Mold inserts might sound like a technical detail, but they play a huge role in shaping the products we use every day, from cars to gadgets.
Mold inserts, precisely designed for molds, enhance accuracy and flexibility, easing maintenance and boosting product quality across industries.
When I first started exploring mold design, the intricacies of mold inserts seemed daunting. But as I delved deeper, I realized their potential to transform production efficiency. From the shape that must sync with the product’s contours to the exacting dimensions that ensure no room for error, every aspect is meticulously crafted. For instance, imagine a slender rod insert fitting perfectly into a complex internal structure of a plastic product, enhancing both its precision and appeal.
Material choice is another critical factor. Selecting the right material, like P20 steel or beryllium bronze, can significantly impact the insert’s durability and performance. I recall my surprise at how beryllium bronze, with its exceptional thermal conductivity, could speed up cooling times in die-casting molds, making the whole process faster.
Understanding mold inserts also means grasping their practical applications. Whether it’s enabling easier maintenance by replacing only damaged parts or improving product quality by ensuring precise fits and finishes, inserts are indispensable. They even allow for versatile molds that can adapt to create different products with minimal changes.
Through these insights, I’ve come to appreciate mold inserts not just as components but as key players in advancing manufacturing technology. They’re the unsung heroes behind many high-quality products we take for granted today.
Mold inserts improve product quality in manufacturing.True
Mold inserts enhance precision, ensuring higher quality products.
Mold inserts are rarely used in the automotive industry.False
Mold inserts are crucial in automotive manufacturing for precision.
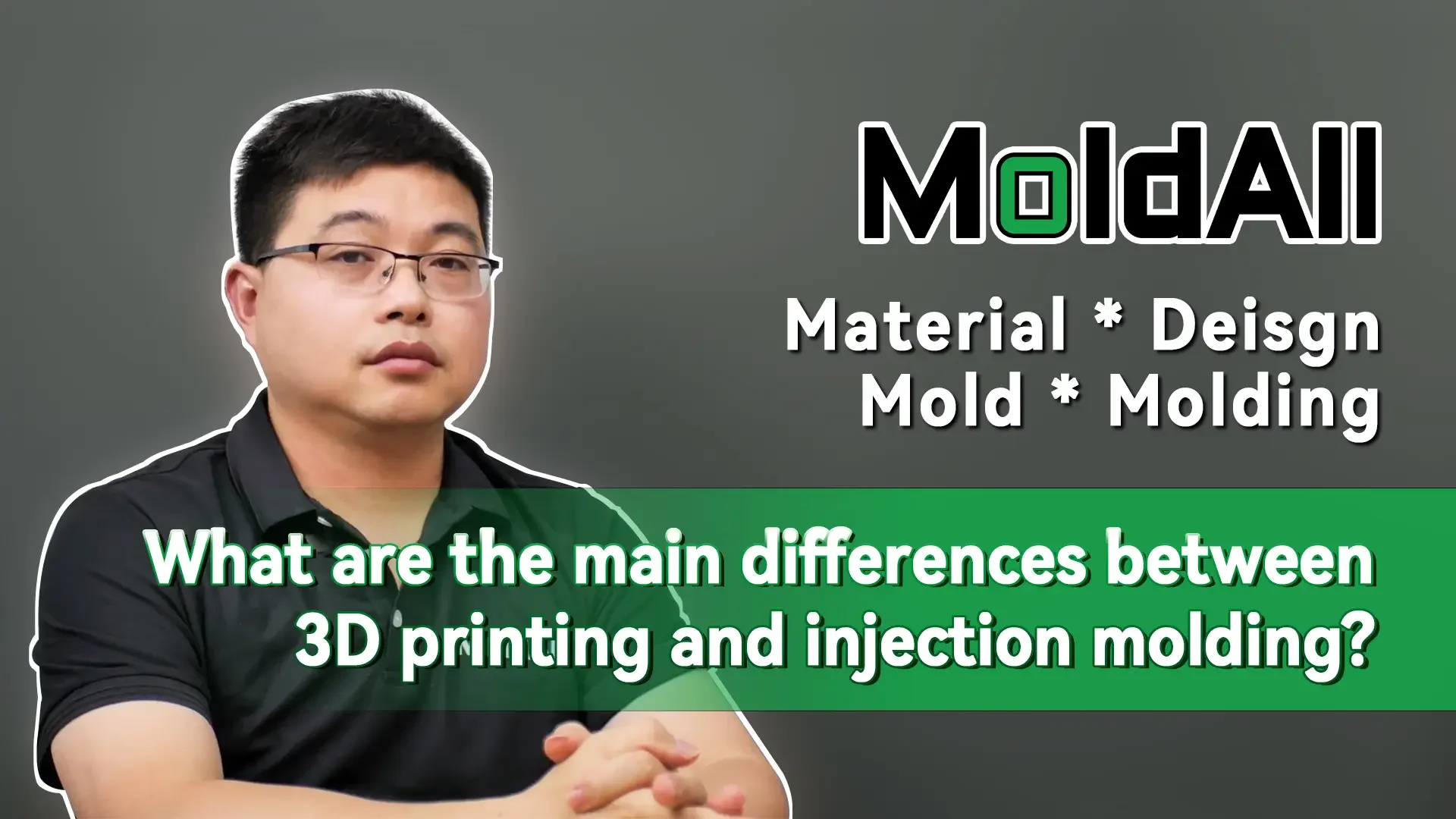
- 1. Why is shape design crucial in mold inserts?
