In the intricate world of plastic injection molding, every detail matters—especially when it comes to efficiency and quality. Let’s dive into the art of mastering the filling and holding stages, where precision makes all the difference.
To optimize the filling and holding stages in plastic injection molding, adjust the injection speed, pressure, and temperature according to product specifications and material characteristics. These adjustments help control melt flow and cooling, reducing defects and improving product quality.
But don’t stop there! Let’s explore the deeper implications of each parameter and uncover strategies that will truly transform your molding process.
Injection speed affects surface quality in molding.True
Adjusting injection speed impacts melt flow, influencing surface finish.
What Role Does Injection Speed Play in Molding Quality?
Injection speed is a pivotal factor in determining the quality of plastic molded products. Adjustments in this parameter can significantly affect the product’s surface finish, dimensional stability, and structural integrity.
Injection speed influences how plastic melt flows into the mold cavity, impacting surface quality and internal stresses. Fast speeds can lead to defects like burn marks, while slow speeds may cause incomplete fills. Balancing speed according to product specifications ensures optimal molding quality.
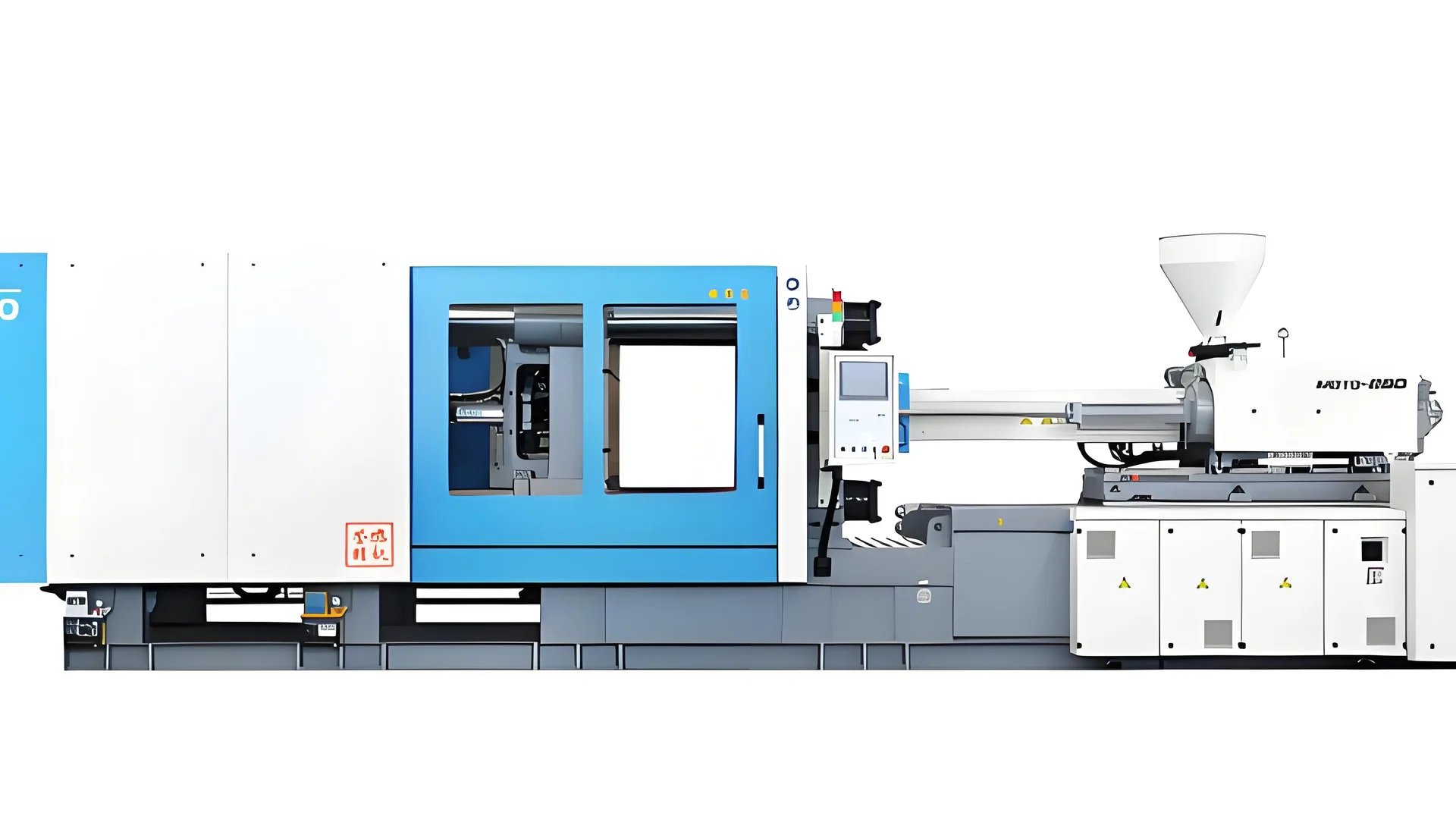
Understanding Injection Speed Dynamics
In plastic injection molding, injection speed dictates how quickly the molten plastic is pushed into the mold cavity. This process is crucial as it determines how well the material fills the cavity and adheres to the mold’s intricacies.
