Have you ever thought about improving your injection mold designs? Mold flow analysis truly changes the game.
Mold flow analysis results guide injection mold design by influencing gate placement, runner systems, and cooling channels. They help identify potential defects, enhancing mold efficiency and significantly improving product quality.
In my journey as a product designer, I saw how mold flow analysis truly affects injection molding. It saves many hours of trial and error. By studying flow paths and cooling systems deeply, I reached smart decisions. This leads to smoother production. It feels like having a guiding light. It helps navigate complex mold design. The process ensures quality and efficiency. Every step counts.
Mold flow analysis improves injection mold design efficiency.True
Analyzing mold flow data helps designers optimize gate placement and cooling channels, leading to more efficient mold designs.
Mold flow analysis is unnecessary for defect identification.False
In reality, mold flow analysis is essential for identifying potential defects in the injection molding process.
- 1. What is Mold Flow Analysis and Why is it Important?
- 2. How Does Gate Design Impact Mold Efficiency?
- 3. How Does Runner System Design Impact Injection Molding?
- 4. How Can Cooling System Optimization Prevent Defects?
- 5. What Are Common Defects in Injection Molding and How Can I Avoid Them?
- 6. How Can Software Tools Really Boost the Accuracy of Mold Flow Analysis?
- 7. Conclusion
What is Mold Flow Analysis and Why is it Important?
Have you ever tried to design the best mold for a product? Mold Flow Analysis (MFA) really transformed the way I improve designs for injection molding. But what does it truly involve and why is it so important?
Mold Flow Analysis, a simulation technique, predicts molten plastic flow in molds, optimizing design, enhancing production efficiency, and preventing errors in final products.
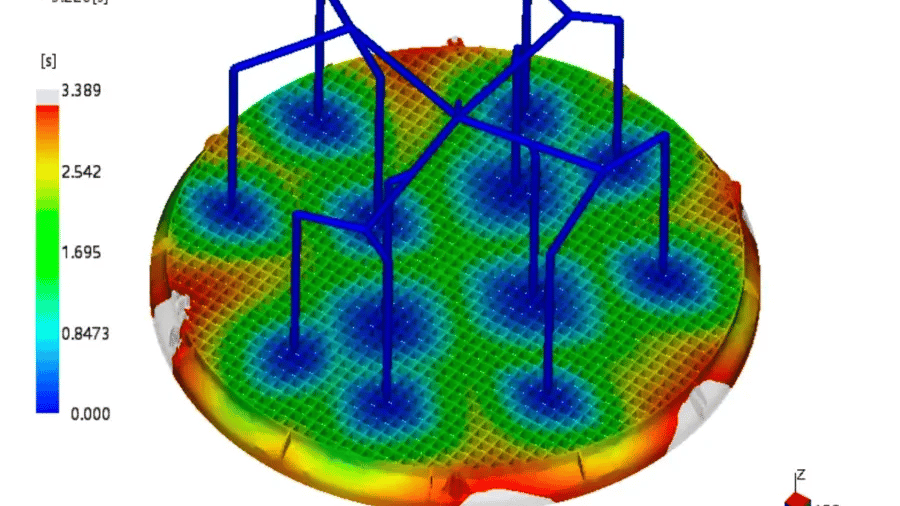
Mold Flow Analysis (MFA) is a simulation technique used in injection molding processes to predict how molten plastic will fill a mold cavity. It plays a crucial role in optimizing the design of the mold, ensuring that the production process is efficient and that the final product meets quality standards. Below, we will explore several important aspects of Mold Flow Analysis and its significance in manufacturing.
Gate Design Optimization
Gate design is vital in ensuring that the molten material flows evenly throughout the mold cavity. Mold Flow Analysis aids in:
-
Position Determination: By visualizing the flow path, designers can pinpoint the best gate location to prevent issues like short shots or trapped air. For example, setting a gate near complex internal structures ensures optimal filling.
-
Quantity Decision: For larger parts, analysis can reveal whether multiple gates are necessary. If a single gate creates unbalanced filling, additional gates can be strategically placed to promote even flow, such as using multiple gates for a large car bumper.
-
Type Selection: Different gate types (side gates, point gates) can impact the final product’s aesthetics and functionality. Analysis results guide designers in selecting the appropriate gate type based on material properties and appearance requirements, like choosing latent gates for high-quality surface finishes.
