In the intricate world of injection molding, mold polishing stands as a pivotal process that elevates not just the appearance but the overall performance of products. Let’s delve into why this step is so essential and how we can master it together.
To effectively polish molds in injection molding, start with coarse abrasives, transition to finer ones, select appropriate tools, apply even pressure, and maintain a consistent polishing direction. Ensuring cleanliness and safety are critical precautions for optimal results.
While these basic steps lay a solid foundation, truly mastering mold polishing requires a deeper understanding of nuanced techniques and precautions. Let’s explore these insights together!
Mold polishing reduces surface defects in injection molded parts.True
Polishing smooths the mold surface, minimizing defects like weld lines.

Why Is Mold Polishing Crucial in Injection Molding?
Mold polishing significantly enhances the quality of injection molded products, impacting both aesthetics and functionality.
Mold polishing is crucial as it improves the surface quality of the mold, leading to better appearance and performance of injection molded parts. It reduces surface defects, enhances product release, and prolongs mold life, ensuring consistent production quality.
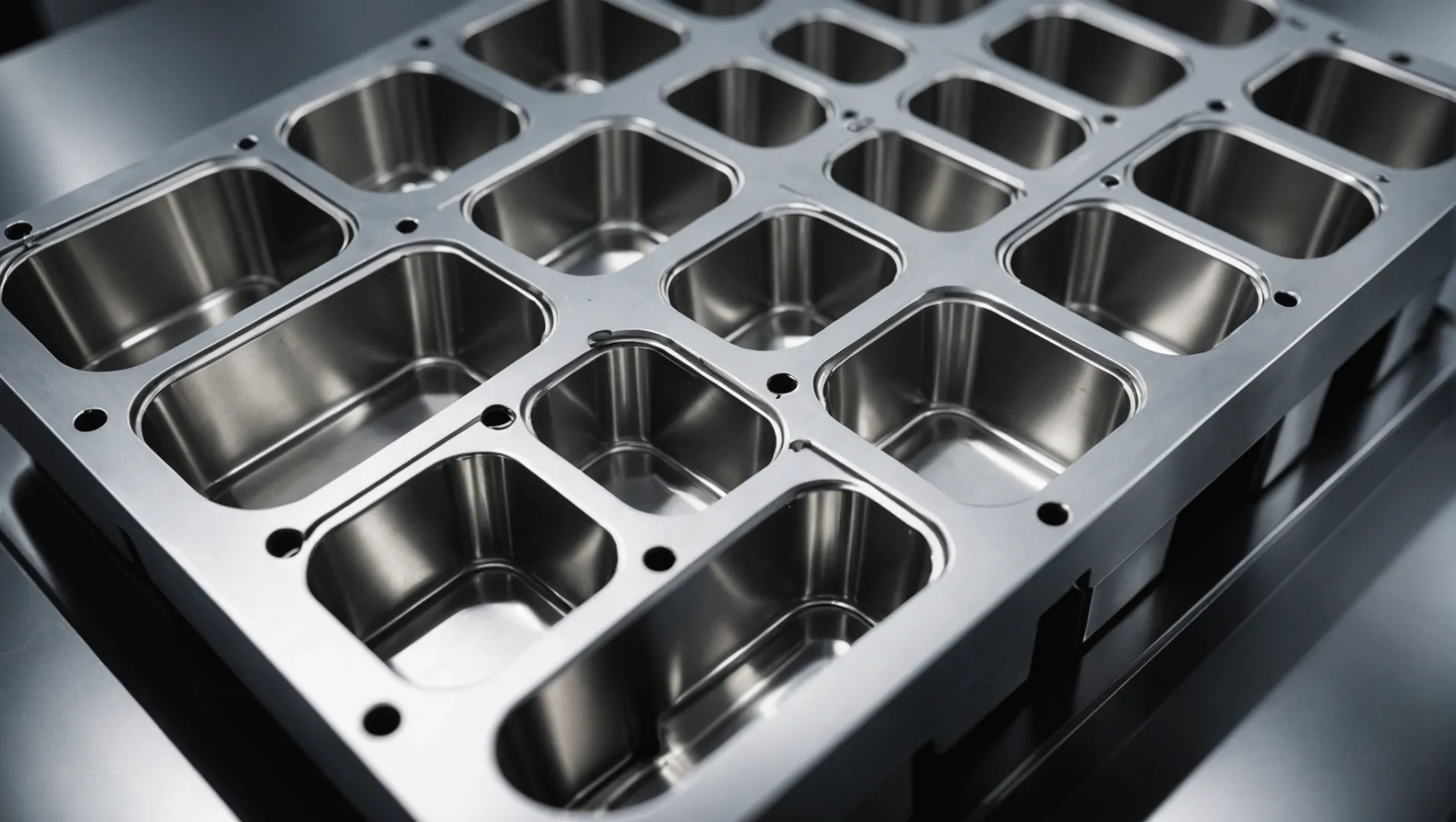
The Role of Mold Polishing in Quality Enhancement
In the world of injection molding1, mold polishing holds paramount importance. A polished mold results in products with superior surface finish, reducing post-processing needs. This is particularly crucial for high-gloss or transparent parts where surface quality directly affects visual appeal.
