In the competitive world of manufacturing, cost efficiency is paramount.
Mold design helps reduce injection molding costs by simplifying mold structures, optimizing runner systems, selecting appropriate materials, and improving processing techniques. These strategies enhance production efficiency, lower maintenance needs, and increase the lifespan of molds, ultimately saving costs.
While this offers a quick overview, delving deeper into each aspect reveals more about how these strategies can be tailored to specific production needs. Let’s explore the expert insights that can transform your injection molding process.
Simplifying mold structures reduces injection molding costs.True
Simplified designs minimize manufacturing complexity, reducing costs.
What Role Does Mold Structure Play in Cost Reduction?
In the world of injection molding, efficient mold structure design is key to cost reduction, improving production efficiency and product quality.
Mold structure influences cost reduction by simplifying designs, optimizing runner systems, and using standard parts. These strategies minimize manufacturing and maintenance costs while enhancing production efficiency. By reducing complexity and using cost-effective materials, businesses can achieve substantial savings.
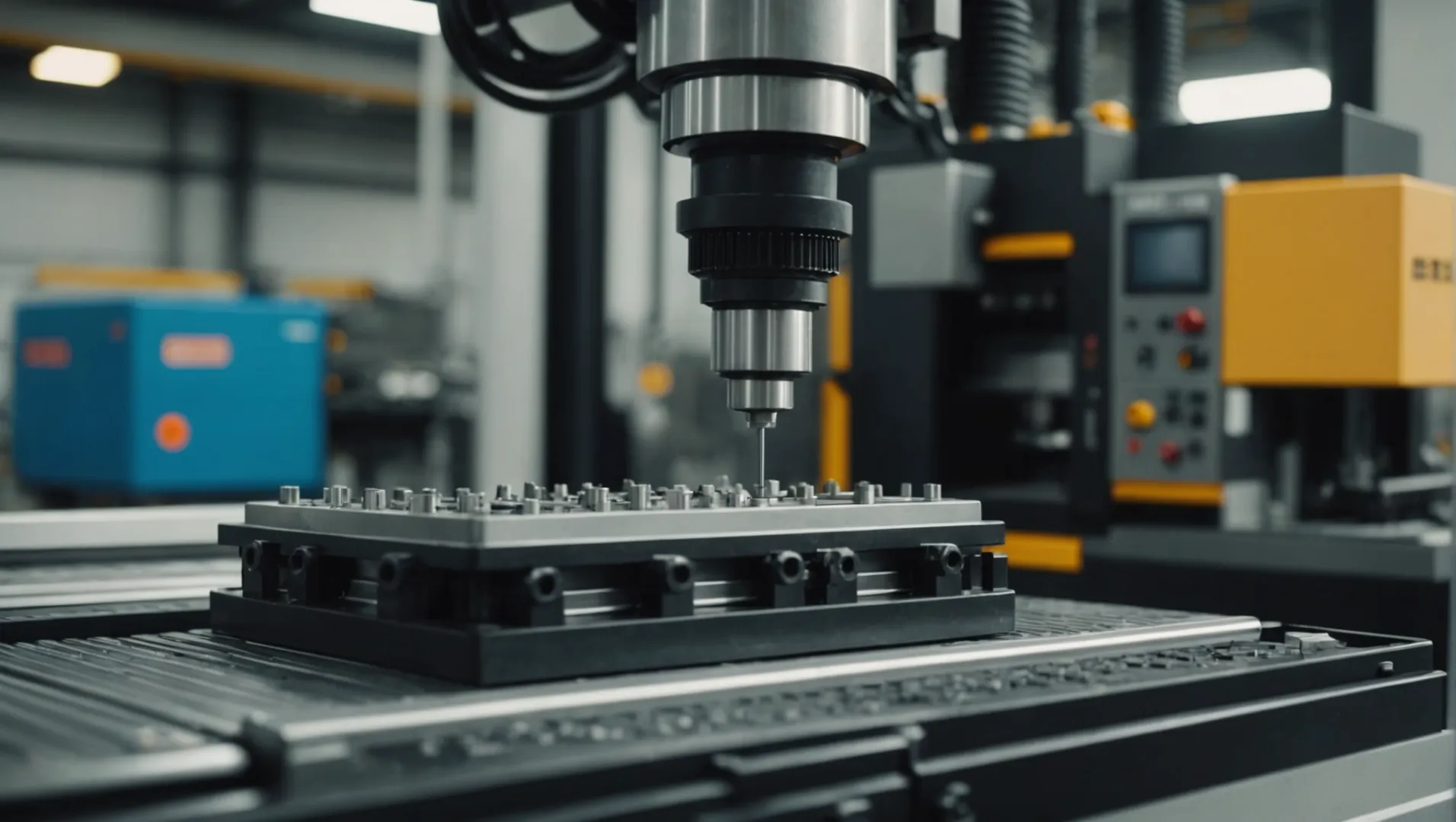
Simplifying Mold Structures
One primary way mold structure affects cost is through simplification. Simplifying mold design by minimizing complex features such as sliders and inclined tops can significantly reduce manufacturing and maintenance costs. For instance, adjusting a product’s design to avoid using sliders for demolding can lead to substantial savings. This approach not only cuts down on initial production expenses but also decreases the likelihood of mechanical failures1 during production, enhancing overall reliability.
