Understanding how to achieve optimal filling balance in multi-cavity molds can transform your injection molding outcomes. Let’s explore effective strategies that truly make a difference!
To optimize filling balance in multi-cavity molds, focus on a balanced runner and gate design, adjust process parameters like injection pressure and speed, and ensure proper equipment maintenance. These strategies enhance product quality and manufacturing efficiency.
While these strategies provide a strong foundation, delving deeper into the specifics of mold design, process parameter fine-tuning, and meticulous equipment upkeep can further refine your molding operations. Keep reading to uncover detailed insights that can transform your production capabilities.
Balanced runner systems ensure uniform cavity filling.True
Balanced runners have equal length and size, reducing flow resistance.
How Does Runner Design Impact Filling Balance?
The runner design in injection molding plays a pivotal role in achieving uniform filling across all cavities, directly influencing product quality and consistency.
A well-designed runner system ensures equal pressure and speed of melt flow to each cavity, achieving a balanced filling process essential for high-quality production.
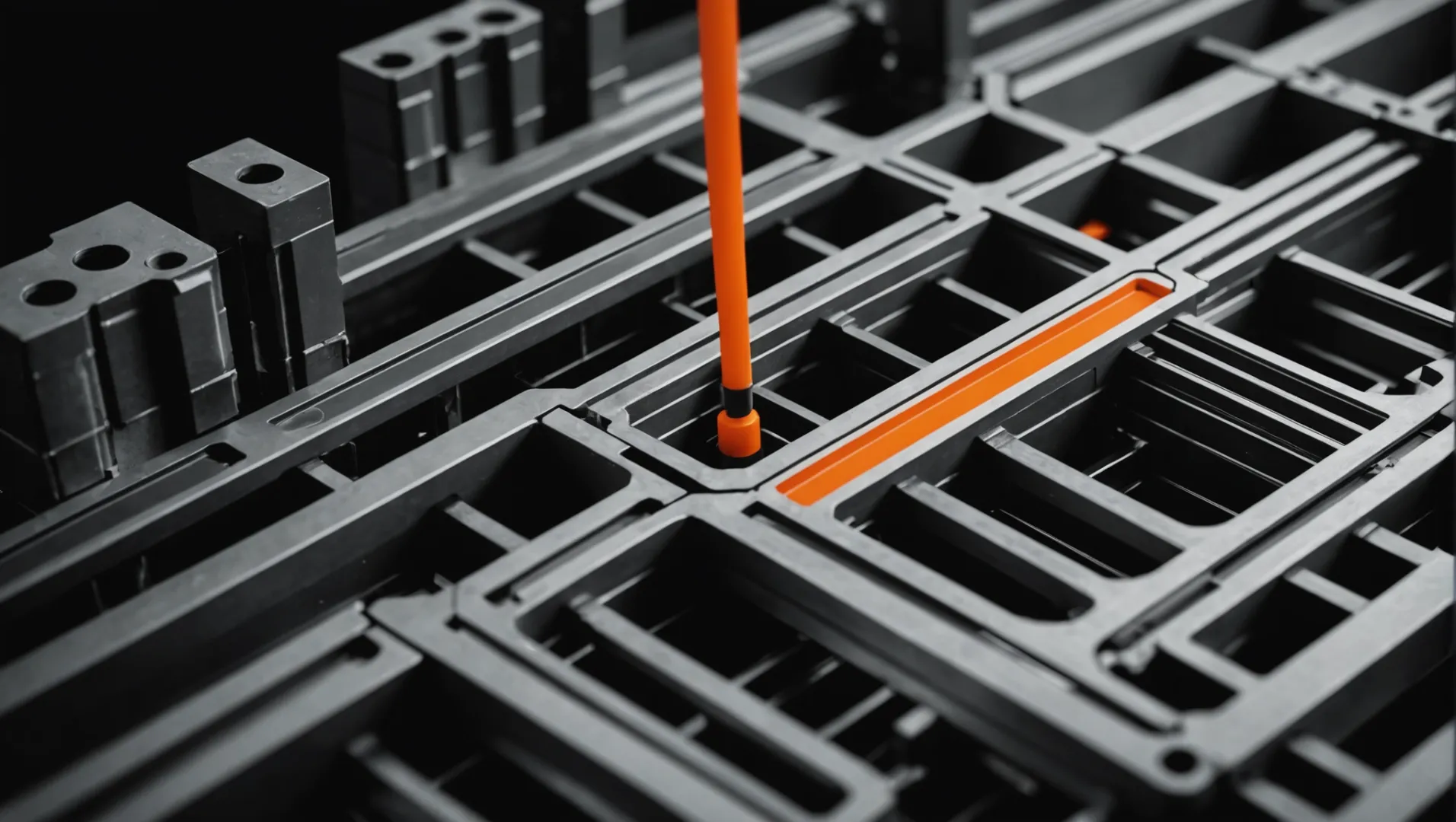
Understanding the Importance of Balanced Runner Systems
In injection molding, a balanced runner system is critical for ensuring that the melt flows to each cavity at the same pressure and speed. This uniformity is vital for maintaining the quality and consistency of the final products. A balanced runner usually has the same length, cross-sectional shape, and size, which helps reduce variations in flow resistance. The balance can be visualized as ensuring equal distribution paths that prevent any one cavity from being overfilled or underfilled.
Key Aspects of Runner Design
-
Length and Cross-Sectional Uniformity
- The runners should have consistent lengths and similar cross-sectional areas to minimize resistance.
- Variations can lead to uneven pressure, causing discrepancies in filling.
- Learn more about balancing runners1
-
