Optimizing an injection mold exhaust system is a game-changer in ensuring high-quality production. But what exactly does it involve?
To optimize an injection mold exhaust system, focus on designing efficient exhaust grooves, utilizing mold part gaps for ventilation, applying breathable materials like breathable steel, and adjusting injection molding process parameters to reduce defects and increase efficiency.
While these foundational steps are crucial, mastering the optimization process involves delving into advanced techniques and maintenance practices that can transform your operations.
Exhaust groove size affects mold performance.True
Proper sizing ensures efficient airflow, reducing defects and enhancing quality.
What Are the Common Challenges in Injection Mold Venting?
Injection mold venting is essential to eliminate air and gases during the molding process. But what are the common hurdles faced in ensuring effective venting?
Common challenges in injection mold venting include inadequate exhaust groove design, improper material selection, and misaligned process parameters. Overcoming these requires meticulous planning, regular maintenance, and precise execution to ensure optimal mold performance and quality.
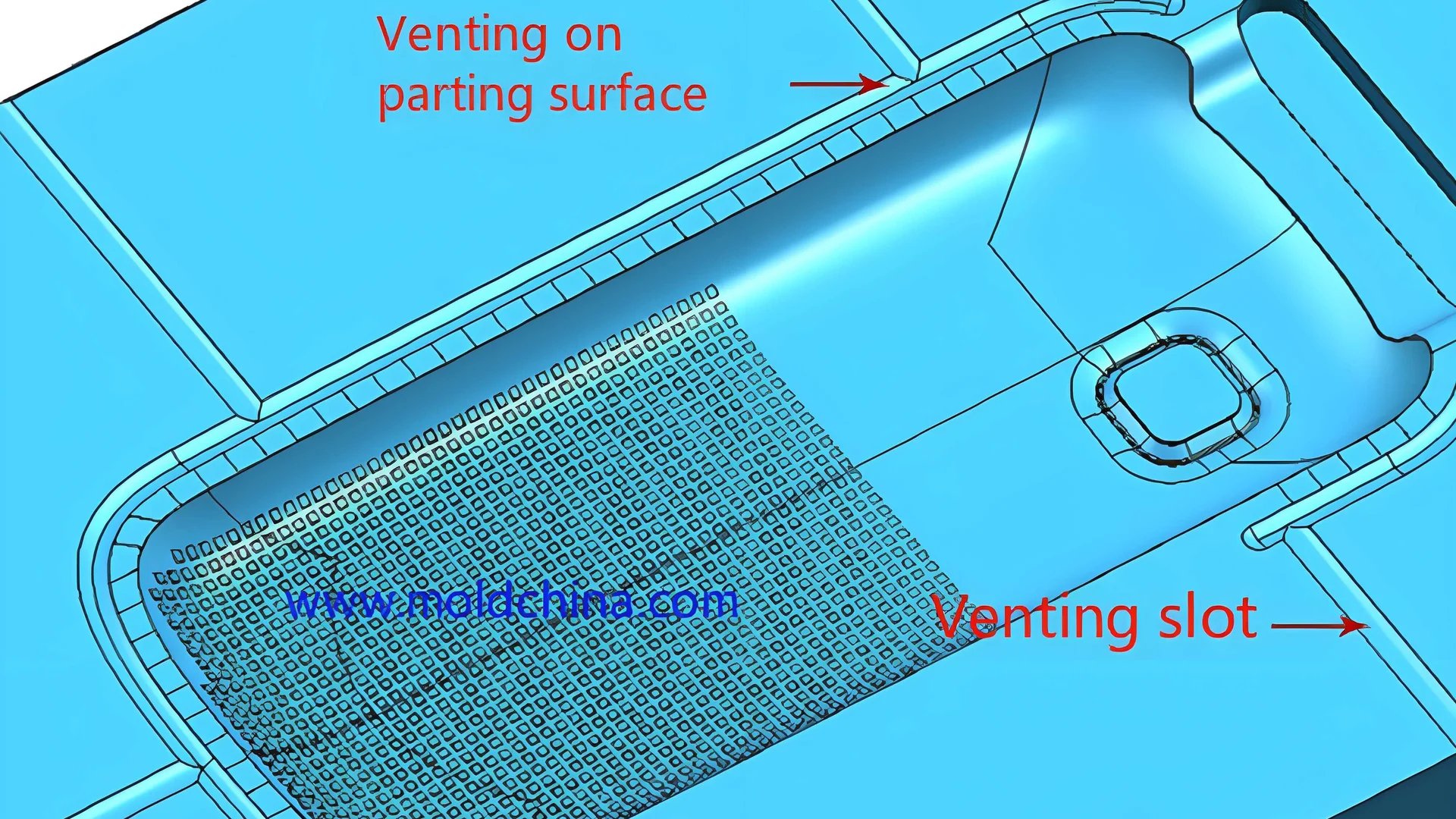
Understanding Venting Problems in Injection Molding
One of the most significant issues in injection molding is dealing with inadequate venting. Poorly designed exhaust grooves1 are a primary concern. These grooves are crucial for allowing trapped air to escape, but when incorrectly sized or placed, they can lead to air traps, resulting in defects like burn marks on the final product.