Utilizing Standard Parts
Using standard mold frames and parts is another strategy to lower costs. Standard components are generally less expensive, readily available, and versatile. Incorporating these elements into mold design can shorten procurement cycles and simplify the manufacturing process, effectively reducing time and cost associated with custom part development.
Optimizing Runner Systems
The design of the runner system is critical in reducing waste and improving material efficiency. By optimizing runner size and shape according to product specifications, companies can ensure smooth plastic flow while minimizing residual waste. For example, using a thinner runner for small products reduces plastic usage. Additionally, implementing a hot runner system can further decrease plastic waste and improve production speed, though this option requires careful consideration of initial investment costs.
Selecting Appropriate Mold Materials
Choosing the right materials for mold construction directly impacts cost efficiency. Lower-cost steels may suffice for low-production runs, whereas high-quality steels are necessary for large-scale productions demanding durability and wear resistance. Additionally, considering machinability and heat treatment performance when selecting materials can further reduce manufacturing costs.
Incorporating Insert Structures
Insert structures in molds can prolong lifespan and reduce maintenance costs. For example, using inserts in areas prone to wear allows for easy replacement without the need for a complete mold overhaul. Material selection for inserts should align with specific part requirements—carbide for high hardness or standard steel for less demanding applications—further tailoring cost savings.
Through these strategic design choices, businesses can significantly reduce injection molding costs while maintaining or even enhancing product quality and production efficiency.
Simplifying mold structures reduces manufacturing costs.True
Reducing complexity in mold design cuts down production and maintenance costs.
Using custom parts always lowers mold production costs.False
Custom parts increase costs due to longer procurement and development times.
How Does Material Selection Impact Mold Costs?
Choosing the right material for mold construction is crucial in managing costs in injection molding.
Material selection impacts mold costs by determining the longevity, maintenance needs, and production efficiency of the molds. Using high-quality materials can reduce wear and tear, lowering long-term expenses.

Importance of Choosing the Right Steel
Selecting the appropriate steel for molds plays a vital role in managing costs. Lower-cost steels might seem appealing initially but could result in higher expenses due to frequent replacements and repairs. For instance, using mirror steel for products requiring high surface quality can enhance durability and reduce long-term costs.
Additionally, considering the machinability and heat treatment performance of mold steel is critical. Opting for materials that are easier to process and treat can significantly cut down manufacturing time and costs. This choice directly influences the efficiency of production cycles.
Leveraging Insert Structures
Insert structures are a strategic way to manage costs, especially in high-wear areas of a mold. By using inserts, it’s possible to replace only the worn-out parts without replacing the entire mold, which drastically reduces maintenance costs. For example, carbide inserts might be used for sections requiring high hardness, while less demanding areas might utilize standard steel inserts.
This approach not only prolongs the mold’s service life but also offers flexibility in material choice, allowing for cost savings without compromising on performance.
Balancing Cost with Production Needs
It’s essential to balance the cost of materials with production requirements. For products with smaller production runs, using less expensive materials might be sufficient. However, for large-scale production, investing in higher-grade materials that ensure durability and efficiency can be more economical in the long run.
The key is to align material choices with specific project needs. By understanding the expected production volume and product specifications, manufacturers can make informed decisions that optimize costs effectively. For more detailed insights into aligning material selection with production goals, explore in-depth material selection strategies2.
High-quality materials reduce mold wear and tear.True
High-quality materials enhance durability, minimizing wear and tear.
Using lower-cost steels always saves money.False
Lower-cost steels can lead to frequent replacements, increasing costs.
Why is Mold Processing Technology Crucial for Efficiency?
Mold processing technology is a key driver of efficiency in manufacturing, significantly impacting production speed and cost.
Mold processing technology enhances efficiency by optimizing machining methods, selecting precise parameters, and integrating special techniques. These strategies ensure higher accuracy, reduced waste, and lower operational costs, making it essential for competitive manufacturing processes.
