Engineers often think about how materials act during injection molding. This complex process is intriguing. My design work has led me to truly value this journey.
Mold flow analysis predicts warpage in injection molded parts by assessing shrinkage, stresses, and cooling patterns. This ensures high-quality production and streamlines design, enhancing the final product’s quality.
Mold flow analysis has turned into my favorite tool for project success. This tool digs deep into how shrinkage, stress and temperature impact molded parts. It does more than just explain material properties. In one project, I found possible warpage early with this analysis. This discovery saved my team many hours of redesign. It really helped a lot.
Mold flow analysis predicts warpage in injection molded parts.True
This claim is true as mold flow analysis assesses factors that influence warpage, ensuring quality in production.
Mold flow analysis is irrelevant to injection molding processes.False
This claim is false; mold flow analysis is essential for predicting and managing issues like warpage in injection molding.
What really causes shrinkage in injection molded parts?
Have you ever thought about why your injection molded parts sometimes do not look as you hoped? Knowing the details of shrinkage really changes product design and manufacturing. Key factors influence success. Let’s explore these to get it right.
Injection molded parts shrink due to anisotropic shrinkage from material changes, uneven shrinkage from wall thickness variations, and residual stresses from flow and thermal effects. Accurate simulations are crucial for predicting deformation.

Understanding Shrinkage in Injection Molding
Shrinkage is a critical aspect of injection molded parts, influenced by various factors that must be considered during the design and manufacturing process. Below are the key factors impacting shrinkage:
1. Consider Shrinkage
Anisotropic Shrinkage
Anisotropic shrinkage occurs because different materials exhibit varying shrinkage rates based on their molecular orientation. As plastics cool, they can shrink differently in the flow direction versus perpendicular to it.
Utilizing mold flow analysis software1 can provide essential shrinkage data for different materials, allowing designers to predict shrinkage accurately based on the flow direction and pressure within the mold cavity.
Uneven Shrinkage
Uneven wall thickness often leads to uneven cooling rates, which directly contributes to shrinkage inconsistencies. For instance, thin-walled sections cool rapidly and thus shrink sooner than thicker sections, leading to potential warping issues.
By analyzing the cooling rate of each section and considering the material’s thermal properties, engineers can better anticipate deformation due to this uneven shrinkage. This process can be enhanced with tools that calculate thermal expansion coefficients2.
2. Residual Stress Analysis
Flow Residual Stress
During the injection molding process, flow residual stresses arise from the shearing effects on the melt. These stresses can lead to significant deformation post-cooling if not managed properly. Mold flow analysis calculates shear rates and stress distributions, helping predict potential deformations.
Thermal Residual Stress
Thermal residual stresses occur when there is a temperature gradient within the part during cooling. For instance, if the mold’s surface is cooler than the core of the part, this temperature differential can introduce significant thermal stress that could impact part integrity.
Using thermoelastic theory simulations3 allows engineers to visualize these stresses and predict their impact on the final product.
3. Comprehensive Simulation and Prediction
Multi-Physics Field Coupling Simulation
Mold flow analysis software incorporates various physical fields during the melt flow and cooling phases. By coupling velocity, temperature, and pressure fields, designers can gain a holistic view of how these factors interact to influence shrinkage and residual stresses.
This simulation helps ensure that any flow residual stress generated during the filling stage is accounted for in subsequent cooling analyses, thus improving prediction accuracy.
Predicting Deformation Amount and Direction
The culmination of comprehensive simulations enables engineers to forecast not only the magnitude but also the direction of deformation in injection molded parts. This predictive capability can be visualized through tools like deformation cloud maps, making it easier for engineers to grasp potential warpage issues.
By understanding these factors, designers can take proactive measures such as optimizing mold cooling systems or adjusting processing parameters to mitigate warpage and enhance product quality. For more detailed insights into this topic, consider exploring advanced simulation techniques4.
Anisotropic shrinkage affects injection molded part dimensions.True
Different materials shrink at varying rates based on molecular orientation, impacting part dimensions during cooling.
Uneven wall thickness causes uniform cooling rates in molding.False
Uneven wall thickness leads to inconsistent cooling rates, resulting in potential warping and deformation in molded parts.
How does residual stress affect the quality of molded components?
Some molded components perform better than others. Residual stress plays a very big role in this. This hidden factor really affects product quality. It also affects longevity.
Residual stress in molded components leads to warping, optical distortion, and durability issues. Understanding its origins in flow and heat during production allows for improved mold flow analysis, enhancing product design and manufacturing quality.
