Facing issues with mold clamping force in your injection molding operations? You’re not alone.
Insufficient mold clamping force is commonly caused by mold design issues, incorrect machine settings, component failures, or material properties. Addressing these factors through optimized design, correct settings, regular maintenance, and material adjustments can effectively solve the problem.
While understanding the root causes is crucial, implementing the right solutions is equally important. This guide dives deeper into each cause and provides actionable solutions to ensure your molding process runs smoothly and efficiently.
Mold size can cause insufficient clamping force.True
Large molds may exceed machine capacity, leading to inadequate clamping.
How Does Mold Design Affect Clamping Force?
Understanding the intricacies of mold design is essential for achieving optimal clamping force.
Mold design significantly impacts clamping force by influencing factors such as mold size, parting surface design, and mold alignment. Addressing these elements can enhance clamping efficiency, ensuring the mold remains sealed during injection molding processes.
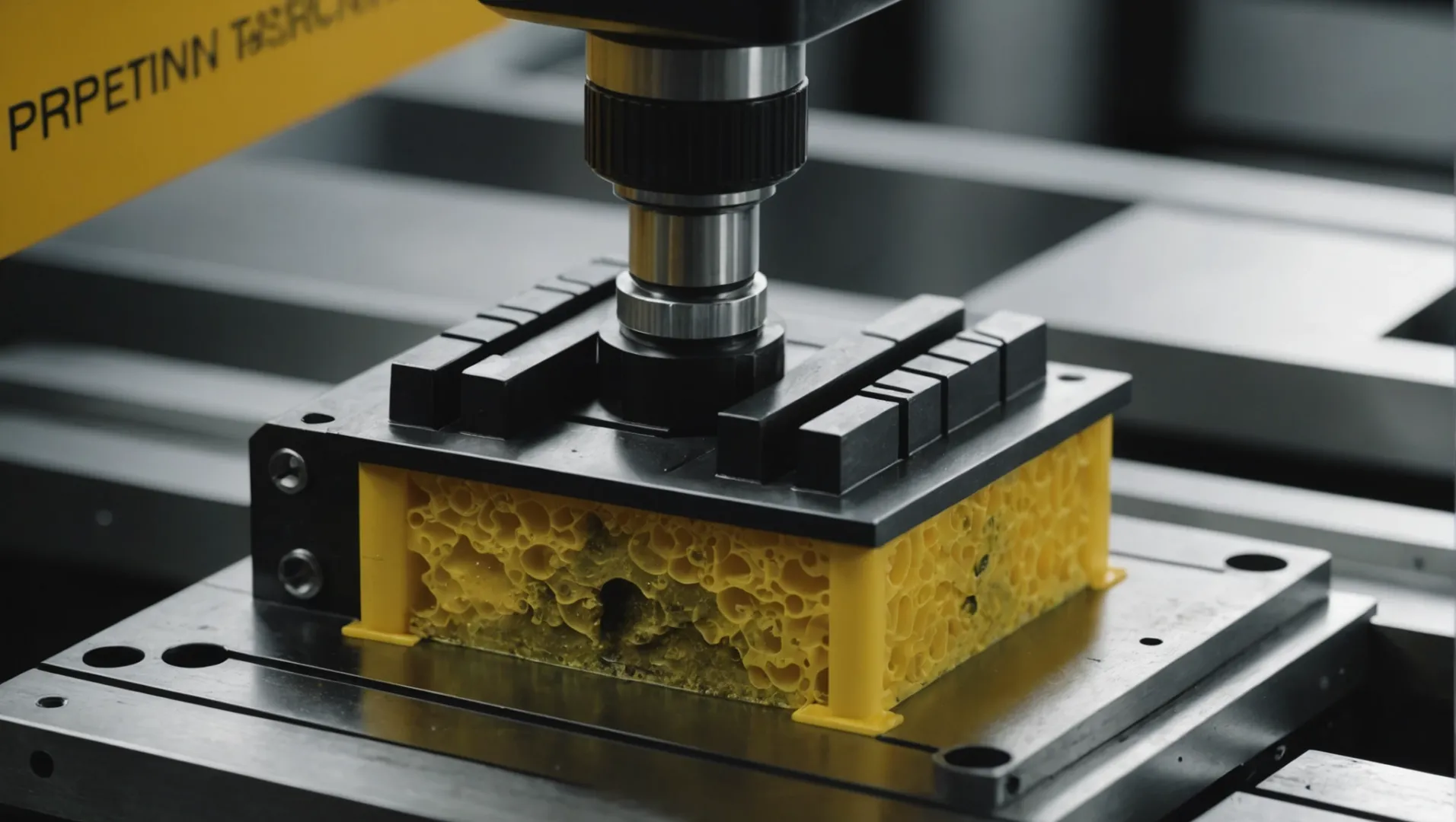
The Impact of Mold Size on Clamping Force
The size of a mold is directly related to the clamping force required during the injection molding process. When the projected area of a mold is too large for the machine’s capacity, the clamping force becomes insufficient. This discrepancy often occurs when attempting to use a machine with inadequate clamping capabilities for a larger mold. Such scenarios can lead to poor sealing and potential defects in the final product.
Example: Consider a scenario where an injection molding machine with a maximum clamping force of 200 tons is used to produce a product requiring 250 tons due to its large mold size. This mismatch results in inadequate force to keep the mold securely closed during injection.
Designing an Effective Parting Surface