Runner System Design
The runner system is crucial for directing molten plastic from the injection machine to the mold cavity:
Aspect | Consideration |
---|---|
Shape and Size Planning | Circular runners typically have less flow resistance, enhancing efficiency. |
Balanced Design | In multi-cavity molds, maintaining balance ensures each cavity fills simultaneously, improving production consistency. |
Cooling System Design
Efficient cooling is critical for preventing defects:
- Pipeline Layout Optimization: MFA simulates cooling processes, helping to position cooling channels where they are needed most, especially in parts with varying wall thicknesses.
- Cooling Parameter Adjustment: Analyzing different cooling parameters can lead to better efficiency. For instance, increasing the flow rate of the cooling medium might significantly reduce cycle time.
Mold Parting Surface Design
The design of the parting surface affects demolding:
- Determine the Parting Position: MFA reveals melt flow at cavity edges, which informs optimal parting surface placement to avoid defects like flash.
- Optimize Parting Surface Shape: Complex shapes may require specially designed parting surfaces to ease demolding and enhance product quality.
Predict and Solve Potential Problems
Mold Flow Analysis serves as a proactive tool to predict and mitigate issues:
- Defect Prevention: By foreseeing potential issues such as sink marks or flash, adjustments can be made during design, such as modifying wall thickness or holding parameters.
- Mold Structure Strengthening: If analysis indicates high pressure on certain mold areas, reinforcing those sections can prolong mold life and improve product quality.
Understanding Mold Flow Analysis allows designers like Jacky to make informed decisions that enhance both product quality and manufacturing efficiency. By leveraging this tool, manufacturers can streamline their processes and achieve better results with their injection molded products.
For further insights on optimizing your designs using Mold Flow Analysis techniques, explore our resources on advanced mold design1.
Mold Flow Analysis optimizes gate design in injection molding.True
MFA helps determine the best gate location and type, ensuring even flow and preventing defects during the injection molding process.
Mold Flow Analysis is unnecessary for efficient production.False
Contrary to this claim, MFA is crucial for optimizing designs and preventing defects, making it essential for effective manufacturing.
How Does Gate Design Impact Mold Efficiency?
