Solving underfill problems in mold design sometimes resembles solving a very complex puzzle. The right strategies change challenges into opportunities to improve.
To fix problems with underfilling in mold design, study gate location and size. Check runner systems, too. Good placement very likely improves the melt flow. Proper size helps fill the cavity completely. Improve exhaust gas control as well. These changes decrease defects in injection molding. Better flow means fewer problems.
These strategies create a very solid foundation. Looking closely at each detail reveals even more potential to improve both efficiency and quality. It’s similar to adjusting a musical instrument; each tweak brings your manufacturing process to harmony. Check out these expert tips. See your production line change.
Gate location affects melt flow in injection molding.True
Adjusting gate position can enhance filling in thin-walled areas.
Runner length has no impact on melt flow efficiency.False
Shorter runners reduce resistance, improving melt flow efficiency.
How Can Gate Location Impact Mold Filling?
Ever thought about why gate placement in molds matters so much? It seems the goal is all about getting the flow perfect!
Gate position affects how the mold fills by controlling the flow path, pressure distribution and risk of defects. Properly positioned gates allow for uniform filling. This reduces air pockets and problems with incomplete filling.
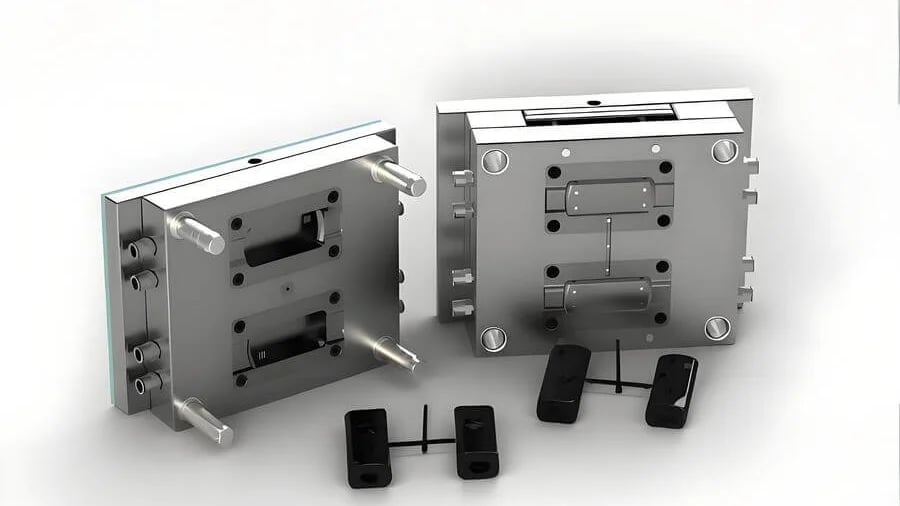
Gate Design Optimization
Adjustment of Gate Location
I discovered that gate placement significantly impacts the process when working with complex shapes like a plastic container with a thin handle. Placing the gate near the handle helped avoid problems with underfilling caused by long melt paths. Small shifts can change everything, similar to steering a ship.
Symmetry plays a big role too. Molding a toy figure with a side gate resulted in an uneven outcome. Aligning the gate along the symmetry axis allowed the melt to flow properly, balancing both sides. It’s like ensuring everyone at the table gets an equal portion.
For complex shapes, placing gates near thin-walled areas or difficult-to-fill zones1 is essential.
Changing the Size and Number of Gates
Gate size is important. Working on large plastic trays showed me that increasing gate diameter from 3mm to 5mm improved performance dramatically. More melt led to fewer defects—less frustration indeed.
Adding more gates sometimes solves problems. A toolbox with many compartments taught me this. Placing extra gates near each section filled compartments evenly and made the process smooth as my morning coffee.
Adjusting gate size according to product complexity is vital for large items or those with thick walls, increasing the gate size can enhance melt flow.
Increasing the number of gates for complex structures2 ensures even distribution.