The design of the mold’s parting surface plays a crucial role in maintaining sufficient clamping force. An improperly designed parting surface can lead to gaps that prevent complete sealing. This situation reduces the clamping force and affects the overall quality of the molded product. Ensuring that parting surfaces are well-designed and fit perfectly is vital for maintaining proper clamping force.
Example: A common issue arises when the parting line isn’t flat or contains impurities, which prevents the mold from closing tightly and leads to flash defects on molded parts.
Mold Alignment and Clamping Force
Mold alignment issues can also affect clamping force. Misaligned molds result in uneven distribution of clamping pressure, which may lead to insufficient force on certain sections of the mold. This misalignment can be rectified by ensuring that molds are installed correctly and that fastening bolts are uniformly tightened to maintain proper alignment.
Example: In one case, uneven bolt tightening caused one side of the mold to experience less pressure, resulting in leakage during molding.
Solutions for Optimizing Mold Design
- Redesign Large Molds: For oversized molds, redesigning to minimize projection area or choosing machines with higher clamping forces can be beneficial.
- Enhance Parting Surface Quality: Regular inspection and maintenance of parting surfaces help maintain their quality and ensure tight seals.
- Ensure Proper Installation: Regularly check mold installation for alignment and even tension across all fastening points.
By focusing on these aspects of mold design1, manufacturers can significantly improve clamping force efficiency, enhancing product quality and production reliability.
Mold size affects required clamping force.True
Larger molds need more clamping force to stay sealed.
Misaligned molds increase clamping force efficiency.False
Misalignment causes uneven pressure, reducing clamping efficiency.
What Machine Settings Can Lead to Clamping Issues?
Injection molding requires precision, and incorrect machine settings can jeopardize clamping force.
Improper machine settings, such as low clamping pressure and incorrect clamping speed, can lead to clamping issues. Ensuring the settings align with mold and product requirements is crucial to maintaining optimal clamping force.