- 2. How Do Dimensional Accuracy and Fit Impact Insert Performance?
- 3. Why Is Material Selection Crucial for Mold Inserts?
- 4. How Do You Connect Mold Inserts Effectively?
- 5. How Do Mold Inserts Improve Product Quality?
- 6. How Do Inserts Make Molds More Versatile?
- 7. Conclusion
Why is shape design crucial in mold inserts?
Imagine crafting a mold insert so perfect it feels like magic in manufacturing.
Shape design in mold inserts is crucial for crafting complex geometries, minimizing stress, easing demolding, enhancing product quality, and prolonging mold life.
Accommodating Complex Geometries
I remember the first time I was tasked with designing a mold for a product that seemed impossible to replicate. It had these intricate internal structures that required the precision of a surgeon. That’s when I realized the true power of shape design in mold inserts. By crafting inserts as slender rods or blocks, I could fit them into the tiniest spaces. For products with side holes or undercuts, slider inserts with a gentle slope made it possible for the mold to open and close smoothly, like a well-rehearsed dance.
One key aspect of mold insert design is its ability to adapt to the complex internal structures1 of products.
Stress Reduction and Longevity
I once faced a situation where my inserts kept wearing out faster than anticipated. It was frustrating until I learned about chamfers and fillets, those little design tweaks that make a world of difference. Chamfers ranging from 30° to 45° and fillets of 0.5-3mm not only prevented damage during installation but also distributed stress evenly, which significantly extended the life of my inserts. This small adjustment saved me both time and money.
Inserts often have chamfers or fillets to minimize stress concentrations and prevent damage during installation.
Enhancing Mold Efficiency
Deep holes used to be my nemesis. Processing them was a nightmare until I discovered that converting these complex parts into separate inserts made everything simpler. Suddenly, I could process them with specialized tools, and even perform precise heat treatment without affecting the rest of the mold. This approach was a game-changer in terms of efficiency.
Incorporating properly designed inserts2 improves mold efficiency by simplifying the processing of complex parts.
Ensuring Product Quality
Precision is everything in my line of work. The first time I saw flash formation due to poor dimensional tolerance, I knew I had to up my game. By ensuring that the dimensional tolerance was within ±0.01 – ±0.05mm, I could maintain consistency in product appearance and dimensions. It’s the kind of attention to detail that makes a product not just good, but exceptional.
Designing inserts with high dimensional accuracy is crucial for maintaining product quality.
Versatility and Adaptability
Versatility is a hidden gem in mold insert design. Being able to swap out inserts for different product variations without redoing the entire mold has been a lifesaver. Whether it’s adding cooling channels or exhaust grooves, this adaptability not only enhances functionality but also boosts efficiency dramatically.
Mold inserts provide versatility by allowing for structural changes without altering the entire mold.
