Have you ever wondered why some plastic pieces don’t come out correctly?
Mold underfilling occurs when plastic does not completely fill the mold during injection molding. Slow injection speeds might be a cause. Low pressure might be another cause. Poor mold design might also contribute. Resolving these problems prevents defects. This prevention guarantees high-quality production. High-quality products are essential.
Understanding why molds do not fill completely is just the start. I recall my first experience with this problem – a hectic day at the factory when we puzzled over why parts were flawed. Examining every factor showed chances for better processes. The next sections explain each element, providing deep insights into fixing and improving molding operations well.
Injection speed affects mold filling completeness.True
Slow injection speeds can cause the melt to solidify early, leading to incomplete filling.
High material viscosity improves flow in molds.False
High viscosity reduces fluidity, making it harder for the melt to fill the mold.
- 1. How Do Injection Parameters Affect Mold Underfilling?
- 2. How Can Mold Design Impact Filling Efficiency?
- 3. Why are material properties critical in preventing underfilling?
- 4. How can I enhance my injection molding process?
- 5. How Can Technology Assist in Detecting and Preventing Underfilling?
- 6. Conclusion
How Do Injection Parameters Affect Mold Underfilling?
Ever thought why that beautifully designed plastic piece ended up not quite right? Those small details in injection settings matter a lot.
Injection parameters hold a crucial role in mold underfilling. They influence how the plastic melt flows and cools. Key elements such as speed, pressure and volume need careful adjustments. Every corner of the cavity needs to be filled. Every corner.
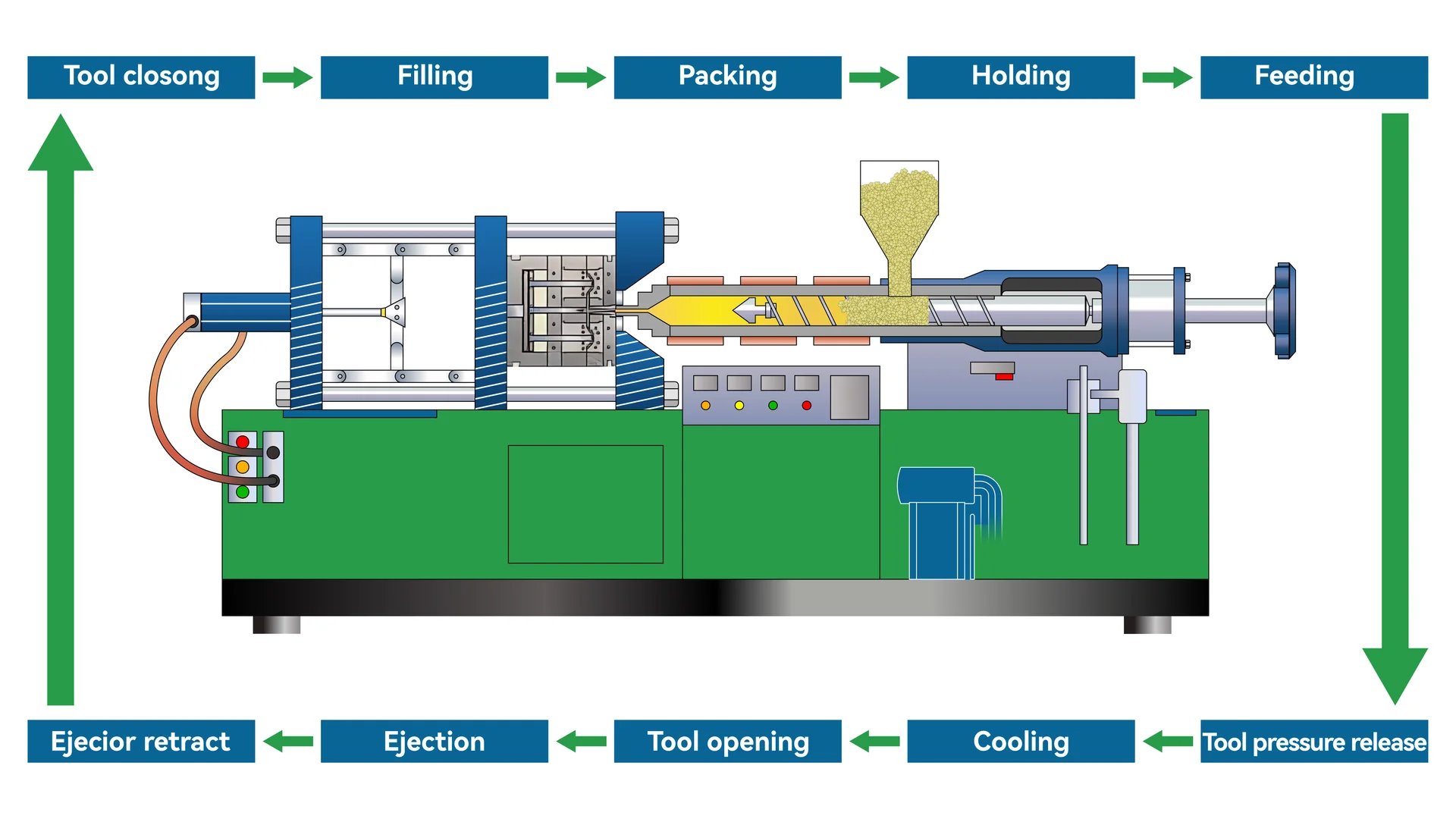
The Importance of Injection Speed
I remember my first days with injection molding and how frustrating underfilled molds were. You think everything is correct, but the product lacks shape or strength. I learned how vital adjusting injection settings is.