Branch Angles and Transition Areas
- Angles and transition areas should be smooth to reduce pressure loss during flow.
- Avoid sharp angles and sudden changes in cross-sectional areas as these can lead to turbulence and inefficient flow.
-
Hot Runner Systems
- For large multi-cavity molds, hot runner systems provide superior control over temperature and pressure at each gate.
- This system helps achieve a better filling balance by allowing precise adjustments.
- Explore benefits of hot runner systems2
Practical Implementation in Injection Molding
Let’s look at how these principles are applied in real-world scenarios:
Parameter | Balanced System Benefit |
---|---|
Pressure Consistency | Ensures uniform melt flow to each cavity |
Temperature Control | Maintains consistent material properties |
Speed Regulation | Prevents overfilling and material wastage |
Case Study: A Multi-Cavity Mold Application
In a recent application, a manufacturer faced issues with uneven product quality due to an unbalanced runner system. By redesigning their runners to have equal lengths and improving the branch transitions, they achieved a significant reduction in product defects. Furthermore, incorporating a hot runner system allowed them to finely tune temperature settings, resulting in more uniform cavity fills.
Implementing these changes not only improved the quality of the final products but also enhanced overall production efficiency. Such examples underscore the importance of precise runner design in injection molding operations.
Balanced runners reduce flow resistance in injection molding.True
Balanced runners ensure uniform melt flow, minimizing variations.
Hot runner systems decrease pressure control in molds.False
Hot runner systems enhance pressure control, improving filling balance.
What Role Does Gate Design Play in Mold Efficiency?
Gate design is pivotal in determining the efficiency and quality of mold production processes.
Gate design significantly affects mold efficiency by influencing material flow, pressure distribution, and cooling time. Proper gate selection and placement ensure uniform filling, reduce defects, and enhance product quality.
