Ever found yourself frustrated by a production defect that seems impossible to solve? I’ve been there too. Optimizing gate position in injection mold design has saved me countless hours of troubleshooting.
To optimize gate position in injection mold design, consider material properties, product structure, and process requirements. Using simulation tools and empirical guidelines helps achieve uniform filling and minimize defects, ensuring better product quality and efficiency.
While understanding these foundational elements is critical, delving deeper into the specifics of gate positioning can significantly elevate the design process. Below, we explore key considerations and advanced techniques to refine your approach to gate optimization.
Simulation tools are essential for gate position optimization.True
Simulation tools predict flow behaviors, aiding in optimal gate placement.
What Are the Key Material Considerations for Gate Position?
In injection mold design, selecting the right gate position is crucial for balancing product quality and manufacturing efficiency.
Key material considerations for gate position include plastic fluidity, shrinkage rates, and material properties. These factors influence where to place the gate to ensure optimal filling, minimize defects, and enhance product quality.
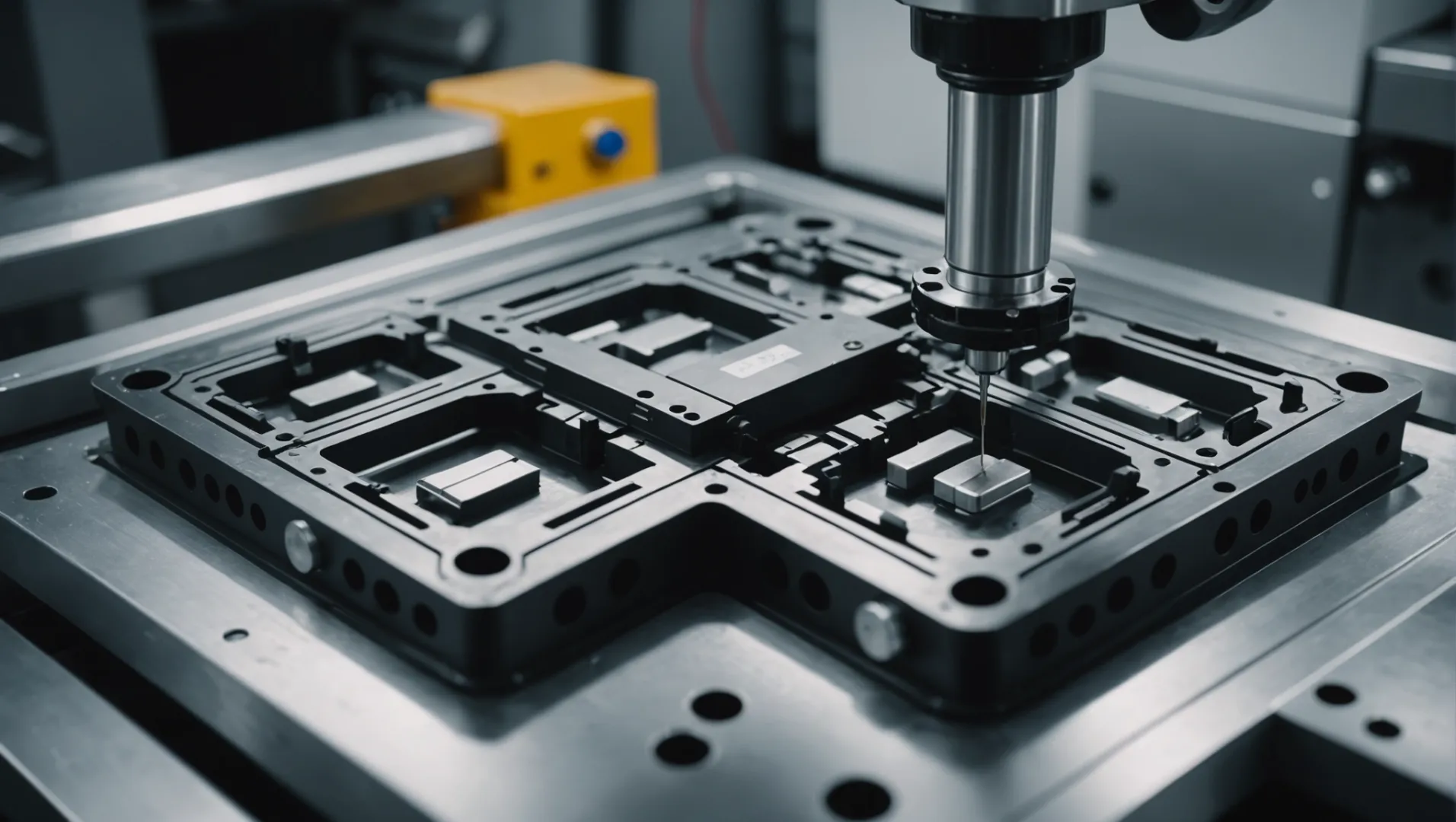
Fluidity of Plastic Materials
The fluidity of a plastic material significantly influences the choice of gate position. Plastics with good fluidity, like polyethylene and polypropylene, can handle gate positions further from critical areas. This strategy reduces potential defects such as flow marks or weld lines by allowing the material to flow smoothly across complex geometries.