Injection speed became very important when working on lightweight electronic cases. We made thin-walled items, and slow speed cooled the melt too soon, leaving the mold incomplete. Precision mattered; changing speed really solved the problem. For more details on this, see thin-walled products1.
The Effect of Injection Pressure
Pressure was another challenge. In a project with complex runner systems and small gates, the melt wouldn’t move properly. Increasing pressure helped it flow correctly. This taught me pressure is vital to overcome resistance and fill the mold completely.
Parameter | Impact on Mold Filling |
---|---|
Injection Speed | Influences cooling and solidification time |
Injection Pressure | Overcomes flow resistance |
Injection Volume | Ensures enough material fills the cavity |
Understanding Injection Volume
Volume caused issues too. We did not adjust the injection stroke after changing molds, leading to less material than needed. This underfilling showed the importance of matching volume to the mold cavity’s needs.
Material Properties Impact
Material properties must not be ignored. High viscosity materials, like plastics with glass fibers, need careful temperature and speed control to avoid underfilling. It is interesting how small changes in settings can make the process smooth. Learn more about glass fiber-filled plastics2.
Optimizing Parameters for Success
Careful attention to each setting and its effect on mold filling is crucial. Adapting the settings to the material and mold design helps in reducing underfilling chances. Learning about mold design’s impact on filling3 provides extra insight into injection setting adjustments.
Injection speed impacts mold filling efficiency.True
Slow injection speed can cause the melt to cool before filling, leading to underfilling.
High material viscosity ensures better mold filling.False
High viscosity reduces fluidity, increasing the risk of underfilling in molds.
How Can Mold Design Impact Filling Efficiency?
Curiosity about how injection molding operates is common. Mold design starts the process. This step is vital. Mold design helps create products smoothly.
Mold design affects how well a mold fills. Gate placement, runner system and air vents matter. Good molds help the melt flow evenly. Products then fill properly. This increases product quality.