Did you ever think about how a tiny design choice spreads through the whole manufacturing process like a wave? Gate design might look like a simple technical point, but it changes everything in injection molding. This small detail is really important. It affects both quality and efficiency.
Gate design impacts mold efficiency by ensuring even melt flow and reducing defects. By optimizing the gate’s position, quantity, and type, manufacturers enhance product quality and streamline production processes.
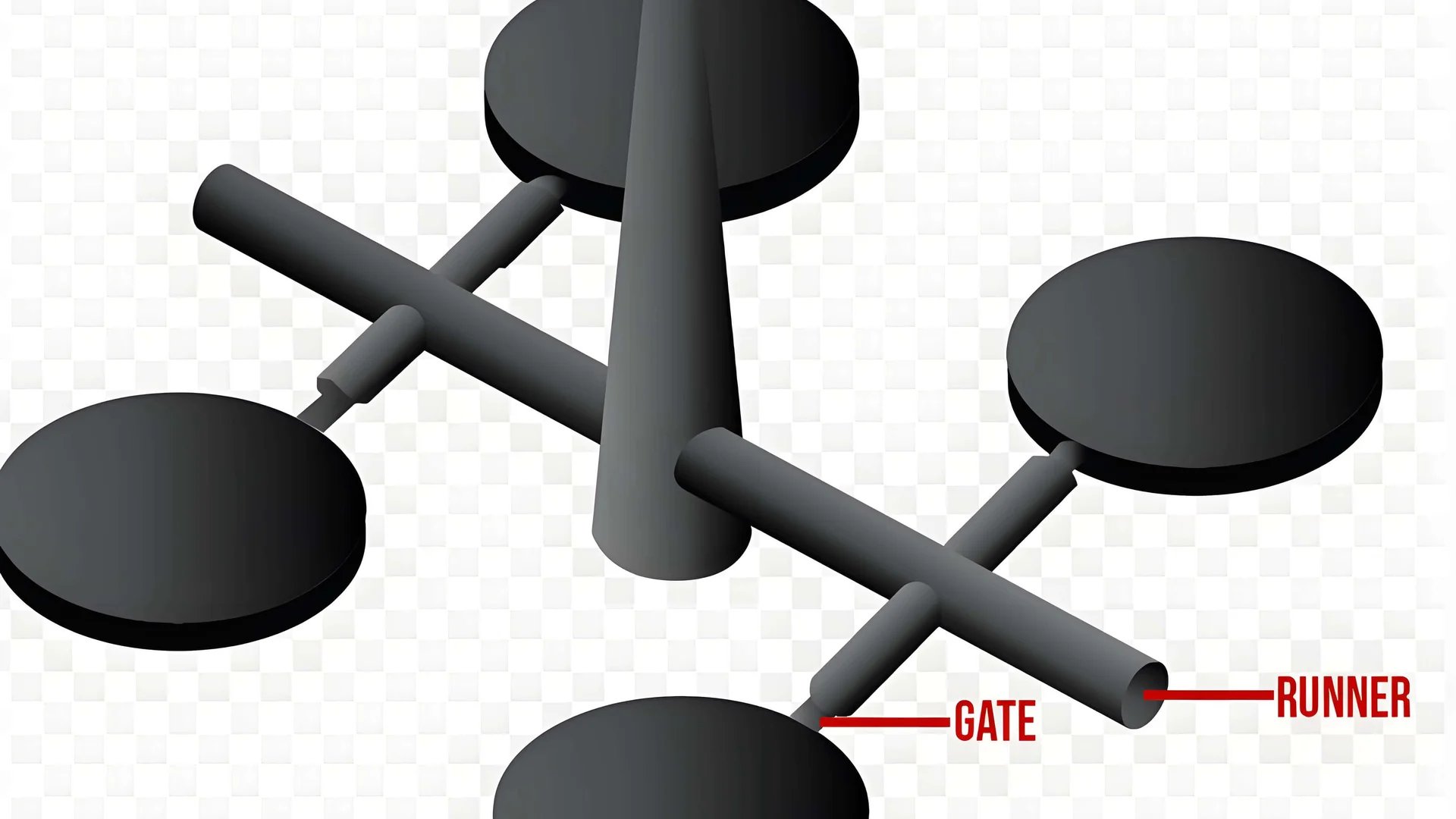
Understanding Gate Design Simplification
When I began in injection molding, complex gate design diagrams confused me. However, gate design is very important. It serves as the backbone for perfect molded parts. Mold flow analysis became my secret tool. It reveals how the melt moves through the cavity, so I could pick the best gate spot for smooth and even filling.
For instance, in parts with complex internal structures, setting the gate at a strategic location allows the melt to reach intricate areas first, preventing defects like short shots and trapped air. This analysis technique2 can be a game changer for manufacturers.
Quantity Choice: Using Multiple Gates
As I gained experience, I worked with larger, more complicated molds. This changed my gate strategies. Sometimes, one gate is not enough. Mold flow analysis helps decide if several gates are needed.
A practical example is the injection of a large car bumper, which typically requires multiple gates to ensure even distribution of the melt throughout the cavity. This balance in design3 can significantly enhance production efficiency and part quality.
Type Selection: Picking the Right Gate
The many gate types can be overwhelming. In the beginning, I struggled choosing between side gates, point gates or latent gates. Each type affects melt flow and the part’s look. So it’s crucial to choose wisely.
For top-notch plastic parts, latent gates often work wonders. They reduce visible surface marks. Seeing how a small choice improved aesthetics was great. It shows the power of thoughtful design decisions and can be as impactful as other design decisions4 in achieving optimal results.
Runner System Design: Path to Efficiency
The runner system is crucial for injection process efficiency. A good design cuts pressure loss and lets the melt flow smoothly from the machine to the cavity.
I found that opting for circular runners greatly improves efficiency due to their lower flow resistance. Here’s a quick comparison of runner shapes:
Runner Shape | Advantages | Disadvantages |
---|---|---|
Circular | Low flow resistance | May require more material |
Trapezoidal | Good balance between size and flow | Can create uneven filling |
This kind of optimization leads to better process outcomes5 and higher-quality molded parts.
