Have you ever thought about how some materials survive in the toughest situations? Meet PA46!
PA46 is a high-performance polyamide known for its excellent mechanical properties, high temperature resilience, and ease of processing. Used widely in automotive and electronics, its unique attributes make it ideal for applications requiring strength and durability under stress.
Knowing the basics helps. Digging deeper into PA46‘s special features and ways to use and process it probably opens up more possibilities in your projects. Learn more to see how PA46 really upgrades your engineering solutions.
PA46 has a melting point of 295°C.True
PA46's melting point is about 295°C, permitting high-temperature strength.
What Are the Key Properties of PA46 That Enhance Its Performance?
PA46 finds popularity in different fields because of its excellent qualities.
PA46 stands out due to its exceptional mechanical strength, high temperature tolerance, low friction, and excellent fluidity. These properties make it a preferred choice for applications requiring durability and precision under challenging conditions.
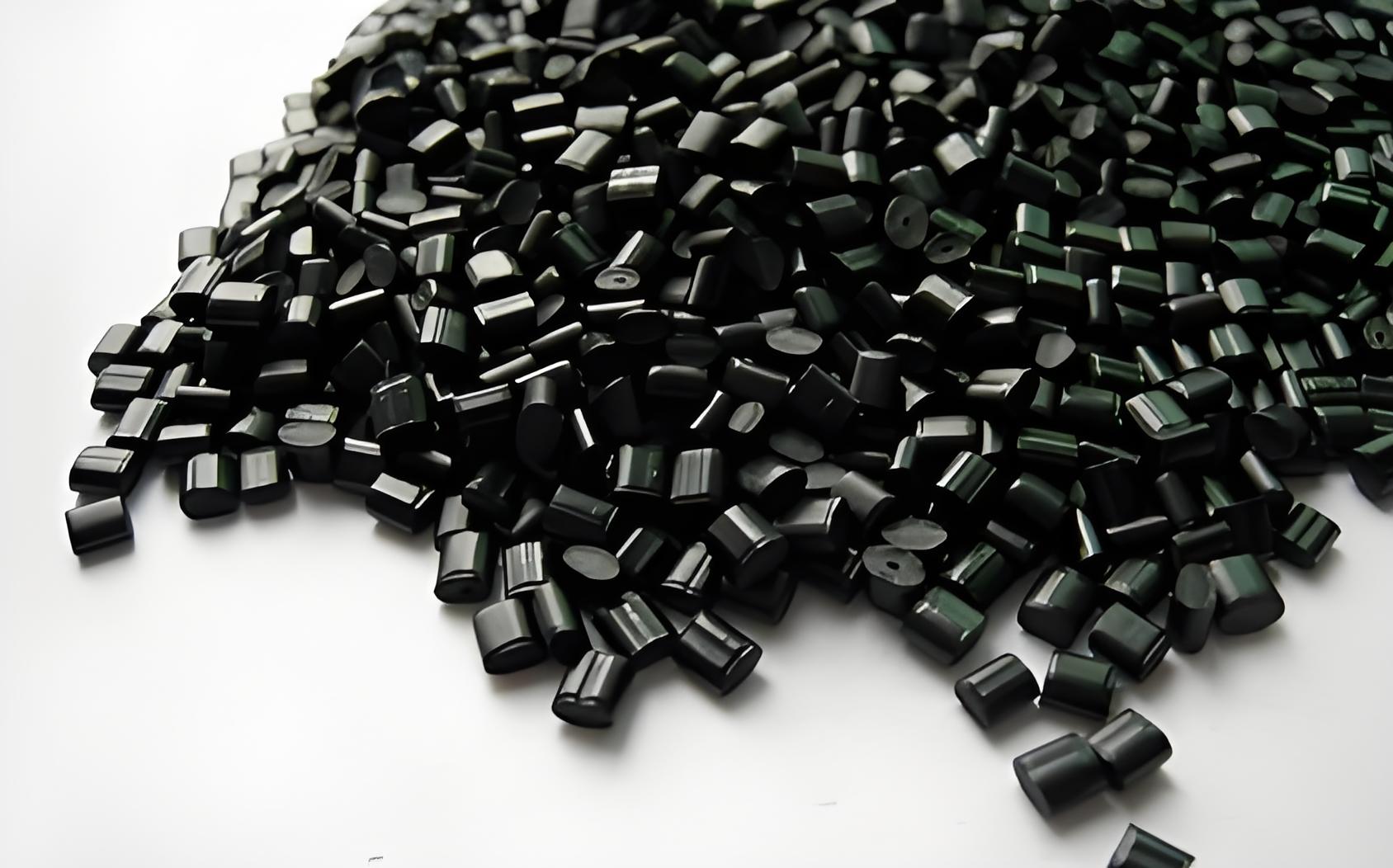
Mechanical Properties of PA46
PA46, known scientifically as polyhexanediylbutanediamine, is a high-performance polyamide resin. This material boasts impressive tensile strength, ranging from 150 to 200 MPa, and bending strength between 200 to 250 MPa. Such mechanical robustness1 makes it ideal for components subjected to high stress.