Conversely, materials with poor fluidity, such as polycarbonate or polyphenylene ether, require gates closer to essential sections of the mold. This proximity ensures that the mold cavity is adequately filled, preventing incomplete filling or voids. Simulation tools can aid in analyzing fluid flow1 to optimize gate placement.
Shrinkage Rates and Material Characteristics
The shrinkage rate of a material dictates its behavior during cooling and solidification. For instance, ABS exhibits a relatively high shrinkage rate, necessitating strategic gate placement in thicker wall sections to mitigate warping or dimensional inconsistencies. A table outlining typical shrinkage rates for common materials could serve as a valuable reference:
Material | Typical Shrinkage Rate (%) |
---|---|
Polyethylene | 1.5 – 3.0 |
Polypropylene | 1.0 – 2.5 |
Polycarbonate | 0.5 – 0.7 |
ABS | 0.4 – 0.8 |
Material-Specific Properties
Each plastic material possesses unique characteristics that influence its behavior in the molding process. Understanding these properties is essential for effective gate positioning:
- Thermal Stability: High-temperature plastics may require specific cooling strategies to avoid degradation.
- Reactivity: Certain plastics react to environmental conditions during molding, influencing gate location to minimize exposure.
- Additives: The presence of fillers or reinforcements can alter flow behavior, requiring adjustments in gate design.
By analyzing these factors, engineers can optimize gate design2 not only to improve manufacturing efficiency but also to enhance the mechanical properties and aesthetic quality of the final product.
Polyethylene requires gates close to critical areas.False
Polyethylene has good fluidity and can handle gate positions further away.
ABS has a higher shrinkage rate than polycarbonate.True
ABS typically shrinks 0.4-0.8%, while polycarbonate shrinks 0.5-0.7%.
How Does Product Structure Influence Gate Placement?
The structure of a product plays a pivotal role in determining the optimal gate placement in injection molding, impacting both quality and efficiency.
Product structure influences gate placement by dictating the flow path and uniformity of plastic fill. Complex shapes, varying wall thicknesses, and product size must be considered to prevent defects like warping and stress concentration.
