In the ever-evolving landscape of injection molding, I’ve found that improving filling speed isn’t just a technical necessity—it’s a game-changer for productivity and quality.
To optimize filling speed in injection molding, focus on equipment adjustments, mold design, material selection, and precise process control. These strategies help in reducing cycle times and defects, enhancing both efficiency and product quality.
But there’s so much more beneath the surface! Let’s dive deeper into each of these areas to uncover the nuanced tactics that can truly elevate your injection molding operations.
Increasing injection pressure always improves filling speed.False
While higher pressure can boost speed, excessive pressure may cause defects like flash.
How Do Equipment Adjustments Impact Filling Speed?
In the realm of injection molding, precise equipment adjustments can significantly influence filling speed, impacting both efficiency and product quality.
Equipment adjustments in injection molding, such as tweaking injection pressure, optimizing injection time, and controlling screw speed, are vital in enhancing filling speed. These changes, when carefully managed, lead to improved efficiency and reduced defects in production processes.
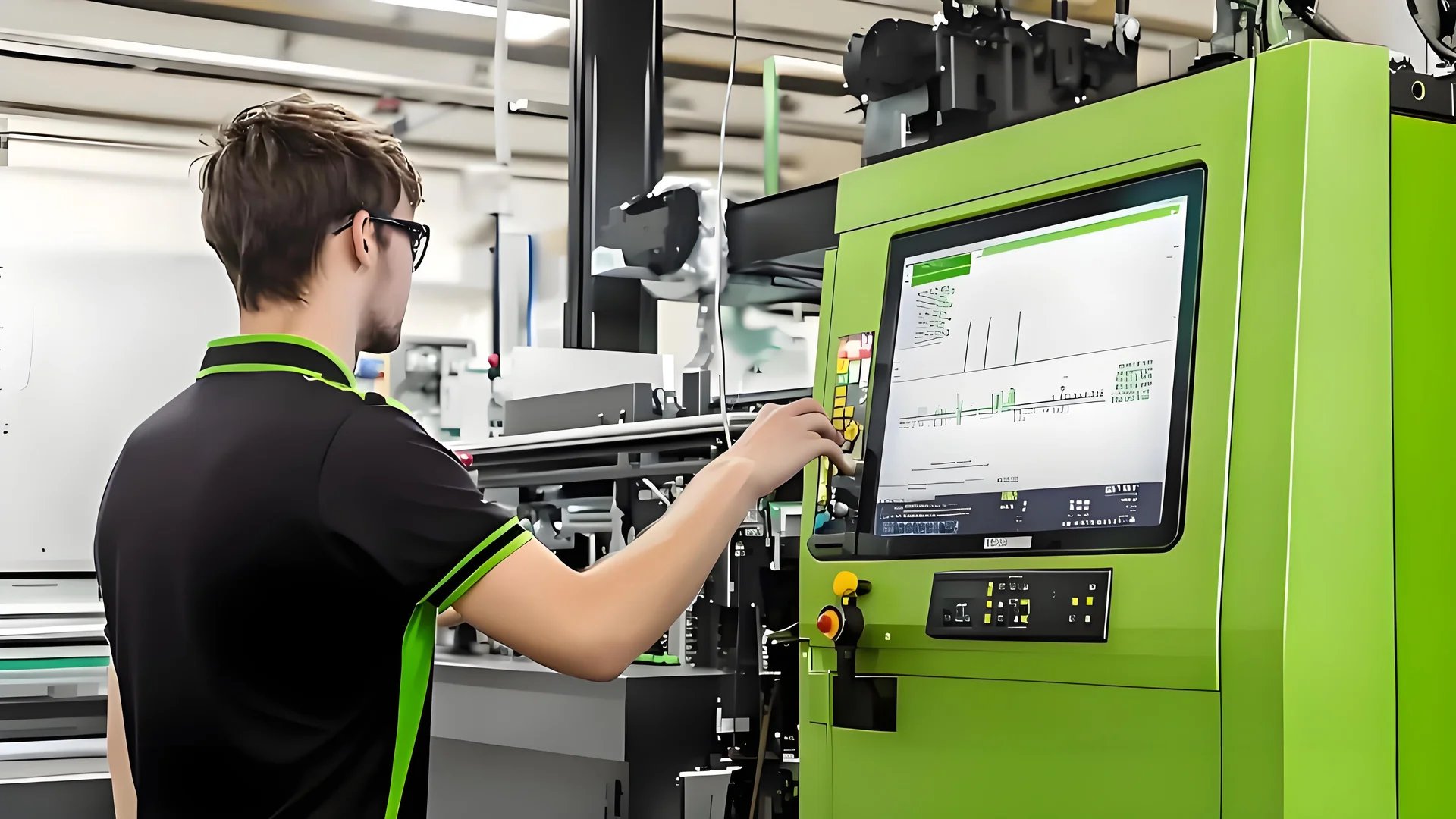
Adjusting Injection Pressure
One of the most effective ways to impact filling speed is through the adjustment of the injection pressure. By increasing the pressure, you can accelerate the flow of molten plastic into the mold. However, it’s crucial to balance this adjustment to prevent issues like flash or demolding difficulties. The optimal pressure varies depending on plastic type and mold structure.
