Injection molding is not just a process; it’s an art form where precision reigns supreme. One of the most critical brushes in this artistry is wall thickness distribution.
To optimize wall thickness distribution in injection molded products, ensure uniform thickness during design, strategically place gates in molds, and carefully adjust injection speeds. These strategies reduce defects like warping and improve product quality.
While this initial answer gives you a solid starting point, let’s dive deeper into each stage of design and manufacturing to uncover nuanced approaches that can further enhance your product’s performance.
Uniform wall thickness reduces warping in injection molded products.True
Uniform thickness ensures even cooling, minimizing internal stress and defects.
How Does Product Design Impact Wall Thickness Distribution?
In the realm of injection molding, product design plays a pivotal role in determining the wall thickness distribution, affecting both structural integrity and aesthetic appeal.
Effective product design ensures uniform wall thickness by minimizing stress concentrations, optimizing structure, and planning gradual transitions. This enhances strength and reduces defects.
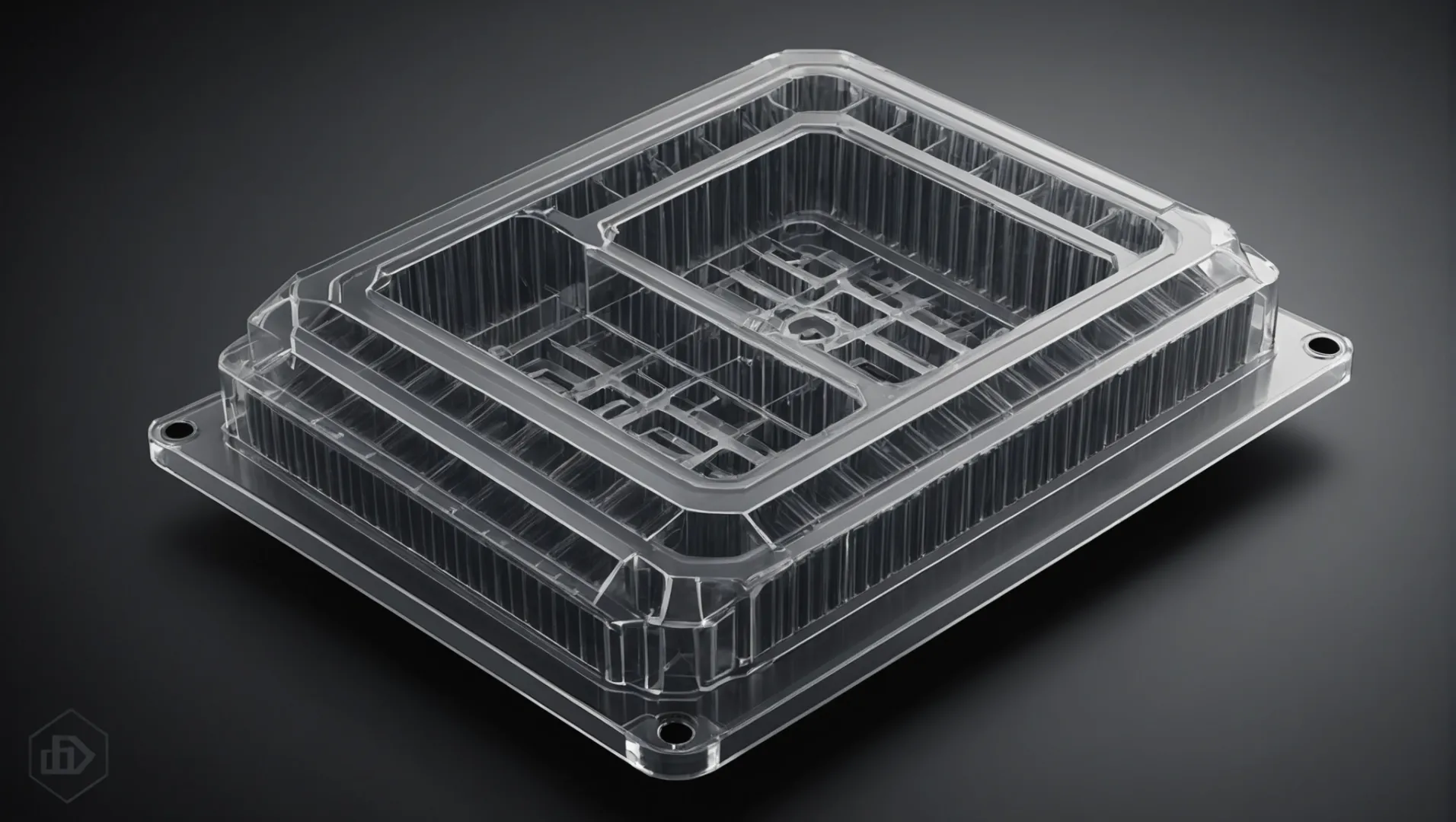
Importance of Uniform Wall Thickness
Uniform wall thickness is crucial in injection molding1 because it prevents stress concentrations, ensures even cooling, and reduces warping. Inconsistent thickness can lead to defects such as sink marks, voids, and internal stresses that compromise product quality and durability.
