For instance, in injection molding, an inclined parting surface requires careful calculation of the combined angle to ensure smooth product release. This can be particularly challenging for complex shapes.
Angle Integration in Different Molding Processes
When examining various molding processes, each has its unique requirements for angle integration. For example, in compression molding10, the focus might be on larger draft angles to accommodate thicker materials. Conversely, die casting11 typically involves tighter angle tolerances due to the high precision required.
Ensuring Smooth Mold Release
Collaboration between angles is essential to avoid product interference during mold release. In injection molding, precise alignment of the parting surface and draft angle is crucial. A mismatch might lead to product sticking or damage during demolding. Simulations often help designers find the optimal angles to ensure smooth release.
Avoiding Interference Through Design Adjustments
One of the main challenges in mold design is avoiding interference. An excessively large parting surface angle combined with a small draft angle could cause friction or collision, damaging both product and mold. Therefore, precise simulations and adjustments are necessary to achieve an efficient design across different processes like rotational molding12. These adjustments also consider material flow and cooling rates, which influence the final product quality.
Parting surface angle affects draft angle effectiveness.True
The parting surface angle influences the starting direction and range of the draft angle.
Draft angle mismatches can cause mold release interference.True
Incorrect design of angles may lead to product and mold interference during release.
Conclusion
The parting surface angle significantly influences the draft angle in mold design, affecting demolding efficiency and product integrity. Proper calculations prevent interference and ensure smooth mold release.
-
Learn how parting surface angles affect draft angles. ↩
-
Explore how these angles ensure smooth mold release. ↩
-
Understand how correct angles prevent mold-product collisions. ↩
-
Learn how optimal draft angles enhance mold design efficiency. ↩
-
Discover how draft angles impact manufacturing outcomes. ↩
-
Understand how parting surface angles affect draft angles in mold design. ↩
-
Learn how matching angles in design aids in seamless mold release. ↩
-
Discover top agents that facilitate smoother mold releases. ↩
-
Explore how parting surfaces affect mold efficiency and product quality. ↩
-
Understand how draft angles accommodate material thickness in compression molding. ↩
-
Learn about precision requirements for angles in die casting processes. ↩
-
Discover design strategies to avoid interference in rotational molding. ↩