Have you ever thought about how the thickness of a mold transforms a product completely? Thickness matters. It alters shape and strength. A thicker mold increases durability. Durability is important. A thinner mold allows more flexibility. Different products require varied levels of thickness. Understanding these differences is crucial. It really influences the final product greatly.
Mold thickness changes how fast something cools. It also impacts the size and shape of products. Thicker molds cool slowly. This delay affects precision. Mistakes like warping might occur. Changing mold thickness is important. It is really crucial for good product quality.
I remember when I first learned about the importance of mold thickness. It was like discovering a secret for better product quality. Different thicknesses change how a product cools and its final size. For instance, in one project, a thicker mold slowed the cooling. We had to wait longer. This showed me how even a few extra millimeters could impact size accuracy and cause warping.
Once, I dealt with issues in thicker molds due to injection pressure. We adjusted our method because the melt had trouble filling the cavity evenly. This caused uneven density. This was a big lesson for me. It affected the product’s look, like annoying silver lines on clear items.
There’s also the pressure-holding stage. I remember adjusting holding times for thicker molds. Too little time led to visible shrink marks on containers. These experiences taught me how important it is to know mold thickness for quality products. Understanding this is key. It’s really like knowing your craft deeply.
Thicker molds require longer cooling times.True
Thicker molds have a longer heat conduction path, slowing cooling.
Higher injection pressure improves product appearance.False
Excessive pressure can cause defects like flying edges and internal stress.
How Does Cooling Speed Influence Dimensional Accuracy?
Picture yourself investing hours in crafting a design, only to discover it distorted and misshapen after completion.
The speed of cooling is vital for the size accuracy of parts. Quick cooling often results in shrinkage and bending. Slow cooling helps with exact shaping. Thick molds slow the cooling process. Thickness affects the final size.
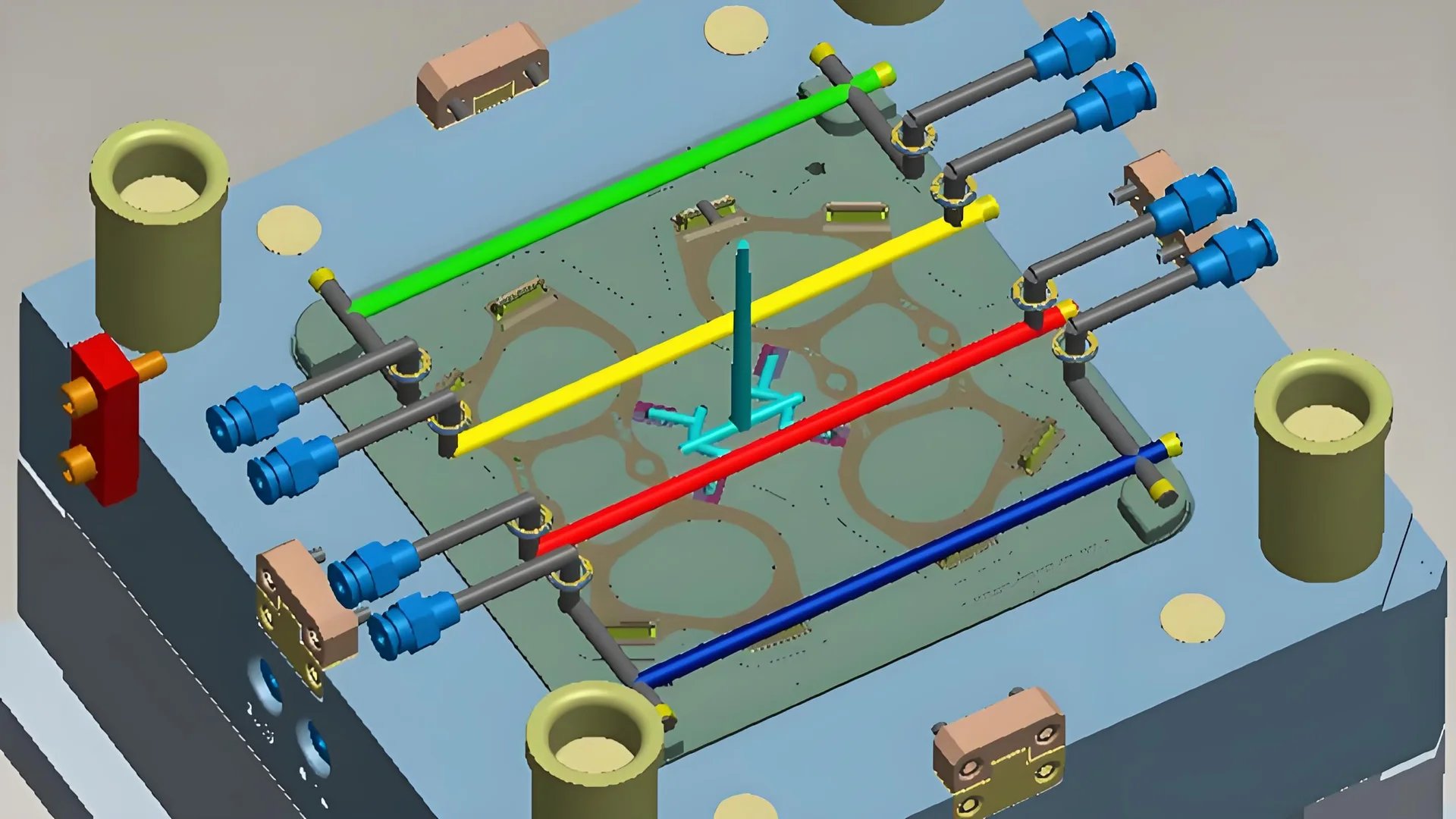
The Science Behind Cooling Speed
Have you ever waited eagerly for a project to finish, only to wonder why things went wrong? Cooling speed might be the hidden reason. It really affects the size and quality of the final product. I once worked on a plastic part where cooling seemed magical but was unpredictable. In injection molding, the thickness of the mold decides cooling speed. A thicker mold takes longer for heat to escape from the plastic to the surface. This stretches the cooling time a lot. For example, a 5mm thick plastic item might need 20 to 30 seconds to cool in a thick mold, but only 10 to 15 seconds in a thin one.
