Imagine a world where every molded product is flawless—this is the promise of a well-designed mold cooling system.
Mold cooling systems are essential to injection molding quality because they ensure uniform temperature distribution, leading to better dimensional accuracy, reduced deformation, and improved surface appearance. They also enhance production efficiency by shortening cycle times and decreasing energy use.
Let’s dive deeper into how strategic cooling system design can eliminate common defects and optimize your production process.
Efficient cooling reduces injection molding cycle times.True
Proper cooling shortens the solidification phase, enhancing production speed.
What Are the Key Components of a Mold Cooling System?
Understanding the key components of a mold cooling system is crucial for enhancing the efficiency and quality of injection molded products.
The essential components of a mold cooling system include cooling channels, temperature controllers, pumps, and heat exchangers. Each plays a vital role in maintaining consistent mold temperatures, thereby preventing defects such as warping and improving overall product quality.
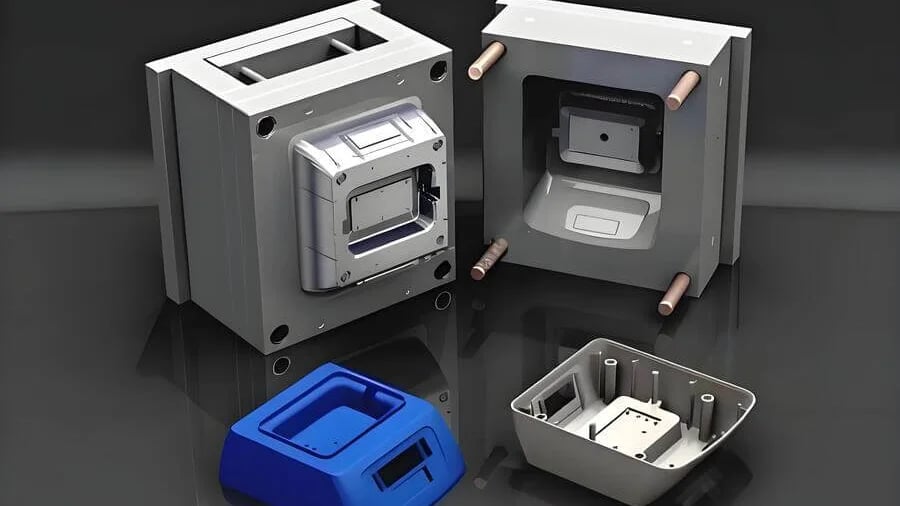
Cooling Channels
Cooling channels are strategically placed pathways within the mold that allow coolant to circulate and remove heat from the mold material. These channels are crucial because they determine how effectively and uniformly the mold is cooled. Inadequate design or placement can lead to uneven cooling, causing defects like warping or sink marks.
A good design often involves optimizing the layout1 of these channels to ensure uniform distribution of temperature across the mold surface. The arrangement should minimize temperature gradients that could result in product deformation.
Temperature Controllers
Temperature controllers are used to maintain the mold at a consistent temperature by regulating the flow of coolant through the channels. These devices are critical for achieving high-quality output, as they prevent overheating and ensure a stable production environment.
Modern controllers can be programmed to respond to changes in mold temperature in real time, adjusting the coolant flow rate accordingly. This precision ensures that products meet exact specifications, which is especially important for precision parts with strict dimensional tolerances.
Pumps
Pumps are the heart of a cooling system, propelling the coolant through the network of channels. The efficiency of these pumps directly impacts the system’s ability to maintain consistent mold temperatures.
Choosing the right pump involves considering factors such as flow rate, pressure capacity, and energy efficiency. An effective pump not only enhances cooling but also contributes to reducing operational costs by lowering energy consumption.
Heat Exchangers
Heat exchangers are employed to transfer heat from the coolant to an external medium, effectively removing it from the system. These components play a pivotal role in maintaining the desired temperature in the mold by ensuring that the coolant can absorb more heat during each cycle.