Designing for Uniformity
1. Consistent Thickness Design
Designers should aim for a consistent wall thickness across the product. This approach helps maintain even cooling rates and minimizes internal stresses. For complex shapes, a gradual transition from thick to thin sections can be used to reduce stress concentration points.
2. Streamlined Product Structure
Eliminating unnecessary structures such as ribs and bosses is crucial as these can create localized thickness variations. When such features are necessary, they should be kept as thin and evenly distributed as possible to maintain uniform cooling and shrinkage.
Design Element | Potential Impact | Optimization Strategy |
---|---|---|
Ribs & Bosses | Increased local thickness | Minimize thickness and distribute evenly |
Demoulding Slope | Uneven wall thickness | Optimize demoulding direction |
Structural Optimization
1. Gradual Transitions
Gradual transitions in wall thickness are essential in areas with complex geometries. This design strategy not only aids in reducing stress concentrations but also helps in achieving smoother material flow during the molding process.
2. Strategic Demoulding Direction
The demoulding direction should be carefully considered to prevent uneven wall thickness caused by the slope of the mold. Proper orientation ensures that the part releases easily without causing additional stress or distortion.
Product design is just the first step in optimizing wall thickness distribution. Other factors such as mold design and material selection also significantly contribute to achieving an ideal balance. For further insights into these aspects, explore mold design strategies2 and material selection considerations3.
Uniform wall thickness reduces warping in injection molding.True
Consistent thickness ensures even cooling, minimizing warping issues.
Ribs and bosses should be thick for structural strength.False
Thick ribs can cause stress; they should be thin and evenly distributed.
What Role Does Mold Design Play in Achieving Uniform Wall Thickness?
Mold design is pivotal in ensuring uniform wall thickness in injection molded products, influencing quality and performance.
Mold design critically impacts wall thickness uniformity by determining gate placement, cooling system effectiveness, and cavity surface treatment. Properly designed molds ensure even melt flow and cooling, minimizing defects like warping and internal stress.
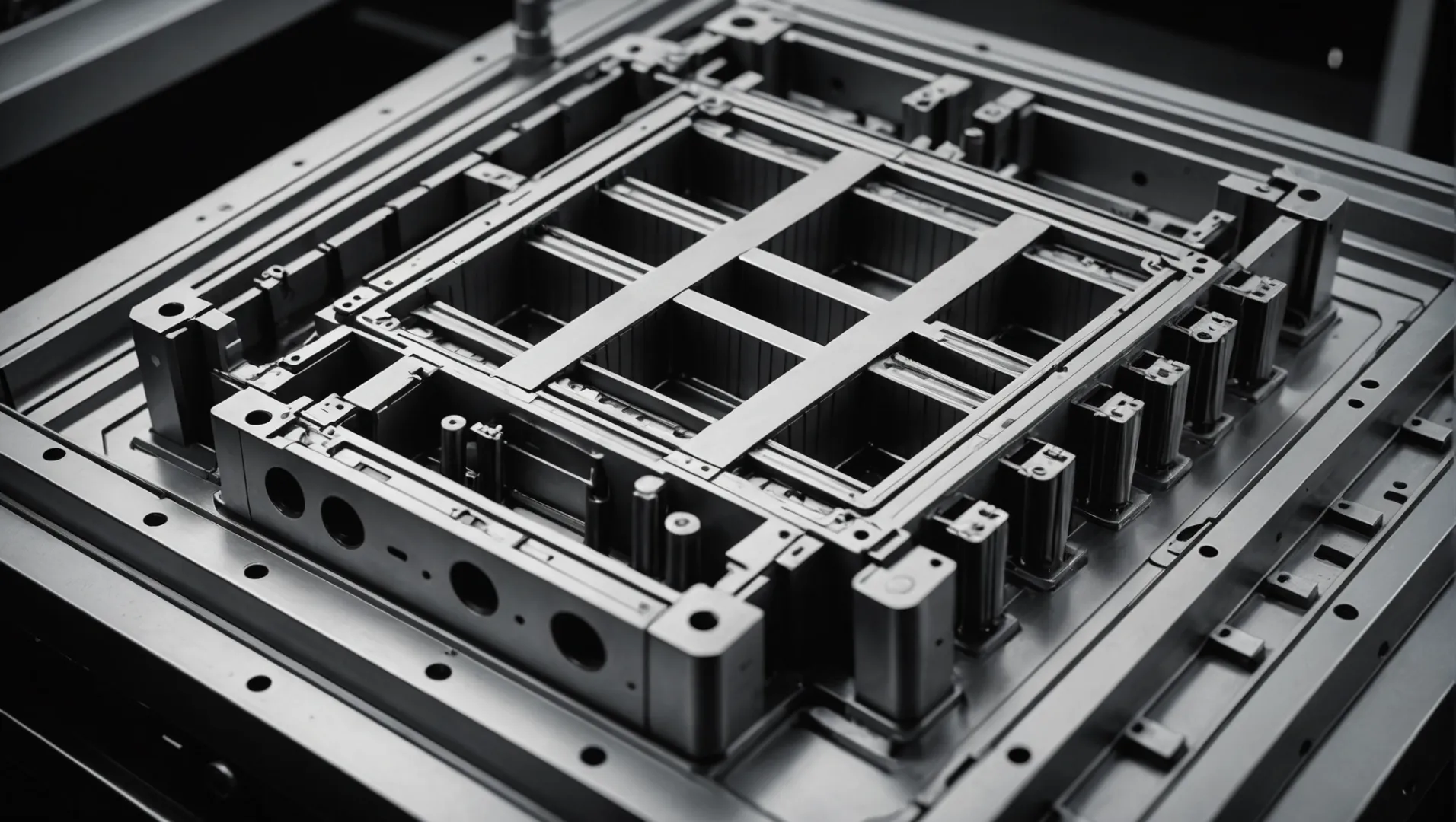
Gate Location and Number Selection
