Have you ever thought about how mold temperature influences your injection molded products? Mold temperature plays a crucial role. Changes in temperature affect the quality. Proper temperature control is essential. Perfect products first require the right conditions.
Mold temperature is very important for the precise size of injection molded products. It affects how products cool, form crystals and deal with heat pressure. When mold temperatures are high, products might grow larger and lose stability. On the other hand, low temperatures often cause products to shrink and change shape unevenly. Accurate mold temperature matters.
I recall my early days in mold design when I first learned about the delicate balance of mold temperatures. It was like finding a hidden layer of complexity that could change an entire production line. Basics suggest that higher temperatures might let materials relax more, leading to bigger sizes, but there’s much more involved. For example, I once changed a mold temperature for a complex design. The change caused unexpected expansion because of increased crystallinity. Lowering the temperature too much, however, resulted in parts not fitting together because they shrank more than expected.
Understanding these interactions showed me that mold temperature isn’t just a machine setting. It’s very crucial for precision in our products. Balancing these factors is not only about technical skill. It’s about predicting outcomes and ensuring each component fits just right. Balancing these factors is really important. Whether dealing with warping from heat stress or handling shrink marks, understanding and managing mold temperature is key to becoming skilled in injection molding.
High mold temperatures increase product size by 0.5% - 1%.True
Higher mold temperatures allow plastic to fill cavities more fully, increasing size.
Low mold temperatures cause uniform shrinkage in products.False
Low temperatures lead to uneven cooling, causing non-uniform shrinkage and defects.
- 1. How Does High Mold Temperature Affect Product Size?
- 2. How Does Low Mold Temperature Affect Dimensional Uniformity?
- 3. Why is mold temperature crucial for crystalline plastics?
- 4. How does mold temperature impact thermal stress and warping?
- 5. How Can I Optimize Mold Temperature Settings?
- 6. Conclusion
How Does High Mold Temperature Affect Product Size?
Have you ever thought about why your plastic item isn’t the size you imagined? The mold temperature might be the reason!
High mold temperatures reduce shrinkage in plastic items, resulting in larger sizes. Slower cooling enables molecular chains to relax and align well. Mold temperature control is very important for accurate product dimensions.
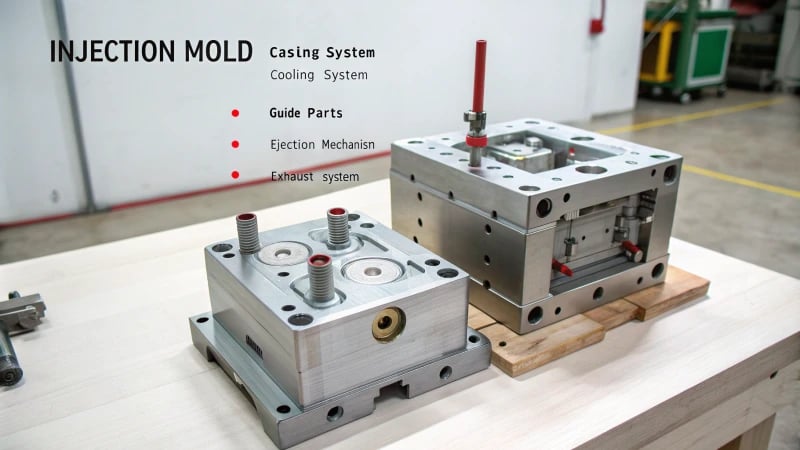
Dimensional Enlargement
In my early career, I noticed strange things happening with mold temperature. One day while designing a product, our products were always bigger than expected. After some investigation, I realized that the mold temperatures were too high. This made me see clearly. Higher temperatures slow cooling. So, tiny plastic chains have more time to relax. They align better and there is less shrinkage.
For instance, raising mold temperature from 40°C to 60°C makes products grow by 0.5% to 1%! The melt fills every part of the mold and stays longer, making denser, bigger products.
Mold Temperature | Product Size Increase |
---|---|
Normal (40°C) | Standard |
High (60°C) | +0.5% to +1% |
Crystalline plastics like polyethylene and polypropylene also behave this way. I saw that high mold temperatures helped crystallization, increasing the product’s size even more. Once, I saw a polypropylene product grow 3% to 5% just by increasing heat. It’s amazing how temperature changes your product so deeply!
In injection molding1, PP products can significantly increase in size due to high mold temperatures.
