Injection molding is more than just a process—it’s an art form that shapes high-quality plastic products. But did you know that the secret to success lies in the feed position?
Optimizing the feed position in injection molding involves strategic planning during product design, mold design, and process parameter adjustments. This ensures balanced melt flow, reduces defects, and enhances both product quality and production efficiency.
While grasping the basics is important, let’s dive into some transformative strategies that can really change the game for your injection molding process.
Uniform wall thickness improves melt flow in injection molding.True
Consistent wall thickness ensures balanced melt flow, reducing defects.
How Does Product Design Impact Feed Position in Injection Molding?
In injection molding, the design phase is crucial for determining the optimal feed position, influencing quality and efficiency.
Product design impacts feed position in injection molding by influencing melt flow through wall thickness analysis and shape considerations, ensuring even distribution and minimal defects.
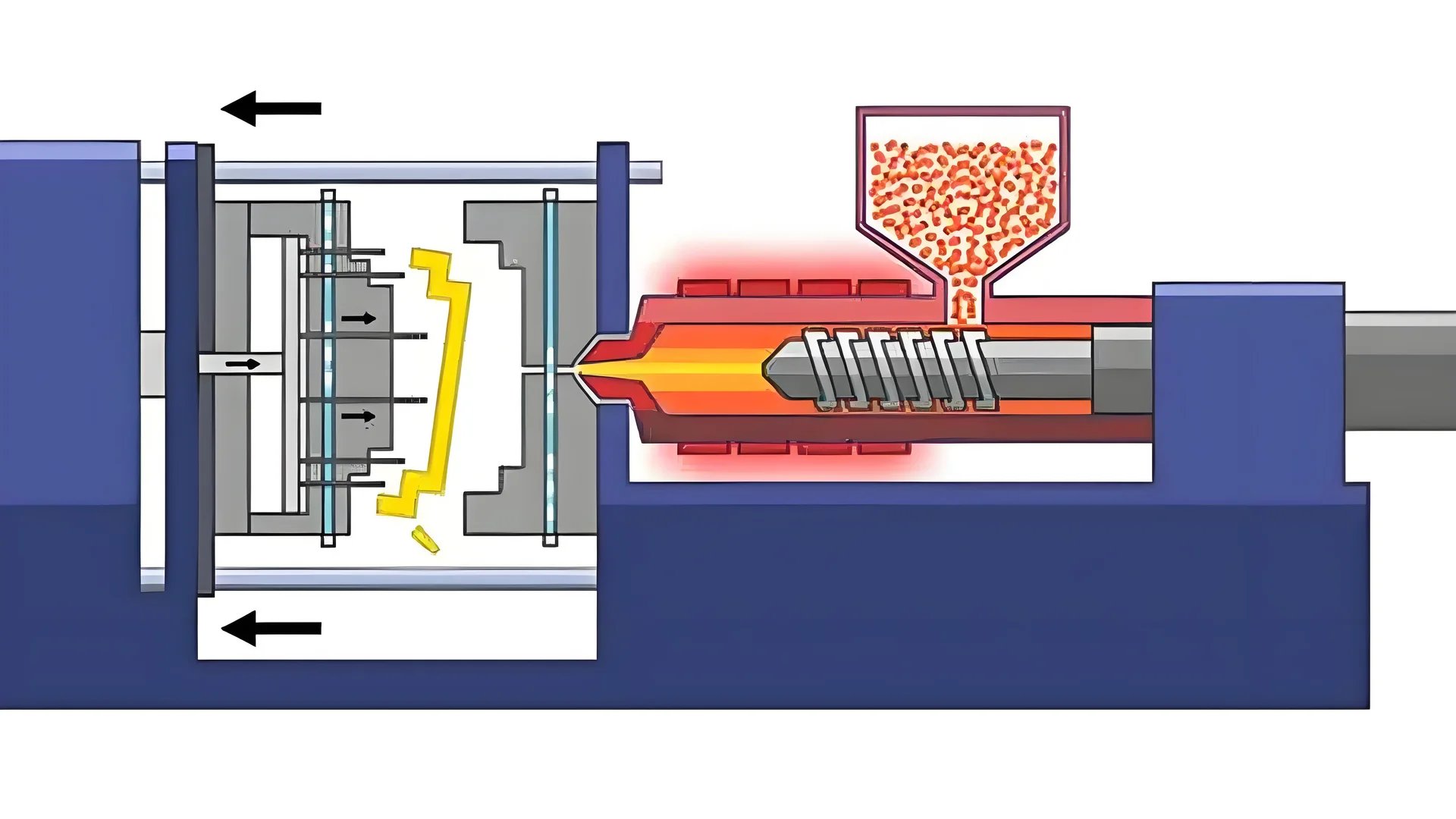
Wall Thickness Considerations
Uniform wall thickness plays a pivotal role in maintaining consistent melt flow. In injection molding, uneven wall thickness can result in unbalanced melt flow, leading to defects such as sink marks or internal voids. During the product design stage, a detailed analysis should ensure uniformity to facilitate an optimal feed position1.
