Have you ever thought about how a small change in mold design could rescue your product from ugly fusion lines?
Careful mold design strategies like optimal gate placement, improved runner systems, and efficient venting enhance melt flow, reducing fusion lines. This results in stronger, more aesthetically pleasing molded parts with fewer defects.
I remember when I first faced the confusing problem of fusion lines. It happened during a project with a new gadget that required perfect looks. The challenge was very hard. But learning about mold design was enlightening. Optimizing gate placement was my first strategy. This allowed the plastic to move smoothly and evenly.
I chose a clever runner system to get material to every mold corner. Venting played a key role. It was like opening windows to let trapped air escape. This prevented a bad flow. Every adjustment was like tuning a musical instrument. Each part needed to work together to reach the goal. As I improved these skills, I realized something important. Attention to detail was not just about preventing lines. It improved the whole production process. I felt really proud of the products created.
Gate placement affects fusion lines in mold design.True
Proper gate placement ensures uniform melt flow, reducing fusion lines.
Venting is irrelevant to reducing fusion lines.False
Proper venting prevents air traps, reducing fusion line defects.
How Does Gate Placement Affect Fusion Lines?
Do you ever think about how gate placement changes a product’s success? Simple decisions often have big impacts.
Gate placement directly affects fusion lines. It determines the path and pressure of molten materials in injection molding. Proper gate placement reduces visible seams. This improves both strength and aesthetic look.
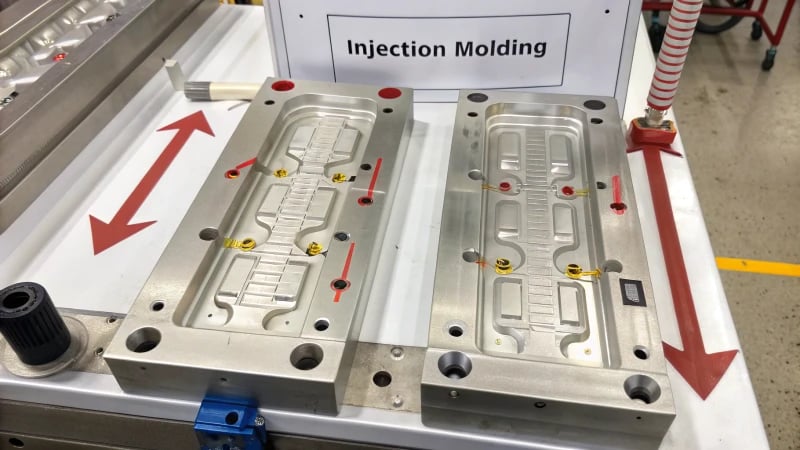
Importance of Gate Placement
Gate placement in injection molding is like a secret recipe. It blends art and engineering. These small details decide how visible seams, called fusion lines, appear. These seams don’t just affect the aesthetic1. They impact the product’s strength, too.
Optimization of Gate Placement
I remember what my mentor said when I began: "It’s all about the flow." This is so true. Optimizing gate placement helps molten plastic move easily. Imagine it like adding a drop of dye in a bowl of water—you want it to spread evenly. A single-point gate at a square mold’s center does just that.
Multi-Point Gate Synergistic Design
Complex designs demand more thought, though. Multi-point gate designs come into play here. Each gate must synchronize the flow well to avoid uneven meeting points. Think about conducting an orchestra; each musician needs to play at the right time, just like each gate requires similar temperatures and pressures at meeting points.
Aspect | Single-Point Gate | Multi-Point Gate |
---|---|---|
Design Simplicity | High | Low |
Ideal for | Simple Shapes | Complex Shapes |
Fusion Line Risk | Lower | Higher (if not optimized) |
Designing the Runner System
The runner system plays an important role. Incorrect designs invite many problems. The runner’s size and shape matter greatly. I once changed to a round cross-section runner—this change reduced heat loss and improved flow balance significantly.
