In the world of injection molding, precision is king. For me, every detail matters when it comes to ensuring high-quality production. Let’s delve into how we can refine clamping accuracy together.
To optimize clamping accuracy in injection molds, focus on precise mold design, high-precision manufacturing processes, correct machine operation, and regular maintenance. These steps ensure consistent part dimensions and prevent defects like flash, enhancing overall production quality.
While this overview provides a quick solution, understanding the detailed methodologies behind each step is essential for achieving optimal results. Dive deeper into the intricacies of mold design, manufacturing techniques, and operational strategies to truly master clamping accuracy.
Flat parting surfaces improve clamping accuracy.True
Smooth, flat surfaces ensure proper sealing and reduce defects.
What Role Does Mold Design Play in Clamping Accuracy?
Mold design is the backbone of clamping accuracy in injection molding, affecting everything from precision to product quality.
Mold design directly impacts clamping accuracy by ensuring precise alignment and structural integrity. Key elements include flat parting surfaces, accurate size calculations, and effective guide mechanisms. These factors help maintain consistent clamping force and reduce defects.

Importance of a Flat Parting Surface
A flat and smooth parting surface is critical for maintaining clamping accuracy. Any irregularities can lead to improper sealing, resulting in defects such as flash. To achieve this, high-precision processing equipment is essential. Utilizing CNC machines ensures that the parting surfaces meet stringent flatness and roughness requirements.
Designing Guide Mechanisms
Guide mechanisms, such as guide pins and sleeves, are instrumental in maintaining the mold’s movement accuracy during opening and closing. These components must be designed with high matching precision. A well-calibrated guide system minimizes deviations and ensures that each cycle repeats with the same clamping accuracy. Moreover, choosing the right materials for these components can further enhance their longevity and effectiveness.
Accurate Size Calculations
Accurate dimensional calculations during the mold design phase are paramount. This includes considering material shrinkage rates and thermal expansion, which can affect the final product dimensions. By employing CAD1 and CAE2 software for simulation analysis, designers can optimize mold structures and sizes. This approach helps ensure that molds meet the desired clamping accuracy post-assembly.
Integrating Modern Technologies
The integration of modern technologies like 3D modeling and simulation tools has revolutionized mold design. These technologies allow for detailed analysis of potential issues before physical mold creation, reducing time and cost associated with trial-and-error methods. Additionally, real-time data collection during the design phase can provide insights into improving clamping accuracy.
Incorporating these elements into mold design not only improves clamping accuracy but also enhances the overall quality of the finished products. Understanding these intricate details allows manufacturers to optimize their processes for better efficiency and product reliability.
Flat parting surfaces are crucial for clamping accuracy.True
Flat surfaces prevent defects like flash by ensuring proper sealing.
Guide mechanisms have no impact on mold movement accuracy.False
Guide mechanisms ensure precise mold movement, affecting accuracy.
How Can Manufacturing Techniques Enhance Clamping Precision?
Precision in manufacturing techniques is pivotal for enhancing the clamping precision of injection molds, impacting both product quality and efficiency.
To enhance clamping precision, employ high-precision processing equipment, implement strict quality control, and ensure meticulous assembly. These techniques minimize deviations and improve accuracy, crucial for maintaining the integrity of injection molds.

High-Precision Processing Equipment
Advanced technology plays a crucial role in refining manufacturing processes. Utilizing CNC machining centers, EDM machines, and precision grinding tools allows manufacturers to achieve tight tolerances and superior surface finishes. These tools ensure that each component meets stringent specifications, thereby enhancing clamping precision.
For instance, CNC machining can maintain dimensional accuracy by cutting parts to exact specifications. When combined with EDM machines, which are excellent for intricate details and hard-to-machine materials, the precision level is significantly heightened.
Strict Quality Control Measures
Implementing rigorous quality control is essential in maintaining high clamping precision. By establishing a comprehensive inspection system, manufacturers can verify dimensions, shapes, and surface qualities. Using precision measuring instruments like three-coordinate measuring machines ensures adherence to design standards.
Quality control doesn’t stop at measurement; it extends to testing assembled molds. Regular testing identifies potential clamping issues early, allowing for timely corrections.
Meticulous Mold Assembly
The assembly process is as critical as the manufacturing itself. Ensuring that all components are installed correctly involves following precise assembly protocols. This not only guarantees that each part fits perfectly but also maintains the overall clamping accuracy of the mold.
During assembly, utilizing guide mechanisms such as guide pins and sleeves can reduce deviation during the mold’s operation. The careful alignment and fitting of these components are vital for seamless mold functionality.
