Every day in my world, molding feels like cracking a new puzzle. The part where the mold separates holds the essential clue.
Determining the parting line in molding involves considering factors like part geometry, mold design, and aesthetics. The parting line should be placed where it minimizes visible seams, facilitates easy ejection, and ensures proper material flow, while maintaining mold strength and reducing production costs.
When I began working with molds, I found that positioning the parting line correctly was critical for success. It’s really not only about technical accuracy. It’s about imagining how each decision affects the whole manufacturing process. These choices impact the look and function of the product. Each new design brings lessons from past experiences. A well-placed parting line can turn a good design into an excellent product. Let’s look at these strategies together. I’ll share some insights and tips that I discovered along my journey.
The parting line affects the product's appearance.True
Improper parting line placement can lead to visible seams or defects.
Parting lines are irrelevant to mold release.False
Correct parting line placement facilitates smooth mold release.
What factors should I consider when choosing a parting line location?
Have you ever looked at a mold design and wondered where to put the hard-to-find parting line? This choice is really important. It changes how the mold looks and how it works.
Selecting the right place for the parting line needs balancing the product’s shape, look and job with how easy it is to make. This lets the mold come out smoothly during injection molding. Material flow must be very effective too.
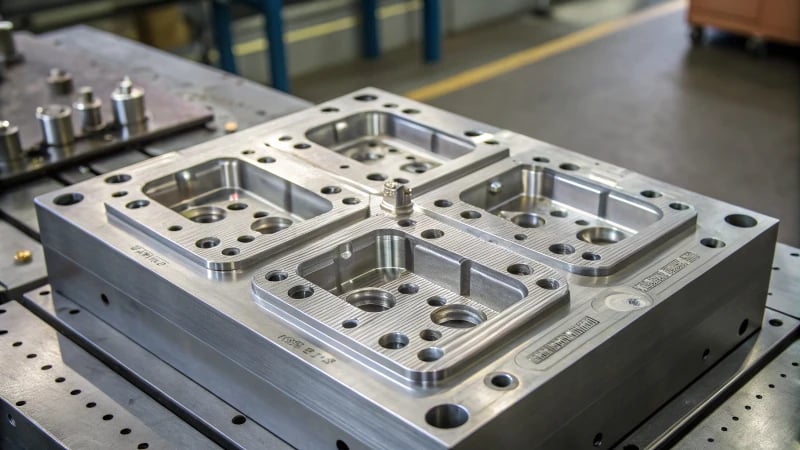
Product Shape and Structure
I remember the first time I decided on a parting line for a project. It felt like fitting pieces of a puzzle together without leaving ugly seams. For products where looks are really important, like sleek rectangular boxes, the parting line should stay hidden. Maybe place it at the bottom or the back. For decorative items with elegant curves, set the line along the curve. This makes it almost invisible.
Looks are important, but so is functionality. A misplaced parting line might cause big problems. I learned this with a plastic bottle cap. The line crossed the sealing surface, leading to leaks and unhappy customers. It’s vital to position it away from important areas.
Manufacturing and Processing Ease
I always believe simplicity is very important in manufacturing. Choosing parting line spots that match regular mold surfaces saves a lot of trouble and money. I worked on a cylindrical product once; an axial parting line made everything simpler and more cost-effective. Complicated lines, on the other hand, can increase costs and wear molds out faster.
Demolding has its own challenges. The parting line needs to help in releasing the product smoothly from the mold. You should align it with the demolding direction.
Injection Molding Processability
Ah, injection molding! It’s where the magic really happens—or where problems start if the material flow isn’t right. I remember sleepless nights worrying about trapped air or uneven filling in thin-walled products. The trick is choosing the parting line spot to let the melt flow evenly across cavities.
Gate position is also crucial; it’s like a dance between the gate and the parting line to guide plastic flow correctly. A side gate needs the parting line on the same side for smooth flow.
Consideration | Key Factor |
---|---|
Appearance | Discreet placement on less visible product areas |
Functionality | Avoid critical function areas like sealing surfaces |
Manufacturing Ease | Use simple parting surfaces for cost-effective mold design |
Demolding | Align parting with demolding direction |
Flow Characteristics | Ensure uniform plastic melt flow |
Gate Position | Coordinate with parting line for effective cavity filling |
Considering these factors leads to both beautiful and functional products while improving production processes efficiently1. Whether designing efficient items or creating something beautiful, these elements are your guides in environments like injection molding2.