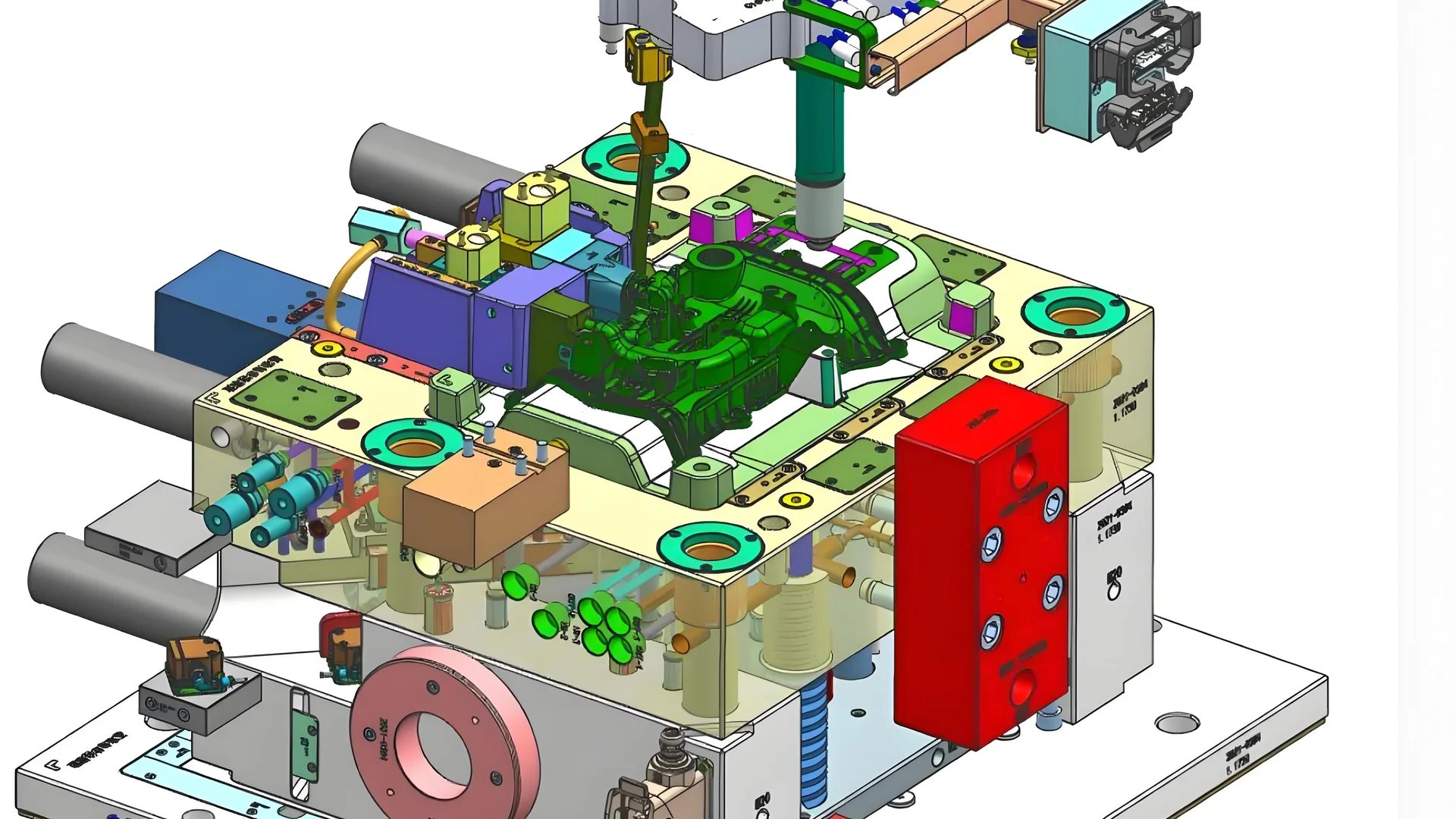
The Role of Gate Design
Imagine pouring water into a strange-shaped cup. Pouring from one spot might miss edges or spill over. This is like gate placement in mold design. Once, I worked on a project with detailed plastic parts. We placed gates too far from thin parts, leading to uneven filling. Adjusting gates fixed the issue, and production became smoother.
Table: Impact of Gate Size and Position
Gate Design Aspect | Potential Impact on Filling |
---|---|
Large gate size | Improved melt flow |
Small gate size | Limited flow, potential underfill |
Optimal gate position | Uniform cavity filling |
Runner System Design Considerations
Think about sipping a thick milkshake through a tiny straw. Annoying, right? Long or thin runners in mold designs slow melt flow. I had a mold with a long runner; the melt cooled4 too much before reaching the end, increasing thickness and complicating filling.
Example: Cold Runner Systems
We had a cold runner design that was too long. The melt lost heat fast, like a smoothie turning into sludge. We redesigned the runner to reduce resistance and improve filling speed.
Importance of Adequate Air Venting
Consider baking. If steam can’t escape, pies puff up or crack. In molds, without good air venting, air pockets block melt flow. I dealt with a deep mold lacking vents; trapped air created back pressure like squeezing toothpaste from a closed tube.
Enough vent slots let air escape efficiently, allowing the melt to spread evenly throughout the cavity.
Material Properties’ Influence
Materials with high viscosity are like honey through a narrow funnel—hard! These need more pressure and speed to fill effectively. We switched to engineering plastics for a project; injection settings changed significantly to suit the new material’s properties.
Understanding these factors helped me choose wisely and really improved filling efficiency and product quality.
Slow injection speed leads to underfilled molds.True
Slow speed causes the melt to cool before filling the cavity.
