I recall when I first selected an injection molding machine. It was like trying to break a secret code.
The mold opening stroke in injection molding machines changes a lot. Machine size influences this stroke. Manufacturers and specific uses also play a role. Small machines have strokes between 150mm and 650mm. Bigger machines might even reach over 2000mm. Mold thickness increases with machine size. Thickness really grows larger as machines grow larger.
At first, these specifications confused me. I needed to think about both the size and how the machine’s details matched our production needs. Understanding if it was a small machine with a 150mm stroke or a large one over 2000mm was very important. I really wanted our chosen machine to fit our specific production demands well. The right parameters probably impact efficiency and product quality a lot. Experience showed me that no single solution fits everything. Each project needs its own unique specifications.
Small injection machines have strokes over 650mm.False
Small injection machines typically have mold opening strokes between 150mm and 650mm.
Large injection machines can exceed 2000mm stroke.True
Large injection machines, especially those over 500T, can have strokes reaching or exceeding 2000mm.
How Does Machine Size Affect Mold Opening Stroke?
Think about putting a big puzzle piece into a small space. Understanding machine size in mold opening feels like this.
Machine size is very important when deciding the mold opening stroke. Bigger machines deal with larger molds because of their long stroke ranges. Smaller machines suit compact molds because they have shorter strokes. Picking the right size probably leads to efficient injection molding processes. Efficient processes mean better results.
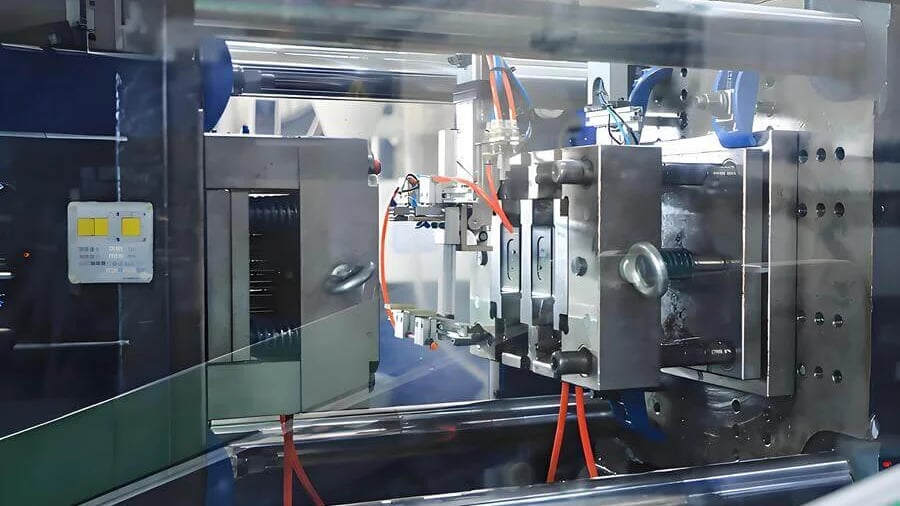
The Role of Machine Size in Mold Opening Stroke
When I first explored injection molding, it felt like solving a puzzle. Each machine follows its own rules, especially about mold opening strokes. This stroke is the distance a mold can open and is key as it decides which products you can produce.
I recall a factory tour with small machines from 30T to 100T. These machines had strokes from 150mm to 650mm. Imagine a 30T machine with strokes from 150mm to 530mm. Such a machine suits small, detailed parts. Medium machines from 100T to 500T1 have strokes from 600mm to 1500mm, handling larger molds.
Big machines, over 500T, really go beyond 2000mm in stroke. I once saw an 850T machine with a stroke from 500mm to 2100mm. It was truly impressive! These machines help with large-scale production.
Impact on Production Efficiency
Choosing the right machine size is like picking the right tool. A machine too small will have wear and face delays, while one that is too large wastes resources. Evaluating mold thickness2 makes this choice easier. Smaller machines handle thicknesses from 100mm to 400mm, whereas larger ones go over 1000mm. The right match matters.
Factors to Consider
Machine size is not the only thing to think about; the application, output volume, and material type matter too. Technology moves fast—new developments can influence choices significantly (technology advancements3). Industry experts provide tailored advice based on extensive experience.
