Injection molding is at the heart of modern manufacturing, but getting the cooling rate just right can feel like a daunting challenge.
To optimize the cooling rate in injection molding, focus on designing efficient cooling systems, selecting appropriate cooling mediums, and adjusting process parameters. These strategies enhance product quality and efficiency by ensuring uniform and rapid cooling, reducing cycle times and defects.
While understanding the basics is essential, delving deeper into specific methods and technologies can significantly improve your injection molding processes. Explore advanced techniques and expert insights in the sections below to truly master cooling optimization.
Conformal cooling reduces cycle times in injection molding.True
Conformal cooling channels enhance uniform heat removal, cutting cycle times.
How Does Cooling System Design Affect Molding Efficiency?
An efficient cooling system is pivotal in injection molding, directly impacting cycle times and product quality.
Cooling system design is crucial for molding efficiency as it affects cooling rate, uniformity, and cycle time. Optimizing the water channel layout, selecting suitable cooling mediums, and using advanced technologies like conformal cooling can enhance production efficiency and product quality.
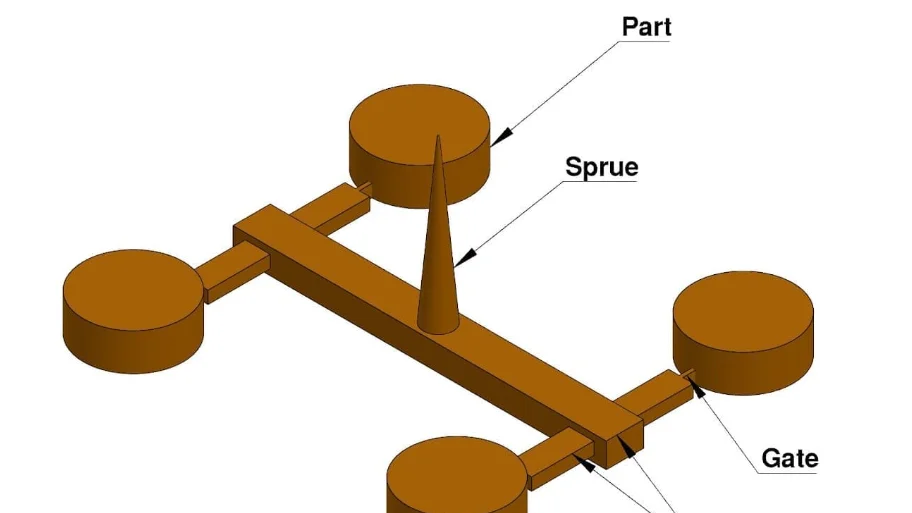
The Role of Cooling System Design in Injection Molding
In injection molding, the design of the cooling system significantly influences molding efficiency1. A well-optimized cooling system ensures that the mold cools rapidly and uniformly, reducing cycle times and improving product consistency. Let’s explore key elements of effective cooling system design:
Optimizing Cooling Channels
A critical aspect of cooling system design is the layout of the cooling water channels. These channels should be positioned as close as possible to the mold cavity surface, allowing for rapid heat removal. The diameter and number of channels should be tailored to the mold size and product requirements, ensuring that the coolant flows evenly throughout the mold.
Selecting Suitable Cooling Mediums
The choice of cooling medium—whether water, oil, or air—affects the heat transfer rate. For instance, water is often preferred due to its high thermal conductivity and capacity to be controlled at various temperatures and flow rates. However, selecting the right medium also depends on the plastic material used and specific product requirements.
Implementing Advanced Cooling Technologies
Incorporating advanced technologies such as conformal cooling can revolutionize cooling efficiency2. Conformal cooling channels, created using 3D printing technologies, are designed to follow the shape of the mold cavity more closely than traditional methods. This results in more uniform cooling and reduced cycle times.
Cooling System Design Aspects | Impact on Efficiency |
---|---|
Channel Layout | Uniform cooling |
Medium Selection | Rapid heat removal |
Advanced Technologies | Shorter cycle times |
Balancing Efficiency with Product Quality
While optimizing for speed, it’s crucial to maintain a balance between efficiency and product quality. Overly aggressive cooling can lead to defects such as warping or stress marks. Thus, continuous monitoring and adjustments are essential to maintain optimal performance.