Design Aspect | Description | Examples |
---|---|---|
Shape Design | Matches product geometry | Slender rods, slider blocks |
Chamfers/Fillets | Reduces stress concentration | 30° chamfers, 1mm fillets |
Dimensional Tolerance | Ensures fit accuracy | ±0.01mm for small inserts |
Versatile Features | Adds specific functions | Cooling channels, exhaust grooves |
Understanding these principles was like unlocking a new level in mold design for me. It wasn’t just about fitting a part; it was about enhancing the entire manufacturing process from quality to cost efficiency.
Chamfers in mold inserts are always 45°.False
Chamfers typically range from 30° to 45°, not always 45°.
Mold inserts can include cooling channels.True
Inserts can have features like cooling channels to enhance functionality.
How Do Dimensional Accuracy and Fit Impact Insert Performance?
Ever wondered how the tiniest details can make or break a design? Dive into the world of dimensional accuracy and fit, and discover their pivotal role in insert performance.
Dimensional accuracy and fit are crucial for insert performance, enhancing product quality and manufacturing efficiency by reducing defects and increasing part durability.
The Importance of Dimensional Accuracy
I remember my first big project in mold design—it’s funny how these moments stick with you. I was sweating bullets over getting the dimensions right. See, dimensional accuracy is like the secret ingredient that ensures inserts nestle perfectly into mold cavities. Imagine building a puzzle where every piece has to fit just right; that’s the challenge we face.
A precise fit prevents defects such as flashing, where excess material leaks out, ruining the finish. This accuracy is typically achieved by maintaining tight tolerances, usually between ±0.01 to ±0.05mm, depending on how precise we need to get.
Factors Influencing Dimensional Accuracy:
- Tolerance Levels: I’ve learned that different applications demand varying tolerance levels. For instance, when working on precision injection molds3 for tiny parts, the tolerances are much tighter than for larger, less detailed components.
- Manufacturing Processes: Techniques like CNC machining, paired with quality control measures such as CMM (Coordinate Measuring Machine) inspections, play a crucial role in hitting those high accuracy marks.
The Role of Fit in Insert Performance
Fit is like the unsung hero in insert performance. It’s about how snugly the insert aligns within the mold cavity. A snug fit ensures stability—no one wants their inserts wandering around causing chaos! An improper fit can lead to insert displacement or even damage from thermal expansion.
Types of Fit:
- Interference Fit: This is what I rely on when a secure hold is non-negotiable. Here, the insert is a tad larger than the cavity, installed either by cold pressing or by heating the cavity first.
- Clearance Fit: This allows for easier insertion and removal but might need additional measures to keep everything in place.
Connection Design for Optimal Insert Fit
You know what really sticks out when working with inserts? Connection designs. They ensure that inserts remain stable during use. Common methods include interference fit, threaded connections, and pin positioning—each with its own perks:
Connection Type | Benefits |
---|---|
Interference Fit | Provides secure, permanent fitting |
Threaded Connection | Allows easy removal and replacement |
Pin Positioning | Ensures precise alignment |
For instance, threaded connections4 are perfect for inserts that need regular maintenance or swapping out, such as exhaust inserts in die-casting molds.
Material Selection’s Impact on Fit and Performance
The right material choice can transform both fit and performance. It’s like choosing the right shoes for a hike—materials matter! Mold steels like P20 offer excellent durability for general purposes, while copper alloys5 excel in specific scenarios with superior thermal conductivity.
- Mold Steel: Ideal for general use with good wear resistance.
- Copper Alloys: Perfect when heat dissipation is key.
- Hard Alloys: Best for high-wear environments due to their extreme hardness.
Selecting materials based on the specific needs of the insert can greatly enhance both performance and lifespan.
Application of Inserts in Molds
Inserts are game-changers in mold performance. They simplify complex structures and make maintenance a breeze. Let me tell you about a time when…
- Improving Product Quality: High-precision inserts can dramatically improve surface smoothness and dimensional accuracy, especially for products needing exact specs.
- Versatility: Inserts enable molds to produce a variety of products by simply swapping them out for different shapes.
These examples highlight why precise dimensional accuracy and a suitable fit are crucial in ensuring optimal insert performance within molds.
Explore further insert design strategies6 to discover how innovative approaches can boost your production outcomes and product quality.
Dimensional accuracy prevents flashing defects.True
Tight tolerances ensure inserts fit well, preventing excess material seepage.
Interference fit allows easy removal of inserts.False
Interference fit is secure and permanent, not ideal for easy removal.
