Mold sticking is a common headache for manufacturers like me, affecting everything from efficiency to product quality.
Mold sticking occurs when the molded product adheres to the mold surfaces during demolding, due to factors like poor mold design, inappropriate process parameters, and unsuitable material choices. Effective prevention involves optimizing mold design, adjusting process conditions, and selecting appropriate materials.
While understanding the immediate causes of mold sticking is essential, delving into detailed preventive measures can significantly enhance production efficiency. Read on to discover expert strategies for addressing these issues comprehensively.
High mold temperature reduces mold sticking risk.False
High mold temperatures increase adhesion, raising the risk of sticking.
How Does Mold Design Influence Mold Sticking?
Mold design plays a pivotal role in preventing mold sticking, impacting production efficiency and product quality.
Mold design influences mold sticking through factors like demolding angle, surface finish, and complexity. An optimized design reduces adhesion risks by ensuring adequate slopes, smooth surfaces, and simplified structures. Proper temperature control and exhaust features further minimize sticking issues, leading to efficient production cycles.
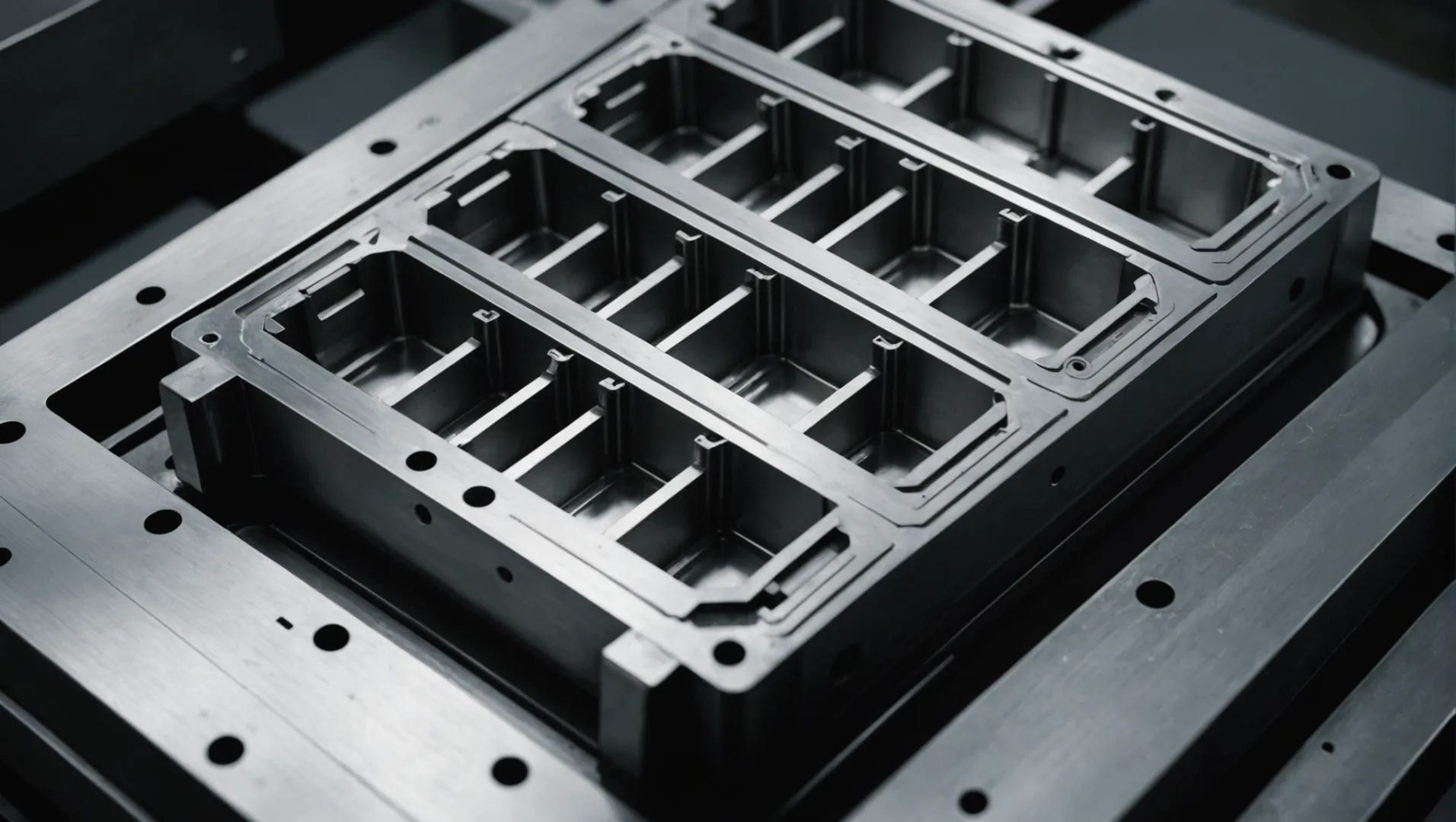
Key Mold Design Elements
The design of a mold significantly affects how easily a product can be removed from it. Here are some critical design elements that influence mold sticking:
- Demolding Angle: A small demolding angle can cause the product to stick due to insufficient clearance. Designing with a slope between 1°-3° ensures easier release.
