In the fast-paced world of manufacturing, optimizing efficiency is paramount for success.
Multiple injection molding enhances manufacturing efficiency by allowing for the integration of different materials or colors in a single mold, improving product strength, sealing, wear resistance, appearance, and reducing assembly processes, thus saving time and costs.
While the initial explanation outlines the basic benefits of multiple injection molding, there’s much more to explore. Dive deeper to understand how these methods can transform your production processes and lead to significant gains in quality and cost-effectiveness.
Multiple injection molding reduces assembly processes.True
It integrates parts in a single mold, saving time and costs.
What Are the Key Benefits of Multiple Injection Molding?
In the competitive realm of manufacturing, leveraging advanced techniques is crucial for product excellence.
Multiple injection molding offers key benefits like enhanced strength, improved sealing, wear resistance, aesthetic versatility, and cost efficiency, transforming the manufacturing landscape.
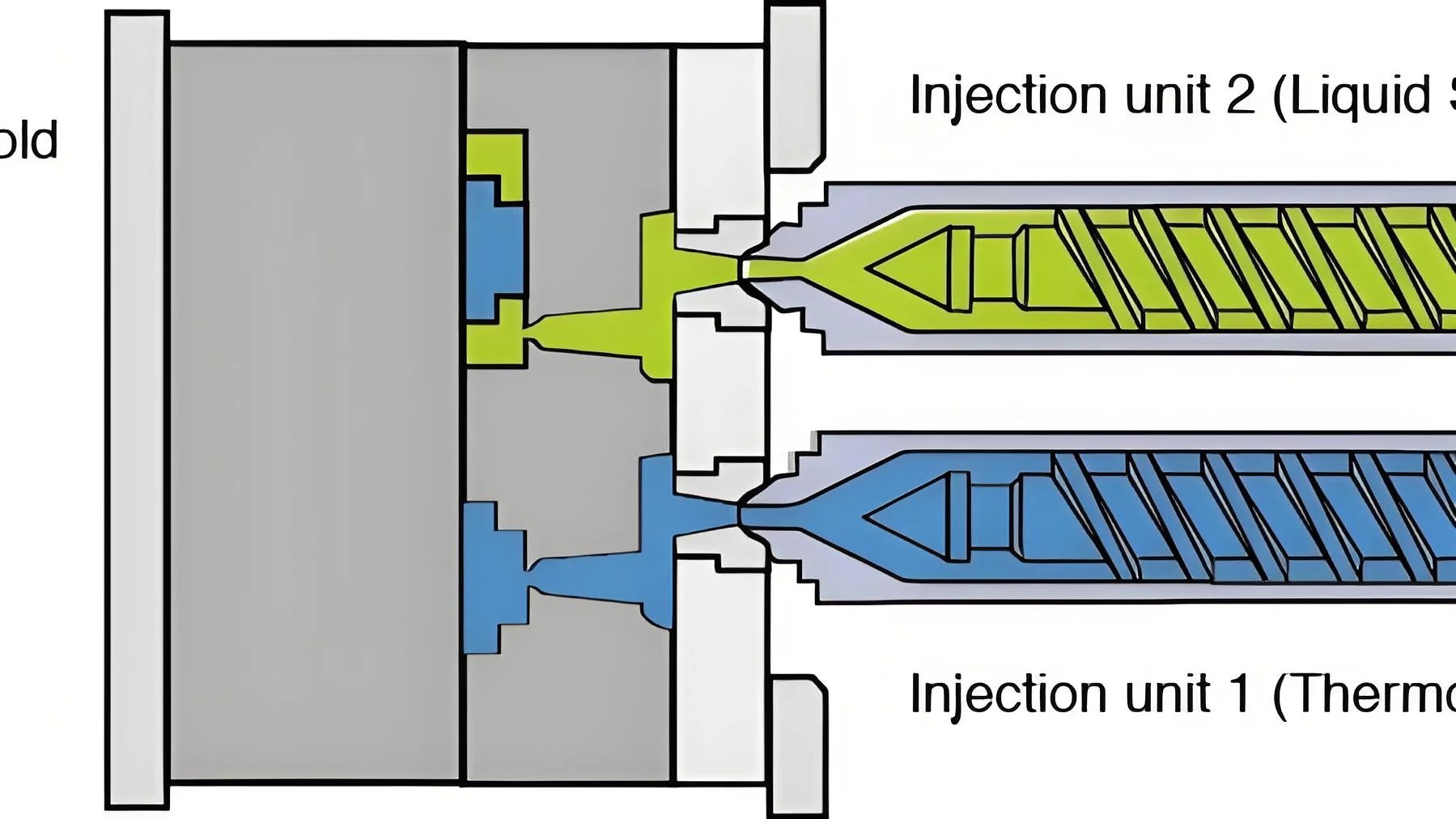
Product Performance Improvement
One of the most significant advantages of multiple injection molding1 is its ability to enhance product performance. This technique allows manufacturers to strategically combine materials with different properties to achieve superior strength. For instance, a structural component can have a core made of high-strength engineering plastic, while areas prone to stress are reinforced with a tougher material. Such meticulous layering results in products that are not only more robust but also have better impact resistance, making them ideal for high-stress applications like sports equipment and tool handles. Additionally, this process is pivotal in improving sealing properties. By injecting elastic materials into critical sealing zones, products like containers and pipes maintain integrity across varying conditions, effectively preventing leaks. A case in point would be medical devices that require reliable seals to store medications safely.