- Impact Strength: Unnotched impact strength reaches up to 80 kJ/m², while notched impacts register between 5 and 10 kJ/m². This ensures resilience against sudden forces.
Thermal Properties of PA46
PA46‘s melting point hovers around 295°C, allowing it to withstand high-temperature environments without losing integrity. Its long-term service temperature caps at 160°C, making it a reliable material for automotive and industrial applications.
- Heat Distortion: Between 190 to 210°C, which safeguards its structural stability under thermal stress.
Processing Advantages
The ease of processing PA46 is another standout feature. It offers excellent fluidity and can be molded into complex shapes with ease. PA46 exhibits high stiffness retention, even in thin-walled parts as slim as 0.1 mm, showcasing its versatility and precision in manufacturing.
- Shrinkage and Water Absorption: With shrinkage rates between 1.5% and 2.5% and low water absorption below 1.5%, PA46 ensures dimensional stability over time.
Comparative Advantage Over Other Materials
When compared to PA6 and PA66, PA46 provides higher heat resistance and faster crystallization. Against PPS, it presents better toughness and moldability, lending itself to intricate designs without compromising on quality.
Applications in Industry
Widely adopted in the automotive sector, PA46 is used for engine parts, transmission systems, and electrical components due to its superior wear resistance and low friction. Its application extends to electronics, manufacturing connectors and switches due to its high dielectric strength.
Explore More on PA46‘s Applications2 to understand how this remarkable material is shaping modern engineering solutions.
PA46 has a melting point of 295°C.True
PA46's high melting temperature lets it endure very high heat.
PA46 absorbs more than 2% water.False
PA46 takes in less than 1.5% water, which gives it good shape stability.
How Does PA46 Compare to Other High-Performance Polymers?
Thinking about top-quality polymers for your task? Discover how PA46 compares with others.
PA46 offers superior high-temperature performance, mechanical strength, and ease of processing compared to other polymers like PA6, PA66, and PPS. Its unique blend of properties makes it ideal for demanding applications in automotive and industrial sectors.
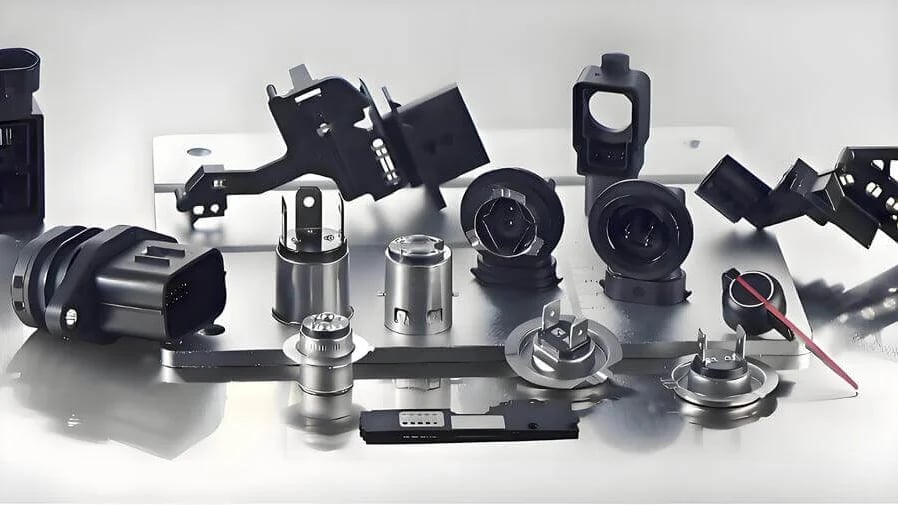
Comparing Mechanical Properties
When examining the mechanical properties, PA46 exhibits impressive tensile and bending strengths ranging from 150 to 200 MPa and 200 to 250 MPa, respectively. This makes it a robust option for applications demanding high strength and rigidity. In comparison, PA6 and PA663 tend to have lower tensile strength, making PA46 preferable where mechanical endurance is critical.
