Let me take you on a journey through the world of manufacturing—where innovation meets efficiency!
Multiple injection molding enhances manufacturing efficiency by enabling the production of complex, multifunctional products in a single process, optimizing material properties, and reducing assembly time and costs.
Dive deeper with me into the fascinating intricacies of multiple injection molding, where we’ll uncover how this technology can transform your production processes and product offerings.
Multi-shot molding reduces production costs.True
Integrating components in one mold cuts assembly steps and material waste.

What are the Key Advantages of Multi-Shot Molding?
Multi-shot molding is transforming manufacturing with its ability to create complex designs and enhance product performance.
Multi-shot molding offers key advantages such as enabling complex structures, integrating multifunctional features, enhancing material properties, and improving both product quality and production efficiency.
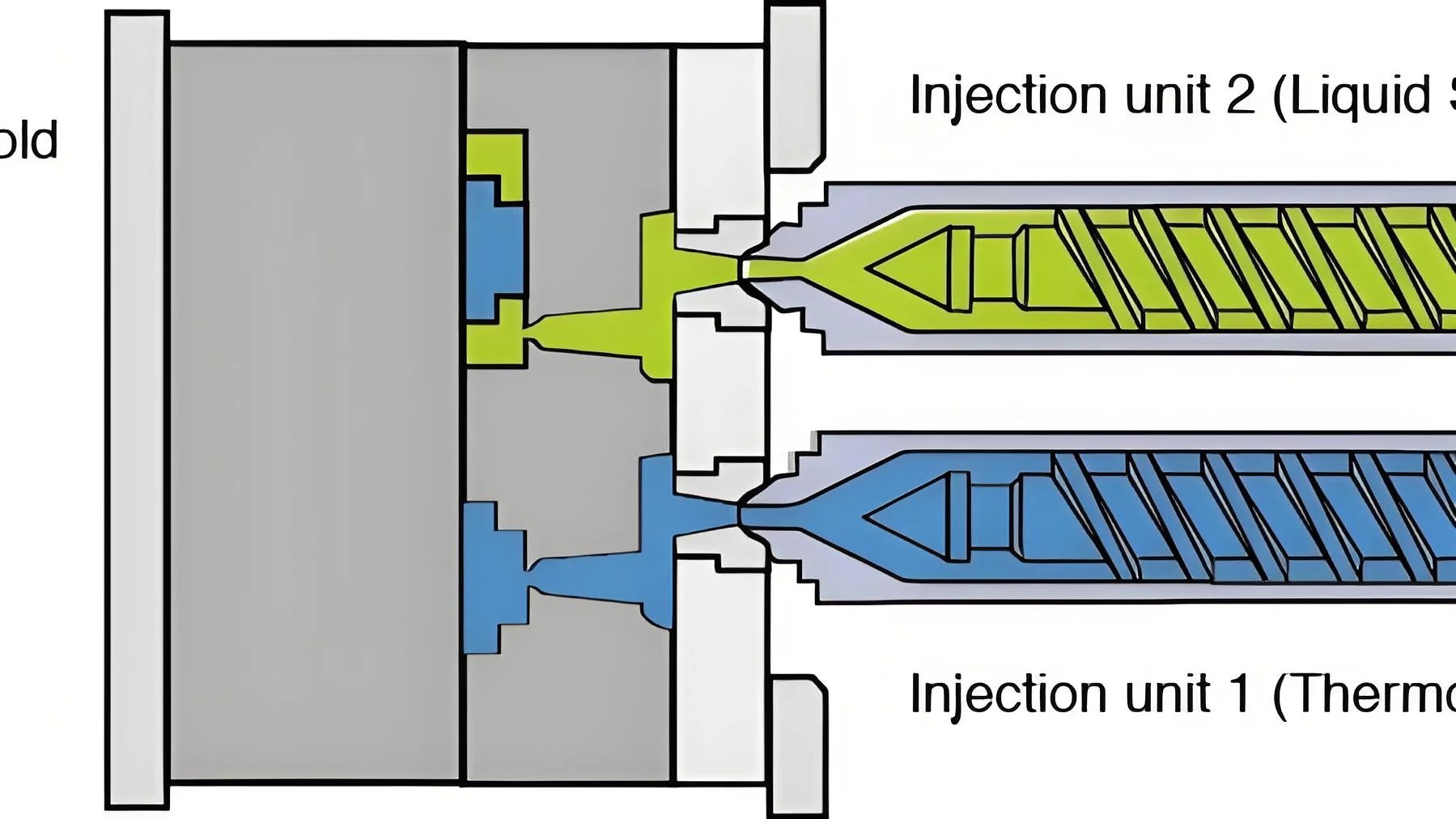
Realizing Complex Structures and Multifunctional Designs
Creating Complex Geometric Shapes
Multi-shot molding excels at producing intricate geometries that single-shot methods struggle to achieve. This process involves injecting different parts in stages, then combining them for precise assembly. Products with internal cavities or fine details, like automotive intake manifolds, benefit from the accuracy and reliability of multi-shot molding.