Polishing minimizes defects such as weld lines and flow marks, which can compromise the structural integrity of parts. By smoothing the mold’s surface, it also facilitates easier ejection of the parts, reducing cycle time and wear on the mold. This enhancement in mold quality leads to consistent product output, meeting stringent industry standards.
Economic and Functional Benefits
From an economic perspective, polished molds help in reducing production costs2. The initial investment in polishing pays off by lowering rejection rates due to fewer defects. Moreover, the lifespan of a polished mold extends significantly, as it is less prone to damage during production.
Functionally, a well-polished mold ensures uniform thickness in molded parts, which is vital for applications where precision is key. By ensuring even material flow, polishing also aids in maintaining dimensional accuracy across large production batches.
Environmental and Safety Considerations
In terms of environmental impact, polishing can contribute positively by reducing material wastage. Parts produced from well-polished molds often require less finishing and trimming, leading to less scrap generation.
Safety-wise, a polished mold reduces the risk of operator injury during part removal due to smoother surfaces. This aligns with industry safety standards3, ensuring a safer working environment.
Challenges and Solutions in Mold Polishing
Despite its benefits, mold polishing poses certain challenges. Over-polishing can lead to dimensional inaccuracies or weaken the mold surface. To counteract this, regular quality checks and professional expertise are essential to maintain balance.
Additionally, careful temperature control4 during polishing prevents overheating, which could otherwise warp the mold or affect its properties. Utilizing intermittent polishing techniques can help manage heat buildup effectively.
By addressing these aspects, manufacturers can leverage mold polishing not just as a cosmetic enhancement but as a strategic tool for improving injection molding efficiency.
Mold polishing reduces injection molding cycle time.True
Polished molds facilitate easier part ejection, thus shortening cycle times.
Unpolished molds produce parts with uniform thickness.False
Polishing ensures even material flow, critical for uniform part thickness.
How to Select the Right Tools for Mold Polishing?
Choosing the right tools for mold polishing is key to achieving a flawless finish in injection molding.
Selecting the appropriate tools for mold polishing involves understanding the specific requirements of each mold part. Use flat polishing machines for flat surfaces, handheld tools for curves, and choose abrasives based on mold material hardness.