Cooling System Design: Keeping Even Temperature
Cooling is very critical to prevent warping. A good cooling system keeps uniform temperature throughout the part, avoiding deformations.
I used mold flow analysis to simulate cooling processes through mold flow analysis; it helped find spots needing better cooling. For example, placing cooling channels near thick sections is a game-changer for consistent temperatures across parts; this cooling optimization6 ultimately boosts production efficiency.
Parting Surface Design: Easy Demolding
Designing the mold parting surface is also key. Through mold flow analysis, I figured out the best parting position to ease demolding while avoiding flash defects.
Moreover, optimizing parting surface shape can enhance demolding efficiency; sloping based on melt flow predictions really helped facilitate easier separation from cavities—greatly improving demolding processes7 and product quality.
Predicting Problems: Taking Action
A very valuable lesson was predicting defects before they occur using mold flow analysis; it let me foresee issues like sink marks or flash—allowing proactive parameter adjustments.
Additionally, if excessive pressure was predicted during molding risks product quality; strengthening mold structure became essential for reliability.
Gate design directly affects melt flow in injection molding.True
The position and type of gate influence how the melt fills the cavity, impacting overall product quality.
Multiple gates are unnecessary for smaller molded parts.False
Larger or complex molds often require multiple gates to ensure uniform filling and avoid defects.
How Does Runner System Design Impact Injection Molding?
Join me in exploring the interesting world of runner system design. This plays a crucial role in injection molding efficiency and product quality. It’s not just a technical detail. It is the point where art meets engineering!
A well-designed runner system in injection molding optimizes molten material flow, balances cavity filling, prevents defects, and enhances production efficiency, thereby significantly improving product quality.
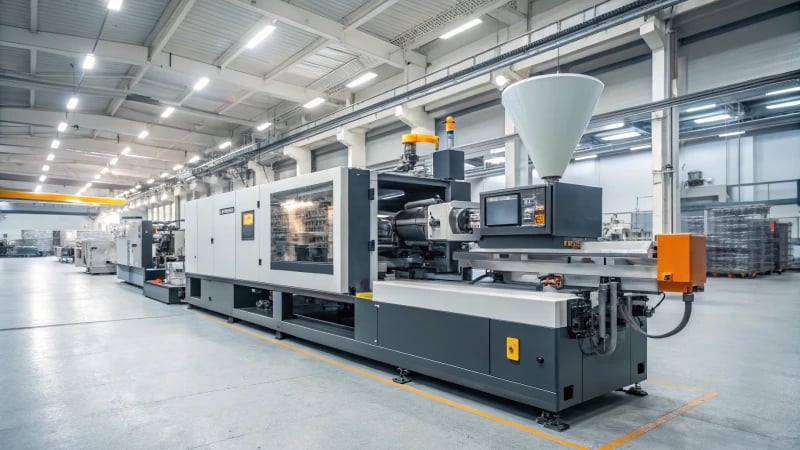
Understanding Runner System Design
The runner system in injection molding serves as a crucial pathway for the melt to travel from the injection machine to the mold cavity. This design directly influences the efficiency, quality, and consistency of the molded parts.
Shape and Size Planning
Mold flow analysis is essential for determining the optimal shape and size of runners.
Runner Shape | Flow Resistance | Ideal Use Case |
---|---|---|
Circular | Low | General use |
Trapezoidal | Moderate | Complex shapes |
By choosing the correct runner shape, manufacturers can reduce pressure loss and ensure smooth melt transmission. For instance, using circular runners is typically preferred as they minimize flow resistance, enhancing the overall efficiency of the injection molding process. More insights can be gained from analyzing runner shapes8.
Balanced Design in Multi-Cavity Molds
In multi-cavity molds, ensuring a balanced runner system is vital.
A balanced design ensures that each cavity fills simultaneously and evenly, which improves quality consistency across molded parts.
Factors Influencing Runner Balance:
- Length: Adjusting the runner length can equalize filling times.
- Diameter: Modifying the diameter helps control flow rates.
An example of this would be adjusting the parameters of a runner system when molding automotive parts to achieve uniform filling. For detailed strategies on balancing runners, see runner balancing techniques9.
Cooling System Integration
An efficient runner design not only considers melt flow but also integrates cooling systems effectively.