Moreover, enhancing wear resistance is another feather in the cap for multiple injection molding. Parts such as gears and bearings benefit from this process by incorporating high-wear-resistance materials in friction-heavy areas. This not only prolongs the lifespan of components but ensures optimal functionality under extreme conditions.
Product Appearance Optimization
Aesthetic appeal can be a decisive factor in product success, and multiple injection molding excels in this arena as well. This method facilitates the combination of various colors and textures, offering an array of design possibilities. For instance, manufacturers can inject transparent materials on the product surface to achieve a crystal-clear effect or use different colored materials to create striking patterns or logos. This capability is particularly beneficial for consumer electronics, where visual appeal significantly influences market competitiveness.
Beyond mere aesthetics, multiple injection molding can be used to achieve special effects such as metallic textures or luminous finishes. These unique appearances can captivate consumers and add value to products like toys, which can feature glow-in-the-dark elements for added allure.
Cost Reduction and Production Efficiency
The economic advantages of multiple injection molding are substantial. By minimizing assembly processes through integrating parts within a single mold, it drastically cuts down on production time and labor costs. This not only enhances efficiency but also improves product quality by reducing human error during assembly.
Furthermore, this process allows for optimized material usage. Manufacturers can allocate high-performance materials only to crucial parts of a product, using less expensive alternatives elsewhere. This strategic approach not only meets performance demands but also significantly trims material costs. For instance, in automotive applications, essential components can be fortified with premium materials while less critical areas use cost-effective substitutes.
In summary, multiple injection molding is an invaluable tool in modern manufacturing, promising improvements across performance, appearance, and economic fronts.
Multiple injection molding enhances product strength.True
Combines materials with different properties for superior strength.
Multiple injection molding increases production time.False
It reduces production time by integrating parts in a single mold.
How Does Multiple Injection Molding Improve Product Strength?
Multiple injection molding is revolutionizing product design by enhancing strength and durability across industries.
By injecting materials with varying properties, multiple injection molding enhances product strength through improved structural integrity, impact resistance, and wear resistance.