Integrating Multifunctional Features
This process allows for the seamless integration of multiple functions within a single product. Consider electronic device housings: a robust, high-strength base can be molded first, followed by layers with anti-slip or aesthetic enhancements. This method not only boosts product performance but also streamlines assembly and lowers production costs.
Improving Product Performance and Quality
Optimizing Material Properties
Multi-shot molding facilitates the combination of materials with different properties—such as strength and corrosion resistance—maximizing their individual advantages. For instance, mechanical parts requiring high wear resistance can feature a surface layer of hard plastic while maintaining a tough inner core, enhancing overall performance.
Material | Property | Example Use |
---|---|---|
Engineering Plastic | High hardness | Surface layer for wear resistance |
Tough Plastic | Good toughness | Inner core for durability |
Enhancing Appearance Quality
The capability to merge multiple colors and textures allows multi-shot molding to create visually appealing products. By controlling each injection precisely, manufacturers can avoid defects like flow marks, ensuring superior appearance quality. High-end cosmetic packaging often employs this technique for an exquisite finish.
Reducing Costs and Improving Production Efficiency
Minimizing Assembly Processes
By injecting multiple components sequentially in a single mold, multi-shot molding cuts down on assembly steps. This streamlining enhances production speed and reduces labor costs. Small appliance housings often integrate several functional parts this way, eliminating extra assembly tasks like screwing or gluing.
Maximizing Material Utilization
This process allows for precise material use based on specific part requirements, minimizing waste. Expensive materials can be strategically injected only where necessary, such as in medical devices where biocompatibility is essential. This targeted approach meets performance needs while keeping costs in check.
By leveraging these advantages, manufacturers can revolutionize their product offerings1, driving innovation and efficiency in their processes.
Multi-shot molding reduces production costs significantly.True
By minimizing assembly processes, it lowers labor and material expenses.
Single-shot molding achieves more complex designs than multi-shot.False
Multi-shot molding excels at producing intricate geometries and multifunctional features.
How Does Multi-Shot Molding Optimize Material Usage?
In the realm of manufacturing, efficient material use is vital for sustainability and cost-effectiveness. Multi-shot molding presents a unique solution.
Multi-shot molding optimizes material usage by integrating diverse materials in a single mold, minimizing waste and maximizing functionality.

Integration of Diverse Materials
Multi-shot molding allows manufacturers to combine different materials in a single product, each selected for its specific properties, such as strength or flexibility. This method ensures that every part of the product uses only the necessary amount of material, significantly reducing waste.
For example, consider the production of a medical device2 that requires biocompatible materials for parts in contact with the body but can use standard plastics elsewhere. Multi-shot molding enables the precise application of these materials only where needed, optimizing usage and maintaining performance.
Reduction of Material Waste
By employing multi-shot molding, the need for additional assembly components is eliminated. Products are molded in their final forms, which means there’s no excess material used in separate parts. This not only reduces waste but also enhances structural integrity.