High viscosity materials improve mold filling efficiency.False
High viscosity reduces fluidity, increasing the risk of underfilling.
Why are material properties critical in preventing underfilling?
Have you ever thought about how mold filling works like magic? Explore the realm of material qualities and learn why they are the silent champions in stopping underfilling.
Material qualities, especially thickness and heat, are key in stopping underfilling. Thick material flows less. Cool temperatures make melting harder, causing incomplete mold filling. Controlling these qualities is important. Mold needs to fill properly.
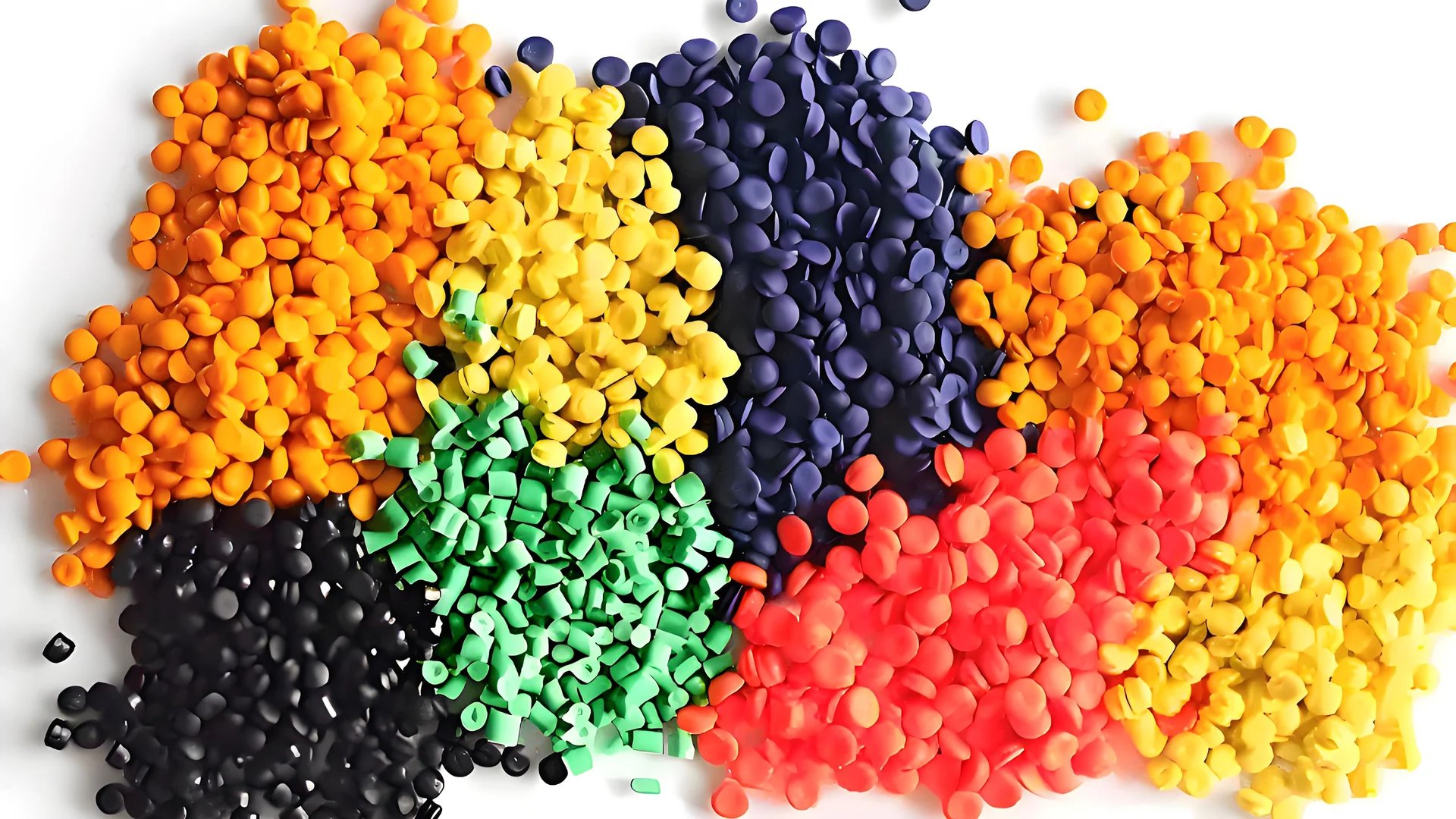
Understanding Viscosity and Its Impact
Ever tried to pour honey on a chilly morning? It doesn’t flow smoothly, right? High-viscosity materials act the same during mold filling. My first encounter with engineering plastics containing glass fibers proved challenging. Regular settings weren’t enough. Injection pressure5 and speed had to rise to move that stubborn material.
