In the fast-paced world of injection molding, every second shaved off production time can make all the difference. I’ve learned this firsthand in my own manufacturing journey.
To optimize cycle time in injection molding, refine mold design, select appropriate materials, and utilize advanced technology to speed up production, improve quality, and reduce costs.
While these strategies set a solid groundwork, diving deeper into the nuances can yield even greater benefits. By exploring advanced techniques and gathering insights from industry experts, I’ve discovered ways to significantly boost operational efficiency. Let me share some of those insights that have truly transformed my approach to injection molding.
Refining mold design reduces injection molding cycle time.True
Improved mold design minimizes cooling and ejection times, enhancing efficiency.
Using outdated technology speeds up injection molding processes.False
Outdated technology often slows down production due to inefficiencies.
What Are the Key Components of Cycle Time?
Back when I first got into manufacturing, cycle time was like a puzzle I couldn’t crack. But understanding its parts became a game-changer.
Cycle time includes processing, inspection, wait, and move times, all crucial for production efficiency.
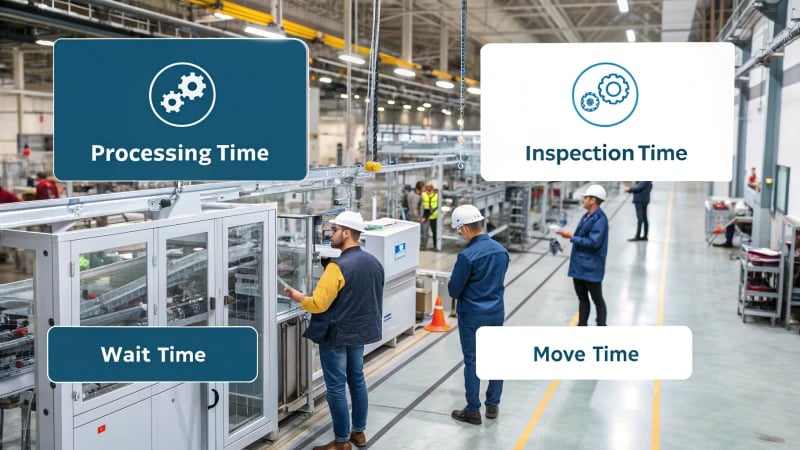
Understanding Processing Time
I’ll never forget my early days on the factory floor. Processing time was a term tossed around a lot, but it took seeing a machine setup firsthand to grasp it. It’s not just the machines whirring away; it’s also about preparing them—like adjusting an old bike before the ride.
- Setup Time: This is like setting the stage before the show begins—preparing equipment to get everything just right.
- Run Time: The main act, where the magic happens as the product gets transformed.
I found that by streamlining setup procedures1 and investing in efficient machinery, we could shave precious minutes off each cycle.
Analyzing Inspection Time
I used to dread inspection time, fearing it would slow things down. But skipping this step can mean disaster later on. Inspection ensures only top-quality products make it to customers’ hands.
- Visual Inspection: It’s like giving your car a once-over before a road trip.
- Automated Testing: Think of it as having a tech-savvy friend double-check everything for you.
By introducing automated systems2, we improved accuracy and speed, making our processes smoother.
Evaluating Wait Time
Wait time is sneaky. It’s those moments when products just sit there, doing nothing—like waiting in line at your favorite coffee shop. Causes range from machine hiccups to labor shortages.
I learned that optimizing workflow scheduling3 and keeping inventory levels just right could cut down on these frustrating pauses.
Assessing Move Time
Move time was something I hadn’t considered until I saw the chaos of transporting materials between stations. It’s like moving furniture around your house; every extra step is wasted effort.
- Intra-process Transport: Moving items within one room.
- Inter-process Transport: Carrying goods through different parts of the house.
We found that rethinking our plant layout significantly reduced transportation delays4, making everything run more smoothly.
Here’s a summary of the components:
Component | Description |
---|---|
Processing | Actual operation time on the product |
Inspection | Quality checks for defects |
Wait | Idle periods between operations |
Move | Transportation of materials/products |
Understanding these elements became crucial in my journey toward efficiency, helping me—and many others—boost productivity in manufacturing.
Processing time includes setup and run time.True
Processing time involves both the preparation (setup) and actual operation (run).