- Example: Consider a plastic casing design where a sudden increase in wall thickness at the corners could lead to defects. By gradually transitioning the thickness from thick to thin, melt flow is more uniform, optimizing the feed position.
Shape and Structure Influences
The geometric shape and structure of a product are critical factors in determining the feed position. Products with complex shapes—like those with deep cavities or undercuts—require strategic placement of the feed position to ensure smooth melt flow.
- Example: For a component with a deep cavity, positioning the feed near this area can help ensure that the melt fills difficult sections first, reducing defects like short shots.
Practical Design Considerations
Incorporating practical design considerations helps enhance the efficiency of the injection molding process. The table below outlines key factors and their potential impact on feed position:
Design Factor | Impact on Feed Position |
---|---|
Uniform Wall Thickness | Promotes balanced melt flow |
Gradual Thickness Transition | Reduces flow resistance |
Complex Shape Proximity | Ensures complete filling of intricate areas |
By paying attention to these factors during the initial design phase, manufacturers can significantly improve both the quality of the final product and the efficiency of the production process. More insights into mold design2 can further enhance understanding of feed position optimization in injection molding.
Uniform wall thickness ensures balanced melt flow.True
Uniform wall thickness helps maintain consistent melt flow, reducing defects.
Complex shapes do not affect feed position.False
Complex shapes require strategic feed placement to ensure complete filling.
What Role Does Mold Design Play in Optimizing Feed Position?
Mold design is a pivotal element in determining the efficiency and quality of the injection molding process. It directly influences how the feed position can be optimized to achieve seamless production.
Mold design plays a crucial role in optimizing feed position by influencing factors such as gate type, runner layout, and cooling system. These elements ensure effective melt flow, reduce defects, and improve product quality and production efficiency.
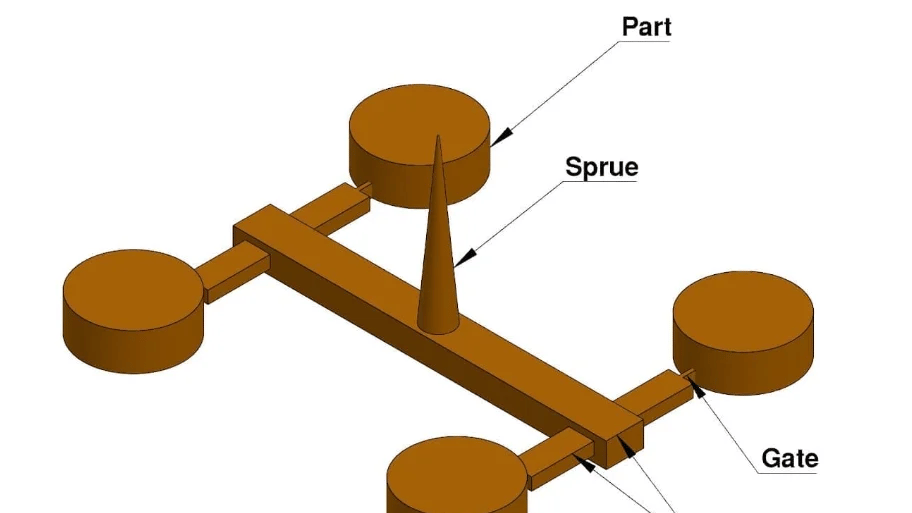
The Significance of Gate Type Selection
Selecting the appropriate gate type is fundamental in optimizing the feed position. The type of gate impacts not only the appearance of the final product but also the ease of manufacturing and efficiency.