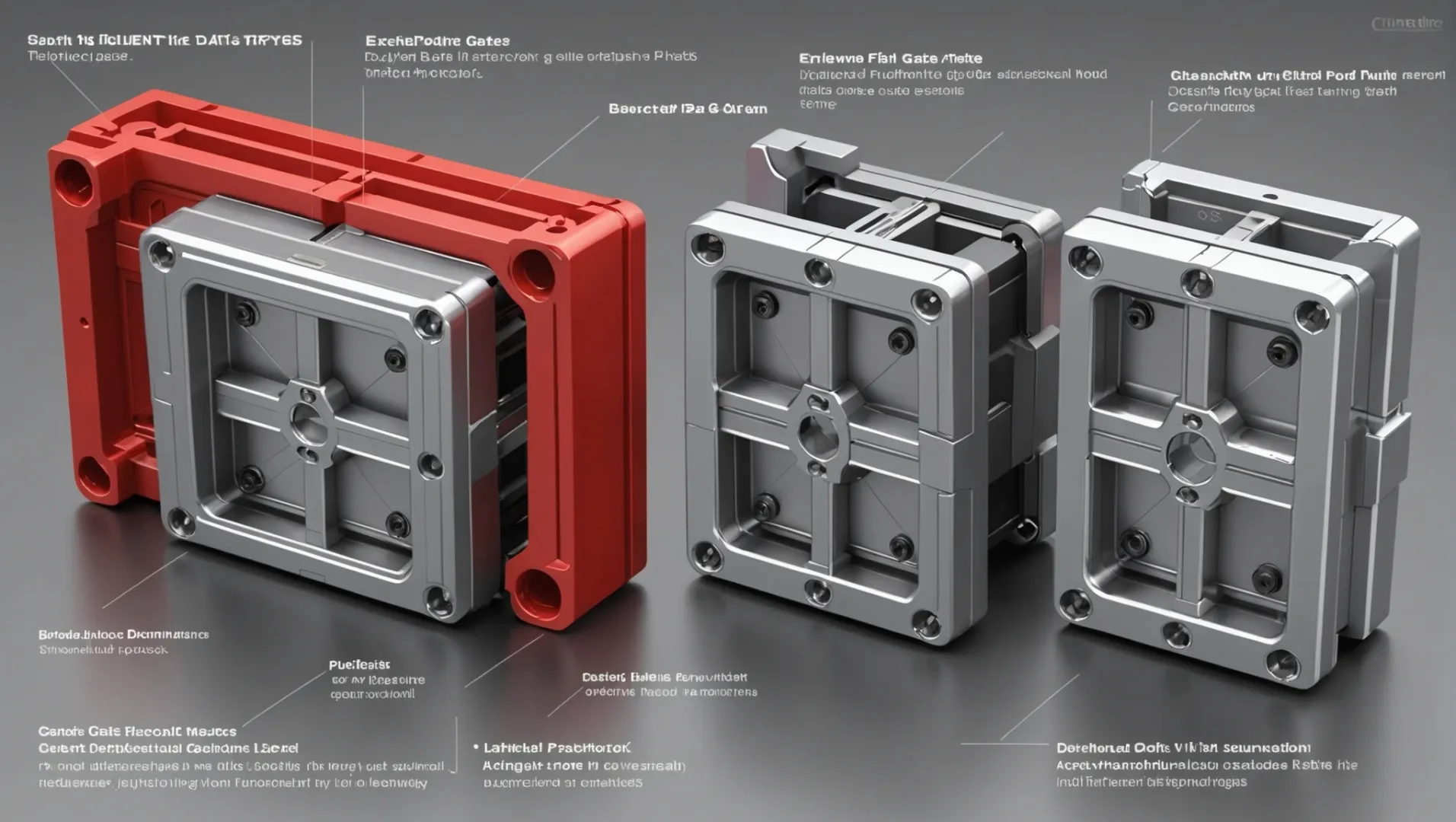
Understanding Gate Types and Their Impact
Gate design isn’t just about where you place the gate but also the type you choose. Common types include side gates, point gates, and latent gates. Each has unique characteristics that can be leveraged depending on the plastic material used and the desired product outcome. For instance, choosing the right gate type3 can mitigate defects such as air traps and weld lines.
- Side Gates: These are versatile and can be used in various applications. They offer easy removal but may leave a noticeable mark on the product.