Inspection time is only manual checks for defects.False
Inspection time includes both manual checks and automated testing.
How Does Mold Design Influence Cycle Time?
Ever wondered how the tiny details in mold design can make a massive difference in production speed?
Mold design impacts cycle time by optimizing heat dissipation, material flow, and cooling efficiency, which enhances production efficiency and reduces costs.
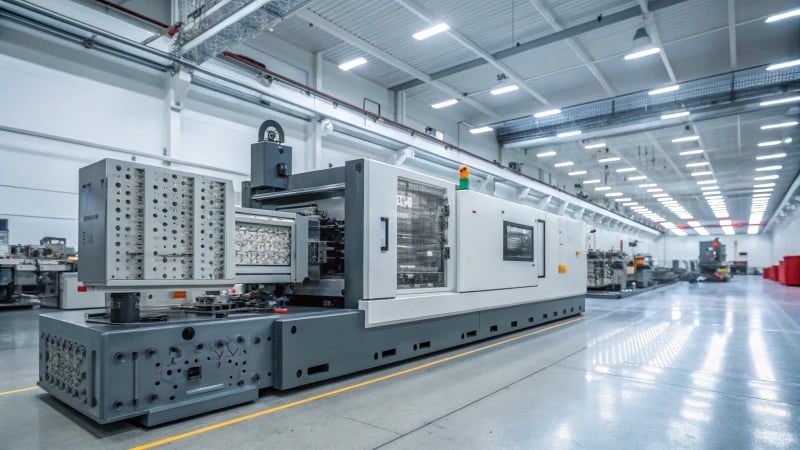
The Role of Heat Dissipation
I remember the first time I realized how crucial heat dissipation was in mold design. It was during a project where we were trying to cut down on cycle times, and the material just wasn’t cooling fast enough. Efficient heat dissipation ensures the mold cools down quickly, which is vital for reducing cycle time. The materials we choose for our molds can make or break this process because some conduct heat better than others. Understanding thermal conductivity5 was a game changer for me.
Importance of Material Flow
Smooth material flow might sound straightforward, but I learned its importance the hard way. On one project, poor flow led to defects and uneven cooling, increasing our cycle times dramatically. Optimizing gate locations and runner systems became essential to ensure that material flows smoothly, filling the mold cavity completely without issues like air pockets or uneven pressure.
Factor | Impact on Cycle Time |
---|---|
Gate Design | Affects fill speed |
Runner System | Influences pressure |
Cooling Efficiency Considerations
Cooling was always a major part of our cycle time struggles. I remember brainstorming with my team on how to design cooling channels more effectively. They need to be strategically placed to ensure uniform cooling across the entire mold cavity. The design of these cooling channels6 directly impacts how quickly we can reuse a mold after a cycle.
Advanced Mold Design Techniques
Discovering advanced techniques like conformal cooling felt like unlocking a new level in a video game. By using 3D-printed molds, we could create custom cooling channels tailored to the part’s shape, allowing for faster and more uniform cooling. It’s innovations like these that offer a competitive edge in mold design and production efficiency.
Collaborative Design Approaches
Collaborative approaches have been my go-to strategy for enhancing mold efficiency. I value the feedback from the production floor; it has often led to necessary adjustments in mold design that optimize for faster cycle times. Leveraging collaboration tools7 facilitates this process, enabling real-time updates and communication between teams.
Heat dissipation reduces mold cycle time.True
Efficient heat dissipation allows molds to cool quickly, reducing cycle time.
Smooth material flow increases cycle time.False
Smooth material flow reduces cycle time by preventing defects and uneven cooling.
What Materials Can Speed Up Cycle Times?
Have you ever wondered which materials can give your production process that extra speed boost?
Materials with high thermal conductivity and low heat capacity, like aluminum, beryllium copper, and certain engineered plastics, can significantly reduce cycle times in production.