Through these meticulous manufacturing techniques, clamping precision3 in injection molds can be significantly enhanced, ensuring high-quality output and operational efficiency.
CNC machining ensures dimensional accuracy in molds.True
CNC machines cut parts to exact specifications, enhancing precision.
Ignoring assembly protocols improves mold clamping precision.False
Proper assembly is crucial for ensuring clamping accuracy in molds.
Why Is Proper Operation Essential for Maintaining Accuracy?
In injection molding, proper machine operation is pivotal in ensuring consistent accuracy and high-quality output. Missteps in operation can lead to decreased precision, affecting both the mold and the final product.
Proper operation in injection molding maintains accuracy by ensuring correct parameter settings, smooth mold handling, and adherence to guidelines. This prevents defects and maintains the clamping force needed for high-quality production.
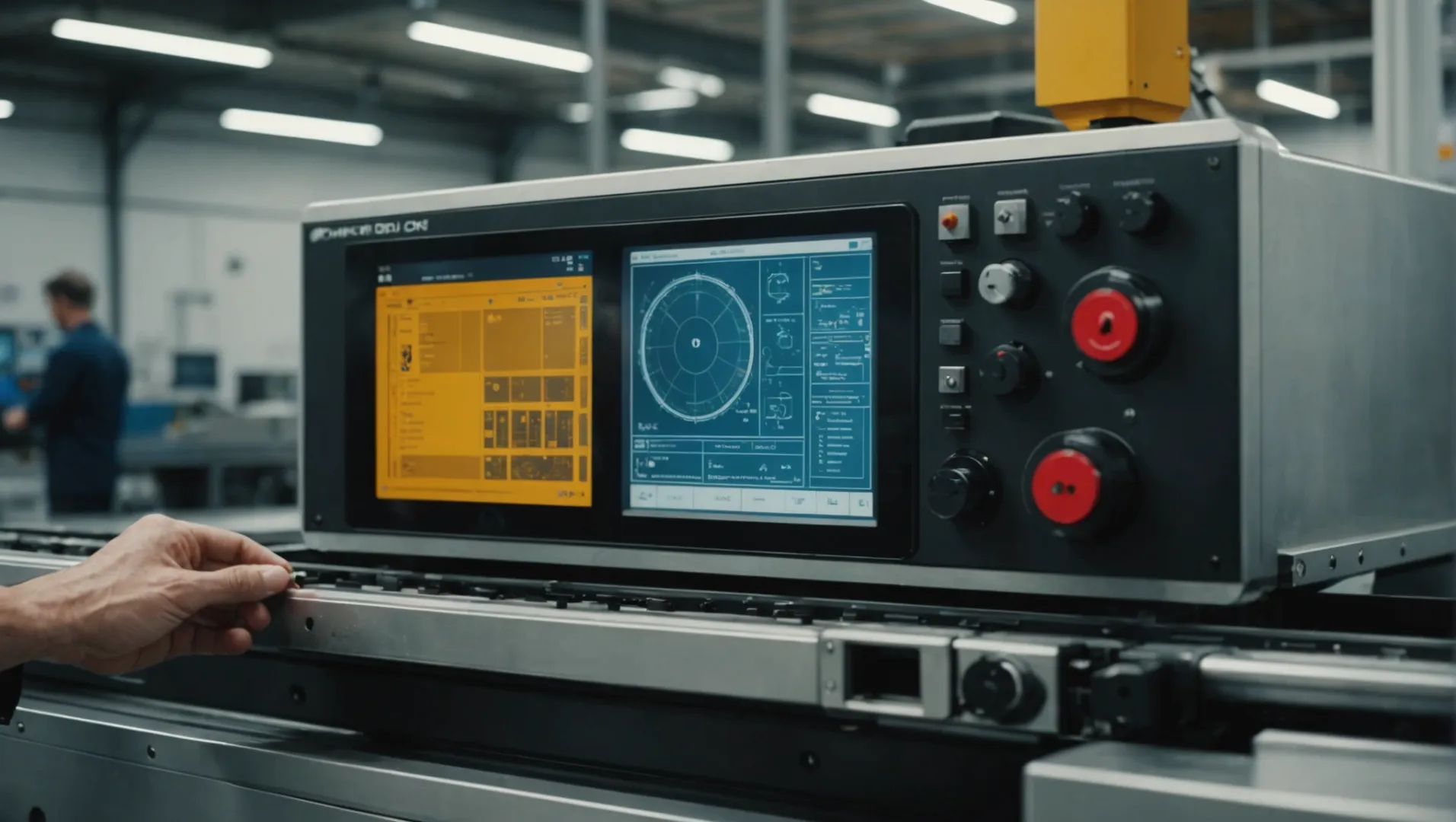
The Significance of Parameter Settings
One of the primary aspects of proper operation is accurately setting machine parameters such as clamping force, injection pressure, and holding time. Incorrect settings can lead to defective products or damage to the mold. For instance, insufficient clamping force might cause plastic flash defects4, whereas excessive force can deform the mold components.