Improvement of Runner System
Adjustment of Runner Length and Diameter
I underestimated the importance of shortening runners until I dealt with heat loss problems. Like a shortcut on the road, shorter runners faced less resistance and allowed easier flow. On large projects, increasing runner diameter ensured smooth movement.
Shortening runner length reduces heat loss and melt resistance by redesigning runners to be more direct, as in molds for small parts, you improve efficiency.
Runner Aspect | Adjustment | Impact |
---|---|---|
Length | Shorten | Less resistance |
Diameter | Increase | Better flow |
Exhaust Gas Design Enhancement
Adding exhaust grooves worked like opening windows on a hot day. Air traps became less of an issue. With intricate structures, breathable materials like air-permeable steel were crucial; they helped fight underfilling from trapped air.
Adding exhaust grooves in deep cavities and other areas3 prone to air retention allows air escape, preventing back pressure issues.
Gate location affects mold filling efficiency.True
Adjusting gate location enhances flow to thin-walled areas, improving fill.
Runner length does not impact melt flow resistance.False
Shortening runner length reduces melt resistance and heat dissipation.
How does runner system design affect underfill prevention?
Some injection molds fill completely, while others do not. The design of the runner system is the key reason.
A good runner system design shapes molding by controlling how easily molten material moves into a mold. This flow control is very important. An optimized fill rate and pressure distribution help avoid underfill problems. This practice raises product quality. Quality is key.
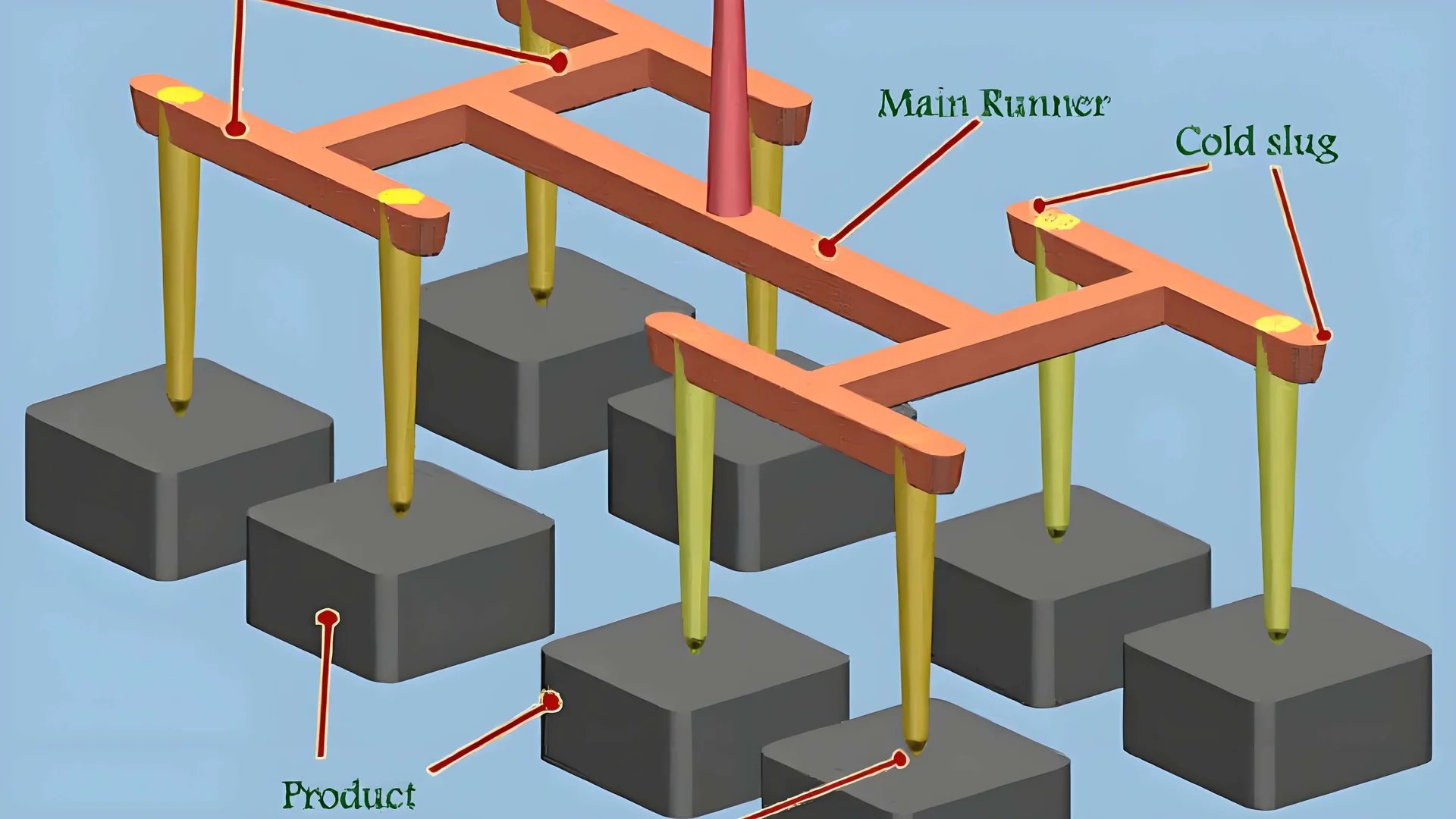
Let’s Talk About Runner Length and Diameter
Imagine you’re working on an injection molding project and the product doesn’t fill right. Maybe the runner length and diameter are the reason. I remember changing these in a project once – it really changed everything! Short runners cut heat loss and resistance. The melt flowed better. Increasing the diameter from 8mm to 10mm was like opening big gates, especially for thick products. It really helped.
