Picture a world where the smallest medical tools are designed so precisely that they change healthcare completely.
Multi-stage injection molding changes medical device manufacturing. This process gives exact control over how fast and hard materials are injected. Products like syringes, infusion sets and medical packaging become very accurate and high-quality. These products meet the strict requirements of the medical field. Very strict requirements.
Thinking back to my days designing plastic parts, I recall the first time I saw multi-stage injection molding. It was like discovering magic in manufacturing. This process creates not only syringes or infusion sets but also makes sure every piece is safe and precise. Adjusting the injection speed at key moments helps avoid defects like jet marks, giving strength and uniformity. From skinny droppers to complicated equipment shells, this technology smoothly changes to fit different needs. It really improves both function and strength in many medical tools.
Multi-stage injection molding improves syringe accuracy.True
This technology allows precise control over molding parameters, enhancing accuracy.
Medical packaging uses single-stage injection molding.False
Multi-stage molding is used for better precision and quality in medical packaging.
- 1. Why is multi-stage injection molding a game-changer in medical manufacturing?
- 2. How Does Multi-Stage Injection Molding Improve Syringe Production?
- 3. Why is Multi-Stage Injection Crucial for Infusion Set Components?
- 4. How does multi-stage injection enhance medical packaging quality?
- 5. How Does Multi-Stage Injection Enhance Medical Equipment Shells?
- 6. Conclusion
Why is multi-stage injection molding a game-changer in medical manufacturing?
Picture creating medical tools with the skill of a watchmaker and the smoothness of a perfectly running engine. That’s the wonder of multi-stage injection molding.
Multi-stage injection molding changes medical manufacturing. It increases dimensional accuracy. It reduces defects. It improves material properties. This process is essential for creating reliable medical devices. It produces high-quality products.
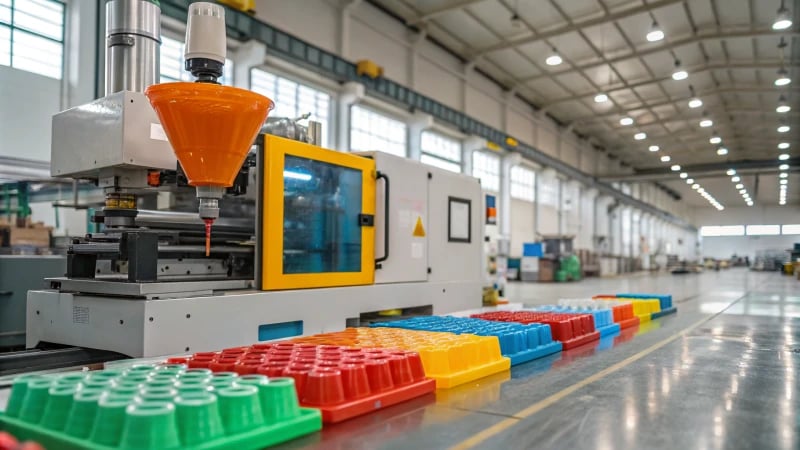
Better Dimensional Accuracy
Precision is very important in medical manufacturing. It is not just a trendy word; it is a necessity. I remember working on syringe production for the first time. At first, the structure appeared simple, but the details were tricky and important. Multi-stage injection molding helped control injection speed and pressure1. This method kept the wall thickness the same everywhere, increasing the syringes’ strength and safety.
Fewer Defects
Defects in medical parts can be terrible, so reducing them is crucial. When I worked on making parts for infusion sets, I saw how complex shapes looked scary. High quality was a must. Adjusting parameters for each stage helped stop jet marks and shrinkage, ensuring each piece stayed intact and strong.
Better Material Properties
Handling medical packaging taught me about the importance of sealing and stability—key to keeping drug quality intact. Multi-stage injection molding gave careful control over how plastic flowed, increasing resistance to compression and improving sealing performance of items like pharmaceutical packaging bottles2.
