The best pressure for injection molding machines lies between 30 and 200 MPa. Many factors influence this range, including the type of material, the size of the product and the mold’s design. Ordinary plastics, like polyethylene, need lower pressures. Engineering plastics, such as polycarbonate, require higher settings because they have thicker flows.
I recall the first time adjusting an injection molding machine. It felt like a mix of science and art. Each material has unique traits and knowing how they impact pressure settings truly matters. Common plastics like polyethylene allow setting pressures between 40 and 100 MPa. There’s less worry about defects. It’s easier.
But engineering plastics like polycarbonate bring a different challenge. They are demanding, often needing pressures between 80 and 160 MPa. Every part of the mold gets filled perfectly. These materials seem to have their own personality!
Filled or reinforced materials create more challenges. Additives need even higher pressures – often between 120 and 200 MPa. These details keep the work exciting. It’s always changing, probably never boring.
The material isn’t the only concern. Product size and mold design affect everything too. Smaller products with simple designs usually need lower pressures, maybe from 30 to 80 MPa. Bigger projects, like automotive dashboards, require higher pressures, 150 MPa or more.
Each project teaches fresh lessons. Balancing these factors is key. Constant learning keeps the passion alive.
PE materials need 40-100 MPa pressure for molding.True
Polyethylene (PE) materials require 40-100 MPa for effective molding due to their fluidity.
Glass fiber reinforced PA needs 80-120 MPa pressure.False
Glass fiber reinforced PA typically requires 120-200 MPa due to increased viscosity and hardness.
- 1. How Do Material Properties Affect Injection Pressure?
- 2. Why Is Product Design Crucial in Setting Injection Pressure?
- 3. How Does Mold Design Influence Injection Pressure?
- 4. How Can You Adjust Pressure for Filled or Reinforced Plastics?
- 5. What Common Mistakes Should You Avoid When Setting Injection Pressure?
- 6. Conclusion
How Do Material Properties Affect Injection Pressure?
Some materials flow easily into molds. Others resist and do not flow. Why does this happen? Maybe you’ve thought about it.
Properties of the material, such as viscosity, fluidity and additives, play a key role in deciding the injection pressure during molding. Common plastics usually need lower pressures. On the other hand, engineering plastics and reinforced materials need higher pressures for correct molding. Correct molding needs higher pressures.
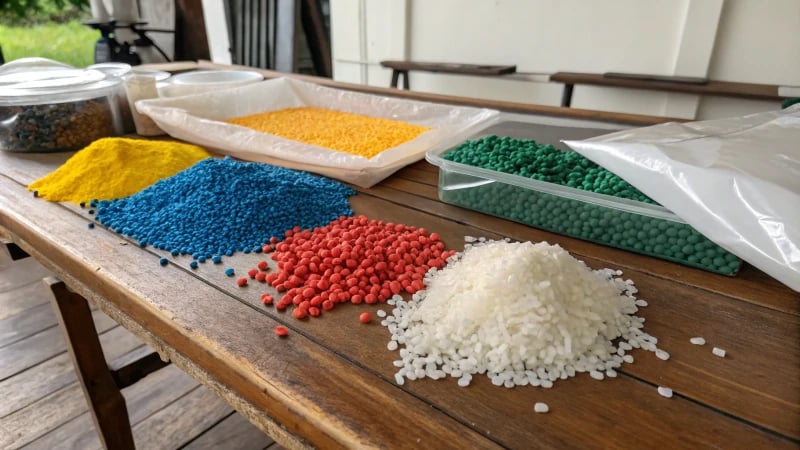
Material Viscosity and Injection Pressure
I recall my early days working in the mold industry, looking at a batch of polyethylene (PE) and feeling surprised at how easily it slipped into the mold. Low-viscosity materials such as PE often need less pressure, around 40 to 100 MPa, because they move into every corner with little resistance. On the other hand, working with polycarbonate (PC) felt like trying to push thick honey through a small straw. It required pressures from 80 to 160 MPa to fill every detail.
Material Type | Viscosity Level | Typical Injection Pressure (MPa) |
---|---|---|
Polyethylene | Low | 40 – 100 |
Polycarbonate | High | 80 – 160 |
Learn more about injection pressure1.