- Surface Finish: High roughness increases friction and adhesion. Polishing the mold surface enhances smoothness, facilitating easy removal.
- Complexity of Structure: Complex mold structures can create barriers to smooth demolding. Simplifying the structure reduces potential sticking points.
Temperature Control
Temperature management within the mold is crucial:
- High Temperatures: Excessive heat can increase adhesion between the plastic and mold surfaces.
- Low Temperatures: Conversely, too low temperatures might result in rapid cooling and uneven shrinkage, causing sticking.
Utilizing heating or cooling systems to maintain an optimal temperature range is essential. This range varies based on the type of plastic used and the desired product specifications.
Exhaust Systems
Proper exhaust systems are vital in preventing pressure build-up, which can lead to sticking:
- Exhaust Grooves and Holes: Design the mold with adequate grooves and holes to allow gases to escape during injection molding.
This approach reduces internal pressures and the likelihood of the product adhering to the mold surfaces.
For further insights into effective mold temperature control1 and designing efficient exhaust systems2, these resources can offer comprehensive guidance on enhancing your mold design strategy.
A small demolding angle increases mold sticking risk.True
Insufficient clearance from a small angle causes products to stick.
High surface roughness decreases mold sticking.False
Rough surfaces increase friction, enhancing adhesion and sticking.
What Role Do Process Parameters Play in Mold Sticking?
In the intricate world of injection molding, process parameters can significantly impact the occurrence of mold sticking, a common and costly issue.
Process parameters such as injection pressure, holding time, and material temperature directly affect mold sticking. Excessive pressure and holding time increase adhesion, while incorrect material temperatures can lead to uneven cooling and shrinkage, causing products to stick to the mold. Adjusting these parameters is crucial for efficient production.
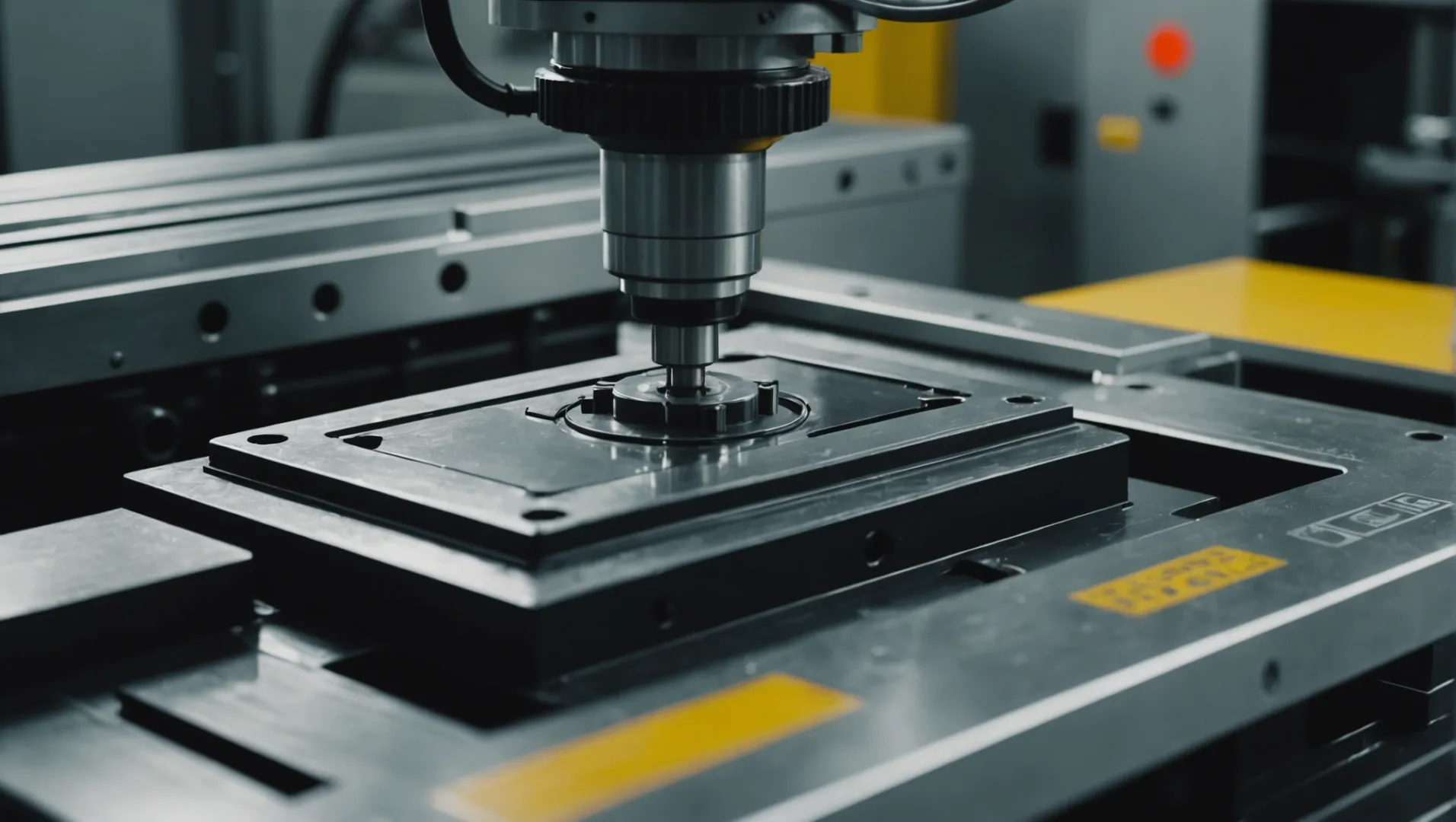
Injection Pressure and Its Impact