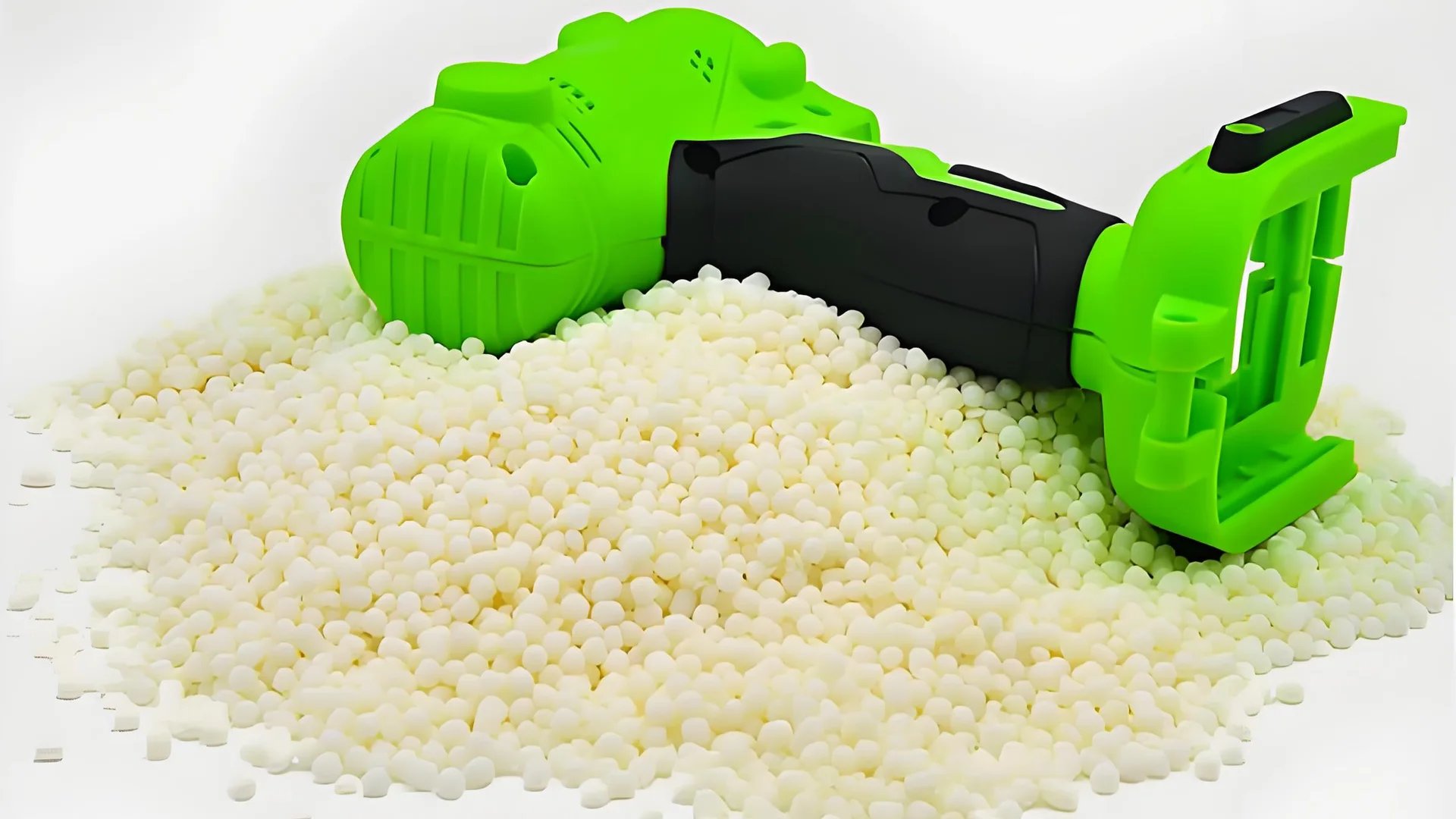
Enhancing Structural Integrity
One of the core advantages of multiple injection molding2 lies in its ability to bolster the structural integrity of products. This is achieved by injecting high-strength engineering plastics as the primary layer in areas subject to high stress. For instance, in automotive components, this technique can significantly enhance the durability of parts like bumpers or dashboards, which are prone to frequent stress and impact.
Boosting Impact Resistance
In industries where products are regularly exposed to impacts, such as sporting goods or tool manufacturing, multiple injection molding plays a vital role in augmenting impact resistance. By using materials with different toughness levels, such as injecting a tough outer layer over a rigid core, manufacturers can ensure that the product withstands heavy use without compromising its longevity. This method is particularly beneficial for products like baseball bats or hammers, which need to endure repeated impacts.
Improving Wear Resistance
Wear resistance is a crucial factor for components that encounter constant friction. In mechanical applications like gears or bearings, multiple injection molding can inject materials known for their high wear resistance in the friction-prone areas. This results in parts that maintain optimal performance even under demanding conditions like high temperature and pressure. For example, in automotive engines, this technique reduces the risk of wear and potential failures, thereby extending the lifespan of engine components.