In addition to groove design, the choice of materials, such as using breathable steel2, plays a critical role. This material allows for better air permeability, yet its application requires careful consideration of porosity and pore size to avoid complications.
The Impact of Process Parameters
Another challenge arises from the injection molding process parameters. An inappropriate injection speed3 can increase air entrapment. Adjusting the speed is vital but must be done carefully to prevent issues like insufficient filling or surface defects.
Similarly, optimizing mold temperature and holding pressure can help manage venting issues. For example, a higher mold temperature might improve fluidity but also risks deformation if not controlled properly.
Regular Maintenance: A Necessity
Finally, maintaining the exhaust system is crucial. Regular checks and cleaning prevent blockages that impair venting efficiency. Compressed air4 and appropriate cleaning tools should be used to maintain mold surfaces and grooves.
A comprehensive understanding of these challenges allows for better planning and execution of mold venting strategies, ultimately leading to enhanced production quality and efficiency.
Inadequate exhaust grooves cause air traps in molds.True
Poorly designed grooves prevent proper air escape, leading to defects.
Breathable steel eliminates all venting issues in molding.False
While it improves permeability, careful material selection is still needed.
How Does Exhaust Groove Design Affect Mold Performance?
The design of exhaust grooves is a pivotal factor in the overall performance of an injection mold. Understanding their impact can enhance production quality significantly.
Exhaust groove design affects mold performance by optimizing airflow, reducing defects, and enhancing part quality through precise placement and sizing.