Understanding equipment is about future-proofing your production line and ensuring long-term success.
Small injection machines have a max stroke of 650mm.True
Small machines typically range from 150mm to 650mm in opening stroke.
Large machines never exceed a 1000mm mold thickness.False
Large machines can accommodate mold thicknesses over 1000mm.
What Factors Influence Mold Thickness Capacity?
Have you ever thought about why mold thickness changes a lot in manufacturing? Explore the realm of injection molding to discover its mysteries.
Mold thickness depends on the size of the machine, the material and the design details. Smaller machines often deal with thinner molds. Larger machines probably handle thicker molds. The choice of material really affects mold thickness. Design details also have a big impact.
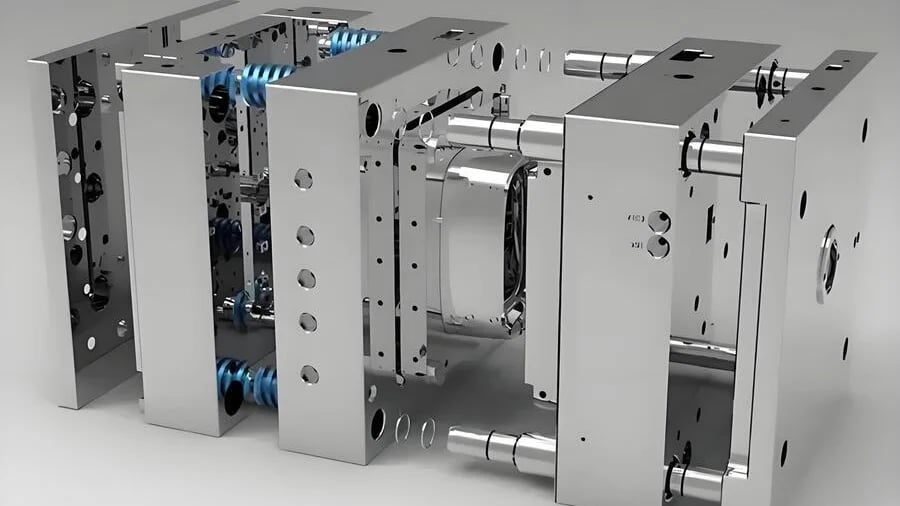
Machine Specifications
When I first started exploring injection molding, I was surprised. Machine size decides mold thickness. Small machines, like those between 30T to 100T, limit mold thickness to 400mm. It’s like stuffing too many clothes into a small suitcase. Large machines over 500T are different. They handle mold thicknesses over 1000mm easily.
One of the primary factors affecting mold thickness capacity is the machine size4. For instance, an 850T machine might accommodate molds from 450mm to 1850mm.
Material Properties
Picking the right material is like choosing a key ingredient in cooking. It either leads to success or failure. High-viscosity materials need thicker molds. It’s like dealing with very thick pancake batter. Every material’s heat and physical traits are important; they decide the best mold thickness.
The choice of material significantly impacts the feasible mold thickness due to their unique thermal and mechanical properties, influencing how they behave under pressure and heat. Material considerations5 are crucial in selecting the right combination of machine and mold design to achieve desired outcomes.
Design Requirements
Design details can change everything. Once, I worked on a project needing thin molds for detailed work. It felt like carving small designs into soap—complex yet satisfying. Simple designs allow thick molds, offering durability with ease during production.
The specific design of a product can dictate the required mold thickness. Complex designs with intricate details might necessitate thinner molds for fine detailing and accuracy in the final product, while simpler designs can often utilize thicker molds for increased durability and stability during production. Design intricacies6 play a significant role in planning the mold thickness capacity.
Temperature and Pressure Settings
Temperature and pressure settings impact mold thickness a lot—picture spreading butter on toast; if butter is too cold, it won’t spread well. Higher temperatures allow even material flow, but high pressures may cause unfilled areas or warping, just like squishing a sandwich too hard.
Temperature and pressure settings during injection molding are vital in determining mold thickness capacity as higher temperatures lead to more uniform material flow potentially allowing for thinner molds while increased pressure required for thicker molds might demand adjustments to avoid defects like warping or incomplete filling. Process conditions7 are essential in optimizing mold thickness for quality and efficiency.