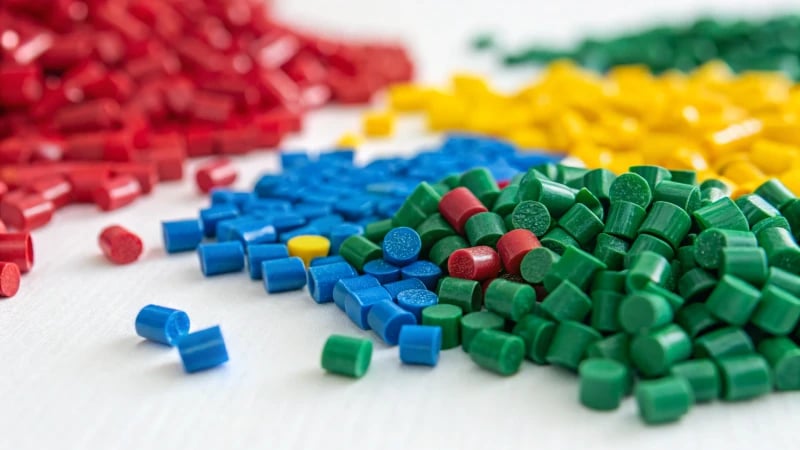
Understanding Material Properties and Their Impact
As a designer, I’ve learned firsthand how critical the choice of materials is in reducing cycle times. Materials that quickly heat up and cool down can really make a difference in keeping production lines humming. Take aluminum, for instance. Its exceptional thermal conductivity allows for rapid temperature changes, making it a favorite in our industry. It’s lightweight, too, which I find especially handy when designing molds.
Materials that facilitate rapid heating and cooling accelerate production8.
Metals Leading the Charge
In my experience, when it comes to metals, aluminum and beryllium copper are the go-to options. Aluminum’s ability to distribute heat evenly is unmatched, and it’s been my trusty companion in countless projects. Beryllium copper, on the other hand, combines strength with superior thermal performance, which is a rare find.
Here’s a comparison to give you a better idea:
Material | Thermal Conductivity | Strength |
---|---|---|
Aluminum | High | Moderate |
Beryllium Copper | Very High | High |
Exploring Engineered Plastics
But what if metals aren’t the right fit? That’s where engineered plastics come into play. These materials are engineered to withstand high temperatures without compromising their structural integrity. One that’s caught my attention is Polyetheretherketone (PEEK). This innovative plastic is not just resilient; it’s also incredibly efficient in applications where metals might fall short.
Polyetheretherketone (PEEK) is one such innovative plastic9 known for its resilience and efficiency.
Impact on Product Performance
Reducing cycle times isn’t just about cranking out more units; it’s also about enhancing product performance. In my work with consumer electronics, I’ve seen how the right material choices lead to quicker assembly lines and more consistent quality control.
Understanding how material properties correlate with product longevity has been essential in ensuring that my designs stand the test of time.
This is where understanding the correlation between material properties10 and product longevity becomes crucial for designers like Jacky.
Exploring these material options has had a profound impact on my work, leading to more efficient and cost-effective production cycles. Whether it’s through metals or plastics, finding that perfect balance has been a rewarding challenge.
Aluminum has high thermal conductivity.True
Aluminum's excellent thermal conductivity aids in rapid heating and cooling.
Beryllium copper is weaker than aluminum.False
Beryllium copper has high strength, surpassing aluminum's moderate strength.
How Can Automation Help Reduce Cycle Time?
Ever wondered how automation could be the secret sauce to speed up production and make life easier?
Automation reduces cycle time by streamlining processes, minimizing errors, and optimizing resource use, leading to increased production speed through the adoption of robotic systems and smart technology.
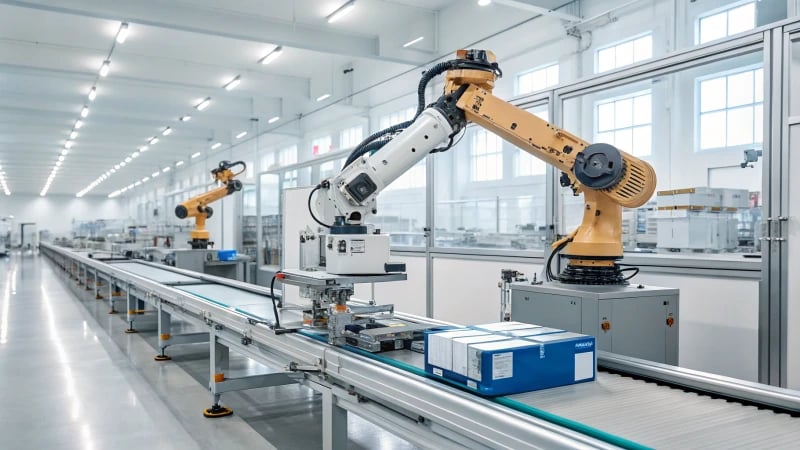
Understanding Cycle Time and Its Impact
I’ve always found it fascinating how cycle time shapes the manufacturing landscape. It’s like a stopwatch starting the moment we sketch that first design11 and only stopping once the final product is shipped out the door. The beauty of reducing cycle time is that it doesn’t just save money; it boosts production rates and keeps our customers smiling.