- Point Gates: Ideal for automatic degating and minimal gate vestige, they are suitable for small, precise components.
- Latent Gates: Used for aesthetic products as they hide the gate vestige within the part.
Gate Size and Placement Considerations
The size of the gate plays a critical role in mold efficiency. A properly sized gate4 ensures adequate flow without causing excessive pressure or material wastage.
- Undersized Gates: Can lead to incomplete filling and high pressure loss, affecting the structural integrity of the product.
- Oversized Gates: While they facilitate easier flow, they might result in excessive material use and longer cooling times.
Positioning is equally crucial. Placing the gate near the geometric center of the cavity can help reduce flow distance and ensure uniform distribution. Multiple gates might be necessary for larger molds to maintain consistency across cavities.
Simulation Analysis for Optimal Gate Design
Simulation tools are indispensable for predicting how changes in gate design affect mold efficiency. By simulating different scenarios, engineers can optimize gate size and placement5 without costly trial-and-error in physical production. This method allows for precise adjustments that lead to better quality control and efficient manufacturing cycles.
Simulation can reveal potential issues like flow imbalances or air entrapment, allowing preemptive design changes that save time and resources in production.
Side gates leave a noticeable mark on the product.True
Side gates are versatile but may leave marks after removal.
Undersized gates increase material wastage in molds.False
Undersized gates cause incomplete filling, not material wastage.
How Can Process Parameters Be Optimized for Better Results?
Process parameter optimization is key to achieving superior results in injection molding.
To optimize process parameters, adjust injection pressure and speed, control mold and melt temperatures, and utilize multi-stage injection. These adjustments ensure better filling balance, enhancing the final product’s quality.
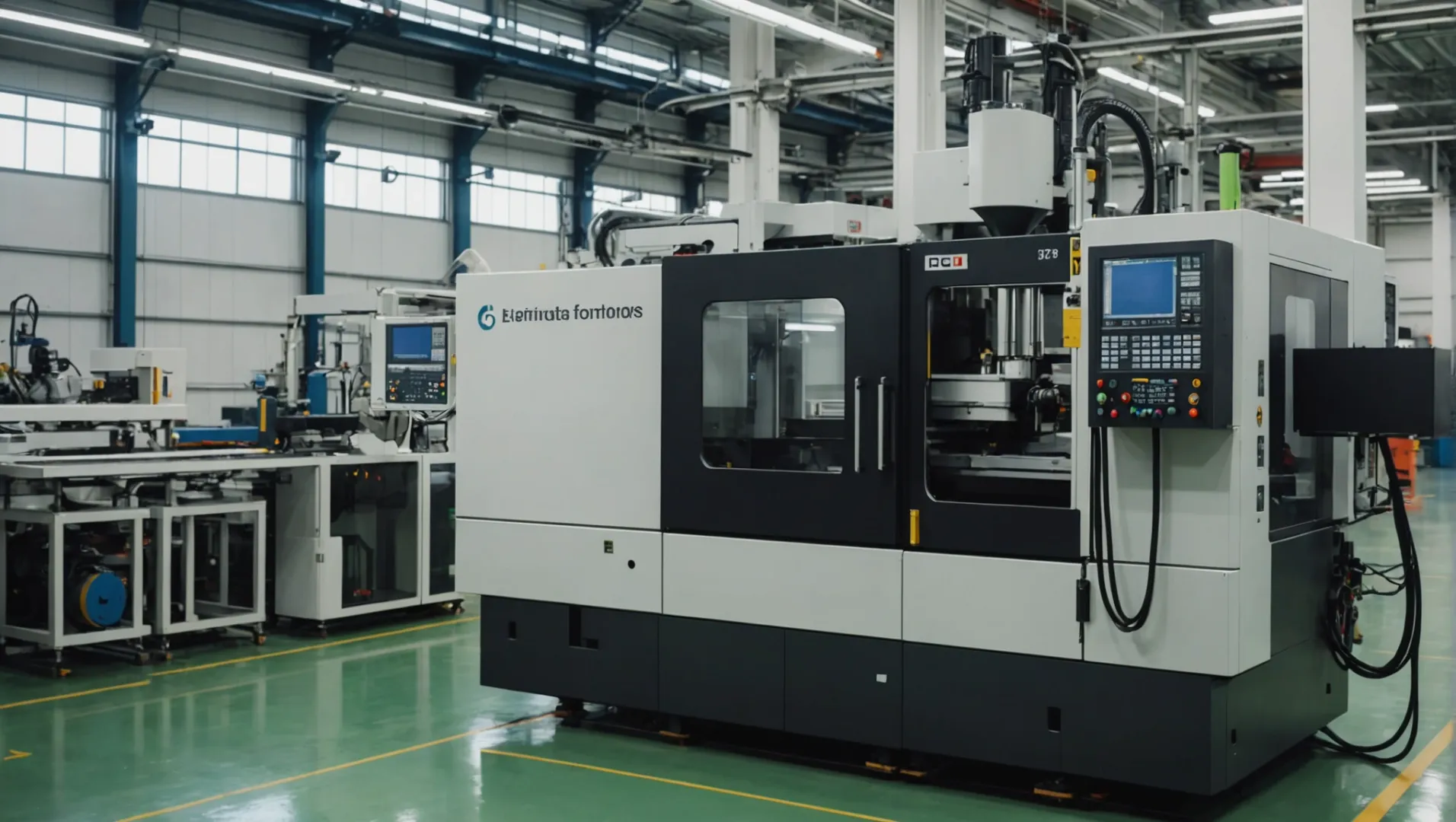
Adjusting Injection Pressure and Speed
Injection pressure and speed are crucial elements in molding operations that require careful calibration. To begin with, a gradual adjustment of these parameters can help identify the best combination for optimal flow dynamics. For instance, increasing the injection pressure can improve the melt’s fluidity but might risk excessive pressure holding and potential deformation of the product. Conversely, an elevated injection speed can reduce filling time but may lead to melt ejection and instability.