Achieving Better Sealing
Sealing efficiency is another area where multiple injection molding excels. By integrating soft elastic materials at sealing joints, products can achieve superior sealing capabilities. This is essential for items such as medical devices or containers that must prevent leaks to function safely and effectively. The ability to maintain an airtight seal across varying environmental conditions is a testament to the versatility and reliability offered by multiple injection molding.
Through these enhancements in strength, manufacturers can produce products that not only meet but exceed industry standards for durability and performance. The strategic use of materials tailored to specific functions underscores the transformative potential of multiple injection molding in modern manufacturing.
Multiple injection molding enhances product impact resistance.True
By using materials with different toughness levels, products withstand impacts.
Single injection molding improves wear resistance better than multiple.False
Multiple injection molding targets friction areas with high wear-resistant materials.
In What Ways Can Multiple Injection Molding Enhance Product Appearance?
Discover how multiple injection molding can revolutionize product design and aesthetics.
Multiple injection molding enhances product appearance by allowing for vibrant colors, diverse textures, and special effects in a single manufacturing process.

Achieving Rich Colors and Textures
Multiple injection molding opens up a world of possibilities for product aesthetics. By injecting different materials or colors into the same mold, manufacturers can create visually stunning products with a blend of rich colors and intricate textures. For example, consumer electronics such as smartphones and tablets can feature glossy finishes and multi-colored designs that enhance their market appeal.
Consider a product like a kitchen appliance handle. By using multiple injection molding3, manufacturers can combine a durable inner core with an attractive, textured outer layer. This not only improves functionality but also adds to the visual appeal, making the product more desirable to consumers.
Creating Unique Special Effects
Beyond colors and textures, multiple injection molding allows for the integration of special effects that can set products apart in competitive markets. Techniques such as metallic finishes, color-changing surfaces, and even luminous effects can be achieved through this process. For instance, a toy manufacturer might inject glow-in-the-dark materials into parts of a toy to captivate children’s imaginations.
This capability is particularly beneficial in industries where aesthetic differentiation is crucial, such as fashion accessories or high-end automotive interiors. By employing innovative material combinations4, designers can craft products that not only meet functional requirements but also offer captivating visual experiences.
Implementing Functional Aesthetic Features
Multiple injection molding isn’t just about appearance; it also offers functional advantages that enhance aesthetic value. For example, incorporating soft-touch materials in areas of high interaction can improve grip and comfort, providing an ergonomic advantage that consumers appreciate.
Incorporating functional design elements such as logos or patterns directly into the product during the molding process eliminates the need for additional post-processing steps like painting or labeling. This not only streamlines production but also ensures consistent quality and durability of the aesthetic features.
By leveraging advanced molding techniques5, companies can enhance both the look and feel of their products, driving customer satisfaction and brand loyalty.
Multiple injection molding allows for vibrant colors.True
Different materials/colors can be injected, creating vibrant aesthetics.
Multiple injection molding cannot create special effects.False
It enables special effects like metallic finishes and luminous designs.
How Does Multiple Injection Molding Reduce Production Costs?
In manufacturing, cutting costs without sacrificing quality is a challenging yet crucial goal.
Multiple injection molding reduces production costs by streamlining assembly, optimizing material usage, and enhancing product performance, which collectively minimize waste and labor expenses.
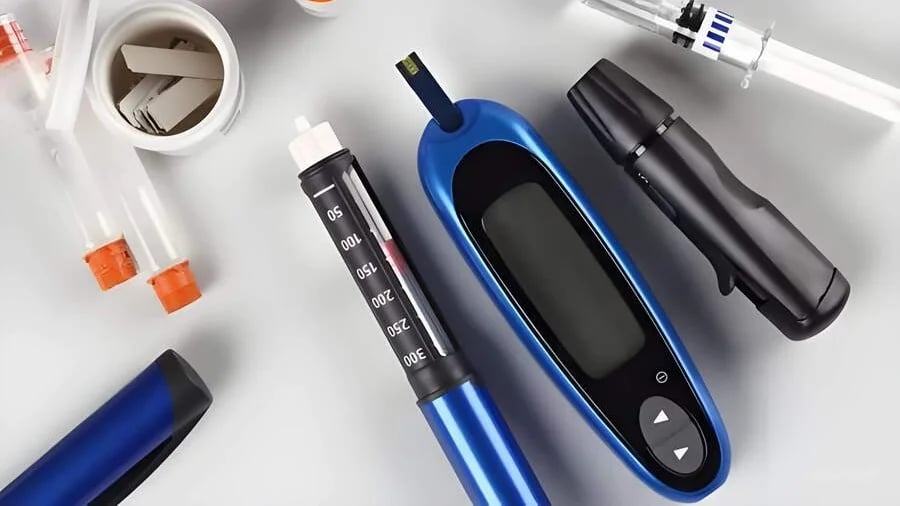
Streamlining the Assembly Process
One of the most significant cost-saving benefits of multiple injection molding6 is the reduction in the assembly process. Traditional methods often require numerous parts to be manufactured separately and then assembled manually, a labor-intensive and error-prone procedure. With multiple injection molding, different components can be molded together in one cycle, significantly decreasing the need for manual assembly. This not only speeds up production but also enhances product reliability by reducing assembly errors.