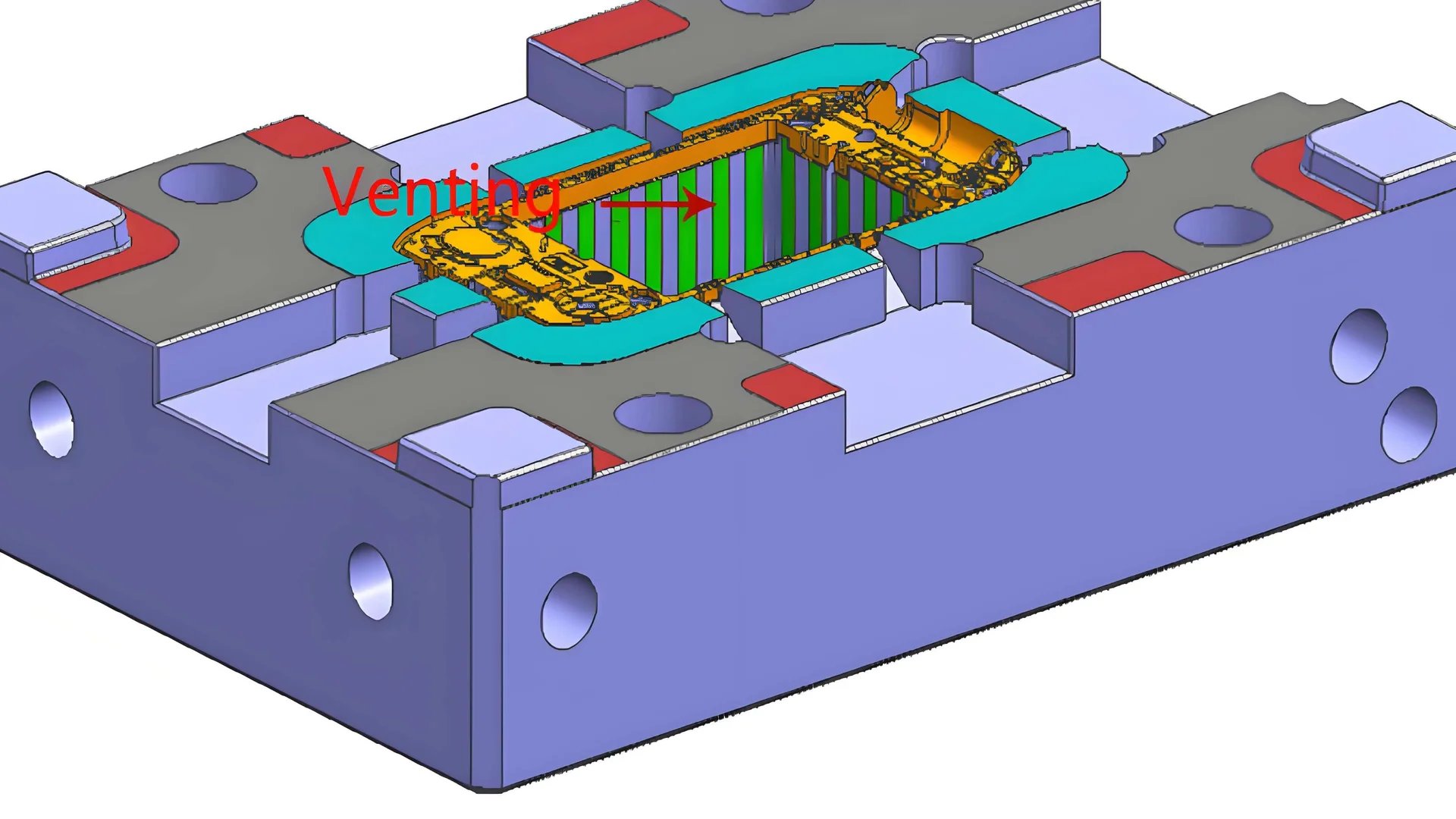
Importance of Exhaust Groove Design in Injection Molds
The exhaust system of an injection mold plays a crucial role in ensuring that air is efficiently expelled during the molding process. This is vital for preventing air traps that can cause defects like short shots, burns, or warping in the final product. A well-designed exhaust groove ensures optimal airflow, directly impacting the mold’s efficiency and product quality.
Strategic Placement of Exhaust Grooves
One of the foremost considerations in designing exhaust grooves is their placement. Typically, these grooves are positioned at the end of the cavity, on the parting line, around inserts, and at the end of the runner. These areas are prone to air accumulation, making them critical for effective exhaust. For complex plastic parts, simulation software can be used to identify potential air trap zones, allowing for targeted groove placement.
Optimizing the Size of Exhaust Grooves
The size of the exhaust groove must be meticulously tailored to suit the specific material and mold design. Generally, groove widths range from 0.025 mm to 0.15 mm, while depths vary between 0.05 mm and 0.15 mm. Materials with higher fluidity may require narrower grooves, whereas those with lower fluidity benefit from wider and deeper grooves. Adjusting these dimensions ensures that air escapes without compromising the mold integrity.