Impact on Dimensional Accuracy
Dimensional accuracy shows how well a product matches its planned size. I have faced this many times. Fast or uneven cooling can twist a product, making it like puzzle pieces that don’t fit. I’ve seen tiny plastic gears lose their round shape or teeth alignment due to uneven cooling and wrong mold thickness.
Slower cooling helps even shrinkage, stabilizes the material, and makes it more likely to get what you planned. That’s important because it ensures that despite taking longer, the end product is closer to its intended design.
Considerations for Mold Thickness
Choosing mold thickness is like picking the right tool; if you choose wrong, you face much frustration. Thinner molds let heat escape faster, lowering risks of shrink marks. However, thicker molds need more time to cool for good accuracy.
This choice is crucial during design as selecting appropriate material or cooling method can significantly impact results. Modern methods are now smartly including these choices for better control in manufacturing processes1.
Practical Applications in Industry
Industries such as cars and planes need precise sizes for their parts to work and look good. Even tiny errors cause big problems. I have been there, adjusting endlessly because parts didn’t fit right.
Cooling speed is vital for improving production by ensuring components meet exact needs through adjustments in parameters like mold thickness and cooling time.
Innovations and Techniques
New technologies are emerging to manage cooling speed effectively. Adaptive cooling systems allow instant changes during production which help keep size and shape of items correct.
Using these technologies has helped me work more efficiently and waste less while ensuring products meet stringent dimensional standards.
It is really essential for those entering 3D printing or additive manufacturing as understanding cooling techniques2 is key to getting very good results.
Thicker molds slow cooling, affecting dimensional accuracy.True
Thicker molds conduct heat slower, leading to uneven cooling and shrinkage.
High injection pressure always improves product appearance.False
Excessive pressure can cause defects like flying edges and internal stress.
How Does Injection Pressure Impact Product Density and Appearance?
Curious about how pressure in injection molding changes your product’s weight and appearance? Let’s explore and understand this interesting link.