Optimizing Injection Time
Shortening the injection time can boost filling speed, yet it requires a delicate balance. If the time is too short, it could lead to incomplete mold filling or bubble formation. It’s essential to consider the plastic’s fluidity and ensure proper mold ventilation. Utilizing precise timing controls can aid in achieving the best results for diverse materials.
Controlling Screw Speed
Increasing screw speed can enhance the melting and conveying rate of plastic materials, contributing to a faster filling process. Yet, too much speed might cause overheating or material degradation. Carefully monitor screw wear and plastic integrity to maintain the quality of both equipment and final products.
Choosing the Right Injection Molding Machine
The choice of equipment plays a pivotal role in filling speed. Factors like injection capacity and clamping force must align with product requirements to avoid bottlenecks. Machines with higher stability reduce production fluctuations, leading to more consistent filling speeds. Review manufacturers’ specifications to ensure optimal machine selection.
These equipment adjustments, when executed with precision, can transform injection molding operations by enhancing filling speed1 and minimizing defects. Understanding the nuances of these adjustments empowers you to make informed decisions that directly influence production outcomes.
Increasing injection pressure speeds up mold filling.True
Higher pressure accelerates molten plastic flow into the mold.
Shorter injection time always improves product quality.False
Too short a time can cause incomplete filling or bubbles.
What Role Does Mold Design Play in Efficiency?
Mold design is pivotal in injection molding efficiency, influencing speed, quality, and cost-effectiveness. An optimized design ensures smooth material flow, reduces cycle times, and minimizes defects.
Mold design significantly impacts injection molding efficiency by optimizing gate systems, enhancing mold exhaust, and improving material flow. Proper design choices reduce cycle times and defects, boosting overall production performance.
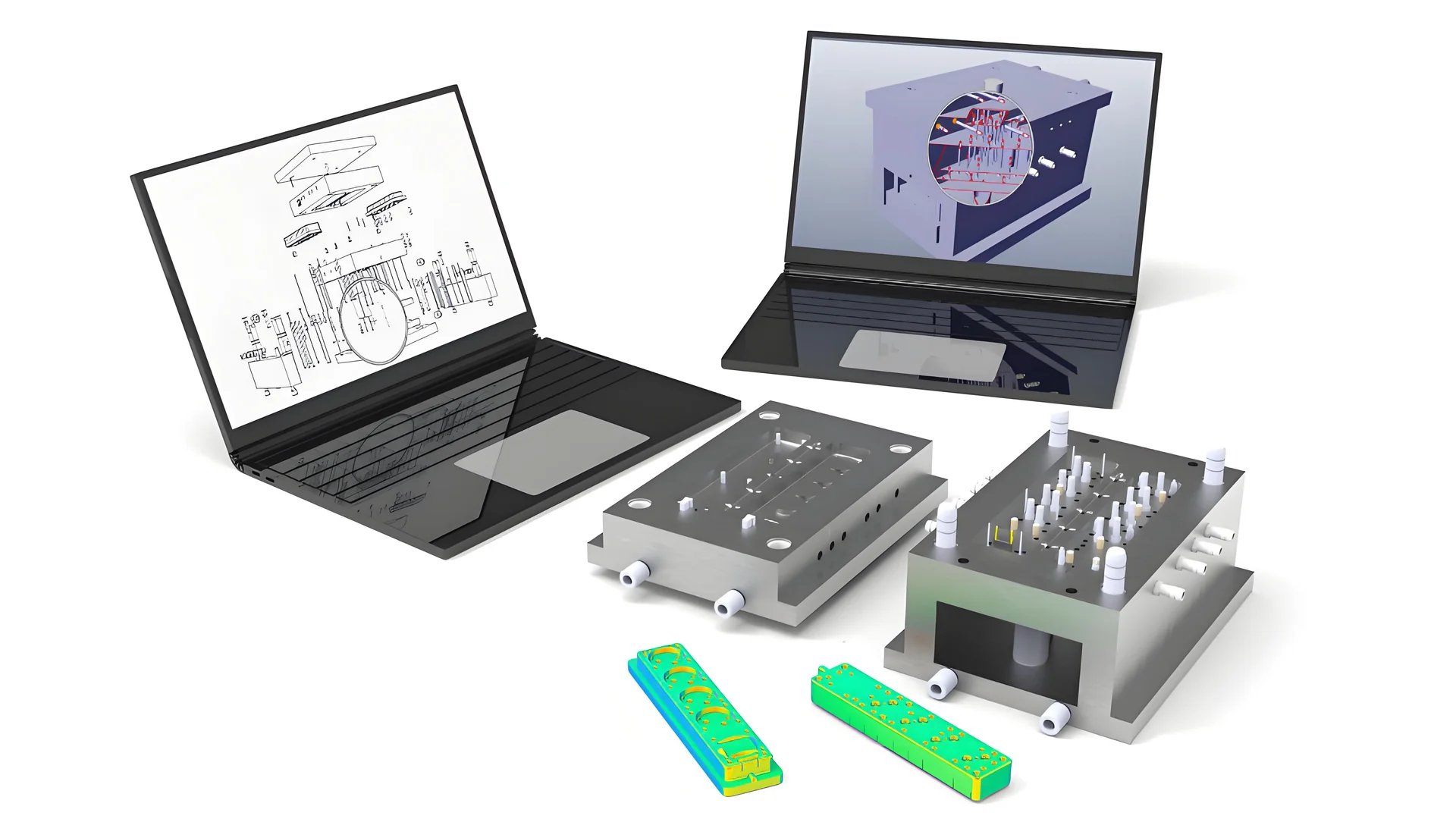
Understanding the Gate System
The gate system is crucial for controlling the flow of molten plastic into the mold cavity. Selecting the appropriate gate type can enhance filling speed and product quality. For instance, choosing the right gate type2 involves considering factors like stress distribution and warpage potential. Direct gates provide faster filling but may increase stress, while point gates offer lower stress with slower filling.
