Ever wondered how to consistently churn out flawless products in injection molding? It’s all about mastering quality control.
Effectively monitor and control post-injection molding quality by employing robust quality assurance protocols, using real-time data analytics for process oversight, and practicing continuous improvement to promptly identify and rectify defects, ensuring high-quality outputs.
In my early days at the factory, I learned that just knowing the basics wasn’t enough. There’s a world of advanced techniques out there that can really elevate your production game. Let me share some insights and methods that have transformed how I approach injection molding, ensuring every product meets my high standards.
Real-time data analytics improve defect detection.True
Real-time data analytics allows for immediate identification and correction of defects.
Quality assurance protocols eliminate all defects.False
While they reduce defects, quality assurance protocols cannot eliminate all errors entirely.
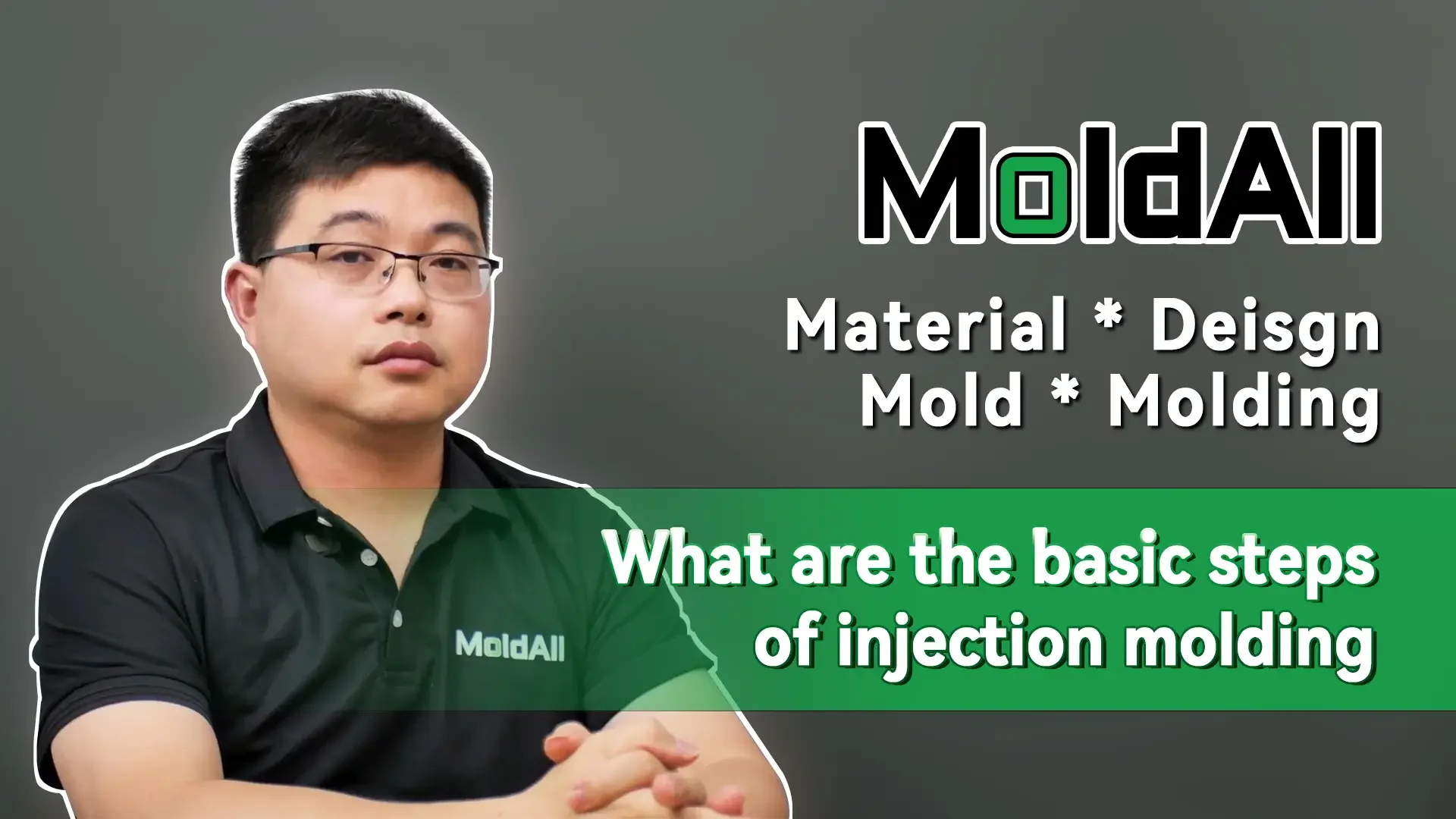
- 1. What Are the Key Quality Assurance Checks in Injection Molding?