Injection pressure changes how the melt goes into the mold. This affects product density and looks. High pressure fills the mold better. But it might cause surface problems. These problems include flying edges. They really affect the appearance.
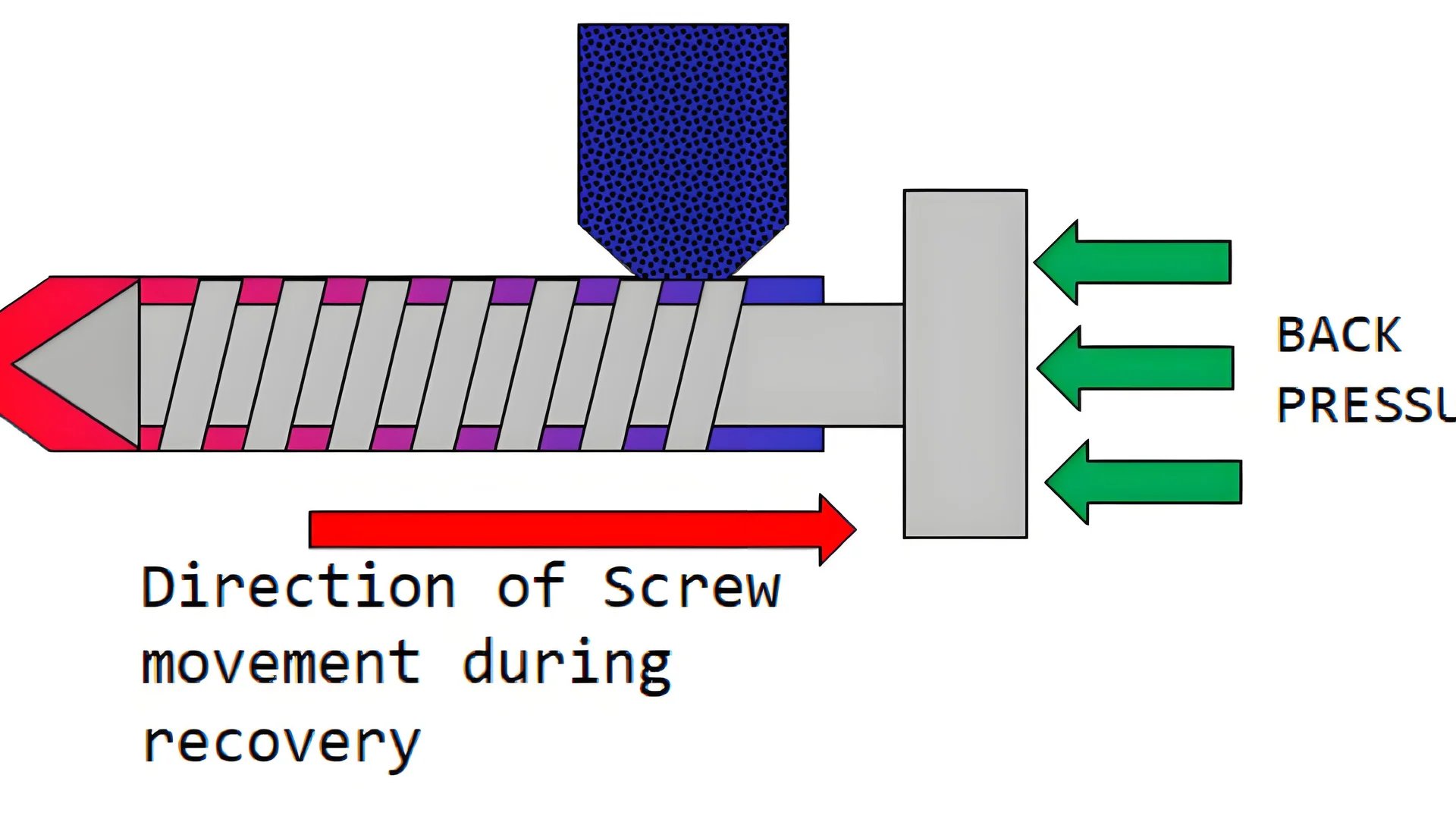
Injection Pressure and Product Density
At first, I felt surprise when I learned about injection molding. Simple pressure plays a big role. Picture pushing toothpaste into a hard mold. That’s what plastic melts do. Thicker molds demand more force to fill every space. More pressure means the inside becomes denser than the outer parts. Pressure affects density.