- Cold Material Cavities: These cavities work like tiny heroes by capturing cold material before it ruins fusion lines. The size must match the material volume and injection cycle.
Mold Parting Surfaces and Air Venting Design
Picking the right parting surface is a skill; avoid areas that need to look good. I worked on a curved project once where choosing the right surface made fusion lines almost disappear.
- Venting Design: Good venting is essential; many times, I’ve adjusted vent slots at cavity corners to get perfect airflow, preventing air pockets from disturbing melt confluences.
Utilizing Mold’s Internal Structure
Small things like flow guide blocks or grooves become lifesavers as they guide melt flows smoothly. Adjusting surface roughness also helps ensure smoother flows with fewer fusion lines.
Gate placement seems technical yet it’s a mix of creativity and accuracy that can really change a project. Mastery in gate types, runner designs, and mold structures raises product quality significantly.
There’s more to discover in this fascinating area; each technique or case study presents a learning opportunity for those interested in delving deeper into specific techniques or case studies related to injection molding2. For further insights, visit the resources available.
Single-point gate placement reduces fusion line risk.True
Centralized single-point gates ensure uniform melt flow, minimizing fusion lines.
Multi-point gates are ideal for simple shapes.False
Multi-point gates suit complex shapes, needing synchronized flow to avoid fusion lines.
How does runner system design influence melt flow?
Have you ever thought about how the design of a runner system changes an injection molding process?
In injection molding, the runner system design is crucial. It controls how the melt flows. This design impacts everything from defect rates to the quality of the final product. Important aspects are gate placement, runner size and proper venting.
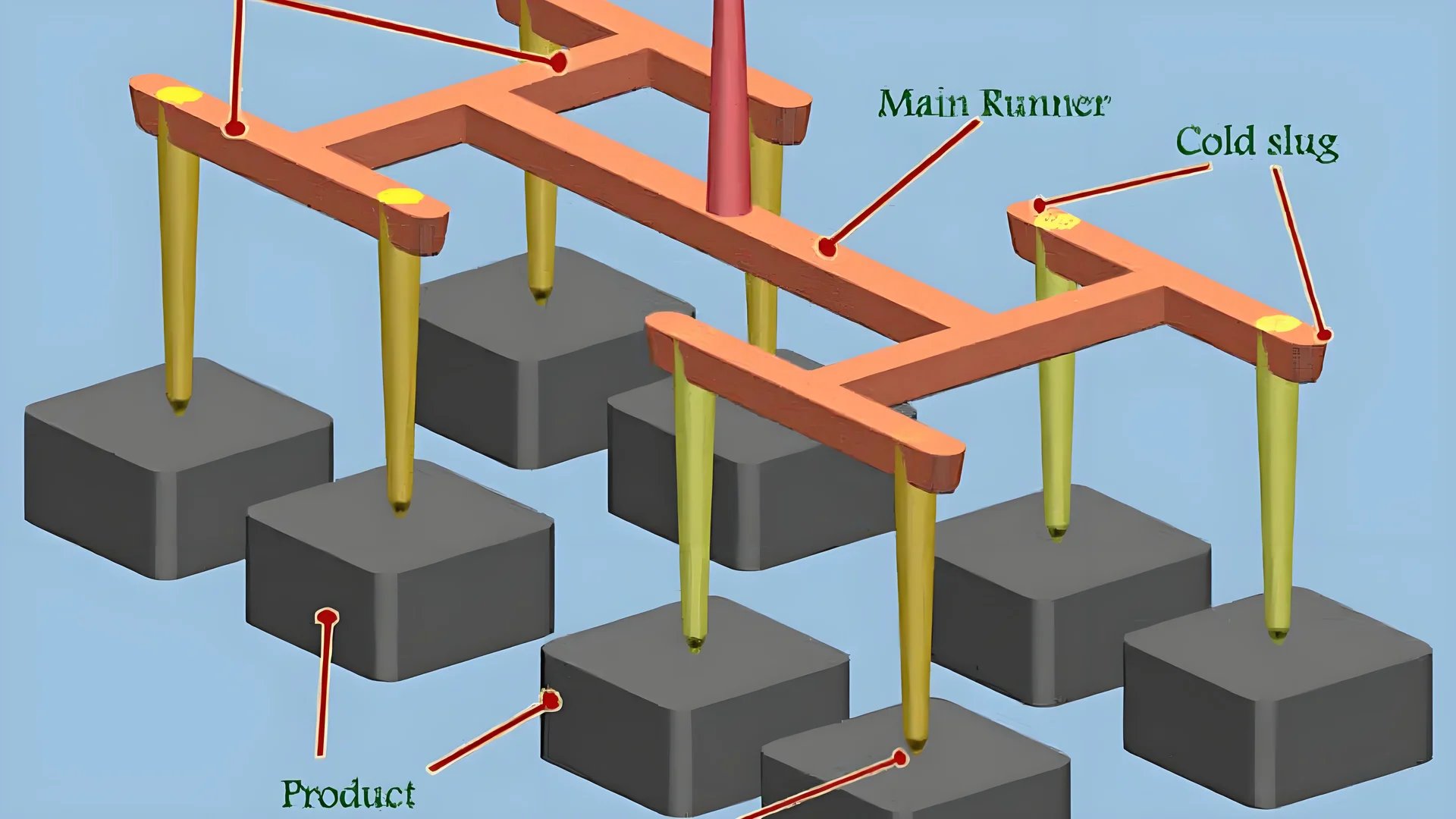
The Importance of Gate Placement
At first, I did not understand the importance of gate placement in injection molds. Imagine this situation: I tried to mold a simple cylinder. Everything seemed perfect on paper, but the result was disappointing. Then, I discovered the magic of placing a single-point gate3 in the center. This change created uniform melt flow and greatly reduced those annoying fusion lines from my earlier efforts. For complex shapes, I found using multiple gates worked best; it’s all about balancing the flow and reducing defects to improve overall quality.