Factor | Impact |
---|---|
Runner Length | Shortening reduces heat dissipation |
Runner Diameter | Larger diameters enhance melt flow rate |
The Magic of a Smooth Runner Surface
I polished a rough runner surface once and the flow improved greatly. It was almost like the melt was happy to have an easier path. A surface roughness below Ra0.8μm cuts friction a lot. Less friction means fewer fill problems. It really does help.
Gate Design: The Unsung Hero
Gate design is often overlooked! I saw how moving gates to better spots can change everything, especially with complex designs. In one project, moving the gate on a toy figure’s symmetry axis changed melt distribution a lot. It was a big win.
- Gate Location: Near thin-walled areas.
- Gate Size/Number: Match product complexity and size.
Explore more on gate design optimization4 for complex shapes.
Breathing Easy with Exhaust Systems
Good exhaust systems give your mold fresh air. I used breathable steel in a tough mold and it worked wonders. Exhaust grooves or holes let trapped air out. Less air means fewer underfill problems. Learn about exhaust system improvements5 for better mold filling.
Knowing these runner system elements really helps product quality. It makes material flow better and cuts defects.
Gate location affects melt flow in complex shapes.True
Adjusting gate location helps fill thin-walled areas efficiently.
Runner surface roughness does not impact melt flow.False
Smoother runners reduce friction, improving melt flow efficiency.
Why is exhaust gas design crucial in injection molding?
Have you ever thought about how small design choices may affect the quality of a molded item? Let’s explore why planning for exhaust gas is very important in injection molding.
In injection molding, exhaust gas design is very important to stop defects like short shots and burn marks. This design lets trapped air escape well. This escape of air helps keep product quality steady. It also helps the mold work better.