Take automotive components like intake manifolds as an example. Using multi-shot molding, complex geometries are created without excess material typically used in joints or connectors. This precision leads to less waste and a more robust final product.
Precision in Material Application
The accuracy of multi-shot molding allows for selective use of materials with specialized properties. High-cost or high-performance materials are used only where necessary, reducing overall material expenditure.
For instance, electronics housings3 benefit from this process by using a strong internal structure with a secondary layer that provides decorative or functional finishes without unnecessarily covering non-essential areas.
Enhancing Product Functionality
Multi-shot molding not only optimizes material usage but also enhances product functionality. By combining materials with different properties in one process, manufacturers can achieve multifunctional designs that would require multiple production steps in traditional methods.
This integration results in products with enhanced features such as improved grip or added insulation, all achieved without extra material or steps. The efficiency gained from these multifunctional designs further optimizes resource use and streamlines production.
Overall, multi-shot molding represents a sophisticated approach to manufacturing that aligns with modern demands for sustainability and efficiency while pushing the boundaries of what can be achieved in product design.
Multi-shot molding reduces material waste in production.True
By integrating materials in one mold, multi-shot molding minimizes excess.
Multi-shot molding increases the need for assembly components.False
It eliminates extra parts by molding products in their final forms.
Can Multi-Shot Molding Improve Product Aesthetics?
Multi-shot molding is revolutionizing product aesthetics by allowing for complex designs and enhanced surface quality in manufacturing.
Yes, multi-shot molding significantly enhances product aesthetics by enabling the integration of multiple colors, textures, and finishes, while also minimizing surface defects for a refined appearance.
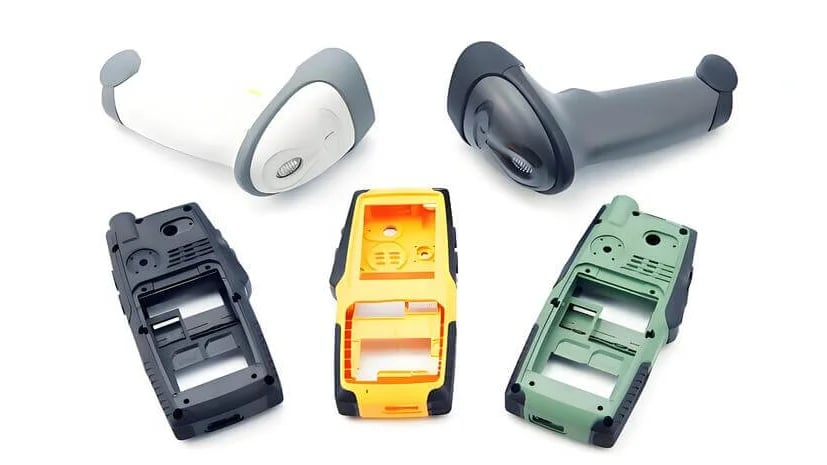
Enhancing Visual Appeal with Multi-Shot Molding
Multi-shot molding allows manufacturers to improve the visual appeal of products by combining different colors, textures, and gloss levels in a single production cycle. This capability is especially beneficial in industries like consumer electronics and automotive, where aesthetics significantly influence consumer choices.
For instance, imagine a smartphone casing that features a seamless blend of glossy and matte finishes, creating a sophisticated look and feel. Such intricate designs are achievable through multi-shot molding4, which eliminates the need for secondary finishing processes, thereby streamlining production.
Minimizing Surface Defects
The process also excels at minimizing common surface defects such as flow marks or shrinkage lines. By precisely controlling each injection’s parameters, manufacturers can ensure a flawless finish. This level of quality control is particularly valuable in high-end product packaging, such as luxury cosmetic containers, where appearance is paramount.
Real-World Applications: Aesthetic Innovation
A notable example of multi-shot molding in action is the production of automotive interior components. Here, the process facilitates the integration of soft-touch materials with high-strength substrates, enhancing both the tactile experience and aesthetic appeal. This multifunctional integration not only improves the product’s visual appeal but also enhances its functional attributes.