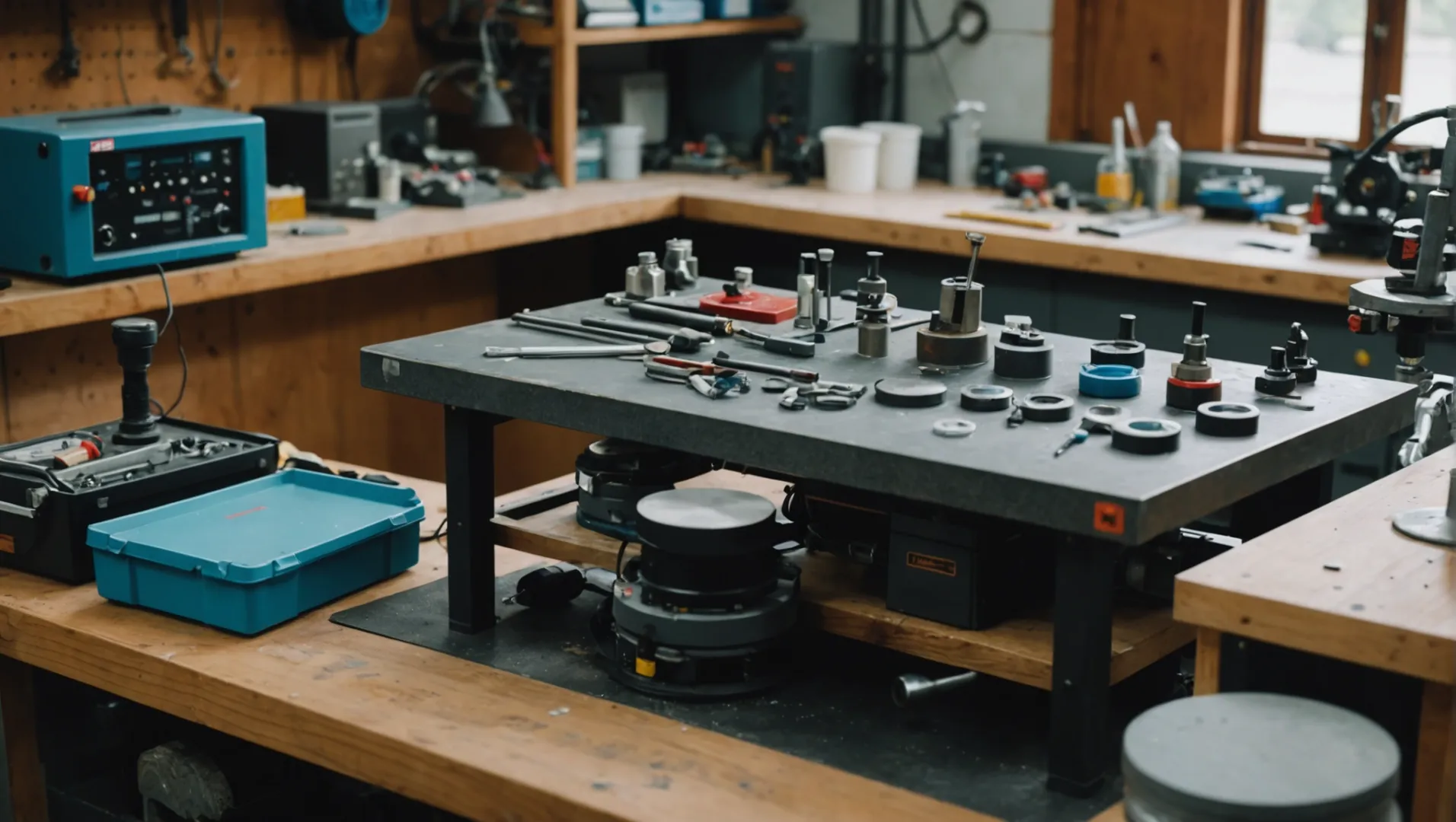
Understanding the Mold Material
The first step in selecting the right tools for mold polishing is understanding the material of the mold itself. Different materials respond differently to polishing techniques:
-
Hardened Steel Molds: For molds made from hardened steel, diamond abrasives are recommended due to their high hardness and precision capabilities. They can effectively remove surface imperfections without causing damage.
-
General Mold Materials: For less hard materials like aluminum or softer steels, silicon carbide or aluminum oxide abrasives are typically more suitable.
Choosing the Right Polishing Machines
The complexity of the mold design will dictate which polishing tools are most effective:
-
Flat Polishing Machines: Ideal for large, flat surfaces. They provide consistent pressure and even finish across expansive areas.
-
Handheld Polishing Tools: Best for curved or intricately shaped areas. These tools offer greater maneuverability and control in tight spaces.
-
Ultrasonic Polishing Equipment: Suitable for intricate and detailed parts where precision is paramount. These devices use high-frequency sound waves to achieve a smooth finish.
Selecting Abrasives and Polishing Pastes
Once you’ve chosen your machines, it’s crucial to pair them with the correct abrasives and polishing pastes:
Mold Material | Recommended Abrasives | Polishing Paste |
---|---|---|
Hardened Steel | Diamond | Diamond Paste |
General Steel | Silicon Carbide | Aluminum Oxide Paste |
Aluminum | Aluminum Oxide | Silicon Carbide Paste |
This choice should be tailored not only to the material but also to the desired surface finish level.
Ensuring Even Pressure and Correct Technique
The technique applied during polishing can significantly influence the outcome:
-
Pressure Control: Consistent pressure is crucial. Too much pressure can create new scratches, while too little can leave the surface unfinished.
-
Polishing Direction: Maintain a consistent direction, preferably following the mold’s texture or using a circular motion. This helps minimize scratching and achieves a smoother finish.
For more insights, consider exploring resources on polishing techniques for molds5 that provide visual guides and expert tips.
By carefully selecting and using the right tools, you not only improve the efficiency of the polishing process but also enhance the quality of the finished product. This systematic approach ensures that each mold meets high standards of performance and aesthetics.