Choosing the right gate location is crucial. Gates should be placed in areas with thicker wall sections to promote uniform filling. Multiple gates or advanced technologies like hot runner systems can be employed to enhance melt distribution. These techniques help maintain a balanced flow, reducing the risk of uneven wall thickness.
Cooling System Optimization
An effective cooling system is integral to achieving uniform wall thickness. The arrangement of cooling channels should be strategic, especially in areas prone to thicker walls. Advanced cooling methods such as jet cooling can be utilized to maintain consistent temperatures throughout the mold, mitigating shrinkage and warping issues.
Cooling Method | Benefits |
---|---|
Jet Cooling | Rapid and uniform cooling |
Heat Pipe Cooling | Efficient heat transfer |
Surface Treatment of Mold Cavities
The surface finish of mold cavities affects how evenly the melt flows and cools. Polishing the cavity surface reduces resistance, promoting uniform wall thickness. Special coatings or textures can be applied to further control melt behavior during filling and cooling, enhancing product consistency.
Case Study: Implementing Multi-Point Gates
Consider a scenario where a complex part requires consistent wall thickness to avoid functional failure. By implementing a multi-point gate system4, engineers ensured the melt reached all sections of the cavity simultaneously, significantly reducing warping incidents.
Mold design is not just about creating a cavity shape; it’s about understanding how every detail—from gate placement to cooling system layout—affects the final product’s integrity. By adopting these strategies, manufacturers can significantly enhance wall thickness uniformity, leading to higher-quality injection molded products.
Gate placement affects wall thickness uniformity.True
Proper gate placement ensures even melt flow, preventing thickness variations.
Surface finish does not impact melt flow behavior.False
Polished surfaces reduce resistance, promoting consistent melt flow and cooling.
How Do Injection Molding Parameters Affect Wall Thickness Uniformity?
Injection molding is a precision-driven process, where parameters critically influence wall thickness uniformity, impacting the final product quality.
Injection molding parameters such as injection speed, holding pressure, and mold temperature significantly impact wall thickness uniformity. Adjusting these parameters optimizes melt flow and cooling rates, reducing defects and enhancing product quality.