Parameter Optimization:
- Regularly review and adjust parameters based on material and product specifications.
- Conduct trials to determine optimal settings for each production run.
Smooth Mold Handling Techniques
Handling the mold correctly during opening and closing operations is critical. Sudden movements or excessive force can impact mold integrity, causing misalignment and reducing accuracy.
Best Practices for Mold Handling:
- Operate the mold with gradual, controlled motions.
- Avoid quick or harsh movements that could displace components or wear out mechanisms.
Adherence to Operating Procedures
Operators must be well-versed with the machine’s operational guidelines. Proper training ensures they understand how to operate efficiently without compromising on precision.
Training Essentials:
- Regular training sessions on updated procedures and technologies.
- Monitoring and feedback systems to ensure adherence to best practices.
In conclusion, maintaining accuracy in injection molding hinges significantly on proper operation. By focusing on parameter settings, smooth handling, and procedural adherence, manufacturers can sustain high precision and quality in their products.
Incorrect clamping force causes plastic flash defects.True
Insufficient clamping force leads to material leaking out, causing flash.
Harsh mold movements improve accuracy in injection molding.False
Sudden or harsh movements can misalign molds, reducing accuracy.
What Maintenance Practices Ensure Long-Term Clamping Reliability?
In the intricate world of injection molding, maintaining the reliability of clamping mechanisms is pivotal for sustained performance and product quality.
Long-term clamping reliability in injection molds hinges on consistent maintenance practices. This involves regular inspections, cleaning, lubrication, and timely replacement of worn components to prevent operational errors and extend mold life.
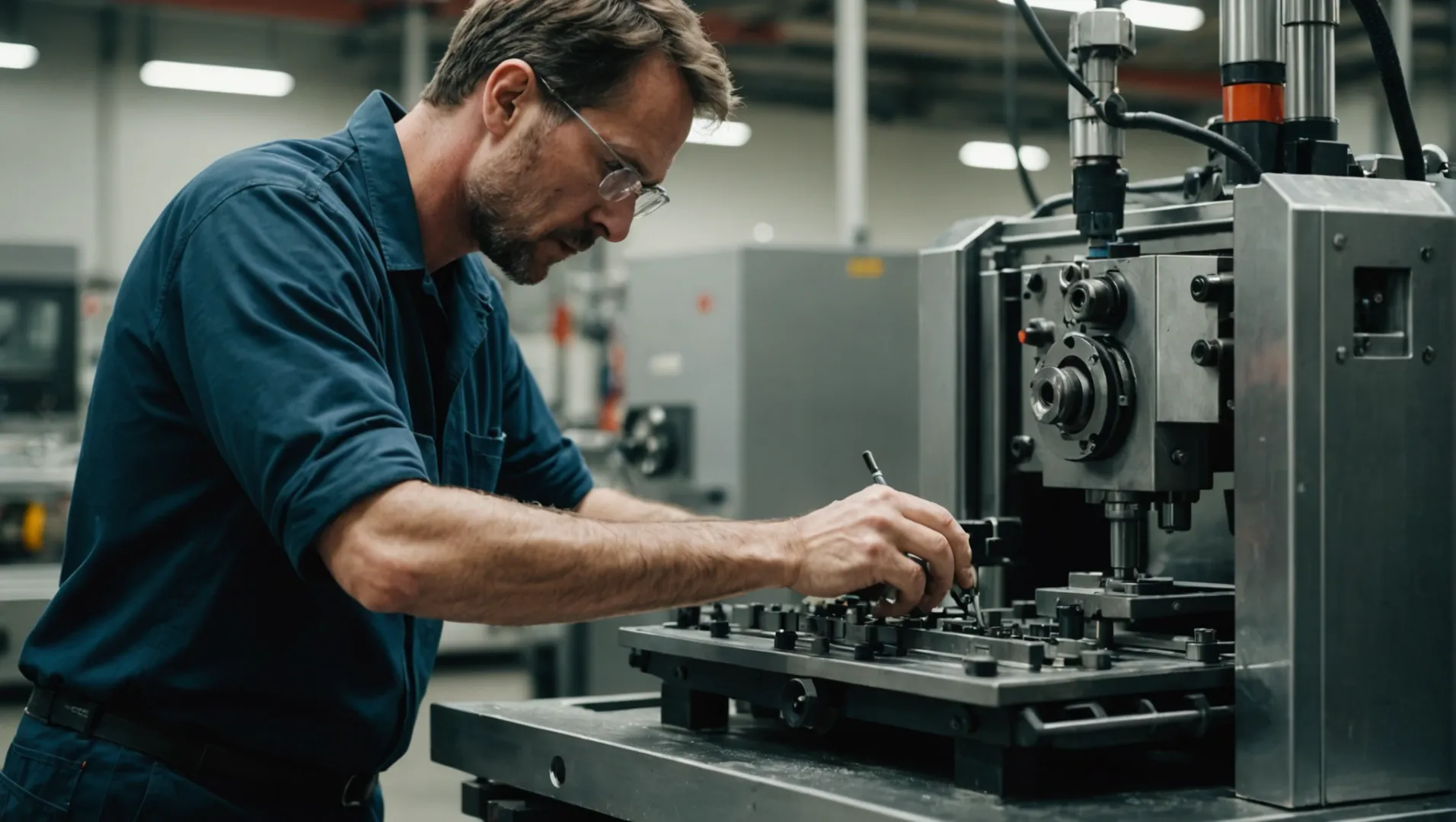
Regular Inspections and Cleaning
One of the most fundamental maintenance practices is conducting regular inspections and cleanings. By routinely checking the mold surface for oil, dust, and other impurities, operators can mitigate factors that contribute to wear and tear. Ensuring the surface is clean helps maintain the clamping accuracy5 by reducing friction and preventing deformation.
A thorough inspection should also involve checking for wear and deformation in various mold parts. Parts that are severely worn should be replaced promptly to sustain the mold’s accuracy and operational efficiency.
Lubrication of Moving Parts
Lubricating the guide mechanism is another essential maintenance task. Proper lubrication minimizes friction resistance, enhancing the smooth movement of the mold during operation. Regular lubrication ensures that the clamping force remains evenly distributed, crucial for sustaining long-term reliability6.