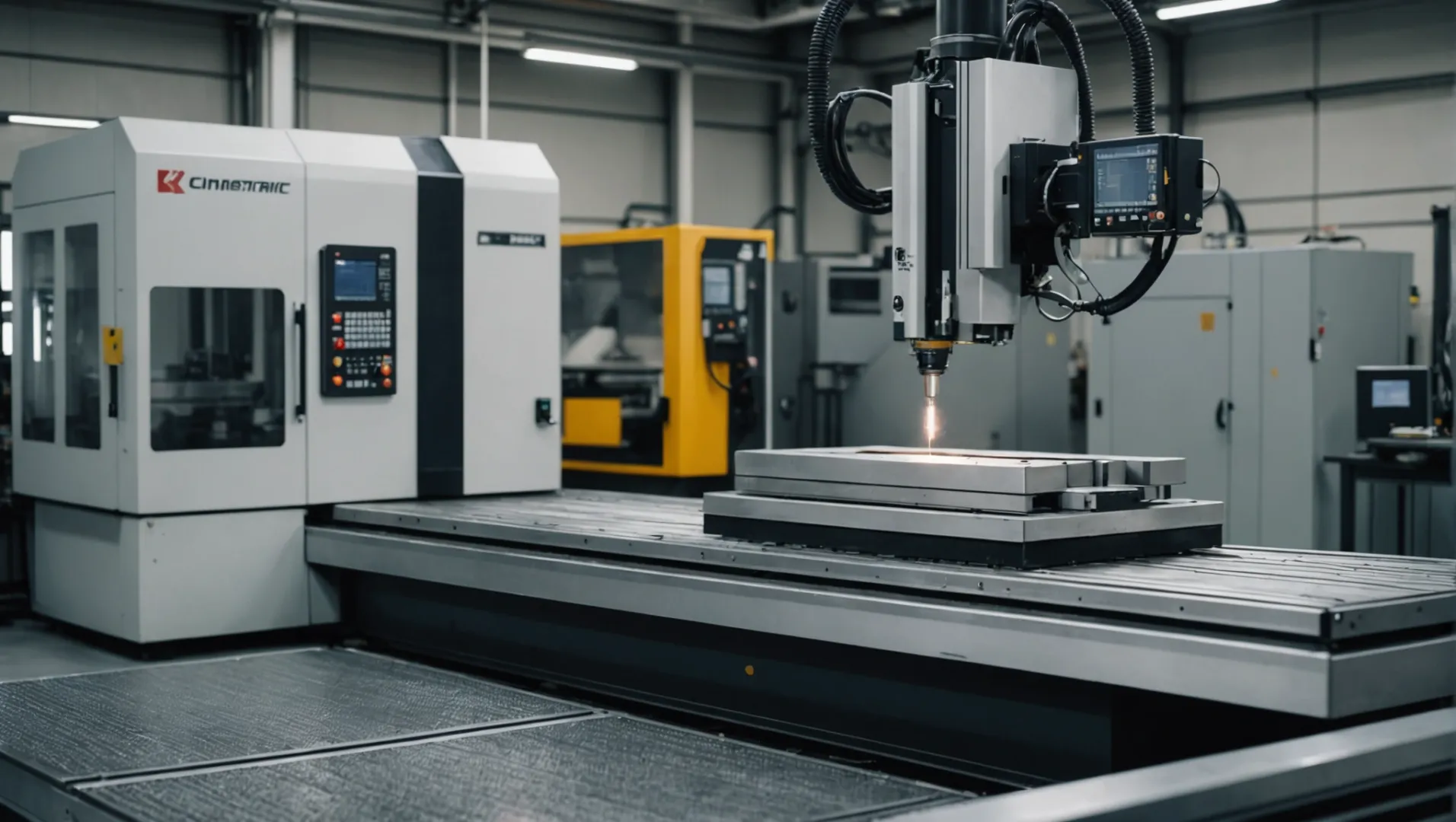
Optimizing Machining Methods
Selecting the appropriate machining method is foundational to enhancing mold efficiency. Techniques like CNC machining centers are ideal for complex curved surfaces, ensuring high precision and quality. For simpler structures, traditional machine tools can suffice, offering cost-effective solutions without compromising on quality. Additionally, incorporating methods such as EDM and wire cutting can address challenges posed by intricate components, improving accuracy and reducing the time required for production.