The choice of heat exchanger—whether air-cooled or water-cooled—depends on specific production requirements and environmental conditions. Water-cooled systems are often preferred for their superior efficiency in large-scale operations where rapid heat removal is necessary.
Integration and Optimization
The seamless integration of these components is key to an efficient mold cooling system. For instance, aligning the capabilities of pumps with those of heat exchangers ensures that neither component becomes a bottleneck in heat removal.
Optimization involves continuous monitoring and tweaking of these components to achieve desired production outcomes while minimizing energy use. Employing advanced technologies such as computer-aided design2 can significantly enhance the design process, leading to more efficient systems.
Cooling channels determine mold cooling efficiency.True
Cooling channels' design and placement directly affect cooling uniformity.
Heat exchangers increase mold temperature.False
Heat exchangers remove heat, preventing mold temperature rise.
How Does Cooling Channel Design Influence Product Quality?
In the intricate world of injection molding, cooling channel design holds the key to producing high-quality plastic products.
Cooling channel design influences product quality by ensuring uniform temperature distribution, which helps maintain dimensional accuracy, reduce deformation, and enhance surface appearance. Properly designed cooling channels also improve production efficiency by minimizing cycle times and energy consumption.
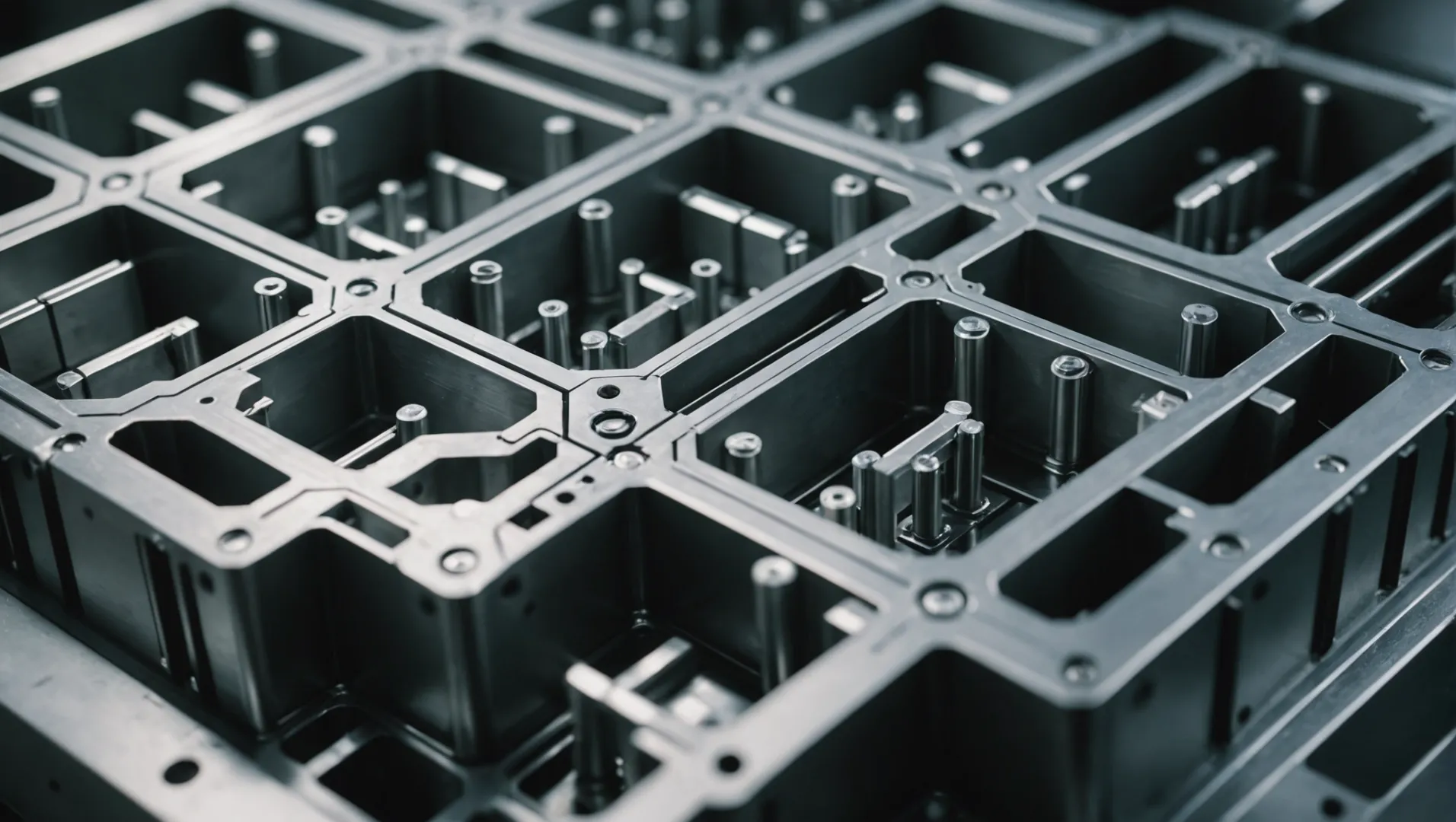
Ensuring Dimensional Accuracy
In injection molding, precision is paramount. The design of cooling channels plays a crucial role in maintaining the dimensional accuracy3 of plastic products. An optimized cooling system ensures even temperature distribution across the mold, thereby achieving consistent cooling and shrinkage rates throughout the molded part.
For instance, when manufacturing precision components like electronic housings, uneven cooling can lead to size discrepancies that exceed tolerance limits. This not only affects the assembly but can also impair the functionality of the final product. By implementing a well-thought-out cooling channel design, manufacturers can maintain stable molding sizes, crucial for high-precision applications.
Reducing Deformation