In summary, knowing these things is key to deciding on mold thickness wisely in injection molding—it’s like solving a puzzle where every part needs to fit perfectly.
Small injection machines have a max stroke of 650mm.True
Small injection molding machines typically have a maximum opening stroke of up to 650mm.
Medium injection machines can't exceed 700mm thickness.False
Medium-sized injection molding machines can accommodate mold thicknesses up to 1250mm.
Why Is Proper Mold Installation Crucial for Efficiency?
Baking a cake in a crooked pan is difficult. Proper mold installation is just as important in injection molding. It saves time. It also saves money. Proper installation is essential.
Correct mold placement is key for success in injection molding. It keeps machines running well, cuts down on errors and reduces breaks. The mold must fit perfectly according to the machine’s rules. This fit is important. It makes products better and speeds up production. It saves money and increases output.
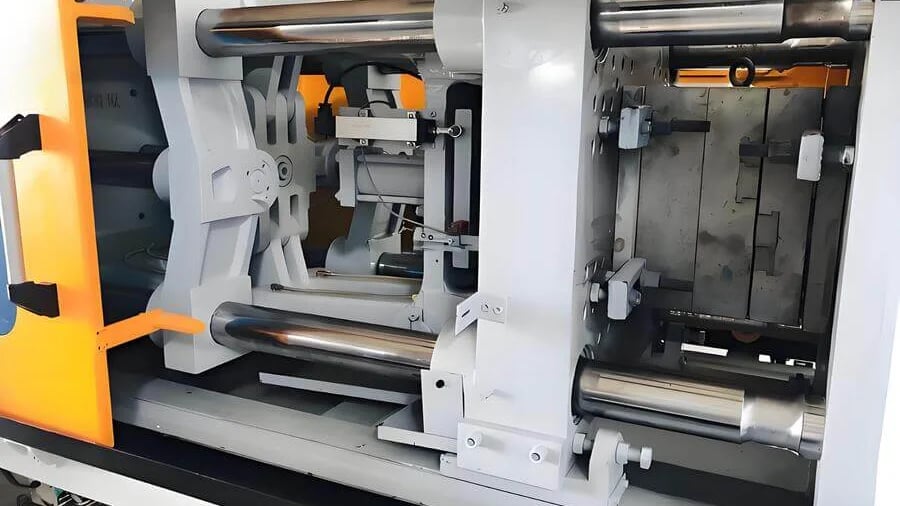
Understanding the Role of Mold Installation
I remember my first time setting up an injection molding machine. It felt like solving a big puzzle. Every part had to fit right. Proper mold installation is vital as it shapes the entire process. The mold must align with machine specifications8 like mold opening stroke and thickness. Different machines have their own ways, just like each baking recipe needs specific time and temperature.
Reducing Production Time with Proper Setup
Think of mold installation like preparing cooking ingredients. If everything is ready, the process runs smoothly. Well-installed molds let machines work fast, shortening cycle times. Small errors lead to problems like warping or incomplete fills—it’s akin to when a cake doesn’t rise because of missing baking powder.
Cost Implications of Improper Mold Installation
Mistakes are costly. My first failed batch of cookies taught me this lesson. Incorrect mold setup wastes materials and causes expenses. Poor installations lead to frequent breakdowns, meaning more maintenance, which is pricey. Sticking to setup instructions saves money; it’s like following a recipe to avoid wasting ingredients.
Enhancing Product Quality
Quality matters in everything, from baking to manufacturing. A well-baked cake makes people want more, just as properly installed molds produce high-quality products. Accurate alignment prevents defects, keeping product quality steady and reducing the need for fixes after production—ensuring customers stay happy with great products.
The Importance of Machine Compatibility
Choosing the correct mold is like finding the right tool for a job. Each molding machine has unique traits affecting mold compatibility; molds must fit these traits to prevent machine strain and allow smooth operation—similar to picking the right cake pan size. Proper planning is crucial; considering machine specifications9 early avoids costly errors later, much like reading a recipe before cooking ensures good results.