Implementing a multi-stage injection process6 allows for pressure and speed adjustments during different phases of the filling process. At the initial stage, lower pressure and speed help avoid melt ejection. Subsequently, increasing these parameters during the mid-stage ensures rapid cavity filling. Finally, a reduced pressure during the holding phase prevents excessive product shrinkage.
Controlling Mold and Melt Temperatures
Mold temperature significantly affects the melt’s fluidity and cooling rate. A higher mold temperature decreases viscosity, enhancing fluidity but also extending cooling time and the production cycle. Achieving uniform temperature across all cavities can lead to a more balanced fill.
Optimizing melt temperature is equally important. Excessively high melt temperatures can cause plastic degradation, while lower temperatures increase flow resistance. Selecting the right temperature based on plastic material properties and production needs ensures consistency across cavities.
Leveraging Simulation and Debugging Techniques
Simulation tools are invaluable in determining the appropriate gate size and positioning, as well as in testing different combinations of injection pressures and speeds. They allow manufacturers to visualize potential outcomes and make informed decisions before actual production begins.
Actual debugging further refines these simulations by testing them in real-world settings. This step helps in fine-tuning process parameters to align with specific production environments.
Continuous Monitoring and Adjustment
Regular monitoring of the entire process ensures that any deviations from the optimal parameters are quickly identified and corrected. This proactive approach not only maintains product quality but also enhances manufacturing efficiency.
Process parameter optimization is an ongoing task that requires attention to detail, knowledge of material properties, and a willingness to experiment with different settings. By mastering these areas, manufacturers can achieve remarkable improvements in their injection molding processes.
Increasing injection speed reduces filling time.True
Higher injection speeds fill molds faster, cutting down cycle time.
Higher mold temperature increases melt viscosity.False
Higher mold temperatures decrease viscosity, improving fluidity.