- Side Gates: Typically simple to process and cost-effective, side gates can, however, leave noticeable marks on the product’s surface. They are ideal for less complex items where aesthetics are not a primary concern.
- Point Gates: Offering a smaller gate mark and suitability for automated production, point gates are often used when minimal surface blemishes are desired. Their complexity, though, can increase manufacturing costs.
- Latent Gates: These automatically sever the gate during demolding, providing superior appearance quality. Ideal for products with high aesthetic requirements, latent gates can be strategically placed in concealed areas.
Choosing the right gate type for your specific product needs is essential for optimizing feed position effectively.
Impact of Runner System Design
The runner system is a crucial conduit through which the melt travels from the sprue to the mold cavity. Its design heavily influences the flow characteristics and pressure loss of the melt.
Runner Cross Section | Advantages | Disadvantages |
---|---|---|
Circular | Lowest flow resistance | Higher processing cost |
Trapezoidal | Easier to process | Moderate flow resistance |
The aim is to ensure a balanced layout, particularly in multi-cavity molds, to maintain consistent feed pressure and melt flow rate across all cavities. This balance reduces defects and enhances product quality.
Cooling System Design Considerations
Efficient cooling systems play a vital role in maintaining optimal mold temperature, which in turn affects melt flow and product quality.
- Localized Cooling: Strategic placement of cooling channels near the feed position prevents overheating and ensures uniform cooling.
- Material Selection: Using materials with high thermal conductivity can expedite heat dissipation, enhancing overall efficiency.
The cooling system must be meticulously designed to avoid disrupting melt flow paths while maintaining temperature consistency across the mold surface. For instance, excessive cooling might lead to uneven shrinkage or warping.
By focusing on these aspects of mold design—gate selection, runner system, and cooling setup—manufacturers can significantly enhance their feed position optimization strategies. Such adjustments not only improve product quality but also streamline production efficiency.
Side gates are ideal for complex items in injection molding.False
Side gates are better for simple items, not complex ones.
Circular runners have the lowest flow resistance in molds.True
Circular runners provide the least flow resistance, aiding efficiency.