Temperature: A Key Factor
Temperature is crucial here too. Try spreading cold butter on toast – it’s tough, isn’t it? When thermoplastics aren’t warm enough, they become hard to handle, causing incomplete molds. I once forgot to change the temperature setting after switching materials. That day taught me patience and accuracy. It was quite the lesson.
Material | Ideal Temperature Range | Viscosity Level |
---|---|---|
ABS | 210°C – 250°C | Medium |
PC | 250°C – 320°C | High |
Influence of Material Composition
Material composition resembles a hidden puzzle piece. Fillers in materials increase thickness, complicating their use. It’s similar to cooking with more ingredients – they might improve the dish but also make it more complex.
Understanding these compositions helps in selecting suitable injection parameters6 to avoid underfilling.
Examples and Case Studies
- Case 1: I remember a project with a thick polymer that didn’t fill the mold completely. We fixed it by adjusting injection speed and pressure. The relief was immediate!
- Case 2: Another time, the wrong material temperature led to incomplete filling. Changing the heat settings improved the situation remarkably.
Reviewing different case studies7 helps in finding practical solutions to these issues. Handling materials with care prevents defects and achieves the best mold filling.
Learning about new materials and technologies is an ongoing journey, one I’ve really embraced in my work.
Injection speed affects mold filling efficiency.True
Slow injection speeds prevent complete mold filling, causing underfilling.
High material viscosity enhances mold fillability.False
High viscosity reduces flowability, hindering complete cavity filling.
How can I enhance my injection molding process?
Have you ever stood near an injection molding machine, puzzled about how small changes could improve its performance? I have experienced that feeling. These tricks might really assist you.
Injection molding gets better by focusing on injection speed and pressure. Mold design needs careful thinking, like where to place gates. Materials should have the right viscosity and temperature.
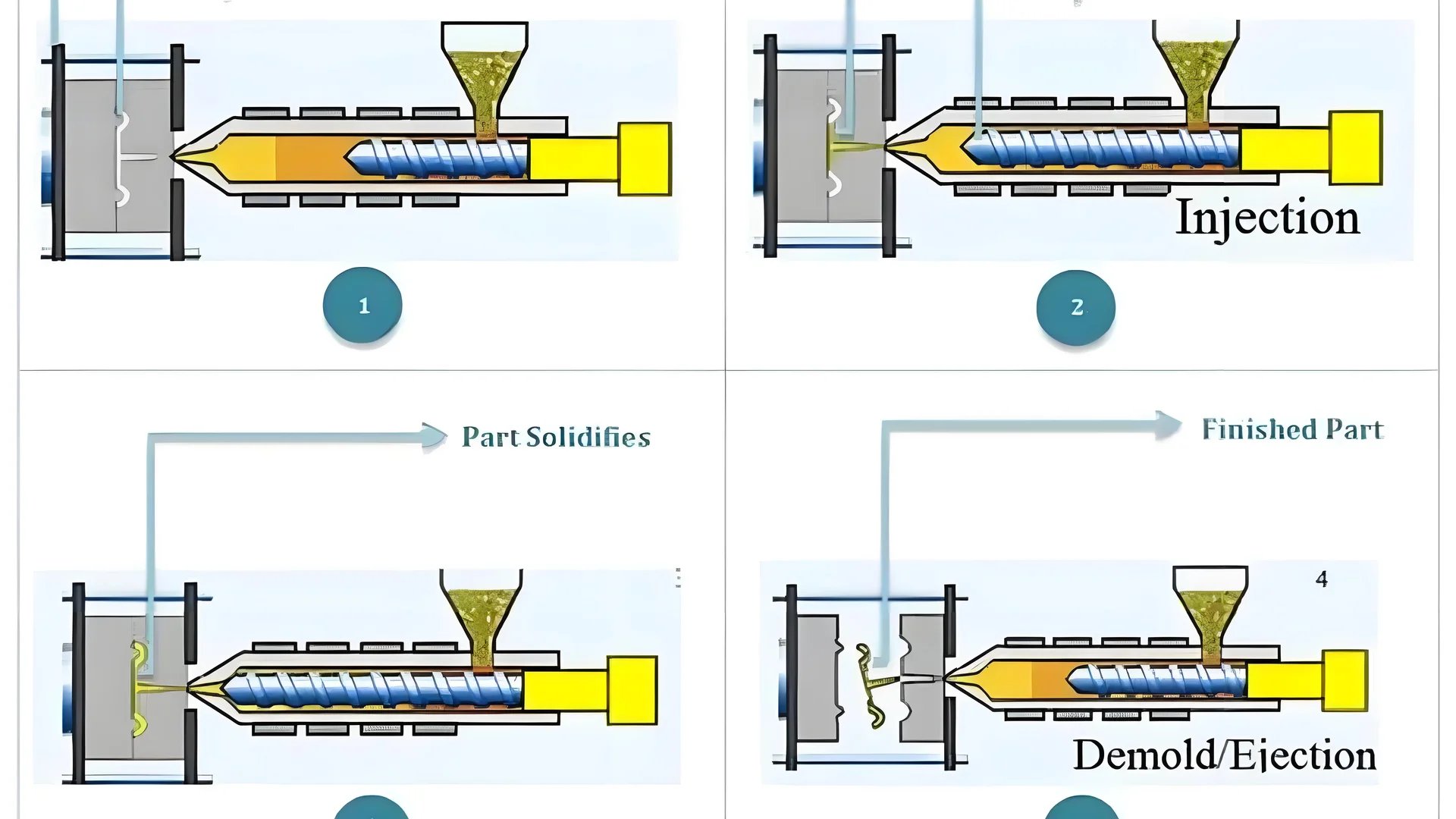
Adjusting Injection Parameters
The first time I stood by an injection molding machine, I noticed that the right settings matter a lot. Think of pouring syrup on pancakes. If it’s too slow, the syrup cools down before spreading – frustrating, right? That’s similar to having a slow injection speed. Thin-walled parts8 need quick injection to avoid turning solid too soon.