- 2. How Can Data Analytics Enhance Injection Molding Quality Control?
- 3. What Are Common Defects in Injection Molding and How to Address Them?
- 4. How Do Continuous Improvement Practices Boost Qualified Rates?
- 5. How Does Operator Training Elevate Quality Control?
- 6. Conclusion
What Are the Key Quality Assurance Checks in Injection Molding?
Ever wondered how injection molding ensures top-notch quality every time? Let me walk you through the crucial checks that keep this process on point.
Key quality assurance checks in injection molding include dimensional verification, visual inspections, mechanical testing, and material analysis to ensure consistency, durability, and compliance with specifications.
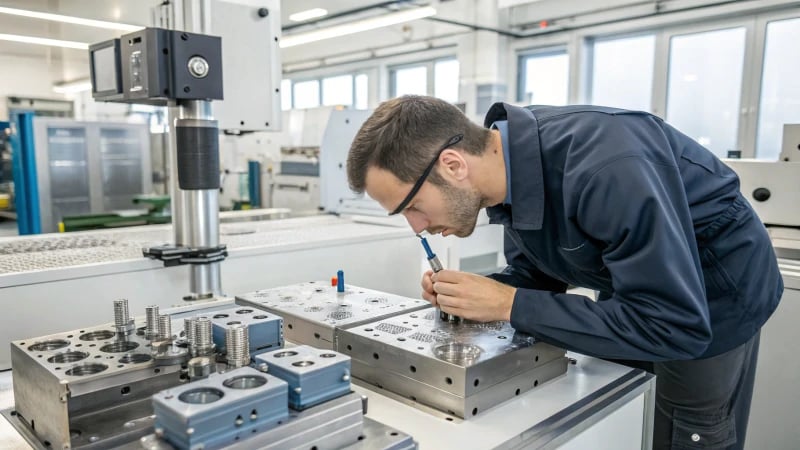
Dimensional Verification
I remember the first time I got my hands on a caliper; it was like wielding a magic wand for precision. Dimensional verification is essential in injection molding, ensuring each part perfectly matches the design specs. Whether using traditional calipers1 or sophisticated CMMs (Coordinate Measuring Machines), these tools help us keep everything within those tight tolerances.
Visual Inspections
Have you ever scrutinized something so closely that you felt like a detective on a case? That’s how I approach visual inspections. Identifying surface defects like scratches or color inconsistencies is crucial. Under just the right lighting, parts are examined to ensure they meet our high aesthetic standards. And with automated vision systems2 now, it’s like having an extra pair of eyes that never tire.
Mechanical Testing
There’s something satisfying about knowing a product can withstand whatever life throws at it. Mechanical testing does just that, putting components through their paces. From tensile tests that pull materials to their limits to impact tests simulating real-world stress, these checks reassure us of the product’s durability.
Test Type | Purpose | Common Tools |
---|---|---|
Tensile Test | Measures tensile strength | Tensile tester |
Impact Test | Evaluates impact resistance | Impact tester |
Material Analysis
Once, I thought all plastics were created equal until I dove into material analysis. It’s fascinating to see how spectroscopy and DSC (Differential Scanning Calorimetry) can tell us exactly what’s inside a material and how it behaves under heat. This ensures we’re using the right stuff for the job every time.
Process Monitoring
Imagine having a dashboard for your injection molding process. Continuous monitoring is just that—it’s like keeping tabs on every heartbeat of the operation. By tracking temperature, pressure, and cycle time with advanced sensor technologies3, adjustments can be made in real-time to maintain optimal conditions.
Understanding these key quality assurance checks isn’t just about ticking boxes; it’s about crafting reliable products that stand up to expectations—both ours and the consumers’. Each step in this meticulous process contributes to the integrity and success of the final product.