How Do Process Parameters Affect Feed Position Optimization?
Understanding process parameters is crucial in refining feed position for injection molding, affecting flow and product quality.
Feed position optimization in injection molding hinges on key process parameters: injection speed, pressure, and mold temperature. These factors impact melt flow dynamics, ensuring efficient filling, minimizing defects, and achieving high-quality outcomes.
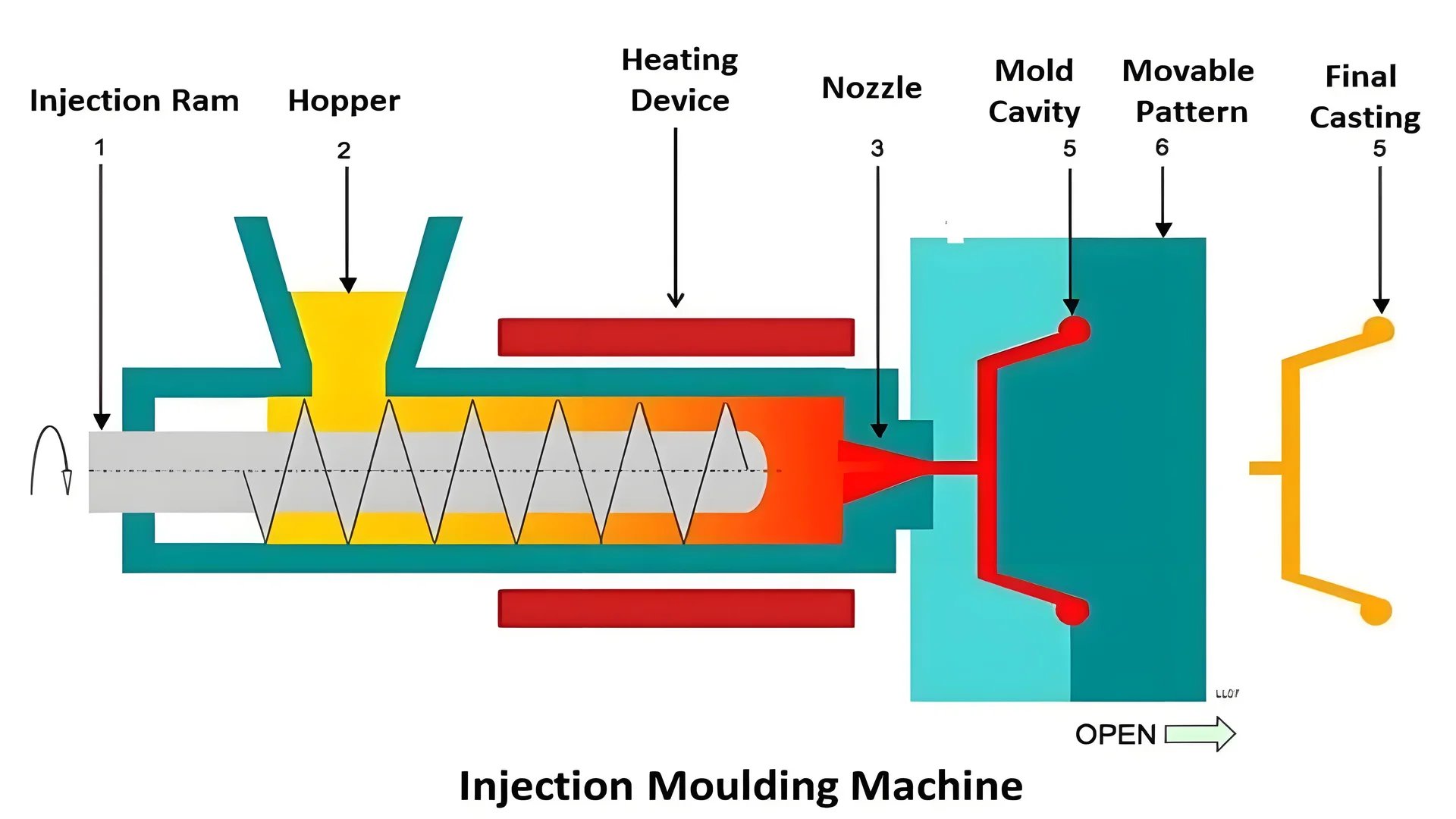
Injection Speed and Its Influence
The speed at which material is injected into the mold plays a pivotal role in determining how well the mold is filled. A higher injection speed can facilitate faster filling, which is particularly beneficial for thin-walled or intricately shaped products. However, this comes with potential downsides, such as jetting and turbulence, leading to defects like surface blemishes.
For instance, consider a complex component with thin walls. A rapid injection speed helps the melt navigate these complexities swiftly, but if the speed is too high, it might create inconsistencies in the material distribution. Therefore, the feed position should be strategically placed to accommodate these variations in speed and ensure even filling.
Managing Injection Pressure
Injection pressure directly affects the material’s ability to fill the mold completely. Too high a pressure might lead to issues like mold deformation or flash, while too low a pressure could result in short shots and shrinkage marks. It’s crucial to balance pressure with the mold design to optimize the feed position.
For large parts requiring a central feed position, increased pressure ensures complete cavity filling without undue stress on peripheral areas. On the other hand, for smaller or more delicate components, moderate pressures combined with strategically positioned feeds can prevent overpacking and ensure structural integrity.
The Critical Role of Mold Temperature
Mold temperature significantly influences the flow characteristics of the melt and ultimately the quality of the finished product. A higher temperature generally enhances melt fluidity, reducing the likelihood of surface defects but potentially extending cooling times.
In scenarios where high surface quality is paramount, maintaining elevated mold temperatures near critical surfaces ensures thorough filling and smooth finishes. Conversely, controlling mold temperature for dimensionally precise parts helps mitigate potential deviations caused by thermal expansion or contraction.