For example, in large, thick-walled plastic products3, high injection pressure might lead to a higher density internally, while areas near the mold wall remain less dense, forming a density gradient.
Once, I handled a project with thick plastic items. It was amazing and hard to see pressure change the inside density. Some parts felt solid; others did not.
Influence on Appearance Quality
The look of finished products was a tricky problem. High pressure fills molds but may cause defects, like extra plastic edges—small bits of plastic that escape through gaps in the mold. This is particularly problematic for products requiring high aesthetic quality, such as transparent plastics.
I recall working on see-through items that turned cloudy due to wrong pressure settings, leading to internal stress within the product and affecting transparency. That taught me balance is delicate; understanding this balance is essential for manufacturers aiming for premium appearance standards in their products.
Cooling Effects and Dimensional Accuracy
Cooling changes everything in molding. Mold thickness cools at various speeds. Thicker molds cool slower, risking shrinkage after removing them from the mold.
If an operator uses high injection pressure but doesn’t account for cooling variations, they might end up with warped or distorted products like bent gears—products that must be precise.
For instance, in precision parts like gears, incorrect cooling and pressure4 combinations can compromise the gear’s tooth precision and roundness.
Pressure-Holding Process and Internal Quality
During the pressure-holding step, patience is key. Thick molds need longer holding times to avoid shrink marks inside critical areas like the bottom and sides of containers.
Rushing this stage results in visible marks; I remember some containers had issues because of short holding times which affected their appearance and strength.
Also, mold thickness impacts stress during cooling—this may cause cracks with stress or temperature shifts during use under external forces or temperature changes.
Understanding these details is essential; these factors are crucial for high-quality products.
Thicker molds require higher injection pressure.True
Thicker molds increase flow resistance, needing higher pressure for cavity fill.
Slow cooling improves dimensional accuracy of molded products.False
Slow cooling can cause shrinkage and warping, reducing dimensional accuracy.
Why is pressure-holding time essential for quality control in injection molding?
Curious why pressure-holding time matters so much in injection molding? Let me explain.