How Automation Achieves Cycle Time Reduction
I remember my first experience with robotic arms on the production line. Watching them work non-stop without needing a coffee break was eye-opening. Their precision eliminates the unpredictability that can come with human workers, ensuring that our operations hum along smoothly, day or night.
Benefits of Automation | Impact on Cycle Time |
---|---|
Consistent Quality | Fewer delays |
Reduced Manual Errors | Faster completion times |
Real-time Data Monitoring | Quick adjustments |
Examples of Automation in Manufacturing
Take Robotic Process Automation (RPA), for instance. I’ve seen firsthand how it transforms assembly lines12, taking over repetitive tasks that used to drain human energy. In the automotive world, robots are the unsung heroes of welding and painting, outperforming even the most skilled humans.
Smart Technologies and Their Role
The advent of the Internet of Things (IoT) has been like getting an upgrade to our factory’s brainpower. Machines talking to each other in real-time means we can catch issues before they snowball into something major. For example, predictive maintenance13 is a game-changer, allowing us to foresee equipment hiccups before they turn into full-blown breakdowns, slashing potential downtime.
Challenges in Implementing Automation
But let’s not sugarcoat it—diving into automation isn’t without its hurdles. I had to grapple with the initial costs and the challenge of shifting workforce dynamics. Training employees to handle these advanced systems wasn’t easy, but it was a necessary step. Integrating cutting-edge tech into our tried-and-true processes felt like a puzzle sometimes. Yet, overcoming these challenges means unlocking automation’s full potential to slash cycle times and supercharge productivity and competitiveness14.
Automation reduces cycle time in manufacturing.True
Automation enhances efficiency by minimizing human error and optimizing processes.
Human workers are more efficient than robots in assembly lines.False
Robots perform repetitive tasks tirelessly, increasing consistency and speed.
How Does Maintenance Affect Cycle Time Optimization?
Ever thought of maintenance as a key player in boosting your cycle times? It’s more than just fixing stuff—it’s about creating a seamless production rhythm.
Effective maintenance reduces downtime, optimizes cycle times, and enhances production efficiency by ensuring machines remain in optimal condition, minimizing delays and improving consistency.
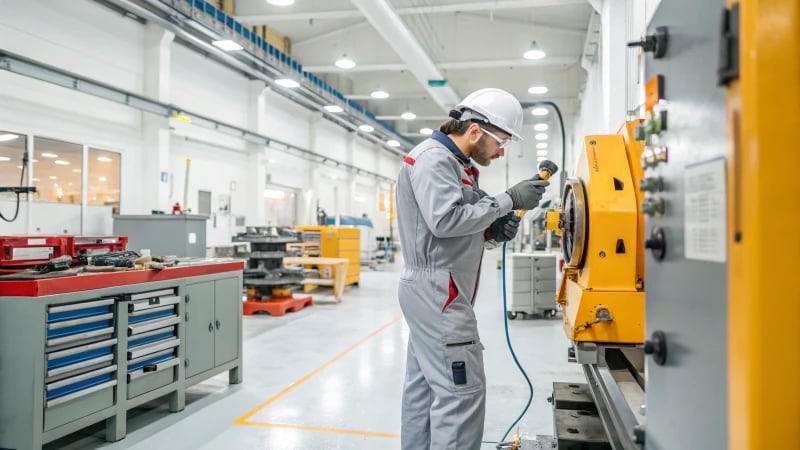
The Role of Preventive Maintenance
Preventive maintenance involves regular, planned interventions to keep machinery in optimal condition. This proactive approach helps avoid unexpected breakdowns and unscheduled downtime. For mold designers15, ensuring molds are clean and lubricated can prevent costly interruptions.