Dimensional Instability
Now, here’s the problem – too much heat can cause issues. I saw products warp after removing them from molds. Imagine a beautiful plastic plate that twists at the edges because it cooled unevenly. The center cooled slower than the edges.
This uneven cooling causes stress, leading to warping—like baking a cake; the center stays soft while the edges firm up—but here it messes with your product’s accuracy.
It is really important to control mold temperatures carefully by watching environmental conditions and changing settings if necessary.
For more insights on this topic, read about thermal stress effects2 on molded products.
Maintaining optimal mold temperatures helps achieve desired product dimensions while minimizing defects.
If the central part of a plate remains hotter than its edges after demolding, thermal stresses may lead to unwanted warping.
Managing High Mold Temperatures
If you want to avoid dimension surprises, learn to adjust mold temperatures:
- Regular monitoring of mold and melt temperatures is crucial.
- Adjust cooling rates based on different materials being used.
- Implement consistent quality checks post-production for assurance.
For practical tips on managing these effectively, explore mold temperature control techniques3. These strategies help ensure my designs always meet high quality standards consistently.
In conclusion, controlling mold temperature is like a secret power for achieving precise dimensions in molded products—getting it right avoids mistakes and problems leading to products you can be truly proud of.
High mold temperatures reduce product shrinkage.True
High mold temperatures allow more time for plastic chains to relax, reducing shrinkage.
Low mold temperatures increase dimensional uniformity.False
Low mold temperatures cause uneven cooling, leading to dimensional non-uniformity.
How Does Low Mold Temperature Affect Dimensional Uniformity?
I recall when I discovered the importance of mold temperature in injection molding through a tough experience. That day was very challenging. Mold temperature truly matters a lot in creating the right product.
When mold temperatures drop too low, products may shrink more. This could lead to uneven sizes because plastic cools down very fast. It causes problems like shrink marks. Such errors influence how parts join together and their precision.
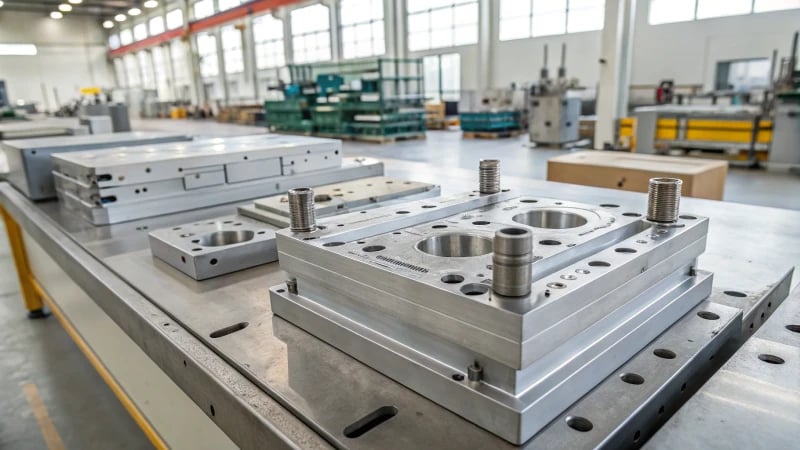
Effect on Size Reduction
Once I had a project with a mold set too cold, which taught me a lot. The plastic cooled too fast, causing the material to tighten instead of relaxing. The result was a smaller final product than expected. Picture something designed perfectly, but it turned out 1%-2% smaller after cooling.
Mold Temperature | Expected Shrinkage |
---|---|
Optimal | 0% |
Too Cold | 1%-2% smaller |
Such shrinkage4 creates big problems for precision parts, especially in gadgets like consumer electronics.
Uneven Size Accuracy
I also faced more resistance to flow due to the cold conditions. This meant the plastic didn’t spread evenly inside. This resulted in uneven sizes and unattractive shrink marks. Thin-walled products suffered more. Imagine trying to pour thick honey into a narrow bottle – it doesn’t go well.
In a case with thin-walled plastics, low temperatures caused unequal wall thickness, which led to internal stress and later, warping. It wasn’t pleasant!
Internal Stress and Warping
Fast cooling lets different product parts cool differently, creating stress inside. This stress may twist or bend products out of the mold. It’s important for designers to find the best mold settings, especially in precise fields.
Understanding these effects is crucial for designers optimizing mold conditions5. For people like Jacky, who want precision and consistency, considering mold temperature significantly improves production and quality.
Best Ways to Keep Uniform Size
I’ve tried changing cooling rates and using materials better at handling cold. New CAD tools predict outcomes under different conditions, keeping me prepared.