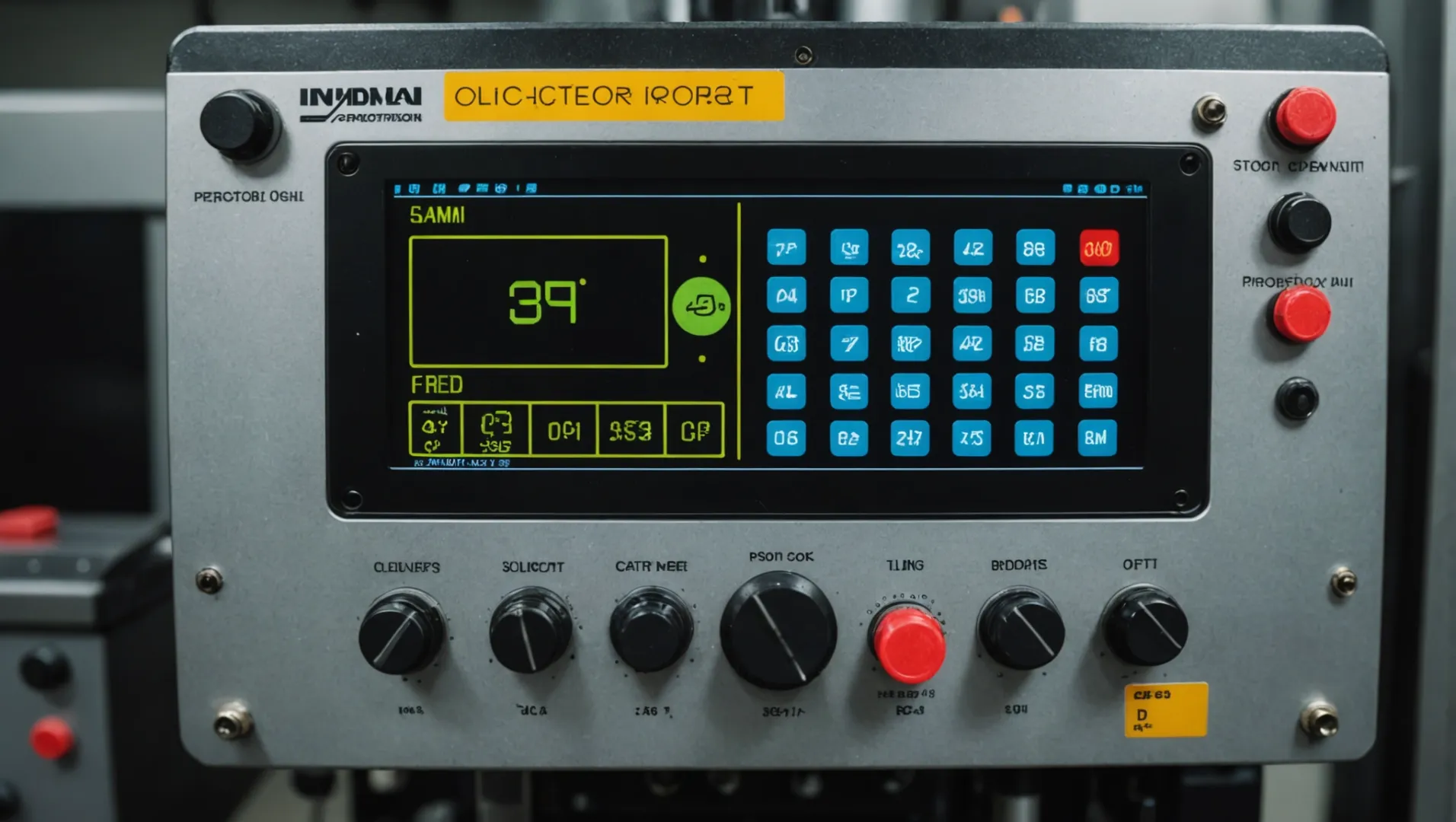
Understanding Machine Settings Impact on Clamping
In injection molding, machine settings play a pivotal role in ensuring the clamping force is both sufficient and consistent. Among these settings, the clamping pressure and clamping speed are two critical parameters that operators must carefully adjust.
Clamping Pressure
One of the most direct impacts on clamping force is the clamping pressure. If the pressure is set too low, it can lead to insufficient force needed to keep the mold tightly closed during injection.