Dimensional verification uses calipers and CMMs.True
Calipers and CMMs are standard tools for measuring dimensions in injection molding.
Visual inspections only identify color variations.False
Visual inspections also identify surface defects like scratches and sink marks.
How Can Data Analytics Enhance Injection Molding Quality Control?
Ever wondered how data analytics can revolutionize injection molding quality control? Let’s dive into how this cutting-edge technology can transform your manufacturing process into a powerhouse of efficiency and precision.
Data analytics boosts injection molding quality by enabling real-time monitoring, predictive maintenance, and process optimization, reducing defects, and ensuring consistent product quality, thereby enhancing efficiency and cutting costs.
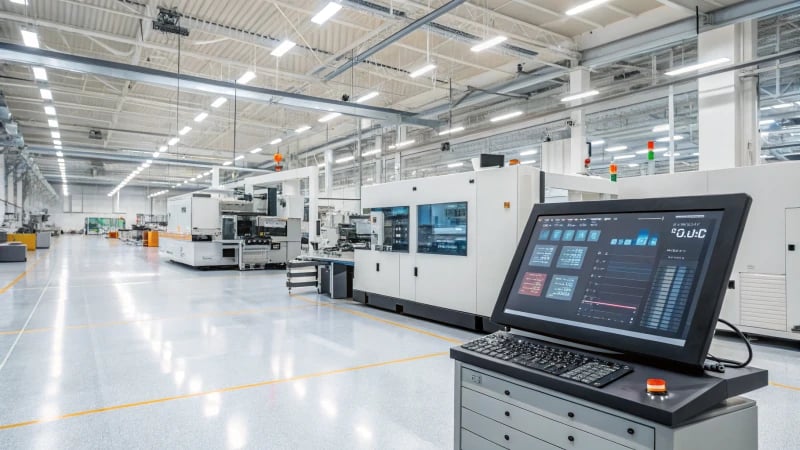
Understanding Data Analytics in Injection Molding
I remember the first time I heard about using data analytics in injection molding. It was during a casual chat with a fellow designer at a conference, and I was fascinated by the potential it had to revolutionize our industry. Essentially, data analytics involves collecting and analyzing vast amounts of production data4 to make informed decisions. Imagine having advanced algorithms at your fingertips that can detect inconsistencies early, reduce waste, and improve cycle times. This approach not only leads to enhanced product quality but also boosts operational efficiency.
Real-Time Monitoring
Picture this: you’re sipping your morning coffee while a dashboard on your screen shows the real-time status of key variables like temperature, pressure, and material flow in your injection molding process. This constant flow of information allows you to identify anomalies5 quickly and address any deviations from the norm immediately. Implementing sensors throughout the machinery gives you a bird’s eye view of the entire production process.
Parameter | Importance |
---|---|
Temperature | Affects material viscosity |
Pressure | Influences part integrity |
Material Flow | Impacts cycle consistency |
Predictive Maintenance
One story comes to mind when I think of predictive maintenance. A colleague once shared how they avoided a major production halt by using historical data to forecast when their equipment was likely to fail. With predictive maintenance algorithms, you can minimize unexpected downtime and extend machine life. By predicting maintenance needs6, interventions can be scheduled during off-peak hours, thus avoiding costly interruptions.
Process Optimization
I’ve seen firsthand how data analytics can aid in optimizing the injection molding process. By evaluating past production data, we were able to fine-tune our parameters to achieve maximum efficiency. This optimization not only reduces cycle times but also improves overall output quality. It’s like having a secret recipe for perfecting every batch.
Benefits of Implementing Data Analytics
Implementing data analytics in injection molding offers numerous benefits:
- Increased Precision: Enhanced accuracy in mold operations leads to fewer defects.
- Cost Savings: Reduced waste and optimized resource usage lower operational costs.
- Quality Consistency: Consistent monitoring ensures uniformity across production batches.
Challenges and Considerations
Of course, adopting data analytics comes with its challenges. I remember the initial setup costs being quite high, and finding skilled personnel to interpret complex data7 was a concern. However, the long-term gains in efficiency and quality made it a worthwhile investment for us.
Incorporating data analytics into injection molding is a forward-thinking strategy that can significantly enhance quality control measures by providing actionable insights and driving continuous improvement processes. Whether you’re just starting out or looking to refine your processes further, embracing this technology could be the game-changer you’ve been searching for.