Application | Key Benefit | Example |
---|---|---|
Syringes | Dimensional accuracy | Prevents uneven wall thickness |
Infusion sets | Quality assurance | Ensures uniform thin walls in droppers |
Packaging | Enhanced sealing | Improves shelf life of drugs |
Complex Component Production
Projects involving medical filter housings need precision everywhere. Multi-stage injection molding allows for specific settings that ensure proper filling of every cavity area, avoiding material shortages or bubbles.
Excellent Aesthetic and Structural Quality
Working on large medical equipment shells showed me the link between beauty and strength. This technique allowed for different speeds in various sections, ensuring both visual appeal and structural integrity3. Using low-speed injections on edges and corners kept appearance precise while preserving equipment’s strength.
Using these advantages means creating medical devices of very high quality—devices that surpass industry standards. Anyone thinking about using this technology should understand these benefits as they help in making smart decisions.
Multi-stage injection molding ensures uniform wall thickness.True
This process controls injection speed and pressure, enhancing accuracy.
Multi-stage injection molding increases defect rates in production.False
It reduces defects like jet marks by adjusting parameters effectively.
How Does Multi-Stage Injection Molding Improve Syringe Production?
Do you ever think about how a plain syringe gets its flawless shape and purpose? Let’s explore the fascinating world of multi-stage injection molding!
Multi-stage injection molding improves syringe production by controlling injection speed and pressure at various stages. This process results in uniform wall thickness and high-quality syringes. Defects like jet marks and overflow are prevented, which is very important for safety and precision.
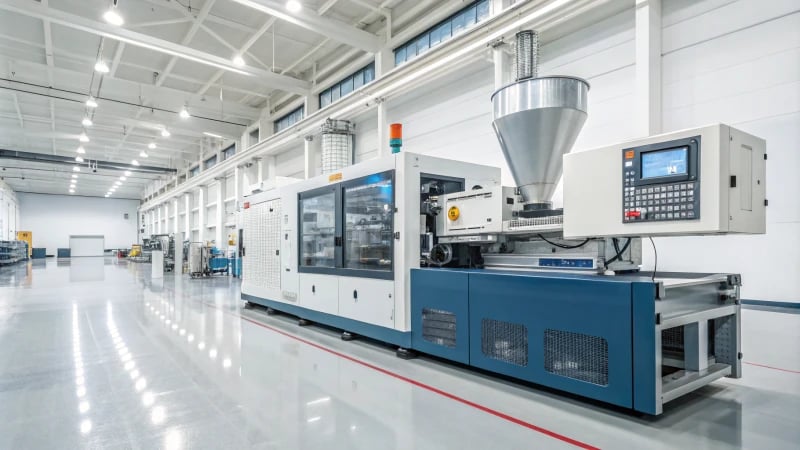
The Process and Benefits of Multi-Stage Injection Molding
Learning about multi-stage injection molding surprised me with its precision in syringe production4. Every millimeter matters here. This technique lets us control speed and pressure during different phases of the molding process. Syringes must meet top standards of quality and reliability.
Ensuring Uniform Wall Thickness
A syringe looks simple, but it needs precise design. I remember a project where tiny changes in wall thickness could weaken the syringe. Initially, a lower injection speed fills the end of the mold cavity gently, preventing marks that spoil the product. Increasing speed then helps efficiency in filling the main cavity. Slowing down before full completion prevents overflow, keeping dimensions tight and appearance perfect.
Injection Speed Control: Key Phases
Phase | Speed | Purpose |
---|---|---|
Initial Phase | Low | Prevent defects such as jet marks |
Main Filling Phase | Increased | Enhance production efficiency |
Final Phase | Reduced | Avoid overflow and ensure dimensional control |
Quality Assurance and Safety
Changing speed and pressure at each step is crucial for even thickness in the syringe barrel. By adjusting parameters like speed and pressure through different stages, multi-stage injection molding ensures uniformity, which is vital for maintaining strength and ensuring safe operation during medical procedures. I once used this method to cut material waste, directly affecting manufacturing costs5 positively.
Enhancing Production Efficiency
This technique raises efficiency, cutting costs and time without losing quality. Increased efficiency in syringe production not only reduces costs but also minimizes cycle times. I’ve seen how precise speed adjustments keep production rates high, essential for meeting large-scale demands in the medical industry.