The integration of these strategies can significantly enhance the efficiency of injection molding processes, leading to better quality products and lower production costs. By focusing on these elements, manufacturers can achieve a competitive edge in a fast-evolving market.
Conformal cooling reduces cycle times in molding.True
Conformal cooling channels follow the mold shape, enhancing heat removal.
Oil is the most efficient cooling medium for injection molding.False
Water is preferred due to its high thermal conductivity and control.
What Role Does Cooling Medium Selection Play in Optimization?
Choosing the right cooling medium can drastically impact injection molding efficiency and product quality.
The selection of a suitable cooling medium is vital for optimizing the cooling process in injection molding. It influences heat transfer rates, cycle times, and ultimately, the quality of the molded product. Different mediums like water, oil, or air offer distinct advantages, which must align with the material and design requirements.
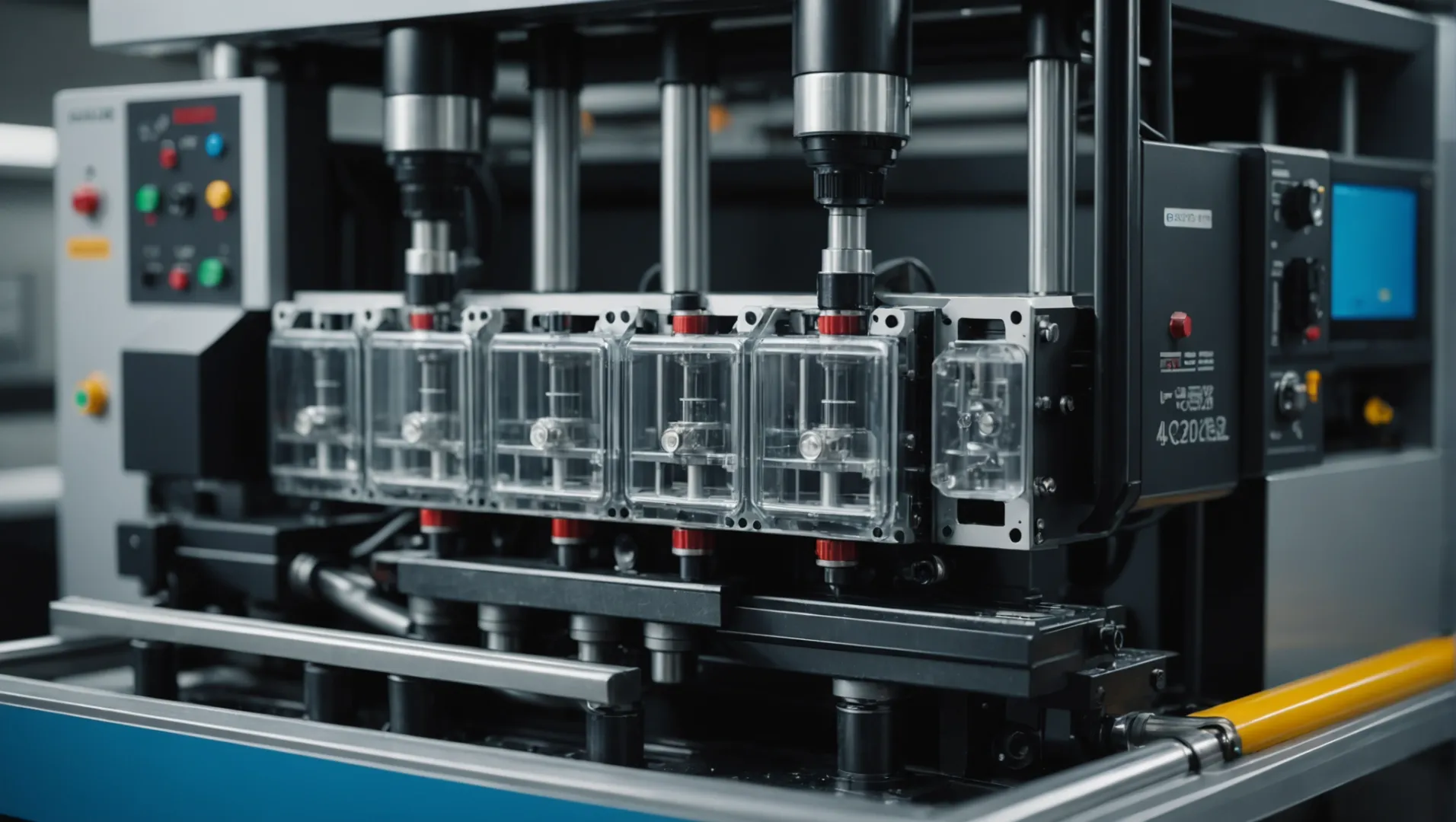
Understanding Different Cooling Mediums
Choosing a cooling medium involves considering the thermal properties of materials, production needs, and environmental conditions. Here’s how different mediums stack up:
- Water: Commonly used due to its high heat transfer capacity and availability. Water’s effectiveness makes it ideal for rapid cooling cycles, though its temperature must be carefully managed to avoid product defects.