By managing mold temperatures and understanding effects, product quality meets strict design standards without needing major fixes.
High mold temperature increases product size by 0.5% - 1%.True
Higher temperatures allow more relaxation time, reducing shrinkage.
Low mold temperature results in larger product dimensions.False
Low temperatures accelerate cooling, increasing shrinkage and reducing size.
Why is mold temperature crucial for crystalline plastics?
Do you ever think about why mold temperature is important when using crystalline plastics? Mold temperature influences plastic quality. The plastic behaves differently based on the temperature set during processing. Crystalline plastics need precise heat levels for proper shaping. Incorrect temperatures lead to poor material performance. Mistakes in heat management can ruin the final product. Temperature control remains crucial for success.
Mold temperature is very important for crystalline plastics. It controls crystallinity. This influence shapes both the precision of the dimensions and the strength of the product. Correct temperature control leads to fewer flaws. Fewer flaws mean better manufacturing results.
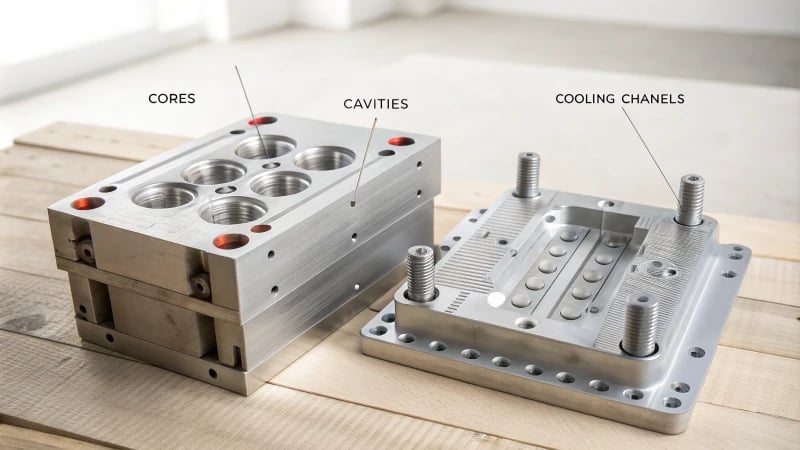
Impact on Dimensional Accuracy
In my early career, I learned about the sensitivity of crystalline plastics like polyethylene and polypropylene to mold temperature. High mold temperatures cause the plastic to swell up to 5% in thickness. I remember a project where I missed this, and the product became larger than planned. This led to many fitting problems.
Very low mold temperatures result in too much shrinkage, shrinking the product more than expected. Nothing fit correctly, leaving me puzzled. It was a big lesson. Getting the right temperature is crucial.
Mold Temperature | Effect on Dimensions |
---|---|
High | Larger dimensions |
Low | Smaller dimensions |
Influence on Crystallinity
Crystallinity is also greatly affected by mold temperature. I recall higher temperatures aligning molecular chains into crystalline structures. This created stronger material but also brought warping challenges if not managed well.
Balancing temperature settings was crucial for the desired product features. It’s a lesson that sticks: fine-tuning temperatures spells the difference between success and failure.
Managing Dimensional Instability
Uneven mold temperatures caused thermal stress in some early projects. This led to warping or distortion after removing the mold. I remember one large plastic plate that looked like a wavy potato chip instead of a smooth component.
Controlling the mold’s cooling cycle is key to consistent temperature across surfaces. Dimensional accuracy6 issues can be mitigated by ensuring even heat distribution.
Practical Considerations for Mold Designers
Over time, I realized that precise temperature control in molds is not just nice but necessary. Advanced monitoring systems and careful adjustments based on materials have become essential techniques.
Such strategies help balance crystallinity and mechanical properties, improving both the look and function of products in consumer electronics7 and more.
These insights have truly helped me refine my strategies and align production with industry standards, aiming for top product quality and performance.
High mold temperature reduces product shrinkage.True
Higher temperatures allow plastic to fill cavities fully, reducing shrinkage.
Low mold temperature increases product size by 3%.False
Lower temperatures increase shrinkage, reducing product size, not increasing it.
How does mold temperature impact thermal stress and warping?
Have you ever considered how mold temperature might affect the quality of your molded products? Mold temperature plays a crucial role. It influences the final outcome of your molded items. Proper mold temperature control ensures top-notch quality. Incorrect temperatures damage the product. A well-maintained mold temperature truly matters.