Impact of Additives and Reinforcements
There was a project with glass fiber-reinforced plastics that left me really stressed. These filled materials increase the viscosity. As a result, they demand a high pressure—sometimes reaching up to 200 MPa—to fill complicated molds. Adjusting the pressure for these additives is very important; otherwise, the parts might not meet quality standards.
Explore how additives2 alter material properties and pressure requirements.
Role of Product and Mold Design
Over time, I learned that not only the material but also the product’s design really matters. Small toy parts are easy with pressures as low as 30 MPa. But large automotive dashboards? Get ready for up to 200 MPa. I remember modifying the mold design many times just to perfect the pressure needs.
The mold’s features, like gate size, significantly impact your pressure settings. A mold with a small gate might need an extra 20 to 50 MPa, forcing you to rethink your approach.
Product Type | Complexity Level | Injection Pressure Range (MPa) |
---|---|---|
Small toy parts | Low | 30 – 80 |
Automotive parts | High | Up to 200 |
Understanding these factors feels like having a superpower in injection molding. It is very much about balancing pressure and design to produce high-quality products efficiently.
The mold structure3 is vital in determining the pressure needed for efficient molding.
Polyethylene injection pressures are 40-100 MPa.True
Common plastics like PE require lower pressures due to better fluidity.
Glass fiber reinforced PA needs 60-80 MPa pressure.False
Reinforced materials need higher pressure, usually 120-200 MPa.
Why Is Product Design Crucial in Setting Injection Pressure?
Product design plays a big role in deciding injection pressure in manufacturing. A well-designed product often leads to efficient pressure setting. Efficient pressure setting is crucial. The right design ensures smooth production. Smooth production helps avoid waste. Proper design also keeps costs low, which is very important. Low costs often lead to better profitability. A smooth and efficient process creates reliable products. Reliable products attract more customers.
Product design plays an important role in setting injection pressure. It decides the material type, size, shape and mold structure. These parts decide how much pressure to use. The product must meet quality and function standards. This is very important.
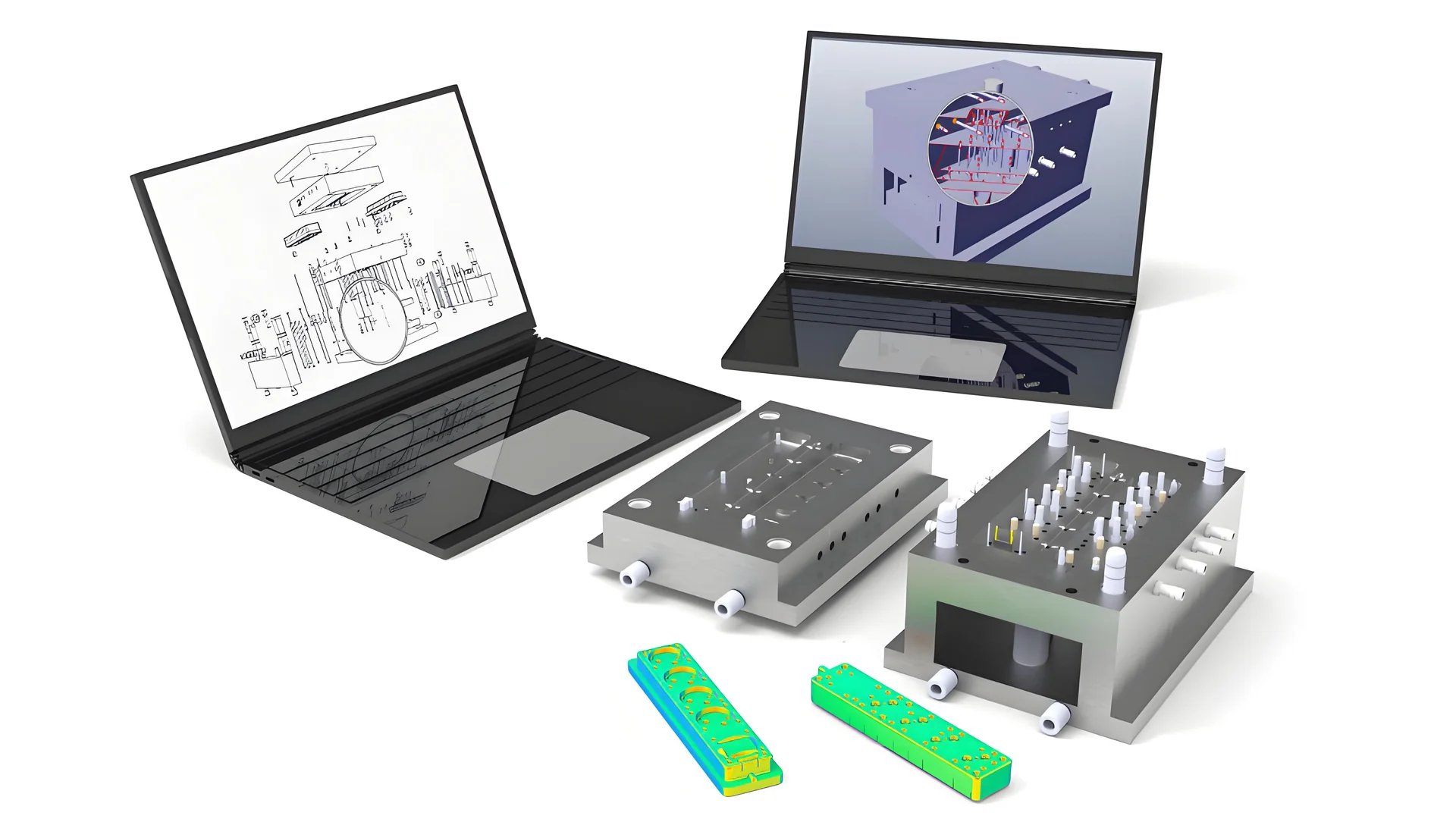