Operators should follow a strict lubrication schedule, using the right type of lubricant as recommended by mold manufacturers. This practice not only prolongs the life of moving parts but also supports the consistent functionality of the clamping mechanism.
Monitoring Clamping Force
Regular monitoring of the clamping force helps detect any imbalances early on. An uneven clamping force can lead to inaccuracies in product dimensions and potential defects like flash. Using precision measuring tools to assess clamping force can help maintain its stability, ensuring long-term operational reliability.
Timely Replacement of Components
Proactive replacement of worn components is critical for avoiding unscheduled downtimes. Establishing a lifecycle plan for each part based on usage data and manufacturer recommendations helps in preemptively addressing wear issues. This approach ensures that the mold operates at peak efficiency7 and maintains its clamping precision over time.
In conclusion, adherence to these maintenance practices not only enhances the longevity of injection molds but also contributes to higher production efficiency and product quality.
Regular inspections prevent clamping errors.True
Inspections identify wear and impurities, ensuring clamping accuracy.
Lubrication is unnecessary for mold longevity.False
Lubrication reduces friction, essential for smooth operation and durability.
Conclusion
Mastering clamping accuracy involves integrating design precision, meticulous manufacturing, and disciplined maintenance. By applying these strategies, you can enhance mold performance, reduce defects, and improve overall efficiency.
-
Discover how CAD software boosts precision in mold design.: AutoCAD is a cornerstone tool for mold designers, offering the ability to create precise 3D models and parametric designs. This software ensures exact … ↩
-
Learn about CAE’s impact on optimizing mold structures.: CAE analysis is used to move the mold filling analysis to the computer, and the mold casting and cooling system’s design scheme can be evaluated and optimized. ↩
-
Explore how advanced equipment and quality control elevate precision.: This technique uses special cooling channels inside the mold that closely conform to the shape of the product, achieving rapid and uniform cooling. This ensures … ↩
-
Learn about causes and prevention of plastic flash defects.: Injection molding flash is a defect that occurs when molten plastic flows out of the mold during injection and solidifies. ↩
-
Learn effective cleaning methods for maintaining mold integrity.: Keeping your injection molds clean is important for maintaining part quality and the life span of … ↩
-
Explore recommended lubrication techniques to reduce friction.: Solid-free high-temperature grease for lubricating ejectors, slides and ejection units in mould and die making that require tight tolerances. ↩
-
Understand component lifecycle management for optimal mold performance.: When the pieces no longer fit, it means the tool cavities are worn. If the elements affect the finished product, then the tool needs to be … ↩