Do your molds often seem to play a tug-of-war with balance?
To create a balanced mold runner system, I adjust runner sizes and use a balanced design. I use CAE software to simulate the process and change things based on sensor information. Temperature control really changes results in hot runner systems. Surface treatment is also vital. It’s very important.
In my early days of mold design, I struggled with uneven runner systems. It felt like juggling too many things at once. Learning about geometric shapes helped a lot. Using advanced simulation tools really transformed the process. Precise temperature control is very important. It often becomes the hidden key to achieving perfect balance.
Uniform runner sizes ensure a balanced mold system.True
Uniform runner sizes distribute material evenly, preventing imbalances.
Temperature control is irrelevant in hot runner systems.False
Temperature control is crucial to maintain material flow consistency.
How does geometric shape design influence runner optimization?
Have you ever thought about how a runner’s shape might greatly affect the efficiency of a mold?
Geometric shapes help create uniform runner sizes and smooth transitions. Designers use simulation tools for this task. These elements together probably improve flow balance and reduce defects. Mold system efficiency increases as a result. Efficiency really goes up.
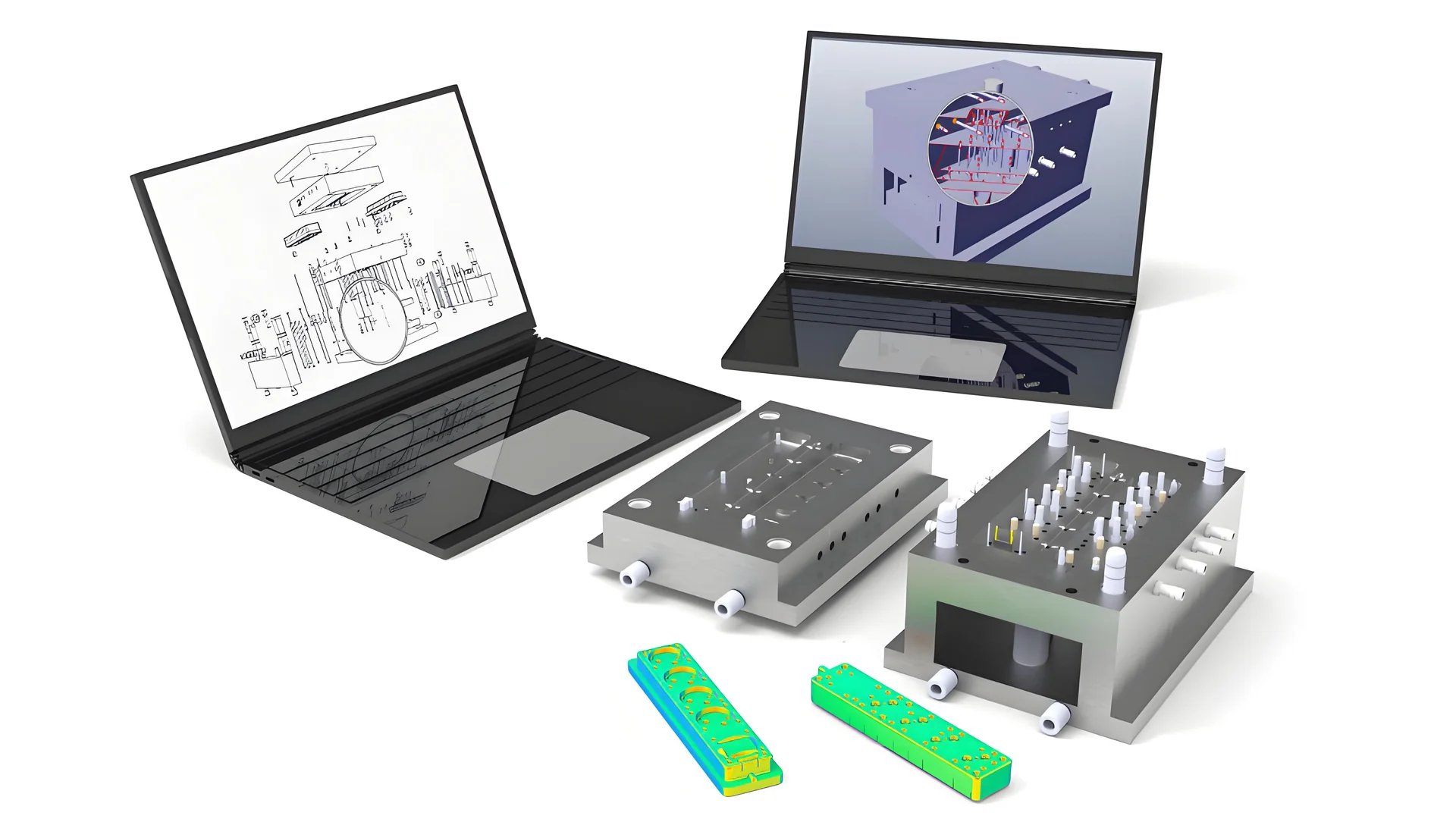
Reflecting on Uniform Runner Sizes
Have you ever tried to solve a puzzle and found one piece that just does not fit? That is what happens when runner sizes differ in a mold. Early in my career, inconsistent flow surprised me until a mentor said uniform runner sizes could solve the problem. In a multi-cavity mold, different runner sizes lead to defects. Main runners, branch runners, and gates should be very similar to avoid this issue. Very similar sizes matter.