Mechanical Properties Table:
Property | PA46 | PA6 | PA66 |
---|---|---|---|
Tensile Strength | 150-200 MPa | 80-110 MPa | 90-120 MPa |
Bending Strength | 200-250 MPa | 100-150 MPa | 120-170 MPa |
Thermal Performance Evaluation
One of PA46’s standout features is its thermal resilience. With a melting point of about 295°C and a long-term service temperature up to 160°C, it surpasses many other polymers. While PPS4 is known for high heat resistance, PA46 offers better toughness and less brittleness, which is vital in environments with fluctuating temperatures.
Thermal Properties Comparison:
Property | PA46 | PPS |
---|---|---|
Melting Point | 295°C | 280°C |
Service Temperature | 160°C | 150°C |
Heat Distortion Temp. | 190-210°C | 160°C |
Processing and Application Advantages
PA46 is celebrated for its superior fluidity, making it easier to process than many alternatives. This feature is particularly advantageous when molding complex shapes or thin-walled parts as small as 0.1 mm without fretting. The polymer also supports faster crystallization and shorter molding cycles, which can significantly improve production efficiency.
In automotive applications, PA46‘s ability to withstand high temperatures and its excellent wear resistance make it ideal for components like engine parts and transmission systems. In comparison, PA6 and PA66 are less suited for such high-temperature demands, although they may be adequate for less demanding roles.
Chemical Resistance
The chemical resistance of PA46 also sets it apart. It withstands a wide array of chemicals better than some of its peers, making it suitable for use in harsh environments. This characteristic is crucial for industrial applications where exposure to various substances is common.
In conclusion, while each polymer has its niche, PA46 stands out for high-temperature applications requiring excellent mechanical properties and processing ease. Whether in automotive, electronics, or industrial sectors, its advantages make it a strong candidate for challenging environments.
PA46 has higher tensile strength than PA66.True
PA46's tensile strength goes from 150 to 200 MPa, but PA66 is between 90 and 120 MPa.
PPS has a higher melting point than PA46.False
PA46 liquefies at 295°C, surpassing PPS's 280°C melting threshold.
What Are the Best Practices for Designing PA46 Molded Parts?
Creating PA46 molded pieces needs a focus on its special qualities and technical aspects for best function.
To design effective PA46 molded parts, focus on maintaining uniform wall thickness, incorporate reinforcement features, use appropriate mold materials, and optimize injection parameters. Understanding PA46‘s mechanical and thermal properties is crucial for enhancing product durability and efficiency.

Using Learning PA46 Properties for Design
When creating parts with PA46, understanding its special features is very important. This strong polyamide shows great strength at high temperatures, excellent wear resistance, and impressive flow. Such traits make it ideal for tough uses in cars and electronics.
Strength and Heat Properties
PA46 shows high pull strength, usually from 150-200 MPa. Its bending strength is also 200-250 MPa, proving its toughness under pressure. The melting point is around 295°C and the heat distortion temperature is 190-210°C, supporting temperatures up to 160°C in the long run.
Top Design Suggestions
Even Wall Thickness
Keeping a consistent wall thickness in PA46 parts helps lower stress points and avoids warping. The wall should not be too thick or too thin. Thick walls take longer to cool and shrink unevenly, while thin walls might not be strong enough.
Strengthening Features
Adding good reinforcement parts can greatly improve strength and stiffness while using materials wisely. The reinforcement should be 0.5-0.7 times the wall thickness, carefully considering height to avoid shrinking problems.
Corner and Edge Design
Smooth corners help lower stress points, increasing part strength. Usually, these corners should have a round edge of 0.2-0.5 times the wall thickness. This idea boosts how the part works and lasts longer.
Mold Material and Injection Molding Settings
Choosing Mold Materials
For PA46, using mold steels like H13 or S136 is wise because of their great heat and wear resistance. Picking the right mold steel is really important for lasting performance, especially in large-scale production.