I remember my first days in product design. Back then, I thought injection molding only meant pouring melted plastic into molds. It seemed like magic. I had to learn it. But soon, I found out our design decisions really affect how well products are made and how good they turn out.
Material-Related Factors
Picking the right material for a product is like finding the perfect ingredients for a meal. Each one changes the result. For instance, with plastics like polyethylene (PE), which flows smoothly, I noticed lower pressures of about 40 to 100 MPa work well. But if I use engineering plastics like polycarbonate (PC), it’s different. They are thick. Pressure must rise to between 80 and 160 MPa to get the quality we want.
Material Type | Typical Injection Pressure (MPa) | Example Application |
---|---|---|
Polyethylene (PE) | 40 – 100 | Plastic containers |
Polycarbonate (PC) | 80 – 160 | Electronic product shells |
This relationship underscores the need for designers4 to understand material properties.
Product Size and Shape
Size and shape dictate the pressure rhythm. Small, simple items like toy parts need only about 30 to 80 MPa. Yet, a big car dashboard needs more. To fill all its complex parts, 150 to 180 MPa is usually required.
Example: A large automotive dashboard mold with complex features might need 150 – 180 MPa to accommodate its intricate shapes.
This shows how essential it is to adapt to each design’s needs. Adaptation is crucial.
Mold Structural Features
The mold’s design also matters. A mold with a big gate and smooth channels lets lower pressure be enough. This is really good for the machines.
Mold Feature | Impact on Pressure Requirements |
---|---|
Large Gate | Lower Pressure Needed |
Small Gate | Higher Pressure Required |
Smooth Runners | Lower Pressure Needed |
Complex Runner System | Higher Pressure Required |
But a small gate with tricky paths needs more pressure. This is unavoidable.
A finely detailed mold structure might require 20 – 50 MPa more pressure to manage flow resistance compared to a standard mold.
These considerations are like pieces of a puzzle, helping me go beyond production standards by looking at all aspects, achieving both efficiency and excellent quality.
PE and PP require 40-100 MPa injection pressure.True
These materials have better fluidity, allowing lower pressures for mold filling.
Filled plastics need lower pressure than common plastics.False
Filled plastics have higher viscosity, needing more pressure to fill molds.
How Does Mold Design Influence Injection Pressure?