- Oil: Offers controlled cooling for high-temperature polymers. Though slower than water, oil is beneficial when thermal stability and precise temperature control are required.
- Air: Useful for low-speed cooling and where water contamination is a concern. Its lower heat transfer capability means longer cycle times, but it provides excellent control over surface aesthetics.
Factors Influencing Medium Selection
Material Compatibility: The plastic’s thermal characteristics should guide medium choice. For instance, materials with high melting points might necessitate oil or advanced water systems to ensure efficient cooling without warping or cracking.
Product Requirements: The intended use and durability of the product influence medium selection. Products needing stringent quality controls may benefit from oil or mixed mediums to maintain uniform cooling.
Cost and Environmental Considerations: Water is generally more cost-effective but poses environmental concerns due to potential waste and contamination. Balancing cost with sustainability often guides the choice between simple water systems and more complex setups using oil or air.
Advanced Cooling Strategies
To further enhance cooling efficiency, technologies such as conformal cooling and 3D printed molds enable precise medium distribution tailored to specific designs. These techniques offer improved uniformity and reduced cycle times by optimizing how the medium interacts with the mold surface.
Explore how these strategies integrate with modern practices in our section on advanced technologies3. This exploration can provide insights into balancing cost, efficiency, and quality for optimal cooling solutions.
Water is the fastest cooling medium in injection molding.True
Water's high heat transfer capacity allows for rapid cooling cycles.
Oil cooling is faster than water cooling in all cases.False
Oil provides controlled, slower cooling, suitable for high-temperature polymers.
Why Are Process Parameter Adjustments Crucial for Quality?
In the intricate world of injection molding, fine-tuning process parameters is vital for achieving top-notch product quality.
Adjusting process parameters in injection molding is crucial because it directly affects cooling rates, product integrity, and efficiency. Key adjustments include material and mold temperatures, holding time and pressure, all of which minimize defects like shrinkage and warping, ensuring superior quality outcomes.

The Impact of Material Temperature
Material temperature in injection molding significantly influences the cooling phase. By lowering the barrel temperature, heat accumulation is reduced, speeding up cooling. However, balancing is crucial to prevent material degradation. Lowering the material temperature can also lead to more consistent part dimensions and surface finish.
Mold Temperature Considerations
Lowering mold temperature enhances cooling efficiency, but too low a temperature may result in defects such as warping or residual stresses. It is crucial to find a balance that maintains product integrity while maximizing cooling speed. Incorporating advanced mold materials with high thermal conductivity can further optimize temperature management.
Adjusting Holding Time and Pressure
Holding time and pressure are pivotal in determining the final shape and mechanical properties of molded parts. Extending the holding time allows for more plastic material to fill cavities completely, reducing shrinkage. Simultaneously, increasing holding pressure helps maintain dimensional stability.
Choosing Suitable Plastic Materials
Different plastics exhibit unique thermal behaviors. Opting for materials with high thermal conductivity or lower specific heat capacity can drastically improve cooling rates. For example, using plastics like polycarbonate might be beneficial when rapid cooling is necessary, although each application demands a specific assessment.