Key Design Elements of Runner Systems
Main Runner and Manifold
In my early career, uneven melt distribution was a common problem. I learned that the size and shape of the main runner and manifold were very important. Choosing a round cross-section helped minimize heat loss and allowed stable melt flow. Avoiding sharp corners reduced stagnation risks, which prevented fusion lines4. Product consistency improved as a result.
Design Aspect | Impact on Melt Flow |
---|---|
Runner Shape | Reduces resistance and heat loss |
Manifold Size | Maintains stable flow |
Cold Material Cavities | Collects cold material, preventing fusion lines |
Cold Material Cavities
Strategic placement of cold material cavities became a key lesson for me. Initially, I missed their role in trapping initial cold material. Discovering this was probably a game-changer as it kept my mold cavity clear of obstacles affecting melt fusion.
Mold Parting Surfaces and Venting Design
Selecting the right parting surfaces was critical in my design process to avoid key appearance areas while managing melt flow effectively. A well-planned venting design released trapped air efficiently, stopping those frustrating air pockets.
Flow Guidance within Molds
Flow guide blocks or grooves directed the melt along paths I desired, providing even distribution around complex structures like ribs or bars. Adjusting surface roughness in the mold was another technique; smoother surfaces significantly improved fusion quality by lowering shunting.
Applying these design principles brought real change to my molding processes. It’s amazing how careful attention can strongly impact product quality and manufacturing efficiency.
Central gate placement ensures uniform melt flow in simple shapes.True
Central gates in simple geometries like squares ensure even melt distribution.
Sharp corners in runner design improve melt flow efficiency.False
Sharp corners increase stagnation risks, hindering efficient melt flow.
Why is Proper Venting Critical in Mold Design?
When I started studying mold design, venting appeared as a small detail. However, venting is crucial. It plays a major role in preventing frustrating defects.
Proper venting in mold design is very important. Trapped air and gases find escape routes during the molding process. This process prevents defects. Air pockets, surface blemishes and incomplete fills reduce significantly.