Maintaining equal runner lengths from the main runner to each cavity is also important. Think of it like a race where every runner needs a fair chance at the finish line. In symmetric molds, good design avoids uneven distances so each cavity fills evenly.
The Art of Smooth Transitions
The first time I saw smooth transitions in a mold, it felt like watching a graceful dance. Gradual changes in runner shapes stop stagnation and turbulence, like a dance that moves smoothly. In hot runner systems, these transitions are really critical because temperature changes can spoil melt flow.
Harnessing Simulation Tools for Balance
Tools like Moldflow1 work like a crystal ball for mold design. Simulations show how melt flows and find issues before cutting steel. Once, simulation found a cavity filling too fast, so we adjusted the design and avoided costly mistakes.
Table: CAE Software Advantages | Advantage | Impact |
---|---|---|
Accurate Simulations | Predicts pressure and speed variations | |
Design Adjustments | Guides modifications for balance |
Surface Treatment in Hot Runners
Surface treatment in hot runners is like giving a car a perfect shine. Techniques like hard chrome plating improve surface smoothness, reducing melt retention and degradation. This is essential to keep the system balanced and efficient.
Combining uniformity, smooth transitions, simulation insights, and surface treatments shapes runner systems optimally. Each part helps to balance and make mold designs more efficient.
For more knowledge on temperature control in hot runners2, check resources with advanced strategies for keeping perfect conditions in injection molding processes.
Uniform runner sizes reduce flow resistance variations.True
Consistent runner sizes ensure equal flow resistance, minimizing defects.
Gradual transitions in runners cause melt stagnation.False
Gradual transitions prevent melt stagnation by ensuring smooth flow.
How Does CAE Software Enhance Runner Balance Analysis?
Picture a tool that helps you grasp and improve the balance in your mold designs. It’s like having a personal coach for your projects.
CAE software such as Moldflow analyzes how materials move in molds. It helps discover imbalances in pressure and speed. Adjustments based on this information lead to better uniformity. This software probably enhances runner balance greatly.
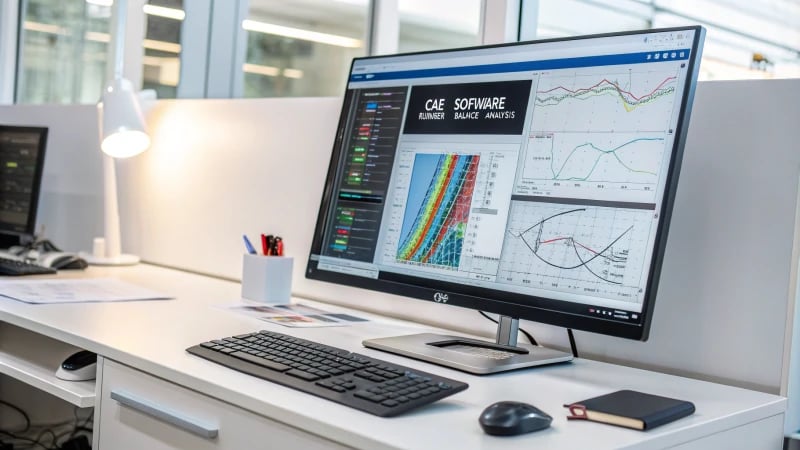
The Role of CAE in Runner Design
I remember when I first saw how Computer-Aided Engineering (CAE) software could transform mold design. It’s like having a crystal ball that shows how materials move through your mold before you create it. Tools like Moldflow simulate the melt flow in your molds. They help you see tricky pressure and speed problems that could cause defects.