Deformation during the molding process is often a consequence of uneven cooling, resulting in internal stresses within the product. A strategically designed cooling channel system can significantly mitigate such stresses by promoting uniform cooling. This is especially vital for large, thin-walled parts such as automotive panels or storage containers.
By increasing the number of cooling channels or optimizing their layout, manufacturers can effectively reduce warping or bending. This not only enhances the structural integrity of the product but also maintains its aesthetic appeal.
Enhancing Surface Quality
Surface defects like shrinkage marks, flow lines, and bubbles are common challenges in injection molding. These issues often arise from uneven cooling4, which affects the surface finish of the product. A robust cooling channel design can help mitigate these defects by ensuring even heat dissipation throughout the mold.
For products requiring high aesthetic standards, such as consumer electronics or cosmetic packaging, achieving a smooth, glossy finish is essential. Proper cooling channel design contributes to a flawless surface appearance by eliminating blemishes and enhancing gloss.
Boosting Production Efficiency
Beyond product quality, an effective cooling channel design is instrumental in enhancing production efficiency. By facilitating rapid heat transfer, it shortens the cooling phase of the molding cycle, thereby accelerating overall production times.
Efficient cooling not only reduces cycle times but also lowers energy consumption. By optimizing cooling channels and selecting appropriate cooling media, manufacturers can achieve significant cost savings while maintaining high production standards. This translates into increased throughput and profitability for injection molding operations.
Cooling channel design affects product surface quality.True
Proper cooling channels ensure even heat dissipation, reducing defects.
Uneven cooling does not impact dimensional accuracy.False
Uneven cooling leads to size discrepancies, affecting precision.
What Techniques Improve Cooling Efficiency in Injection Molding?
Effective cooling techniques are crucial in injection molding to enhance product quality and production efficiency.
Techniques to improve cooling efficiency in injection molding include optimizing cooling channel design, using advanced cooling media, and employing simulation tools for precise thermal management. These methods ensure consistent mold temperatures, reducing defects and improving cycle times.