Groove Dimension | Range |
---|---|
Width | 0.025 – 0.15 mm |
Depth | 0.05 – 0.15 mm |
Avoiding Over-Extended Grooves
While sufficient ventilation is crucial, excessive length in exhaust grooves can complicate mold processing and lead to ineffective exhaust. Ideally, the groove length should not exceed 50 mm. For larger areas requiring ventilation, segmenting the groove design is recommended.
Using Gaps for Exhaust in Mold Parts
Another innovative approach involves using the natural gaps between mold components as exhaust channels. For instance, increasing the gap between parting surfaces (typically between 0.02 mm and 0.05 mm) can aid in venting without causing overflow issues. Similar strategies apply to gaps between ejector pins and holes or between sliders and slides.
Leveraging Breathable Materials
Incorporating materials like breathable steel can also significantly enhance exhaust efficiency. This porous material allows air to escape while maintaining structural integrity. Its application is especially beneficial in regions where air entrapment is problematic, such as deep cavities or thin-walled sections of molds.
By combining strategic design with innovative materials, manufacturers can achieve superior mold performance, reducing defects and enhancing product quality through efficient exhaust systems.
Exhaust grooves reduce mold defects by optimizing airflow.True
Proper exhaust groove design ensures efficient air expulsion, minimizing defects.
Groove length should not exceed 100 mm for effective exhaust.False
Optimal groove length is under 50 mm to avoid processing issues.
Why Is Regular Maintenance Crucial for Exhaust Systems?
Neglecting the upkeep of your exhaust system can lead to costly downtime and quality issues. Discover why routine maintenance is essential.
Regular maintenance of exhaust systems ensures optimal performance by preventing blockages, maintaining air permeability, and enhancing product quality in injection molding.
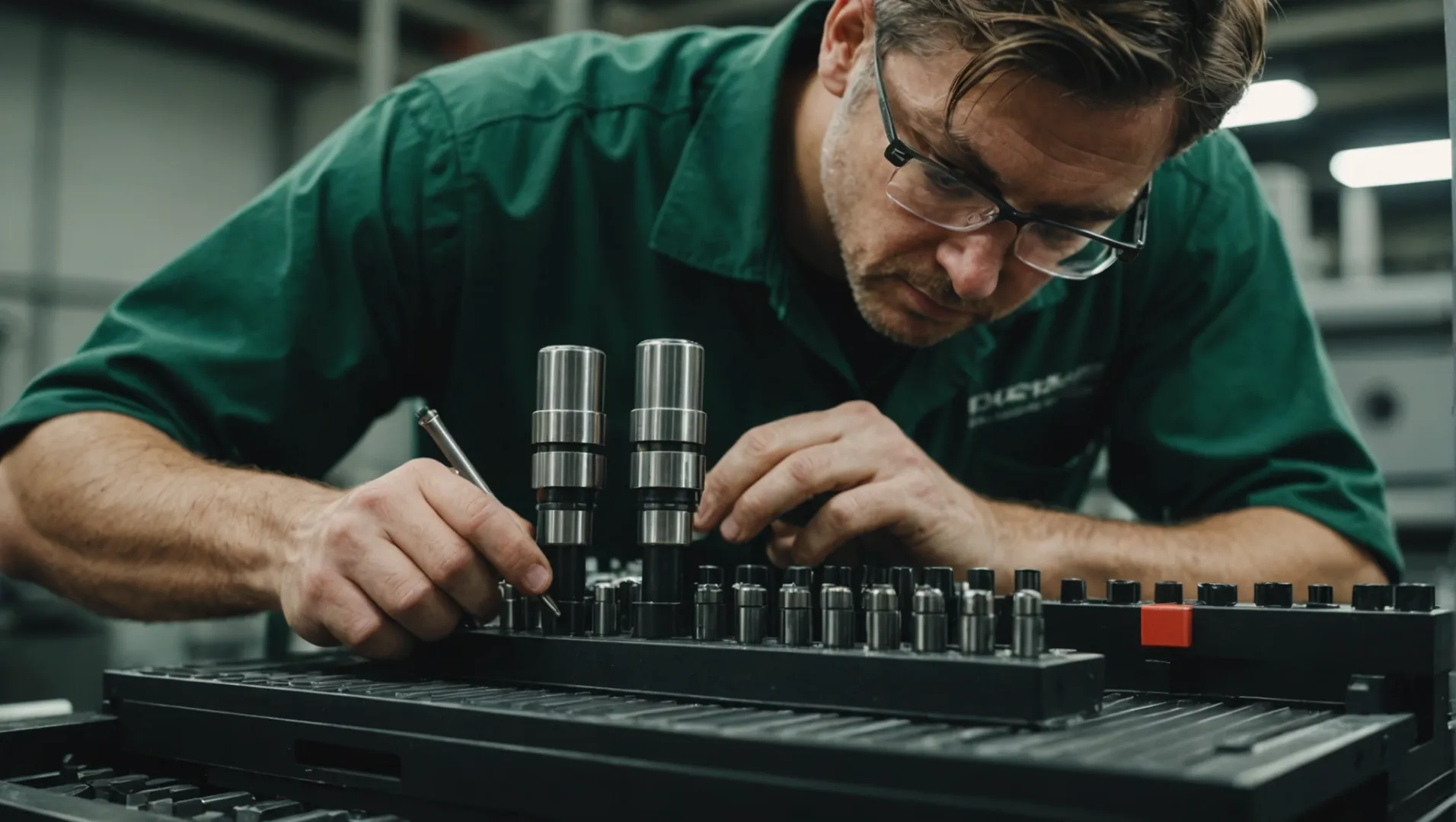
The Importance of Preventing Blockages