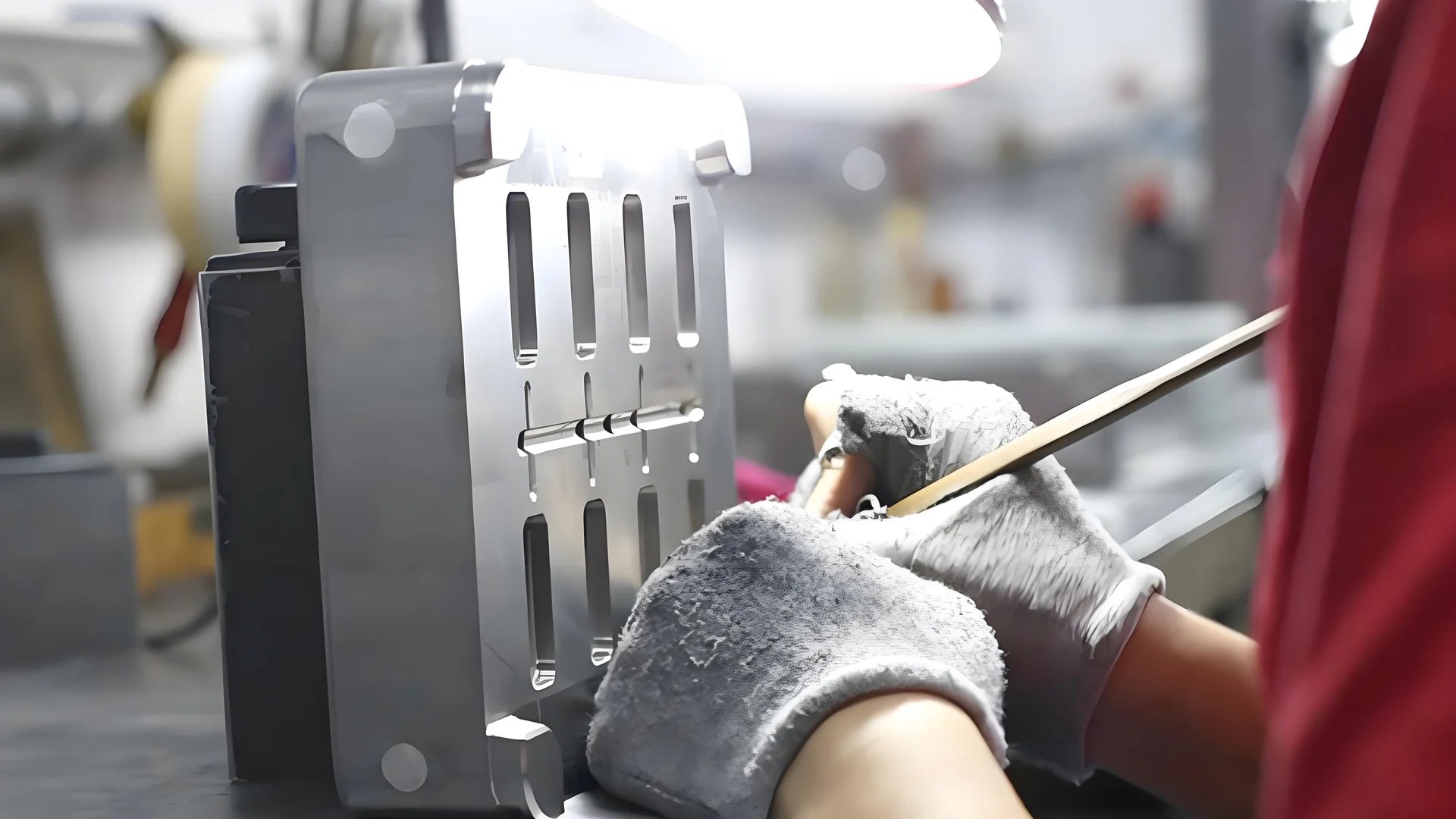
Understanding Exhaust Gas in Injection Molding
Imagine trying to fill a complex mold with melted plastic, but annoying air bubbles keep blocking the way. These trapped bubbles might cause short shots, where the plastic doesn’t fully fill the mold, or they might cause burn marks when air catches fire under pressure. So, a clever exhaust system is very important.
Methods of Exhaust Gas Design
Exhaust Grooves and Holes
Exhaust grooves or holes really change the game when placed in the right spots. For instance, in a project with deep mold cavities, adding exhaust grooves only 0.03mm wide and 0.2mm deep allowed air to escape easily. Around ejector pins, exhaust holes helped all parts work smoothly and reduced defects significantly.