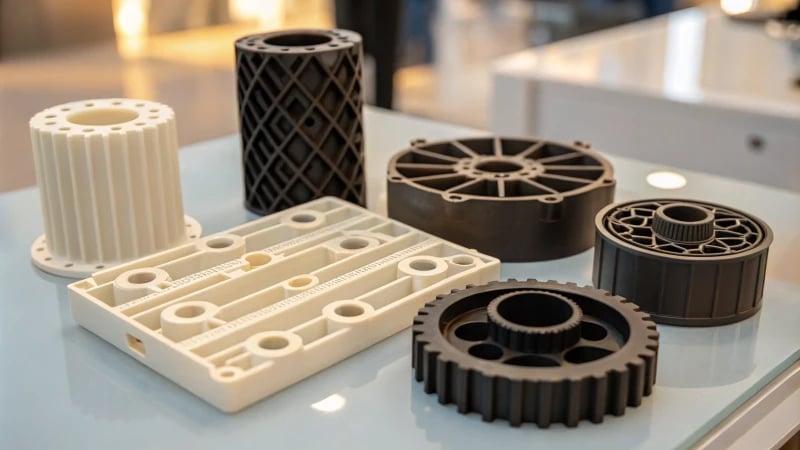
Understanding Residual Stress in Injection Molding
Residual stress is an internal stress that exists within molded components after they are manufactured. It significantly impacts the quality of these parts in various ways, including dimensional stability, durability, and overall performance.
Types of Residual Stress
-
Flow Residual Stress
When melted plastic flows into a mold, different speeds create flow residual stress. The center moves faster than the edges, causing uneven shear stress distributions. This can result in:- Warping of the part as it cools
- Inconsistencies in mechanical properties across the component
To better understand this process, flow analysis5 tools can be utilized.
-
Thermal Residual Stress
Thermal residual stress occurs during cooling. Picture this: when the mold is cool and the inside is still hot, uneven temperature distributions generate thermal gradients that can cause:- Cracking or deformation in thicker sections
- Dimensional inaccuracies affecting assembly
Mold flow analysis can simulate these conditions to predict thermal residual stress effects.
Impact on Component Quality
The effects of residual stress on molded components can be categorized into several areas:
Effect | Description |
---|---|
Dimensional Stability | Residual stress may lead to warpage, causing parts to not meet design specifications. |
Optical Distortion | Parts used in optical applications may experience distortion due to internal stresses. |
Durability | High levels of residual stress can lead to premature failure or fatigue under load. |
Managing Residual Stress
To mitigate the effects of residual stress, manufacturers can adopt several strategies:
- Utilizing Mold Flow Analysis: Predicting shrinkage and stress distributions helps in redesigning molds and processes to minimize issues.
- Optimizing Cooling Rates: By ensuring even cooling rates through careful design of cooling channels, thermal gradients can be reduced.
- Material Selection: Choosing materials with favorable shrinkage properties for specific applications can alleviate some residual stresses.
By leveraging comprehensive simulation tools that factor in both thermal and flow characteristics, engineers can gain insights into how residual stress will manifest in molded parts. This approach not only aids in predicting potential issues but also empowers designers to implement corrective measures early in the design process. For more information on optimizing these processes, check out our guide on mold design best practices.
Residual stress can cause warping in molded components.True
Warpage occurs due to uneven cooling and internal stresses, impacting dimensional stability.
Thermal gradients do not affect the durability of molded parts.False
Uneven cooling creates thermal residual stress, leading to potential premature failure in components.
How Can Mold Flow Analysis Software Benefit Your Injection Molding Process?
Faced any unexpected challenges in your injection molding projects? Explore how mold flow analysis software changes your approach. This tool improves your results.
Mold flow analysis software enhances injection molding by predicting shrinkage, analyzing residual stresses, and offering detailed simulations, leading to improved product quality, increased efficiency, and fewer defects, making it an essential tool for designers.