Diamond abrasives suit hardened steel molds.True
Diamond abrasives are ideal for hardened steel due to their hardness.
Flat polishing machines are best for curved surfaces.False
Flat machines suit flat surfaces; handheld tools are better for curves.
What Safety Measures Should Be Taken During Mold Polishing?
Ensuring safety during mold polishing is crucial to prevent injuries and maintain a healthy work environment.
Key safety measures include wearing protective gear, controlling temperature, ensuring equipment safety, and maintaining cleanliness to prevent accidents and enhance efficiency.
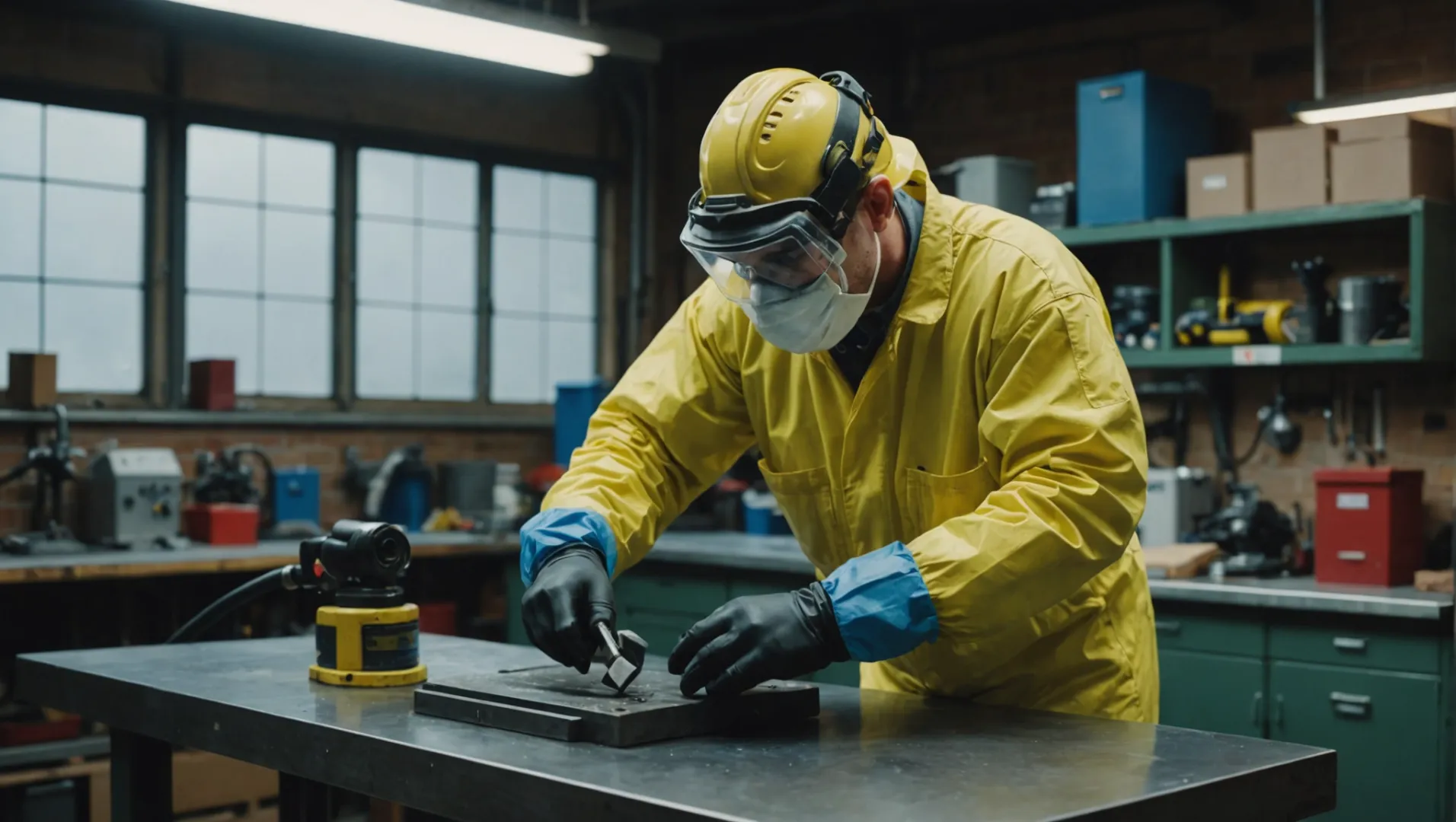
Importance of Safety in Mold Polishing
Mold polishing is an essential phase in injection molding, but it poses various risks if not handled properly. The process involves using abrasive materials that can generate dust and debris, which may be harmful if inhaled. Additionally, improper handling of tools can lead to physical injuries. Therefore, implementing safety measures is paramount to protect workers and ensure a smooth workflow.