Why Is Material Selection Crucial for Mold Inserts?
Ever wonder why picking the right material for mold inserts is such a big deal? It’s like choosing the perfect foundation for your dream home – it’s all about longevity and quality.
Selecting appropriate materials for mold inserts is essential to ensure durability, heat resistance, and superior product quality, resulting in improved production efficiency and a longer mold lifespan in injection molding.
Understanding Mold Insert Materials
I remember the first time I had to choose a material for mold inserts. I was overwhelmed, much like picking the right fabric for a bespoke suit. It’s not just about what looks good on paper but understanding the role each material plays in enhancing production efficiency7 and prolonging mold life. Here’s a quick guide to some popular materials and where they shine:
Material | Properties | Applications |
---|---|---|
P20 Steel | Balances toughness with workability | General inserts |
H13 Steel | High wear resistance | Molds for glass fiber |
Copper Alloy (Beryllium Bronze) | Efficient thermal management | Complex designs needing heat dissipation |
Tungsten Carbide Hard Alloy | Unmatched durability | Extreme wear environments |
Influence of Material Properties on Performance
The material properties8 are like the DNA of mold inserts—they determine everything. For example, P20 steel is my go-to for general inserts because it balances toughness with workability. On the other hand, when dealing with materials like glass fiber that demand high wear resistance, I prefer H13 steel.
Design Considerations in Material Selection
When I design molds, the complexity of the structure often dictates the material choice. It’s like deciding whether you need a sturdy hiking boot or a sleek dress shoe. Copper alloys, particularly beryllium bronze, are lifesavers for designs needing efficient thermal management. And when durability is non-negotiable, tungsten carbide hard alloy steps up to the plate.
Practical Applications of Mold Inserts
In real-world applications, mold inserts can be the unsung heroes of efficiency and cost-effectiveness. They allow mold designers9 like me to replace worn parts without a complete overhaul of the mold. This not only slashes operational costs but also minimizes downtime.
Precision-manufactured inserts guarantee dimensional accuracy, which is crucial for maintaining the quality and reliability of finished products. By strategically choosing insert materials, manufacturers can optimize production processes and enhance product quality while reducing long-term costs. It’s essential to grasp the unique properties and applications of different materials to design molds that not only meet but exceed expectations.
Copper alloy is suitable for high heat dissipation molds.True
Copper alloys have excellent thermal conductivity, ideal for heat dissipation.
Tungsten carbide is used for general injection molds.False
Tungsten carbide is used in high-wear environments, not general molds.
How Do You Connect Mold Inserts Effectively?
Diving into mold insert connections is like finding the perfect puzzle piece—each method has its unique fit and function.
Effective mold insert connection uses interference fit, threaded connection, and pin positioning fit for secure alignment, tailored to design and operational needs.
Understanding the Basics
Mold inserts are like the unsung heroes in injection molding10. They offer incredible flexibility and precision. I remember the first time I realized how choosing the right connection method could make or break a project. It hit me hard how much these choices impact performance and longevity.
Interference Fit
Think of interference fit as the snug hug your favorite sweater gives you. The insert’s diameter is slightly larger than the mold’s hole, creating a secure hold. I’ve learned that cold pressing is perfect for smaller inserts, while hot fitting is the go-to for larger pieces. Just last month, I was working on a complex mold with deep grooves. Using interference fits made the job seamless.
Advantages | Considerations |
---|---|
Secure fit | Requires precise measurement |
No additional hardware | Potential for stress |
Cold pressing is suitable for smaller inserts, while hot fitting involves expanding the hole with heat before inserting the component.
Threaded Connection
Threaded connections are my trusty tool when frequent insert removal is needed. With external threads on the insert and internal threads on the mold, swapping parts feels as easy as changing light bulbs. During one hectic week, we had to repeatedly replace parts in a die-casting11 mold. This method saved us so much time and headache.
Consider this method in situations where molds undergo frequent maintenance.
Pin Positioning Fit
When it comes to precision, pin positioning fits are unbeatable. They remind me of those precise jigsaw puzzles where every piece clicks perfectly into place. By using pins through holes in both insert and mold, alignment is spot-on. It’s ideal for those high-precision molds with tight tolerances.