Balancing Parameters for Optimal Results
Optimization of feed position through precise control of process parameters involves an intricate balancing act. Below is a simplified table illustrating how each parameter affects feed position decisions:
Parameter | Impact on Feed Position Optimization |
---|---|
Injection Speed | Influences flow rate; higher speeds may require strategic placement to avoid defects. |
Injection Pressure | Determines fill capacity; balanced pressures prevent deformation and defects. |
Mold Temperature | Affects melt fluidity; high temperatures enhance surface quality but may delay cooling. |
By carefully adjusting these parameters, manufacturers can ensure that the feed position is optimized for both efficiency and quality in injection molding operations. This comprehensive approach not only improves product outcomes but also enhances overall production efficiency.
For further insights into optimizing process parameters in injection molding, explore this detailed guide3.
Higher injection speed reduces surface blemishes.False
Higher speeds can cause jetting and turbulence, increasing surface defects.
Mold temperature affects melt fluidity in injection molding.True
Higher mold temperatures enhance melt fluidity, improving fill quality.
What Are Common Challenges in Feed Position Optimization and How to Overcome Them?
Feed position optimization is fraught with challenges that can affect the quality and efficiency of injection molding processes. Understanding these issues is crucial to overcoming them effectively.
Challenges in feed position optimization include uneven wall thickness, complex product shapes, unsuitable gate types, and improper process parameters. Overcoming these involves careful product and mold design, strategic gate selection, and fine-tuning of injection speed and pressure to ensure balanced melt flow and minimize defects.
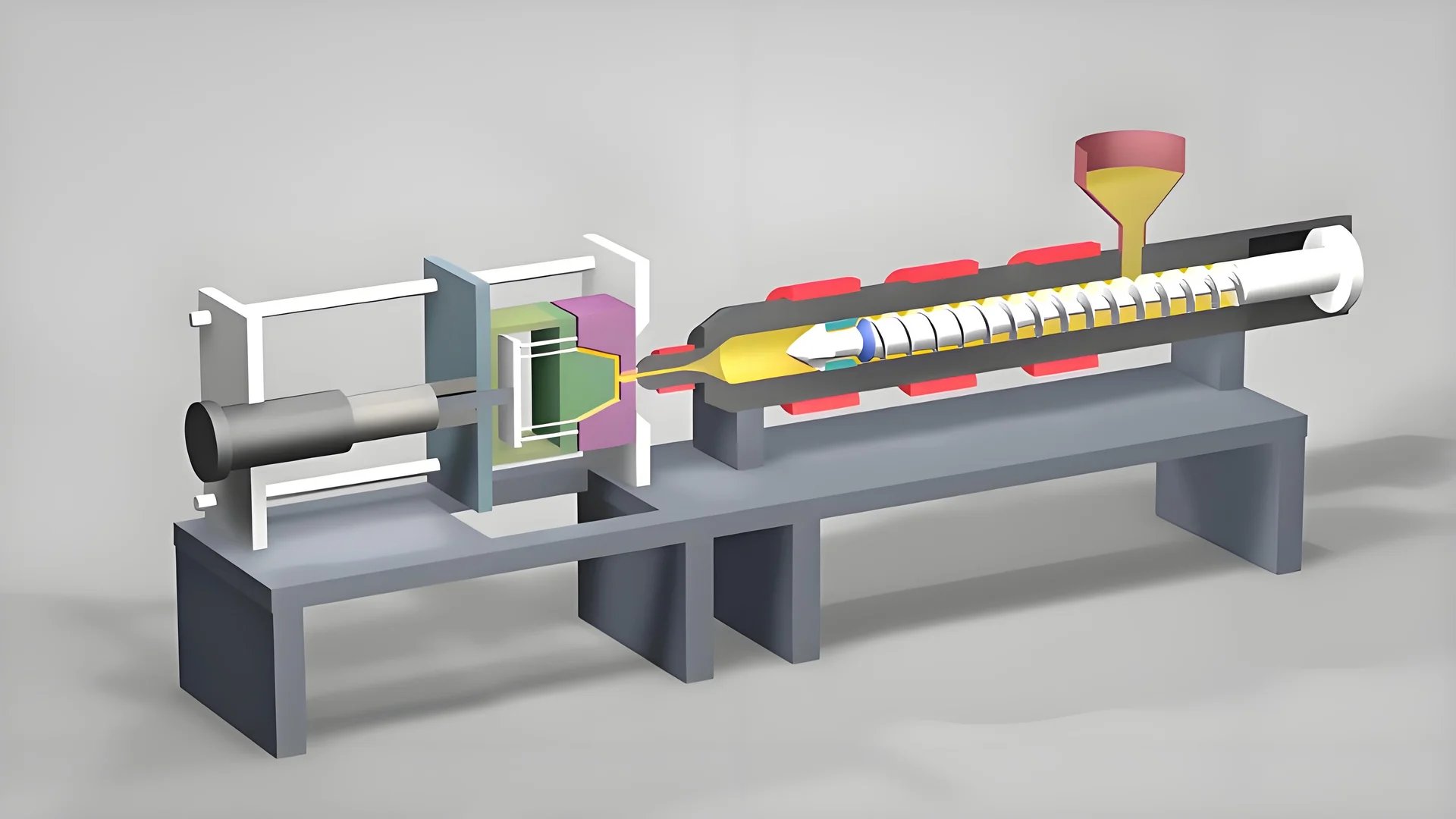
Uneven Wall Thickness: A Persistent Challenge
Uneven wall thickness can lead to unbalanced melt flow, which complicates feed position optimization. This issue often stems from inadequate wall thickness analysis4 during the product design phase. For instance, abrupt changes in wall thickness can create sink marks or voids, making it difficult to determine an effective feed position.
Solution:
To address this, ensure uniformity in wall thickness or gradually transition between different thicknesses to balance the flow resistance. This strategic approach allows for a more predictable melt flow, facilitating better feed position selection.
Complex Product Shapes
Products with intricate shapes pose another significant challenge in optimizing feed position. Features such as deep cavities or undercuts can hinder smooth melt flow if not adequately addressed during the design phase.
Solution:
Position the feed as close as possible to these complex areas. For example, in a product with a deep cavity, setting the feed near this section ensures it is filled promptly, reducing defects like short shots or pores.
Gate Type Selection
Choosing the right gate type is crucial for effective feed position optimization. Each type—side, point, or latent—has unique implications for melt flow and surface quality.
Solution:
Select a gate type that aligns with the product’s specific requirements. For instance, for products with high appearance demands, a latent gate5 positioned discreetly enhances both the aesthetic and functional aspects of the finished product.
Process Parameter Adjustments
Incorrect process parameters, such as injection speed and pressure, can lead to poor feed position performance. Fast injection speeds may cause jetting, while inadequate pressure might result in incomplete fills.
Solution:
Adjust injection speed and pressure according to the product’s design and material properties. For thin-walled or complex products, higher speeds may be appropriate, whereas thick-walled products might benefit from reduced speeds to prevent overheating.
In conclusion, overcoming challenges in feed position optimization requires a multifaceted approach. By addressing issues at each stage—product design, mold design, and process parameter adjustment—manufacturers can achieve more consistent quality and enhanced production efficiency.
Uneven wall thickness leads to sink marks.True
Uneven wall thickness can cause unbalanced melt flow, leading to defects.
Latent gates are ideal for high appearance demands.True
Latent gates enhance both the aesthetic and functional aspects of products.
Conclusion
By embracing these strategies, you’ll not only enhance your product quality but also streamline your production processes.
-
Learn how uniform wall thickness impacts melt flow in injection molding.: Proper wall thickness will reduce the risk of cosmetic defects in plastic parts. Walls in any plastic-molded part should be no less than 40 to 60 percent that … ↩
-
Discover how mold design influences feed position and overall efficiency.: Molds designed for injection molding are engineered for efficiency in various aspects of production. Firstly, they facilitate rapid cycle times, … ↩
-
Learn advanced techniques for fine-tuning process parameters effectively.: The 8 Key Parameters in Injection Molding Process Optimization to Avoid Defects · 1. Temperature Control: · 2. Injection Speed: · 3. Cooling … ↩
-
Learn how wall thickness impacts melt flow and feed position.: During product design, the significance of wall thickness is about reducing material usage while improving part quality and production speed. Reduced Raw … ↩
-
Discover why latent gates improve aesthetic and functional qualities.: It has advantages of good transmission pressure, strong … Latent gate is the most commonly used gate type for our injection molds. ↩