Overall, multi-stage injection molding really changes syringe production by improving quality, safety, and efficiency. This offers an advantage in making complex medical devices with strict quality standards. Exploring these techniques in medical device manufacturing6 can be very enlightening.
Multi-stage injection molding prevents syringe defects.True
By controlling speed and pressure, it minimizes defects like jet marks.
Uniform wall thickness is irrelevant in syringe production.False
Uniform thickness is crucial for strength and functionality of syringes.
Why is Multi-Stage Injection Crucial for Infusion Set Components?
Ever thought about why those small medical tools work so well?
Multi-stage injection plays a key role for infusion set parts. It carefully controls how fast and how hard the injection happens. This control leads to uniform products. This process cuts down on mistakes. The outcome is better quality and safe products used in medicine. Product quality is very important.

Understanding Multi-Stage Injection
I recall walking into a busy manufacturing plant for the first time. The machines hummed rhythmically, filling the air. Awe and curiosity surrounded me. Multi-stage injection molding fascinated me the most. It acts like an orchestra conductor, controlling speed and pressure of injection7. Different stages create complex shapes with great accuracy. Precision is essential in the medical field.
Stage | Function |
---|---|
Initial Stage | Low-speed injection to fill the mold smoothly |
Main Filling Stage | Increased speed for efficiency |
Final Stage | Reduced speed for accuracy and quality control |
Application in Infusion Set Components
My work with medical components showed the need for even wall thickness in infusion sets, like droppers or connectors. Imagine pouring syrup evenly on a pancake. The multi-stage process is similar: it starts slow, speeds up, then slows to prevent overflow. Uniformity in components remains critical in healthcare.
Benefits of Multi-Stage Injection
- Precision: Speed and pressure adjustments let each part fit perfectly.
- Safety: Fewer defects reduce risks during medical procedures.
- Efficiency: This method increases production while keeping quality high.
Examples in Practice
Reflecting on my experiences, it’s akin to crafting a fine art piece. With droppers, low-speed injection lets melt flow in smoothly. Speed increases for quick filling and pressure stays low during cooling to avoid shrinkage. Connectors need varied speeds for different thicknesses; this maintains structural strength.
Going beyond, multi-stage injection8 is not just about creating objects; it’s about precision. Syringe production or filter housing molding demonstrate its potential. This method gives more control and flexibility compared to older methods.
Using multi-stage injection molding helps meet strict medical standards. This approach promotes patient safety and improves treatment effectiveness. It not only enhances reliability but also streamlines production processes, making it an indispensable part of modern healthcare manufacturing.
Multi-stage injection reduces defects in infusion sets.True
The process controls speed and pressure, preventing issues like jet marks.
Uniform wall thickness is not crucial for droppers.False
Uniform wall thickness ensures structural integrity and prevents leaks.
How does multi-stage injection enhance medical packaging quality?
Did you ever really notice the beauty of a well-made medical syringe for the first time? The exactness and quality amazed me. Multi-stage injection molding contributes much to this perfection.
Multi-stage injection molding greatly improves the quality of medical packaging. This process carefully controls the speed and pressure of the injection. Packaging ends up with walls of even thickness. The sealing becomes better. It also reduces the stress inside products like syringes and infusion sets. Products like syringes and infusion sets benefit from this reduction in stress.
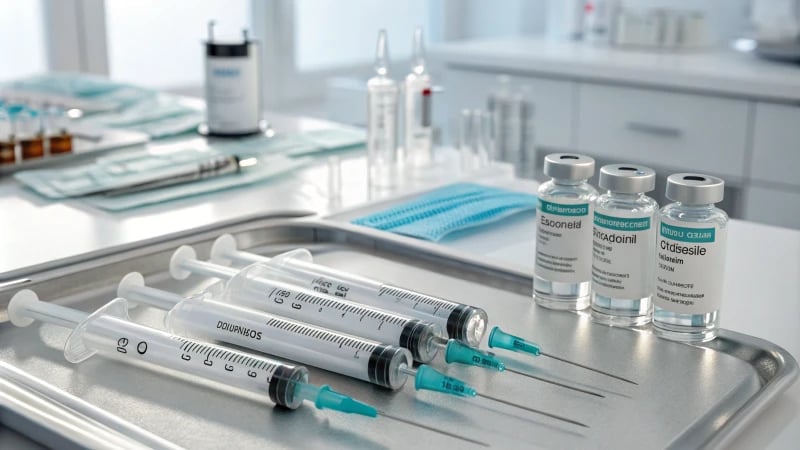
Precision in Syringe Production
In my early days of product design, I was really surprised by how precise a syringe needed to be. Multi-stage injection helps control speed and pressure at different times. Starting slow causes the plastic to fill the mold very evenly, stopping annoying defects. When the mold is almost full, speed increases for fast filling, then it slows down for a perfect finish. This produces syringes with uniform wall thickness. Very safe and very strong syringes.