One of the primary reasons regular maintenance is crucial for exhaust systems is to prevent blockages. Over time, the exhaust grooves and breathable steel can accumulate debris, such as dust and oil, which impedes air flow. This accumulation can lead to defects in molded products due to improper ventilation. By routinely checking these components, mold operators can ensure that air channels remain clear, facilitating efficient gas expulsion during the molding process.
Tools for Cleaning
To maintain clear exhaust channels, tools such as compressed air and copper wire brushes can be employed. These tools effectively dislodge and remove any build-up without damaging the mold’s surface.
Maintaining Air Permeability in Breathable Steel
Breathable steel, known for its porous structure, plays a significant role in enhancing the exhaust system’s effectiveness. However, its performance can diminish if not regularly checked for air permeability. During maintenance checks, ensuring that the breathable steel retains its porosity is vital.
Replacement Indicators
Should the breathable steel show signs of reduced permeability, it may require replacement. Failure to do so can result in compromised product quality due to inadequate air removal.
Enhancing Product Quality Through Consistent Upkeep
Regular maintenance directly correlates with product quality improvement. Well-maintained exhaust systems minimize defects like air traps and blemishes on molded parts. By keeping the mold surface clean and free from impurities, manufacturers can ensure the aesthetic and structural integrity of their products.
Best Practices for Exhaust System Maintenance
- Scheduled Inspections: Implement a routine check schedule for all exhaust components.
- Use Appropriate Cleaning Agents: Opt for agents that do not damage mold surfaces.
- Monitor Process Parameters: Ensure that parameters such as injection speed and mold temperature are optimized for current conditions.
These practices not only enhance efficiency but also extend the lifespan of the mold itself, reducing long-term costs associated with repairs and replacements.
For more insights on maintaining mold surfaces, refer to our guide on cleaning mold surfaces effectively5.
Regular maintenance prevents exhaust blockages.True
Routine checks keep air channels clear, ensuring efficient gas expulsion.
Breathable steel does not require regular checks.False
Breathable steel needs regular checks to maintain air permeability.