Parting lines should be on visible product areas.False
Parting lines should be discreetly placed on less visible areas.
Aligning parting lines with demolding direction aids release.True
Proper alignment facilitates smooth product release during demolding.
Why does product shape affect parting line placement?
Have you ever wondered how your product’s shape affects the placement of those annoying parting lines? Learn how product design influences both the looks and usability of your creation. A really good design improves aesthetics. A poor design ruins functionality.
The shape of a product determines where the parting line goes. It affects both how the product looks and how it works. Curved designs cleverly conceal lines along tangents. Rectangular shapes probably hide lines in less obvious places. Lines must stay away from seals and moving parts for the product to work well. This is very important. Efficiency depends on it.
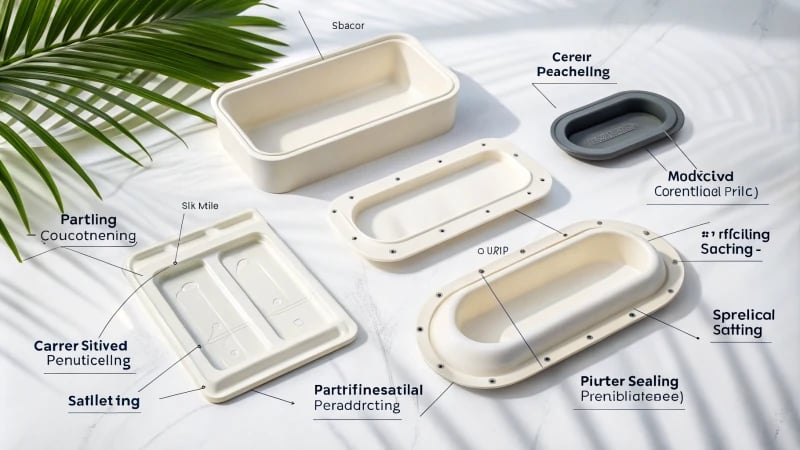
Appearance and Aesthetics
I have spent many hours working on product designs. Beauty must meet practicality. When working with a rectangular gadget, I often place the parting line3 at the bottom or back. This placement avoids a visible seam that might ruin a sleek look.
Curves provide an ideal setting to hide these lines. Lines run along the curve so they become a part of the design. Curves really create magic by leveraging the product’s natural lines for concealment.
Functional Integrity
Once, I worked on designing a bottle cap. I learned that parting line placement is crucial for function. If the line is on the sealing surface, leaks can occur. Now I always put it on the side or top to ensure functional efficiency remains intact.
Complex designs with moving parts also need careful line placement. The line should never interfere with gears or hinges to prevent operational interference and keep everything working smoothly.
Manufacturing Simplicity
I have seen what happens when parting surfaces complicate things. Keeping it simple, like using an axial line on a cylinder, avoids problems and simplifies production processes.
Shape Type | Recommended Parting Line Strategy |
---|---|
Rectangular | Place at back or bottom |
Curved | Align with curvature tangent |
Cylindrical | Use axial alignment |
Simplicity in lines also makes production easier as complex lines cost more and reduce mold life due to increased complexity.
Processability in Injection Molding
I once struggled with thin-walled designs and air traps. The secret is making the plastic flow evenly. Strategic parting line placement helps ensure even cavity filling, reducing defects like air traps.
Matching gate and line positions can probably change everything; they reduce flaws and improve product quality4. For example, pairing a side gate with a same-side parting line enhances product quality by guiding plastic flow effectively.
Understanding these details is very important—it is like cracking a secret code for creating molds that work well and look great.
Parting lines on bottle caps should be on the sealing surface.False
Placing parting lines on sealing surfaces can compromise sealing efficacy.
Curved product designs benefit from tangent-aligned parting lines.True
Aligning parting lines with curvature tangents helps conceal them effectively.
Why Is Manufacturing Ease Important in Parting Line Design?
Have you ever thought about why some designs simplify production while others cause problems?