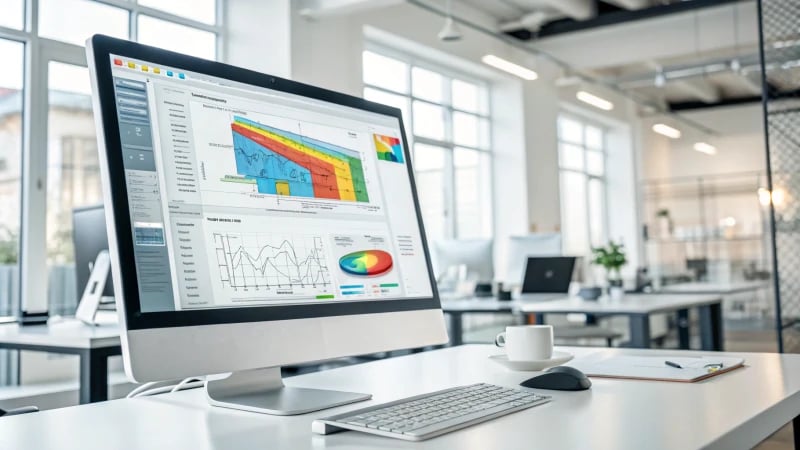
Understanding Mold Flow Analysis Software
Mold flow analysis software acts like a wise friend in the injection molding industry. In my early days, I struggled with design problems. I wished for a way to foresee how my designs would behave. This software simulates the flow of molten plastic through a mold, letting us foresee future issues. It really helps improve efficiency and quality in our products.
1. Consideration of Shrinkage
One important thing about mold flow analysis is dealing with anisotropic shrinkage. Plastics shrink differently based on their properties and geometry. I was shocked to find out that shrinkage varies greatly based on the flow direction and the material’s traits. One time, I designed a part that warped due to ignoring this effect. The software predicts shrinkage changes based on flow direction and pressure, helping us get closer to achieving the ideal final product.
The issue of uneven shrinkage also arises. Thinner parts cool faster than thicker ones. I recall a project where uneven wall thickness caused major deformation. Mold flow analysis calculates cooling speeds and considers the thermal expansion of materials, which helps avoid these problems.
2. Residual Stress Analysis
Residual stresses are sneaky problems that harm molded parts, leading to warping or cracking and risking design integrity. The software highlights two types of residual stress:
- Flow residual stress: Different flow speeds cause shear stress in the material. In one project, understanding this helped me adjust designs early, saving time and resources.
- Thermal residual stress: Uneven temperatures during cooling cause these stresses. I had a warped part because I ignored these temperature differences. The software simulates these changes, enabling informed design adjustments.
3. Comprehensive Simulation and Prediction
Mold flow analysis shines in its comprehensive simulation ability by integrating various physical aspects like velocity, temperature, and pressure during filling and cooling processes. For example, seeing how residual stresses changed helped me predict potential warpage.
Moreover, it provides a clear visualization tool as another big advantage—the deformation cloud map clearly shows predicted warpage, indicating both the amount and direction of part deformations. This insight lets me take early action by optimizing mold design or tweaking injection parameters.
Advantages of Mold Flow Analysis Software |
---|
Predicts shrinkage |
Analyzes residual stress |
Simulates multi-physics interactions |
Visualizes deformation trends |
Enhances production efficiency |
Reduces risk of defects |
Optimizes material selection |
In summary, mold flow analysis software acts like a safety net; it minimizes defects and improves material use for high-quality production. For anyone in plastics manufacturing, using this technology leads to outstanding product designs and efficient processes.
Mold flow analysis software predicts shrinkage accurately.True
The software calculates anisotropic shrinkage based on material properties, ensuring a precise final product.
Residual stress analysis is not possible with mold flow software.False
Mold flow analysis effectively identifies and analyzes both flow and thermal residual stresses in molded parts.
How can engineers optimize designs based on mold flow analysis results?
Did you ever deal with the annoyance of a design mistake that could have been dodged? I certainly did. Knowing how to use mold flow analysis turns possible failures into great successes. These successes appear early in the design phase.
Engineers use mold flow analysis to optimize designs by considering shrinkage, examining residual stresses, and applying detailed simulations to accurately predict deformations.