Optimizing Infusion Set Components
Working on an infusion set, I found wall thickness to be really important. Multi-stage injection allowed adjustments during molding. Droppers, for example, need thin, even walls. Beginning with a slow injection speed lets the material enter smoothly and then, by upping the speed, the filling becomes faster. This method keeps droppers clear, accurate and reliable. Safe use is very crucial.
Advancing Medical Packaging Production
Medical packaging must be excellent to protect what’s inside. Multi-stage injection fine-tunes plastic flow, leading to even wall thickness in bottles and tubes. This strengthens their sealing ability and pressure resistance. Adjustments also reduce stress, avoiding deformation. It keeps all drugs and reagents really safe.
Component | Key Benefit | Injection Stage |
---|---|---|
Syringe | Uniform wall thickness | Slow start, fast middle |
Infusion set dropper | Even thin walls | Gradual speed increase |
Packaging bottles | Improved sealing | Precise flow control |
Complex Medical Filter Housing
Filter housings opened my eyes. They have very complex structures. Multi-stage injection lets us manage speed and pressure based on thickness and shape. Low speeds avoid defects in thin areas; higher speeds cover thick areas fully, preventing material shortages and bubbles. This method ensures filters are high quality and perform well.
Enhancing Medical Equipment Shells
I helped design a medical monitor shell that needed both beauty and strength. Multi-stage injection allowed speed adjustments to match the shell’s structure. Slow speeds preserved details on edges while faster speeds improved efficiency without losing strength. This technique gave a good-looking and tough shell that withstands hard use with ease.
Understanding multi-stage injection9 probably helps in better product design and manufacturing, especially in the medical field.
Multi-stage injection ensures uniform syringe wall thickness.True
The process controls speed and pressure, ensuring uniformity in wall thickness.
Multi-stage injection reduces internal stress in medical packaging.True
Precise control over plastic flow reduces stress, preventing deformation.
How Does Multi-Stage Injection Enhance Medical Equipment Shells?
Have you ever thought about how the outer parts of medical devices reach such precise quality and strength?
Multi-stage injection molding is important for creating medical equipment shells. This technique carefully adjusts speed and pressure during the injection process. It provides consistent results. It results in strong products. It creates attractive surfaces. These qualities meet the strict demands of the medical field. These are really high standards.
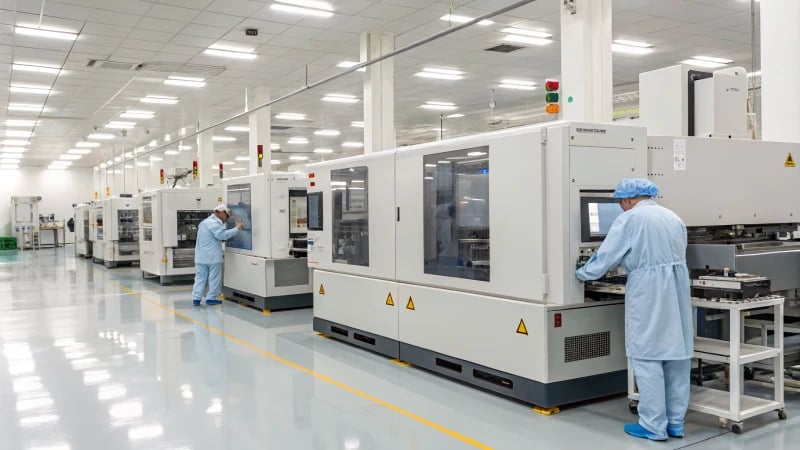
Understanding Multi-Stage Injection in Medical Equipment Manufacturing
Picture crafting a delicate sculpture. Every move must be precise. Multi-stage injection molding is similar. We adjust injection speed and pressure at different times, much like changing paintbrush pressure to create varied textures. This is very useful with complex medical equipment cases10. Fine-tuning each stage achieves amazing accuracy and high quality.