Why Is Equipment Maintenance Critical for Mold Performance?
Equipment maintenance is essential for ensuring that molds perform optimally, impacting both efficiency and product quality.
Equipment maintenance is crucial for mold performance as it ensures reliability, reduces downtime, and maintains the precision required for high-quality production. Regular maintenance of machines and molds helps avoid defects, prolongs equipment life, and ensures consistent product quality.
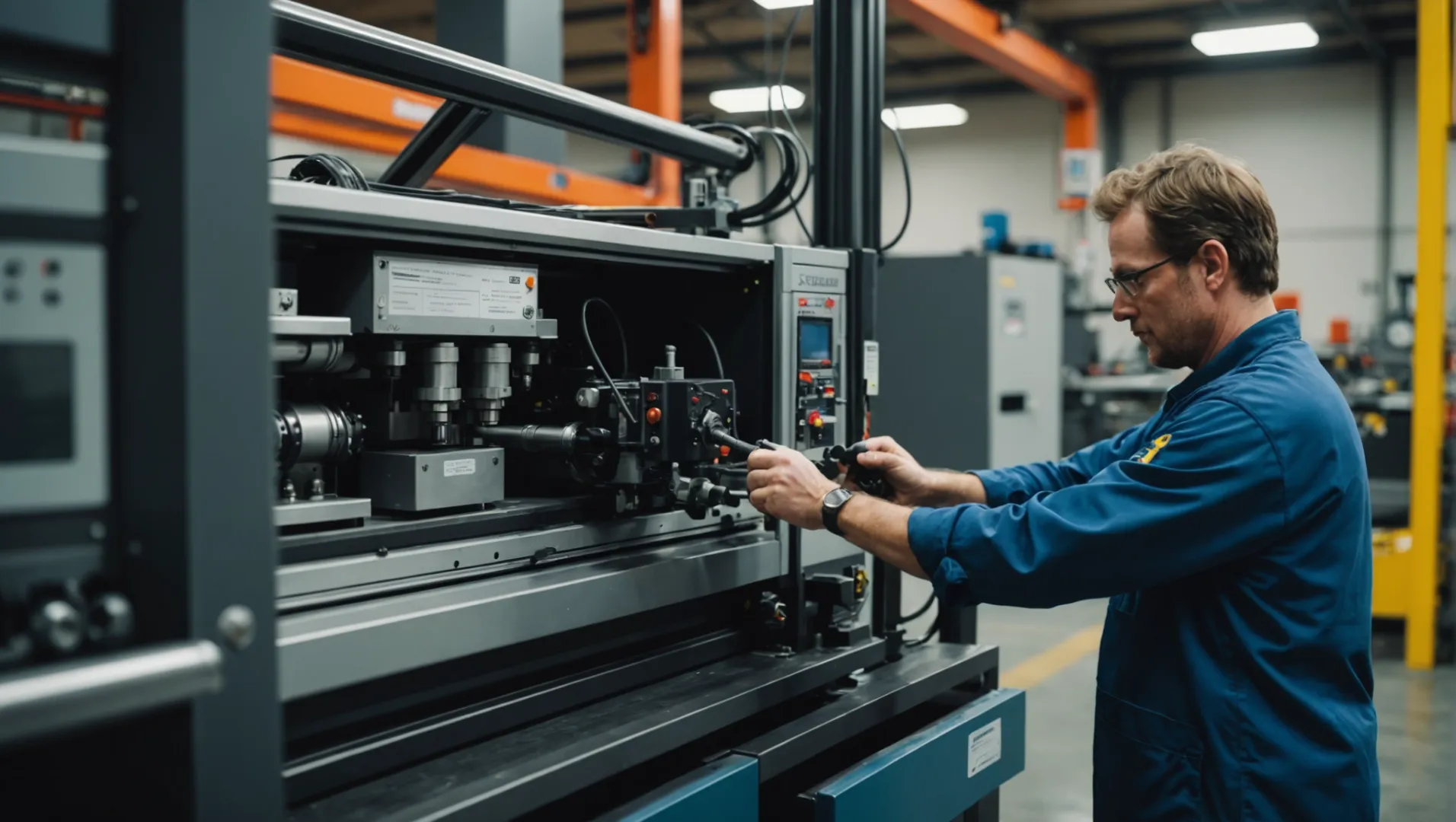
Ensuring Reliability and Reducing Downtime
One of the primary reasons why equipment maintenance7 is critical for mold performance is the reliability it provides. Injection molding machines are complex systems that require precision in operation. Regular maintenance checks help identify potential issues before they lead to machine breakdowns, thus reducing unexpected downtime. For instance, checking the hydraulic system regularly can prevent leaks that could disrupt the molding process.