-
Fast Injection Speed: When the injection speed is too fast, it can cause phenomena such as melt spraying and burning. Melt spraying leads to uneven distribution of material, often resulting in cosmetic defects or weakened structural areas. On the other hand, high speeds can be beneficial for thin-walled products, ensuring the melt quickly fills the cavity before cooling begins.
-
Slow Injection Speed: Conversely, if the injection speed is too slow, issues such as short shots—where the mold does not fill completely—and flow marks may arise. These defects compromise both aesthetic and functional aspects of the final product.
Injection Speed | Advantages | Disadvantages |
---|---|---|
Fast | Quick fill for thin walls | Burn marks, melt spraying |
Slow | Controlled fill for complex shapes | Short shots, flow marks |
Application-Based Speed Adjustment
Adjusting injection speed should be closely aligned with the product’s design and material properties:
-
Thin-Walled Products: A higher injection speed is generally preferable. This approach ensures that the melt rapidly fills the cavity, minimizing cooling time which can lead to solidification before complete fill.
-
Thick-Walled Products: Lower speeds are often advantageous as they reduce internal stresses that may lead to warping or cracking post-molding. By controlling the rate of fill, manufacturers can maintain uniformity in wall thickness and density.
Impact on Product Quality
Properly adjusting injection speed not only affects surface aesthetics but also plays a significant role in maintaining structural integrity. For instance, a well-calibrated speed setting prevents excessive internal stresses which can lead to mold damage1, product flash, or even failure during use.
Moreover, choosing the right speed helps in achieving a balance between cycle time and product quality2, ultimately impacting production efficiency and cost-effectiveness.
Conclusion
While injection speed is just one of many parameters in injection molding, its role is undeniably critical. By understanding how it interacts with other factors like temperature and pressure, manufacturers can better optimize their processes for improved product quality.
Fast injection speeds can cause burn marks.True
Fast speeds increase friction and temperature, leading to burn marks.
Slow injection speeds eliminate all defects.False
Slow speeds can cause defects like short shots and flow marks.
How Can Injection Pressure Be Optimized for Different Plastics?
Injection pressure is pivotal in molding quality, yet varies with plastic types. Tailoring it correctly enhances both efficiency and product integrity.
Optimizing injection pressure involves adjusting it based on plastic fluidity, product design, and wall thickness. Proper calibration minimizes defects and maximizes mold filling efficiency.