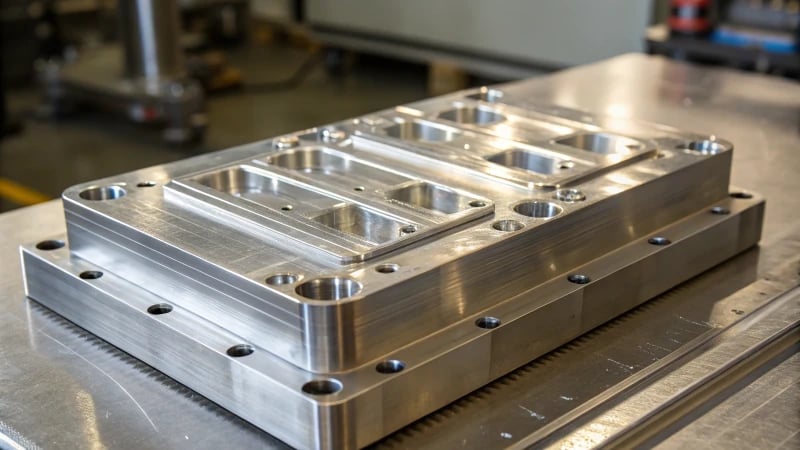
The Role of Venting in Mold Design
Venting is a critical aspect of mold design5 that ensures the quality of molded products. When molten plastic is injected into a mold, air and gases are displaced. If not vented properly, defects like air pockets or surface blemishes can occur. I learned this lesson the hard way during my first major project.
Effective Venting Techniques
- Venting Slots: Placing these slots strategically at locations where the mold fills last, such as corners or edges, significantly enhances efficiency.
- Gas Permeable Steel: This material allows gases to pass through while containing the plastic, ensuring a smooth venting process.
Venting Aspect | Description |
---|---|
Location | Corners, edges |
Material | Gas permeable |
Depth & Width | Depends on material |
Avoiding Common Defects with Proper Venting
Without proper venting, several issues may arise:
- Air Pockets: These gaps weaken the part’s strength by creating voids within the molded part.
- Surface Blemishes: Trapped air and gases cause cosmetic flaws on the product’s surface.
- Incomplete Fills: Air can block plastic flow, leaving parts unfilled.
Through trial and error, I found that venting slots should not be too wide or too shallow. The size depends on factors like the type of plastic used and injection molding settings6.
Interplay of Venting and Runner System Design
The runner system design also affects venting efficiency. A well-designed runner system facilitates better flow and reduces backpressure, allowing air to escape easily.
- Main Runner & Manifold: Their size and shape must align with product needs to maintain steady flow and support effective venting.
- Cold Material Cavities: Positioned at the end of flow to capture cooler materials that may block proper venting.
By arranging these components effectively, I optimized the venting process7, promoting seamless fusion of the melt and minimizing defects. Noticing these small details avoids costly rework or defects and makes molds work efficiently.
Venting prevents air pockets in molded products.True
Proper venting allows trapped air to escape, avoiding voids.
Gas permeable steel is ineffective for venting.False
Gas permeable steel efficiently lets gases pass, aiding venting.
How Do Internal Mold Structures Influence Melt Flow?
Have you ever thought about how small features in mold design change how melted plastic moves to become a perfect product?
Internal mold structures affect melt flow. They strategically place gates. They design effective runner systems. They adjust surface textures. These elements lead to even distribution. They minimize fusion lines. They improve product quality. They really improve quality.