What Role Do Process Parameters Play in Exhaust Optimization?
Discover how injection molding process parameters influence exhaust efficiency and product quality.
Process parameters, such as injection speed, mold temperature, and holding pressure, play a vital role in optimizing exhaust by affecting melt flow, gas expulsion, and defect reduction in injection molding.

Understanding the Influence of Injection Speed
The injection speed directly impacts how quickly the molten material fills the mold cavity. A slower injection speed6 can minimize air entrapment by allowing gases to escape more effectively through the exhaust system. However, if the speed is too slow, it may result in incomplete filling, affecting the final product’s integrity.
Conversely, a faster injection speed7 increases the risk of trapping air pockets within the mold, which can lead to surface defects and reduced product quality. Balancing this parameter requires careful consideration of material properties and the complexity of the mold design.
The Impact of Mold Temperature on Exhaust Efficiency
Mold temperature is crucial in determining the viscosity of the molten plastic. A higher mold temperature lowers the melt’s viscosity, enhancing its flowability and aiding in better gas evacuation through exhaust grooves.
However, excessively high temperatures can cause material degradation or even deformation of the final product. Therefore, setting an optimal mold temperature is essential for maintaining structural integrity while optimizing exhaust efficiency.
Adjusting Holding Time and Pressure
Increasing the holding time and pressure ensures that the melt remains in a compressed state longer, pushing out any remaining gases from the cavity. While higher pressure improves gas expulsion, it can also introduce internal stresses within the molded part.
Finding a balance between holding pressure8 and time is crucial to enhance exhaust performance without compromising product durability. This balance varies depending on the material used and the intricacy of the mold design.
Case Studies: Real-World Applications
Consider a case where adjusting these parameters transformed production outcomes. A manufacturer dealing with frequent surface blemishes and voids found that reducing injection speed and slightly increasing mold temperature improved exhaust efficiency dramatically. This adjustment led to fewer defects and increased throughput.
Such real-world applications highlight how fine-tuning process parameters can optimize exhaust systems and improve overall injection molding operations.
Slower injection speeds reduce air entrapment.True
Slower speeds allow gases to escape, minimizing air pockets.
Higher mold temperature increases melt viscosity.False
Higher temperatures decrease viscosity, improving melt flowability.
Conclusion
By implementing these optimization strategies, you can elevate your injection molding process, ensuring superior product quality and efficiency. Let’s get started!
-
Discover how to design effective exhaust grooves to prevent molding defects.: Properly opening the venting groove can greatly reduce the injection pressure, injection time, holding time and clamping pressure. ↩
-
Learn how breathable steel improves air permeability and product quality.: Compared with conventional solid steel, the breathable mould steel can also offer additional benefits, including decreased injection pressure, … ↩
-
Explore the impact of injection speed on air entrapment and venting efficiency.: In fact, you probably can’t vent it enough, and will need to reduce the injection velocity in order for the air to evacuate in time. ↩
-
Find out which tools effectively clean and maintain mold surfaces.: The 5 Injection Mold Cleaning Methods · Chemical cleaning · Ultrasonic immersion cleaning · Dry ice blasting · Soft plastic media blasting · Laser cleaning. ↩
-
Learn effective methods for cleaning mold surfaces to prevent blockages.: Keeping your injection molds clean is important for maintaining part quality and the life span of … ↩
-
Explore how slower speeds help minimize air entrapment issues.: Injection Speed: Too fast or too slow injection speeds can cause various defects, such as poor surface finish or air entrapment. ↩
-
Learn about potential defects from excessive injection speeds.: High-speed flow reduces heat loss and, due to high shear heat from friction, causes an increase in melt temperature, slowing down the thickening … ↩
-
Understand how pressure adjustments aid gas removal.: Once the mold is filled, holding pressure comes into play. This is a lower pressure applied to the molten plastic to pack the material into the … ↩