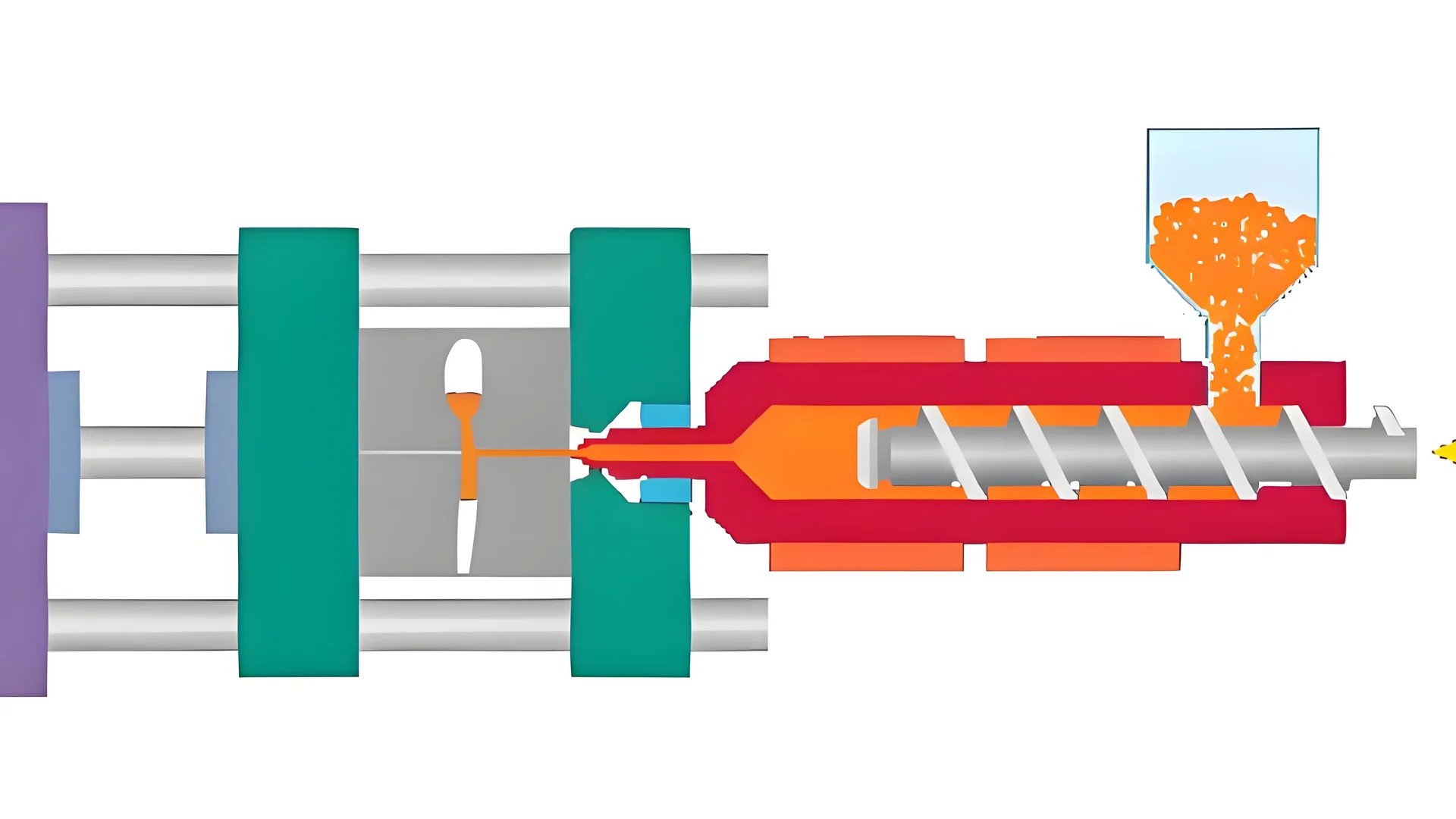
Understanding the Role of Injection Pressure
Injection pressure is a critical parameter that influences the flow of molten plastic into a mold cavity. By optimizing this pressure, manufacturers can ensure the efficient filling of complex geometries while minimizing potential defects such as flashing or short shots. The ideal injection pressure is determined by various factors including the type of plastic used, the product’s dimensions, and wall thickness.
Factors Influencing Injection Pressure
1. Plastic Fluidity
- Plastics with Poor Fluidity: These require higher injection pressures to ensure complete mold filling. For example, polycarbonate (PC) has high viscosity and often necessitates increased pressure.