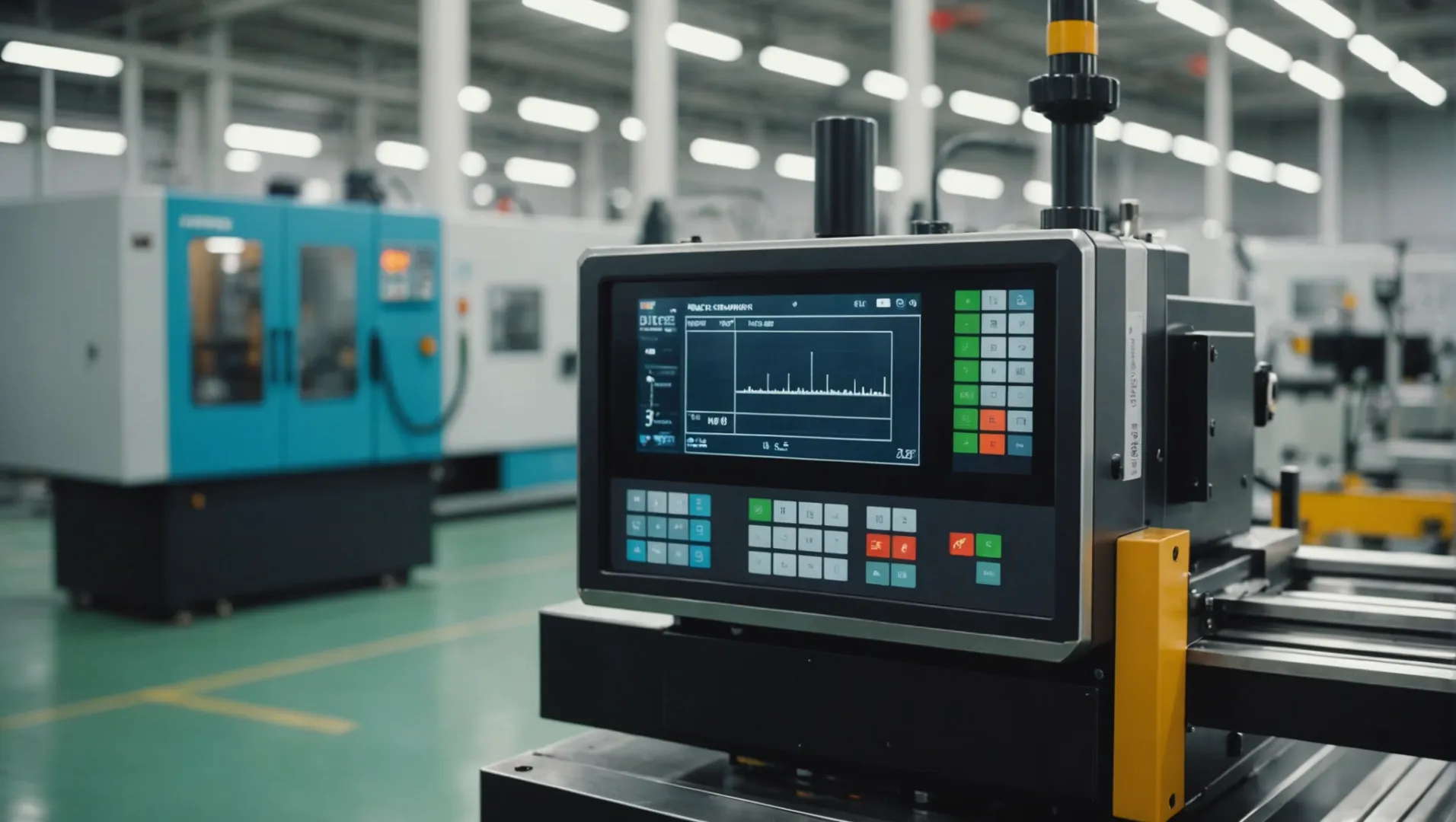
Injection Speed Control
Controlling the injection speed is pivotal in maintaining uniform wall thickness. During the initial filling phase, a higher injection speed can ensure rapid cavity filling. However, in the later stages, slowing down the injection speed helps prevent issues like jetting and turbulence. This careful management results in a more consistent thickness across the product.
For example, a product with varying wall thickness may suffer from uneven fill if the injection speed is not adjusted. By setting higher speeds initially and then gradually decreasing them, manufacturers can balance the flow and maintain uniformity.
Holding Pressure and Time Adjustment
The settings for holding pressure and time are crucial for compensating shrinkage during cooling. Higher holding pressures are often necessary for thicker parts to maintain uniform thickness as they cool. Extending the holding time ensures thorough compensation for shrinkage but must be balanced to avoid increased internal stresses.