Real-time monitoring detects anomalies in injection molding.True
Real-time data collection identifies deviations quickly, enhancing quality.
Data analytics in injection molding increases defect rates.False
It reduces defects by improving precision and consistency in production.
What Are Common Defects in Injection Molding and How to Address Them?
Ever stared at an injection-molded part and wondered, "What went wrong here?" Let’s dive into the common hiccups and fixes in injection molding.
Common injection molding defects include flow lines, sink marks, and weld lines. Address these by optimizing mold design, adjusting processing parameters, and selecting appropriate materials.
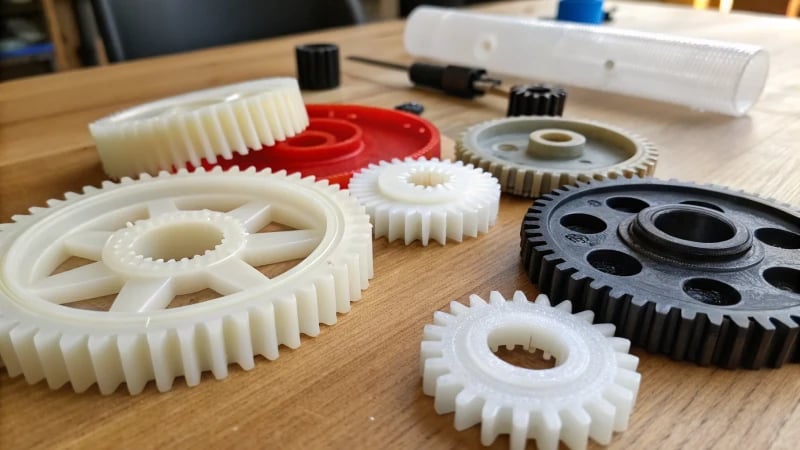
Understanding Flow Lines
I remember the first time I spotted flow lines on a piece fresh off the mold. It was like the plastic had its own artistic flair, but in the world of manufacturing, that’s not exactly desirable. Flow lines appear as streaks or patterns on the surface, usually when the plastic flows unevenly or cools at different rates.
Causes and Solutions:
- Causes: It’s often down to uneven cooling or those sluggish injection speeds.
- Solutions: Speed things up a bit with a faster injection or tweak that mold temperature. Learn more about injection speeds8.
Tackling Sink Marks
The dreaded sink marks—those pesky depressions that make a part look like it just woke up from a nap on a hard pillow. I used to think they added character, but they actually come from material shrinkage during cooling.
Causes and Solutions:
- Causes: Often, it’s thick wall sections or simply not enough cooling time.
- Solutions: Go for uniform wall thicknesses or extend that cooling period. Explore wall thickness design9.
Managing Weld Lines
Weld lines are where two flow fronts meet, and instead of a seamless merger, they leave a scar. It’s like the part has a story to tell, but one that weakens its structure.
Causes and Solutions:
- Causes: Usually, it points to poor mold design or low melt temperatures.
- Solutions: Consider modifying the gate placement or upping the melt temperature. Discover gate placement strategies10.
Material Selection
Ah, the choice of material—it’s like picking out a partner; you want one that complements your needs. The right material can significantly impact defect occurrence.
-
Considerations:
Material Type Impact on Defects ABS Prone to flow lines Polypropylene Susceptible to sink marks
Choosing wisely can mitigate potential issues and boost product reliability. Explore material properties11.
Flow lines are caused by slow injection speeds.True
Flow lines occur when plastic flows unevenly due to slow speeds.
ABS is less prone to flow lines than Polypropylene.False
ABS is more prone to flow lines compared to Polypropylene.
How Do Continuous Improvement Practices Boost Qualified Rates?
Ever wondered how some companies seem to always get it right, turning out top-notch products while others struggle? The secret often lies in continuous improvement practices.
Continuous improvement enhances qualified rates by identifying inefficiencies and implementing effective changes, fostering a culture of learning and adaptability for better performance and quality outcomes.