Application | Aesthetic Feature | Example |
---|---|---|
Consumer Electronics | Glossy-matte combinations | Smartphone cases |
Automotive | Soft-touch panels | Dashboard components |
Packaging | Unique textures | Cosmetic containers |
These examples illustrate how multi-shot molding enables manufacturers to push the boundaries of design and create products that stand out in competitive markets. By leveraging this technology, companies can deliver aesthetically pleasing products that meet consumers’ high standards for quality and innovation.
Multi-shot molding allows for seamless color integration.True
It enables combining multiple colors in a single cycle, enhancing aesthetics.
Multi-shot molding increases the need for secondary finishing.False
It reduces the need by achieving desired finishes during production.
How Does This Process Reduce Production Costs?
In today’s manufacturing landscape, cost reduction is paramount. Multi-shot molding offers an innovative pathway to achieving this objective.
Multi-shot molding reduces production costs by integrating multiple components into a single mold, minimizing assembly steps and material waste, and increasing efficiency.
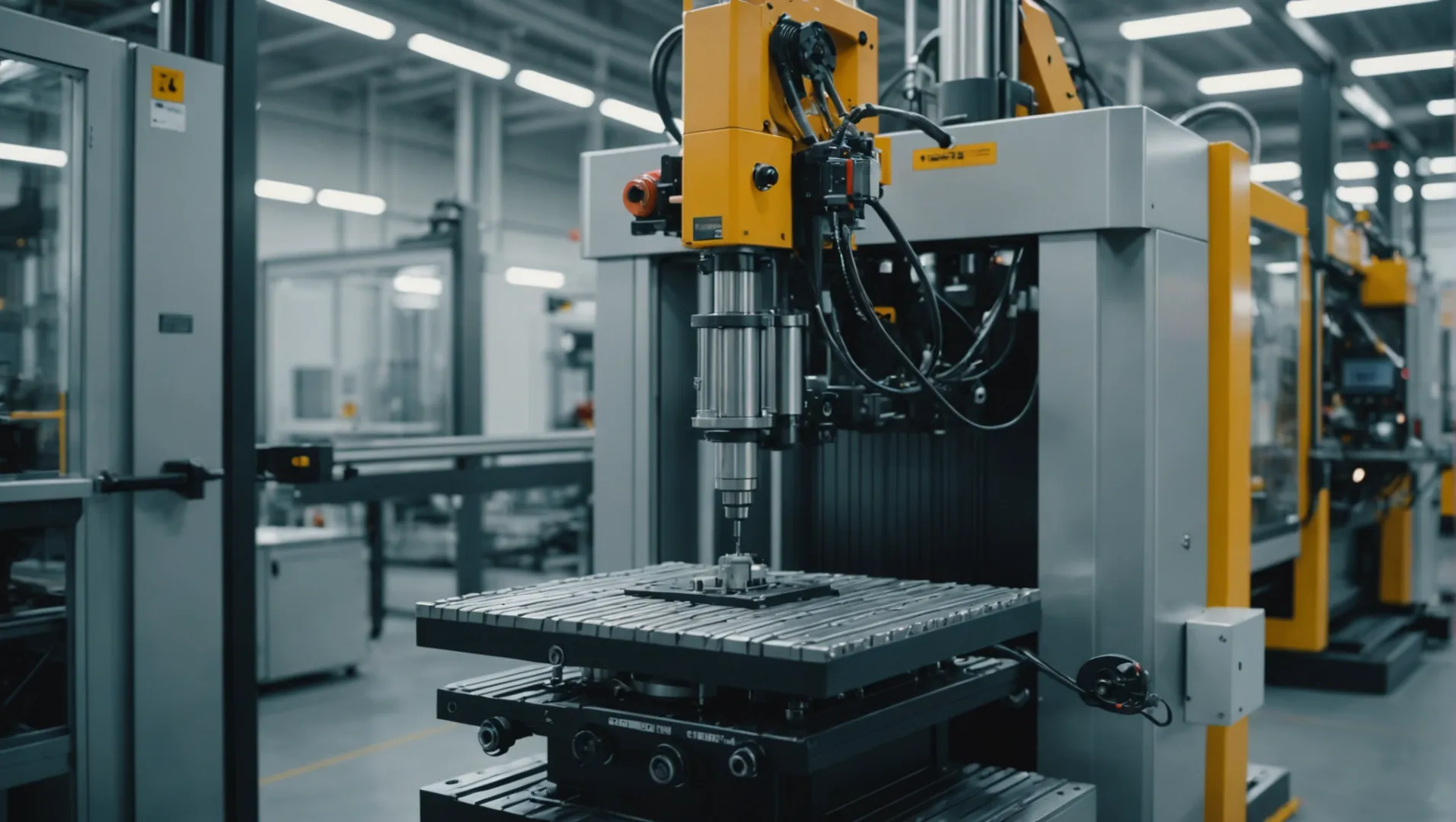
Streamlining Assembly Processes
One of the primary ways multi-shot molding reduces production costs is by minimizing the need for separate assembly steps. Traditional manufacturing often requires multiple components to be produced separately and then assembled, which involves additional labor and time. With multi-shot molding, different parts of a product can be molded together in one sequence, significantly reducing the number of assembly processes required.
For instance, consider the manufacturing of a complex electronic device housing. Using traditional methods, each layer of the housing might need to be produced separately and then pieced together manually or through additional machinery. In contrast, multi-shot molding can integrate these layers in a single process, combining functionality and reducing the steps required to achieve the final product. This not only speeds up production but also cuts down on labor costs.
Enhancing Material Utilization
Multi-shot molding enables precise control over material usage, which can lead to substantial cost savings. By injecting materials only where they are needed based on the product’s requirements, manufacturers can avoid unnecessary waste. This approach is particularly beneficial when working with expensive materials.