Have you ever thought about how mold design in plastic injection molding might affect your process? Mold design affects pressure and efficiency. Let’s explore how it influences these elements.
Mold design greatly influences injection pressure. Elements such as gate size, runner system and product complexity are very important. A smart design reduces pressure requirements. This improves efficiency and enhances product quality in injection molding.
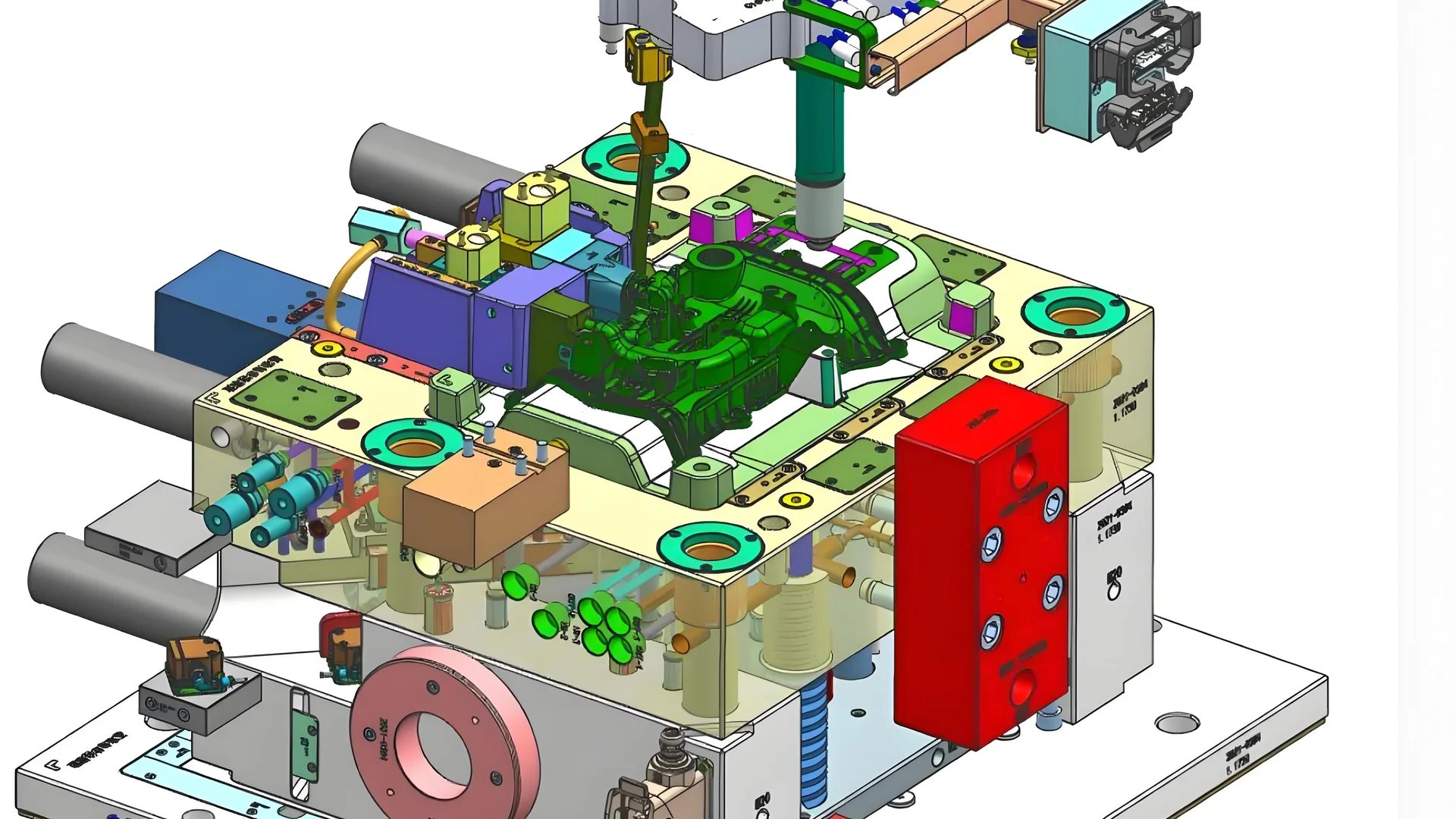
Influence of Material-Related Factors
Material selection is really important in injection molding5. Properties matter, and the type of plastic material used determines the range of pressures required. For instance:
-
Common Plastics: Plastics like polyethylene (PE) and polypropylene (PP) often fill smoothly at lower pressures, around 40 – 100 MPa. In one project with PP containers, we used 70 MPa, which worked perfectly with no defects.