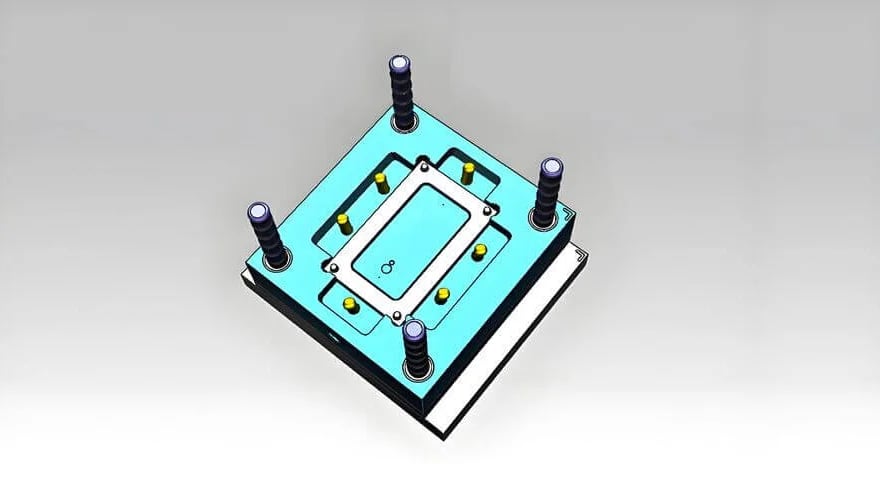
Optimizing Cooling Channel Design
The design of cooling channels plays a pivotal role in enhancing the efficiency of the cooling process. By strategically placing these channels, manufacturers can achieve uniform cooling, which is crucial for maintaining dimensional accuracy and reducing internal stresses that lead to deformation. For instance, increasing the number of cooling channels or arranging them to follow the contours of the mold can significantly improve heat dissipation.
Consider large thin-walled plastic parts like boxes; here, warping is a common issue due to uneven cooling. A well-designed cooling channel system can mitigate this by ensuring even temperature distribution across the mold surface.
Advanced Cooling Media
Switching from traditional water-based systems to more advanced cooling media can dramatically increase efficiency. Media such as thermal oils or specialized cooling fluids offer superior heat transfer properties, enabling faster cooling cycles. This is particularly beneficial in high-volume production settings where every second saved per cycle translates into substantial cost reductions.
For example, in the production of automotive interior parts, which often require high aesthetic standards, using advanced cooling fluids can reduce surface defects like shrinkage marks and bubbles by promoting even solidification.
Simulation Tools for Thermal Management
Incorporating simulation tools5 into the design phase allows engineers to predict and optimize the thermal behavior of molds before physical prototyping. These tools provide detailed insights into potential hot spots and enable adjustments in channel design and layout to achieve optimal cooling.
Simulations are particularly useful when dealing with complex mold geometries where traditional trial-and-error methods may fall short. By modeling various scenarios, manufacturers can ensure that the final mold design supports both product quality and efficient cycle times.
Maintenance and Monitoring
Regular maintenance and monitoring of the cooling system are crucial for sustained efficiency. Over time, mineral deposits or blockages can reduce the effectiveness of cooling channels. Implementing a preventive maintenance schedule6 ensures that systems operate at peak performance.
Moreover, integrating real-time monitoring systems can alert operators to any deviations in temperature or flow rates, allowing for quick corrective actions. This proactive approach helps maintain consistent product quality while minimizing downtime.
In summary, by leveraging optimized designs, advanced materials, simulation tools, and diligent maintenance practices, manufacturers can significantly enhance the cooling efficiency of injection molding processes.
Advanced cooling media reduce cycle times in injection molding.True
Advanced media offer superior heat transfer, speeding up cooling cycles.
Simulation tools are ineffective for optimizing mold thermal behavior.False
Simulations provide insights into hot spots, optimizing mold design.
Why Is Uniform Cooling Essential for High-Quality Molds?
Achieving uniform cooling is crucial for producing high-quality molds, influencing everything from dimensional accuracy to surface finish.
Uniform cooling in mold design is critical as it ensures consistent shrinkage, minimizes deformation, and enhances surface quality, preventing defects like sink marks and bubbles. It also improves production efficiency by reducing cycle time and energy usage.