Gate Size and Position: Adjusting these can greatly influence efficiency. A larger gate size can facilitate faster filling; however, it should not compromise the product’s appearance. Positioning gates strategically ensures even plastic flow, improving both speed and quality.
Enhancing Mold Exhaust Systems
Efficient exhaust systems are essential to reduce resistance during filling. Implementing features like exhaust grooves on parting surfaces helps vent trapped air and volatiles. Adding exhaust grooves3 prevents defects such as bubbles and incomplete fills, thereby enhancing the overall filling speed.
Structural Optimization: A well-designed mold avoids dead corners and narrow channels that can hinder flow. Materials like breathable steel can be used to improve air permeability, facilitating smoother plastic movement within the mold.
Material Flow and Mold Structure
The mold’s internal structure plays a significant role in determining how easily material flows. Streamlined designs with minimal obstructions enable quicker and more consistent filling. Optimizing mold structure4 helps reduce cycle times and enhances product consistency by ensuring smooth flow paths.
In summary, meticulous attention to mold design details such as gate type, exhaust efficiency, and material flow can dramatically improve injection molding efficiency. These enhancements contribute to reduced cycle times and fewer defects, ultimately elevating production quality and profitability.
Larger gates always improve product appearance.False
Larger gates can facilitate faster filling but may compromise appearance.
Exhaust grooves prevent bubbles and incomplete fills.True
Exhaust grooves help vent trapped air, reducing defects like bubbles.
Why Is Material Selection Critical for Filling Speed?
Choosing the right material is essential in injection molding, as it directly affects the filling speed and the overall efficiency of the process. The wrong material choice can lead to production delays and increased defect rates.
Material selection is crucial for filling speed because it influences plastic flow, thermal stability, and drying requirements. By selecting materials with optimal fluidity and stability, manufacturers can achieve faster filling speeds and enhance production efficiency.