Breathable Materials
What happens if grooves and holes don’t work? Using breathable materials, such as breathable steel, might very well save the day. This steel lets air move through its tiny pores, offering a smart solution when usual techniques don’t succeed.
Optimizing Venting Systems: A Comparative Table
Method | Application Example | Benefits |
---|---|---|
Exhaust Grooves | Deep cavities in molds | Prevents air compression and back pressure |
Exhaust Holes | Around ejector pins | Ensures smooth operation and reduces defects |
Breathable Materials | Complex internal structures | Solves underfilling when air cannot escape |
Impacts on Injection Molding Performance
Correct exhaust gas design not only improves mold performance6, but also enhances product quality while lowering waste and production costs. With fewer defects to handle, cycle time becomes faster. It really speeds up!
Related Considerations in Mold Design
Fine-tuning exhaust gas design requires thinking about other things like gate location and runner systems. Changing the gate size7 may also help spread the material evenly, avoiding possible defects.
Incorporating exhaust gas design into these wider considerations lets manufacturers reach a high level of molding success.
Adjusting gate location reduces risk of underfilling.True
Positioning gates near thin-walled areas ensures even melt flow.
Increasing runner diameter decreases melt flow resistance.True
Larger diameters allow more melt to pass smoothly, improving filling.
What Materials Improve Mold Ventilation?
Exploring mold ventilation materials helps create fresher, healthier air. The right decisions keep your space free from mold.
Breathable steel and porous plastics shine in mold ventilation. These materials help air move through the space. Moisture reduction takes place effectively. Mold growth chances probably lessen significantly. Mold risks stay very low. This is important. Mold risks stay very low.
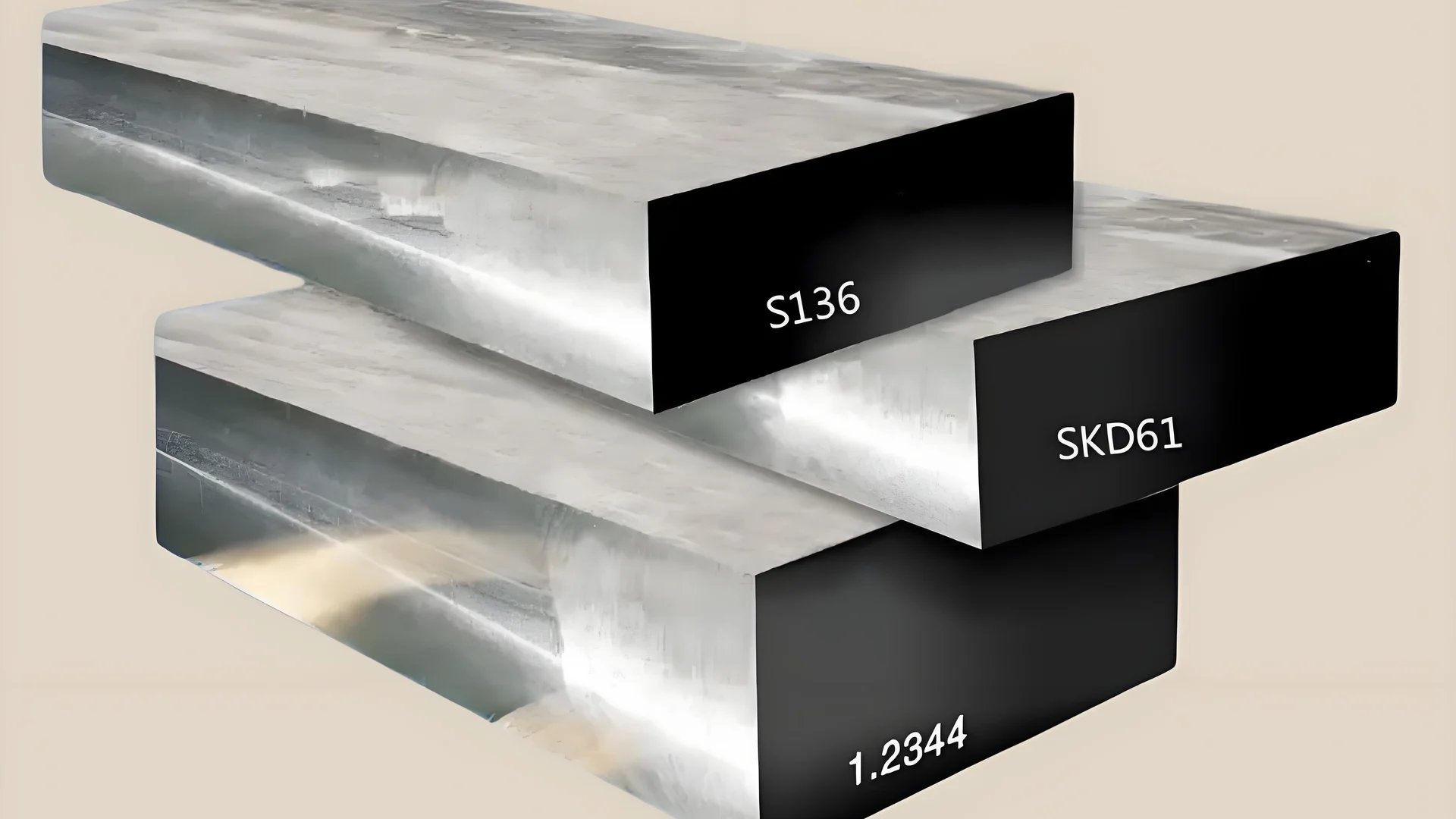
Breathable Steel
Breathable steel is an innovative material used in mold making to improve ventilation. Its porous nature allows air to escape through the steel itself, which is particularly useful in complex structures8 where traditional exhaust solutions aren’t feasible.
I remember a time working on a project with detailed plastic toys for children. The toys needed to be perfect in both appearance and safety. Breathable steel became a surprising savior. Its tiny holes let air escape, especially in tricky areas where usual methods often failed. Once, it solved a hard air problem in a toy’s little nose. It saved the project and my sanity. It was a real relief.