Small injection machines have a max stroke of 650mm.True
Small injection molding machines typically have a mold opening stroke up to 650mm.
All injection machines have the same mold thickness capacity.False
Injection molding machines vary in mold thickness capacity based on size and type.
How Do I Choose the Right Injection Molding Machine?
Have you ever felt stressed picking the best injection molding machine? Many people feel the same. I will share my story and ideas to help you choose wisely.
Selecting the correct injection molding machine involves understanding several important factors. The size of the mold and shot size matter a lot. Tonnage and machine type are also crucial. Specific production needs should guide decisions. Think about mold opening stroke and thickness range for effective manufacturing. Hydraulic, electric and hybrid machines offer different benefits. Match these types to your application requirements and budget. Choose wisely.
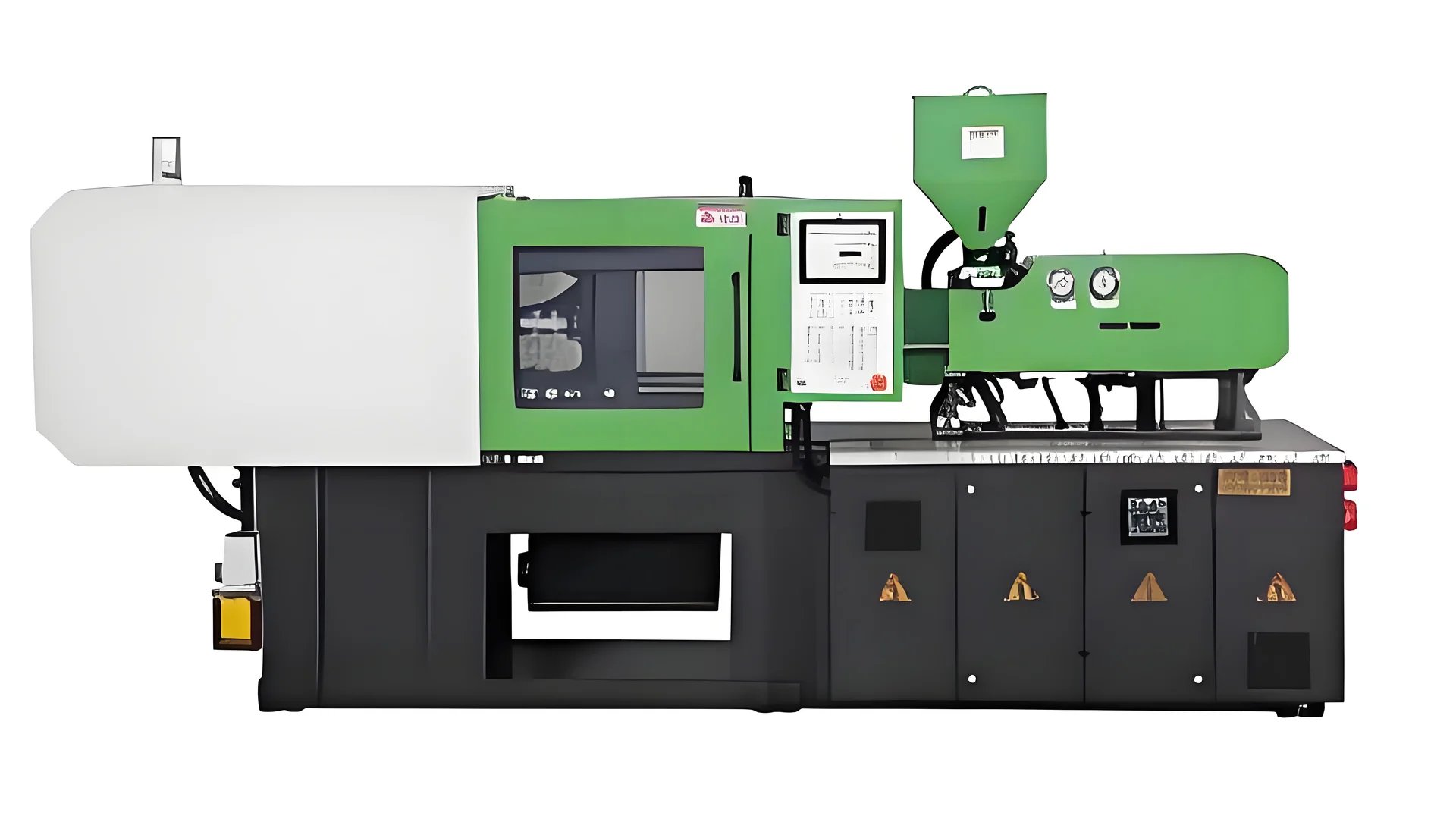
Evaluating Mold Size and Machine Capacity
Imagine walking into a big warehouse full of injection molding machines. I was amazed by the different types offering speed and precision. The first important step was figuring out the right mold size for my project. Small machines, from 30T to 100T, provided mold opening strokes between 150mm and 650mm. These machines were ideal for my tiny projects where space was tight. For medium tasks, machines ranging from 100T to 500T, with strokes ranging from 600mm to 1500mm, worked well. Larger molds fit into machines over 500T, accommodating strokes up to 2000mm or more. This sizing guide10 was my essential tool. I checked it often.