Injection pressure is crucial in determining how tightly the molten plastic fills the mold cavity. When the pressure is too high, it forces the plastic into every crevice, enhancing adhesion between the product and mold surfaces. This not only increases the risk of sticking but also challenges demolding techniques3. By fine-tuning the pressure to an optimal level, manufacturers can reduce this risk.
Holding Time: Balancing Coolness and Adhesion
The holding time refers to the duration the plastic remains under pressure after injection before it cools. Extended holding times allow more cooling within the mold, strengthening adhesion as the product conforms closely to the mold’s surface. However, too short a holding time might result in incomplete product formation. Adjusting this parameter is vital; thus, understanding its delicate balance can significantly minimize sticking issues.
Material Temperature Control
Material temperature plays a dual role in mold sticking. High temperatures enhance plastic fluidity, making it easier to fill molds but simultaneously increasing adhesion. Conversely, temperatures that are too low cause rapid cooling, leading to uneven shrinkage and sticking. Monitoring and maintaining appropriate material temperatures tailored to each type of plastic can prevent these pitfalls. Temperature monitoring systems4 offer precise control over this critical parameter.
The Importance of Speed Adjustment
Injection speed, though often overlooked, influences how well the plastic flows into the mold and ultimately impacts demolding success. Too fast, and it may lead to defects; too slow, and the material might not fill all necessary spaces or create unnecessary friction with the mold surfaces. Optimizing speed5 according to product size and complexity is essential for reducing mold sticking without compromising on quality.
High injection pressure increases mold sticking risk.True
Excessive pressure forces plastic into crevices, enhancing adhesion.
Short holding times reduce mold sticking issues.False
Too short holding times may lead to incomplete product formation.
How Can Material Selection Impact Mold Sticking?
Choosing the right material is crucial to preventing mold sticking in injection molding processes.
Material selection significantly affects mold sticking by influencing viscosity, demolding performance, and impurity content. Using materials with lower viscosity and high-quality standards reduces adhesion, while avoiding impurities enhances fluidity and eases demolding.