- Advantages: Ensures accurate alignment
- Ideal For: High-precision molds with tight tolerances
Pin positioning12 ensures no movement during injection, maintaining consistent part quality run after run.
Application Examples
- Injection Molding: Often employs interference fits due to their simplicity and strength.
- Die Casting: Frequently utilizes threaded connections for ease of replacement during maintenance.
- Precision Molds: Benefit from pin positioning fits to maintain exact tolerances throughout long production cycles.
Understanding these methods not only helps in optimizing mold design but also in enhancing product quality13. Each method’s suitability depends on factors like material, mold complexity, and production requirements.
Interference fits require additional hardware.False
Interference fits do not require additional hardware; they rely on precise measurements.
Threaded connections are ideal for frequent maintenance.True
Threaded connections allow easy removal and replacement, suiting frequent maintenance needs.
How Do Mold Inserts Improve Product Quality?
Ever wondered how mold inserts can transform the quality of manufactured products?
Mold inserts improve product quality by offering precise design flexibility, optimal material choices, and enhanced dimensional accuracy, leading to superior surface finishes, structural integrity, and fewer manufacturing defects.
I remember the first time I learned about mold inserts—it was like discovering a secret ingredient in a recipe that everyone loves. These little game-changers have made a big difference in my work as a designer. They allow me to tweak designs with incredible precision, which is crucial when you’re trying to balance aesthetics and functionality.
Design Flexibility and Precision
Mold inserts allow for intricate shape design14 adjustments without compromising the overall mold structure. For instance, slender rods can be used for complex interiors while thin plates suit products with reinforcing ribs. This flexibility ensures designs meet exact specifications.
Incorporating chamfers or fillets at insert edges prevents scratching and stress concentration, enhancing the mold’s longevity. The precision in dimension design15 ensures that inserts fit perfectly, maintaining high tolerance levels. Such precision is crucial in molds requiring tight dimensional control, where even minor discrepancies can lead to defects.
Insert Design | Purpose |
---|---|
Shape Design | Fits complex structures |
Dimension Design | Ensures tight tolerances |
Material Selection for Enhanced Quality
Choosing the right materials16 for inserts is vital. Mold steel like P20 or H13 offers durability, with the latter being ideal for high-pressure scenarios. Copper alloys like beryllium bronze provide excellent thermal conductivity, vital in molds needing rapid heat dissipation.
Hard alloys such as tungsten carbide are preferred in high-wear environments, ensuring inserts withstand rigorous use. This material choice directly affects the insert’s performance and longevity, contributing to the product’s quality.
Improved Processing and Maintenance Efficiency
Inserts simplify the processing of complex mold features, such as deep holes or narrow grooves. By allowing these to be machined separately, inserts improve efficiency and reduce processing complexity. They also enable targeted heat treatments to enhance hardness without affecting the entire mold.
Furthermore, inserts facilitate easy maintenance and replacement17, reducing downtime and costs. When inserts wear out, they can be quickly replaced without impacting the main mold body, ensuring continuous production without compromising product quality.
Enhancing Surface Finish and Dimensional Accuracy
When it comes to appearance—especially for transparent plastics—surface finish is key. High-precision machining ensures that inserts meet stringent requirements, leading to products that look and fit great.
Additionally, inserts help control critical dimensions by allowing precise adjustments during the design phase. This capability is particularly beneficial in producing parts with exact matching dimensions, ensuring consistent quality across production runs.
Versatility Through Mold Inserts
Integrating special features18 into molds using inserts feels like adding secret weapons to my design arsenal. Whether it’s cooling channels or exhaust grooves, these features enhance functionality and product quality.
The adaptability of inserts also means I can easily swap them out for different shapes or features, increasing mold utility and reducing costs—it’s like getting multiple products from one setup.
Mold inserts improve design flexibility in manufacturing.True
Inserts allow intricate shape adjustments without compromising mold structure.
Copper alloys are unsuitable for molds needing rapid heat dissipation.False
Copper alloys, like beryllium bronze, offer excellent thermal conductivity.
How Do Inserts Make Molds More Versatile?
Have you ever marveled at the flexibility and precision that inserts bring to mold design?
Inserts enhance mold versatility by allowing adaptable designs, simplifying maintenance, and improving quality. They enable interchangeable parts, reducing costs and boosting manufacturing efficiency.