Personal Protective Equipment (PPE)
Wearing appropriate protective gear6 is one of the most fundamental safety measures. Operators should wear masks to prevent inhalation of dust particles, goggles to protect their eyes from debris, and gloves to safeguard their hands against sharp objects and abrasives.
Equipment Safety
Ensuring the safe operation of polishing tools is critical. Before starting the process, inspect all equipment to ensure they are in good condition. Malfunctioning tools can cause accidents or damage the mold surface. It is also essential to follow the manufacturer’s guidelines for tool use and maintenance.
Temperature Control
The polishing process generates heat, which can affect both the mold and the operator. Excessive heat may alter the mold’s dimensions and compromise its integrity. Operators should control the speed and pressure applied during polishing to prevent overheating. Implementing intermittent polishing7 allows the mold to cool down, reducing the risk of heat-related issues.
Cleanliness and Workspace Organization
A clean workspace minimizes the risk of accidents. Before polishing, ensure that the mold surface is free from oil, dust, or any other impurities that could interfere with the process. Regular cleaning of the workspace prevents buildup of debris, which can lead to slips or contaminations.
Training and Professionalism
Mold polishing requires skilled professionals who understand the nuances of the process. Proper training ensures that operators are aware of potential hazards and know how to mitigate them effectively. Continuous education and practice help maintain high standards of safety and efficiency.
Implementing these safety measures not only protects workers but also enhances the quality and precision of mold polishing. By fostering a safe working environment, manufacturers can achieve better results and prolong the lifespan of their equipment.
Wearing PPE is optional during mold polishing.False
PPE is essential for safety, preventing injuries from dust and debris.
Intermittent polishing helps control heat buildup.True
Pausing allows molds to cool, reducing heat-related risks.
How Can Over-Polishing Be Avoided in Mold Production?
In mold production, over-polishing can lead to thinner surfaces and reduced mold strength, impacting longevity.
Avoid over-polishing by regularly inspecting surface quality, using precise pressure control, and adhering to specific surface finish requirements. Employ skilled operators to ensure optimal polishing levels.
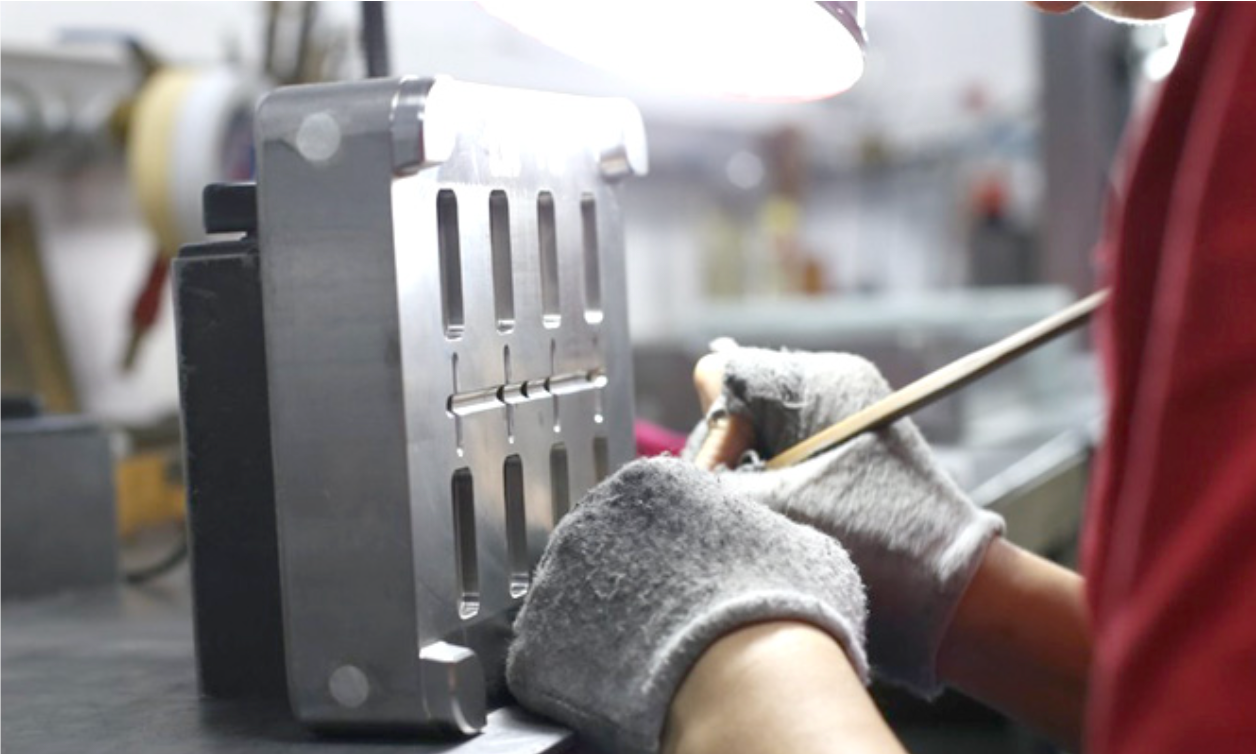
Understanding the Risks of Over-Polishing
Over-polishing in mold production can diminish the structural integrity of the mold. The thinning of surfaces not only affects the mold’s strength but also its ability to produce accurate and high-quality products consistently. Recognizing the signs of over-polishing early can prevent costly damage.