- Pipeline Layout Optimization: The layout must ensure that cooling occurs evenly across different wall thicknesses.
- Cooling Parameter Adjustment: The analysis of cooling parameters, such as flow rate and temperature, can lead to significant improvements in production efficiency.
For instance, if certain areas of a mold are found to be cooling unevenly, adjustments can be made to the cooling pipeline layout to address these issues. More on cooling system optimizations can be explored through cooling techniques10.
Predicting and Solving Potential Problems
Runner system design also plays a role in defect prevention during injection molding. By utilizing mold flow analysis, designers can foresee potential issues such as sink marks or flash.
- Defect Prevention: Early identification of possible defects allows for adjustments in design parameters before production begins.
- Mold Structure Strengthening: Predictive analysis can indicate where additional support may be necessary to withstand pressures during the injection process.
For further understanding of defect prevention methodologies, refer to defect analysis resources11.
Circular runners minimize flow resistance in injection molding.True
Using circular runners reduces pressure loss, leading to more efficient melt transmission in the injection molding process.
Balanced runner design ensures uniform filling in multi-cavity molds.True
A balanced runner system allows all cavities to fill at the same time, improving consistency and quality of molded parts.
How Can Cooling System Optimization Prevent Defects?
Have you ever wondered how improving a cooling system helps reduce defects? It’s really interesting that effective cooling connects directly to the quality of our molded products. Let’s explore this topic together.
Optimizing cooling systems in injection molding ensures even cooling, reducing defects like warping and sink marks, ultimately enhancing product quality.
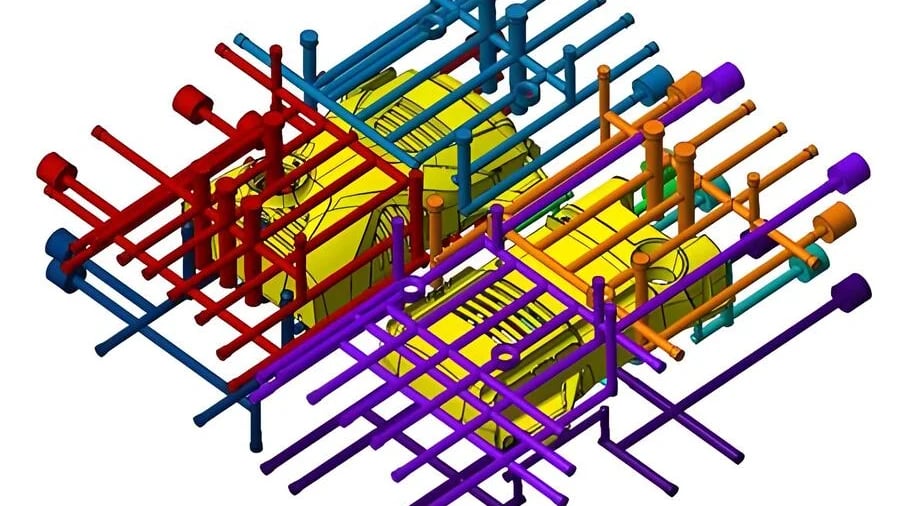
Understanding Cooling System Optimization
Cooling system optimization is crucial for maintaining the quality of injection molded parts. By ensuring that the cooling process is efficient, manufacturers can prevent defects that arise due to uneven cooling or improper heat dissipation.
Importance of Even Cooling
An even cooling process helps in avoiding warping and distortion of the molded parts. When certain areas cool faster than others, it can lead to uneven shrinkage, causing defects such as sink marks and warping.
For instance, this study12 demonstrates how optimized cooling layouts can mitigate these issues effectively.
Key Strategies for Optimization
- Pipeline Layout Optimization
- Utilizing mold flow analysis to predict cooling patterns can help in designing an effective cooling pipeline layout.
- By placing cooling channels closer to thicker sections of the mold, designers can ensure uniform cooling rates.
Pipeline Location | Effect on Cooling Rate |
---|---|
Near thick walls | Faster cooling |
Away from thick walls | Slower cooling |
-
Cooling Parameter Adjustment
- Adjusting the temperature and flow rate of the cooling medium is vital.
- Higher flow rates can significantly reduce cooling times, which directly affects productivity.