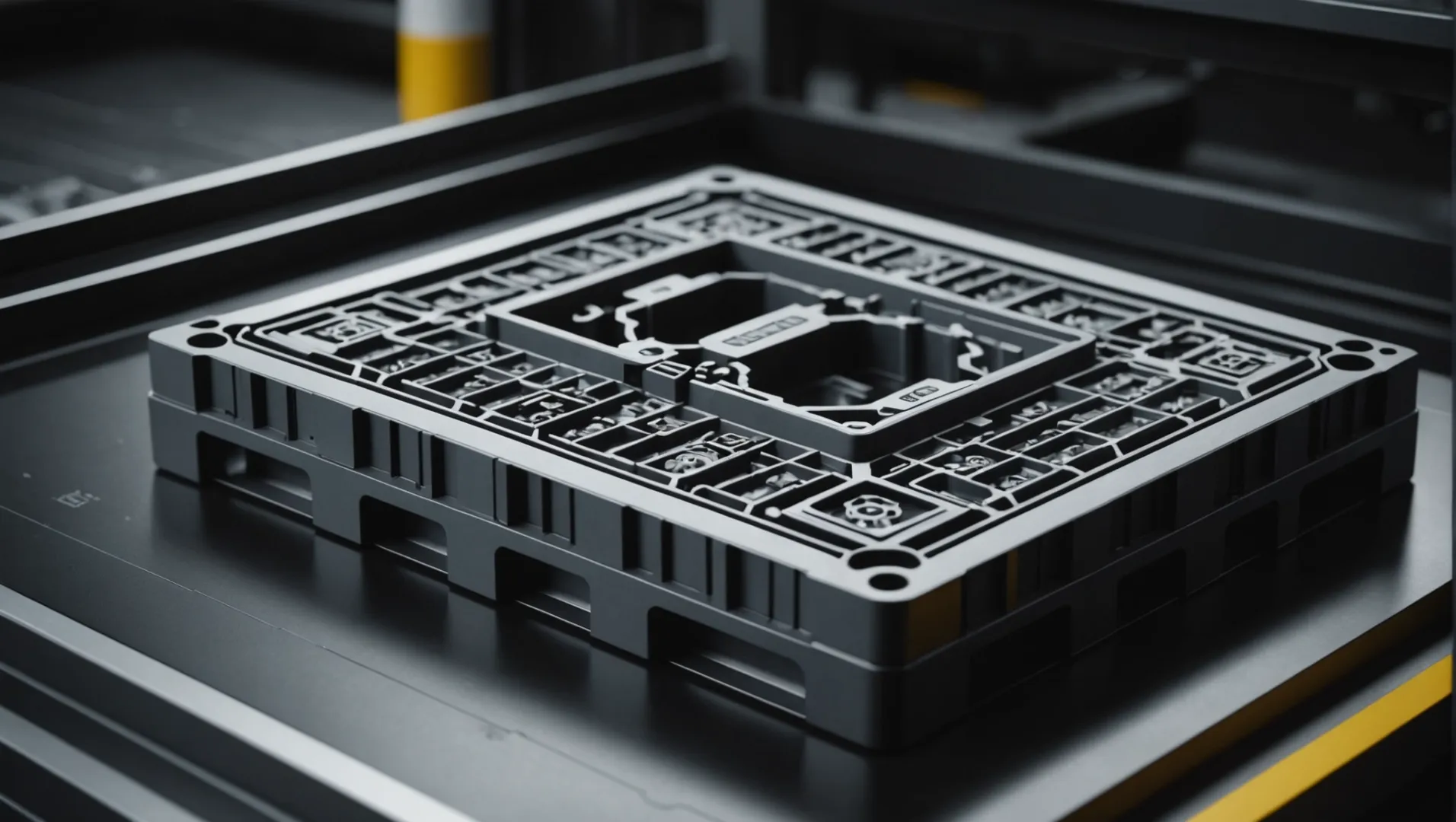
Understanding Product Complexity
When it comes to products with complex shapes, ensuring the plastic fills evenly is paramount. For instance, products with multiple protrusions, grooves, or holes require careful gate positioning. Utilizing simulation analysis can determine the optimal gate location, ensuring all areas are reached simultaneously, thus preventing material shortages or excess.
Example: Multi-Protrusion Components
Consider a component with several protrusions. If the gate is poorly positioned, some areas may experience overfilling while others may be inadequately filled. Simulation analysis3 helps visualize flow paths and adjust gate placement for uniform distribution.
Wall Thickness Considerations
Changes in wall thickness also significantly impact gate positioning. The transition between different thicknesses should be smooth to avoid stress concentration and warping. The gate should ideally be placed where wall thickness is uniform.
Case Study: Sudden Thickness Changes
For components with abrupt changes in wall thickness, gates should not be placed near these transitions. Instead, position them where the thickness remains consistent. This avoids potential deformation and ensures structural integrity.
Handling Large Products
Large products often necessitate multiple gates to achieve uniform filling. The gates should be strategically distributed to prevent local overheating or cooling.