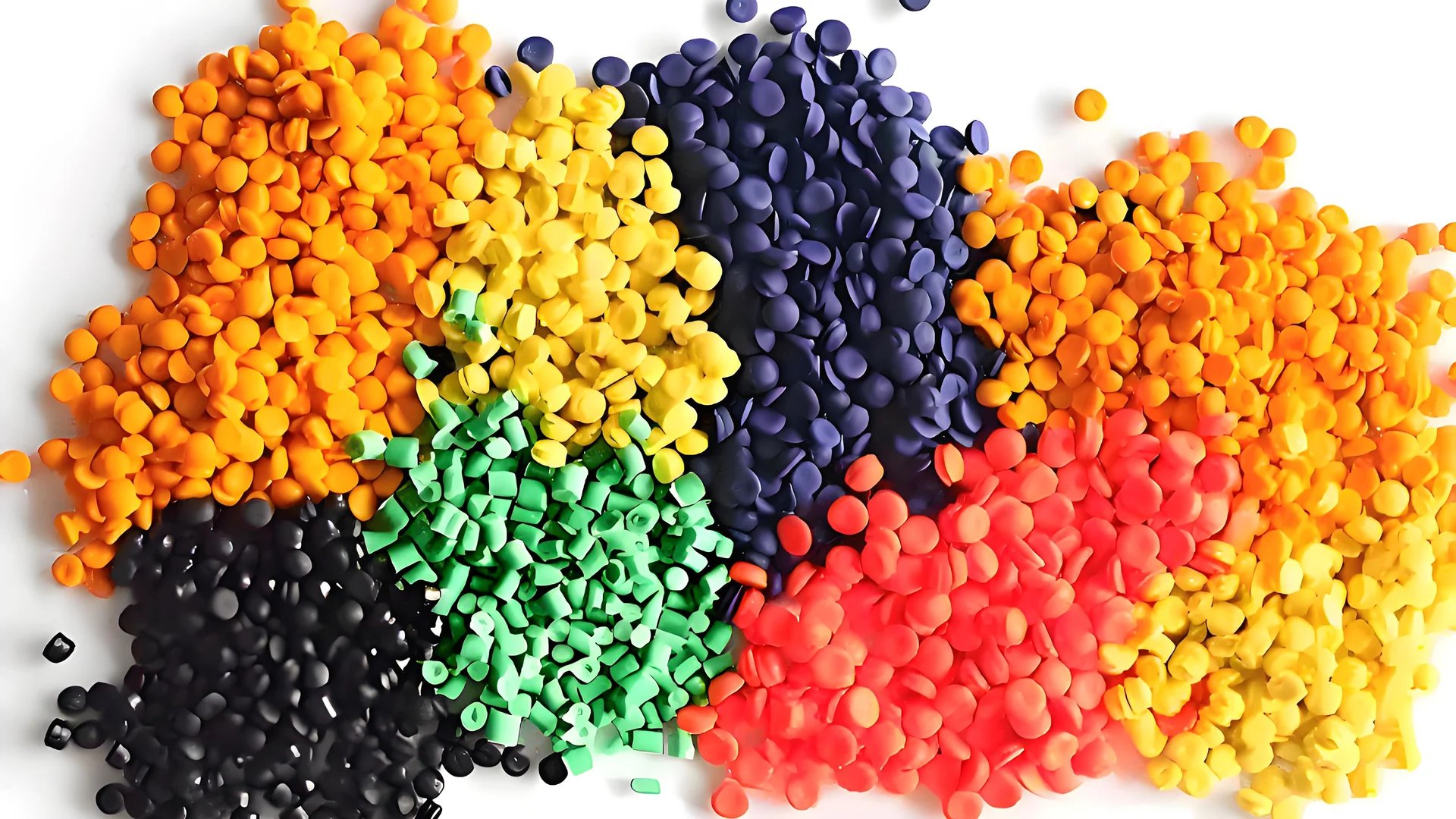
Understanding Material Characteristics
In injection molding, the choice of plastic material significantly impacts how quickly and efficiently the mold is filled. The two primary characteristics that influence this are fluidity and thermal stability.
- Fluidity: Plastics with high fluidity can flow more easily into mold cavities, reducing the required injection pressure and increasing filling speed. For instance, using a polycarbonate with low viscosity allows for rapid mold filling, which can be advantageous for complex designs.
- Thermal Stability: Choosing materials with good thermal stability ensures that they can be processed at higher temperatures without degrading. This property enhances fluidity and filling speed. Understanding thermal stability5 is vital in selecting appropriate materials for specific applications.
The Importance of Plastic Drying
Moisture content in plastic granules can severely impede filling speed. During injection, moisture can turn into steam, increasing resistance and slowing down the process. Ensuring plastics are thoroughly dried can mitigate these issues.