Example: In a recent project, increasing the flow rate by 20% reduced the cooling time by 15%, which improved overall cycle times. For more insights on this optimization technique, check out this resource13.
-
Predicting Potential Defects
- Advanced mold flow analysis not only optimizes cooling but also predicts potential defects during the design phase.
- By simulating different scenarios, designers can identify problems like flash or sink marks before they occur, allowing proactive measures to be implemented.
The Role of Gate Design in Cooling
Optimizing gate design also contributes to the effectiveness of the cooling system. Gates control how the molten plastic enters the mold and influence the filling pattern, which in turn affects cooling:
- Position Determination: Correct gate placement can ensure faster filling of complex shapes, leading to more uniform cooling.
- Quantity Decision: For large parts, multiple gates may be necessary to achieve consistent filling and hence uniform cooling.
- Type Selection: Different types of gates (like side or point gates) can have varying effects on flow and cooling efficiency.
For practical examples of how gate optimization impacts cooling performance, refer to this article14.
Conclusion
By employing thorough analysis and strategic design adjustments, manufacturers can optimize their cooling systems to prevent defects in injection molded parts. The interplay between design parameters and cooling effectiveness plays a crucial role in ensuring high-quality production outcomes.
Even cooling prevents warping in injection molded parts.True
Even cooling is essential to avoid warping, ensuring uniform shrinkage and high-quality molded products.
Optimizing cooling systems reduces production cycle times.True
Adjusting cooling parameters can significantly decrease cooling times, enhancing overall productivity in manufacturing processes.
What Are Common Defects in Injection Molding and How Can I Avoid Them?
I explored the world of injection molding more deeply. I soon understood that defects are terrible for product quality. Here are my thoughts on common problems. Learn to avoid them and save time. Avoiding these issues really helps reduce frustration.
Common injection molding defects include short shots, sink marks, flash, warping, and cavitation. Avoid them by optimizing gate design, adjusting cooling systems, conducting mold flow analyses, and thoroughly inspecting molds.
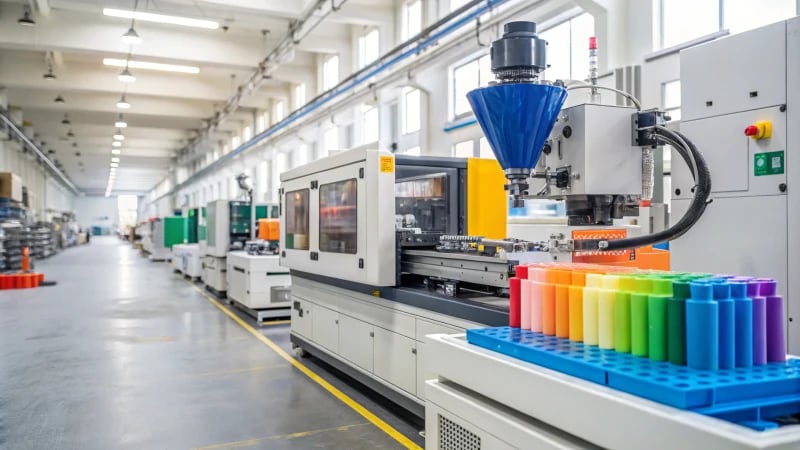
Common Defects in Injection Molding
Injection molding is a fascinating process. It requires skill and precision. Small errors might lead to big problems. These problems affect product quality. Understanding defects helps in learning from mistakes.
1. Short Shots
Short shots occur when the molten plastic does not fill the entire cavity of the mold, leading to incomplete parts. This can result from insufficient injection pressure or incorrect gate design. To avoid short shots:
- Gate Design Optimization: Analyzing mold flow showed the best gate position. Proper placement first reaches complex areas with melt.
- Mold Flow Analysis: Running analyses became my strategy. It found the best gate type and number, ensuring uniform filling throughout the mold.
Solutions | Description |
---|---|
Gate Positioning | Analyze flow to find optimal gate locations. |
Use Multiple Gates | For large parts, consider additional gates to enhance flow. |
2. Sink Marks
Sink marks are depressions that occur on the surface of molded parts due to uneven cooling and shrinkage. They can be avoided by:
- Cooling System Design: A better pipeline layout created uniform cooling, placing cooling pipes near thick sections to balance temperature differences.