Maintenance Task | Frequency | Impact on Cycle Time |
---|---|---|
Lubrication | Weekly | Reduces friction, ensuring smooth operation |
Calibration | Monthly | Enhances precision, reducing defects |
I remember the first time I truly grasped the power of preventive maintenance. It was during a project where we were under tight deadlines, and the last thing we needed was unscheduled downtime. I learned that preventive maintenance, with its regular check-ups and interventions, is like a health plan for machinery—keeping everything in peak condition so we don’t hit any nasty surprises.
Predictive Maintenance: The Data-Driven Approach
Predictive maintenance leverages data analytics to foresee potential issues before they lead to failures. Sensors and IoT devices monitor equipment health, providing insights into wear and tear. This method allows for targeted interventions, reducing unnecessary maintenance tasks and optimizing resource allocation.
Then there’s predictive maintenance, which feels like something out of a sci-fi movie with its data analytics and sensor technology. I recall a time when sensors detected unusual vibrations in our equipment, signaling potential issues long before they escalated. Thanks to these insights, we could tackle problems proactively, ensuring our production line ran smoothly without any hiccups.
For example, sensor technology16 can detect vibrations indicating potential issues, allowing for timely maintenance before problems arise.
Reactive Maintenance: Handling the Unexpected
While not ideal for cycle time optimization, reactive maintenance is essential for addressing unforeseen breakdowns. Quick response teams can minimize the impact on production schedules. However, relying solely on reactive measures can lead to increased downtime and inefficiencies.
Of course, we can’t always predict every glitch. That’s where reactive maintenance steps in. While it’s not ideal to rely on it exclusively for cycle time optimization, having a swift response team ready to leap into action is crucial. I’ve been there—when unexpected breakdowns happen, the ability to respond quickly can save the day and keep production schedules on track.
Incorporating a balanced strategy that combines preventive, predictive, and reactive maintenance is crucial for optimizing cycle times. This holistic approach ensures machines are always in top condition, minimizing delays and maximizing throughput.
Curious about how different strategies can mesh together? Dive into more maintenance management strategies17 to discover ways to integrate these approaches effectively.
Preventive maintenance reduces unscheduled downtime.True
Preventive maintenance involves planned interventions, preventing unexpected breakdowns.
Reactive maintenance is best for cycle time optimization.False
Reactive maintenance addresses unforeseen issues, often increasing downtime.
Conclusion
Optimize injection molding cycle time by refining mold design, selecting suitable materials, and leveraging automation to enhance efficiency, reduce costs, and improve product quality.
-
Streamlining setup procedures can significantly reduce processing time, improving overall cycle efficiency. ↩
-
Automated systems speed up inspection processes while maintaining accuracy, thus reducing cycle time. ↩
-
Efficient workflow scheduling minimizes wait times, enhancing production line efficiency. ↩
-
Optimized plant layouts reduce move times by minimizing transportation distances. ↩
-
Explores how different mold materials affect heat dissipation, impacting cycle times. ↩
-
Shows how strategic cooling channel placement can reduce cycle times by enhancing cooling efficiency. ↩
-
Highlights tools that improve communication between design and production teams, optimizing mold designs. ↩
-
This link explores materials specifically designed to enhance production efficiency, offering practical insights for optimizing manufacturing processes. ↩
-
Discover the unique attributes of PEEK plastic, which make it a preferred choice for high-temperature applications, enhancing design flexibility and efficiency. ↩
-
Understanding this correlation helps designers like Jacky select materials that improve both production speed and product lifespan. ↩
-
Explore how automating initial design processes can streamline production timelines and enhance efficiency. ↩
-
Learn how RPA transforms assembly lines by increasing speed and reducing errors. ↩
-
Discover how predictive maintenance prevents equipment failures and minimizes downtime. ↩
-
Understand how automation boosts competitiveness by reducing costs and increasing production speed. ↩
-
Discover why mold maintenance is crucial for minimizing production disruptions and maintaining quality. ↩
-
Learn how sensors can predict machinery failures, helping reduce unexpected downtimes. ↩
-
Gain insights into effective maintenance strategies that enhance operational efficiency. ↩