Mold temperature changes cooling speeds and molecule positions. This shift affects heat stress and shape bending. Good temperature control reduces flaws, like bending and this improves size accuracy. It also helps the product stay stable.
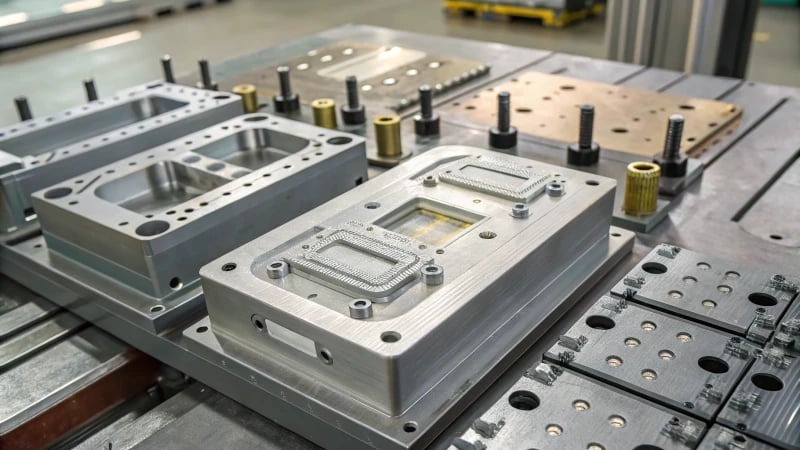
Influence of Mold Temperature on Cooling Rates
I recall my early industry days, standing next to noisy machines, watching hot plastic flow like a lava stream. The mold temperature quietly decided the final fate of the product. High temperatures slowed cooling and allowed the plastic to settle nicely with less shrinkage. A low temperature sped up cooling, which sometimes caused problems like shrinkage or bending.
Temperature | Effect on Cooling |
---|---|
High | Slower cooling, less shrinkage |
Low | Faster cooling, more shrinkage |
Dimensional Changes with Temperature Variations
Once, we worked with polypropylene and increased the mold temperature slightly. Our product surprised us by turning out bigger than expected! The higher temperature increased crystallinity, which expanded the size just enough to mess with our measurements. I learned that a small 0.5%-1% change sometimes really changes everything!
When the mold temperature is high, plastics like polypropylene can experience increased crystallinity, causing expansion. This expansion can result in a product larger than intended, leading to issues with dimensional accuracy. For example, in thermoplastic molding8, a rise in mold temperature from 40°C to 60°C can increase size by 0.5% – 1%.
Inducing Thermal Stress
Picture this: crafting a big plastic plate. If the mold’s center stays hot while the edges cool unequally, the plate may bend like a potato chip. Such thermal stresses have caused many sleepless nights in the factory.
- Example: In large plates, hotter centers cause curls, making them bulge or warp.
Uneven temperature distribution during cooling can create thermal stresses. These stresses may cause warping or deformation post-demolding.
Managing Warping with Controlled Temperatures
I have learned to respect the careful control of mold temperatures to prevent warping. It’s like baking a perfect soufflé; finding the right balance stops everything from falling apart. By watching temperatures and slowly cooling the material, warping is very reduced.
Proper management of mold temperature is crucial to avoid warping. By understanding the thermal properties of materials, designers can optimize mold temperatures to reduce thermal stress.
- Table: Impact of Mold Temperature on Warping
Mold Temperature | Risk of Warping |
---|---|
High | Increased |
Low | Decreased |
Practical Applications for Designers
Designers like me connect beauty with function while handling production limits. CAD software tools help predict mold conditions and identify issues early. It acts like a magic ball for manufacturing, letting us adjust details and avoid expensive errors.
Designers working in consumer electronics need to balance aesthetic and functional requirements with manufacturing constraints. Utilizing CAD software to simulate mold conditions and predict outcomes can help mitigate risks associated with thermal stress and warping.
By understanding these subtle points is key for better products and smooth production.
High mold temperature reduces product shrinkage.True
Higher mold temperatures allow plastic to fill the cavity more fully, reducing shrinkage.
Low mold temperature increases dimensional uniformity.False
Low temperatures cause uneven cooling, leading to dimensional non-uniformity and defects.
How Can I Optimize Mold Temperature Settings?
Have you ever thought about why some plastic pieces turn out flawless while others bend or get smaller? The key lies in setting the mold temperature perfectly.