Adjusting Injection Conditions
Key conditions like pressure, speed, and temperature need careful tuning for PA46. Pressure generally ranges from 80-150 MPa to fill molds properly at speeds of 50-100 mm/s. A mold temperature of 80-120°C with good cooling time helps reach a high-quality finish.
Following these suggestions can greatly improve how PA46 parts work and last. For more details or insights into PA46, check out special resources on injection molding tips5 or PA46 material handling6.
PA46 has a melting point of around 295°C.True
PA46's melting point reaches roughly 295°C, helping with very high-temperature uses.
Uniform wall thickness in PA46 parts prevents warping.True
Keeping even wall thickness assists in lowering stress and twisting in PA46 components.
How Can You Optimize PA46 Injection Molding Processes?
Improving PA46 injection shaping probably leads to better quality and higher efficiency in your factory.
To optimize PA46 injection molding, focus on precise control of processing parameters like drying, temperature, and pressure. Ensure proper mold design to maintain uniform wall thickness and incorporate reinforcements. Select suitable equipment and materials to improve product quality and reduce defects.
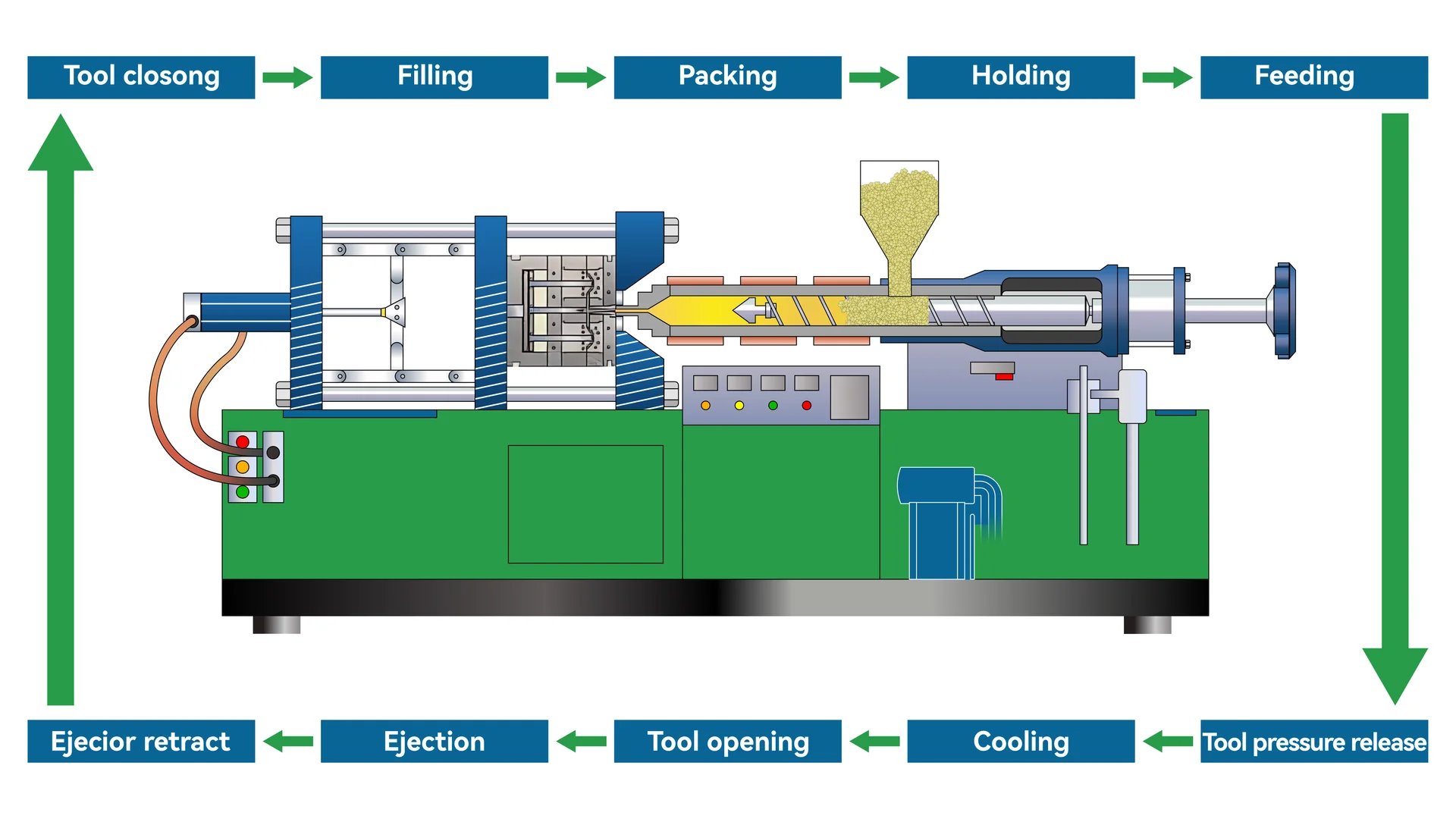
Importance of Preparing Before PA46 Injection Molding
Planning well is key for good results in PA46 injection molding7. Picking the right PA46 material is very important because different brands and types suit different product needs. Drying the material removes water and stops problems like bubbles. Best drying involves heating at 100-120°C for 4-6 hours, with moisture less than 0.05%.