Regular Inspection
One effective strategy to avoid over-polishing is conducting regular inspections during the polishing process. This involves checking the surface quality frequently to ensure that it meets the necessary specifications without exceeding them. By doing so, operators can make timely adjustments to their techniques if signs of over-polishing appear.
Pressure Control Techniques
Maintaining precise pressure8 during the polishing process is crucial. Applying too much force can quickly lead to over-polishing, while insufficient pressure might not achieve the desired finish. A balanced approach ensures that the mold’s surface is polished just enough without compromising its thickness.
Adhering to Surface Finish Requirements
It is vital to adhere strictly to the defined surface finish requirements for each project. These standards provide a clear guideline on how much polishing is necessary. Operators should be familiar with these specifications and adjust their methods accordingly.
Employing Skilled Operators
Professional operators possess the expertise to determine the correct amount of polishing needed for each mold. Their experience allows them to select appropriate tools and techniques tailored to specific mold materials and designs. By utilizing skilled operators, manufacturers can significantly reduce the risk of over-polishing.
Balancing Heat and Time
The friction from polishing generates heat, which can negatively affect mold dimensions if not managed properly. It is important to monitor temperature levels and allow cooling periods during extended polishing sessions. This balance prevents excessive heat build-up that could exacerbate over-polishing effects.
By implementing these strategies, manufacturers can mitigate the risks associated with over-polishing, ensuring that their molds maintain optimal performance and durability throughout their production lifecycle.
Regular inspections prevent over-polishing in mold production.True
Frequent checks allow timely adjustments, avoiding excessive polishing.
Over-polishing strengthens the mold's structural integrity.False
Over-polishing thins surfaces, weakening the mold and reducing strength.
Conclusion
By adopting these tips and precautions, you can ensure superior mold polishing results that significantly enhance product quality. Reflect on these practices to boost efficiency and safety in your production process.
-
Explores why mold polishing is vital in injection molding.: Plastic injection mold polishing is a technique that helps to obtain smooth mold surfaces. It does this by removing the convex parts of the mold … ↩
-
Highlights cost-saving advantages of mold polishing.: The economy continues to downshift, capping growth in moldmaking. ↩
-
Details industry safety measures related to mold use.: When equipment is operating normally, it’s essential to avoid contact with any part of the machinery, except for the safety door and control panel of the inj … ↩
-
Discusses methods to manage heat during polishing.: Always move the brush laterally when it comes into contact with the workpiece to avoid creating circular dwell marks, especially in corners where a 90° or 180° … ↩
-
Discover advanced techniques and tips from industry experts.: Generally, mold polishing techniques use wool wheels, whetstone strips, and sandpaper for manual polishing. the mold polishing process. In other … ↩
-
Learn about essential protective gear to ensure personal safety.: Choose the correct personal protective equipment (PPE) while removing mold from damaged structures or during construction. ↩
-
Discover strategies for managing heat to prevent damage.: Common Mold Polishing Methods · 1. Physical Polishing · 2. Chemical Polishing · 3. Electrolytic Polishing · 4. Ultrasonic Polishing · 5. Fluid … ↩
-
Discover techniques for maintaining optimal pressure during mold polishing.: If you need a higher polish, try yellow diamond with a brush, then felt, then hand rub. I got the book from Gesswein. ↩