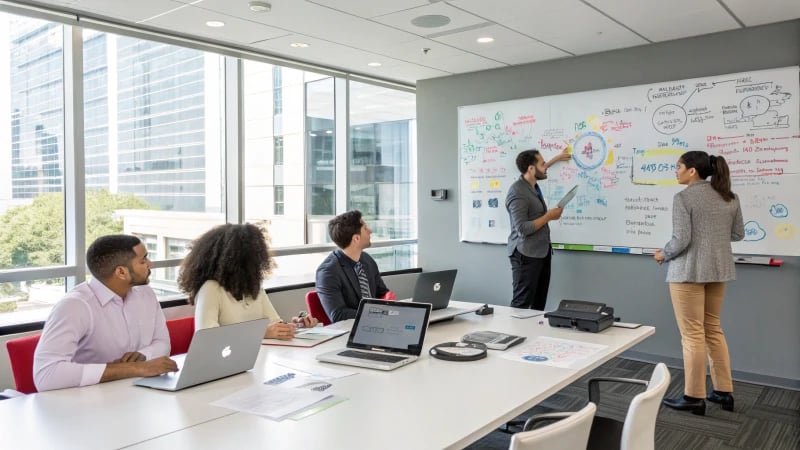
Understanding Continuous Improvement
I remember when I first got into product design, I thought big overhauls were the only way to fix problems. But then, I learned about continuous improvement and how small tweaks could make a world of difference. It’s all about those ongoing efforts to better products, services, or processes. This isn’t just about keeping things the same; it’s about constantly evolving through feedback, teamwork, and the willingness to embrace change. One of the first methodologies I encountered was Kaizen12, which taught me the importance of discipline and collaboration.
Mechanisms of Continuous Improvement
-
Identifying Inefficiencies:
I’ve sat through countless audits where we meticulously comb through processes to find what’s dragging us down. These sessions can be eye-opening and often spark ideas for streamlining operations.
-
Employee Involvement:
When I first started involving team members in the improvement process, I was blown away by their insights. Those on the frontlines often have the best ideas for removing roadblocks because they face them daily.
-
Feedback Loops:
Keeping the lines of communication open with continuous feedback has been a game-changer in ensuring improvements stick and evolve as needed.
Real-World Applications
I recall working with a manufacturing firm that decided to adopt lean management practices. They used methods like 5S13 to clean up operations, and the results were immediate—higher-quality products with fewer defects were rolling off the line.
Practice | Benefit |
---|---|
Kaizen | Encourages innovation |
Lean | Reduces waste and inefficiencies |
Six Sigma | Improves process quality |
Benefits in Performance Reviews
Continuous improvement doesn’t just stop at product quality; it’s also about how we grow as professionals. By setting clear goals and reviewing progress regularly, I found that we can align personal achievements with company goals. This kind of alignment boosts accountability and motivation in ways I never imagined.
Implementing Continuous Improvement
Starting small was key for me when I began implementing these practices:
- Start Small: Begin with manageable changes that fit seamlessly into what you’re already doing.
- Training: Offering training in methodologies like Six Sigma or Agile14 was instrumental in getting everyone on the same page.
- Leadership Support: Having leaders who are committed to this process is crucial. Their buy-in can drive the momentum needed for real change.
Reflecting on my journey, it’s clear that embracing continuous improvement has not only made me a better designer but has also enriched our team culture, driving us toward excellence every day.
Kaizen emphasizes large overhauls for improvement.False
Kaizen focuses on small, incremental changes rather than large overhauls.
Lean management reduces waste in manufacturing processes.True
Lean management practices aim to streamline operations by reducing inefficiencies and waste.
How Does Operator Training Elevate Quality Control?
Ever wonder how crucial training is in keeping your product’s quality top-notch?
Operator training enhances quality control by enabling operators to detect defects, comprehend machinery, and follow standards, thus minimizing errors and improving consistency.