- Plastics with Good Fluidity: Lower pressures can suffice, reducing the risk of mold damage or excessive flashing. Polypropylene (PP), known for its excellent flow properties, exemplifies this.
2. Product Design Considerations
- Complex Geometries: Higher pressures help fill intricate designs. This is crucial for products with detailed features or thin walls where swift cavity filling is necessary to prevent solidification.
- Simpler Designs: These may allow for reduced pressure settings, which conserves energy and prolongs mold life.
Plastic Type | Recommended Pressure Range (MPa) |
---|---|
Polycarbonate | 80-150 |
Polypropylene | 40-90 |
Balancing Pressure with Other Parameters
Injection Speed: A higher injection speed can compensate for lower pressure in certain scenarios, especially for thin-walled parts where fast fill times prevent premature cooling.
Barrel Temperature: Setting an appropriate temperature can enhance fluidity, potentially reducing the need for elevated pressures. For instance, crystalline plastics might require higher temperatures to lower viscosity effectively.
Practical Applications
- Case Study in Automotive Parts: In automotive component manufacturing, adjusting injection pressure according to the material’s characteristics and the part’s function (e.g., dashboards vs. internal brackets) can significantly enhance production efficiency and part quality.
By understanding these variables, manufacturers can adjust the injection pressure strategically3 to achieve optimal results in diverse molding scenarios. This adaptive approach ensures not only quality but also cost-efficiency by reducing waste and prolonging equipment lifespan.
Polycarbonate requires higher injection pressure than polypropylene.True
Polycarbonate has higher viscosity, needing more pressure for mold filling.
Simpler product designs require higher injection pressures.False
Simpler designs often need lower pressures, conserving energy and mold life.
Why Is Temperature Control Crucial in Injection Molding?
Precision in temperature control can make or break the quality of injection molded products. Here’s why it matters.
Temperature control in injection molding ensures proper melt flow, prevents defects like warping, and enhances overall product quality. Adjusting barrel, mold, and cooling temperatures based on material properties and product design is vital for consistent, high-quality production.
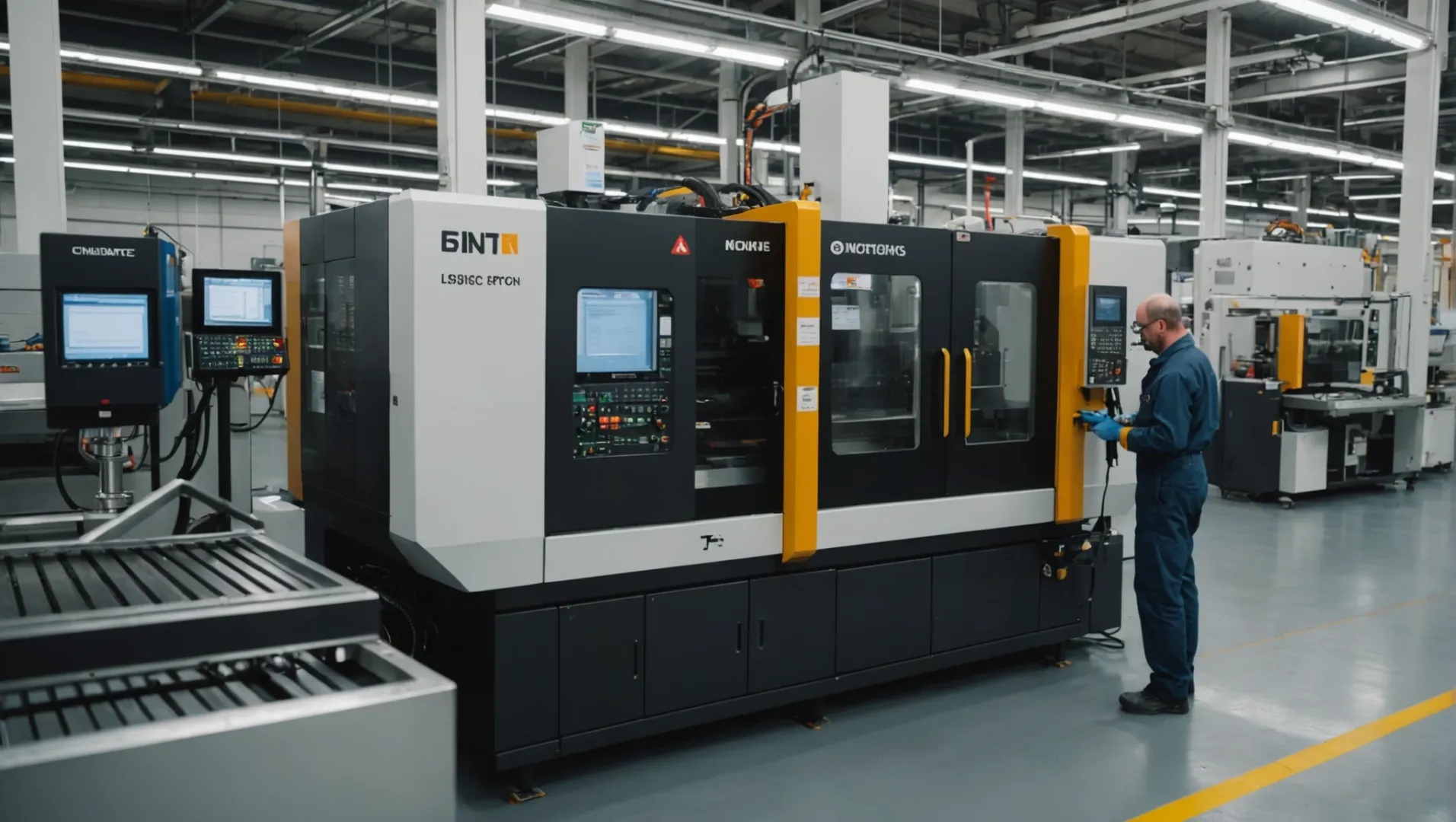
The Role of Barrel Temperature