For example, in the production of medical devices5, manufacturers can use biocompatible materials only in areas that come into contact with the body, while using more cost-effective materials elsewhere. This strategic use of materials ensures that performance standards are met without excessive expenditure.
Reducing Material Waste
The accurate material control afforded by multi-shot molding also reduces waste. In traditional processes, excess material often results from trimming or cutting components to fit them together. Multi-shot molding eliminates this waste by shaping components precisely during the initial molding phase.
Take the automotive industry, where components such as intake manifolds often require complex designs. Multi-shot molding allows for precise production of intricate shapes without excess trimming, thus conserving material and reducing costs.
By leveraging these advantages, multi-shot molding not only enhances manufacturing efficiency but also offers a tangible way to reduce production costs. As manufacturers continue to explore this technology, its potential to transform product development and streamline operations becomes increasingly evident.
Multi-shot molding reduces labor costs.True
By integrating components into a single mold, assembly steps are minimized.
Traditional molding uses less material than multi-shot.False
Multi-shot molding uses precise material application, reducing waste.
Conclusion
Embracing multiple injection molding is a game changer for manufacturers, driving efficiency while enhancing product quality. Let’s innovate together!
-
Explore how multi-shot molding revolutionizes product offerings and manufacturing processes.: Multi-shot injection molding, also known as multi-color injection molding, refers to the process where two or more colors or different materials are molded. ↩
-
Explore how biocompatible materials are selectively used to reduce waste.: Two-shot, or multi-shot injection molding, is a highly efficient manufacturing process in which molded parts from two or more different … ↩
-
Learn about using multi-layered materials for functional electronics housings.: The LSR Multi-Shot technology allows for part weight and space optimization, complex designs, the integration of multiple materials, and multiple functions into … ↩
-
Explore how multi-shot molding transforms product aesthetics and consumer appeal.: Improved Product Quality & Durability. By using multiple materials, multi-shot injection moulding can enhance product performance and quality. The process … ↩
-
Explore why biocompatible materials are essential for patient safety and device efficacy.: These materials have many advantages, such as non-toxicity, biocompatibility, and biodegradability, the use of natural biomaterials has … ↩