Store materials safely. Keep PA46 in cool, dry places below 25°C with humidity under 50% to keep it strong.
Adjusting Equipment and Settings
Choose a suitable injection molding machine based on the product’s size and weight. Important settings include:
- Injection Pressure: Usually between 80 – 150 MPa, adjusted for the specific product.
- Injection Speed: Fast speed (50 – 100 mm/s) helps quick cavity filling.
- Screw Speed: Moderate speed (50 – 100 rpm) helps mix the material well.
- Mold Temperature: Set between 80 – 120°C based on the product.
- Cooling Time: Varies with size and thickness, usually 10 – 30 seconds.
Mold Design Tips
Good mold design improves PA46 injection molding efficiency8. Even wall thickness lowers the risk of stress. Reinforcing adds strength with less material. Tips are:
- Wall Thickness: Balance is key; too thick cools slowly, too thin may break.
- Reinforcement Design: Make it 0.5 – 0.7 of wall thickness, keep height controlled.
- Rounded Corners: Make radius 0.2 – 0.5 of wall thickness to lower stress.
Table: Suggested Molding Settings for PA46
Setting | Suggested Range |
---|---|
Injection Pressure | 80 – 150 MPa |
Injection Speed | 50 – 100 mm/s |
Screw Speed | 50 – 100 rpm |
Mold Temperature | 80 – 120°C |
Cooling Time | 10 – 30 seconds |
Following these tips probably improves the quality and function9 of PA46 molded items.
Drying PA46 at 80°C for 2 hours is optimal.False
Best drying for PA46 involves 100-120°C over 4-6 hours.
Injection pressure should be 80-150 MPa for PA46.True
The suggested pressure for injecting PA46 falls between 80-150 MPa.
Conclusion
Welcome the strong features of PA46 for your next engineering task. Knowing its qualities might raise your product’s performance and efficiency.
-
Learn about the mechanical strength attributes of PA46.: It has excellent wear resistance, outstanding level of stiffness, good electrical insulation properties and high chemical resistance. ↩
-
Discover how PA46 is utilized across various sectors.: This combination makes the material ideal for high-temperature applications due to excellent mechanics as well as wear and friction behavior. ↩
-
Understand how PA6 and PA66 compare in mechanical strength.: Although they have a similar set of properties, there are still slight differences. PA6 has slightly lower temperature resistance than PA66 and is also … ↩
-
Learn why PA46 excels in thermal resilience over PPS.: It is known that high thermal resistant polymer such as PPS and PA46 are used in automotive industry as products (such as fuel injection … ↩
-
Gain deeper insights into advanced PA46 injection molding techniques.: Adding 30% glass fiber to PA plastic can effectively improve the mechanical properties, heat resistance and aging resistance of PA injection … ↩
-
Explore best practices for handling and processing PA46 material.: Use low or moderate holding pressures in case of cushion variations. ▫ Use reverse tapered nozzles. Adjust nozzle temperature (but do not set too low) to avoid … ↩
-
Learn effective pre-preparation strategies for optimizing PA46 injection molding.: 1.Mold Preparation: The mold is prepared by cleaning and lubricating its surfaces to ensure smooth part ejection and prevent defects. 2.Material … ↩
-
Explore design techniques that enhance the efficiency of PA46 molding.: Guidelines for injection molding mold design · 1. The shape of the hole should be as simple as possible, generally take the round. · 2. The axial … ↩
-
Find methods to improve the quality of PA46 molded products.: Establish and adhere to rigorous quality assurance checks and tests to guarantee that injection molded parts meet required standards. Any flaws … ↩