-
Engineering Plastics: Engineering plastics like polycarbonate (PC) need higher pressures, between 80 – 160 MPa, due to high viscosity. A challenge arose with a clear PC electronic product shell. We increased the pressure to about 130 MPa for the ideal fill and look.
-
Reinforced Plastics: Reinforced plastics, such as those with glass fibers, are tough. These need 120 – 200 MPa due to increased viscosity. I remember a strong industrial part from glass fiber-reinforced PA material. Moving the melt through the mold took great pressure!
Product Size and Shape Considerations
The size and shape of the product matter too:
Product Type | Injection Pressure Range (MPa) |
---|---|
Small, simple parts | 30 – 80 |
Large, complex items | 150 – 180 |
For example, larger complex items like a car dashboard I worked on needed between 150 – 180 MPa due to intricate shapes and different wall thicknesses that test design skills.
Impact of Mold Structural Features
Mold structural features are the unseen champions in mold design strategies6. The structural features can dramatically affect injection pressure:
- Gate Size: A larger gate can reduce pressure needs significantly.
- Runner System: I redesigned a runner system once; it became shorter and smoother, lowering resistance and reducing required pressure.
- Venting: Correct venting can cut down needed pressure. Once, poor venting forced us to raise pressure by about 40 MPa for smooth operation.
Knowing these factors helps me develop efficient molds that optimize manufacturing processes7, saving resources while maintaining quality. Each project teaches something new and deepens my respect for mold design.
Polyethylene requires 80-160 MPa for injection molding.False
Polyethylene typically requires 40-100 MPa, not 80-160 MPa.
Small toy parts need 30-80 MPa injection pressure.True
Small and simple products like toy parts require lower pressures.
How Can You Adjust Pressure for Filled or Reinforced Plastics?
Understanding plastics might seem complicated, especially when adjusting pressure for filled or reinforced materials.