Consider the injection pressure as well. It’s like trying to squeeze toothpaste from a nearly empty tube. It needs just the right push. Without enough pressure, the melted material doesn’t flow well through complex mold designs.
Parameter | Issue | Solution |
---|---|---|
Speed | Too slow | Increase speed |
Pressure | Insufficient | Boost pressure |
Volume | Too low | Adjust injection volume |
Improving Mold Design
Designing a mold feels like solving a puzzle. If a piece or a gate is misplaced, the entire picture falls apart. Proper gate placement helps the liquid plastic flow smoothly—no roadblocks allowed!
Gates are only part of the story. The runner system is the highway for the plastic. If it’s too long or has many bumps, things slow down, causing issues. Imagine filling a balloon with a tiny hole; it’s why good air venting is important to prevent pressure build-up.
Improving air venting by adding exhaust slots can prevent back pressure from trapped air, ensuring full cavity filling. Explore more about venting techniques9 that enhance mold filling efficiency.
Changing Material Properties
I once handled a thick material, like pouring cold honey. High-viscosity materials need extra pressure and speed to fill every part of the mold.
Temperature is also crucial. If too cool, even the most fluid thermoplastics become stubborn. Keeping a good temperature helps things run smoothly.
For plastics filled with glass fibers, consider temperature adjustments10 to facilitate easier flow during injection.
Using these strategies probably helps improve your process. Intricate designs come out well and defects stay away.
Injection speed affects mold filling success.True
Injection speed impacts the ability of plastic melt to fill the mold cavity.
High material viscosity improves mold filling.False
High viscosity reduces fluidity, making it harder to fill molds effectively.
How Can Technology Assist in Detecting and Preventing Underfilling?
Have you ever thought about how technology saves your production line from the problem of underfilling? Dive into the technology changing precision in manufacturing.
Technology helps find and stop underfilling problems. It uses smart sensors, AI programs and careful control systems. These devices adjust injection settings and improve mold design. They also change material properties. Product quality really benefits.