For example, when molding intricate plastic products, breathable steel can be strategically placed in areas that are prone to air retention, allowing for seamless airflow.
Porous Plastics
Porous plastics are another excellent choice for enhancing ventilation. These materials are designed with micro-holes that permit air passage while maintaining structural integrity.
Porous plastics came in handy during my kitchen remodel. These materials suited moldings with deep spaces very well. They have tiny holes allowing air to pass while staying strong. This was huge in stopping air bubbles from ruining my new cabinets.
A common application is in the manufacture of products with deep cavities, where these plastics help prevent air pockets from forming during the molding process.
Material | Advantages |
---|---|
Breathable Steel | Allows air escape in complex mold structures |
Porous Plastics | Prevents air pockets and maintains product shape |
Silicone Rubber
Silicone rubber is renowned for its flexibility and resistance to moisture. It can be used in molds to create seals that prevent unwanted air and moisture ingress, thereby controlling humidity levels effectively.
Silicone rubber was key when I needed flexibility and resistance to moisture. It acted like an unseen helper, balancing between keeping moisture out and letting air in. Ideal for molds needing frequent changes, silicone rubber provided the flexibility that ensured the process ran smoothly.
In addition, silicone rubber’s inherent qualities make it ideal for molds that require frequent adjustments or modifications.
Incorporating Advanced Materials
Exploring advanced materials9 like composite resins or treated metals can also contribute to improved ventilation. Composite resins are lightweight yet sturdy, providing an excellent balance between strength and permeability.
Trying out advanced materials felt like discovering new opportunities. Composite resins and treated metals became essential tools for me:
- Composite Resins: Light yet strong, offering the perfect mix for complex designs.
- Treated Metals: Reduce friction by enhancing airflow through reduced surface friction—perfect for detailed mold designs.
By selecting these materials carefully not only improved my designs but also boosted my confidence in designing projects more efficiently while reducing flaws from bad air movement.