Understanding Shot Size and Tonnage
Then came the tricky part of shot size and tonnage. Shot size means the amount of material injected. Tonnage is the force needed to keep the mold shut during injection. It was vital to match these with product details to avoid mistakes in production. I always checked these factors for precise production efficiency11. This was a very important part of my process.
Choosing Between Hydraulic, Electric, and Hybrid Machines
Choosing between hydraulic, electric, and hybrid machines was like deciding between an old truck, a fast sports car or a flexible SUV. Each had unique benefits:
- Hydraulic Machines: Strong and affordable; perfect for big production runs.
- Electric Machines: Impressive precision and energy savings; great for detailed work.
- Hybrid Models: Combine benefits of both hydraulic and electric; versatile for many uses.
Matching these to my application needs12 helped me decide wisely.
Considering Mold Thickness Range
Mold thickness was another key factor:
- Small Machines: Suited thicknesses from 100mm to 400mm.
- Medium Machines: Dealt with thicknesses from 150mm to 700mm.
- Large Machines: Handled molds up to 1000mm or more.
Checking mold thickness with machine capacity ensured smooth operational performance13 without damage—like getting jeans that fit just right!
Cost-Effectiveness and Efficiency
Finally, let’s discuss money because everybody loves saving a little, right? Initially focusing on price made sense but soon realizing long-term savings mattered more:
- Machines with higher energy efficiency (like electric ones) promised lower running costs despite higher initial prices.
- Balancing budget against potential savings in production efficiency14 and maintenance proved smart.
To sum up, selecting the right injection molding machine felt like mixing ingredients for a winning recipe—each part tailored to my special production needs ensuring efficiency and cost savings.
Small machines have a mold opening stroke up to 650mm.True
Small injection molding machines have strokes between 150mm and 650mm.
All injection machines have a uniform mold thickness range.False
Mold thickness ranges vary by machine size, not uniform across all.
Conclusion
Injection molding machine specifications vary by size and application, with small machines having strokes of 150-650mm and thicknesses of 100-400mm, while large machines exceed 2000mm and 1000mm respectively.
-
Explore detailed specifications for medium-sized injection molding machines. ↩
-
Discover optimal mold thickness ranges for various machine sizes. ↩
-
Learn about new technologies enhancing injection molding processes. ↩
-
Explore how machine size directly affects mold thickness capacity. ↩
-
Learn why material choice impacts feasible mold thickness. ↩
-
Discover how product design dictates mold specifications. ↩
-
Find out how settings affect mold thickness decisions. ↩
-
Learn how adhering to mold specs optimizes efficiency and quality. ↩
-
Discover how machine specs influence molding efficiency and quality. ↩
-
Learn industry standards for matching mold sizes with machine capacities. ↩
-
Discover strategies to optimize production efficiency in molding processes. ↩
-
Understand which machine types suit different manufacturing needs. ↩
-
Explore how mold compatibility affects machine performance. ↩
-
Assess long-term cost benefits versus initial investment in machines. ↩