The Role of Processing Parameters
Careful selection of processing parameters—such as cutting speed, feed rate, and cutting depth—is critical. By optimizing these parameters, manufacturers can enhance processing efficiency and minimize costs. These adjustments not only accelerate production cycles but also extend the lifespan of cutting tools by reducing wear. Implementing high-speed cutting technology further boosts efficiency by enabling faster cutting speeds and feeds while maintaining lower cutting forces.
Special Processing Techniques
Specialized processing techniques play a pivotal role in achieving precise mold structures that conventional methods might not handle efficiently. For instance, EDM3 allows for the creation of complex geometries with high precision, vital for intricate mold designs. Similarly, wire cutting offers a solution for achieving tight tolerances that are otherwise challenging, ensuring that the final product meets exacting standards.
These advanced techniques collectively enhance the processing capability of molds, ensuring that they deliver high performance over extended production runs. By integrating these methods into the production workflow, businesses can achieve significant cost savings and elevate their manufacturing capabilities.
CNC machining centers are ideal for simple mold structures.False
CNC machining centers are best for complex surfaces, not simple ones.
EDM allows creation of complex geometries with high precision.True
EDM is used for precise, intricate mold designs, enhancing accuracy.
How Can Regular Maintenance Extend Mold Lifespan?
Regular maintenance is essential for extending mold lifespan and optimizing production costs. But how does it work?
Regular maintenance extends mold lifespan by preventing wear and tear, minimizing downtime, and reducing the need for costly repairs. By routinely cleaning, inspecting, and replacing worn components, manufacturers can maintain mold efficiency and functionality, ultimately enhancing productivity and cost-effectiveness.

Importance of Routine Maintenance
Routine maintenance of injection molds is akin to getting regular check-ups for machinery. Consistent care ensures that all parts of the mold are in optimal condition, which significantly reduces wear and tear over time. This practice not only extends the mold’s operational life but also maintains the quality of the products being manufactured. Ignoring maintenance can lead to severe issues like rust, which compromises both the mold and the final product.
Key Maintenance Practices
-
Cleaning
Cleaning is fundamental to mold maintenance. Residue from materials can accumulate on the mold surfaces, leading to defects in products. Regular cleaning helps to prevent this buildup and ensures that each product meets quality standards.
-
Inspection and Replacement
Regular inspections allow for early detection of wear and potential failure points within the mold. This proactive approach involves checking for signs of rust, wear on key parts, and ensuring all moving components are well-lubricated. If any parts are found to be worn out or damaged during inspections, they should be replaced immediately to prevent further damage.
-
Lubrication
Proper lubrication minimizes friction between moving parts, reducing wear and extending the lifespan of the mold. It’s important to use the right type of lubricant suited for the specific materials and conditions under which the mold operates.
Benefits of Regular Maintenance
Implementing a robust maintenance schedule can prevent unexpected breakdowns that halt production, saving both time and money. Moreover, consistent maintenance ensures that molds produce high-quality outputs with minimal defects, enhancing customer satisfaction and maintaining competitive edge in the market.
Implementing a Maintenance Schedule
Creating a detailed maintenance schedule is crucial. This schedule should outline regular cleaning sessions, inspection checklists, lubrication routines, and timelines for component replacements. By adhering to a structured plan, manufacturers can keep their molds in top working condition and avoid costly repairs or replacements.
In conclusion, while regular maintenance requires time and resources upfront, it pays off significantly by extending mold lifespan, improving product quality, and reducing overall production costs. For more insights on mold structure design4 and its impact on cost efficiency, exploring expert opinions can provide valuable guidance.
Regular maintenance extends mold lifespan.True
Routine care prevents wear, reduces downtime, and avoids costly repairs.
Ignoring maintenance improves mold efficiency.False
Neglect leads to rust and defects, compromising mold and product quality.
Conclusion
By implementing effective mold design strategies, you can significantly reduce injection molding costs while maintaining quality. Consider these insights to optimize your production processes for better financial outcomes.
-
Explore the advantages of minimizing mechanical complexity for enhanced reliability.: It’s a highly repeatable process that enables companies to create high volumes of identical plastic parts with good tolerances at a low cost per part. ↩
-
Discover detailed strategies for aligning material choice with production goals.: Learn how to select the right material for your injection molding design with this technical overview of thermoplastic resins. ↩
-
EDM is vital for precision in complex mold designs.: Like the Ram EDM, the wire EDM uses electrical current to remove material. The difference is that instead of using a machined electrode, a wire … ↩
-
Discover how thoughtful design reduces costs and enhances efficiency.: Designing reasonable fillets at corner positions can reduce EDM operations and related material costs, significantly saving on mold processing … ↩