Pressure-holding time is crucial in injection molding. The material must fill the mold properly. This step reduces shrinking and stress inside. It hardens the material under pressure. This step keeps the size exact. It stops problems like bending or breaking.
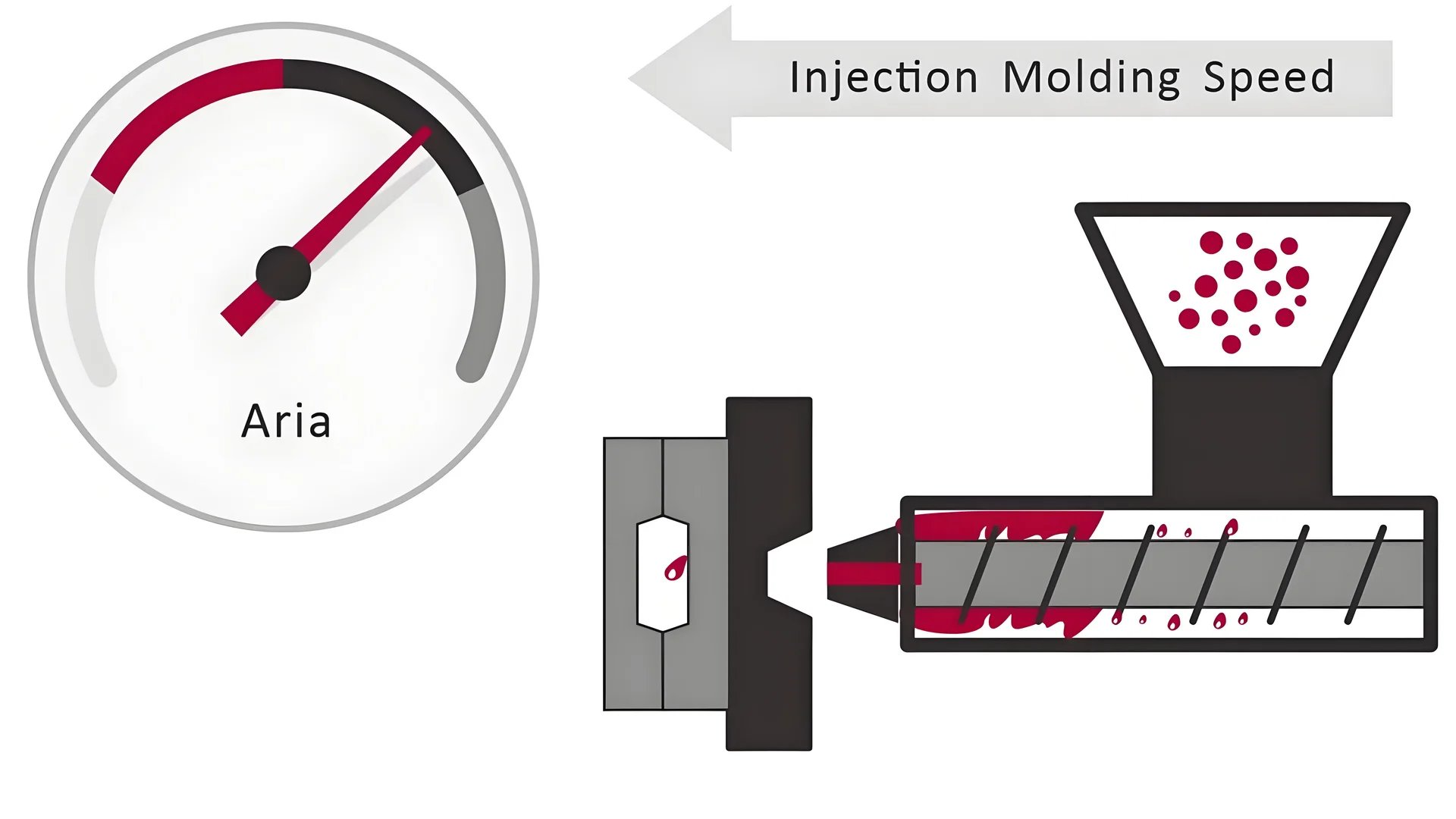
Cooling Effect and Dimensional Accuracy
The cooling effect is very important for keeping molded items the right size. Think about this: if a mold is thick, it cools slower. This can cause it to shrink or warp after removing it from the mold. I worked on a project with plastic parts with 5mm walls. We had to carefully change cooling times. If cooling is uneven, precision gears could become far from precise.
When the mold thickness varies5, it affects the cooling speed. Thicker molds cool more slowly, which can lead to continued shrinkage and potential warping after demolding.
Injection Molding Pressure and Quality
Pressure in injection molding is also very important. Thicker mold cavities need more pressure to fill completely. This creates density differences. We noticed this in large, thick products. Too much pressure causes surface flaws.
The injection pressure required during the molding process influences the product’s density and appearance. Excessive pressure can cause surface defects like flashing or internal stresses that affect transparency in products like clear plastic containers.
Pressure Retention and Internal Stress
I found out how crucial pressure retention is. Not enough holding time results in visible shrink marks. This was common in thick-walled containers where strength was a must.
The pressure retention phase ensures that the material remains under pressure long enough to solidify properly, avoiding shrink marks and internal defects.
Understanding these things was like solving a puzzle for me. Adjusting pressure-holding time based on mold thickness and material properties helped improve product performance and longevity while minimizing defects.
Thicker molds cool faster than thinner ones.False
Thicker molds cool slower due to longer heat conduction paths.
High injection pressure can cause product surface defects.True
Excessive pressure may lead to surface defects like flying edges.
How does mold thickness lead to internal stress issues?
Have you ever considered how the thickness of a mold affects your plastic products? Enter the interesting world of mold design. Those extra millimeters might stop cracks or warps. Thickness protects creations. Maybe, this detail is the key.
Mold thickness controls cooling rates, injection pressure and stress spread in molded products. Thicker molds cool slowly. This slow cooling affects size accuracy and inside stress. These problems might cause defects like warping or cracking. Balancing mold design is very important for good product quality.