Geometric Shape Design and Uniformity
When I began designing runners, I learned that consistency is very important, just like in life. Keeping runner sizes the same is crucial, especially in multi-cavity molds, where differences can cause big imbalances. I often adjusted the diameters of circular branch runners to make them match. It’s about balance. Every cavity must get equal melt flow.
Design Aspect | Consideration |
---|---|
Runner Size Uniformity | Consistent diameters and lengths |
Gradual Transition | Smooth changes between runner shapes |
Simulation and Analysis
In my design work, importing a 3D model into CAE software felt like testing my mold. By changing parameters like pressure, speed, and filling time, I could see how the melt behaved. If one cavity filled faster than another, I adjusted the runner’s size or shape and tested again. Balance was key.
- Simulation Parameters: Change pressure, speed, filling time
- Outcome: Balanced melt flow in all branches
Experimental Verification
After I had my design ready, a trial mold was the next step. Pressure and temperature sensors showed what happened inside the mold during production. This data was very valuable for fine-tuning – adding throttle valves to ensure each cavity filled correctly.
Special Considerations for Hot Runners
Hot runner systems presented a challenge with keeping even temperature. Every nozzle needed separate control to prevent problems like local overheating. Designing the hot runner plate required smart planning to spread heat evenly and avoid uneven melt flow.
Aspect | Description |
---|---|
Temperature Control | Independent units for each hot nozzle |
Surface Treatment | Hard chrome plating for reduced melt retention |
Using CAE software3 in my work helped me face these challenges, keeping runner balance4 achieved in every project. It’s like an expert advisor always at my side.
CAE software identifies runner pressure imbalances.True
CAE software simulates melt flow to detect pressure discrepancies in runners.
Hot runner systems don't require temperature control.False
Temperature control is crucial for hot runners to ensure uniform heating.
What should you consider when working with hot runner systems?
Hot runner systems might seem difficult. Understanding them turns challenges into chances. These systems help create efficiency. They also spark innovation.
Important aspects of hot runner systems involve shaping even geometric forms. Exact temperature control is very crucial. Advanced simulation methods help achieve this. These elements improve how smoothly material flows. This reduces mistakes in the injection molding process. Fewer defects result, which is really significant.
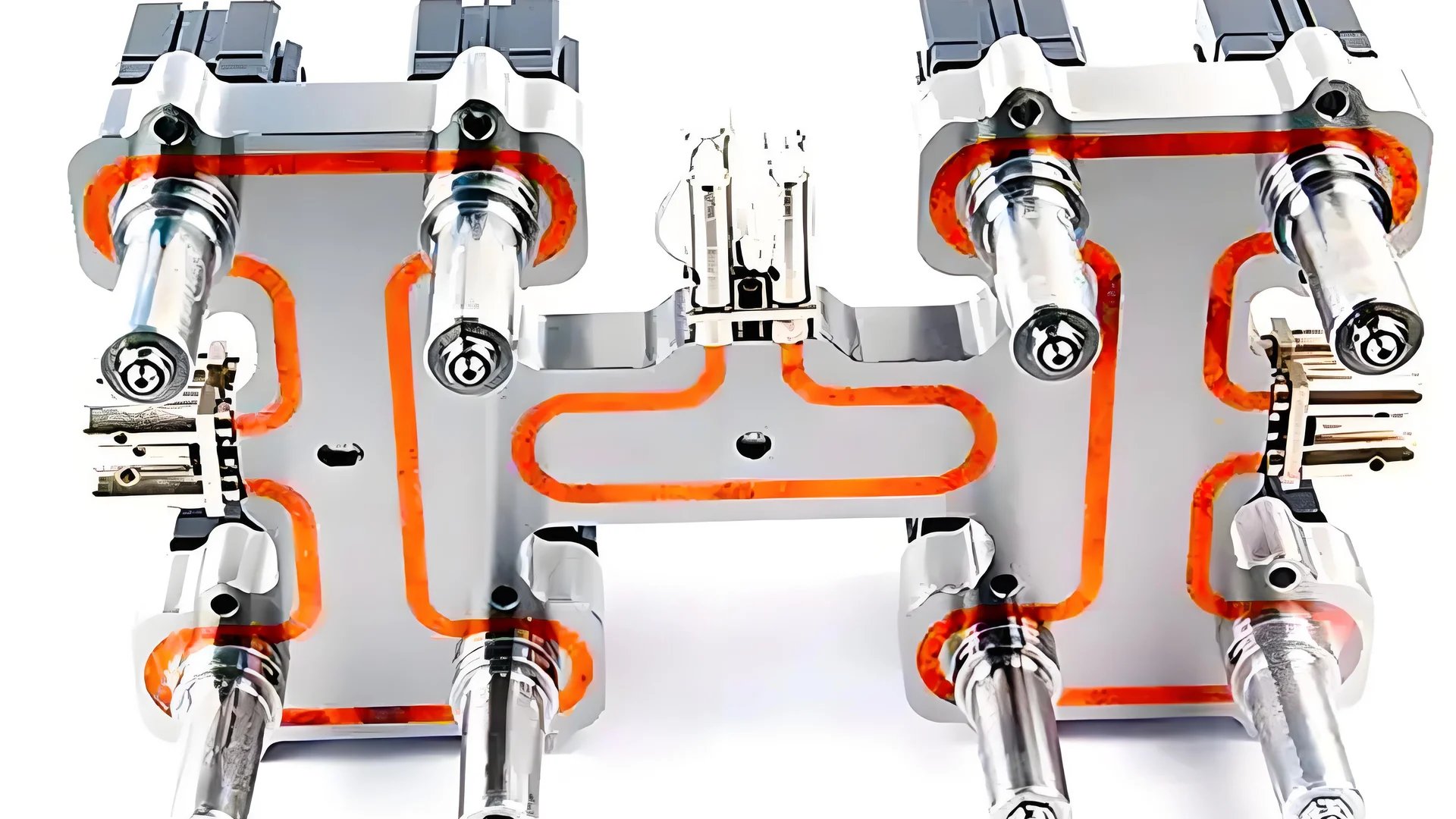
Geometric Shape Design