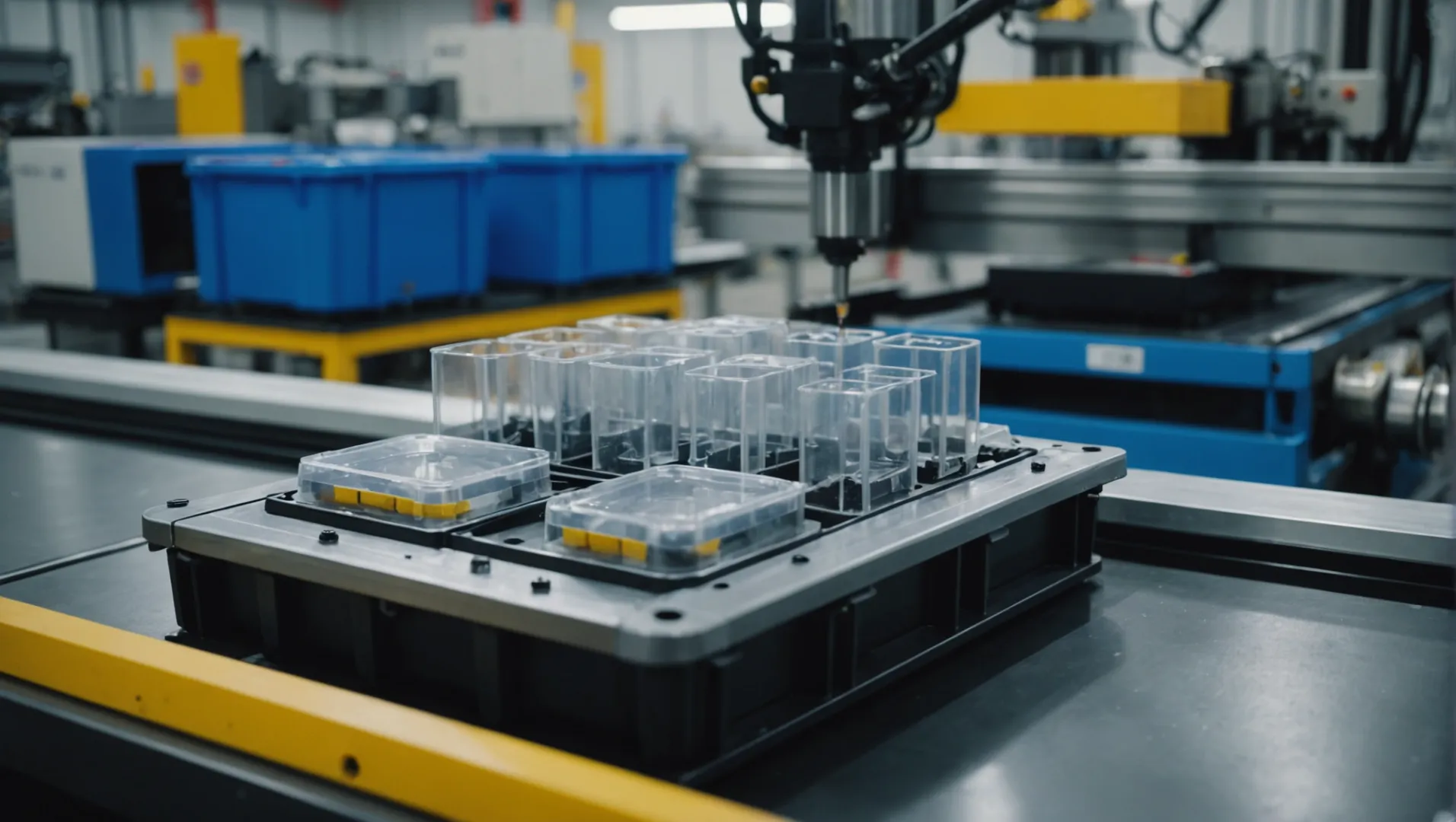
Understanding Material Properties and Their Impact
The properties of the plastic material used in injection molding play a pivotal role in mold sticking. Materials with high viscosity often exhibit stronger adhesion to mold surfaces, making demolding a challenge. Selecting a material with inherently lower viscosity can reduce this adhesion, enhancing the demolding process6.
Moreover, some materials are designed with additives that improve their demolding capabilities. For instance, certain thermoplastics are engineered to have better flow characteristics, reducing the likelihood of sticking. The presence of these additives can make a notable difference in production efficiency.
The Role of Impurities in Material Selection
Impurities within a plastic material can negatively impact its fluidity and overall performance during molding. These impurities may cause uneven cooling or even lead to defects that exacerbate mold sticking issues. Thus, ensuring the purity of the material is paramount.
Manufacturers often employ rigorous quality control measures to ensure that materials are free from contaminants. For example, high-performance polymers such as polyether ether ketone (PEEK) are renowned for their purity and performance, making them less prone to causing sticking issues.