Example: When manufacturing thin-walled components, a higher clamping pressure is often necessary to counteract the injection pressure. Failing to adjust this correctly can result in defects or poor-quality products.
To correct this, operators should assess the mold’s requirements and adjust the pressure incrementally, observing changes in product quality and mold sealing.
Clamping Speed
The speed at which the clamping occurs can also affect force distribution. A clamping speed that’s too fast can result in violent collisions, potentially damaging the mold and leading to uneven force distribution. Conversely, a speed that’s too slow may allow for leakage during clamping, thus reducing effective force.
Example: High-precision molds often require a carefully controlled clamping speed to ensure uniform force application without risking mechanical damage.
Operators should begin with a slower speed and gradually increase it while monitoring for any signs of leakage or force inconsistency.
Injection Molding Machine Calibration2
Regular calibration of injection molding machines ensures that all parameters, including those affecting clamping force, are accurate and aligned with production needs. Calibration involves checking and adjusting the machine’s sensors and control systems to ensure precision.
Monitoring and Adjustments3
Implementing regular monitoring protocols allows operators to quickly identify deviations in clamping performance. This includes using digital monitoring systems to track pressure and speed over time, enabling proactive adjustments before issues arise.
In summary, accurate machine settings are fundamental for maintaining efficient clamping force. Operators must be diligent in adjusting and monitoring these settings to prevent issues related to insufficient clamping.
Low clamping pressure leads to poor mold sealing.True
Insufficient pressure fails to keep the mold tightly closed, causing defects.
High clamping speed ensures even force distribution.False
Too fast a speed can cause collisions, leading to uneven force and damage.
Why Is Regular Maintenance Critical for Clamping Force?
Regular maintenance is crucial in maintaining optimal clamping force in injection molding machines.
Routine maintenance ensures the proper functioning of components essential to maintaining clamping force, such as the clamping cylinder and toggle mechanism. Neglecting maintenance can lead to wear and leakage, reducing clamping efficiency and causing production setbacks.