Table: Gate Placement Strategies for Large Products
Aspect | Strategy |
---|---|
Uniform Filling | Employ balanced gate systems |
Structural Strength | Avoid weak mold areas for gate placement |
Processing Feasibility | Consider ease of manufacturing and mold longevity |
For large-scale items, a balanced gate system ensures equal flow resistance at each entry point. This setup is crucial to maintain product quality and minimize potential defects.
Conclusion
Understanding the interplay between product structure and gate placement is essential for optimizing injection mold design. By leveraging techniques like simulation analysis and carefully considering factors such as complexity and size, designers can enhance both the quality and efficiency of their manufacturing processes.
Gate placement affects product quality in injection molding.True
Correct gate placement ensures uniform plastic fill, reducing defects.
Wall thickness changes do not impact gate placement.False
Thickness variations affect flow, requiring careful gate positioning.
Which Process Requirements Should Be Prioritized in Gate Optimization?
Optimizing the gate position in injection mold design involves balancing numerous process requirements to enhance production quality and efficiency.
Prioritize injection pressure, cooling systems, and demolding methods in gate optimization to ensure efficient and defect-free manufacturing. Consider simulation tools for precise adjustments.

Injection Pressure and Speed
When optimizing gate position, the injection pressure and speed play crucial roles. The gate should be positioned relative to the nozzle to mitigate pressure loss. Low-pressure scenarios necessitate a gate closer to the nozzle, while high-pressure setups allow for greater flexibility in gate placement. High-speed injection demands precise gate positioning to ensure rapid cavity filling, thus minimizing injection defects.
Example:
A study on optimizing gate positions for low-pressure applications4 demonstrated a marked improvement in product quality when gates were placed closer to the nozzle. This minimizes pressure loss and reduces the risk of defects.
Cooling System Coordination
The cooling system’s effectiveness significantly influences gate positioning. It’s vital to avoid gate placements that could disrupt cooling, especially near water channels. A coordinated approach ensures consistent product cooling, which is essential for maintaining dimensional accuracy and reducing warping.
Example:
In a case involving cooling systems in injection molding5, strategic gate placement away from cooling channels resulted in enhanced product quality by ensuring even cooling.
Demolding Methods
Effective demolding is critical for maintaining product integrity. Gates should facilitate easy demolding, avoiding areas that complicate ejection or risk damaging the product. Gate size and shape should complement the chosen demolding method, reducing the likelihood of gate breakage or residue issues.
Example:
Research on demolding efficiency improvements6 highlighted how appropriate gate placement simplified ejection processes and reduced potential for damage, thus enhancing production efficiency.
Table: Process Requirement Prioritization
Process Requirement | Key Considerations |
---|---|
Injection Pressure | Position gate based on pressure levels |
Cooling System | Coordinate with cooling channels |
Demolding Method | Facilitate smooth ejection; avoid key areas |
While these process requirements form the backbone of effective gate optimization, leveraging simulation tools can provide precise adjustments and predictive insights into how various factors interact during production. Simulation not only reduces trial runs but also enhances the designer’s ability to foresee potential issues, thus streamlining the optimization process.
Gate position affects injection pressure loss.True
Positioning gates closer to the nozzle minimizes pressure loss, reducing defects.
Cooling channels should be near gates for better cooling.False
Gates should avoid cooling channels to ensure even product cooling.
What Advanced Techniques Can Improve Gate Positioning?
Gate positioning in injection molding is a nuanced art, requiring precision and adaptability to optimize production.
Advanced techniques for improving gate positioning include utilizing simulation software, applying empirical guidelines, and conducting mold trials. These methods help predict flow behaviors, refine gate locations, and ensure balanced filling, leading to superior product quality and enhanced manufacturing efficiency.