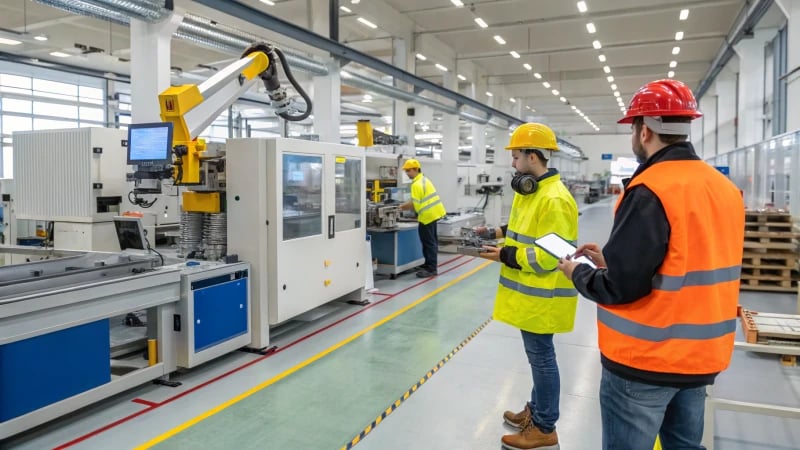
Understanding the Importance of Operator Training
I’ve seen firsthand how operator training can make or break product consistency and defect minimization. Skilled operators act like sentinels on the production line, catching potential issues15 before they snowball into costly problems. Imagine an operator who can see a subtle misalignment in a mold that could ruin hundreds of units if unnoticed. This proactive vigilance doesn’t just enhance product quality but also pumps up production efficiency.
Impact on Operational Efficiency
I recall my early days when handling machinery felt like navigating a complex maze. Proper training transformed that feeling of uncertainty into mastery. A well-trained operator, much like myself now, can troubleshoot with a kind of sixth sense, swiftly resolving hiccups and keeping the wheels of production turning smoothly. This translates to higher throughput and better resource utilization, which any manager would celebrate.
Before Training | After Training |
---|---|
Frequent errors | Fewer errors |
High downtime | Reduced downtime |
Inconsistent quality | Consistent quality |
Cost-Benefit Analysis
Initially, the cost of training might feel like an extra burden, but it’s akin to investing in a sturdy foundation for a house. The long-term savings from reduced waste and rework far outweigh the initial expense. Think about how the cost of a single defect can ripple through production. By benchmarking16 training outcomes against industry standards, companies can tangibly see the payoff.
Enhancing Quality Standards
In my journey, staying updated with industry regulations was crucial. Training programs that include the latest regulatory updates empower operators to adapt quickly and ensure compliance, sparing us from unnecessary fines and reputational setbacks. Regular feedback loops17 and assessments have been game-changers for me, allowing continuous refinement of skills and closing any knowledge gaps promptly. This cycle of improvement is vital for sustaining high-quality standards over time.
Operator training reduces product defects.True
Training equips operators to spot and address issues early, reducing defects.
Training increases production downtime.False
Proper training minimizes downtime by enabling quick issue resolution.
Conclusion
Mastering quality control in injection molding involves robust protocols, real-time data analytics, and continuous improvement practices to ensure defect-free products and optimize production efficiency.
-
Calipers are essential tools for precise dimensional measurements, critical for maintaining quality in injection molding. ↩
-
Automated vision systems enhance inspection efficiency by quickly identifying surface defects in molded parts. ↩
-
Advanced sensors provide real-time data for process optimization, crucial for maintaining quality control in injection molding. ↩
-
Discover how analyzing production data can refine injection molding processes by identifying inefficiencies and enhancing quality control. ↩
-
Learn techniques for detecting anomalies in injection molding to ensure consistent product quality. ↩
-
Explore how predictive maintenance can reduce downtime and extend machinery lifespan. ↩
-
Gain insights into interpreting complex data sets to enhance manufacturing processes. ↩
-
Adjusting injection speed can prevent flow lines, improving part appearance. ↩
-
Uniform wall thickness helps reduce sink marks, enhancing structural integrity. ↩
-
Proper gate placement minimizes weld lines, increasing part strength. ↩
-
Understanding material properties aids in selecting the right plastic to avoid defects. ↩
-
Discover how the Kaizen methodology can promote teamwork and innovation within your organization. ↩
-
Learn how the 5S methodology can help streamline operations and reduce waste. ↩
-
Explore how Agile methodologies can enhance flexibility and responsiveness in business processes. ↩
-
Explore how skilled operators proactively identify issues, ensuring production quality remains high and defect rates low. ↩
-
Learn how organizations measure training effectiveness by comparing outcomes with industry benchmarks. ↩
-
Discover why incorporating feedback loops in training is vital for continuous improvement and skill refinement. ↩