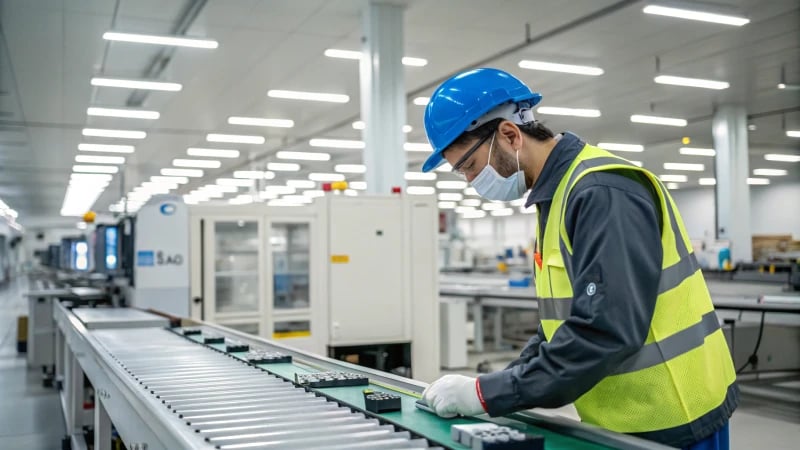
Optimizing Injection Settings
In my early days of working in manufacturing, intuition and manual checks helped us avoid underfilling. But now, everything has changed with new technology. Modern injection machines have sensors and smart software that do the hard work. These systems watch and change injection settings quickly. For example, they keep the injection speed right, stopping early cooling in thin pieces, which was often a big problem before.
- Control of Injection Speed: Imagine the trouble with plastic that cools too soon and doesn’t fill the mold. Sensors stop this by controlling speed.
- Pressure Control: Keeping good pressure is key, especially for tricky mold shapes. Technology now gives the exact push needed.
- Volume Precision: Automatic systems set the volume perfectly, ensuring the screw size matches the mold space.
Improving Mold Structure
I used to draw mold designs on paper. Now, CAD software has changed this process, letting me test and study flow before cutting metal. Technology lets us improve mold designs greatly.
Mold Design Element | Technological Solution |
---|---|
Gate Fine-Tuning | Simulation Software |
Efficient Runner Systems | Flow Analysis Tools11 |
- Gate Fine-Tuning: It feels like a puzzle – checking flow to make sure the melt spreads evenly.
- Efficient Runner Systems: Improvements help reduce resistance with smoother surfaces and better sizes.
Changing Material Properties
Guessing material behavior was common for me before. Not anymore. Tools like rheometers now show us viscosity changes, really important for setting temperatures for materials like glass-filled plastics.
- Material Temperature Control: Sensors adjust temperatures quickly to keep flow perfect.
- Handling Viscosity: Smart algorithms predict changes so we can adjust early.
These innovations not only stop underfilling – they improve product quality by lowering defects and waste. These technologies probably made our production more trustworthy and cheaper to run. Check more about material property changes12 for competitive advantage.
Using these technologies, I’ve watched manufacturers reduce underfilling, keeping quality consistent and meeting standards. Each tool is really important for keeping fill levels right in many manufacturing scenarios.
Injection molding developments13 keep growing, bringing new chances for exactness and creativity in creating and producing products.
Slow injection speed leads to mold underfilling.True
A slow injection speed allows the melt to cool and solidify prematurely.
High material viscosity improves mold filling efficiency.False
High viscosity reduces fluidity, making it harder to fill molds effectively.
Conclusion
Mold underfilling occurs due to slow injection speed, insufficient pressure, and poor design. Understanding these factors helps prevent defects and ensures high-quality plastic production.
-
Learn about ideal injection speeds to prevent underfilling in thin-walled products, which are prone to cooling quickly. ↩
-
Discover specific challenges and solutions for molding high viscosity materials like glass fiber-filled plastics. ↩
-
Gain insights into how mold design considerations influence the filling process and impact product quality. ↩
-
Explore how different gate designs influence melt flow and overall mold filling efficiency. ↩
-
Explore how varying injection pressure impacts mold filling efficiency and addresses issues like high viscosity. ↩
-
Understand the role of injection parameters in preventing defects like underfilling in molding processes. ↩
-
Explore real-world examples demonstrating the impact of material properties on manufacturing outcomes. ↩
-
Understanding the impact of injection speed can help you optimize production of thin-walled plastic products. ↩
-
Learn about advanced venting techniques that improve mold filling efficiency and reduce defects. ↩
-
Explore how adjusting material temperature can aid in processing high-viscosity plastics effectively. ↩
-
Learn about tools that enhance mold design by simulating melt flow dynamics. ↩
-
Explore how technology adjusts material properties to prevent underfilling. ↩
-
Stay updated on the latest technological innovations in injection molding. ↩