Designers find it easy to create parting lines in manufacturing. This approach leads to smooth mold creation and removal. Smooth molds save money and improve product quality. Designers also think about shape, look and function. Designers optimize the production process. It is very efficient.
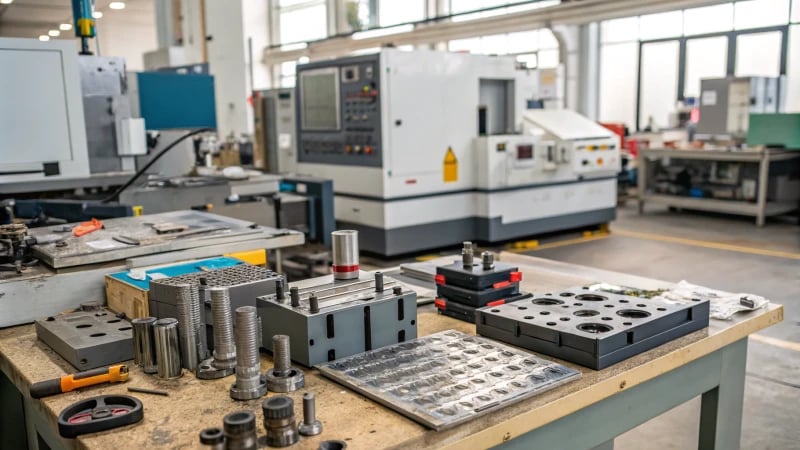
Understanding the Role of Parting Line Design
When I began examining the details of mold design, one thing became very clear: the parting line is much more than just a seam. It is the place where the two halves of a mold join, and its location affects the manufacturing process significantly. I realized that placing these lines wisely improves both the appearance and function of the final product.
By considering the shape and structure of the product5, manufacturers can strategically place parting lines to enhance both appearance and functionality.
Aspect | Consideration |
---|---|
Appearance | Place parting lines in inconspicuous areas like the back or bottom for rectangular enclosures. |
Functionality | Avoid placing lines on sealing surfaces to maintain product integrity. |
Importance of Simple Parting Surfaces
I remember working on a round product and understood that picking an axial parting line simplified everything. Simplicity in design aids in construction and makes maintenance easier too. Too complicated designs cause problems; they make the mold’s manufacturing process troublesome, decreasing its accuracy and service life6.
- Ease of Mold Release: Smooth removal of parts from molds is essential. Ensure parting lines allow for smooth demolding by aligning with the mold’s opening direction to avoid possible damage during release.
Processability in Injection Molding
During my time with injection molding, I noticed the importance of plastic flow inside the mold. Well-placed parting lines help plastic fill the mold evenly, reducing flaws such as trapped air.
- Flow Characteristics: Thin-walled products need thoughtful line placement; positioning parting lines at the end of melt flow aids uniform filling.
- Gate Position Impact: The combination of parting lines and gate positions defines the path of melt flow, directly affecting product quality7.
Carefully refining these design choices improves production efficiency remarkably. Designers can achieve higher product quality and effectiveness in manufacturing processes, ensuring every design choice becomes important.
Parting lines affect mold release ease.True
Proper parting line placement ensures smooth demolding, preventing damage.
Complex parting surfaces reduce manufacturing costs.False
Complex designs increase mold difficulty and cost, impacting accuracy and lifespan.
How Do Gate Position and Plastic Flow Affect Parting Lines?
Have you ever wondered why some plastic products appear perfect while others show ugly lines? The secret is in the gate position and how plastic flows during mold design. Maybe this is new information for you. The way the plastic moves really matters.
Gate position controls plastic movement inside the mold. This decision importantly influences where the parting line sits. Aligning gates with flow directions helps reduce flaws. This alignment results in a very smooth and seamless product appearance. A smooth appearance is really important.