Consider a thick-walled part that needs to retain its shape post-molding; a properly adjusted holding pressure ensures it does not deform as it cools. However, it’s essential to avoid excessive holding times to prevent stress accumulation and prolonged cycles.
Mold Temperature Control
Mold temperature plays a significant role in influencing the cooling rate of the melt. By increasing the mold temperature, the cooling process slows down, allowing the melt to distribute more evenly within the cavity. This approach helps achieve better wall thickness uniformity.
For products with non-uniform wall thickness, local heating or cooling can be used to maintain even distribution throughout. It’s a delicate balance: too high a mold temperature can prolong cycles and increase energy costs.
Parameter | Effect on Wall Thickness Uniformity |
---|---|
Injection Speed | Controls flow dynamics and fill quality |
Holding Pressure | Compensates for shrinkage during cooling |
Mold Temperature | Influences cooling rates and uniformity |
By fine-tuning these parameters, manufacturers can significantly enhance wall thickness uniformity, reducing defects like warping and improving overall product quality. For more insights on adjusting injection molding parameters5, exploring expert guidelines can provide further detailed strategies.
Higher injection speed ensures uniform wall thickness.True
Initially high speeds fill cavities quickly, ensuring even distribution.
Mold temperature has no effect on wall thickness uniformity.False
Mold temperature affects cooling rates, impacting thickness uniformity.
Why Is Material Selection Crucial for Optimizing Wall Thickness?
Material selection plays a pivotal role in the consistency and quality of wall thickness in injection molded products. Choosing the right materials can dramatically affect product strength, shrinkage, and overall performance.
Selecting materials with optimal fluidity and shrinkage characteristics is crucial for uniform wall thickness in injection molding. Proper additives enhance material performance, reducing defects and improving product quality.
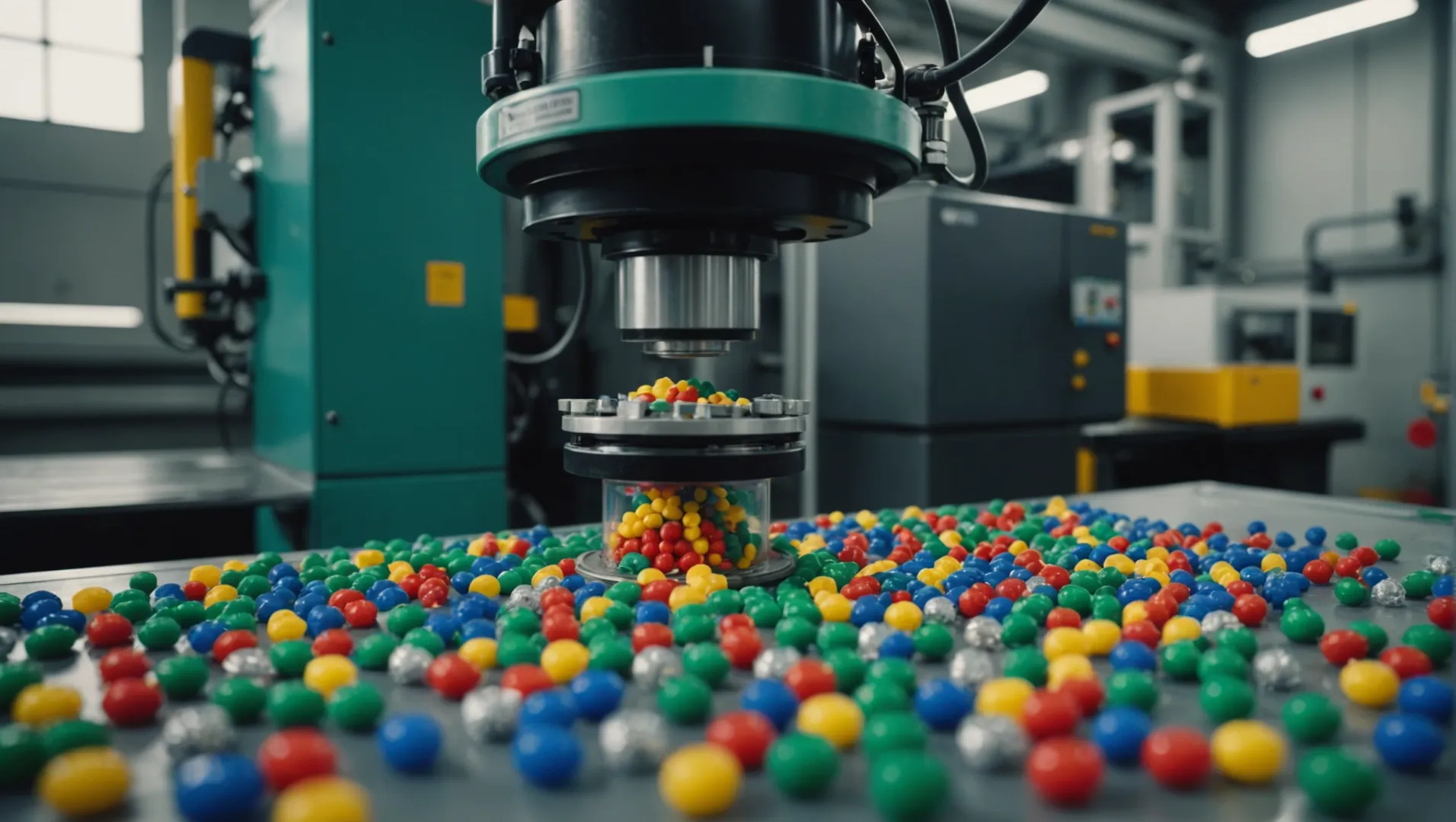
Understanding Material Characteristics
The choice of material is fundamental in injection molding6. Different plastics possess unique properties that can affect how evenly the material flows and cools within the mold. Fluidity is a key characteristic; materials with high fluidity fill molds more uniformly, reducing variations in wall thickness. Shrinkage characteristics also play a critical role, as materials with uneven shrinkage can lead to warping or other defects.
Role of Additives
Incorporating additives such as fillers or enhancers can significantly optimize material performance. For instance, adding glass fibers7 can improve the material’s strength and reduce shrinkage variability. These enhancements lead to a more controlled and consistent wall thickness across complex geometries.
Additive Type | Purpose | Benefits |
---|---|---|
Fillers | Increase density | Reduce shrinkage, improve rigidity |