When I first started learning about injection molding5, I felt confused by the many small details that changed everything between success and failure. Understanding the design of geometric shapes in hot runner systems was crucial. Uniform shapes are very important. Imagine a symphony where every part must work perfectly together.
Aspect | Consideration |
---|---|
Runner Size Uniformity | Matching the sizes of main runners, branch runners, and gates lets the melt flow smoothly, like a well-rehearsed tune. |
Balanced Layout | Creating a balanced layout was like piecing together a tricky puzzle. Matching runner lengths from the main runner to each cavity significantly decreased differences in flow time. |
Gradual and smooth transitions are necessary where the runner shape changes, such as from main to branch runners, stopping any blockages.
Temperature Control
Temperature control is important, like baking a perfect soufflé. Every degree counts. Multiple heating zones need control units and careful monitoring by sensors.
For instance, keeping temperature differences within a tight range – no more than ±5℃ – maintains a consistent melt, leading to a perfect final product. Designing the hot runner plate also needs care. Placing heating elements like rods in the right spots spreads heat evenly.
Runner Balance Analysis and Simulation
Simulation is also key in design. Using CAE software6 like Moldflow changed everything for me. It’s like using a magic ball to see problems before they happen.
By testing our mold’s 3D model, we adjusted settings and fixed imbalances before starting production:
- Example Adjustments:
- The first time we used these simulations, we learned how even small changes could affect melt pressure, speed, and filling times.
- Tiny adjustments have a big effect on direction.
After manufacturing, trial molds show if our ideas work. Pressure and temperature sensors give real data for final tweaks:
- Adding throttle valves or adjusting layouts creates harmony.
- Fine-tuning based on sensor data can correct unbalanced filling issues.
Runner Surface Treatment
Special treatments like hard chrome plating on runner surfaces finish the work like adding the final polish to a masterpiece. They make the flow smoother by reducing blockages and melt degradation.
Achieving a surface roughness of Ra0.2 – 0.4μm allows smoother melt flow.
Focusing on these elements helped us optimize hot runner systems7. This improved efficiency and raised the quality of injection molding, ensuring each product met high standards.
Uniform runner size ensures even melt flow.True
Consistent runner sizes help maintain uniform melt flow across the system.
Temperature control is not crucial in hot runner systems.False
Precise temperature control is essential for consistent melt fluidity.
How Can Experimental Verification Boost Runner System Efficiency?
Imagine this꞉ a running system perfectly directing energy, due to testing. It’s like finding secret power!