Barrel temperature profoundly impacts the fluidity of the plastic melt. By adjusting this parameter, manufacturers can control the melt viscosity and ensure it fills the mold cavity effectively. For instance, crystalline plastics generally require higher barrel temperatures compared to amorphous types to achieve adequate flow.
A precisely managed barrel temperature4 prevents decomposition of the plastic while maintaining its fluidity. Excessive temperatures can lead to material degradation, impacting the final product’s strength and appearance. On the other hand, too low a temperature may cause incomplete filling, resulting in short shots.
Optimizing Mold Temperature
Mold temperature directly affects the cooling rate of the product, which is crucial for its structural integrity and surface finish. A higher mold temperature5 can enhance surface quality and reduce internal stress but might complicate demolding processes. Lower temperatures, however, can hasten cycle times but might lead to poor surface finish and increased residual stress.
For crystalline plastics, maintaining a high mold temperature is essential to achieve the desired crystallinity in the product. Conversely, amorphous plastics benefit from a lower mold temperature to prevent unwanted stress.
Cooling Time Considerations
The cooling stage solidifies the shape of the plastic part. Controlled cooling prevents warping and shrinkage, which can lead to inconsistencies in product dimensions. Adjusting the cooling time6 according to the wall thickness and size of the part is crucial.
Longer cooling times are typically required for thick-walled products to ensure uniform cooling throughout the part. For thin-walled products, shorter cooling times suffice, but care must be taken to avoid distortion.
Balancing Temperature with Pressure and Time
Temperature adjustments are closely interlinked with pressure and time settings in both the filling and holding stages. For optimal results, all three parameters should be harmonized based on the specific material and product design requirements. This holistic approach ensures that the molded parts meet quality standards consistently.
In summary, meticulous temperature control within injection molding not only enhances product quality but also optimizes manufacturing efficiency by minimizing defects and ensuring consistency across production batches.
Barrel temperature affects melt viscosity in injection molding.True
Adjusting barrel temperature controls plastic fluidity, ensuring mold fill.