Adjust pressure for filled or reinforced plastics based on material type, mold design and product complexity. Pressures between 120 and 200 MPa suit glass fiber-reinforced materials. These pressures work well for glass fiber reinforcements.
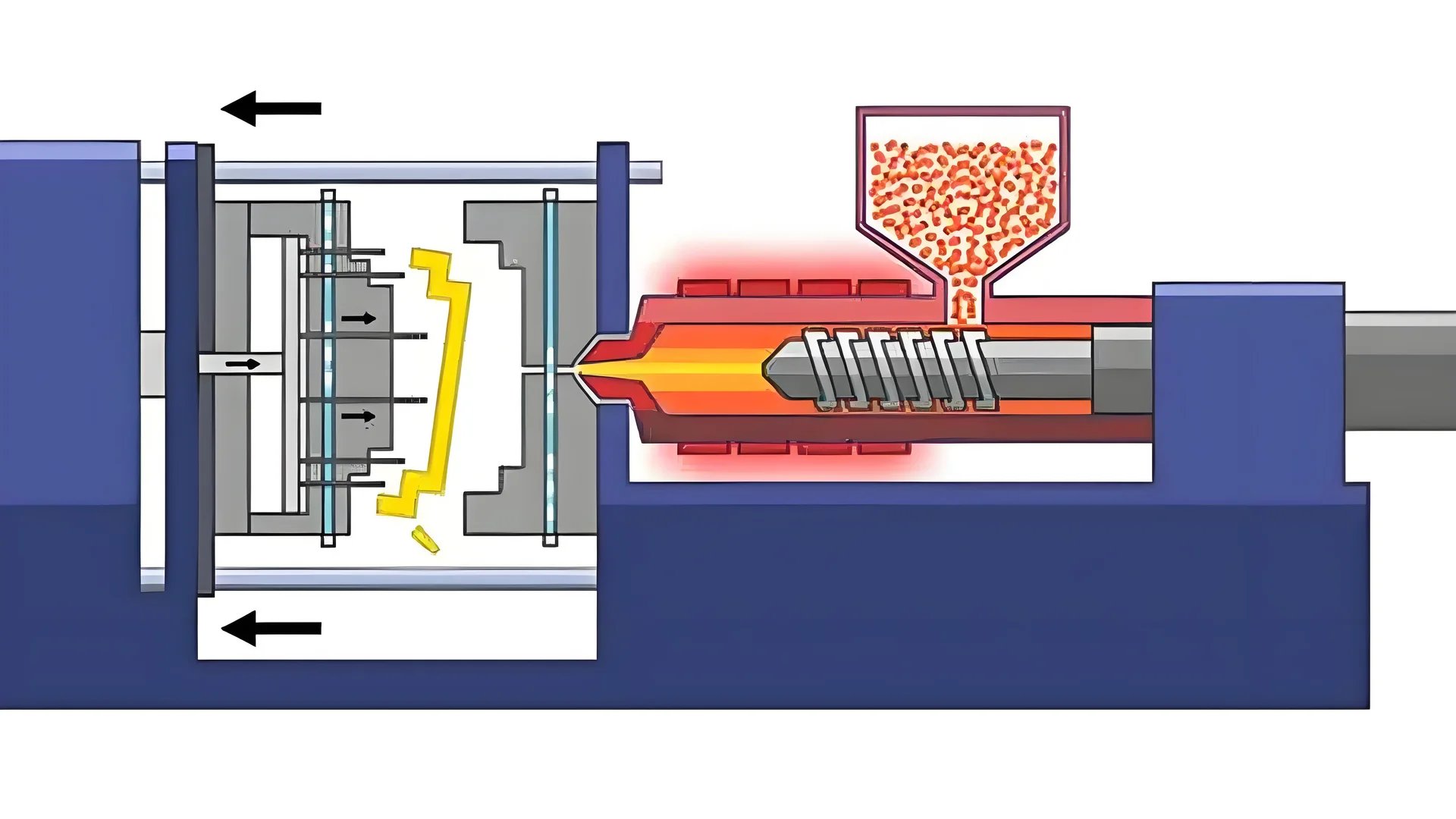
Changing Pressure for Different Materials
For plastics with additives like glass fibers, higher injection pressures are essential due to their thicker flow. For example, glass fiber reinforced PA materials8 may need pressures from 120 – 200 MPa to fill all the tricky mold spaces properly.
Pressure Advice for Various Plastics
Material Type | Injection Pressure Range (MPa) |
---|---|
Polyethylene (PE), Polypropylene (PP) | 40 – 100 |
Polycarbonate (PC), Polyamide (PA) | 80 – 160 |
Glass Fiber Reinforced PA | 120 – 200 |
Impact of Product and Mold
The size and shape of a product greatly affect pressure choices. For small items, like a tiny dinosaur toy I designed once, lower pressures (30 – 80 MPa) were enough. But large, detailed items like car parts need between 100 and 200 MPa.
Moreover, the mold’s structural features play a crucial role. Molds with small gates and complex paths use more pressure to fight resistance. Consider using a mold with optimized venting9 to reduce necessary pressure.
Mold Structure and Pressure Example
Mold Feature | Effect on Pressure |
---|---|
Large Gate, Smooth Runners | Lower Pressure Needed |
Small Gate, Complex Runners | Higher Pressure Needed |
Careful checking of these factors taught me how to adjust pressure for different cases. This way, issues like short shots or excess material are stopped, improving product quality and making production better. Using process optimization tools10 is really helpful in reaching great results.
Injection pressure for PE is 40-100 MPa.True
Polyethylene typically requires 40-100 MPa due to its fluidity.
Glass fiber PA needs 80-100 MPa injection pressure.False
Glass fiber reinforced PA needs 120-200 MPa due to high viscosity.
What Common Mistakes Should You Avoid When Setting Injection Pressure?