Trial molds and sensors in runner systems test experimental setups. These tools monitor pressure and temperature. Balanced flow is very important. They find any defects. This process greatly increases efficiency.
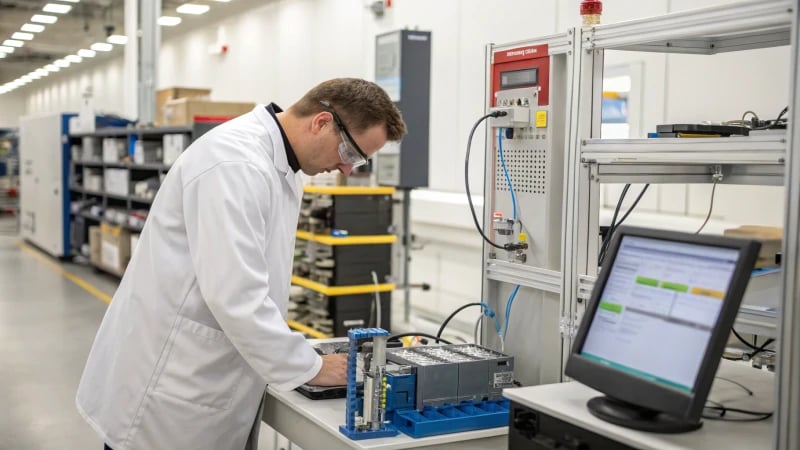
Importance of Experimental Verification
I remember the first time I started designing a runner system. It felt like a maze full of challenges and learning. Experimental verification showed its importance. This process connects theoretical designs with real-world functions, balancing what we plan on paper and how it works in life.
During a project, such as creating a new geometric shape8 for a runner, keeping all sizes uniform is very important for efficiency. Once, I faced a problem where small differences caused unexpected flow resistance. Verification techniques helped reveal these issues early, saving lots of time and resources. Small deviations become big problems.
Utilizing Sensors and Trial Molds
I appreciate sensors during trial mold phases. With them, you understand exactly where issues occur—it’s like having a secret weapon. Observing variables like pressure and temperature showed me where the melt flow was not balanced, leading to easy fixes.
For example, adjusting runner sizes when one cavity filled too fast made operations smooth.
Parameter | Measurement Tool | Purpose |
---|---|---|
Pressure | Pressure Sensors | Detects imbalance in flow |
Temperature | Temperature Sensors | Ensures consistent melt flow |
Role of Computer-aided Engineering (CAE)
Software like Moldflow9 is my go-to tool. It simulates scenarios before physical molds are touched, showing inefficiencies before they become costly errors. This proactive method not only avoids mistakes but saves material.
Special Considerations for Hot Runner Systems
In hot runner systems, careful temperature control is essential. Each zone needs careful monitoring to prevent overheating or undercooling, keeping the system balanced.
Surface treatments like hard chrome plating10 reduce melt retention and improve flow consistency.
Keeping uniform temperatures across nozzles is crucial for smooth operation and avoiding defects like flash or incomplete fills. Experimental verification allows real-time adjustments, offering a lifeline for perfect balance based on sensor data.
Experimental verification ensures uniform runner size.True
Verification detects imbalances early, ensuring uniformity in runner size.
Hot runner systems do not need temperature control.False
Temperature control prevents overheating or undercooling, crucial for efficiency.
Conclusion
Optimize mold runner systems by ensuring uniform sizes, smooth transitions, precise temperature control, and utilizing CAE software for simulations to achieve balanced melt flow and reduce defects.
-
Discover how Moldflow optimizes mold designs by simulating melt flow dynamics and identifying potential issues before production. ↩
-
Explore effective methods for maintaining consistent temperatures in hot runner systems to ensure uniform melt fluidity. ↩
-
Learn how Moldflow simulates melt flow to enhance runner balance analysis. ↩
-
Explore the advantages of CAE software in achieving balanced injection molding. ↩
-
Explore how geometric shape design impacts the efficiency and quality of hot runner systems. ↩
-
Learn how CAE software like Moldflow aids in designing balanced hot runner systems. ↩
-
Discover how surface treatments improve performance and longevity of hot runner systems. ↩
-
This link explores why geometric shape design is crucial for optimizing runner efficiency. ↩
-
Discover how CAE software enhances injection molding processes through simulation. ↩
-
Learn how hard chrome plating improves surface smoothness in hot runners. ↩