Injection Stage | Speed Setting | Pressure Setting | Purpose |
---|---|---|---|
Initial Filling | Low | Moderate | Prevents defects like jet marks |
Main Filling | High | High | Enhances production efficiency |
Final Filling | Low | Moderate | Ensures dimensional accuracy and avoids overflow |
Applications in Syringe Production
Syringe manufacturing is like solving a puzzle. It seems simple, but precision is important. We start slowly to fill the mold without marks. Then, increase the pace for efficiency. Near full, we slow again to control properly. This checks and perfects wall thickness11. It’s all about safety and strength.
Infusion Set Component Manufacturing
Creating droppers and connectors feels like conducting music. Every part adds to the piece. Slowly starting lets the melt flow well. A quick increase fills it completely. Finally, we reduce speed to keep everything equal and clear, avoiding marks and keeping size true for dimensional accuracy12.
Enhancing Medical Packaging
Protecting valuable contents is key in medical packaging. Controlling melt flow with multi-stage injection gives even wall thickness, which leads to better resistance and sealing. Adjusting the process reduces internal stress, preventing failures and keeping drugs safe for longer through improved drug protection13.
Impact on Medical Filter Housing
Complex filter housings caught my interest on first try. Multi-stage injection helps here by ensuring lower speeds fill thin parts smoothly while faster speeds ensure thicker parts form right, preventing material gaps and bubbles—enhancing the filter’s quality14 and performance.
Medical Equipment Shell Manufacturing
Making large device shells is like crafting art—a beautiful look and strong structure must align. Multi-stage injection lets us change settings for each part’s needs: slow speed improves edges while medium or high speeds improve larger sections resulting in shells with excellent appearance quality15 and long-lasting strength.
By setting injection parameters precisely, multi-stage molding changed how medical equipment shells are made—products meet strict safety and function standards, something I am very proud of.
Multi-stage injection prevents jet marks in medical shells.True
Initial low-speed injection reduces flow velocity, minimizing surface defects.
High-speed injection decreases efficiency in syringe production.False
High speed enhances efficiency by filling molds quickly during the main stage.
Conclusion
Multi-stage injection molding enhances medical device manufacturing by ensuring precision, reducing defects, and improving material properties, crucial for producing high-quality syringes, infusion sets, and medical packaging.
-
Exploring this can help understand how precise control leads to better product quality. ↩
-
Learn how this technique enhances packaging quality and longevity. ↩
-
Understanding the role of structural integrity can highlight the importance of manufacturing precision. ↩
-
This link explores various precision techniques used in syringe manufacturing, crucial for understanding how quality is achieved. ↩
-
Understand strategies for reducing costs in medical device production, helping businesses maintain profitability. ↩
-
Discover practical applications of this technique in the industry to see its benefits in action. ↩
-
Learn about precise control mechanisms in multi-stage injection molding that ensure consistent quality. ↩
-
Discover various applications of multi-stage injection molding in producing medical devices. ↩
-
Explore how multi-stage injection molding benefits medical device manufacturing with precision improvements. ↩
-
Explore how multi-stage injection molding enhances production efficiency and quality in medical equipment manufacturing. ↩
-
Learn why maintaining uniform wall thickness is critical for syringe functionality and safety. ↩
-
Discover how this technique achieves precision in manufacturing complex medical components. ↩
-
Understand how it improves the sealing and stability of medical packaging. ↩
-
Find out how it enhances the quality and performance of medical filter housings. ↩
-
Learn how multi-stage injection molding refines the aesthetic quality of equipment shells. ↩