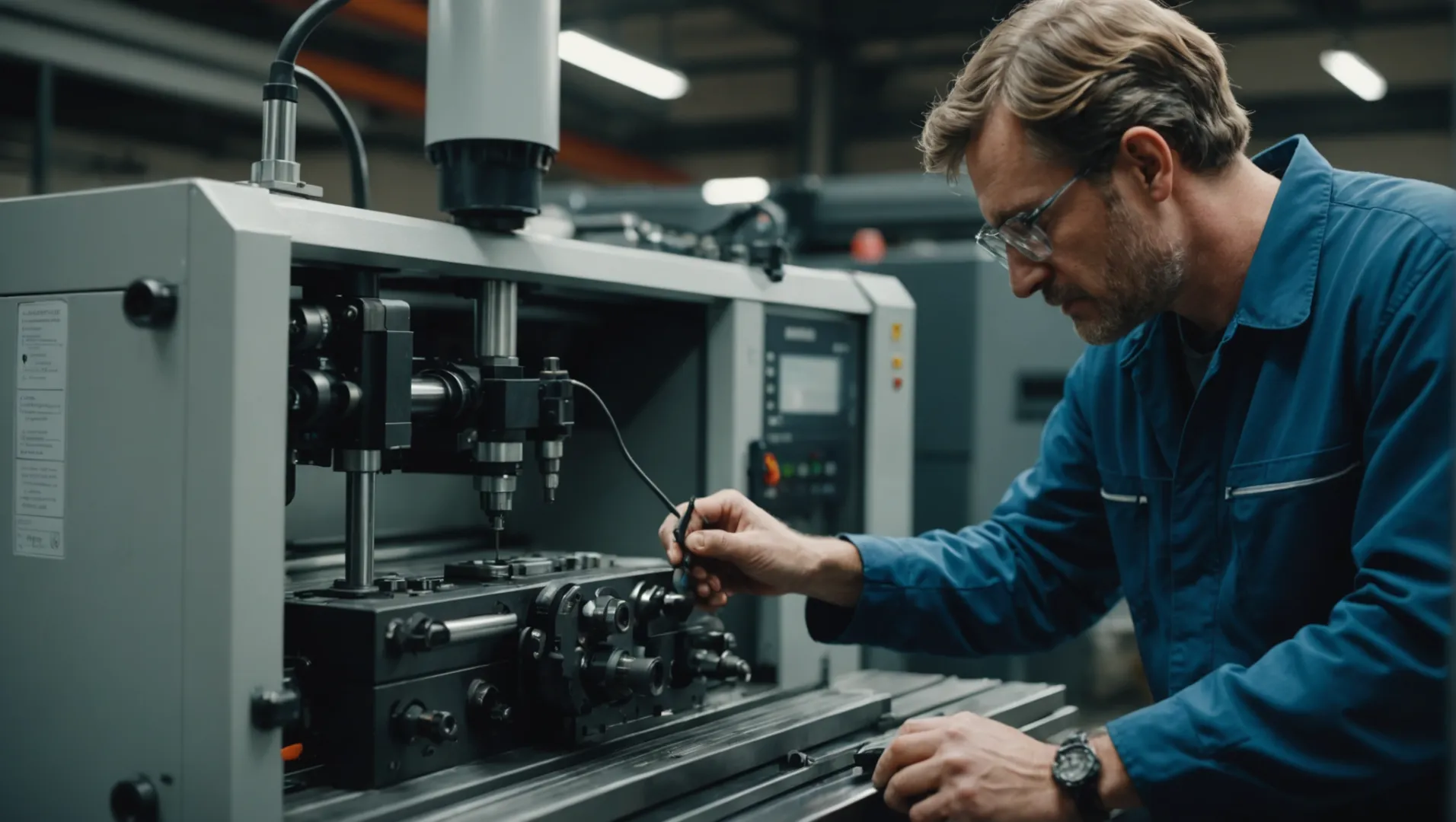
Importance of Maintaining the Clamping Cylinder
The clamping cylinder is pivotal in providing the force necessary to keep molds securely closed during the injection process. Regular inspection and maintenance of this component prevent leaks and ensure consistent pressure. For example, checking seals4 for wear and replacing them as needed can mitigate the risk of force loss.
The Role of the Toggle Mechanism
The toggle mechanism amplifies the clamping force, making it a critical element in the system. If this mechanism is not maintained, wear and tear can lead to inefficient force transmission. By lubricating joints5 and replacing worn parts, operators can maintain optimal clamping performance.
Maintenance Task | Frequency | Purpose |
---|---|---|
Inspect clamping cylinder | Monthly | Identify leaks or wear in seals |
Lubricate toggle joints | Bi-weekly | Ensure smooth movement and force transfer |
Check for abnormal noises | Ongoing | Detect issues early to prevent failures |
Impact of Ignoring Maintenance
Neglecting maintenance can cause several issues that hinder production efficiency. For instance, undetected leaks in the clamping cylinder could lead to inconsistent product quality, while unlubricated toggle joints might result in uneven clamping pressure, damaging molds and increasing downtime.
Implementing a Maintenance Schedule
A structured maintenance schedule not only prevents failures but also extends the lifespan of equipment. By adopting a proactive approach, such as setting specific intervals for component inspections6, businesses can enhance operational reliability and product consistency.
Regular maintenance prevents clamping force loss.True
Routine checks and repairs ensure components function properly, maintaining force.
Ignoring maintenance leads to increased production efficiency.False
Neglecting upkeep causes component wear, reducing efficiency and causing delays.
How Do Material Properties Influence Clamping Efficiency?
The efficiency of clamping in injection molding hinges significantly on the material properties used.
Material properties influence clamping efficiency primarily through their impact on mold expansion and fluidity during the injection process. High-fluidity materials can cause insufficient clamping force by exerting excessive expansion forces on the mold. Adjusting material composition or processing parameters can help manage these effects.