Picture the joy of finally understanding how to adjust injection pressure settings. This achievement transforms your molding process into a smooth and flawless operation. The operation becomes defect-free.
Incorrect injection pressure often leads to defects such as warping, incomplete fills or too much flash. Injection pressure problems cause warping. Always think about material type, mold design and product details when adjusting pressure.
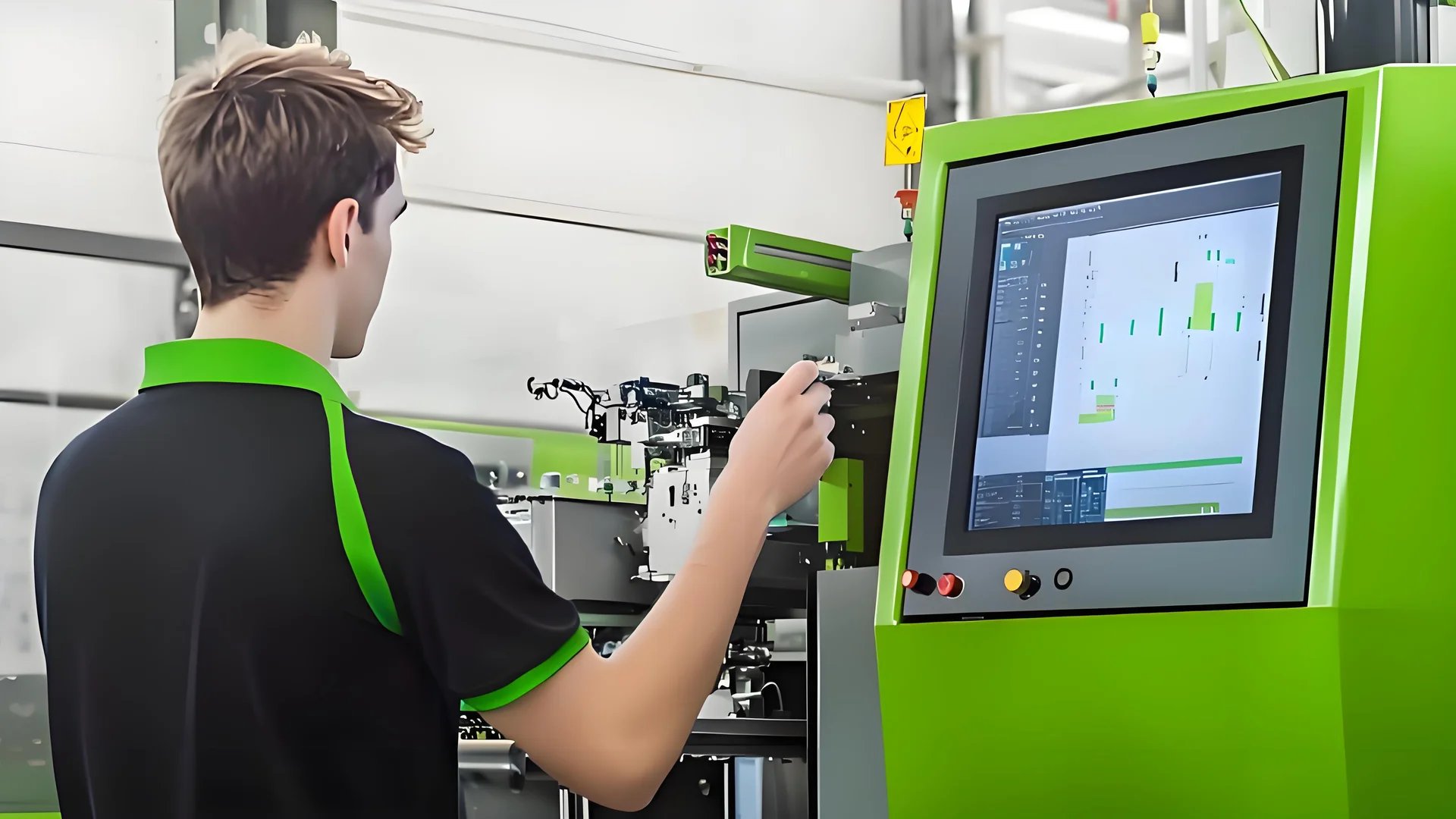
Mistake 1: Ignoring Material Characteristics
I remember working with polyethylene (PE) and polypropylene (PP) for the first time. I really thought I understood everything, but defects appeared. These materials often need lower pressure because they flow easily. For example, a simple PP container usually needs about 60 – 80 MPa. This helps prevent problems like unwanted edges.