Material Type | Recommended Drying Time | Drying Temperature |
---|---|---|
ABS | 2-4 hours | 80°C – 90°C |
Nylon | 4-6 hours | 70°C – 80°C |
PET | 4-6 hours | 120°C – 160°C |
For example, drying ABS plastic correctly influences its performance6 in the molding process.
Matching Material with Product Requirements
Selecting a material isn’t just about speed; it must also meet product specifications and quality standards. For products requiring high precision or durability, engineers might choose a tougher plastic despite its lower fluidity, balancing filling speed with product integrity.
Consulting with material experts to match the plastic’s properties with product needs7 can help in achieving optimal production outcomes.
Impacts on Production Efficiency
Overall, thoughtful material selection enhances not just filling speed but also contributes to reducing cycle times and improving product consistency. Using materials like high-flow polyethylene for large parts or high-performance engineering plastics for components under stress demonstrates how material choice can optimize efficiency.
Effective selection of materials considering their flow characteristics and processing requirements is critical for achieving desired filling speeds and maintaining quality standards in injection molding.
High fluidity plastics increase filling speed.True
Plastics with high fluidity flow easily into molds, boosting speed.
Moisture in plastics does not affect filling speed.False
Moisture turns to steam, increasing resistance and slowing speed.
How Can Process Control Enhance Injection Molding Efficiency?
Achieving high efficiency in injection molding demands meticulous control of the entire process. By refining process parameters, manufacturers can significantly boost productivity while minimizing waste and defects.
Process control in injection molding involves precise temperature management, multi-stage injection techniques, and material preheating. These practices enhance the fluidity of the plastic, optimize filling speed, and improve product quality.
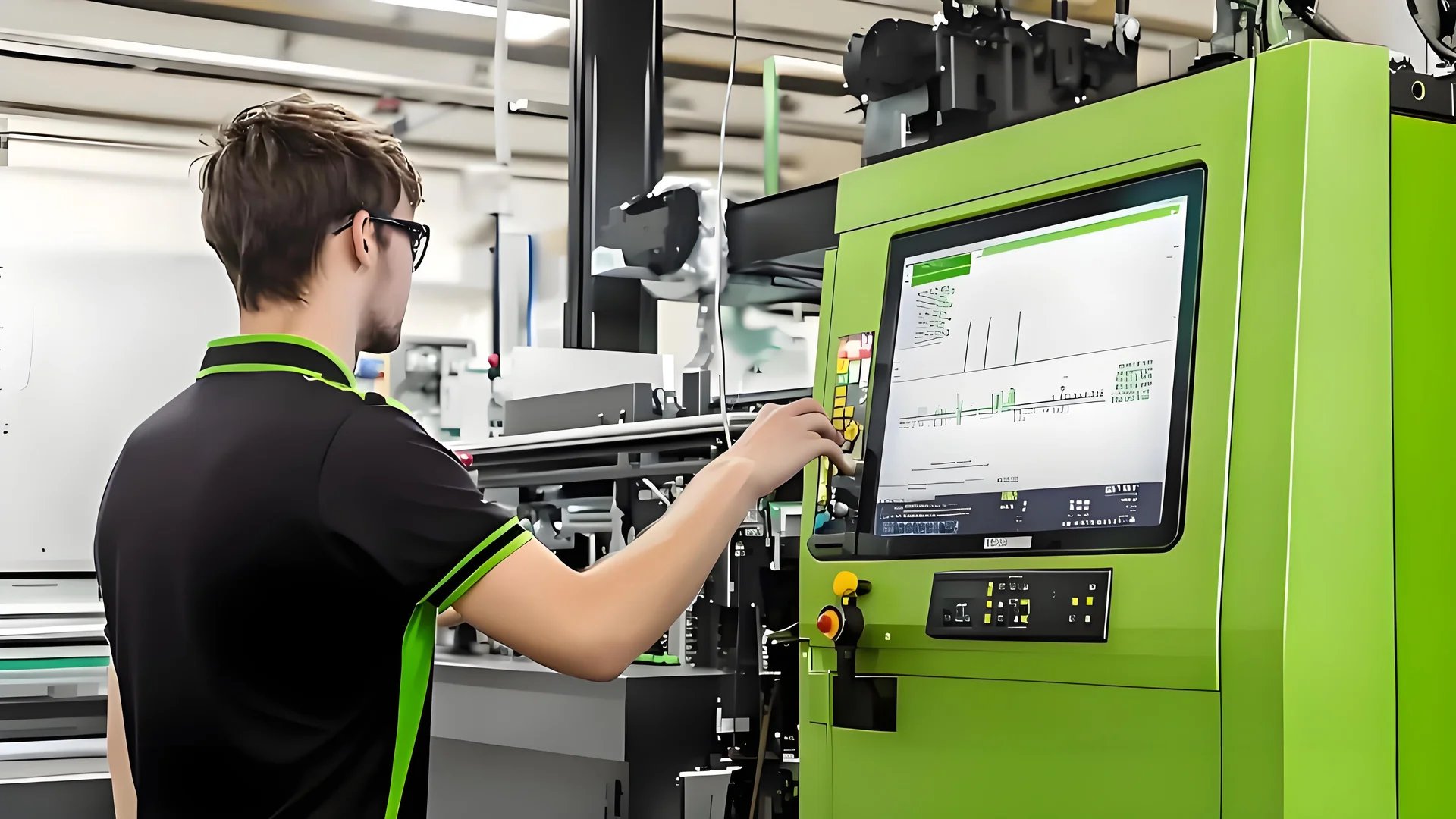
The Importance of Temperature Management
Controlling mold temperature is a critical factor in enhancing injection molding efficiency. Properly managed temperatures can reduce the viscosity of plastic materials, improving their fluidity and filling speed. However, caution is necessary to prevent overheating, which could lead to defects like warping or decomposition. Techniques such as hot air drying and infrared heating are effective for preheating plastic, ensuring that it fills molds efficiently.