- Parameter Adjustment: Changing cooling flow rate and temperature was crucial; higher flow rate sped up cooling based on cooling efficiency studies15.
3. Flash
Flash is an unwanted excess material that appears at the parting line of a mold, often caused by excessive injection pressure or poor mold alignment. To prevent flash:
- Mold Parting Surface Design: Proper parting surface position, found through mold flow analysis, reduced flash and ensured smooth demolding.
Prevention Strategies | Description |
---|---|
Parting Position Optimization | Use analysis results to set the parting surface for easy demolding. |
Regular Maintenance | Ensure molds are well-aligned and maintained regularly. |
4. Warping
Warping occurs when molded parts deform as they cool down unevenly, leading to parts not fitting correctly in assemblies. To mitigate warping:
- Balanced Runner System: A balanced runner system was essential; mold flow analysis helped ensure every cavity filled evenly.
- Cooling Parameter Adjustments: Adjusted parameters with simulation data for uniform cooling.
5. Cavitation
Cavitation refers to voids happening from trapped air or gas during the injection process; this can be avoided by:
- Defect Prevention Strategies: Early mold flow analysis predicted potential cavitation issues before they occurred, enabling design changes accordingly.
- Optimize Wall Thickness: Adjusting wall thickness using analysis results led to uniform melt distribution.
Investigating these defects in injection molding improved product quality and efficiency; every challenge taught valuable lessons.
Short shots can occur due to insufficient injection pressure.True
Insufficient injection pressure is a common cause of short shots in injection molding, leading to incomplete parts.
Warping is caused by uniform cooling of molded parts.False
Warping occurs from uneven cooling, not uniform cooling, affecting part fit in assemblies.
How Can Software Tools Really Boost the Accuracy of Mold Flow Analysis?
Have you ever thought about the magic behind mold flow analysis? Software tools are changing how accurately this important process works. These tools probably help designs become both smarter and more efficient. Designs are really improving.
Software tools enhance mold flow analysis accuracy through realistic simulations, detailed visualizations, and predictive analytics, enabling better design decisions, defect reduction, and improved production efficiency.
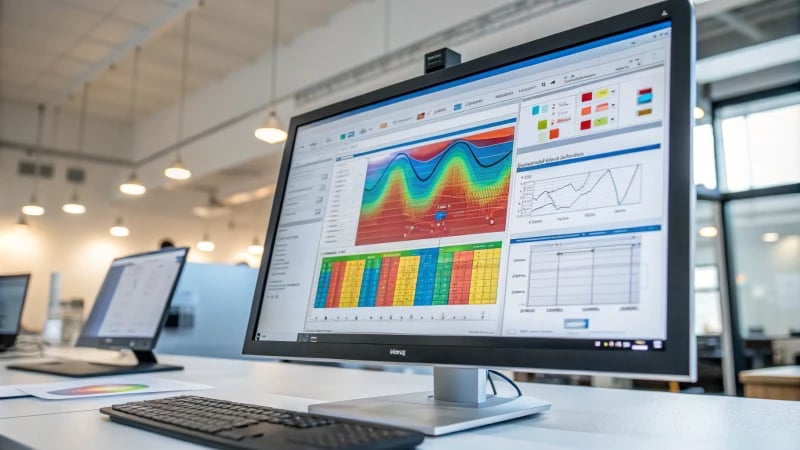
Understanding Mold Flow Analysis
Mold flow analysis (MFA) is a critical step in the injection molding process that simulates how molten plastic flows into a mold. Software tools enhance this analysis by offering advanced simulations, allowing designers to visualize potential issues before actual production.
The enhanced accuracy of MFA can be attributed to several factors:
-
Realistic Simulation Environments
Modern software tools provide realistic simulation environments that mimic real-world conditions. This includes temperature variations, pressure changes, and material properties.- Example: Once, I used software to see how a temperature change affected the melt’s thickness for a tricky part. It was eye-opening. Even small changes could alter how it flowed.
-
Detailed Visualization
Advanced visualization techniques enable users to see flow paths, filling times, and cooling effects in real-time. This helps in identifying bottlenecks and optimizing designs effectively.- Example: During a project, I could visibly detect where air traps might form, allowing me to modify the gate design before creating any physical models. It saved time and resources.