For example, consider a product that traditionally required multiple screws and joints to hold various parts together. By using multiple injection molding, these can be integrated within a single mold, eliminating the need for additional fastening hardware.
Optimizing Material Usage
Multiple injection molding allows manufacturers to strategically use materials based on the specific needs of different product areas. This optimization means that expensive materials are only used where absolutely necessary, while more cost-effective options can be employed elsewhere. For instance, a component that requires high durability at one end can be made from premium-grade plastic, while the remainder can utilize a less expensive alternative.
This targeted approach ensures that performance is uncompromised while keeping material costs in check. For example, in a car part, using a robust plastic where high wear is expected and a cheaper variant in less critical areas can lead to substantial savings.
Enhancing Product Performance
By enhancing product performance through improved strength, sealing, and wear resistance, multiple injection molding indirectly contributes to cost reductions. Products that perform better and last longer require fewer replacements and repairs. This leads to fewer warranty claims and lower after-sales service costs for manufacturers.
Moreover, products with superior performance often command higher prices in the market, allowing manufacturers to achieve better profit margins. For instance, an electronic device with enhanced impact resistance due to multiple injection molding can be marketed as a premium product.
Reducing Waste and Labor Costs
The integration of different materials and colors within the same mold also leads to significant reductions in waste. Traditional processes that involve painting or additional processing steps often result in leftover materials or defective products. Multiple injection molding minimizes these inefficiencies by producing finished components in a single cycle.
Additionally, labor costs are reduced due to decreased dependency on manual assembly and post-processing tasks. The streamlined production line enabled by this technology allows for faster turnaround times and lower labor expenses.
In summary, by reducing assembly needs, optimizing material selection, enhancing product performance, and minimizing waste and labor costs, multiple injection molding stands out as a powerful tool for reducing production expenses while maintaining or even improving quality.
Multiple injection molding reduces manual assembly needs.True
It combines components in one cycle, minimizing manual labor.
Using multiple injection molding increases material waste.False
It optimizes material usage, reducing waste through precise allocation.
Conclusion
Multiple injection molding offers a strategic advantage in manufacturing by improving product quality and reducing costs. Embrace this technology to enhance efficiency and stay competitive in the market.
-
Explore how this technique revolutionizes product strength and efficiency.: The most important reasons are production speed and efficiency, potential cost savings, and, in some cases, improved color consistency. ↩
-
Discover how multiple injection molding integrates diverse materials for enhanced product performance.: Multi-shot plastic injection molding is the process of injecting two or more plastic materials or colors into a single mold simultaneously to create a single … ↩
-
Explore how various colors and textures enhance product appeal.: Two-color injection molding is a process that allows two different colors of plastic to be used in a single molded part. ↩
-
Discover innovative aesthetic effects achievable with this technology.: Special effect compounds can increase consumer appeal, provide beneficial features, mimic other materials, and add visual impact to your plastic products! ↩
-
Learn about integrating functional aesthetics in product design.: You can also improve the design and function of products automatically and cost-effectively. Multi-component molding is highly diverse and … ↩
-
Explore detailed advantages of this method for cost-effective manufacturing.: The main reason to use multi-cavity molding is the massive increase in production efficiency it can offer. When using a single-cavity mold, each … ↩