Moreover, by maintaining the electrical components, you ensure that all sensors and controllers function correctly, avoiding costly interruptions and quality issues.
Prolonging Equipment Life
Regular maintenance not only prevents sudden failures but also extends the lifespan of the equipment. This is particularly important for multi-cavity molds where even minor wear and tear can lead to significant performance issues. For example, lubricating moving parts such as ejector pins and sliders ensures smooth operation and reduces wear, thus extending the mold’s operational life.
A detailed maintenance schedule should include:
Component | Maintenance Activity | Frequency |
---|---|---|
Hydraulic System | Check for leaks | Monthly |
Electrical System | Inspect sensors | Quarterly |
Mold Parts | Lubricate moving parts | Bi-weekly |
Machine Calibration | Verify settings | Annually |
Maintaining Precision and Consistency
Precision is key in injection molding to ensure each cavity is filled correctly. Regular cleaning and maintenance of the mold itself help maintain this precision. Over time, residues from plastic materials can accumulate on the mold surfaces, affecting the flow balance and ultimately the quality of the final product. Regular cleaning prevents these buildups and maintains the mold’s accuracy.
Furthermore, maintaining precise calibration of the injection machine ensures that injection pressure and speed remain consistent, which is critical for producing high-quality products.
In conclusion, while a robust maintenance strategy requires time and resources, it pays off by ensuring high-performance levels of molds and equipment. Investing in regular maintenance enhances product quality, reduces operational costs, and improves overall production efficiency.
Maintenance reduces mold downtime significantly.True
Regular checks prevent breakdowns, ensuring continuous operation.
Ignoring maintenance enhances mold precision.False
Neglect leads to residue buildup, affecting flow and quality.
Conclusion
Mastering these optimization strategies leads to superior mold performance and product quality. Reflect on your current practices and consider implementing these improvements for enhanced efficiency.
-
Explore techniques for achieving uniform melt flow distribution.: Figure 1: Two naturally balanced (symmetric) runner systems and one counter-example. Figure 2: An artificially balanced runner system. Page 2. Injection Molding. ↩
-
Discover how hot runners improve filling balance and efficiency.: While both hot runner and cold runner systems have their benefits, for design flexibility as well as reduced cycle times and costs, hot runner … ↩
-
Explore various gate types to enhance mold efficiency.: Gates come in various designs, including edge gates, sub gates, and direct sprue gates, which we will discuss further below. ↩
-
Learn how gate size impacts flow and efficiency.: The ideal gate size is based on the wall thickness of the part, the volume of the part, the material viscosity under processing conditions, the … ↩
-
Understand how simulations refine gate designs effectively.: Gate placement in the molding design is critical, as it affects the quality of the parts being manufactured, as well as the ability to correctly inject the … ↩
-
Explore how multi-stage injection enhances mold filling precision.: Multi-stage injection and multi-stage pressure holding are part of molding process. Control of multi-stage injection can effectively improve … ↩
-
Understand how maintenance impacts reliability and reduces production downtime.: Injection molding tool maintenance is crucial to developing consistent, high-quality injection mold medical devices. Plastic injection molding contract … ↩