Plasticizers | Improve flexibility | Enhance fluidity |
Stabilizers | Enhance thermal stability | Maintain consistent properties under heat |
Ensuring Material Dryness
Moisture content in plastic materials can drastically affect the fluidity and quality of the melt. Proper drying techniques are essential to ensure that moisture does not compromise the material’s ability to flow smoothly through the mold. High moisture levels can lead to defects such as bubbles and silver streaks, disrupting wall thickness uniformity.
Material Compatibility with Design
Selecting materials that align with the product design is crucial. For instance, products requiring high-impact resistance should use materials designed to withstand stress without compromising wall thickness integrity. Understanding how a material interacts with both design and mold parameters ensures optimal performance.
By carefully selecting and preparing materials, manufacturers can achieve superior wall thickness uniformity, enhancing both product quality and production efficiency.
High fluidity materials reduce wall thickness variation.True
Materials with high fluidity fill molds uniformly, minimizing thickness variation.
Moisture in plastics improves wall thickness consistency.False
Moisture leads to defects like bubbles, disrupting thickness uniformity.
Conclusion
By applying these strategies, you’ll not only improve wall thickness distribution but also elevate your product’s quality and durability.
-
Learn why consistent wall thickness is vital for product quality.: Proper wall thickness will reduce the risk of cosmetic defects in plastic parts. Walls in any plastic-molded part should be no less than 40 to 60 percent that … ↩
-
Discover how mold design influences wall thickness uniformity.: This guide walks you through everything from quoting, design analysis, and shipment to best practices that ensure your model is optimized for molding. ↩
-
Explore how choosing the right materials aids in uniformity.: The wall thickness is the basic parameter that determines the overall thickness of the product and is often specified during the structural design process. ↩
-
Explore how multi-point gates enhance melt distribution and product uniformity.: After the plastic fills the mold cavity, the gate acts as a restriction point, solidifying and forming a small residual mark called a gate mark … ↩
-
Explore advanced techniques for parameter adjustments in injection molding.: Walls in any plastic-molded part should be no less than 40 to 60 percent that of adjacent walls, and all should fit within recommended thickness ranges for the … ↩
-
Discover how various plastics influence flow and cooling processes.: Learn how to select the right material for your injection molding design with this technical overview of thermoplastic resins. ↩
-
Learn how glass fibers enhance strength and reduce shrinkage.: Glass fibers combine the properties of glass with those of plastics. This makes injection molding possible. But the injection molding of … ↩