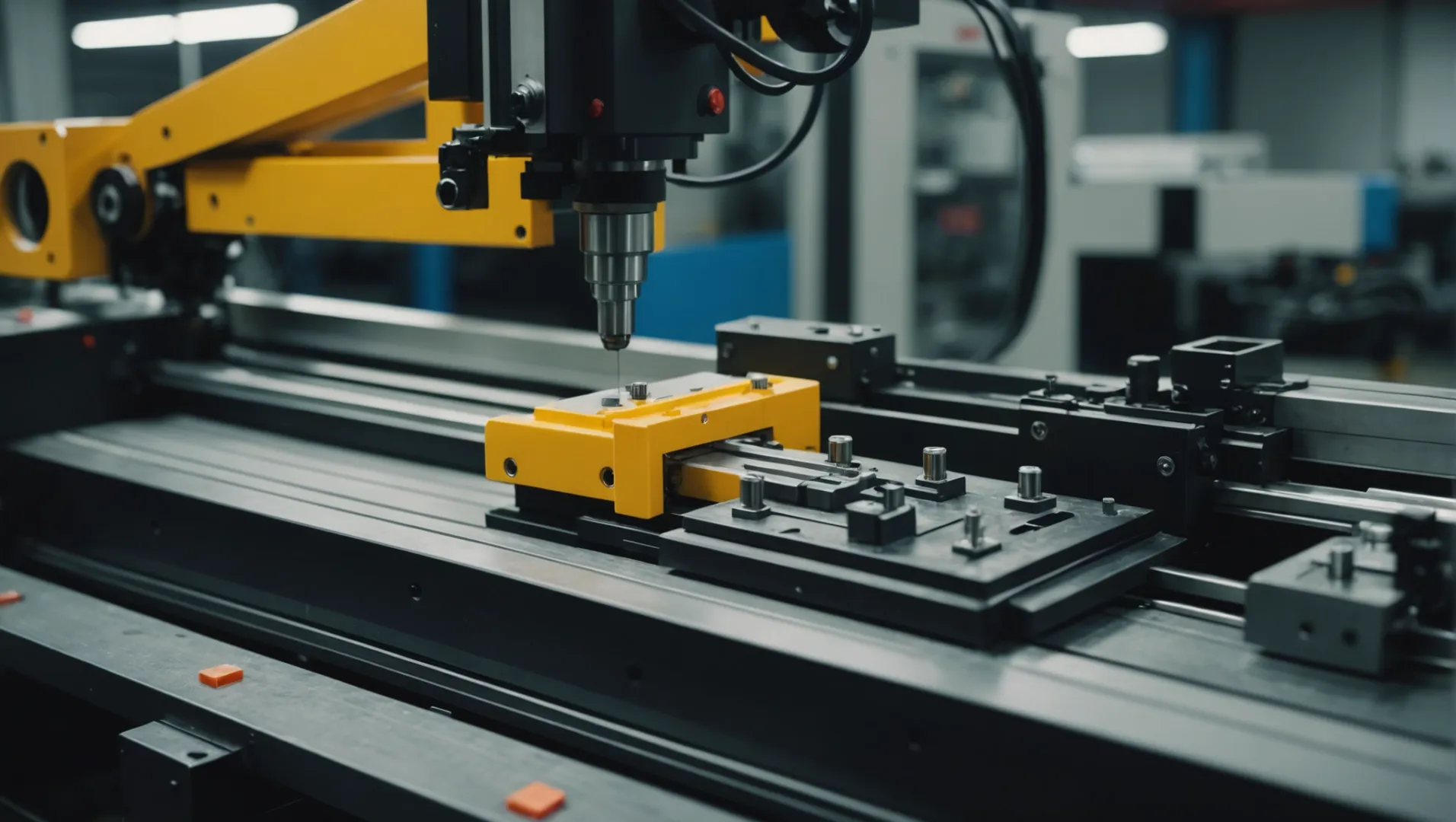
Understanding Material Fluidity and Its Impact
One of the primary ways material properties affect clamping efficiency is through fluidity. High-fluidity materials, such as certain engineering plastics, tend to flow easily into mold cavities. This characteristic, while beneficial for filling complex molds, can lead to increased expansion forces that challenge the clamping force. The material’s ability to flow freely can push against the mold surfaces, making it difficult to maintain a secure seal.