Lower mold temperatures reduce cycle times but increase stress.True
Lower temperatures quicken cycles but may cause poor surface finish.
What Are Common Challenges in the Holding Stage?
Navigating the holding stage in plastic injection molding presents distinct challenges that can impact product quality and manufacturing efficiency.
Common challenges in the holding stage of plastic injection molding include excessive internal stress, shrinkage marks, and difficulty in demolding. These issues arise from incorrect holding pressure, time, and mold temperature settings, requiring precise adjustments based on product characteristics to ensure optimal outcomes.

Understanding the Role of Holding Pressure
Holding pressure is crucial as it compensates for cooling shrinkage by injecting additional plastic melt into the cavity post-filling. If set too high, it can lead to excessive internal stress and make demolding difficult. Conversely, too low a pressure may result in shrinkage marks and size instability.
To navigate these challenges, it’s vital to consider the product’s shape, size, and wall thickness. Larger or thicker products typically require higher holding pressure, whereas smaller or thinner products benefit from reduced pressure. Adjusting holding pressure7 effectively can significantly impact product quality.
The Importance of Holding Time
Holding time refers to the duration the plastic melt is maintained under holding pressure. An overly extended holding time can introduce excessive stress and lengthen production cycles, while a short duration might lead to unstable sizes and shrinkage.
Optimal holding time varies based on product dimensions; larger or thicker items need longer durations. Understanding and adjusting the holding time appropriately is critical for achieving desired outcomes.
Product Type | Suggested Holding Time |
---|---|
Large/Thick Walls | Longer |
Small/Thin Walls | Shorter |
Mold Temperature: A Balancing Act
Mold temperature plays a pivotal role in determining product quality. High temperatures can complicate demolding and cause deformation, whereas low temperatures may lead to poor surface quality and increased internal stress.
Adjusting mold temperature requires considering plastic type, product shape, and size. For crystalline plastics, higher temperatures are generally better; for amorphous plastics, reducing the temperature is advisable. Controlling mold temperature8 is essential for minimizing defects and enhancing finish quality.
By examining these factors critically, manufacturers can mitigate common holding stage challenges, leading to improved efficiency and superior product results.
High holding pressure causes excessive stress.True
High holding pressure increases internal stress, complicating demolding.
Low mold temperature improves surface quality.False
Low mold temperatures can lead to poor surface quality.
Conclusion
Optimizing your injection speed, pressure, and temperature is key to enhancing quality and efficiency in plastic injection molding. Take these insights to heart, experiment, and watch your production improve!
-
Learn about avoiding mold damage through correct speed settings.: Generally, at the same injection speed, higher injection pressure improves the plastic’s flow capability, enhancing the dimensional precision … ↩
-
Explore strategies for optimizing cycle time while maintaining quality.: Maintaining a proper balance between the injection speed, pressure, and cooling time is important to achieve high-quality, defect-free molded … ↩
-
Learn advanced techniques for efficient injection pressure optimization.: Steps to INJECTION MOLDING Process Optimization · 1. Tool functionality examination · 2. Short shot testing · 3. Gate seal studies · 4. Sample parts evaluation/data … ↩
-
Learn how precise barrel temperature impacts melt viscosity and product quality.: Shown here are the four basic barrel zones on an injection molding machine that must be set up properly, along with the nozzle body and tip. ↩
-
Discover how mold temperature influences surface finish and stress levels.: In amorphous polymers such as ABS and polycarbonate, higher mold temperatures produce lower levels of molded-in stress and consequently better … ↩
-
Explore strategies for adjusting cooling times to enhance product consistency.: Injection molding cycle time or Cooling time is one of the major factors in improving and maintaining efficiency in the injection molding process. ↩
-
Discover strategies for setting optimal holding pressure in molding.: Hold pressure and speed are usually 50% – 65% of the top injection pressure and speed. That is to say, the holding pressure is approx. 0.6 – 0.8 … ↩
-
Learn why precise mold temperature control is crucial for quality.: Stable mold temperature reduces fluctuations in molding shrinkage, improving dimensional stability. For crystalline plastics, high mold … ↩