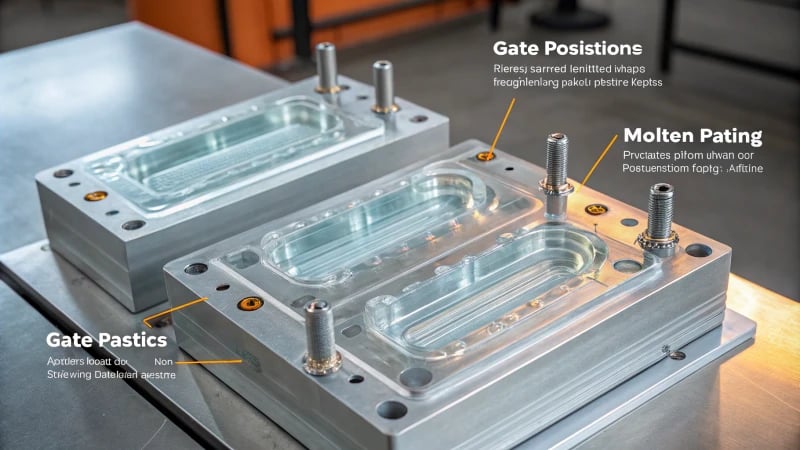
Gate Position’s Role in Mold Design
In injection molding, the gate acts as the entry point for molten plastic into the mold cavity. Its position dictates how the plastic flows, impacting where the parting line forms. Aligning the gate with flow paths ensures even filling, reducing defects like air traps and short shots.
I remember my first project with a rectangular plastic box8. Placing the gate near corners seemed simple but took time to understand how this guided flow toward the center. This ensured even filling and reduced defects like trapped air. Aligning the gate with natural flow paths produces a uniform and attractive parting line.
For example, putting the gate near corners may make parting lines disappear on visually appealing products. It’s like a magician’s trick with plastic! Understanding how gate positions control flow is crucial as it affects where parting lines form.
Plastic Flow Dynamics
Flow dynamics are fascinating. Imagine water moving through a garden hose; it doesn’t just rush straight but swirls and changes course due to obstacles and bends. Molten plastic moves similarly. Knowing these flow characteristics helps place parting lines where they’re not noticeable.
I worked on a decorative item with intricate curves. Aligning the parting lines along these curves kept it visually elegant, much like solving a puzzle where each piece fit perfectly.
Balancing Functionality and Appearance
A balance between appearance and function is a regular challenge in design. Consider plastic bottle caps—no parting line should disrupt the sealing surface to keep liquids securely inside.
Strategic parting line placement can really improve both looks and function. Whether it’s on the side of a cap or away from essential areas in parts like gears or hinges, every choice leads to a flawless product.
Design Aspect | Considerations |
---|---|
Appearance Requirements | Hide lines in inconspicuous areas or along curves |
Functional Requirements | Avoid lines on critical or moving sections |
Ease of Manufacturing | Simplify mold designs for cost-effectiveness |
Ease of Mold Release | Align parting line with demolding direction |
Ease of Manufacturing
Simple mold design greatly influences manufacturing ease. I learned this by working on cylindrical products; using axial parting lines made the manufacturing process simple and reduced costs.
However, complex designs with twisted surfaces increase difficulty and expenses. Tools like flow simulation tools9 have been very helpful as they show how plastic fills a cavity, helping me adjust gate positions wisely.
Each mold release should feel smooth and effortless, like a dance move. Aligning parting lines with removal directions is important to ensure each product comes out as planned, reducing surprises and increasing quality.
Gate position affects parting line visibility.True
Gate placement influences plastic flow, affecting parting line visibility.
Parting lines should be on sealing surfaces for better function.False
Parting lines on seals can compromise functionality, so they're avoided.
Conclusion
Determining the parting line in molding involves balancing product shape, aesthetics, functionality, and manufacturing ease to enhance appearance and ensure effective mold release.
-
Learn about methods to enhance efficiency in product manufacturing through strategic design choices. ↩
-
Understand why injection molding is pivotal in manufacturing and how it impacts design choices. ↩
-
Discover why strategic parting line placement is critical in maintaining both the aesthetics and function of products. ↩
-
Learn how aligning gate positions with parting lines can enhance product quality and minimize manufacturing defects. ↩
-
Discover how strategic parting line placement can enhance product aesthetics while maintaining functionality. ↩
-
Learn about how complex mold designs can increase costs and affect manufacturing efficiency. ↩
-
Understand how aligning gate positions with parting lines improves plastic flow and product quality. ↩
-
Explore why strategic gate placement enhances product quality and minimizes visual defects in molded parts. ↩
-
Discover tools that help designers visualize and optimize plastic flow within molds. ↩