Material Type | Viscosity | Impurity Level | Demolding Performance |
---|---|---|---|
Low Viscosity | Low | Low | High |
High Viscosity | High | Medium | Medium |
Impure Materials | Variable | High | Low |
Incorporating Mold Release Agents
Another aspect of material selection involves using mold release agents. These agents are mixed with the plastic material to reduce the adhesion between the plastic and the mold. However, caution is advised in their use; excessive amounts can affect the final product’s surface quality.
Selecting a compatible mold release agent that matches both the material properties and the product requirements is crucial. This tailored approach ensures optimal performance without compromising product aesthetics or structural integrity.
By carefully evaluating these factors and selecting materials that align with your production needs, you can effectively mitigate mold sticking issues and improve the overall efficiency of your injection molding operations.
Materials with lower viscosity reduce mold sticking.True
Lower viscosity materials flow better, reducing adhesion to molds.
Impure materials improve demolding performance.False
Impurities hinder fluidity and cooling, worsening demolding issues.
What Are Some Advanced Techniques to Prevent Mold Sticking?
Tackling mold sticking requires advanced strategies beyond basic fixes, elevating both efficiency and quality.
Advanced techniques to prevent mold sticking include optimizing cooling systems, utilizing anti-stick coatings, and leveraging automation technologies to monitor and adjust parameters in real-time.
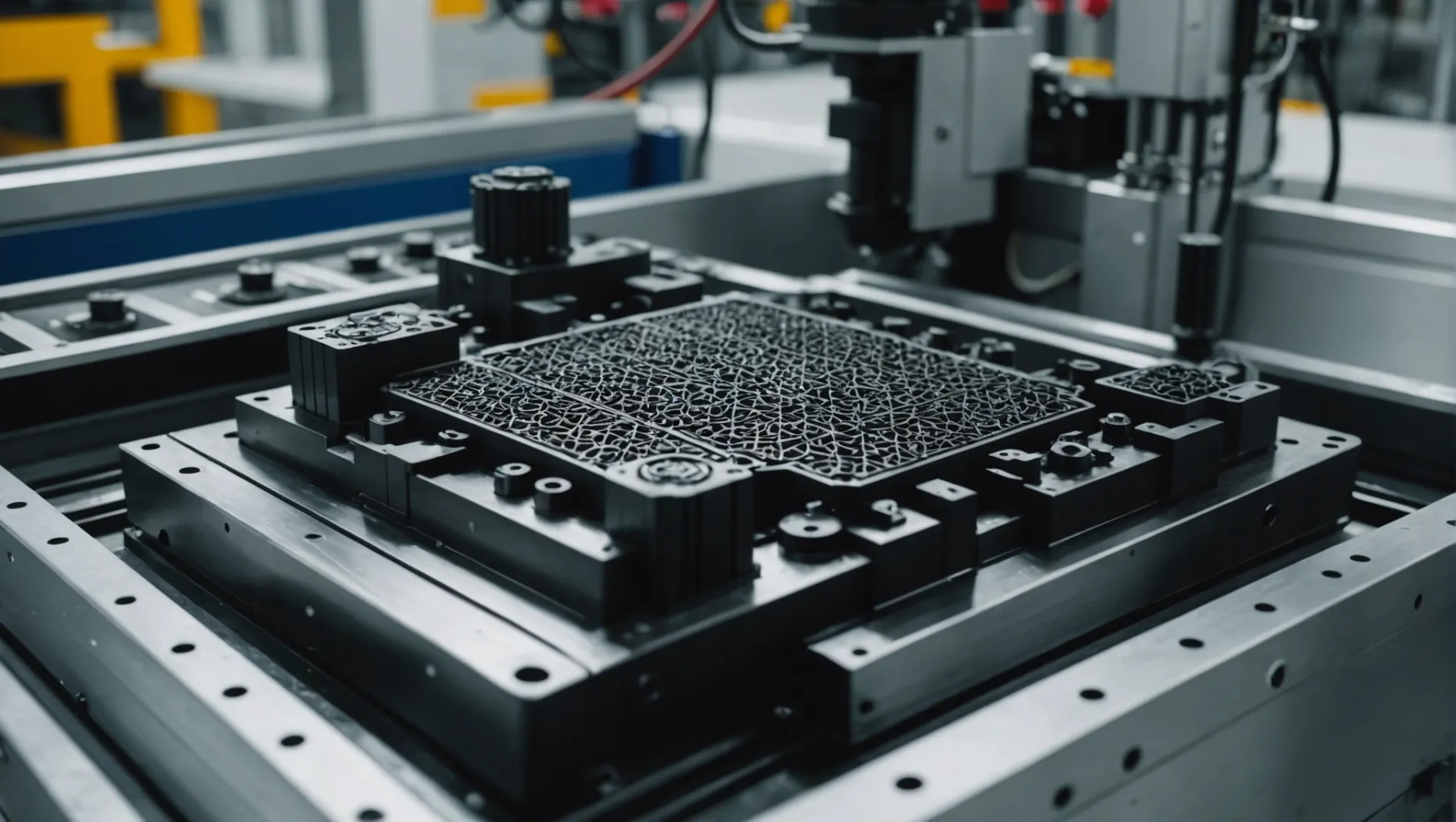
Enhancing Cooling Systems
An essential advanced technique involves optimizing the mold’s cooling system. Efficient cooling systems maintain consistent temperature distribution, minimizing the risk of temperature-related sticking issues. Consider implementing variable temperature control systems that adjust cooling rates based on real-time data. Such systems can reduce cycle times and improve product quality by maintaining optimal mold temperatures throughout the production cycle.