Multi-Stage Injection Techniques
Multi-stage injection is a sophisticated technique that adjusts injection speed and pressure at different stages of the process. In the initial stage, a higher speed can be employed to fill the mold quickly. Subsequently, reduced speed and pressure help avoid issues like flash or bubbles. This method not only optimizes filling speed but also maintains the integrity of the final product.
For instance, in the early phase of filling, using higher injection speed allows for rapid mold filling. As the process continues, decreasing speed and pressure ensures a smooth finish and minimizes defects. Implementing such a multi-stage approach can result in improved cycle times and enhanced overall efficiency.
Preheating Plastic Materials
Preheating plastics before injection is another valuable strategy to improve efficiency. By increasing the temperature of the material slightly before it enters the mold, manufacturers can enhance fluidity and reduce resistance during filling. This step is particularly beneficial when working with materials that require higher processing temperatures due to their composition.
Various methods are available for preheating, such as using hot air or infrared heaters. Selecting the appropriate method depends on the specific type of plastic used and its thermal properties. By ensuring plastics are adequately preheated, the overall efficiency of the injection molding process is significantly enhanced.
Incorporating these advanced process control strategies not only boosts injection molding efficiency8 but also ensures a consistent quality of products. Such precision in controlling the injection process can lead to significant improvements in production rates and product reliability.
Preheating plastics reduces mold filling resistance.True
Preheating enhances fluidity, lowering resistance during mold filling.
Multi-stage injection increases defect rates in molding.False
It optimizes speed and pressure, reducing defects like flash or bubbles.
Conclusion
Optimizing filling speed is a holistic journey that blends equipment, molds, materials, and processes. By fine-tuning these elements, we can achieve faster cycles and higher quality products.
-
Learn how equipment tweaks can enhance filling speed and efficiency.: Adjusting the injection speed helps prevent issues like flow lines or air traps. 3. Cooling Time: The cooling time is the duration the part … ↩
-
Gain insights into selecting suitable gate types for improved efficiency.: Types of Injection Molding Gate · 1. Direct or Sprue Gates · 2. Edge Gates · 3. Submarine Gates · 4. Cashew Gates · 5. Diaphragm Gates · 6. Hot Runner … ↩
-
Learn about the benefits of exhaust grooves in mold design.: Properly opening the exhaust groove can greatly reduce the injection pressure, injection time, holding time and clamping pressure, making the … ↩
-
Explore strategies to enhance material flow within molds.: Mold flow analysis is a software-based simulation that predicts how a plastic resin will flow into and fill an injection mold. Learn more. ↩
-
Learn how thermal stability affects material processing.: Stable mold temperature reduces fluctuations in molding shrinkage, improving dimensional stability. For crystalline plastics, high mold … ↩
-
Discover the impact of proper drying on ABS quality.: Drying plastic resin is used to minimize or eliminate complications that may be caused by too much moisture in a plastic material. ↩
-
Find tips on aligning material choice with product needs.: Learn how to select the right material for your injection molding design with this technical overview of thermoplastic resins. ↩
-
Discover more techniques for optimizing injection molding processes.: Variable mold temperature technologies include systems that allow temperature control during the injection molding process. ↩