The Role of Advanced Cooling Technologies
Implementing technologies such as conformal cooling4 channels designed via 3D printing can offer uniform cooling by matching complex part geometries. This approach reduces cycle times and enhances product consistency by preventing localized overheating or undercooling.
Monitoring and Continuous Adjustment
Finally, constant monitoring and adjustments based on real-time feedback can lead to optimal results. Leveraging IoT-enabled sensors5 to track temperature and pressure variations can provide valuable insights for ongoing process improvements.
Lower mold temperatures reduce warping.False
While lower temperatures enhance cooling, they can increase warping risk.
IoT sensors optimize injection molding adjustments.True
IoT sensors provide real-time data for precise process adjustments.
How Can Advanced Technologies Enhance Cooling Performance?
In an era of rapid technological advancements, cooling systems in injection molding are seeing transformative improvements.
Advanced technologies such as conformal cooling and 3D printing optimize cooling performance by customizing cooling circuits for enhanced efficiency and uniformity, significantly reducing cycle times and improving product quality.
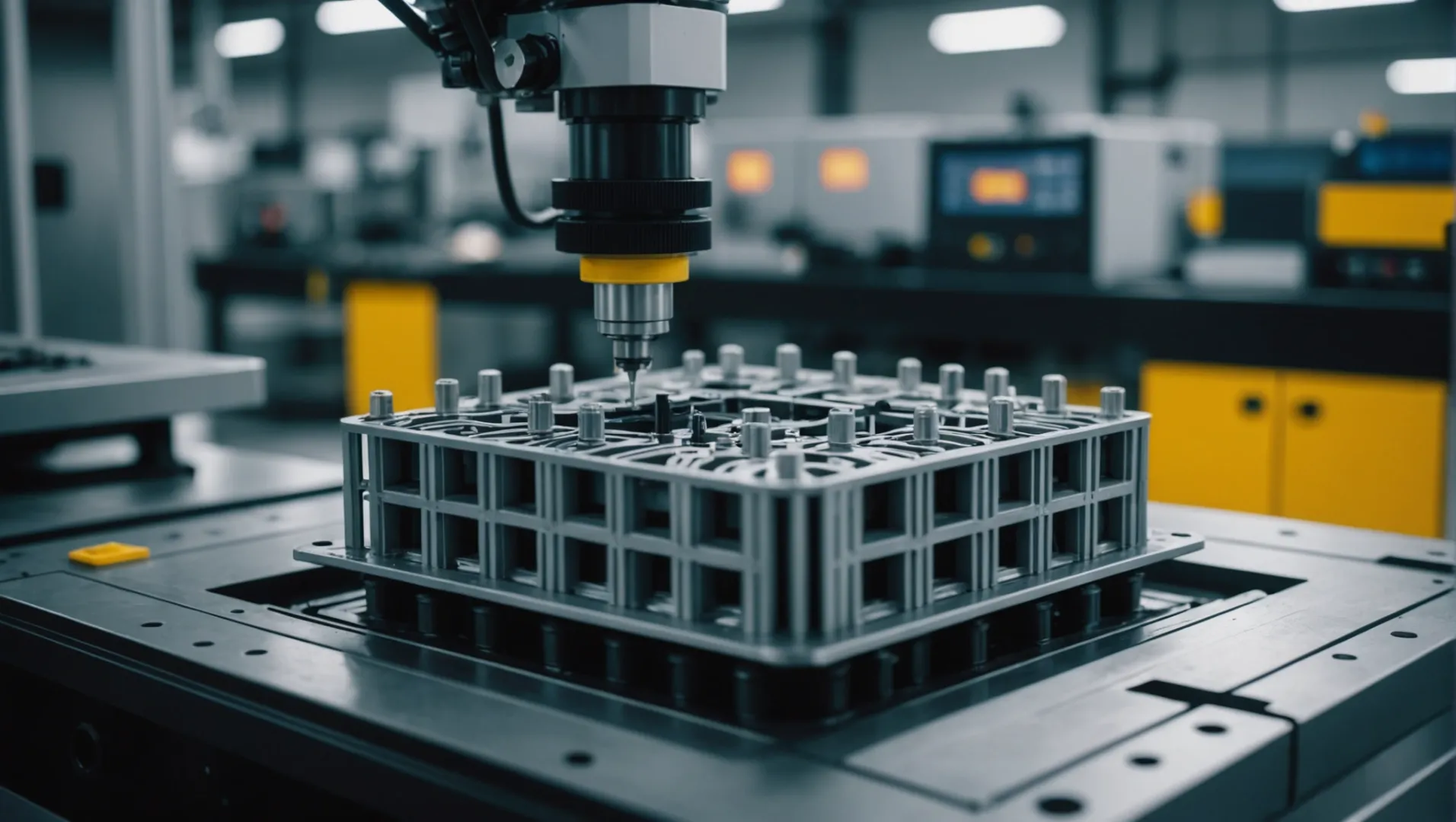
Embracing Conformal Cooling Technology
Conformal cooling involves designing cooling channels that closely follow the contours of the mold. Unlike traditional straight-line channels, these customized pathways ensure more efficient heat extraction from the molded part. This leads to quicker cycle times and reduced energy consumption.