Gate size should increase for larger products.True
Larger products require increased gate size to enhance melt flow.
Rough runner surfaces improve melt flow.False
Smooth runners reduce friction, improving melt flow efficiency.
How Does Mold Surface Quality Affect Product Outcome?
Do you ever ask yourself how the smallest details decide a product’s success or failure?
A mold’s surface quality greatly affects how the final product looks, feels and works. A smooth mold helps the material flow evenly. This reduces flaws. It also improves appearance and strength. This is crucial. This is very important for creating high-quality items.
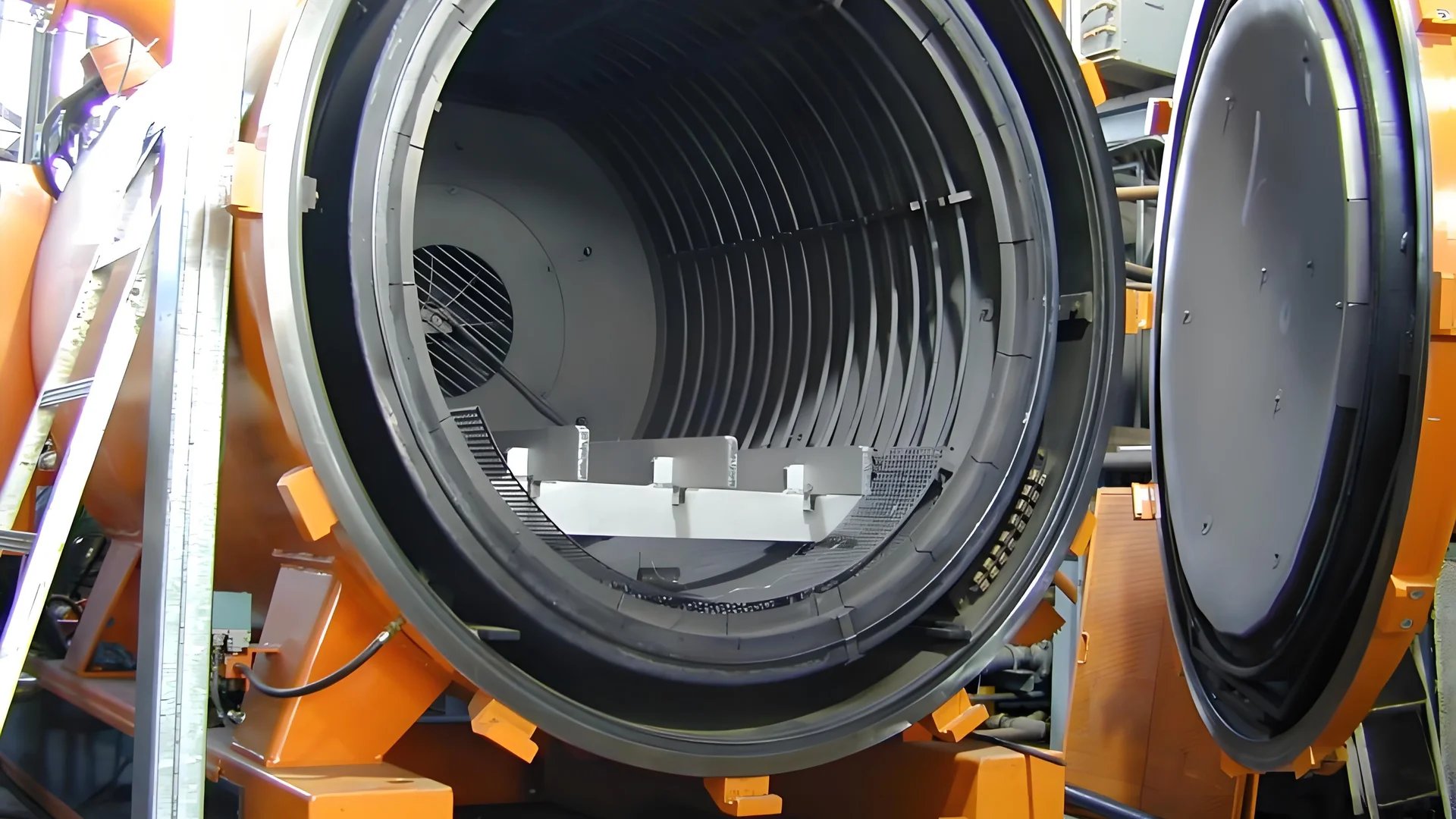
The Role of Surface Finish in Aesthetic and Functionality
The first time I noticed a polished mold’s impact was unforgettable. It felt like magic – seeing the molten material slide into each corner without any trouble. With less friction, a smooth surface lets the melt move easily10, giving a finish so even that flaws almost disappear. Look at electronic enclosures, for instance. A glossy finish not only looks stylish but also acts like a shield, keeping dirt away and its shine intact for a long time.