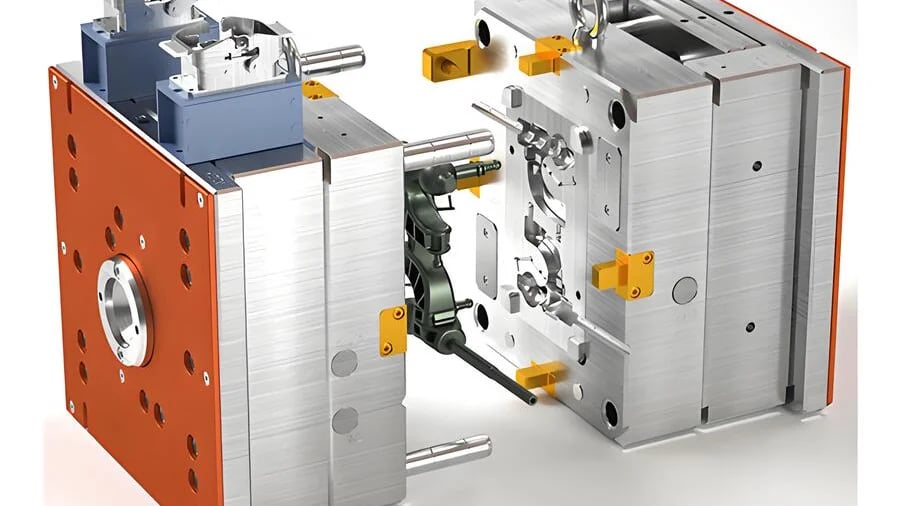
Cooling Effects on Dimensional Accuracy
I remember facing a warped product for the first time. It was frustrating. So much effort went into the design. The thickness of the mold is important. A thick mold is like a giant blanket, slowing cooling. I once worked on a project with a 5mm thick plastic wall. The cooling time increased from 10-15 seconds in a thin mold to 20-30 seconds in a thick one. This difference may cause shrinkage or warping after removal, affecting fit – like trying to fit a bent puzzle piece into a perfect slot. Precision parts, like plastic gears, depend on this process. Knowing these details helped me to adjust my mold design for better precision6.
Injection Pressure and Density Variations
Getting the right injection pressure was a big lesson for me. A thicker mold needs more pressure to fill it correctly. I once worked with a large, thick-walled product. Without changing the pressure, the center became denser than the edges, causing problems. This imbalance affected structure and caused visible defects. High pressures caused flying edges and cloudiness in clear products. For appearance, balancing pressure and mold thickness is key to keeping good surface quality7.
Pressure-Holding and Internal Stress
Patience during the pressure-holding phase is rewarding. Thicker molds need more time for proper solidification. Rushing this can cause shrink marks that ruin the look and strength of my thick-walled containers. Also, skipping proper pressure steps can create internal stresses that cause cracks with a light touch or temperature change. Knowing how mold thickness affects stress helped me design stronger products and really improve durability8.
By understanding mold thickness, I found ways to balance design choices with material behavior, reducing internal stresses along the way. Every project taught me something new about finding that balance.
Thicker molds increase cooling time for plastic products.True
Thicker molds slow heat conduction, extending cooling time to 20-30 seconds.
Higher injection pressure reduces internal stress in products.False
Excessive pressure can cause defects and increase internal stress, not reduce it.
Conclusion
Mold thickness significantly influences cooling rates, injection pressure, and product quality. Thicker molds slow cooling, affecting dimensional accuracy and internal stress, while higher pressures can lead to surface defects.
-
Explore why mold thickness is crucial in determining product quality. ↩
-
Learn about innovative techniques for managing cooling speed effectively. ↩
-
Explore how pressure influences density distribution in thick-walled products. ↩
-
Learn about cooling time’s role in maintaining dimensional accuracy. ↩
-
Discover how mold thickness affects cooling rates and product quality. ↩
-
Learn how mold thickness affects precision in gear manufacturing. ↩
-
Discover how injection pressure influences product surface appearance. ↩
-
Explore strategies for enhancing durability through mold design. ↩