To set the best mold temperature, I consider the type of material, the size of the product and how fast it cools. Getting these elements right helps avoid problems like shrinking or bending. This approach really improves precision and the product’s quality. Quality matters.
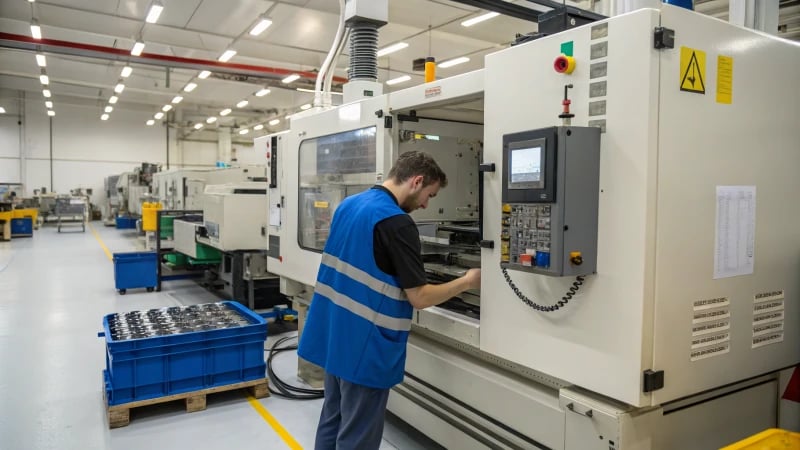
Understanding Material-Specific Needs
Different materials need unique handling to get great results. Crystalline plastics, such as polypropylene9, like higher mold temperatures. This heat helps them form crystals, leading to larger products. On the opposite side, amorphous plastics are more fragile – they require lower temperatures to stop the problem of shrinking.
Temperature’s Impact on Size Accuracy
Experience taught me that high mold temperatures might cause parts to grow in size. At first, I was amazed by how much a little change in heat could change the size. Imagine shaping a thermoplastic and seeing it become 0.5%-1% bigger after it cools down, just because the temperature increased from 40°C to 60°C! This happens because the plastic settles and straightens as it cools slowly.
Mold Temperature | Effect on Dimensions |
---|---|
High | Enlarged size, better density |
Low | Increased shrinkage, reduced size |
Cooling Rates
Finding the right balance is vital. Cooling too quickly leads to uneven sizes, creating trouble spots like shrink marks. I remember dealing with uneven thickness in a thin-walled task. Fast cooling caused many internal stress problems.
Setting Mold Temperature for Different Products
For larger parts, I notice the center must not keep more heat than the sides or the piece might bend. A very even temperature helps avoid stress-related bending.
Monitoring and Control Systems
Advanced monitoring systems changed the game for me. Real-time temperature data keeps everything in line. Tools like thermal cameras10 or infrared sensors11 give precise measurements and adjustments.
Testing and Improving
Ongoing experiments and improvements have been crucial for me. Keeping detailed notes of successes and failures has built a helpful resource for future projects. This method saves both time and enhances quality in the end.
Focusing on these details has helped me pick good temperature settings for molds, leading to better results in my molding work.
High mold temperature increases product size by 0.5% - 1%.True
Higher mold temperatures allow more plastic relaxation, reducing shrinkage.
Low mold temperature reduces product size by 3% - 5%.False
Low mold temperatures typically cause a reduction of 1% - 2% in size.
Conclusion
Mold temperature significantly affects the dimensional accuracy of injection molded products, influencing size, stability, and potential defects through its impact on cooling rates and crystallinity.
-
Explore how different factors in injection molding affect product size to optimize your manufacturing process. ↩
-
Learn about thermal stress impacts on molded products to prevent defects and ensure quality. ↩
-
Discover methods to control mold temperatures effectively, ensuring consistent product quality and dimensions. ↩
-
Understand how low temperatures increase shrinkage and affect part dimensions. ↩
-
Gain insights into designing molds for optimal precision and reduced defects. ↩
-
Learn techniques to prevent warping and maintain dimensional stability in molded products. ↩
-
Discover best practices in mold design for optimizing electronic component manufacturing. ↩
-
Explore detailed effects of mold temperatures on thermoplastic properties. ↩
-
Explore how polypropylene’s crystallization affects product volume and dimensional accuracy, offering insight into optimal temperature settings. ↩
-
Learn about the benefits of thermal cameras in maintaining precise mold temperatures, which are crucial for high-quality injection molding. ↩
-
Discover how infrared sensors improve accuracy in monitoring mold temperatures, enhancing product quality in injection molding. ↩