Key Features of Software Tools
Feature | Benefits |
---|---|
Gate Design Optimization | Helps determine optimal gate positions and types |
Runner System Design | Ensures balanced flow across multiple cavities |
Cooling System Design | Optimizes cooling efficiency to prevent warping |
Predictive Analysis | Identifies potential defects before they happen |
Gate Design Optimization
Software tools help optimize gate design in three significant ways:
- Position Determination: Accurate simulations show the best gate location to ensure even filling and reduce defects like short shots. For complex parts, software identifies the best gate spot so melt reaches everywhere efficiently.
- Quantity Decision: Analysis results can indicate whether multiple gates are necessary for larger parts, like car bumpers, ensuring that the melt fills evenly without unbalanced areas.
- Type Selection: Different gates have unique effects on melt flow and part appearance. Software assists in choosing the right gate type based on design specifications and material properties.
Runner System Design
An effective runner system is crucial for ensuring that the melt reaches all cavities uniformly:
- Shape and Size Planning: I used software to study flow resistance for choosing the best runner shape and size. Circular runners often offer less resistance compared to trapezoidal ones.
- Balanced Design: In multi-cavity molds, achieving balance is essential. Software reveals how different runner setups affect filling times across cavities, enabling adjustments to maintain consistency.
Cooling System Design
Proper cooling is vital to minimize defects:
- Pipeline Layout Optimization: Cooling simulations show areas with uneven cooling risks. This helps me place cooling channels strategically, like near thick sections, to prevent warping.
- Cooling Parameter Adjustment: These tools test different cooling settings, allowing me to discover the best flow rates and temperatures for quicker cooling times.
Predicting and Solving Potential Problems
Software tools excel at anticipating issues:
- Defect Prevention: Mold flow analysis often predicts defects such as sink marks or flash. By adjusting wall thickness based on predicted outcomes can enhance final product quality.
- Mold Structure Strengthening: If simulations show weak spots under pressure, I modify the mold structure accordingly for strength ensuring durability.
Understanding how these software capabilities translate into tangible benefits can significantly elevate the design process for professionals like Jacky, ensuring that products not only meet aesthetic standards but are also optimized for mass production efficiency.
Further Reading
to explore more about mold flow analysis software options, check out these resources:
Software tools improve mold flow analysis accuracy significantly.True
Advanced simulations and visualizations from software tools lead to more precise mold flow analysis, reducing defects and enhancing production efficiency.
Mold flow analysis requires no software for accurate results.False
Contrary to this claim, software is essential for realistic simulations and detailed insights in mold flow analysis, ensuring optimal design decisions.
Conclusion
Mold flow analysis optimizes injection mold design by guiding gate placement, runner systems, and cooling channels, significantly improving production efficiency and product quality.
-
This link offers deeper insights into Mold Flow Analysis methodologies and benefits for your design process. ↩
-
Explore this link for deeper insights into optimizing gate design for better mold efficiency. ↩
-
Learn about various types of gates and their specific impacts on mold efficiency. ↩
-
Understanding runner system designs will help you enhance your mold efficiency effectively. ↩
-
Find out how cooling systems affect mold efficiency and ways to optimize them. ↩
-
Discover strategies for effective parting surface designs to prevent defects during demolding. ↩
-
Get insights on predicting potential issues during molding and how to address them early. ↩
-
Learn about key runner design principles that can enhance your injection molding processes. ↩
-
Discover effective techniques for balancing runner systems in multi-cavity molds. ↩
-
Find out how to optimize cooling systems within runner designs for better efficiency. ↩
-
Understand how to prevent defects through effective runner system strategies. ↩
-
Clicking this link will provide you with deeper insights into advanced cooling techniques that can enhance product quality. ↩
-
Explore this link for effective strategies on adjusting cooling parameters for optimal results. ↩
-
This link offers practical case studies on gate design and its impact on cooling efficiency. ↩
-
Learn about effective mold design strategies that can help prevent injection molding defects. ↩
-
Explore top software options that can elevate your mold flow analysis capabilities and improve accuracy significantly. ↩
-
Learn how mold flow analysis can prevent defects in injection molding and optimize product designs. ↩
-
Understand the critical role of cooling system design in enhancing the quality of molded parts through effective simulations. ↩