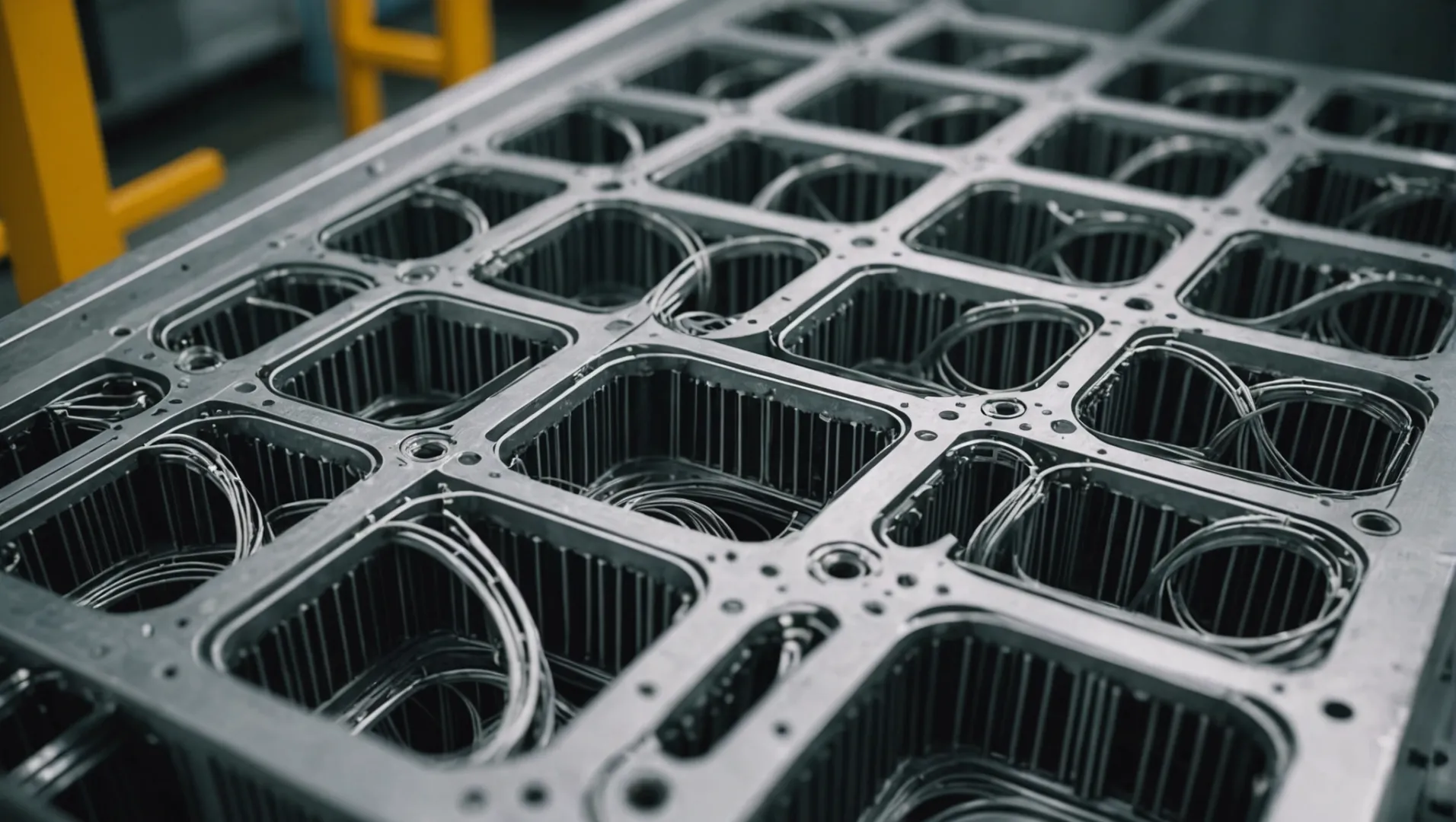
Impact on Product Dimensional Accuracy
Uniform cooling is essential for maintaining the dimensional accuracy of molded products. This aspect becomes particularly crucial when dealing with precision plastic parts. By distributing mold temperature evenly, the cooling system ensures that all areas of the mold cool at a consistent rate. This uniformity prevents some sections from shrinking more than others, thereby maintaining the intended size and shape of the product.