Anti-Stick Coatings
Applying specialized anti-stick coatings to molds can significantly reduce adhesion. These coatings create a barrier between the mold surface and the plastic, facilitating easier demolding. Options include PTFE-based coatings, which offer excellent non-stick properties and can withstand high temperatures. It’s crucial to select a coating that complements the specific plastic material being used to ensure compatibility and effectiveness.
Automation and Real-Time Monitoring
Leveraging automation technologies can enhance precision in injection molding operations. Implementing real-time monitoring systems allows for automatic adjustments to process parameters like temperature, pressure, and cooling rates. For instance, smart sensors can detect anomalies in mold conditions, enabling immediate corrective actions. This approach not only prevents sticking but also improves overall process efficiency.
Advanced Mold Design Innovations
Incorporating cutting-edge mold design features, such as collapsible cores or floating plates, can aid in reducing mold sticking incidents. These designs allow for easier ejection of complex shapes and reduce the stress exerted on molded parts during demolding. Additionally, integrating venting systems that utilize micro-venting technology can effectively release trapped gases, decreasing pressure build-up between the mold and the product.
Material Innovation and Modification
Exploring novel material formulations or modifying existing materials can prevent sticking issues. Research into low-viscosity polymers or the addition of specific fillers can enhance demolding performance. Furthermore, experimenting with hybrid material combinations could lead to improved flow characteristics and reduced adhesion properties.
For further insights into these advanced techniques, exploring more detailed research studies7 or industry case studies8 may provide valuable knowledge on successful implementations across various sectors.
Anti-stick coatings can withstand high temperatures.True
PTFE-based coatings are known for their high-temperature resistance.
Automation technologies decrease mold sticking incidents.True
Real-time monitoring and adjustments improve precision, reducing sticking.
Conclusion
By addressing mold design, optimizing process parameters, and selecting suitable materials, manufacturers can significantly reduce mold sticking issues. Implement these strategies for seamless injection molding operations.
-
Explore techniques for maintaining optimal mold temperatures efficiently.: This article delves into the intricacies of mold temperature, and its effects on various aspects of the molding process and offers insights into setting the … ↩
-
Discover strategies for designing molds with efficient exhaust systems.: Position of exhaust system in mold is very important. Although exhaust system design is not complicated, it plays a vital role in normal injection of mold. ↩
-
Explore how injection pressure influences demolding success.: Three, high injection pressure can force the mold open at the parting line. This creates flashing on the part, but more importantly, it can … ↩
-
Discover systems that ensure precise temperature control.: Our sensors for the monitoring of injection molding processes includes pressure sensors (direct, indirect, contactless) and temperature sensors. ↩
-
Learn strategies for optimizing injection speed effectively.: Adjustments to the switching position (S3) can also help overcome injection molding defects such as flash and poor appearance at the flow end. ↩
-
Explore efficient strategies for improving the demolding process.: Logic Corp.’s ICE process retracts the core slightly while the part remains in the cavity, held in place by ejectors, stripper plate, and/or shop air. ↩
-
Explore in-depth studies on advanced techniques for preventing mold sticking.: Low-surface-energy mold coatings can eliminate part sticking, reduce cycle time and increase mold life. ↩
-
Discover practical examples of advanced techniques implemented in industries.: Examining real-world case studies is an excellent way to gain insights into the practical application of injection molding techniques and … ↩