Conformal cooling is often achieved through 3D printing techniques6, allowing intricate designs that traditional machining cannot produce. This technology enhances cooling performance by improving the uniformity and speed of heat dissipation, leading to superior product quality and reduced production costs.
Leveraging 3D Printing for Cooling Optimization
The integration of 3D printing in mold design allows for more complex geometries in cooling channels, which can be tailored to specific product requirements. By using this approach, manufacturers can achieve optimal heat distribution, minimizing hotspots and warping in the final product.
For instance, a mold designed with 3D-printed conformal cooling channels7 may require less maintenance and offer longer service life due to uniform cooling stress distribution. This innovation not only enhances cooling performance but also supports sustainable manufacturing practices by reducing waste and energy usage.
Exploring Other Technological Advances
Apart from conformal cooling and 3D printing, other advanced technologies like temperature control units equipped with real-time monitoring systems are making significant strides in optimizing cooling performance. These systems can dynamically adjust the cooling medium’s temperature and flow rate, adapting to changes in production conditions to maintain optimal cooling efficiency.
Additionally, the use of simulation software to model the thermal behavior of molds before production helps identify potential inefficiencies in the design phase. This proactive approach enables precise adjustments to be made, ensuring that the final product meets quality standards with minimal trial and error.
Incorporating these advanced technologies requires a comprehensive understanding of their capabilities and limitations. However, when applied effectively, they offer transformative benefits in terms of efficiency, quality, and cost-effectiveness.
Conformal cooling reduces cycle times.True
Conformal cooling enhances heat extraction efficiency, leading to quicker cycles.
3D printing hinders cooling channel customization.False
3D printing enables complex, customized cooling channel designs for better efficiency.
Conclusion
Effective cooling rate optimization is key to superior injection molding performance. By applying these strategies, you can enhance quality, efficiency, and cost-effectiveness.
-
Discover how cooling system design impacts efficiency and product quality.: An improper injection mold cooling process, then, will almost always result in part defects that require rework or discard. The cooling process … ↩
-
Learn about the advantages of using conformal cooling in molding.: With conformal cooling, you can achieve higher quality molded parts with fewer weld lines, reduced surface roughness, less warpage, and most … ↩
-
Discover how cutting-edge technologies optimize cooling efficiency and product quality.: The most representative ones are: pulse cooling technology, CO2 gas cooling technology and nano fluid cooling technology. This article will … ↩
-
Explore how conformal cooling enhances efficiency and quality in injection molding.: With conformal cooling, you can achieve higher quality molded parts with fewer weld lines, reduced surface roughness, less warpage, and most … ↩
-
Discover how IoT sensors improve monitoring and adjustments in molding processes.: The IoT utilizes sensors for data collection and networks for data transportation. Standalone equipment inhibits the collective knowledge of the … ↩
-
Discover how 3D printing enhances conformal cooling channel design efficiency.: Improved Cycle Time. Reduced injection molding cycle time by up to 70% · Better Part Quality. Reduced warpage; Reduced scrapped parts; Reduced surface roughness … ↩
-
Learn about the advantages of 3D-printed conformal cooling in molds.: Such cooling channels are designed to closely follow the contours of the product, enabling rapid and uniform cooling inside the mold. 3d cooling channel design … ↩