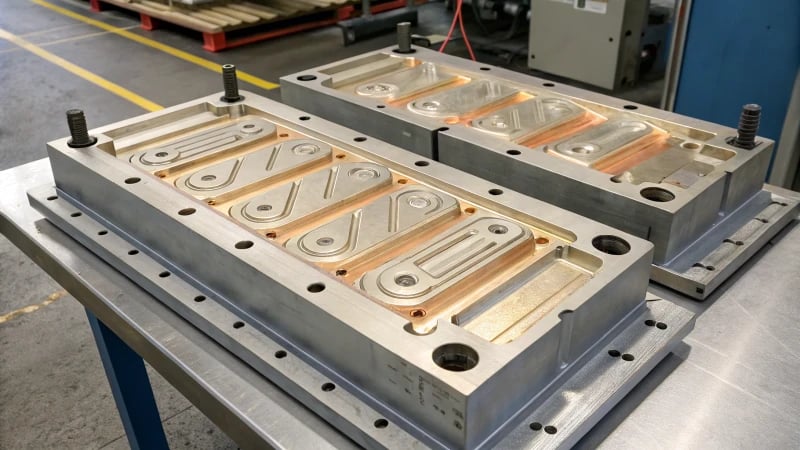
Gate Placement Optimization
Imagine working on a project where placing one small gate changes everything. It’s like when I moved my living room furniture and suddenly had much more space! In mold design, putting the gate in the center of a square or round shape helps the plastic spread evenly. It’s like sunlight through a window. This smart positioning reduces troublesome fusion lines that spoil a product’s smooth appearance.
Larger or complex shapes require multiple gates, like many doors letting a crowd leave a stadium smoothly. Multi-point gate designs allow each gate to work with others, guiding the melt easily through the mold. When melt from different gates meets at similar temperatures and pressures, it blends beautifully like a well-played symphony.
Runner System Design
A good runner system is like planning a perfect road trip route. The right size and round shapes reduce heat loss and resistance, helping the melt flow effortlessly through the mold. Imagine a car smoothly gliding down a highway. Avoiding sharp corners is important, much like avoiding surprising speed bumps!
Cold material cavities at the flow channel’s end act like little traps for chilly materials. These could disrupt your journey (melt fusion). Matching their size to the plastic volume and injection cycle gives you a smooth ride every time.
Feature | Importance |
---|---|
Main Runner Size | Ensures stable melt flow |
Manifold Shape | Minimizes resistance |
Cold Material Cavities | Prevents cold material disrupting fusion |
Mold Parting Surfaces and Venting
Choosing mold part surfaces is like picking a shirt that doesn’t need ironing. Avoiding part surfaces in key areas stops visible marks just as skipping tricky seams prevents wrinkles on clothes. With complex surfaces, even melt flow reduces weld lines.
Venting design is very important. It’s like opening windows to bring in fresh air, preventing air pockets that spoil your product. Strategic venting slots at cavity corners help, making sure everything works smoothly.
Utilizing Mold Internal Structures
Internal mold structures guide the melt like expert guides lead tourists on scenic tours. Flow guide blocks or grooves steer the path, filling every space evenly. Adjusting surface roughness in tricky areas smoothens the journey, similar to freshly paved roads.
For practical tips, explore our plastic injection molding techniques8. These show theory with real-world examples. By refining these parts, manufacturers improve melt flow hugely. Quality and efficiency benefit from this.
Look deeper into runner system designs9. They really affect different materials and shapes.
Central gates minimize fusion lines in square molds.True
Central gates provide uniform radial flow, reducing fusion lines.
Round runners increase heat loss in the melt flow.False
Round runners actually minimize heat loss and resistance.
How Does Surface Roughness Influence Manufacturing Defects?
Do you ever think about how something as basic as surface texture affects a product’s quality? Sometimes it decides the product’s success or failure.
Surface roughness is very important in manufacturing. It affects how materials interact and helps reduce defects. Fine-tuning surface textures allows manufacturers to reduce problems like fusion lines and air pockets. This process really improves product quality. It also increases durability. Durability matters a lot.