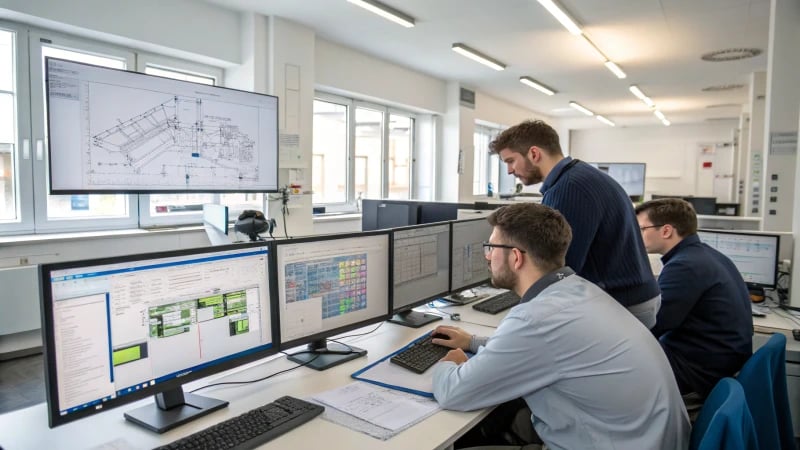
Understanding Shrinkage in Mold Flow Analysis
One key factor I learned about is shrinkage. I discovered that plastics shrink in different ways, known as anisotropic shrinkage, when they cool. This means different parts of a plastic item shrink at different rates, depending on flow direction.
By utilizing mold flow analysis software, engineers can obtain shrinkage data for specific plastic materials, allowing for a more accurate prediction of how parts will behave post-molding.
Anisotropic Shrinkage
I recall a project involving a fragile part for consumer electronics. After the filling and holding phases, I studied shrinkage predictions in different areas based on the flow direction and pressure distribution of the melt. This helped me create molds that were not just effective but highly precise, ensuring accuracy and proper functionality.
Addressing Residual Stress
Another valuable aspect of mold flow analysis I found is residual stress analysis. As melted material fills complex cavities, flow residual stress happens due to shear forces.
Mold flow analysis calculates shear rates and stress distributions during the flow process, which helps predict part behavior after cooling. I have experienced how this stress can cause deformations during cooling; by performing a detailed residual stress analysis, we identified the cause and adjusted our process.
Moreover, engineers should also consider thermal residual stress, which arises from uneven temperature distribution. A large temperature difference between a mold’s surface and part interior causes thermal stresses.
I remember a situation with a significant temperature difference leading to warping that nearly disrupted our schedule. Mold flow analysis allowed us to simulate temperature changes and evaluate thermal stress effectively.
Comprehensive Simulation Techniques
Multi-Physics Field Coupling Simulation
To improve design optimization, I used comprehensive simulation and prediction methods. By combining velocity, temperature, and pressure during the melting and cooling stages, mold flow analysis gave me a complete view of potential problems.
For example:
Physical Field | Impact on Design |
---|---|
Velocity Field | Determines flow rate and filling efficiency |
Temperature Field | Affects cooling rates and shrinkage prediction |
Pressure Field | Influences packing and holding pressure |
This approach helped me understand how flow residual stress from filling stages influences cooling deformation.
Predicting Deformation Amount and Direction
Detailed simulations with mold flow analysis let me foresee the final warpage deformation amount and its direction. Visual tools like deformation maps show deformation levels across parts, helping spot issues early.
This foresight lets me act proactively; I adjust the mold cooling system or injection molding parameters as needed. With these insights, I have reduced warpage significantly, really improving product quality.
Strategies for Design Optimization
Using insights from mold flow analysis allows engineers like Jacky to make informed decisions about:
- Optimizing Mold Cooling Systems: Altering cooling channels based on temperature patterns.
- Modifying Injection Molding Parameters: Changing speed and pressure for better filling.
- Improving Plastic Part Structure Design: Redesigning parts to manage uneven shrinkage or stress spots.
By integrating these strategies into their design processes, I’ve seen great growth in production efficiency and product quality—it’s truly a game-changer! For more advanced tips, feel free to explore further6.
Mold flow analysis helps predict anisotropic shrinkage.True
Engineers use mold flow analysis to understand how plastics shrink differently based on flow direction, aiding in design accuracy.
Residual stress analysis is unnecessary in mold design.False
Residual stress analysis is crucial for predicting deformation and ensuring the integrity of molded parts during cooling.
Conclusion
Mold flow analysis predicts warpage in injection molded parts by evaluating shrinkage and residual stresses, improving design accuracy and production efficiency.
-
Discovering more about shrinkage factors will enhance your understanding of injection molding processes and improve your designs. ↩
-
Learning about residual stress analysis can help you mitigate issues in your designs effectively. ↩
-
This link offers insights into comprehensive simulation methods that can optimize your manufacturing process. ↩
-
Enhance your knowledge of deformation prediction for better product quality. ↩
-
Exploring this link will provide deeper insights into managing residual stress effectively in molded components, enhancing your design process. ↩
-
Discovering best practices in mold flow analysis can help streamline your design processes and improve product quality. ↩