Understanding the material-related factors11 is crucial:
Material Type | Typical Pressure Range (MPa) |
---|---|
Polyethylene (PE), Polypropylene (PP) | 40 – 100 |
Polycarbonate (PC), Polyamide (PA) | 80 – 160 |
Glass Fiber Reinforced PA | 120 – 200 |
Engineering plastics like polycarbonate (PC) or polyamide (PA) are different. They are more difficult due to their thickness and strength needs. I recall a transparent PC electronic shell project where the injection pressure had to be exactly right between 100 – 140 MPa for a perfect finish.
Mistake 2: Overlooking Product and Mold Features
I once ignored the effect of product size and mold complexity. I worked on a small toy part and used low pressure, which was correct. Then, the project changed to a big car dashboard, suddenly requiring 150 – 180 MPa to fill all the tiny details.
The size and complexity of your product play a vital role in determining pressure:
- Small, simple parts might only need 30 – 80 MPa.
- A large dashboard requires up to 180 MPa.
Also, mold features such as gate size and runner systems impact pressure needs. The gate size, runner system, and venting in the mold are very important. A bigger gate and smoother runners allow lower pressure; in contrast, a mold with tight areas might need higher pressure12 by about 20 – 50 MPa more to push through resistance.
Mistake 3: Failing to Adjust for Additives
I learned hard lessons about additives like glass fibers that change thickness. Once, with glass fiber-reinforced PA, I did not adjust the pressure resulting in warping and wear.
Additives such as glass fibers increase viscosity, demanding higher pressures. It’s important to adjust your settings based on whether you’re working with filled or reinforced materials. Adjusting injection settings13 without consideration for these additives can lead to defects like warping or excessive wear on machinery.
Mistake 4: Inadequate Monitoring and Adjustment
I used to think real-time monitoring was not necessary until making many defective parts became too easy.
Real-time monitoring of injection pressure is often underestimated. Without continuous adjustments based on feedback, you risk producing a large volume of defective parts.
Implementing real-time monitoring systems14 can aid in maintaining the correct pressure throughout production.
Avoiding these mistakes secures not just quality but also efficient production. Match your injection settings to each project’s specific needs—a lesson I’ve learned that continues to be very beneficial.
PE materials require 100-160 MPa injection pressure.False
PE materials typically need 40-100 MPa due to better fluidity.
Large automotive parts need 150-180 MPa pressure.True
Complex shapes and sizes in automotive parts require higher pressures.
Conclusion
Optimal injection pressure for molding ranges from 30 to 200 MPa, influenced by material type, product size, and mold design. Understanding these factors ensures quality production.
-
Discover how different viscosity levels impact the required injection pressure in molding processes. ↩
-
Understand how additives influence material properties and adjust molding pressures. ↩
-
Learn how different mold designs can affect the necessary injection pressure for effective molding. ↩
-
Discover how mastering material properties enhances design decisions and impacts manufacturing efficiency. ↩
-
Explore different plastic materials used in injection molding to understand their properties and requirements. ↩
-
Discover mold design strategies that can enhance injection molding efficiency and product quality. ↩
-
Learn about methods to streamline manufacturing processes in injection molding for better efficiency. ↩
-
Learn specific pressure settings for glass fiber-reinforced materials to ensure proper mold filling and quality. ↩
-
Explore how optimized mold venting can help lower necessary pressure in injection molding. ↩
-
Discover tools that assist in optimizing injection molding pressure for improved production results. ↩
-
Learn more about how different material properties influence the appropriate setting of injection pressure. ↩
-
Understand how mold complexity necessitates higher pressures to ensure complete filling. ↩
-
Discover techniques for modifying injection parameters when working with filled or reinforced materials. ↩
-
Find out about systems that help maintain proper injection pressure during production. ↩