For example, consider the production of precision components like gears or electronic connectors. In such cases, even a slight deviation in size can lead to significant performance issues. A well-designed cooling system that ensures uniform temperature distribution can help maintain tight tolerances and prevent costly production errors.
Reducing Deformation
Internal stresses induced by uneven cooling can cause significant deformation in molded products. A well-optimized cooling system mitigates this issue by reducing stress differentials within the product. Large thin-walled products, such as plastic storage boxes, are particularly prone to warping if cooling is not uniform.
To achieve this, engineers can increase the number of cooling channels and strategically position them to ensure even heat dissipation. Such measures help in minimizing deformation and preserving the structural integrity of the product.
Enhancing Surface Quality
The surface quality of a product is greatly influenced by how uniformly it cools. Uneven cooling can lead to defects such as shrinkage marks, flow lines, and bubbles, which mar the appearance of the final product. For example, products with high visual standards, like smartphone cases or automotive interiors, demand a flawless finish.
By optimizing the cooling system to ensure even cooling across all areas of the mold, manufacturers can significantly reduce the occurrence of these surface defects. Additionally, achieving a smooth and glossy finish is possible when the entire surface cools evenly, enhancing both aesthetic appeal and perceived value.
Boosting Production Efficiency
Uniform cooling doesn’t just affect product quality; it also has a direct impact on production efficiency. Efficient cooling systems reduce cycle times by accelerating the rate at which products solidify and can be ejected from molds. This enhancement not only increases throughput but also reduces energy consumption, thereby lowering operational costs.
Consider large-scale production environments where each second saved per cycle translates into substantial economic benefits. By using advanced cooling techniques and materials, companies can achieve quicker cooling rates without compromising on quality.
Overall, designing an effective mold cooling system7 requires careful consideration of several factors, including channel layout and cooling medium choice. Ensuring uniformity in cooling leads to superior product quality and enhanced manufacturing efficiency.
Uniform cooling prevents mold deformation.True
Even cooling reduces internal stresses, minimizing product warping.
Uneven cooling enhances surface quality.False
Uneven cooling causes defects like shrinkage marks and bubbles.
Conclusion
In conclusion, optimizing your mold cooling system is pivotal for achieving superior injection molding quality and efficiency. Reflect on your current processes to unlock these benefits.
-
Learn strategies for optimizing channel placement for uniform temperature distribution.: Optimizing the design of the conformal cooling channel can increase the cooling rate of injection mold. The aim of this study was the problem of low cooling … ↩
-
Explore how CAD tools improve mold cooling system efficiency.: Experience superior mold design in CATIA V5 for your CAD/CAM services. Enhance precision, efficiency, and productivity in your manufacturing processes. ↩
-
Learn why maintaining dimensional accuracy is crucial for precision components.: Manufacturing Precision of Mold Dimensions: The precision with which the mold is manufactured is a key factor in determining the dimensional accuracy of the … ↩
-
Explore how uneven cooling leads to surface defects in molded products.: Uneven cooling also lengthens molding cycle. This is because uneven cooling causes plastic to shrink unevenly, leaving a high residual stress … ↩
-
Explore cutting-edge tools that optimize mold design through thermal simulations.: With the best-in-class analysis technology, Moldex3D can help you carry out in-depth simulation of the widest range of injection molding processes and to … ↩
-
Learn how regular maintenance enhances system performance and prevents costly downtimes.: 1. Preventive maintenance of injection molding machine`s hydraulic system · (1) Selection of hydraulic oil · (2) Working temperature of … ↩
-
Gain insights into optimizing mold designs for uniform cooling.: The right mold components can help improve mold cooling and thereby produce higher-quality parts. ↩