Design Adaptability with Inserts
Picture this: you’re working on a mold for a product with a myriad of intricate shapes and features. Instead of reworking the entire mold each time, inserts come to the rescue. They let me tweak the design easily, thanks to their ability to modify specific mold features without overhauling the whole structure. I’ve seen this firsthand when designing for products needing complex geometries like side holes or undercuts. Using slider inserts19, I can achieve these shapes effortlessly, ensuring precision in reinforced rib structures with just a thin plate insert.
Improved Maintenance and Cost Efficiency
I remember the days when maintaining molds was a tedious task. But with inserts, things are so much simpler. If an insert gets worn out, you just swap it for a new one—no need for lengthy repairs or replacements. Imagine the wear and tear an injection mold faces when exposed to high-pressure plastic melts. By opting for wear-resistant materials like H13 steel20, I’ve managed to significantly extend the mold’s life. Plus, with threaded connections, replacing inserts during maintenance is a breeze, optimizing efficiency like never before.
Insert Type | Material | Application |
---|---|---|
Wear-resistant | H13 Steel | High-pressure molds |
Thermal Conductive | Beryllium Bronze | High heat dissipation requirements |
Enhancing Product Quality
One of the most satisfying parts of my job is seeing a product come out just right. Inserts have been key in achieving superior aesthetics and accuracy. By using advanced machining techniques on critical areas processed as separate inserts, I ensure uniform surface textures and precise dimensions—particularly important for transparent plastic products.
For cases like electronic casings with strict dimensional requirements, inserts help maintain controlled tolerances, ensuring every piece fits perfectly through accurate dimension design21.
Application Versatility in Molds
Switching up products with ease is another perk of using inserts. By swapping out different designs, I can cater to various items without crafting new molds each time. It’s amazing how inserts can enhance mold functionality by adding features like built-in cooling channels or exhaust grooves, reducing cycle times and eliminating defects such as pores.
Inserts transform molds into adaptable tools that keep pace with ever-changing market demands. They’ve given me a competitive edge through enhanced design flexibility and operational efficiency. If you’re keen on further boosting mold performance, check out our guide on mold maintenance strategies22.
Inserts allow molds to produce multiple products efficiently.True
Swapping inserts of varied designs enables the production of different items.
Inserts increase mold wear and maintenance costs.False
Inserts reduce wear and maintenance costs by being easily replaceable.
Conclusion
Mold inserts enhance manufacturing by improving precision, flexibility, and product quality. They simplify maintenance and adapt designs for various applications, ensuring efficient production processes across industries.
-
Explore how molds accommodate intricate designs, enhancing manufacturing versatility and product functionality. ↩
-
Discover methods to streamline manufacturing processes using well-designed mold inserts for better efficiency. ↩
-
Explore how different tolerance levels affect the precision of injection molds. ↩
-
Learn about the advantages of using threaded connections for easy maintenance. ↩
-
Understand why copper alloys are chosen for their thermal conductivity. ↩
-
Discover strategies that enhance production outcomes through better insert design. ↩
-
Learn how optimizing production efficiency can enhance mold longevity and reduce costs. ↩
-
Explore how specific material properties influence the performance and durability of mold inserts. ↩
-
Discover how mold designers contribute to efficient manufacturing through precise insert design. ↩
-
Learn about the basics of injection molding, including its processes and applications. ↩
-
Discover the die-casting process, its benefits, and typical applications in manufacturing. ↩
-
Explore how pin positioning ensures precision in mold inserts for high-quality production. ↩
-
Understand how mold inserts contribute to enhancing product quality during manufacturing. ↩
-
Learn about various insert shapes tailored for complex structures. ↩
-
Understand how precise dimension design enhances mold performance. ↩
-
Explore optimal materials for different insert applications. ↩
-
Discover how easy insert maintenance reduces downtime. ↩
-
Find out how special features like cooling channels improve products. ↩
-
Discover how interchangeable inserts streamline production by allowing different product variations without full mold replacement. ↩
-
Learn why H13 steel is favored for its durability in high-pressure environments, extending mold life. ↩
-
Explore how precise dimension design ensures product quality with consistent tolerance levels. ↩
-
Find strategies to enhance mold performance and longevity through proactive maintenance practices. ↩