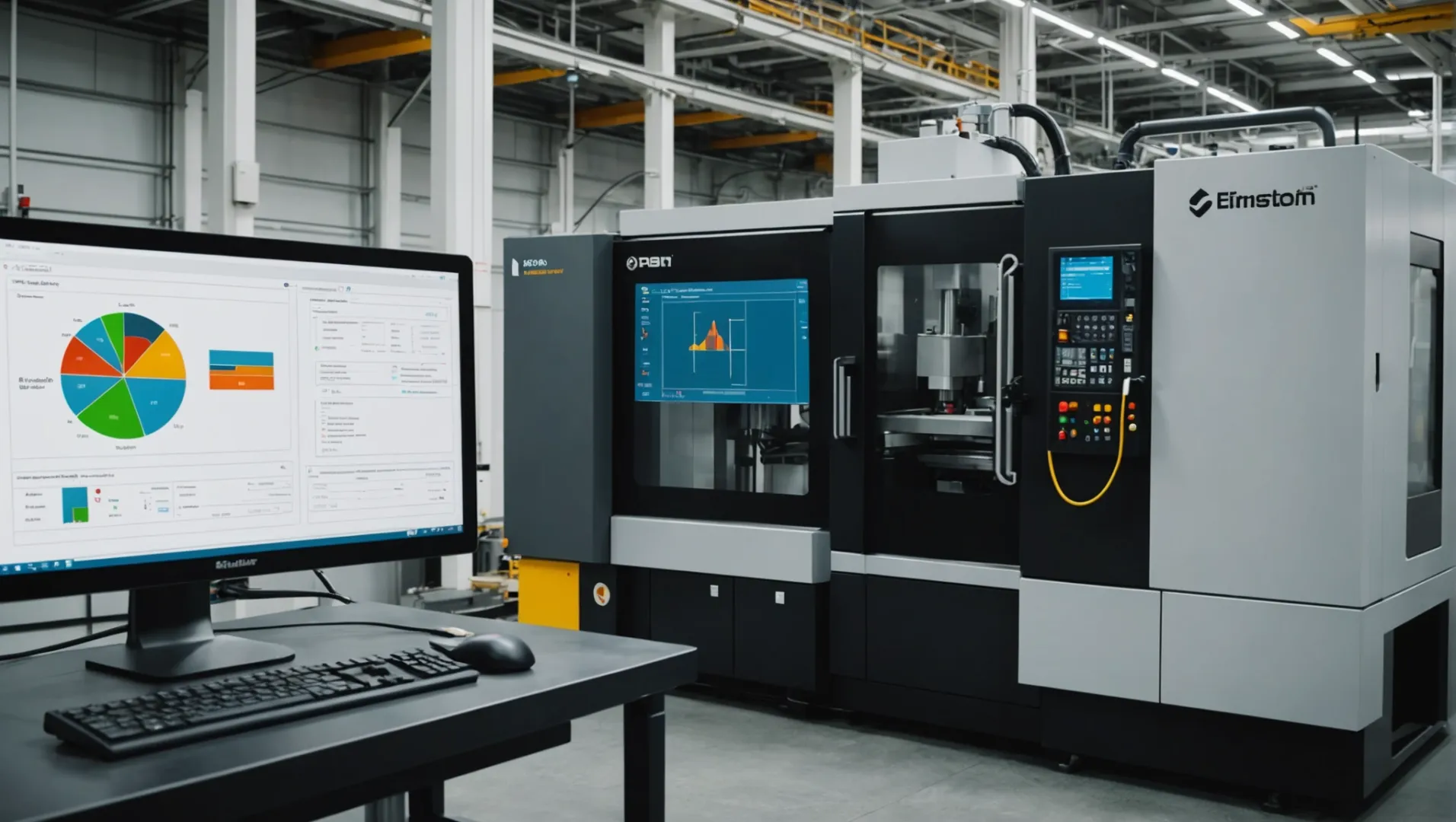
Simulation Software: A Modern Approach
Simulation software allows designers to model different gate positions, predicting how plastics will flow and fill a mold. This software assesses variables like filling time, pressure distribution, and temperature changes. Using this data, designers can fine-tune gate positions to minimize defects such as air traps and weld lines. By simulating these scenarios virtually, costly trial-and-error stages in physical production can be reduced. For example, simulation analysis techniques7 provide valuable insights into optimizing complex shapes.
Empirical Guidelines: Leveraging Experience
Empirical rules, based on years of industry experience, guide designers in gate positioning. These guidelines suggest placing gates in the thickest part of a product or avoiding corners to reduce stress concentrations. While they may not always offer the best solution, they serve as an essential starting point, providing a foundation for empirical optimization strategies8 to be customized for specific projects.