Surface Quality and Structural Integrity
Nothing frustrates more than seeing a design ruined by unevenness or weak points. I discovered, through challenges, that these problems often come from rough mold surfaces. By carefully improving smoothness through polishing, we keep cooling balanced and protect the product’s shape and strength. It’s like placing a suit of armor on your product.
Enhancements in Gate and Runner Design
Gate Design Optimization:
- Gate Location Adjustment: I had to move the gate by the handles of plastic containers once and wow, what a change! This small change brings even filling, especially in tough thin-walled areas.
- Size and Number Adjustments: For bigger molds, increasing the gate size helps a lot. Adding extra gates in complex parts can make a huge difference too.
Product Type | Gate Adjustment |
---|---|
Thin-walled containers | Close to thin areas |
Large trays | Larger gate diameter |
Complex toolboxes | Additional auxiliary gates |
Runner System Improvements
Runner Length and Diameter Adjustment:
I tried shortening runners to lessen heat loss. In bigger items, making the runner diameter larger helps the melt flow more smoothly.
- Surface Quality: Polished runners? Absolutely! They cut friction greatly, meaning fewer issues of incomplete fills – a real lifesaver in production.
Exhaust Gas Design Improvement
Exhaust Slot Implementation:
Deep cavities benefit from exhaust slots, stopping annoying trapped air that leads to pressure build-up. Well-placed exhaust holes are very important for clear air release.
Mold Feature | Exhaust Design |
---|---|
Deep cavities | Exhaust slots |
Parting surfaces | Regular exhaust holes |
Concentrating on mold surface quality is like perfecting an art – it improves product outcomes significantly. This focus not only makes products look better but also ensures they stay firm and work well. Those keen to learn more should explore further resources on mold improvements11 for valuable insights into bettering production strategies.
Gate location affects mold filling efficiency.True
Positioning gates near thin-walled areas ensures even melt flow.
Runner surface quality doesn't impact mold filling.False
Smoother runners reduce friction, enhancing melt flow efficiency.
Conclusion
This article explores effective mold design solutions for underfill issues, focusing on gate optimization, runner system improvements, and exhaust gas design to enhance efficiency and product quality.
-
Explore how different gate placements affect mold filling in complex shapes, improving your designs. ↩
-
Learn why multiple gates can optimize mold filling for complex products. ↩
-
Understand how exhaust design enhances mold filling by allowing trapped air to escape. ↩
-
Explore strategies for gate placement and sizing that improve filling efficiency in complex molds. ↩
-
Discover methods to enhance air evacuation from molds, reducing defects like underfill. ↩
-
Learn about the benefits of a well-designed exhaust system in improving mold efficiency and product quality. ↩
-
Understand how adjusting gate size can enhance material distribution and complement exhaust gas strategies. ↩
-
This link explains how breathable steel’s unique properties enhance airflow and prevent air retention. ↩
-
Explore how advanced materials like composite resins optimize mold design by improving airflow and strength. ↩
-
Learn how smoother surfaces facilitate efficient melt flow, reducing defects. ↩
-
Discover methods to enhance mold quality, ensuring superior product performance. ↩