For instance, in scenarios involving high-fluidity plastics7, the clamping force may appear insufficient because the mold cannot fully counteract the material’s expansive pressure. This often necessitates adjustments in either the clamping pressure or the selection of materials with slightly reduced fluidity.
Strategies to Optimize Material Usage
To mitigate issues caused by high-fluidity materials, several strategies can be employed:
-
Material Selection: Opt for materials with lower inherent fluidity when possible. Alternatively, consider using additives or fillers that can reduce fluidity without compromising the material’s desirable properties.
-
Process Adjustments: Fine-tune the injection process by lowering the injection temperature or pressure. These changes can decrease the expansion force exerted by the material.
Here’s a quick comparison table to illustrate how different adjustments can affect clamping efficiency:
Adjustment Strategy | Expected Outcome |
---|---|
Lower Injection Temperature | Reduces material expansion, improving seal |
Add Fillers | Decreases fluidity, enhancing mold stability |
Increase Clamping Force | Counters expansion forces directly |
Case Study: Adjusting for Material Properties
Consider a case where a manufacturer faced issues with high-fluidity polycarbonate. By introducing a glass-fiber filler, they reduced the material’s fluidity. Additionally, they adjusted the injection temperature downward by 10 degrees Celsius, which resulted in significant improvement in clamping efficiency.
The Role of Consistent Material Quality
Consistency in material quality is crucial for maintaining efficient clamping. Variations in batches can lead to unexpected changes in fluidity or expansion characteristics, requiring constant recalibration of machine settings.
Using standardized material quality tests8 can help ensure consistency and reliability, minimizing disruptions in production and maintaining optimal clamping conditions.
High-fluidity materials reduce clamping efficiency.True
High-fluidity materials increase expansion forces, challenging clamping force.
Lowering injection temperature increases material fluidity.False
Lowering temperature decreases fluidity, reducing expansion forces.
Conclusion
Addressing clamping force issues can significantly enhance product quality and operational efficiency. Regularly evaluate machine settings, maintain components, and adjust designs and materials for the best results.
-
Learn how mold design tweaks improve clamping efficiency.: In injection molding, the magnitude of clamping force may affect the quality of plastic parts. A small clamping force may produce defects such as flashes … ↩
-
Gain insights into proper calibration for optimal machine performance.: First starts by contacting the manufacture of the injection molder and ask them what must be calibrated, how it must be done, and who they … ↩
-
Learn effective methods for parameter monitoring and adjustments.: Best practices. Regularly Monitor and Adjust Parameters: Keeping a close eye on parameters like injection pressure, mold temperature, and … ↩
-
Learn how seal checks prevent clamping force loss.: Make sure your hydraulic equipment is well sealed, so you can avoid any damage or leaks from faulty seals. There are a number of causes of faulty seals, and it … ↩
-
Discover how lubrication improves clamping efficiency.: Mainly to ensure the formation of lubricating oil film on the four guide columns, L-AN46 mechanical oil can be lubricated through oil cups and … ↩
-
Find out how inspections enhance machine longevity.: Your inspections should regularly check the mold for any condensation, as well as the nearby parts for any signs of deformity caused due to … ↩
-
Understand why high-fluidity impacts clamping force and explore mitigation strategies.: The fluidity of plastics varies with molding process conditions. Good fluidity is associated with high molding temperature and high injection pressure. ↩
-
Learn about tests ensuring consistent material properties for better clamping.: The first stage is the design stage, followed by Mold and Pre-Production Inspection and In Process Quality Control and Final Inspection. ↩