Mold Trials: Testing Real-World Viability
Actual mold trials remain indispensable in gate optimization. Testing enables designers to observe product quality directly and make informed adjustments to gate locations. By examining variables such as appearance quality and mechanical properties, mold trials validate the practical application of theoretical designs. This iterative process ensures the final product meets desired standards. For example, real-world mold trials9 confirm adjustments suggested by simulation and empirical data.
Balancing Multiple Gates for Large Products
For larger products, using multiple gates might be necessary to achieve uniform filling. The placement of these gates needs to be carefully balanced to avoid issues like local overheating or uneven cooling. A balanced gate system ensures equal flow resistance at each gate, promoting even material distribution. This technique not only improves the overall quality but also extends the life of the mold by reducing stress on weaker structural areas. Insights on multi-gate balancing10 can offer detailed strategies for tackling large-scale projects effectively.
Considerations for High-Speed Injection Molding
In high-speed injection processes, the gate position must facilitate rapid cavity filling without causing defects like flow marks. Adjusting gate shape and size can accommodate the needs of high-speed production, ensuring that the plastic reaches all parts of the mold swiftly and evenly. High-speed injection techniques11 highlight adjustments that can mitigate common pitfalls in fast-paced environments.
Integration with Cooling Systems
The coordination between gate positioning and the cooling system is vital. Proper alignment ensures that products cool evenly, maintaining dimensional accuracy. Avoid placing gates too close to cooling channels to prevent adverse impacts on cooling efficiency. For instance, an understanding of cooling integration strategies12 helps maintain quality during the cooling phase.
Simulation software reduces trial-and-error in molding.True
Simulation predicts flow behaviors, minimizing physical trials.
Empirical guidelines always offer the best gate solutions.False
They provide a starting point but may not be optimal alone.
Conclusion
In conclusion, optimizing gate positions requires a holistic approach that considers materials, structure, and process. Embrace simulation analysis and hands-on testing to elevate your injection molding projects.
-
Explore how different plastic fluidities affect gate placement strategies.: Plastic flowing from a single gate will create noticeable weld lines as it flows around obstructions in the mold; High injection pressures and … ↩
-
Learn methods to enhance gate design for better product quality.: For starters, gates can and should be placed in non-cosmetic areas whenever possible. And in those cases where a gate must be located in a less-than-desirable … ↩
-
Explore how simulation tools optimize gate placement for complex components.: Simulation of Injection Molding a CAE technology that analyzes the filling behavior of resin injected into a mold from an injection molding machine. ↩
-
Learn how positioning closer to nozzles improves quality in low-pressure scenarios.: Gates designed for low-pressure use might not provide adequate sealing or easy operation under higher pressures. ↩
-
Discover how strategic placement enhances cooling efficiency.: 1. Water-Cooled Systems. Water-cooling systems are the go-to choice for injection molders, thanks to their efficiency and cost effectiveness. ↩
-
Understand how optimal gate placement facilitates easier product ejection.: Ever wanted to incorporate new design features but worry about manufacturability? Or encountered a difficult to de-mold product line? ↩
-
Simulation analysis helps refine gate positioning by predicting flow behaviors.: Injection molding simulation software is used to make better molded parts and reduce defects. It does this by digitally simulating virtually … ↩
-
Empirical guidelines offer foundational strategies for gate optimization.: In injection mold, design of gate location is among the most critical factors in achieving dimensionally accurate parts and high … ↩
-
Mold trials validate theoretical designs with real-world testing results.: The number of injection mold trials directly affects production efficiency and product quality, so it needs to be flexibly controlled according … ↩
-
Balancing multiple gates ensures uniform filling and reduces defects.: This lesson covers the factors to consider when implementing a multiple gating strategy, how different runner dimensions impact filling behaviors and injection … ↩
-
These techniques optimize gate positioning for fast-paced production.: The key technologies of high-speed injection molding machines include precise temperature control, precise pressure control, high-speed screw injection molding … ↩
-
Proper integration ensures even cooling and maintains product accuracy.: Valve gates provide several advantages when using hot runners, including better appearance, safety and an overall better product. ↩