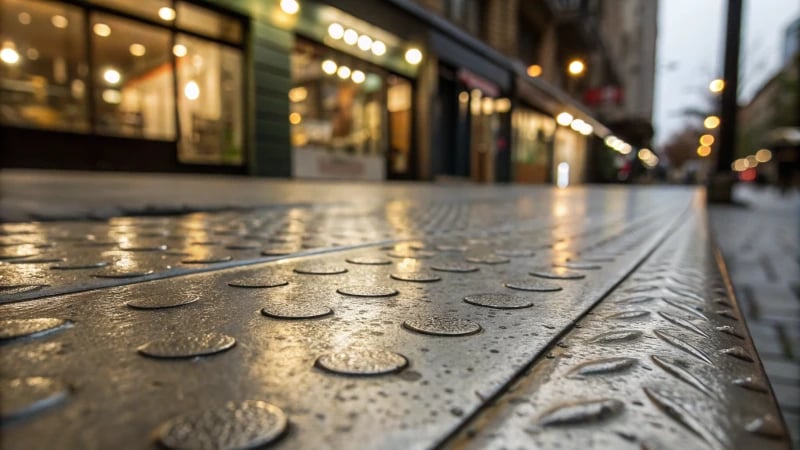
The Impact of Surface Texture on Material Flow
When I first explored mold design, I was really amazed. Even small changes in surface texture changed how materials behaved during production. Picture pouring honey over a smooth table and then a rough one. Surface roughness affects how materials move. A smooth surface allows materials to flow evenly, filling molds uniformly. This smoothness reduces defects like fusion lines.
Roughness Level | Effect on Material Flow |
---|---|
High Roughness | Increased flow resistance |
Medium Roughness | Balanced flow control |
Low Roughness | Smoother, consistent flow |
Defect Reduction Through Surface Optimization
In injection molding, I quickly realized adjusting mold core surface roughness is very important. It’s like tuning a guitar to get perfect sound. With the right adjustments, defect rates can drop dramatically. Adjusting roughness helps materials fuse better, stopping air pockets and uneven joins.
- Example: I once faced a tough project. In areas prone to shunting, reducing roughness improved melt flow and fusion quality.
Practical Applications in Mold Design
Optimization of Gate Placement:
- Placing single-point gates well encourages balanced material flow. For complex shapes, using a multi-point gate design10 helps the melt meet evenly.
Design of Runner Systems: Good runner and manifold size keeps flow steady. It also reduces heat loss and minimizes stagnation and flaws.
Design Element | Purpose |
---|---|
Main Runner Size | Stabilizes flow, reduces heat loss |
Cold Material Cavities | Traps cold melt, prevents defects |
Air Venting and Surface Roughness Synergy
Designing vents was another big lesson for me. Well-vented molds let gases escape easily. Adjusting surface roughness near vents enhances air expulsion and reduces defect formation.
- Venting Strategy: Placing vents in smart spots ensures air and gas escape smoothly, avoiding air pockets that lead to defects.
Conclusion
Surface roughness is not just a small detail; it’s a key factor in lowering manufacturing defects. Optimizing it greatly improves product quality and reliability. Knowing how it interacts with other design parts is crucial for the best results in manufacturing processes.
This analysis shows the great importance of careful surface texture management in cutting defects across many uses.
High surface roughness increases flow resistance.True
High roughness creates friction, hindering material movement.
Surface roughness has no effect on defect rates.False
Adjusting roughness optimizes flow, reducing defects.
Conclusion
Optimizing mold design through strategic gate placement, runner systems, and effective venting significantly reduces fusion lines, enhancing product appearance and strength in injection molding processes.
-
Discover how strategic gate placement enhances product appearance by minimizing visible seams. ↩
-
Learn about the critical role of gate placement in achieving defect-free products. ↩
-
Learn about single-point gates and how they ensure uniform melt flow in molds with simple geometries. ↩
-
Understand the causes of fusion lines and how proper runner design can prevent them. ↩
-
Discover why venting is vital for eliminating defects like air traps in molds. ↩
-
Learn about the critical parameters that influence how effectively a mold is vented. ↩
-
Explore strategies to enhance venting efficiency in injection molds. ↩
-
Discover practical applications of guiding melt flow in injection molding. ↩
-
Learn how runner systems influence melt flow and product quality. ↩
-
Learn about multi-point gate strategies for achieving better melt distribution in complex mold designs. ↩